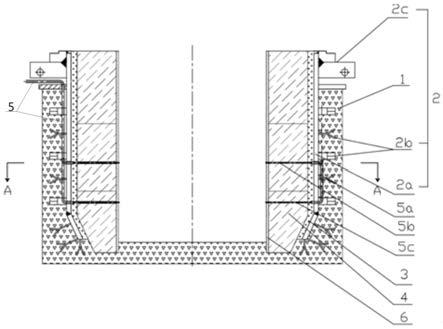
[0001]
本实用新型涉及钢铁炉外精炼领域,尤其是涉及一种浸渍管。
背景技术:[0002]
真空精炼是目前钢铁生产中普遍使用的精炼手段,它可以生产出高纯净度的优质钢种,满足越来越高的使用要求。rh真空精炼法是众多真空精炼设备中精炼速度最快的,它能够与其它冶炼环节协调工作,近年来受到了冶金工作者的普遍重视,得到了大力发展。
[0003]
rh真空精炼法的特征是在真空室下部设有两根与其相通的浸渍管,脱气处理时将浸渍管插入钢液,靠真空室被抽成真空后建立的压差使钢液由环流管进入真空脱气室,同时通过不断向上升浸渍管吹入惰性气体(如氩气、氮气),这些惰性气在钢水的高温和真空室上部低压作用下迅速膨胀,以氩气泡浮力作用为驱动力带动钢液向上运动,钢液到了真空室后由于压力差作用由下降浸渍管流回钢包,冲向钢包底部和包壁,形成真空熔池和钢包间的循环运动,实现钢液脱气、精炼等目的。
[0004]
浸渍管由钢结构、钢壳外部的浇注料、钢壳内部的自流料、工作衬砖四层结构组成,其中埋设有氩气管道。目前,氩气管出口段垂直于浸渍管中轴线,等距环向对置排布,各出口段中心线会交于浸渍管中轴线。精炼时,各氩气管排出的气泡群呈近抛物线的形式向上运动。该设计存在一定的局限性:该氩气管排布设计使得排出的气泡靠浮力和上部真空作用呈近抛物线的形式各自向上运动,搅拌能力相对较弱,钢水洁净化、成分及温度均匀化等耗费时间较长,精炼效率偏低,钢水温降较大;对于浸渍管工作衬砖,因长时间处于高温、炉渣/钢水的侵蚀及冲刷等恶劣环境下,使用寿命偏低。
[0005]
因此,提出一种增进精炼过程中钢液循环流动效率、提高浸渍管耐火内衬使用寿命的浸渍管,是本领域技术人员的基本诉求。
技术实现要素:[0006]
为了克服背景技术中的不足,本实用新型公开了一种浸渍管。
[0007]
为了实现所述发明目的,本实用新型采用如下技术方案:
[0008]
一种浸渍管,包括浸渍管本体,浸渍管本体包括从外向内依次设置的浇注料、钢结构、自流料和工作衬砖,在钢结构、自流料和工作衬砖上穿设有氩气管,氩气管包括主管a、上排氩气管支管b和下排氩气管支管c,上排氩气管支管b设置有多根,分别穿设在浸渍管本体的中部;下排氩气管支管c设置有多根,分别穿设在浸渍管本体的下部,且至浸渍管本体下沿的距离为整只浸渍管本体高度的1/4~1/3,上排氩气管支管b和下排氩气管支管c分别与浸渍管本体的中轴线垂直设置,且等距倾斜分布;
[0009]
钢结构包括钢胆a、锚固件b和法兰c,在自流料和浇注料之间设有钢胆a,钢胆a通过锚固件b与浇注料固定,在钢胆a的外部且位于上边缘处固定有法兰c,在工作衬砖的内表面上设有涂层;
[0010]
主管a包括连通设置的直角管体和环形管,环形管为不封闭环,直角管体的横向管
设置在浇注料的外部,直角管体竖向管的下部和中部分别连通有环形管,竖向管竖直设置在浇注料内,且靠近浇注料的内面设置,两根环形管分别沿钢胆a的圆周方向且位于浇注料内,上排氩气管支管b和下排氩气管支管c的外端分别与中部环形管、下部环形管连通,且上排氩气管支管b和下排氩气管支管c分别穿过自流料、工作衬砖及涂层设置在浸渍管本体内部。
[0011]
所述的浸渍管,上排氩气管支管b与下排氩气管支管c上下交错设置。
[0012]
所述的浸渍管,涂层厚度为0.5~1mm。
[0013]
所述的浸渍管,浇注料的上端口位于钢胆a的上部。
[0014]
由于采用了上述技术方案,本实用新型具有如下有益效果:
[0015]
本实用新型所述的浸渍管,上排氩气管支管b5和下排氩气管支管c5均垂直于浸渍管本体的中轴线且等距分布,上排氩气管支管b5和下排氩气管支管c5的中心线呈等距倾斜分布,精炼时,氩气管排出的氩气泡呈螺旋上升状,而非直线或抛物线上升,这种特点可使钢液形成较强的扰动,加快了气-液、液-液(如钢-渣脱硫)、钢水中的合金熔化及反应,且增加了钢液-氩气间的接触面积,进而提高了两相间的传质速率,精炼效果及生产能力提升,钢水温降小,利于节能降耗;由于氩气管设计为等距倾斜分布而使精炼效率大幅提高,因此在达到相同精炼效果的前提下,工作衬砖处于恶劣环境中的时长相对缩短,有效使用寿命得以提高。
附图说明
[0016]
图1为本实用新型的主视结构示意图;
[0017]
图2为图1 的a-a剖视图;
[0018]
图3为氩气管展开的示意图;
[0019]
图中:1、浇注料;2、钢结构, 2a、钢胆, 2b、锚固件,2c、法兰;3、自流料;4、工作衬砖;5、氩气管, 5a、主管, 5b、上排氩气管支管, 5 c、下排氩气管支管;6、涂层。
具体实施方式
[0020]
通过下面的实施例可以详细的解释本实用新型,公开本实用新型的目的旨在保护本实用新型范围内的一切技术改进。
[0021]
结合附图1-3所述的浸渍管,包括浸渍管本体,浸渍管本体包括从外向内依次设置的浇注料1、钢结构2、自流料3和工作衬砖4,在钢结构2、自流料3和工作衬砖4上穿设有氩气管5,氩气管5包括主管a5、上排氩气管支管b5和下排氩气管支管c5,上排氩气管支管b5设置有多根,分别穿设在浸渍管本体的中部;下排氩气管支管c5设置有多根,分别穿设在浸渍管本体的下部,且至浸渍管本体下沿的距离为整只浸渍管本体高度的1/4~1/3,上排氩气管支管b5和下排氩气管支管c5分别与浸渍管本体的中轴线垂直设置,且等距倾斜分布;
[0022]
钢结构2包括钢胆a2、锚固件b2和法兰2c,在自流料3和浇注料1之间设有钢胆a2,钢胆a2通过锚固件b2与浇注料1固定,在钢胆a2的外部且位于上边缘处固定有法兰2c,在工作衬砖4的内表面上设有涂层6;
[0023]
主管a5包括连通设置的直角管体和环形管,环形管为不封闭环,直角管体的横向管设置在浇注料1的外部,直角管体竖向管的下部和中部分别连通有环形管,竖向管竖直设
置在浇注料1内,且靠近浇注料1的内面设置,两根环形管分别沿钢胆a2的圆周方向且位于浇注料1内,上排氩气管支管b5和下排氩气管支管c5的外端分别与中部环形管、下部环形管连通,且上排氩气管支管b5和下排氩气管支管c5分别穿过自流料3、工作衬砖4及涂层6设置在浸渍管本体内部。
[0024]
所述的浸渍管,上排氩气管支管b5与下排氩气管支管c5上下交错设置。
[0025]
所述的浸渍管,涂层6的各组分按质量百分比包含:中位径粒度为5~10μm的mgo 75-85%、中位径粒度为2~5μm的镁铝尖晶石 8-15%、中位径粒度为10~15μm的al粉3~5%、中位径粒度为2~3μm的活性氧化铝微粉1~3%和中位径粒度为2~10μm的tio
2 1~3%,外加2~3%的粘结剂。
[0026]
所述的浸渍管,所述粘结剂为树脂、镁铝溶胶或铝酸镁中的一种或任意两种的组合。
[0027]
所述的浸渍管,涂层6厚度为0.5~1mm。
[0028]
所述的浸渍管,浇注料1的上端口位于钢胆a2的上部。
[0029]
浸渍管的制作方法,实施例的具体操作步骤如下:
[0030]
(1)制备钢结构2:按照设计要求采用二保焊将锚固件b2、法兰2c焊接在钢胆a2上;
[0031]
(2)工作衬砖上氩气管5成孔:按照设计要求将干燥后的工作衬砖4钻孔;
[0032]
(3)工作衬环砖组装:将磨切处理过的合格工作衬砖4行预组,用胶结剂粘结为一体,并用空压机在环砖外部打2~3环钢带,紧固环砖;
[0033]
(4)含表面涂层6的工作衬环砖的制备:采用湿法喷涂或等离子喷涂的方式在打紧的工作衬环砖4的内表面喷涂涂层6,喷涂后于干燥窑中100~200℃干燥6~18小时;其中,涂层6的各组分按质量百分比包含:中位径粒度为5~10μm的mgo 85份、中位径粒度为2~5μm的镁铝尖晶石 6份、中位径粒度为10~15μm的al粉3份、中位径粒度为2~3μm的活性氧化铝微粉3份和中位径粒度为2~10μm的tio
2 3份,外加2份的粘结剂。
[0034]
(5)工作衬环砖与钢结构2组装:将上述步骤(4)干燥后的工作衬环砖与氩气管5及钢结构2组装并试气,检查氩气管5是否堵塞及气密性是否合格等;
[0035]
(6)模具组装:清理干净的模具,刷脱模油,然后将步骤(5)所述的组装体与模具组装在一起;
[0036]
(7)浇注:将步骤(6)制备好的组装体吊运至振动台,先浇注自流料3,再浇注浇注料1,边震动边浇注;
[0037]
(8)养护及烘烤:将步骤(7)浇注好的浸渍管带模养护10~12小时,脱模养护10~12小时,然后入干燥窑220~280℃烘烤24~48小时,即得成品。
[0038]
本实用新型未详述部分为现有技术。
[0039]
为了公开本实用新型的发明目的而在本文中选用的实施例,当前认为是适宜的,但是,应了解的是,本实用新型旨在包括一切属于本构思和实用新型范围内的实施例的所有变化和改进。