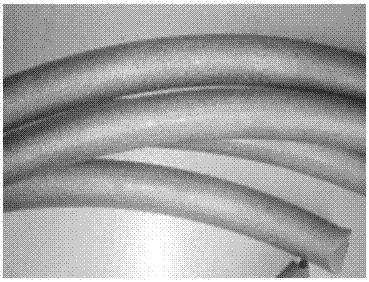
本发明属于冶金
技术领域:
,具体涉及一种0cr17连铸坯及其生产方法。
背景技术:
:0cr17因耐蚀性较好,加工成零部件表面光亮,广泛应用于家电、汽车等行业。目前国内生产0cr17不锈钢线材的企业较多,线材轧制用铸坯为连铸坯,因该钢种传热性能较差凝固过程温降梯度大,细化晶粒元素含量低,这导致其细小等轴晶层薄且柱状晶发达,因此易在铸坯表面、皮下产生裂纹遗传至轧制工序,使线材产生裂纹,在铸坯冷却过程中因晶粒粗大,会因热应力产生裂纹甚至引起连铸坯断裂。连铸坯角部虽然存在圆角,但受连铸机结晶器铜管加工限制及铸坯冷却因素影响,铸坯圆角半径尺寸几乎不受控,这导致大量铸坯圆角半径较小,较小的铸坯圆角半径,在轧制时因角部轧制变形过大及温降偏大塑性下降,使线材表面均不同程度的出现通条折叠、裂纹,导致后续冷镦开裂。若通过结晶器铜管设计增大铸坯圆角半径,不仅影响结晶器铜管通钢量,更易导致连铸机漏钢事故。本发明从连铸机结晶器流量、二冷流量、结晶器电磁搅拌参数设计,连铸坯缓冷,铸坯角部修磨倒角参数计算设计,使送轧钢的连铸坯表面合格率达99%以上,确保消除了连铸坯表面、皮下裂纹,并通过修角减少角部轧制展宽变形、降低角部温降,消除0cr17线材折叠、裂纹,盘条表面检验合格率达到95%以上。技术实现要素:本发明要解决的技术问题是提供一种0cr17连铸坯;本发明还提供了一种0cr17连铸坯的生产方法。为解决上述技术问题,本发明所采取的技术方案是:一种0cr17连铸坯,所述连铸坯化学成分组成及质量百分含量为:c:0.04-0.06%,si:0.25-0.45%,mn:0.40-0.55%,p≤0.035%,s≤0.030%,cr:16.50-16.75%,ni≤0.60%,余量为fe和不可避免的杂质。本发明还提供一种0cr17连铸坯的生产方法,所述方法包括连铸机结晶器水流量、二冷水流量、结晶器电磁搅拌参数控制及连铸坯缓冷、铸坯角部修磨倒角平面宽度控制。本发明所述连铸机结晶器水流量控制为1450-1550l/min。本发明所述二冷水流量控制,连铸机工作拉速为1.1m/min;1区水流量为45.8-46.2l/min,2区水流量为36.8-37.2l/min,3区水流量为19.8-20.2l/min。二冷水流量与拉速关系,下表用于连铸机非稳态浇铸及微机控制计算:连铸机拉速(m/min)≤1.01.11.31.51.61.71区水流量(l/min)3846546568722区水流量(l/min)3037434952553区水流量(l/min)162023272931本发明所述结晶器(结晶器铜管壁厚12mm)电磁搅拌参数控制,电流370a、频率4hz。本发明所述连铸坯缓冷控制,连铸坯切割完毕经固定集坯床直接进缓冷坑盖盖缓冷,连铸坯表面温度≤300℃出坑。本发明所述铸坯角部修磨倒角平面宽度控制为:8.5-22mm。铸坯角部修磨倒角平面尺寸最大值≤2*(2*细小等轴晶层厚度2)1/2=2*(2*8*8)1/2,计算结果为≤22mm。本发明所述方法适用于150mm*150mm断面的0cr17连铸坯。本发明所述方法生产的送轧钢连铸坯表面合格率在99%以上,盘条一检合格率99%以上,酸洗二次检验合格率在95%以上本发明方法采用的原理是:0cr17为铁素体不锈钢,碳含量低,铬含量高,传热较差,钢水凝固、冷却过程温降梯度大,易产生较大热应力,当热应力超过晶界结合强度时会产生裂纹,连铸坯的表面、皮下裂纹源于结晶器内,在后续冷却过程进一步扩展,该裂纹会遗传至轧制工序导致线材表面裂纹。本发明通过控制连铸坯凝固、冷却过程传热,降低热应力来解决以上问题。通过结晶器水流量设计实现结晶器弱冷避免裂纹产生;二冷水流量参数设计、连铸坯缓冷可适当降低连铸坯表面温降,从而降低凝固、冷却过程连铸坯内外温度梯度进而降低热应力。以上综合作用不仅可以降低、消除连铸坯表面、皮下裂纹,还可增大连铸坯等轴晶区,从而改善线材裂纹。连铸坯角部在轧制过程中宽展变形高于其他部位,易在轧槽边缘形成折叠,且连铸坯角部在轧制过程中为二维传热,轧制过程中热损失大、温降高,使塑性下降,从而形成裂纹。连铸坯在生产中角部虽有一定圆角半径可以克服以上问题,但受连铸机结晶器铜管加工限制及连铸坯冷却因素影响,铸坯圆角半径尺寸几乎不受控,这导致大量铸坯圆角半径较小,因此需要通过对铸坯角部修磨满足轧制要求。本发明对连铸坯角部修磨倒角平面最小尺寸设计,可以减少连铸坯角部轧制过程中宽展变形量,并降低连铸坯轧制过程中温降,增加角部塑性,同时对连铸坯角部修磨倒角平面最大尺寸进行设计计算,避免粗大晶粒裸露,粗大晶粒裸露不仅使铸坯塑性降低,而且会导致铸坯轧制加热时晶界氧化,使线材表面出现裂纹。本发明通过连铸机结晶器水流量、二冷水流量、结晶器电磁搅拌参数控制,连铸坯缓冷、铸坯角部修磨倒角平面宽度控制,消除了0cr17连铸坯裂纹,提高了连铸坯送轧钢合格率,降低了线材裂纹。本发明0cr17盘条的产品标准参考:《不锈钢盘条》gb/t4356-2002。采用上述技术方案所产生的有益效果在于:1、本发明通过连铸机结晶器流量、二冷流量、结晶器电磁搅拌参数控制,连铸坯缓冷、铸坯角部修磨倒角平面宽度控制,使送轧钢连铸坯表面合格率在99%以上,确保消除了连铸坯表面、皮下裂纹。2、本发明通过修角减少角部轧制展宽变形、降低角部温降,消除0cr17线材折叠、裂纹,盘条一检合格率99%以上,酸洗二次检验合格率在95%以上。附图说明图1为实施例1的0cr17铸坯低倍表面质量图;图2为实施例1酸洗后的0cr17线材试样图;图3为实施例1酸洗后整包的0cr17线材图;图4为对比例1的0cr17铸坯低倍表面质量图;图5为对比例1酸洗后的0cr17线材试样图。具体实施方式下面结合具体实施例对本发明作进一步详细的说明。实施例1本实施例0cr17连铸坯化学成分组成及其质量百分含量为:c:0.043%,mn:0.50%,si:0.36%,p:0.018%,s:0.002%,cr:16.71%,ni:0.07%,其余为铁和不可避免的杂质元素。本实施例0cr17连铸坯生产方法包括连铸机结晶器水流量、二冷水流量、结晶器电磁搅拌参数控制及连铸坯缓冷、铸坯角部修磨倒角平面宽度控制,具体工艺步骤如下所述:(1)结晶器水流量:1480l/min;(2)二冷水流量(l/min):1区:45.8l/min;2区:36.8l/min;3区:20l/min;拉速1.1m/min;(3)结晶器电磁搅拌参数:电流370a、频率:4hz;(4)连铸坯出坑温度:265℃;(5)铸坯角部修磨倒角平面宽度9mm。按本实施例工艺生产送轧钢连铸坯合格率100%,铸坯低倍表面质量见图1;轧制的φ5.5mm规格的0cr17盘条,一检合格率99.8%;酸洗后表面质量良好,无折叠及目视可见裂纹,酸洗后二检合格率98.5%,酸洗后的0cr17线材试样见图2,酸洗后整包的0cr17线材见图3。(其他实施例附图与本实施例相似,故省略。)实施例2本实施例0cr17连铸坯化学成分组成及其质量百分含量为:c:0.044%,mn:0.50%,si:0.36%,p:0.016%,s:0.002%,cr:16.71%,ni:0.07%,其余为铁和不可避免的杂质元素。。(1)结晶器水流量:1547l/min;(2)二冷水流量(l/min):1区:46.1l/min;2区:37.1l/min;3区:19.8l/min;拉速1.1m/min;(3)结晶器电磁搅拌参数:电流370a、频率:4hz;(4)连铸坯出坑温度:283℃;(5)铸坯角部修磨倒角平面宽度15mm。按本实施例工艺生产送轧钢连铸坯合格率100%,轧制的φ5.5mm规格的0cr17盘条,一检合格率99.2%;酸洗后表面质量良好,无折叠及目视可见裂纹,酸洗后二检合格率98.3%。实施例3本实施例0cr17连铸坯化学成分组成及其质量百分含量为:c:0.049%,mn:0.53%,si:0.39%,p:0.017%,s:0.002%,cr:16.68%,ni:0.07%,其余为铁和不可避免的杂质元素。(1)结晶器水流量:1500l/min;(2)二冷水流量(l/min):1区:46l/min;2区:37l/min;3区:20.1l/min;拉速1.1m/min;(3)结晶器电磁搅拌参数:电流370a、频率:4hz;(4)连铸坯出坑温度:300℃;(5)铸坯角部修磨倒角平面宽度19mm。按本实施例工艺生产送轧钢连铸坯合格率99.3%,轧制的φ6.5mm规格的0cr17盘条,一检合格率99.1%;酸洗后表面质量良好,无折叠及目视可见裂纹,酸洗后二检合格率97.5%。实施例4本实施例0cr17连铸坯化学成分组成及其质量百分含量为:c:0.044%,mn:0.46%,si:0.36%,p:0.016%,s:0.002%,cr:16.71%,ni:0.07%,其余为铁和不可避免的杂质元素。(1)结晶器水流量:1455l/min;(2)二冷水流量(l/min):1区:46.1l/min;2区:37.2l/min;3区:19.9l/min;拉速1.1m/min;(3)结晶器电磁搅拌参数:电流370a、频率:4hz;(4)连铸坯出坑温度:247℃;(5)铸坯角部修磨倒角平面宽度20mm。按本发明工艺生产送轧钢连铸坯合格率99%,轧制的φ6.5mm规格的0cr17盘条,酸洗后表面质量良好,一检合格率99%;无折叠及目视可见裂纹,酸洗后二检合格率96.6%。实施例5本实施例0cr17连铸坯化学成分组成及其质量百分含量为:c:0.060%,mn:0.55%,si:0.45%,p:0.028%,s:0.030%,cr:16.75%,ni:0.35%,其余为铁和不可避免的杂质元素。(1)结晶器水流量:1550l/min;(2)二冷水流量(l/min):1区:46.2l/min;2区:36.9l/min;3区:20.2l/min;拉速1.1m/min;(3)结晶器电磁搅拌参数:电流370a、频率:4hz;(4)连铸坯出坑温度:285℃;(5)铸坯角部修磨倒角平面宽度22mm。按本发明工艺生产送轧钢连铸坯合格率99.4%,轧制的φ6.0mm规格的0cr17盘条,一检合格率99.1%;酸洗后表面质量良好,无折叠及目视可见裂纹,酸洗后二检合格率95.9%。实施例6本实施例0cr17连铸坯化学成分组成及其质量百分含量为:c:0.040%,mn:0.40%,si:0.25%,p:0.035%,s:0.010%,cr:16.50%,ni:0.60%,其余为铁和不可避免的杂质元素。(1)结晶器水流量:1450l/min;(2)二冷水流量(l/min):1区:45.9l/min;2区:37.1l/min;3区:20.0l/min;拉速1.1m/min;(3)结晶器电磁搅拌参数:电流370a、频率:4hz;(4)连铸坯出坑温度:276℃;(5)铸坯角部修磨倒角平面宽度8.5mm。按本发明工艺生产送轧钢连铸坯合格率99.5%,轧制的φ6.5mm规格的0cr17盘条,一检合格率99.2%;酸洗后表面质量良好,无折叠及目视可见裂纹酸洗后二检合格率97.2%。对比例1本对比例提供常规的0cr17连铸坯生产工艺。0cr17连铸坯化学成分组成及其质量百分含量为:c:0.055%,mn:0.45%,si:0.35%,p:0.025%,s:0.008%,cr:16.65%,ni:0.09%,其余为铁和不可避免的杂质元素。(1)结晶器水流量:1710l/min;(2)二冷水流量(l/min):1区:65l/min;2区:50l/min;3区:30l/min;拉速1.4m/min;(3)结晶器电磁搅拌参数:电流280a、频率:5hz;(4)连铸坯出坑温度:无缓冷;(5)铸坯角部修磨倒角平面宽度:不倒角。按本发明工艺生产送轧钢连铸坯合格率80%,铸坯圆角半径5mm,等轴晶率10%,铸坯存在表面裂纹、皮下裂纹,铸坯低倍表面质量见图4;轧制的φ5.5mm规格的0cr17盘条,一检合格率80%;酸洗后表面质量存在裂纹,目视可见裂纹,酸洗后二检合格率75%,酸洗后的0cr17线材试样见图5。通过图1、4和图2、5对比,可以看出:采用本发明后铸坯等轴晶率由10%提高至30%以上,铸坯表面裂纹、皮下裂纹消失,通过角部倒角使角部尖锐现象消失,可有效减少轧制过程铸坯角部热量损失及展宽变形,消除了线材裂纹及折叠。以上实施例仅用以说明而非限制本发明的技术方案,尽管参照上述实施例对本发明进行了详细说明,本领域的普通技术人员应当理解:依然可以对本发明进行修改或者等同替换,而不脱离本发明的精神和范围的任何修改或局部替换,其均应涵盖在本发明的权利要求范围当中。当前第1页12