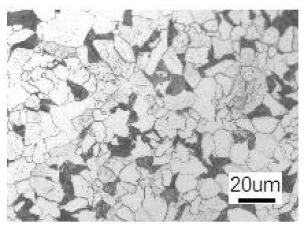
一种80~100mm厚风电用钢板的生产方法
技术领域
1.本发明涉及热轧领域,尤其涉及一种80~100mm厚风电用钢板的生产方法。
背景技术:2.随着我国风电事业的发展,风电的装机容量越来越大,风电塔筒的高度越来越高,用以制作风电塔筒的钢板越来越厚。现在制造风电塔筒的钢板主要以屈服强度355mpa的钢板为主,钢板厚度主要集中在8mm~100mm之间,风力发电设备主要在野外使用,环境温度变化剧烈,因此要求制造风电塔筒的钢板不仅要强度满足要求,还要求具有良好的韧性,尤其是低温韧性。随着钢板厚度增加,轧制时压缩比减小,轧后冷速小,钢板心部与表面温差大,钢板的机械性能控制难度较大。因此风电用厚钢板,尤其是80mm厚以上的钢板一般都采用正火处理来保证钢板性能,而正火处理增加了制造成本,延长交货周期,由于正火后钢板强度下降,还需添加较多的合金,增加了钢板的合金成本。
3.公开号cn 102312156 a的专利“一种60mm以下保性能低合金q345e+b钢板及其生产方法”提供了一种q345e含b钢板的生产方法。该方法生产钢板性能满足要求。但该方法适用于厚度在60mm以下的钢板生产,且钢里含有b,铸坯浇铸时容易产生裂纹。
4.公开号cn 102764959 a的专利“一种150~300mm厚低合金高强度钢板制造工艺方法”提供了一种q345e的厚规格钢板制造方法。该方法生产钢板性能满足要求。但该方法需要将两块板坯焊接起来进行轧制,生产难度较大;同时该方法要求钢板轧后进行正火处理,工序复杂,生产成本高。
5.公开号cn 102764959 a的专利“大厚度核电用q345d钢板及其生产方法”提供了一种q345d的厚规格钢板制造方法。该方法生产钢板性能满足要求。但该方法要求加入较多的合金,钢板的合金成本高;同时该方法要求钢板轧后进行正火处理,工序复杂,生产成本高。
技术实现要素:6.为了解决上述技术问题,本发明的目的是提供一种表面质量良好,生产工艺简单,制造成本低,低温韧性良好的屈服强度355mpa级80~100mm厚风电用钢板的生产方法。
7.为解决上述技术问题,本发明采用如下技术方案:
8.本发明一种80~100mm厚风电用钢板的生产方法,包括:
9.1).铁水冶炼前必须安排脱硫,脱硫后必须扒渣;冶炼时不得加入渣钢、海绵铁;
10.2).转炉采用单渣工艺冶炼;渣层厚度49~51mm;出钢时间5~7分钟;出钢温度1580~1640℃;采用低碳锰铁和硅铝铁合金脱氧合金化;
11.3).钢水进行rh炉处理,rh真空处理时间不少于20分钟,纯脱气时间不少于17分钟;
12.4).连铸坯的厚度为300mm,宽2200mm,钢水浇铸时过热度控制在16~31℃,连铸时采用轻压下,轻压下位置为6、7、8三段,总压下量为5.6mm;使用低碳钢保护渣,拉速为0.85m/min;使用电磁搅拌,电磁搅拌位置为4段,电磁搅拌的频率为5hz,电磁搅拌的电流为
360a;
13.5).加热工艺:板坯加热时采用步进式加热炉,连铸坯出炉温度1220-1240℃,加热时间280~360分钟;板坯在均热段的加热时间不少于40分钟;
14.6).钢板控轧控冷工艺:板坯加热好之后进行两阶段控制轧制,第一阶段开轧厚度为板坯厚度,第一阶段开轧温度1210~1230℃,第一阶段终轧温度≥1080℃,第一阶段高温延伸轧制时至少有两道次单道次压下率≥13%,第一阶段轧制速度为1.5m/s,咬入速度为0.8m/s;第二阶段钢板的开轧厚度为140~150mm,第二阶段钢板开轧温度为880~895℃,第二阶段终轧温度为800~820℃,第二阶段末道次压下率≥5%;钢板轧完后进行层流冷却,冷却速度为5~7℃/s,终冷温度为640~655℃;
15.7).钢板生产完毕后,需下线堆垛缓冷不少于48小时;
16.8).生产的钢板厚度为80mm~100mm厚。
17.进一步的,其化学成分按重量百分比为:c:0.06~0.08%;si:0.3~0.4%;mn:1.4~1.5%;nb:0.02~0.03%;v:0.015~0.025%;p≤0.015%;s≤0.005%;ca:0.0012~0.0027%;als:0.019~0.035%;其余为铁和不可避免杂质。
18.进一步的,采用300mm厚、2200mm宽的连铸坯;铁水冶炼前进行脱硫,脱硫后扒渣;冶炼时不加入渣钢、海绵铁;转炉采用单渣工艺冶炼;渣层厚度51mm;出钢时间5分钟;出钢温度1640℃;采用低碳锰铁和硅铝铁合金脱氧合金化;钢水进行rh炉处理,rh真空处理时间为20分钟,纯脱气时间为17分钟;钢水浇铸时过热度为31℃,连铸时采用轻压下,轻压下位置为6、7、8三段,总压下量为5.6mm;使用低碳钢保护渣,拉速为0.85m/min;使用电磁搅拌,电磁搅拌位置为4段,电磁搅拌的频率为5hz,电磁搅拌的电流为360a;板坯加热时采用步进式加热炉,连铸坯出炉温度为1240℃,加热时间为280分钟;板坯在均热段的加热时间为40分钟;板坯按重量百分比化学成分为:c 0.06%,si 0.4%,mn 1.4%,nb 0.02%,v 0.025%,p 0.015%,s 0.005%,ca 0.0012%,als 0.035%;其余为铁和不可避免杂质;轧制成厚度为80mm的钢板,钢板生产完毕后,下线堆垛缓冷52小时。
19.进一步的,采用300mm厚、2200mm宽的连铸坯;铁水冶炼前进行脱硫,脱硫后扒渣;冶炼时不加入渣钢、海绵铁;转炉采用单渣工艺冶炼;渣层厚度49mm;出钢时间7分钟;出钢温度1580℃;采用低碳锰铁和硅铝铁合金脱氧合金化;钢水进行rh炉处理,rh真空处理时间为21分钟,纯脱气时间为17.5分钟;钢水浇铸时过热度为16℃,连铸时采用轻压下,轻压下位置为6、7、8三段,总压下量为5.6mm;使用低碳钢保护渣,拉速为0.85m/min;使用电磁搅拌,电磁搅拌位置为4段,电磁搅拌的频率为5hz,电磁搅拌的电流为360a;板坯加热时采用步进式加热炉,连铸坯出炉温度为1220℃,加热时间为360分钟;板坯在均热段的加热时间为55分钟;板坯按重量百分比化学成分为:c 0.08%,si 0.3%,mn 1.5%,nb 0.03%,v 0.015%,p 0.012%,s 0.003%,ca 0.0027%,als 0.019%;其余为铁和不可避免杂质;轧制成厚度为100mm的钢板,钢板生产完毕后,下线堆垛缓冷48小时。
20.进一步的,采用300mm厚、2200mm宽的连铸坯;铁水冶炼前进行脱硫,脱硫后扒渣;冶炼时不加入渣钢、海绵铁;转炉采用单渣工艺冶炼;渣层厚度50mm;出钢时间6分钟;出钢温度1610℃;采用低碳锰铁和硅铝铁合金脱氧合金化;钢水进行rh炉处理,rh真空处理时间为22分钟,纯脱气时间为18分钟;钢水浇铸时过热度为21℃,连铸时采用轻压下,轻压下位置为6、7、8三段,总压下量为5.6mm;使用低碳钢保护渣,拉速为0.85m/min;使用电磁搅拌,
电磁搅拌位置为4段,电磁搅拌的频率为5hz,电磁搅拌的电流为360a;板坯加热时采用步进式加热炉,连铸坯出炉温度为1232℃,加热时间为342分钟;板坯在均热段的加热时间为51分钟;板坯按重量百分比化学成分为:c 0.07%,si 0.36%,mn 1.44%,nb 0.024%,v 0.019%,p 0.013%,s 0.002%,ca 0.0023%,als 0.032%;其余为铁和不可避免杂质;轧制成厚度为90mm的钢板,钢板生产完毕后,下线堆垛缓冷51小时。
21.与现有技术相比,本发明的有益技术效果:
22.1)本发明生产工艺简单,生产周期短;以廉价的si、mn合金为主,添加少量的nb、v,通过合适的冶炼、连铸、加热、控轧、控冷工艺,就能生产出机械性能良的屈服强度355mpa级80~100mm厚风电用钢板。钢板不用进行热处理,制造成本和合金成本较低,生产周期短。
23.2)钢板的强度、塑性、韧性良好,组织为细小的铁素体+珠光体。钢板的屈服强度在360mpa~395mpa之间,抗拉强度在500~526mpa之间,延伸率在28%~38.5%之间,-40℃冲击功在185j~236j之间。
附图说明
24.下面结合附图说明对本发明作进一步说明。
25.图1为本发明实施例1的钢板的金相组织图;
26.图2为本发明实施例2的钢板的金相组织图;
27.图3为本发明实施例3的钢板的金相组织图。
具体实施方式
28.以下结合实施例对本发明作进一步描述。
29.实施例1
30.一种80~100mm厚风电用钢板的生产方法,采用300mm厚、2200mm宽的连铸坯;铁水冶炼前进行脱硫,脱硫后扒渣;冶炼时不加入渣钢、海绵铁;转炉采用单渣工艺冶炼;渣层厚度51mm;出钢时间5分钟;出钢温度1640℃;采用低碳锰铁和硅铝铁合金脱氧合金化;钢水进行rh炉处理,rh真空处理时间为20分钟,纯脱气时间为17分钟。钢水浇铸时过热度为31℃,连铸时采用轻压下,轻压下位置为6、7、8三段,总压下量为5.6mm;使用低碳钢保护渣,拉速为0.85m/min。使用电磁搅拌,电磁搅拌位置为4段,电磁搅拌的频率为5hz,电磁搅拌的电流为360a,铸坯中心偏析为c3.0。板坯加热时采用步进式加热炉,连铸坯出炉温度为1240℃,加热时间为280分钟。板坯在均热段的加热时间为40分钟。板坯的(重量百分比)化学成分,按重量百分比:c 0.06%,si 0.4%,mn 1.4%,nb 0.02%,v 0.025%,p 0.015%,s 0.005%,ca 0.0012%,als 0.035%;其余为铁和不可避免杂质。轧制成厚度为80mm的钢板,钢板生产完毕后,下线堆垛缓冷52小时。详细的轧制及冷去工艺见表1,其力学性能见表2。
31.表1轧制及冷却工艺
[0032][0033]
表2钢板力学性能
[0034][0035]
实施例2
[0036]
一种80~100mm厚风电用钢板的生产方法,采用300mm厚、2200mm宽的连铸坯;铁水冶炼前进行脱硫,脱硫后扒渣;冶炼时不加入渣钢、海绵铁;转炉采用单渣工艺冶炼;渣层厚度49mm;出钢时间7分钟;出钢温度1580℃;采用低碳锰铁和硅铝铁合金脱氧合金化;钢水进行rh炉处理,rh真空处理时间为21分钟,纯脱气时间为17.5分钟。钢水浇铸时过热度为16℃,连铸时采用轻压下,轻压下位置为6、7、8三段,总压下量为5.6mm;使用低碳钢保护渣,拉速为0.85m/min。使用电磁搅拌,电磁搅拌位置为4段,电磁搅拌的频率为5hz,电磁搅拌的电流为360a,铸坯中心偏析为c2.0。板坯加热时采用步进式加热炉,连铸坯出炉温度为1220℃,加热时间为360分钟。板坯在均热段的加热时间为55分钟。板坯的(重量百分比)化学成分,按重量百分比:c 0.08%,si 0.3%,mn 1.5%,nb 0.03%,v 0.015%,p 0.012%,s 0.003%,ca 0.0027%,als 0.019%;其余为铁和不可避免杂质。轧制成厚度为100mm的钢板,钢板生产完毕后,下线堆垛缓冷48小时。详细的轧制及冷去工艺见表3,其力学性能见表4。
[0037]
表3轧制及冷却工艺
[0038][0039]
表4钢板力学性能
[0040][0041]
实施例3
[0042]
一种80~100mm厚风电用钢板的生产方法,采用300mm厚、2200mm宽的连铸坯;铁水冶炼前进行脱硫,脱硫后扒渣;冶炼时不加入渣钢、海绵铁;转炉采用单渣工艺冶炼;渣层厚度50mm;出钢时间6分钟;出钢温度1610℃;采用低碳锰铁和硅铝铁合金脱氧合金化;钢水进行rh炉处理,rh真空处理时间为22分钟,纯脱气时间为18分钟。钢水浇铸时过热度为21℃,连铸时采用轻压下,轻压下位置为6、7、8三段,总压下量为5.6mm;使用低碳钢保护渣,拉速为0.85m/min。使用电磁搅拌,电磁搅拌位置为4段,电磁搅拌的频率为5hz,电磁搅拌的电流为360a,铸坯中心偏析为c2.5。板坯加热时采用步进式加热炉,连铸坯出炉温度为1232℃,加热时间为342分钟。板坯在均热段的加热时间为51分钟。板坯的(重量百分比)化学成分,按重量百分比:c 0.07%,si 0.36%,mn 1.44%,nb 0.024%,v 0.019%,p 0.013%,s 0.002%,ca 0.0023%,als 0.032%;其余为铁和不可避免杂质。轧制成厚度为90mm的钢板,钢板生产完毕后,下线堆垛缓冷51小时。详细的轧制及冷去工艺见表5,其力学性能见表6。
[0043]
表5轧制及冷却工艺
[0044]
[0045][0046]
表6钢板力学性能
[0047][0048]
以上所述的实施例仅是对本发明的优选方式进行描述,并非对本发明的范围进行限定,在不脱离本发明设计精神的前提下,本领域普通技术人员对本发明的技术方案做出的各种变形和改进,均应落入本发明权利要求书确定的保护范围内。