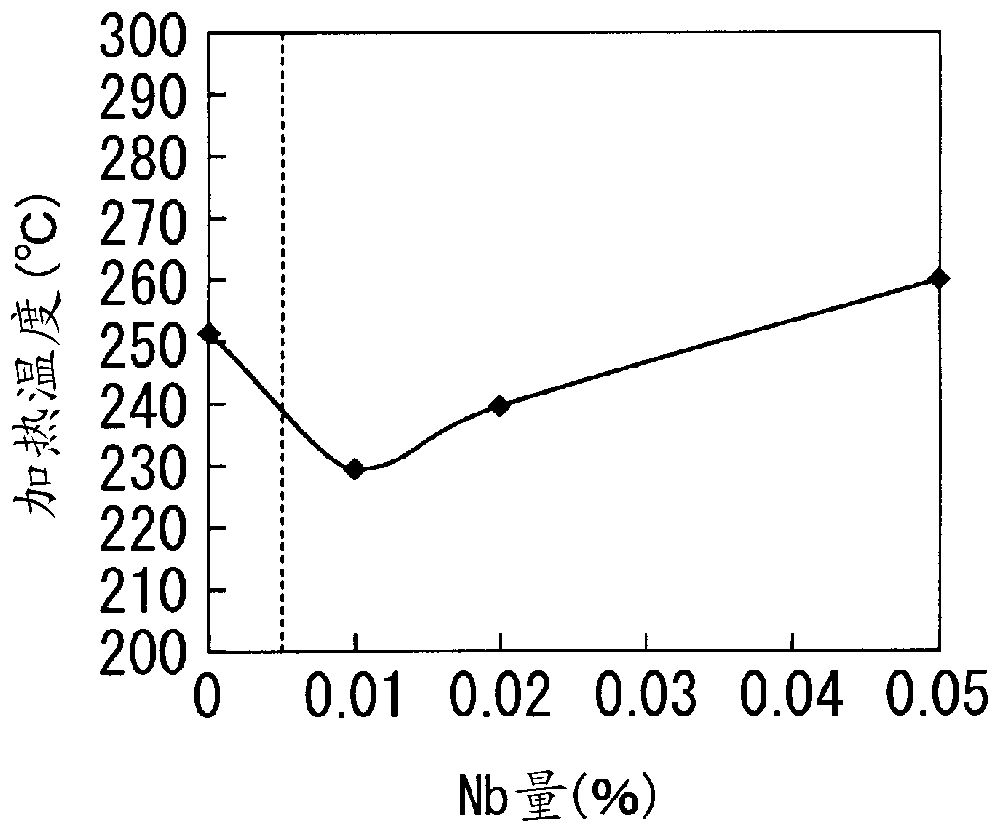
本发明涉及通过淬火回火处理被制造的作为各种机械零件的材料的高碳冷轧钢板。特别地涉及如下高碳冷轧钢板,前述高碳冷轧钢板的板厚不足1.0mm,前述高碳冷轧钢板在短时固溶处理淬火后,又在低温回火处理后,兼备充分的硬度(600~750hv)和优异的冲击特性(韧性),能够适当地应用于还对于耐久性、耐磨损性等要求苛刻的织针等。这里,短时固溶处理是指在760~820℃的温度范围内在3~15分的时间内进行的处理,低温回火处理是指200~350℃的温度范围下的处理。
背景技术:
:一般地,jis所规定的机械结构用碳素钢(s××c)或碳素工具钢(sk)被使用于各种大小的各种机械零件。在作为轧平材料被使用的情况下,在经过冲裁加工、各种塑性加工成形为零件形状后,进行淬火・回火处理。由此,被赋予既定的硬度和韧性(冲击特性)。特别是,例如,一种编织针织布料的织针,所述织针在以高速重复往复运动的同时,将线拖拉来编织针织布料。因此,织针在与旋转驱动部接触的针主体的针踵部需要充分的强度和耐磨损性,在末端部需要优异的冲击特性,在与线互相摩擦的钩部还需要充分的耐磨损性。作为织针用材料被使用的高碳冷轧钢板在板厚为1.0mm以上的情况下用作横织机用织针,在其板厚不足1.0mm的情况下适合用作圆织机或纵织机用织针。对于圆织机或纵织机用织针,具有0.4~0.7mm的板厚的材料多被使用,因为这样的织针将细径的线高速编织。织针用材料不仅需要具有优异的冷加工性(以下也称作二次加工性),而且需要在成形为针形状(二次加工)并淬火回火后,具有充分的硬度和在针末端部处的充分的韧性。jis所规定的机械结构用碳素钢(s××c)或碳素工具钢(sk)等所谓的高碳钢根据含碳量,将用途较细地分类。在含碳量不足0.8质量%的等级、即具有亚共析成分的钢,铁素体相的分数较高,因此,冷加工性优异,但难以得到充分的淬火硬度。因此,具有亚共析成分的钢不适合需要钩部的耐磨损性、针主体的耐久性的织针用途等。另一方面,0.8质量%以上的等级、即在具有亚共析成分的钢中,含碳量大于1.1质量%的高碳钢具有优异的淬火性,但由于较多地含有碳化物(渗碳体),冷加工性极端地差。因此,该等级不适合进行槽切加工等精密且细微的加工的织针用途等。含碳量比1.1质量%大的高碳钢被限定于刀具、冷作模具等具有简单形状且需要高硬度的零件用途。以往以来,对于织针,含有c:0.8~1.1质量%的碳素工具钢或合金工具钢或含有将这些钢的成分作为基础来向其添加第3元素的钢的成分的材料被广泛使用。在该织针的制造过程中,该材料被供于冲裁(剪切加工)、切削、拉丝、机械结合、弯曲等多种多样的塑性加工。因此,该织针制造用的材料需要具备针的制造工序中的材料加工时具有充分的加工性(二次加工性),并且具备在作为针实际使用时所要求的淬火回火处理后的硬度特性、冲击特性(韧性)。在织针的制造中,为了确保既定的硬度特性,对材料进行淬火回火处理。在该回火处理中,一般采用在200~350℃的温度范围下的低温回火处理。但是,当增加对于淬火性有效的mn、cr的添加量时,或较多地添加其他的第3元素时,重视硬度特性,有马氏体相的回火不充分,导致冲击特性(韧性)的提高不充分或韧性值不均的情况。另一方面,以提高织针的冲击特性为目的,减少材料的化学成分的作为杂质元素的p、s,使p的晶界偏析、mns夹杂物的生成极小化,实现将这些元素的不利影响的减少也是有效的对策。但是,从制钢技术上及成本经济性的观点出发,在通过减少p、s来实现织针的冲击特性的提高的方面存在极限。作为使冲击特性提高的手段,以往已知微观组织的细微化是有效的。例如,在专利文献1及2中,公开了添加ti、nb、v等碳氮化物形成元素来利用这些元素的细微碳氮化物使金属组织细微化的技术。但是,这些元素一般作为含有0.8质量%以下的含碳量的亚共析成分的钢的韧性提高对策而被添加。特别地,在200~350℃的低温回火条件下的马氏体相的冲击特性的各个第3元素的影响(特别是相互作用)未被充分弄清,假设各个元素的效果等价来进行成分设计的情况较多。例如,在专利文献1中所记载的技术将含有c:0.5~0.7质量%的亚共析钢作为对象,向其添加v、ti、nb等碳氮化物形成元素,来将旧奥氏体粒细微化,由此使韧性值(冲击特性)提高。在专利文献2中所记载的技术将含有c:0.60~1.30质量%的亚共析钢到过共析钢的具有广泛的碳含量的钢作为对象,根据需要,向其添加ni:1.8质量%以下、cr:2.0质量%以下、v:0.5质量%以下、mo:0.5质量%以下、nb:0.3质量%以下、ti:0.3质量%以下、b:0.01质量%以下、ca:0.01质量%以下的一种或二种以上,将未溶解碳化物的体积分数(vf)控制在(15.3×c质量%-vf)超过8.5~不足10.0的范围,由此使冲击特性提高。专利文献1:日本特开2009-24233号公报。专利文献2:日本特开2006-63384号公报。然而,专利文献1所记载的技术限于亚共析钢,是期待通过添加v、ti、nb等碳氮化物形成元素,来借助这些细微碳氮化物将旧奥氏体粒细微化的效果的技术。由于碳浓度是亚共析成分,所以专利文献1所记载的技术也是改善铁素体母相的成形性的技术。因此,难以将该技术应用于织针那样的需要高硬度的机械零件。此外,在专利文献2所记载的技术中,对于碳含量为0.67~0.81质量%的范围的亚共析钢,添加mo、v、ti、nb、b等。该mo、v、ti、nb、b等的添加显然为欲将亚共析钢的特性改善的添加。专利文献2没有公开任何关于各个第3元素在具有超过0.81质量%的含碳量的钢中的作用及其最佳化。进而,专利文献2所记载的技术关于第3元素的添加量,仅规定了不会由于第3元素对冲击值造成不利影响的上限值,未规定其下限值。由此,也可以说,专利文献2未公开以下技术:在预期的范围内添加第3元素,积极地希望添加元素的作用来增强冲击特性。进而,关于高碳冷轧钢板,专利文献1、专利文献2也未公开以下技术:在3~15分那样的短时固溶处理保持时间进行淬火,并且通过200~350℃的低温回火后,将所希望的冲击特性及既定硬度有利地改善,此外,关于板厚不足1.0mm的钢板进行评价冲击特性的技术也未被公开。技术实现要素:因此,本发明的目的在于提供一种高碳冷轧钢板(以下也简称作“冷轧钢板”),前述高碳冷轧钢板在实施短时固溶处理后和淬火及低温回火处理后,能够显示冲击值为5j/cm2以上、且硬度为600~750hv的范围的机械特性,前述高碳冷轧钢板的板厚不足1.0mm。本发明人们为了解决上述问题,对于高碳冷轧钢板的化学成分的适当的添加范围和钢中的碳化物的粒径和存在方式进行了广泛研究。从加工性、淬火性、低温回火后的硬度和韧性等观点来看,本发明将含碳量限于适合织针的c:0.85质量%以上1.10质量%以下,本发明的核心是发现以下内容:为了显示目标特性,在该含碳量的范围作为第3元素在既定的范围添加nb,并且控制碳化物的平均粒径和球化的程度较为有效。特别地,本发明人们开发了,将以往韧性评价较难的板厚不足1.0mm的钢板为对象的、用于韧性评价的新的试验法(新冲击试验法)。将新的试验法(新冲击试验法)在图1及图2中表示。利用该新冲击试验法,对于添加了各种第3元素的板厚不足1.0mm的高碳冷轧钢板,调查淬火和低温回火状态的冲击值。结果,发现以下新的内容:只有既定量的nb的添加是满足上述目标的特性的。本发明是基于这样的知识而作出的。即,本发明人们为了解决上述课题而进行锐意研究,发现以下内容:对于将基本成分规定为c:0.85~1.10质量%,mn:0.50~1.0质量%,si:0.10~0.35质量%,p:0.030质量%以下,s:0.030质量%以下,cr:0.35~0.45质量%的范围的高碳钢必须添加0.005~0.020质量%的nb,将碳化物的球化和平均粒径控制在既定的范围,由此能够得到兼具优异淬火性和优异韧性的高碳冷轧钢板,还发现这也能够实现淬火处理时间的短缩或回火温度的下降。此外,通过采用适当的评价薄板的冲击特性的试验方法,能够规定适当的化学成分及碳化物的球化率、平均粒径。首先,对本发明人们进行的实验结果进行说明。一种冷轧钢板(小于1mm厚)以如下方式被制造:对于热轧钢板(4mm厚),分别重复冷轧(辊制压下率:25~65%,最终为3~50%)和软化退火及球化退火(640~700℃)5次,前述热轧钢板具有的成分以质量%计含有1.01%c-0.26%si-0.73%mn-0.42%cr-0.02%mo,进而将nb的量变化为0%、0.010%、0.020%、0.055%来添加,剩余部分为fe及不可避的杂质。对于所得到的冷轧钢板,实施以780℃、800℃的两个级别的加热温度、使保持时间在0~16分的范围内变化的固溶处理后,进行油淬火,然后测定维氏硬度(hv)。将所得到的结果以固溶处理的加热保持时间(分)和淬火硬度(hv)的关系表示在图3(加热温度:800℃)、图4(加热温度:780℃)。根据图3、图4可知,nb含量为0.010质量%的冷轧钢板以最短的加热保持时间,能够确保超过700hv的淬火硬度。当nb含量超过0.010质量%时,短时间加热保持的硬度上升减慢。根据图4的结果,在固溶处理的加热温度为780℃的情况下,求出淬火硬度到达700hv的加热保持时间,将与nb含量的关系在图5中表示。图5示出当nb含量为0.020质量%以上时,淬火硬度到达700hv的固溶处理的加热保持时间大致恒定。当nb含量为0.005~0.015质量%的范围时,为了确保所希望的淬火硬度(700hv)的固溶处理的加热保持时间变为最短,同时能够确保稳定的淬火性。进而,以该范围的nb含量,能够缩短固溶处理的加热保持时间。根据以上事实,发现使nb含量变为0.005~0.015质量%的范围,是能够有效防止针加工制造商中的如下问题的对策,前述问题为,淬火引起的膨胀不均和淬火引起的弯曲。与此同时,对于具有各种nb含量的冷轧钢板,实施加热温度:800℃、加热保持时间:10分的固溶处理,进行油淬火,进而实施回火处理。在回火处理中,回火温度设为150℃、200℃、250℃、300℃、350℃的各种温度,将保持时间设为1小时。回火处理后调查冲击特性。另外,冲击特性使用图1、图2所示的新试验法来进行。将所得到的结果表示在图6中。冲击值在回火温度为200℃以上的情况下,nb含量为0.010质量%的情况最高。根据图6,求出得到冲击值:5j/cm2的回火温度,将与nb含量的关系在图7中表示。图7示出得到冲击值:5j/cm2的回火温度在nb含量:0.010质量%的钢板的情况为最低。当nb含量超过0.020质量%地增加时,得到冲击值:5j/cm2的回火温度为高温侧。在回火温度为高温时,硬度低下,作为针的耐久性下降。此外,发现nb含量不足0.005质量%的情况下,为了确保所希望的冲击值,需要使回火温度为高温。图5、图7示出,为了兼具回火后的高硬度和优异冲击特性,nb含量的下限为0.005质量%,上限为0.020质量%。进而,为了使固溶处理的加热保持时间为短时间,优选地使nb含量的上限被设为0.015质量%。本发明是基于该见解进一步加以研究而完成的。即,本发明的要旨如下所述。[1]一种高碳冷轧钢板,其特征在于,钢板的化学成分含有,c:0.85~1.10质量%,mn:0.50~1.0质量%,si:0.10~0.35质量%,p:0.030质量%以下,s:0.030质量%以下,cr:0.35~0.45质量%,nb:0.005~0.020质量%,剩余部分为fe及不可避杂质,分散于前述钢板中的碳化物的平均粒径dav和球化率(nsc/ntc)×100%分别满足下述(1)式及(2)式,前述钢板的板厚不足1.0mm,0.2≤dav≤0.7(μm)(1);(nsc/ntc)×100≥90%(2);其中,(1)式的平均粒径dav为各个圆的直径的平均值,此时,假设前述圆具有与在钢板截面被观察的各个碳化物相等的面积,前述圆的直径即为圆等效直径,而且,(2)式的ntc及nsc分别为,ntc:每100μm2观察面积的碳化物的总个数,nsc:满足dl/ds为1.4以下的条件的碳化物个数,将碳化物的长轴设为dl,短轴设为ds。[2]一种前述[1]所述的高碳冷轧钢板,其特征在于,前述化学成分还含有从mo及v内选择的1种或2种,各自的含量均为0.001质量%以上且不足0.05质量%。[3]一种高碳冷轧钢板的制造方法,其特征在于,对由[1]或[2]所述的化学成分组成的热轧钢板重复进行冷轧及球化退火来制造高碳冷轧钢板的方法中,分散于前述高碳冷轧钢板中的碳化物的平均粒径dav、球化率nsc/ntc分别满足下述(1)式及(2)式,前述高碳冷轧钢板的板厚不足1.0mm,0.2≤dav≤0.7(μm)(1);(nsc/ntc)×100≥90%(2);其中,(1)式的平均粒径dav为各个圆的直径的平均值,此时,假设前述圆具有与在钢板截面被观察的各个碳化物相等的面积,前述圆的直径即为圆等效直径,此外,(2)式的ntc及nsc分别为,ntc:每100μm2观察面积的碳化物的总个数;nsc:满足dl/ds为1.4以下的条件的碳化物个数,将碳化物的长轴设为dl,短轴设为ds。[4]前述[3]所述的高碳冷轧钢板的制造方法,其特征在于,对前述热轧钢板重复进行冷轧及球化退火的次数设为2~5次。[5]前述[3]或[4]所述的高碳冷轧钢板的制造方法,其特征在于,前述冷轧的辊制压下率为25~65%,前述球化退火的温度为640~720℃。本发明的高碳冷轧钢板是以下钢板:板厚不足1.0mm、特别地板厚薄至0.4~0.7mm的薄的高碳冷轧钢板,将碳化物的平均粒径的大小控制为0.2~0.7μm的大小,同时将球化率控制为90%以上。若对于该钢板,实施淬火、回火的热处理,即使通过3~15分这样短时间的固溶处理,也能够通过淬火、低温回火的热处理得到良好的冲击特性(冲击值:5j/cm2以上)及硬度特性(600~750hv)。进而,本发明的高碳冷轧钢板在短时固溶处理后,淬火,成为包括不可避免地残留γ相的马氏体相后,在进行200~350℃的所谓的低温回火的条件下,对于以往的高碳冷轧钢板,在硬度和冲击特性(韧性)的平衡的方面发挥明确的优越性。即,使用本发明的高碳冷轧钢板,能够确保优异淬火性,并且能够得到淬火回火后的韧性优异的高碳钢制机械工具零件。特别地,在本发明中被公开的冷轧钢板适合如下用途:前述用途不仅需要硬度和韧性的平衡,还需要耐磨损性和耐疲劳特性,例如织针那样的苛刻的使用环境下需要优异的耐久性。附图说明图1是表示用于本发明的评价的冲击试验的试验装置的例子的说明图。图2是表示用于本发明的评价的冲击试验的试验片的形状的说明图。图3是表示淬火硬度和固溶处理的加热保持时间的关系的图表(加热温度:800℃)。图4是表示淬火硬度和固溶处理的加热保持时间的关系的图表(加热温度:780℃)。图5是表示能够得到淬火硬度700hv的固溶处理的加热保持时间和nb含量的关系的图表。图6是表示冲击值和回火温度的关系的图表。图7是表示能够得到冲击值:5j/cm2的回火温度和nb含量的关系的图表。具体实施方式以下,对本发明的实施方式进行说明。首先,本发明的钢板是,将热轧钢板根据需要进行软化退火,交替重复冷轧和球化退火,作为高碳冷轧钢板得到的板厚不足1.0mm的钢板。之后,对该高碳冷轧钢板进行既定的二次加工及固溶处理,然后实施淬火和回火处理,作为织针等部件(机械零件)被使用。首先,对将本发明的钢板的化学成分规定为c:0.85~1.10质量%、mn:0.50~1.0质量%、si:0.10~0.35质量%、p:0.030质量%以下、s:0.030质量%以下、cr:0.35~0.45质量%、nb:0.005~0.020质量%的理由在以下进行说明。c:0.85~1.10质量%c是高碳冷轧钢板的热处理后为了得到充分的硬度的必需元素。决定其下限值,使得能够确保织针等那样的精密零件中的600~750hv的硬度,此外决定其上限值,使得能够将碳化物量控制在不妨碍多种多样的冷加工的浓度。即,下限值为了在短时间的淬火回火处理中稳定地确保600hv的硬度而规定为0.85质量%。上限值作为能够承受冲裁性、模锻性(swagingproperty)、弯曲性、切削性等多方面的塑性加工的上限而规定为1.10质量%。若通过重复冷轧和球化退火来进行碳化物的球化处理,则冷加工性被改善。但是,若c超过1.10质量%,则也出现热轧工序或冷轧工序中的轧制负荷变高,或线圈端部的破损的发生频率显著变高等制造工序上的问题。因此,c规定为0.85~1.10质量%的范围。另外,该范围优选为0.95~1.05质量%。mn:0.50~1.0质量%mn是对于钢的脱氧有效的元素,并且同时是通过使钢的淬火性提高来能够稳定地得到既定的硬度的元素。在以被应用于苛刻的用途的高碳钢板为对象的情况下,mn在0.50质量%以上本发明的效果显著。因此,下限值规定为0.50质量%。另一方面,若mn超过1.0质量%,则热轧时mns大量析出而粗大化,所以零件加工时破损等多有发生。因此,上限值规定为1.0质量%。由此,mn规定为0.50~1.0质量%的范围。另外,该范围优选为0.50~0.80质量%。si:0.10~0.35质量%si是钢的脱氧元素,所以在熔炼清浄钢上是有效的元素。si也是提供马氏体的抗回火软化性的有效的元素。由此,下限值规定为0.10质量%。若大量添加,则低温回火下的马氏体的回火不充分,使冲击特性劣化,所以其上限值规定为0.35质量%。因此,si规定为0.10~0.35质量%的范围。p:0.030质量%以下,s:0.030质量%以下p、s作为杂质元素不可避免地存在于钢中,均对冲击特性(韧性)造成不利影响,所以优选地尽量减少。p为0.030质量%以下、s为0.030质量%以下的含有量在实际使用上都是没有问题的。由此,p规定的含量为0.030质量%以下,s的含量规定为0.030质量%以下。另外,为了维持更优异的冲击特性,优选地,设为p的含量为0.020质量%以下、s的含量为0.010质量%以下的含有量。cr:0.35~0.45质量%cr是使钢的淬火性提高的元素。但cr固溶于碳化物(渗碳体)中会引起在加热阶段的碳化物的再溶解延迟,而因此大量地添加cr,则cr相反地阻碍淬火性。因此,将cr的上限值规定为0.45质量%。考虑淬火回火后的硬度和冲击特性的平衡,cr的下限值规定为0.35质量%。由此,cr规定为0.35~0.45质量%的范围。nb:0.005~0.020质量%nb以往作为在热轧时扩大钢的未再结晶温度区的元素,同时作为以nbc析出而有助于奥氏体粒的细微化的元素而被公知。因此,也有期待冷轧工序以后的组织的细微化效果对高碳钢添加nb的情况。在本发明中,将淬火后的低温下的回火的韧性恢复为主目的,将nb以0.005~0.020质量%添加。若是微量的nb添加,则nb呈稀薄(希薄)固溶状态,不形成充分的nbc来有助于组织的细微化。nb呈稀薄固溶状态,由此被认为具有bcc结构的铁素体相和马氏体相中的c的扩散被促进。即,淬火处理的加热时从球状碳化物溶向铁素体相的c向奥氏体相的扩散、及、回火处理的加热时马氏体相中的过饱和固溶c的扩散和析出被促进。结果,在现在的时间考虑能够使短时间加热下的淬火性的提高和低温回火处理的韧性的恢复的并存。若nb被超过0.020质量%地添加,则nbc的析出变得显著,不能确保nb的稀薄固溶状态,相应地不能确认由nb的稀薄固溶状态引起的c的扩散的促进效果。因此,nb添加量的上限规定为0.020质量%。另外,优选为0.015质量%以下。另一方面,nb添加量不足0.005质量%的话,无法期待上述效果。因此,nb添加量的下限规定为0.005质量%。由此,nb规定为0.005~0.020质量%的范围。上述的成分是基本的成分,在本发明中作为任意的选择元素,根据需要,还能够含有从mo及v中选择的1种或2种。mo及v会被不可避地分别含有以下的量:mo:不足0.001质量%、v:不足0.001质量%。在本发明中,为了使淬火性或回火后的冲击特性提高,可以将mo和v比不可避免地含有的浓度多地添加。但是,若将mo、v在既定量以上地添加,则nb的添加效果丧失。所以为了将nb的添加效果最大限度地发挥,在添加的情况下,优选地将mo和v的含量控制为以下的范围。mo:0.001质量%以上且不足0.05质量%mo是对于钢的淬火性提高有效的元素。但添加量较多时,在200~350℃的低温回火下,有时使冲击特性恶化。因此,在添加mo的情况下,其添加量被规定为比不可避地含有的浓度多的0.001质量%以上、不妨碍冲击特性的范围的不足0.05质量%。优选地,mo的添加为0.01~0.03质量%。v:0.001质量%以上且不足0.05质量%v是在通过将钢组织细微化来有效地提高冲击特性的元素,但是是有时使淬火性恶化的元素。因此,在添加v的情况下,其添加量被规定为比不可避地含有的浓度多的0.001质量%以上、不妨碍淬火性的范围的不足0.05质量%。优选地,v的添加是0.01~0.03质量%。上述的成分以外的剩余部分是fe及不可避的杂质。接着,对本发明的钢板的碳化物进行说明。在本发明的高碳冷轧钢板中,分散于钢板中的碳化物的平均粒径(dav)和球化率(nsc/ntc)需要分别满足下述(1)式及(2)式。0.2≤dav≤0.7(μm)…(1)(nsc/ntc)×100≥90%…(2)这里,(1)式的平均粒径(dav)(μm)为,设想具有与在钢板截面观察的各个碳化物相等的面积的圆时,各个圆的直径(圆等效直径)的平均值。平均粒径(dav)处于该范围会使得冲击特性优异,而且有即使通过短时固溶处理也容易地实现所希望的淬火硬度的效果。在经验上,平均粒径(dav)不足0.2μm会使加工成针形状的二次加工时的负荷增大。平均粒径(dav)超过0.7μm则不被优选,这是因为这使得通过短时固溶处理难以实现所希望的淬火性提高。本发明中还将碳化物球化的比例即球化率用(2)式的ntc及nsc定义。这里,ntc是每100μm2观察面积的碳化物的总个数。此外,nsc是在同一观察视野中视为球化的碳化物的个数,设为满足dl/ds为1.4以下的条件的碳化物个数。这里,将碳化物的长轴设为dl,短轴设为ds。碳化物不能称为被形成为完全的球状,但根据观察面而被观察为椭圆形的情况较多。所以根据长轴和短轴的比(dl/ds),规定球化的程度。根据该情况,本发明将满足dl/ds为1.4以下的条件的碳化物视为球化,定义其个数即nsc。此外,球化率(nsc/ntc)×100为90%以上是因为发现,球化率在该范围的话会提高钢板的二次加工性的经验上的见解。以上说明的碳化物的平均粒径及球化率的测定使用扫描型电子显微镜,通过将二次电子显微镜图像以2千倍的倍率观察来进行。通过使用冷轧后的钢板,以与热处理前的样品的压延方向成直角方向切下板状试验片。进行树脂埋入等处理,并且在板厚中央部附近的100μm2观察面积的范围内,对碳化物进行测定,来测定圆等效直径、dl/ds比、ntc、nsc,并且计算5个视野的平均值。对于这些测定及计算,使用市售的画像解析软件“winroof”(商品名)。接着,对本发明的钢板的制造方法进行说明。本发明使用的热轧钢板可以是通常的制造条件下所得到的。例如,在本发明中被使用的热轧钢板能够如下地被制造:将具有前述的化学成分的钢片(slabs)加热至1050~1250℃,在800~950℃的终轧温度下对已加热的钢片进行热轧,在600~750℃的卷绕温度下卷绕该产物。在这一点上,热轧钢板的板厚可以适当设定,来获得基于所希望的冷轧钢板的板厚的优选的冷轧压下率。重复冷轧(25~65%)和球化退火(640~720℃)两次以上,由此制造板厚不足1.0mm的高碳冷轧钢板。该冷轧(25~65%)和球化退火(640~720℃)分别优选地进行2~5次。在本发明中,重复冷轧(25~65%)和球化退火(640~720℃)两次以上。其理由是,如下所述,控制碳化物的平均粒径(dav)和球化率(nsc/ntc)×100来分别满足上述的(1)式及(2)式。首先,通过冷轧,破损被导入至碳化物,而且通过球化退火,开始压碎的碳化物球化。但是,仅通过一次的球化退火,难以将碳化物的球化率提高至90%以上,会残留棒状或板状的碳化物。那样的情况下,也会对淬火性有不利影响,使形成精密零件的冷加工性恶化。因此,为了使碳化物的球化率(nsc/ntc)×100为90%以上,最适合的是交替重复冷轧和球化退火。结果,得到钢板中细微且球化率高的碳化物的分布。特别地,优选为2~5次的冷轧和2~5次的球化退火。若对冷轧的辊制压下率不足25%的钢板(冷轧钢板)进行球化退火,则碳化物会粗大化。另一方面,在冷轧的辊制压下率超过65%的情况下,有时冷轧操作的负荷过大。因此,冷轧的辊制压下率优选为25~65%的范围。另外,在最终的冷轧中,冷轧后不进行球化退火,所以辊制压下率的下限不被特别地限定。若球化退火温度比640℃低,则球化容易不充分,若以比720℃高的温度重复球化退火,则碳化物容易粗大化。因此,球化退火温度优选为640~720℃的范围。球化退火的保持时间可以以该范围的温度在9~30小时的范围内适当选择来进行。在这一点上,关于以冷轧前的热轧钢板的软化为目的的软化退火,也优选同样的温度范围。以上是本发明的高碳冷轧钢板的制造方法。为了制成作为该钢板的最终的目的的织针那样的机械零件,在该钢板加工成既定的形状之后,优选进行以下的热处理。将分布有90%以上球化的碳化物的高碳冷轧钢板加工成各种机械零件后(冲压加工、槽切加工、挤锻加工等),然后进行固溶处理,急冷(淬火),并且实施回火处理。在固溶处理将中,加热温度设为760~820℃,并且将加热保持时间设为较短时间的3~15分。淬火(急冷)优选地使用油。在回火处理中,优选地将回火温度设为200~350℃。回火温度更优选为250~300℃。由此,能够制造具有硬度600~750hv的各种机械零件。若固溶处理的加热保持时间比15分长,则碳化物过度溶入,奥氏体粒粗大化,由此淬火后的马氏体相变粗,这使得冲击特性劣化。因此,固溶处理的加热保持时间的上限优选为15分。另一方面,若加热保持时间比3分短,则碳化物的溶入不充分,这使得淬火变得困难。所以固溶处理的加热保持时间的下限优选为3分。更优选为5~10分的范围。在回火温度不足200℃的情况下,马氏体相的韧性恢复不充分。另一方面,若回火温度超过350℃,则虽然冲击值恢复,但硬度低于600hv,所以耐久性、耐磨损性成为问题。由此,回火温度的适当范围优选为200~350℃。另外,更优选为250~300℃。回火的保持时间能够在30分~3小时的范围适当选择来进行。实施例将具有各种各样的化学成分的钢真空溶解并铸入30kg的钢块。将该钢块切片(slab),然后以1150℃的加热温度、870℃的终轧温度的条件进行热轧,来生产4mm及2mm的热轧钢板。之后,以表1所示的制造条件进行冷轧及球化退火,形成板厚为0.4mm以上且不足1.0mm的冷轧钢板。接着,对该冷轧钢板,以表2所示的条件,进行固溶处理(被装入800℃的炉中10分),然后进行油淬火,并进行回火(回火温度:250℃)。从回火处理后的钢板抽取既定的试验片,其之后被供于冲击试验及硬度测定试验。硬度测定根据jisz2244的规定,以维氏硬度计测得的在负荷5kg重(试验力:49.0n)的条件下进行。冲击特性通过沙尔皮冲击试验来评价。冲击试验片设为刻痕宽度为0.2mm的u刻痕试验片(刻痕深度2.5mm、刻痕半径0.1mm)。图1表示在试验装置上设置有试验片的状态,图2表示试验片的形状。之所以采用这样的试验片及试验方法,是由于以下的理由。存在如下问题,在以往被使用的金属材料用沙尔皮冲击试验装置中,试验装置的额定容量为50j以上,对于本发明作为对象的板厚不足1.0mm的钢板过大,结果不能进行准确的评价。作为试验装置的额定容量比50j小的冲击试验装置,使用1j的冲击试验装置((株)东洋精机制作所制,型号为dg-gb)。该试验装置是基于炭素纤维强化塑料的沙尔皮冲击试验方法(jisk7077)的沙尔皮冲击试验机。将该试验装置在将支承台间距离被从60mm改为40mm的条件下使用。在本试验装置中,将支承台间距离从60mm改为40mm,是为了得到与对于金属材料的沙尔皮冲击试验方法的jis规格(jisz2242)接近的条件。使用将u刻痕通过放电加工来形成的试验片,来得到刻痕深度为2.5mm、刻痕半径为0.1mm(刻痕宽度为0.2mm)的试验片,如图2所示。沙尔皮冲击试验时不足1.0mm的薄板的情况下板的挠曲成为问题。因此,将刻痕半径变小,来通过使应力集中系数变高,使沙尔皮冲击试验时的板的挠曲成为最小限度,能够得到稳定的冲击值。通过采用该试验方法及试验片形状,确认能够得到与实际使用环境接近的状态的冲击特性。在本发明中,判断成冲击值的数值为5j/cm2以上的情况下冲击特性优异。表1条件no.冷轧钢板的制造条件(辊制压下率、退火温度)1热轧(2mm)→冷轧(20-65%)→球化退火(700℃)→冷轧(3-50%)2a热轧(2mm)→冷轧(10-20%)→球化退火(600-635℃)→冷轧(10-20%)→球化退火(600-635℃)→冷轧(3-50%)2b热轧(2mm)→冷轧(25-65%)→球化退火(640-720℃)→冷轧(25-65%)→球化退火(640-720℃)→冷轧(3-50%)2c热轧(2mm)→冷轧(70-85%)→球化退火(600-635℃)→冷轧(70-85%)→球化退火(600-635℃)→冷轧(3-50%)2d热轧(2mm)→冷轧(10-20%)→球化退火(640-720℃)→冷轧(10-20%)→球化退火(640-720℃)→冷轧(3-50%)5a热轧(4mm)→软化退火(700℃)→冷轧(25-65%)→球化退火(690℃)→冷轧(25-65%)→球化退火(680℃)→冷轧(25-65%)→球化退火(660℃)→冷轧(25-65%)→球化退火(640℃)→冷轧(3-50%)5b热轧(4mm)→软化退火(700℃)→冷轧(10-20%)→球化退火(690℃)→冷轧(10-20%)→球化退火(680℃)→冷轧(10-20%)→球化退火(660℃)→冷轧(10-20%)→球化退火(640℃)→冷轧(3-50%)表2(实施例1)固溶处理后进行油淬火,确认涉及截面硬度及冲击值的各种添加元素的影响。将试验结果与化学成分一同表示在表3及表4中。冷轧钢板的制造条件为两者都用5a的条件(表1)。辊制压下率控制在被记载于表1的范围。截面硬度通过将在压延直角方向上切出的试验片埋入于树脂,将截面研磨后,在板厚中央部进行测定。冲击值使用在压延平行方向上抽取的冲击试验片来测定。将所得到的结果(硬度和冲击值)在表3及表4表示。冲击值比5j/cm2大且同时硬度满足600~750hv的条件评价为◎,不满足冲击值及硬度的上述目标值的某一个的情况评价为×。表3注1)其他元素;p:0.010-0.020质量%,s:0.001-0.010质量%注2)固溶处理温度:800℃,加热保持时间:10分,回火温度:250℃注3)◎:优秀,×:劣质。表4注1)其他元素;p:0.010-0.020质量%,s:0.001-0.010质量%注2)固溶处理温度:800℃,加热保持时间:10分,回火温度:250℃注3)◎:优秀,×:劣质。在表3所示的例子中,含碳量偏离下限值的例子(钢种no.1)显示了冲击值及淬火回火硬度偏离目标值。含碳量偏离上限值的例子(钢种no.6)显示了淬火回火硬度超过目标值600~750hv,且冲击值低于目标值5j/cm2。不含nb的例子中,含碳量为0.85质量%的例子(钢种no.2、比较例)、含碳量为1.10质量%的例子(钢种no.4、比较例)显示的冲击值均低于目标值5j/cm2,评价为×。与此相对,相当于发明例的化学成分的钢板(钢种no.3、5、7、8、9、10)显示的淬火回火硬度在目标范围内,且显示优异的冲击特性。在表4所示的例子中,具有相当于发明例的化学成分的钢板(钢种no.15、16、17、19、21)显示的淬火回火硬度都满足目标值600~750hv,且显示优异的冲击特性。不添加nb的例子(钢种no.11)、不添加nb而v添加量超过0.05质量%的例子(钢种no.12)、不添加nb而mo添加量超过0.05质量%的例子(钢种no.13)、nb+mo复合添加且nb添加量比0.005质量%少的例子(钢种no.14)、nb+mo复合添加且nb添加量超过0.020质量%的例子(钢种no.18)、nb+mo复合添加且mo添加量比0.05质量%多的例子(钢种no.20)、nb+mo+v复合添加且v添加量比0.05质量%多的例子(钢种no.22),显示淬火回火硬度满足目标值600~750hv,但显示不好的冲击特性,或显示冲击特性满足目标值5j/cm2但显示低淬火回火硬度,或显示淬火回火硬度及冲击特性都低于目标值的下限。(实施例2)使用具有钢种no.3(表3)的化学成分的热轧钢板,使表1所述的冷轧和球化处理的制造条件变化,在该条件下得到表5所示的板厚的冷轧钢板。将所得到的冷轧钢板的球化率、碳化物平均粒径在表5中表示。进而,对所得到的冷轧钢板与实施例1同样地,以表2所示的条件,在固溶处理后实施油淬火和低温回火。将所得到的冷轧钢板的固溶处理和淬火回火后的截面硬度及冲击值与实施例1同样地测定,在表5中表示。表5注1)表3中所述的钢种no.3注2)固溶处理温度:800℃,加热保持时间:10分,回火温度:250℃注3)◎:优秀,×:劣质。球化退火次数为1次的例子(制造条件no.1)的球化率不充分,且冲击特性不好。球化退火次数为2次的情况,将球化退火温度设为600~635℃,将辊制压下率设为10~20%来组合分别进行两次球化退火和冷轧,球化不充分,冲击特性不好(制造条件no.2a)。若将球化退火温度设为600~635℃,将辊制压下率设为70~85%来组合分别重复两次球化退火和冷轧,则得到的冲击特性充分,但碳化物的平均粒径偏离下限,淬火回火处理后的硬度超过目标值(制造条件no.2c)。若将球化退火温度设为640~720℃,将辊制压下率设为10~20%来组合分别重复2次球化退火和冷轧,则球化充分,但碳化物的平均粒径超过目标值的上限,冲击特性不好(制造条件no.2d)。这是被认为由于若碳化物过大,则淬火时马氏体基底的未溶解碳化物变得相当大,且容易变为破坏时的起点,未溶解的碳化物与马氏体基底的界面的面积较大,冲击特性不好。与此相对,若通过将球化退火温度设为640~720℃、将辊制压下率设为25~65%的组合分别重复2次球化退火和冷轧,则球化率、碳化物粒径、淬火回火后的硬度分别收敛于目标值的范围,且得到优异的冲击特性(制造条件no.2b)。若将球化退火次数设为4次时,使第1次~第4次的冷轧的辊制压下率都为25~65%,则球化率、碳化物粒径收敛于目标值的范围,也得到优异的冲击特性(制造条件no.5a)。若使得与制造条件no.5a的球化退火温度相同,使第1次~第4次的冷轧的辊制压下率都为10~20%,则碳化物粒径超过目标值变为过大,得到不好的冲击特性(制造条件no.5b)。(实施例3)使用具有钢种no.16(表4)的化学成分的热轧钢板,使表1所述的制造条件变化,得到具有表6所示的板厚的冷轧钢板。将所得到的冷轧钢板的球化率、碳化物平均粒径在表6中表示。进而,与实施例1同样地对所得到的冷轧钢板以表2所示的条件,在固溶处理后实施油淬火和低温回火。将所得到的冷轧钢板的固溶处理后和后来的淬火回火后的截面硬度及冲击值与实施例1相同地测定,在表6中表示。使用相当于本发明的制造方法的制造条件no.2b、no.5a进行冷轧、球化退火的钢板满足目标球化率、目标冲击值。表6注1)表4中所述的钢种no.16注2)固溶处理温度:800℃,加热保持时间:10分,回火温度:250℃注3)◎:优秀,×:劣质。产业上的可利用性具有本发明范围的化学成分的钢板通过nb的添加,淬火性提高,且热处理后的冲击特性被改善,且因此适用于用作在苛刻的环境被使用的机械工具零件中的过共析钢。含有c为0.85~1.10质量%的过共析钢板适合用于织针那样的苛刻的使用环境下需要硬度和韧性平衡的用途。当前第1页12