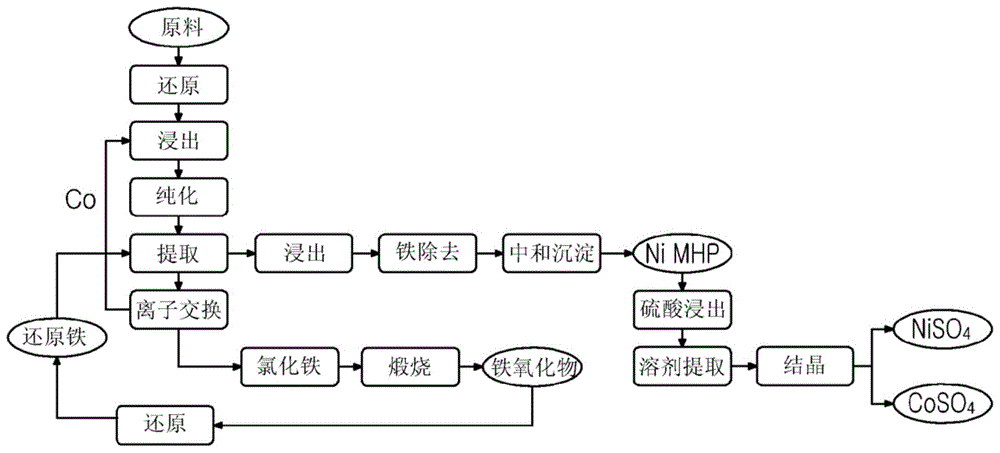
本公开内容涉及从含有镍、铁和钴的原料中回收镍和钴的方法。
背景技术:
:作为含镍和铁的矿石,提供了红土矿,镍氧化物矿石,并且根据矿物相其可以分类为褐铁矿、腐泥土等。由于这些矿石具有钝态特性并且具有高的耐酸性,因此对酸的溶解反应缓慢。因此,作为用于有效浸出镍的方法,已经提出了通过在高温和高压下溶解于在高压釜中的酸中来回收镍的方法,称为“高压酸浸出(hpal)法”。当在室温下进行镍浸出反应时,即使在浸出持续数月或更长时间之后,镍回收率也不超过约85%。然而,作为镍氧化物矿石湿法冶炼的代表性方法,当使用hpal法时,可以在2小时内浸出90%或更多的镍。作为用于通过hpal法回收镍的技术的实例,可以提供专利文献1和2。然而,已知hpal法应在高压釜中在高温和高压下进行,并且由于强酸性而主要与钛材料一起使用,因此,设备成本非常高并且维护成本高。此外,由于需要使用苛性钠、昂贵的沉淀剂、或环境有害的沉淀剂例如h2s来浓缩镍,因此可能存在用于防治污染的设备成本增加的问题。此外,当通过应用以上方法对褐铁矿镍矿石进行浸出时,可以进行高速浸出,但是由于褐铁矿矿石具有高的铁含量和低的镍含量,因此当通过酸溶解浸出镍时,相对大量的铁可以被浸出,而少量的镍可以被浸出,使得难以从浸出的材料中分离铁和镍。作为减少以上问题的技术,存在专利文献3、4和5等中公开的技术。专利文献3和4公开了通过从具有低品质的镍的矿石中分离和回收镍和铁来有效地浓缩镍并从这样的浓缩物中回收镍铁的方法。专利文献5公开了通过还原作为过程副产物获得的煅烧铁矿石,然后用作用于沉淀的浆料来提高在沉淀之后的镍浓缩物的镍含量的方法。然而,即使在上述方法的情况下,在沉淀经还原的原料中,除了镍和铁之外还含有大量的杂质例如mg和si,并且当在沉淀之后回收镍铁时产生大量的副产物例如炉渣等。此外,即使在沉淀之后,铁的含量也高于镍的含量并且可以用作镍铁,但是其不适用于生产具有高含量镍的高纯度镍。[现有技术文献][专利文献](专利文献1)韩国专利特许公开第10-2007-7020915号(专利文献2)日本专利特许公开第2010-031341号(专利文献3)韩国专利第10-1353721号(专利文献4)韩国专利第10-1359179号(专利文献5)韩国专利第10-1657810号技术实现要素:技术问题本公开内容的一个方面是提供用于从含有镍、铁和钴的原料中有效回收镍和钴的方法。技术方案根据本公开内容的一个方面,用于回收镍和钴的方法包括:用含有氢的还原气体还原含有镍、铁和钴的原料;向经还原的原料中添加酸,并用酸对原料进行浸出,以获得含有镍离子、铁离子和钴离子的溶液;向溶液中添加含铁或镁的氢氧化物以产生杂质已经被除去的提纯溶液;通过向含有镍离子和钴离子的提纯溶液中添加用于沉淀的还原铁来沉淀镍和钴;向在沉淀中获得的沉淀物中添加酸以进行浸出,以获得含有镍离子、铁离子和钴离子的溶液;向含有镍离子、钴离子和铁离子的溶液中添加碱性试剂并用含氧气体氧化所述溶液以除去铁;以及向溶液中添加碱性试剂以获得镍和钴的氢氧化物。根据以下关系表达式,用于沉淀的还原铁的量可以为存在的镍离子和钴离子的摩尔总和的1.5倍至2.5倍。[关系表达式1]还原铁的量(晶种比率)=(用于沉淀的还原铁中金属fe的含量)/(浸出溶液中ni+co离子的含量)用于沉淀的还原铁可以通过用固体碳或还原气体间接还原由镍冶炼过程的副产物获得的氯化铁煅烧铁矿石来获得。用于沉淀的还原铁的还原率可以为80%至99%。用于沉淀的还原铁的颗粒尺寸可以为5μm或更小。当用还原气体还原氯化铁煅烧铁矿石时,还原温度可以为500℃至950℃。当用还原气体还原氯化铁煅烧铁矿石时,还原温度可以为500℃至950℃。氯化铁煅烧铁矿石的形成可以包括:蒸发和浓缩在镍冶炼过程中作为滤液产生的含铁离子和氯离子的溶液以获得浓缩溶液;使浓缩溶液结晶以获得氯化铁晶体;将氯化铁晶体和浆料固液分离;以及煅烧氯化铁晶体以获得氯化铁煅烧铁矿石。含铁离子和氯离子的溶液可以是在镍冶炼过程中产生的滤液,镍冶炼过程包括:将含有镍和铁的镍矿石溶解在盐酸中以获得镍离子和铁离子被浸出的浸出溶液;通过向浸出溶液中添加碱性试剂来调节ph,并通过固液分离从浸出溶液中除去固体杂质;向浸出溶液中添加含有镍和铁的镍矿石,然后使镍作为镍铁沉淀;以及通过固液分离过滤和回收固体沉淀物。添加到经还原的原料中的酸可以包括通过用离子交换树脂处理在沉淀之后过滤的后过滤液体以回收剩余的镍和钴并用酸除去离子交换树脂而获得的含镍和钴的酸。通过离子交换树脂获得的含镍和钴的酸可以被重新引入浸出过程中。碱性试剂可以为选自氢氧化钙和碳酸钙中的一者或更多者。可以用硫酸对镍和钴的氢氧化物进行浸出并使其经历溶剂提取,以产生硫酸镍和硫酸钴。在通过添加碱性试剂获得镍和钴的氢氧化物时,浸出溶液中的氯组分和钙组分可以以氯化钙的形式除去。可以添加h2s代替碱性试剂。有益效果根据本公开内容的一个实施方案,可以从含有镍、铁和钴的原料中回收有价值的金属,例如高浓度的镍和钴。详细地,本公开内容中的一个实施方案可以更适合应用于这样的情况:其中镍浓度相对低而铁浓度相对高,并因此当浸出镍时,大量的铁被浸出,而少量的镍被浸出,难以将铁和镍彼此分离。附图说明图1为举例说明根据本公开内容的一个实施方案的镍和钴回收方法的示意性流程图。具体实施方式在下文中,将参照多个实施方案描述本公开内容的优选实施方案。然而,本公开内容的实施方案可以被修改为多种其他形式,并且本公开内容的范围不限于下述实施方案。根据本公开内容中的一个实施方案,提供了用于由含有镍、铁和钴的原料生产高浓度的镍浓缩物的方法。用于回收镍和钴的方法包括:用含有氢的还原气体还原含有镍、铁和钴的原料;向经还原的原料中添加酸,并用酸对原料进行浸出,以获得含有镍离子、铁离子和钴离子的溶液;向溶液中添加含铁或镁的氢氧化物以产生杂质已经被除去的提纯溶液;通过向含有镍离子和钴离子的提纯溶液中添加用于沉淀的还原铁来沉淀镍和钴;向在沉淀中获得的沉淀物中添加酸并进行浸出以获得含有镍离子、铁离子和钴离子的溶液;向含有镍离子、钴离子和铁离子的溶液中添加碱性试剂并用含氧气体氧化所述溶液以除去铁;以及向溶液中添加碱性试剂以获得镍和钴的氢氧化物。本公开内容可以应用的含有镍-铁的原料没有特别限制,并且可以使用任何含有镍和铁的原料,只要其含有镍和铁即可,并且详细地,可以使用镍矿石,例如褐铁矿或腐泥土。镍矿石具有含量为1%至2.5%的ni和15%至55%的fe,尽管其含量根据矿石的类型而变化。在褐铁矿矿石的情况下,镍浓度低至1%至1.8%,铁浓度高至30%至55%。本公开内容的一个实施方案也可以有效应用于从这样的含有相对低的镍的褐铁矿中回收镍。在下文中,将详细描述根据本公开内容的一个实施方案的由含有镍、铁和钴的原料生产镍浓缩物的方法。预处理含有镍、铁和钴的原料在从含有镍、铁和钴的原料中回收镍时,如果需要的话,可以进行预处理过程以在还原过程中有效地还原含有镍、铁和钴的原料。该预处理过程包括干燥、研磨和焙烧。含有镍、铁和钴的原料通常含有约20%至40%的附着水和约10%的结晶水。在含有这样的附着水的情况下,研磨效率降低,以及在焙烧含有镍-铁的原料之后进行研磨的情况下,担心由于高温而可能对粉碎设备造成负担。因此,在将原料研磨成细颗粒之前,可以对含有镍-铁的原料进行干燥,并且干燥没有特别限制,只要附着水可以蒸发即可。例如,干燥可以在100℃至200℃的温度范围内进行。在其中在干燥之后粉碎含有镍、铁和钴的原料的情况下,颗粒尺寸可以为1mm或更小。1mm或更小的颗粒尺寸可以提高还原和浸出效率。颗粒尺寸的下限没有特别限制,但是为了粉碎过程的效率可以为10μm或更大。另一方面,在干燥过程中可能没有除去结晶水,导致还原反应中的反应效率降低。因此,可以通过焙烧处理除去结晶水。根据矿石的类型,焙烧处理可以在250℃至850℃的温度范围内进行。用含有氢的还原气体还原含有镍、铁和钴的原料将含有镍、铁和钴的原料还原以获得经还原的含有镍、铁和钴的原料。还原可以使用含有氢作为还原剂的还原气体在550℃至950℃的温度范围内进行。在还原温度低于550℃的情况下,由于还原不充分并且在随后浸出时的回收率降低,因此沉淀效率也可能降低。随着还原温度升高,浸出产率和沉淀效率可以增加。然而,如果还原温度高于950℃,则还原效率不会增加,并且可加工性由于颗粒间烧结而可能降低。作为还原气体,可以使用含有氢的气体。存在使用co气体代替氢的情况,但是在这种情况下,需要在1000℃或更高的高温下进行还原,并且此外,在高温下还原的粉末的活性可能降低,并且浸出速率可能降低,并且此外,沉淀效率可能降低。作为还原气体,可以使用含有氢的气体,并且氢也可以单独使用或与惰性气体组合使用。惰性气体的实例包括氦气、氩气、二氧化碳、氮气等。含有氢的还原气体的另外的实例包括在铁矿石冶炼过程中产生的含有50%或更多的氢的焦炉煤气(cog)、或者在甲烷氢重整反应中产生的气体、含有65%或更多的氢的含有氢的lng重整气体。还原气体中含有的氢与含有镍、铁和钴的原料中的以氧化态存在的镍和铁的氧反应以产生水,从而进行还原。作为一个实例,在使用褐铁矿矿石的情况下的理论还原反应示于下式1中。(ni0.1fe0.9)ofe2o3+4h2=(ni0.1fe0.9)+2fe+4h2o……式1还原气体中含有的氢的量可以增加超过理论当量比以获得有效的还原反应。在这种情况下,考虑到过程成本的增加,理论当量比的摩尔比可以为1至5倍、2至5倍、2至4倍等。可以获得通过上述反应还原的含有镍、铁和钴的原料,并且可以回收引入的氢中未参与反应的氢并且将其重新引入过程中。向经还原的原料中添加酸,然后进行浸出,以获得含有镍离子、铁离子和钴离子的溶液根据本公开内容中的一个实施方案,将经还原的原料浆化,然后向浆料中添加酸以溶解和浸出浆料的经还原的原料中含有的镍、铁和钴,使得镍离子化为镍离子,铁离子化为铁离子,并且钴离子化为钴离子。浸出酸可以为盐酸、硫酸等。此外,酸可以通过以下过程获得:用离子交换树脂处理在稍后描述的沉淀之后过滤的后过滤液体以回收剩余的镍和钴,然后用酸除去树脂以获得混合有含镍和钴的酸和浸出酸的酸。离子交换树脂通常可以为双吡啶甲基胺树脂,或者作为离子交换树脂,可以使用能够选择性地吸附镍和钴的树脂。如上所述,将含镍和钴的酸与浸出酸混合以溶解镍和铁钴,从而进一步回收在沉淀操作中没有沉淀而被过滤的镍和钴。通常,当用酸对通过上式1的还原反应还原的经还原的原料进行浸出时,经还原的原料中的镍铁通过下式2和3所示的反应被酸溶解,并且作为镍铁离子浸出。(ni0.1fe0.9)+2fe+6hcl=(ni0.1fe0.9)cl2+2fecl2+3h2...式2(ni0.1fe0.9)+2fe+3h2so4=(ni0.1fe0.9)so4+2feso4+3h2...式3当使用盐酸作为酸以将这样的经还原的原料浸出到酸中时,如从上式2可以看出,应以(fe+ni)的摩尔数的两倍或更多的摩尔数添加盐酸。然而,如果以超过(fe+ni)的摩尔数的4倍的量添加盐酸,则可能无法获得浸出效率的进一步提高,因此,可以以(fe+ni)的摩尔数的2倍至4倍的摩尔量添加盐酸。另一方面,在使用硫酸作为酸的情况下,如从上式3可以看出,可以以含有镍铁的原料的(fe+ni)的摩尔数的不小于1倍且不大于两倍的摩尔数添加硫酸。向溶液中添加含铁或镁的氢氧化物以产生杂质已经被除去的提纯溶液另一方面,含有镍、钴和铁的原料中含有的氧化物例如al2o3、sio2、cr2o3等几乎不会被酸溶解并且可以作为固相剩余物保留下来,但其中一些可能被酸溶解并被洗脱到浸出溶液中。洗脱的al、si、cr等是在随后的沉淀操作中可能劣化沉淀能力以及镍、钴和铁沉淀物的品质的元素,因此可以在沉淀操作之前除去。溶解在上述浸出溶液中的元素例如al、si和cr可以通过经由向浸出溶液中添加碱性试剂来改变浸出溶液的ph而作为固体氢氧化物被沉淀并除去。在这种情况下,添加用于控制浸出溶液的ph的碱性试剂没有特别限制并且可以没有限制地使用,只要可以增加浸出溶液的ph即可。例如,可以单独使用或组合使用诸如ca、mg、fe和ni的金属的氢氧化物以及诸如cao和mgo的氧化物。添加到浸出溶液中的碱性试剂的量没有特别限制,但是可以以其中浸出溶液的ph可以被调节至1.5至3.5的范围的量添加。浸出溶液的ph通常为1或更小,并且其酸度由于添加的酸而相对高。当将ph调节至以上范围内时,溶液中的杂质例如al、si、cr等作为氢氧化物有效地沉淀。然而,如果在添加碱性试剂时ph大于3.5,则溶液中的镍、钴和铁作为氢氧化物沉淀,因此,其回收率可能降低。待添加用于控制浸出溶液的ph的碱性试剂没有特别限制,并且可以没有限制地使用,只要可以增加浸出溶液的ph即可。例如,可以单独使用或组合使用诸如ca、mg、fe和ni的金属的氢氧化物以及诸如cao和mgo的氧化物。如上所述沉淀的固体剩余物可以通过过滤容易地分离,并且可以通过固液分离器(例如压滤机或滗析器)分离以获得含有镍离子、钴离子和铁离子的浸出溶液。通过向含有镍离子和钴离子的提纯溶液中添加用于沉淀的还原铁来沉淀镍和钴浓缩的镍离子、铁离子和钴离子作为镍浓缩物沉淀。在本公开内容的一个实施方案中,当作为镍浓缩物沉淀时,使用通过固体碳或还原气体间接还原的还原铁作为用于沉淀的晶种材料,并且可以为粉末形式。当向含有镍离子、铁离子和钴离子的溶液(浸出溶液)中添加用于沉淀的还原铁时,通过由下式4或5表示的反应,溶解的镍离子和铁离子的镍被用于沉淀的煅烧还原铁的铁取代而产生镍浓缩物金属。(fecl2+nicl2+cocl2)+3fe=fenico+3fecl2...式4(feso4+niso4+coso4)+3fe=fenico+3feso4...式5如上式中的取代反应的原理基于铁、镍和钴之间的自然电位差。例如,在含铁离子和镍离子的溶液中通过镍与用于沉淀的铁粉末的铁之间的自然电位差形成电池,并且在阳极位点处,通过铁的氧化进行溶解反应,并且在阴极位点处,进行其中含铁离子和镍离子的溶液中的镍离子被还原并沉淀的反应。通过诸如钴和铁的机理进行反应,并且进行钴离子被还原并沉淀的反应。用于沉淀的还原铁需要非常高的活性以实现镍的有效沉淀。具有这样高活性的还原铁可以通过在700℃至900℃下用氢还原在该过程中通过煅烧氯化铁晶体获得的铁氧化物来获得。更详细地,用于沉淀的还原铁可以通过用固体碳或还原气体直接还原由镍冶炼过程的副产物获得的氯化铁煅烧铁矿石来获得。氯化铁煅烧铁矿石可以由在使用盐酸溶液从含有镍和铁的镍矿石中回收镍的镍冶炼过程中作为滤液产生的含铁离子和氯离子的溶液获得。用于获得在本公开内容的一个实施方案中使用的氯化铁煅烧铁矿石的过程的一个实例如下。通过蒸发和浓缩在使用盐酸溶液从含有镍和铁的镍矿石中回收镍的镍冶炼过程中作为滤液产生的含铁离子和氯离子的溶液获得浓缩溶液。然后,通过使浓缩溶液结晶获得氯化铁晶体。随后,使氯化铁晶体和浆料经历固液分离。煅烧氯化铁晶体,从而获得氯化铁煅烧铁矿石。含铁离子和氯离子的溶液可以通过以下过程获得。例如,含铁离子和氯离子的溶液可以是在镍冶炼过程中产生的滤液,镍冶炼过程包括:用盐酸溶解含有镍和铁的镍矿石以获得其中镍离子和铁离子被浸出的浸出溶液的浸出操作;通过向浸出溶液中添加碱性试剂来调节ph并通过固液分离从浸出溶液中除去固相杂质的ph调节操作;向浸出溶液中添加含有镍和铁的镍矿石,然后使镍作为镍铁沉淀;以及通过固液分离从浸出溶液中过滤和回收固相沉淀物的沉淀物回收操作。另一方面,当使用还原气体还原氯化铁煅烧铁矿石时,还原温度可以为500℃至950℃。如果还原温度低于500℃,则存在速度方面的问题,其中作为煅烧铁矿石的fe氧化物的fe2o3在不通过作为还原中间相的feo的情况下从fe3o4还原成fe,导致相对长的还原时间。如果还原温度高于950℃(这对于发生还原而言是过高的温度),则还原fe被烧结或者能量被过度消耗,从经济效率的观点来看这可能是有问题的。作为还原气体,可以使用氢、co、其混合气体、或含有氢和co中至少一者的气体。例如,还原气体可以为100%的氢、或100%的co、或氢和co的混合气体、或氢+co+lng重整气体、或诸如cog的混合气体等。当使用固体碳作为还原剂还原氯化铁煅烧铁矿石时,还原温度可以为700℃至1200℃。如果还原温度低于700℃,则存在还原花费长时间的问题。如果还原温度高于1200℃,则还原fe被烧结或者能量被过度消耗,这在经济效率方面可能是有问题的。作为固体碳,可以使用煤、焦炭等。除了fe和ni之外,用于沉淀的还原铁还可以以总含量的5重量%或更少,详细地3重量%或更少含有诸如mg、si、al等的元素。例如,用于沉淀的煅烧还原铁可以以总含量的58重量%至72重量%含有fe,以1重量%或更少含有ni,以5重量%或更少、详细地3重量%或更少含有mg、si和al,以及剩余部分的氧和其他杂质。另一方面,用于沉淀的煅烧还原铁的还原率可以为80%至99%。如果还原率小于80%,则在沉淀操作中容易确保97%或更大的ni沉淀率,但是由于用于沉淀的煅烧还原铁中的杂质(例如未还原的氧等)的含量高,因此在沉淀之后的ni浓缩物的ni含量低,并因此存在后续过程的成本增加的缺点。当还原率超过99%时,杂质的量低,但是存在这样的缺点:由于在还原之后由用于沉淀的煅烧还原铁中的金属fe烧结而导致的颗粒尺寸增加,使得沉淀速率降低。另外,就考虑额外的还原成本而言,大于95%的高还原率可能是不利的。用于沉淀的煅烧还原铁的平均颗粒尺寸可以为5μm或更小。限制用于沉淀的煅烧还原铁的颗粒尺寸的原因是为了在沉淀过程期间在溶液中增加使用于沉淀的煅烧还原铁中的金属fe和浸出溶液中的ni离子顺利反应的比表面积。颗粒尺寸可以通过一般的干式/湿式研磨法来控制。除了由氯化铁晶体获得的铁氧化物之外,在还原之后具有高比表面积和高活性的铁氧化物或还原铁也可以应用于本公开内容中的一个实施方案。可以根据用于浸出的经还原的原料的量来控制用于还原镍和钴的待添加到含铁离子、镍离子和钴离子的溶液中的用于沉淀的还原铁的量。作为确定镍的沉淀回收率和所得最终产物的镍浓度以及铁与镍的比率的因素,这样的铁粉的使用率是非常重要的。在本公开内容的一个实施方案中,用于沉淀的还原铁的量可以根据含铁离子和镍离子的溶液的镍含量而变化。为了满足95%或更大的镍回收率,可以满足由以下关系表达式1限定的以重量%计1.5倍至2.5倍的添加量。添加量(晶种比率)=(用于沉淀的还原铁中的fe含量)/(浸出溶液中的ni+co离子含量)关系表达式1是考虑到待沉淀的溶液中的镍和钴的含量来限定用于沉淀的铁粉末的量的式。在这种情况下,考虑到上述式4和5中的用于沉淀的还原铁中的金属铁与浸出溶液中的镍离子的沉淀反应,可以添加含有浸出溶液中含有的镍和钴含量的1.5倍至2.5倍的金属铁的用于沉淀的还原铁。如果铁的量小于1.5倍,则用于沉淀的铁粉末的量小,使得在沉淀之后镍浓缩物的镍含量变得高至40%或更大。然而,溶液中可能存在未参与沉淀反应的镍离子是高度可能的,这在回收率方面不好。如果铁的量超过2.5倍,则可以获得高至约99%的高镍回收率,但是在沉淀之后镍浓缩物中的镍含量过低,因此,在后续过程中用于附加过程例如铁除去的额外成本将增加。向在沉淀操作中获得的沉淀物中添加酸,然后进行浸出,以获得含有镍离子、钴离子和铁离子的溶液在制备镍、钴和铁沉淀物之后,添加酸以溶解镍、钴和铁沉淀物,然后进行再浸出,以使镍离子化为镍离子,钴离子化为钴离子,并且铁离子化为铁离子。虽然酸浸出操作中使用的酸没有特别限制,但是可以使用盐酸或硫酸。通常,当用酸对通过上式1的还原反应还原的经还原的原料进行浸出时,反应如下式6和7所示地表示,以通过酸溶解镍、钴和铁沉淀物中的镍、钴和铁以分别浸出为镍离子、钴离子和铁离子。(ni,co,fe)+6hcl=(ni,co,fe)cl2++3h2…式6(ni,co,fe)+3h2so4=(ni,co,fe)so4+3h2…式7向在以上操作中获得的含有镍-钴和铁的溶液中添加碱性试剂并用含氧气体氧化所述溶液以除去铁从通过再浸出获得的含有镍、钴和铁的酸浸出溶液中除去铁伴随着以下的氧化和还原反应。例如,在本公开内容的一个实施方案中,氧化沉淀法包括将fe2+离子氧化成fe3+离子的过程和中和fe3+离子以作为固体沉淀物如feooh沉淀的过程,如以下反应式所示。氧化反应:fe2++1/4o2+1/2h2o=fe3++oh-...式8中和反应:fe3++3oh-=feooh+h2o…式9总反应:fe2++1/4o2+2oh-=feooh+1/2h2o...式10氧气的引入不仅可以通过纯氧气来实现,也可以通过引入空气来实现。详细地,氧气可以以每1l浸出溶液0.01l/分钟至0.2l/分钟的速率引入,在引入空气的情况下,空气可以以引入速率的2倍至10倍的速率引入。例如,空气的引入可以以每升浸出溶液0.02l/分钟至2l/分钟的速率进行。当氧气和空气的引入速率小于以上范围时,fe2+离子氧化成fe3+离子的过程可能不充分地进行。当氧气和空气的引入速率超过以上范围时,氧气和空气的消耗量增加,这在成本方面可能是一个缺点。为了氧化fe2+离子,可以使用诸如过氧化氢、naocl等的氧化剂。由于氧化剂具有高的氧化速率,因此可以在短时间内除去fe,但氧化剂的成本昂贵。因此,在其中fe以比ni和co更高的浓度存在于浸出溶液中的情况下,氧化剂相对于ni和co的成本过高。因此,根据本公开内容中的一个实施方案,使用廉价的氧气或空气作为氧化剂,尽管氧化反应速率低于过氧化氢和naocl的氧化反应速率。此外,为了增加诸如氧气和空气的气体与溶液之间的反应效率,应增加气泡的界面面积。为此,可以减小气泡尺寸以增加气泡与溶液之间的界面的面积。根据本公开内容中的一个实施方案,气泡小型化方法没有特别限制,并且例如,可以使用微气泡发生器来进行。根据发生原理,微气泡发生器可以分类为多种类型,例如螺旋液流型、文丘里型、喷射型、加压溶解型等。本公开内容中可以使用其任何类型。酸浸出溶液的温度可以保持在40℃至99℃。如果酸浸出溶液的温度小于40℃,则反应速率降低。如果酸浸出溶液的温度大于99℃,则水蒸发且能量消耗增加。当fe2+离子被氧化成fe3+离子时,可以在比ni2+离子和co2+离子更低的ph区域内以固体形式发生中和沉淀,从而添加能够供应oh-离子的中和剂以以固体形式沉淀fe3+离子。可以将固体粉末形式的中和剂与水混合以以浆料的形式添加,并且在这种情况下,基于中和剂的重量,中和剂可以与按重量计1至10倍的水混合。中和剂可以为基于ca的中和剂、基于mg的中和剂或其混合物。基于ca的中和剂可以为选自石灰石、caco3、cao和ca(oh)2中的至少一者,基于mg的中和剂可以为选自例如菱镁矿、mgco3、mgo和mg(oh)2中的至少一者。通过添加这样的中和剂,fe3+离子以固体形式沉淀。在这种情况下,ni和co可能与fe共沉淀是高度可能的,并且随着溶液的ph增加,共沉淀损失增加。另一方面,如果仅将ph保持在低水平下来显著降低ni和co的损失,则铁除去率降低并且生产率降低。因此,就ni/co损失和生产率而言,在铁除去过程期间将ph保持在合适的范围区域内可以是非常重要的。因此,根据本公开内容中的一个实施方案,在添加中和剂以使氧化的fe3+离子沉淀成固体的操作中,可以将ph保持在2至4的ph。如果ph小于2,则铁除去率降低并且生产率降低。如果ph高于4,则存在ni和co与fe共沉淀的共沉淀损失增加的问题。另一方面,如果中和剂进给速率快于fe2+离子至fe3+离子的氧化反应速率,则供应的oh-离子使溶液的ph增加,使得ni和co的损失增加。另一方面,如果中和剂进给速率慢于氧化反应速率,则溶液的ph降低,但是总的铁除去率降低。因此,通过使fe2+离子至fe3+离子的氧化反应速率和中和剂的添加速率相匹配,可以将溶液的ph保持在适当的范围区域内。为此,在本公开内容的一个实施方案中,可以添加具有与中和剂的含量中的fe相同摩尔量的ca、mg或其混合物。因此,可以确保一定水平的铁除去,同时显著降低ni和co损失。详细地,中和剂可以以每升浸出溶液0.05g/分钟至0.2g/分钟的速率引入。例如,当溶液中的fe浓度为1摩尔时,添加1摩尔的caco3。然而,由于在fe浓度降低的过程的后半段中铁除去率可能显著降低,因此通过使用氧气的氧化沉淀法可以除去大部分的fe,并且可以用具有快速反应的过氧化氢、naocl等除去少量的剩余fe。然而,由于在随后的操作中可以通过诸如溶剂提取等的其他方法除去少量的剩余fe,因此并不总是需要使用过氧化氢、naocl等。向溶液中添加碱性试剂以获得镍和钴的氢氧化物可以将不含铁的含有镍和钴的溶液中的镍和钴制备为固体氢氧化物以用于商业化。通过以与上述除去浸出溶液中的杂质例如al、si、cr等的方法相同的方式改变含有镍和钴的溶液的ph可以使溶解在含有镍和钴的溶液中的镍和钴作为固体氢氧化物沉淀。虽然添加到含有镍和钴的溶液中的碱性试剂没有特别限制,但是碱性试剂可以以使得含有镍和钴的溶液的ph可以被控制到8至10的范围内的程度的量添加。通过在除去铁的同时通过添加碱性试剂作为中和剂,含有镍和钴的溶液的ph通常为2至4。当将ph调节到以上范围内时,溶液中的镍和钴分别作为氢氧化物ni(oh)2和co(oh)2有效地沉淀。当添加碱性试剂时ph为8或更小时,溶液中的镍和钴可能不会作为氢氧化物沉淀并且可能保留在溶液中,使得其回收率可能降低。添加用于控制浸出溶液的ph的碱性试剂没有特别限制并且可以没有限制地使用,只要其可以增加浸出溶液的ph即可。例如,可以单独使用或组合使用诸如ca、mg、fe、ni等的金属的氢氧化物和诸如cao、mgo等的氧化物。固相的经沉淀的镍和钴的氢氧化物容易通过过滤分离并且可以通过固液分离器(例如压滤机或滗析器)进行分离,以获得具有固相的镍和钴的氢氧化物。利用所获得的镍和钴的氢氧化物,根据稍后提供的目标产品,可以通过已知的湿法或还原法等生产各种产品,例如镍和钴金属、镍和钴的硫酸盐、镍和钴的氯化物等。例如,用硫酸对镍和钴的氢氧化物进行浸出以通过已知技术(例如溶剂提取等)清除少量杂质,并且通过蒸发结晶可以产生镍和钴的硫酸盐,例如niso4、coso4等,这可以用作二次电池阳极的原料。此外,可以在600℃或更高的温度下焙烧镍和钴的氢氧化物以分别产生镍和钴的氧化物,例如nio和coo,然后用还原剂(例如氢、一氧化碳或煤)进行还原以分别产生镍和钴金属。在下文中,将更详细地描述本公开内容的实施方案。以下实施方案旨在进一步举例说明本公开内容,而不旨在限制本公开内容。发明实施方式实施方案将具有下表1中示出的组成的褐铁矿矿石在150℃的回转窑中干燥30分钟,然后使用超级磨机进行粉碎以制备平均颗粒尺寸为约15μm的粉末。将获得的粉末在保持在700℃至800℃的焙烧炉中焙烧1小时以从矿石粉末中除去结晶水。将经焙烧的镍矿石从煅烧炉中排出并装入关掉氧气的回转窑还原炉中。然后,使用所制备的矿石粉末中含有的(ni+fe)的摩尔数的2倍的氢,在850℃下将矿石还原以产生经还原的矿石。分析通过这样的还原获得的经还原的矿石的组分并示于下表1中。在表1中,各组分的含量表示重量%,并且其剩余部分为氧和少量的cr、mn等。将如上所述产生的经还原的矿石在填充有氮气的缺氧罐中冷却,并向150g经还原的矿石中添加150ml水以制备浆料。[表1]nifemgsialco干燥矿石1.3344.21.73.92.40.18经还原的矿石1.8561.62.45.43.30.25另一方面,在80℃的温度下和1个大气压下使含铁离子和氯离子的溶液(其为镍冶炼过程的副产物)蒸发和结晶以获得氯化铁晶体,然后使其进行固液分离。然后,在800℃的温度下煅烧氯化铁晶体以制备铁氧化物。铁氧化物的组成示于下表2中。在表3中示出的条件下间接还原具有下表2中所示的组成的铁氧化物以制备用于沉淀的还原铁。如上所述制备的用于沉淀的还原铁的组成示于下表4中。表4还示出了根据相关技术的用于沉淀的还原矿石的组成。在下表2和4中,各组分的含量表示重量%,并且其剩余部分为氧和少量的cu、zn等。[表2]mgcamnfesialpscl铁氧化物0.600.0151.3269.00.012<0.005<0.005<0.0050.068[表3]还原剂类型还原温度(℃)还原时间段用于沉淀的还原铁氢气850℃60分钟[表4]沉淀晶种类型mgcamnfeconisial用于沉淀的还原铁0.810.021.7993.70.100.330.020.01用于沉淀的还原矿石2.350.131.0061.60.291.855.413.33对于如上所述制备的经还原的原料的浆料,向浆料中添加20%浓度的盐酸以制备1升溶液,然后搅拌以进行其中镍离子、钴离子和铁离子从经还原的矿石中浸出的酸浸出反应。将通过浸出反应获得的浸出溶液浓缩以提供具有如下表5所示的多种ni和co组分含量的浸出溶液。为了从制备的浸出溶液中沉淀镍、钴和铁沉淀物,向浸出溶液中添加如上所述制备的用于沉淀的还原铁和用于沉淀的还原矿石以进行镍、钴和铁沉淀物的取代和沉淀反应。用于沉淀的还原铁和用于沉淀的还原矿石的量示于下表5中。在取代和沉淀反应进行2小时之后,分离镍、钴和铁沉淀滤饼和溶液,然后检测滤饼的ni和co含量,并分别检测沉淀率,结果示于表5中。沉淀率通过下式来计算。沉淀率(%)={(浸出溶液的金属含量-在沉淀之后溶液的金属含量)/(浸出溶液的金属含量)}×100[表5]如表5所示,可以看出,在满足本公开内容的条件的实施方案例中,沉淀96%或更多的ni和50%或更多的co。详细地,可以确保含有约20重量%或更多的ni的高浓度沉淀物。另一方面,如表5所示,偏离本公开内容的条件的比较例1和2的ni浓缩物以其量不含有20%的量,并且沉淀率也低,因此,难以如本公开内容中那样确保具有高ni和co含量的沉淀物。使用盐酸对如上所获得的镍、钴和铁沉淀物进行浸出,并使用作为中和剂的caco3和氧气除去铁。如表6所示,浸出过程中的各元素的回收率均为99%或更大,并且随后的铁除去过程中的铁的除去率为99.9%或更大。[表6]分类nicofe沉淀物20.4%1.24%43.2%浸出之后的液体16.0g/l0.90g/l34.8g/l浸出回收率99.9%99.8%99.5%铁除去之后的液体13.0g/l0.68g/l0.033g/l铁除去过程回收率99.0%96.2%0.1%或更小通过向如上所述除去铁获得的镍和钴溶液中添加碱性试剂可以制备镍和钴的氢氧化物。用作中和剂的碱为氢氧化钙。表7示出了镍和钴的氢氧化物二者的回收率为99.99%或更大。[表7]分类nico铁除去之后的液体13.0g/l0.68g/l镍、钴的氢氧化物32.46%1.88%氢氧化物回收率>99.99%>99.99%虽然以上已经举例说明和描述了实施方案,但是对于本领域技术人员明显的是,在不脱离由所附权利要求限定的本公开内容的范围的情况下可以进行修改和变化。当前第1页12