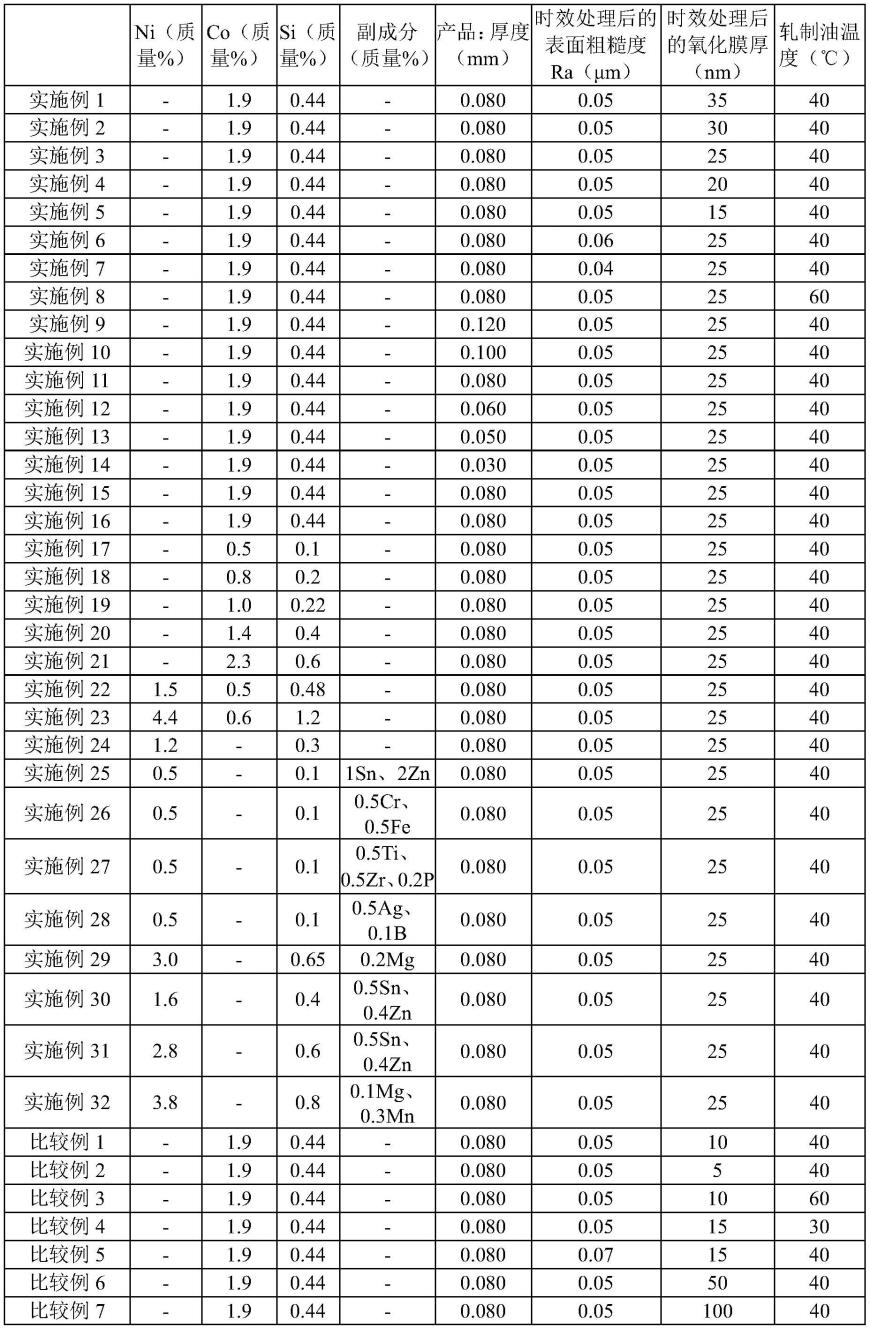
铜合金、伸铜品及电子机器零件
1.本发明是中国专利申请号为202010212628.3,发明名称为“铜合金、伸铜品及电子机器零件”,申请日为2020年03月24日的专利申请的分案申请。
技术领域
2.本发明涉及一种铜合金、伸铜品及电子机器零件。
背景技术:3.在铜及铜合金的条及箔的制造中,已知冷轧中会调整表面的光泽度。冷轧中被控制的条件为轧制速度、轧制油的黏度、轧制油的温度、加工度、工作辊的表面粗糙度、工作辊的直径等。
4.例如,日本特开2006-281249号公报(专利文献1)中记载了以下内容:使用纯铜的轧制铜箔作为使用了覆铜积层板的挠性印刷配线板(fpc),冷轧中对下述式(1)所规定的油膜当量进行调整:
5.(油膜当量)={(轧制油黏度、40℃的动态黏度;cst)
×
(轧制速度;m/分)}/{(材料的降伏应力;kg/mm2)
×
(辊咬入角;rad)}
…
(1)。
6.若根据专利文献1,基于上述式(1),使用低黏度的轧制油或减慢轧制速度等来控制油膜当量,由此可调整由纯铜构成的轧制铜箔的光泽度。
7.现有技术文献
8.专利文献
9.专利文献1:日本特开2006-281249号公报。
技术实现要素:10.[发明所要解决的课题]
[0011]
存在于轧制辊与轧制铜箔之间的油膜的厚度并不是严格地均匀,而是混合存在厚的部分和薄的部分。油膜厚的部分和油膜薄的部分中,表面的塑性变形的态样不同。
[0012]
油膜薄的部分相比于油膜厚的部分,作用于表面的按压力较大,形成在轧制辊表面的凹凸的束缚较强。因此,油膜薄的部分会因形成在轧制辊表面的凹凸而使得表面的氧化膜被破坏,出现新生面。另一方面,油膜厚的部分相比于油膜薄的部分,作用于表面的按压力较小,形成在轧制辊表面的凹凸的束缚较弱。因此,油膜厚的部分会因具有流动性的油膜介于其间而使得表面的氧化膜受到保存。
[0013]
在轧制铜箔形成来自金属组织的局部凹陷,该局部凹陷被称为油坑(oil pit)。油坑是轧制铜箔的表面中油膜局部变厚的部分。油坑会残留氧化膜形成凹陷,阻碍光的反射,会妨碍提高光泽度。因此,于由纯铜构成的轧制铜箔的情形时,如果油膜当量小,那么存在于轧制辊与轧制铜箔之间的油膜变薄,结果可抑制油坑的产生,而获得光泽度高的轧制铜箔。
[0014]
然而,已知即使对卡逊合金(corson alloy)将油膜当量控制为较小的情形,亦只
能获得显著低于由纯铜的实绩所预想者的光泽度。特别是厚度0.1mm以下的卡逊合金箔中该倾向很强烈。
[0015]
进而,在通过控制油膜当量来提高光泽度的研究中,已知到处可见焊接性差的铜合金。特别是光泽度低的卡逊合金箔中该倾向很强烈,光泽度高的合金箔中也有焊接性差的铜合金。
[0016]
因此,本发明提供一种光泽度高且焊接性良好的卡逊铜合金以及使用其的伸铜品及电子机器零件。
[0017]
[解决课题的技术手段]
[0018]
本发明的实施方案的铜合金于一方面是如下铜合金,其为含有合计0.5~5.0质量%的ni及co中的1种以上,0.1~1.2质量%的si,其余部分由铜及不可避免的杂质构成的轧制材,沿与轧制方向成直角的方向测定的表面的表面粗糙度rsk为-0.50~0.70,沿与轧制方向平行的方向测定的表面的60度光泽度g60
rd
为200以上。
[0019]
本发明的实施方案的铜合金于一实施例中,沿与轧制方向成直角的方向测定的表面的60度光泽度g60
td
为150以上。
[0020]
本发明的实施方案的铜合金于另一实施例中,沿与轧制方向成直角的方向测定的表面的表面粗糙度ra为0.03~0.20。
[0021]
本发明的实施方案的铜合金于再另一实施例中,于轧制材的表面具备镀敷处理层,沿与轧制材的轧制方向成直角的方向测定的该镀敷处理层的表面的60度光泽度g60
td
为250以上。
[0022]
本发明的实施方案的铜合金于再另一实施例中,以总量计含有0.005~3.0质量%的sn、zn、mg、cr、mn、fe、ti、zr、p、ag、b中的1种以上。
[0023]
本发明于另一方面为具备有上述铜合金的伸铜品。
[0024]
本发明于再另一方面为具备有铜合金的电子机器零件,电子机器零件包括相机零件。
[0025]
[发明的效果]
[0026]
若根据本发明,可提供一种光泽度高且焊接性良好的铜合金以及使用其的伸铜品及电子机器零件。
具体实施方式
[0027]
以下,对本发明的实施方案进行说明。本发明的实施方案的铜合金为含有合计0.5~5.0质量%的ni及co中的1种以上,0.1~1.2质量%的si,其余部分由铜及不可避免的杂质构成的轧制材,沿与轧制方向平行的方向测定的表面的60度光泽度g60
rd
为200以上。
[0028]
(ni、co及si的添加量)
[0029]
ni、co及si通过适当的时效处理而以ni-si、co-si、ni-co-si等金属间化合物的形式析出。该析出物的作用使得强度提高,由于会因析出而使得固溶于cu基材中的ni、co及si减少,因此导电率提高。然而,如果ni与co的合计量未达0.5质量%或si未达0.1质量%,则难以获得高强度的铜合金。如果ni与co的合计量超过5.0质量%或si超过1.2质量%,则会因热轧裂开等而导致合金的制造变得困难。
[0030]
因此,本发明的实施方案的铜合金将ni与co中的1种以上设为合计0.5~5.0质
量%,将si设为0.1~1.2质量%。ni与co中的1种以上的添加量更优选为0.8质量%以上,再更优选为1.2质量%以上。ni与co中的1种以上的添加量更优选为4.0质量%以下,再更优选为3.0质量%以下。si的添加量更优选为0.35质量%以上,再更优选为0.40质量%以上。si的添加量优选为0.90质量%以下,更优选为0.80质量%以上。
[0031]
(其他添加元素)
[0032]
作为副成分的sn、zn、mg、cr、mn、fe、ti、zr、p、ag、b有助于强度上升。进而,zn对提高镀sn的耐热剥离性有效,mg对提高应力缓和特性有效,cr、mn对提高热加工性有效。如果sn、zn、mg、cr、mn、fe、ti、zr、p、ag、b以总量计未达0.005质量%,则无法获得上述效果,如果超过3.0质量%,则弯曲加工性显著降低。因此,本发明的实施方案的铜合金优选为以总量计含有0.005~3.0质量%的这些元素,更优选含有0.01~1.0质量%。
[0033]
(光泽度)
[0034]
本发明的实施方案的铜合金其表面沿与轧制方向平行的方向测定的表面的60度光泽度g60
rd
为200以上,更优选为250以上,再更优选为300以上。由此可获得坑状凹凸被抑制的具有高金属光泽的铜合金。
[0035]
铜合金表面的60度光泽度g60
rd
越高,越可显示出高光泽,因此虽然产品外观变得优异,但如果光泽度g60
rd
过高,则有时无法获得良好的焊料润湿性。并非限定于以下,但与轧制方向平行的方向上的表面的光泽度g60
rd
典型上优选为200~500,典型上更优选为250~250。
[0036]
60度光泽度g60
rd
可通过下述方式求得:使用依照jis z8741的例如日本电色工业股份有限公司制造的光泽度计handy gloss meter pg-1等各种光泽度计,对与轧制方向平行的方向的入射角60
°
的光泽度进行测定。
[0037]
进而,本发明的铜合金沿与轧制方向成直角的方向上的60度光泽度g60
td
为150以上,典型上为150~450,更典型上为200~400。
[0038]
(镀敷处理层的光泽度)
[0039]
本发明的铜合金即使在通过实施规定的镀敷处理而于铜合金表面形成有0.1~20μm左右的镀敷处理层的情形时,也可维持高光泽度。即,本发明的铜合金于轧制材的表面具备镀敷处理层,沿与轧制材的轧制方向成直角的方向测定的情形时的镀敷处理层表面的60度光泽度g60
td
为250以上。若根据本发明,可获得具有镀敷处理层的铜合金,该镀敷处理层的耐氧化性优异,视觉品质方面也具有外观性优异的高金属光泽。
[0040]
作为镀敷处理层,可列举:镀铜层、镀锡层、镀ni层或镀金层,或者将这些镀层以表面镀敷及底层镀敷的形式组合而成的层,或者将这些镀层以条纹状或点状配置而成的层等。尤其是通过配置镀ni层作为镀敷处理层,而可获得具备外观及耐蚀性优异的高光泽的镀敷处理层的铜合金。
[0041]
(表面粗糙度rsk)
[0042]
于本发明的实施方案中,表面粗糙度rsk表示基于由jisb0601“产品的几何特性规格(gps)-表面性状:轮廓曲线方式-用语、定义及表面性状参数”(2017年)所定义的指标所测得的结果。例如,可基于jis规格b0601(2013),使用非接触的激光式表面粗糙度计,例如激光科技公司制造的共焦显微镜及附属的计算软体,根据轧制材表面沿与轧制方向成直角的方向的表面粗糙度分布算出。
[0043]
jisb0601中粗糙度曲线呈现出山与谷隔着平均线交替相连的形状。当以平均线作为对称轴时,rsk是表示山与谷的对称性的指标,可根据其定义概念性地将rsk理解成如下。
[0044]
(1)当高度高且宽度窄的山较多,深度浅且宽度宽的谷较多时,rsk取正值。高度高且宽度窄的山越多并且深度浅且宽度宽的谷越多,rsk的绝对值就越大。
[0045]
(2)当高度低且宽度宽的山较多,深度深且宽度窄的谷较多时,rsk取负值。高度低且宽度宽的山越多并且深度深且宽度窄的谷越多,rsk的绝对值就越大。
[0046]
(3)当山的高度与谷的深度相同且山的宽度与谷的宽度相同时,rsk显示为0。
[0047]
于通过冷轧精加工后的铜合金的表面,多多少少存在因冷轧及冷轧以外的步骤中的处理或加工所产生的局部凹陷。如果局部凹陷存在的密度高,则当rsk为正值时,rsk的绝对值显示出较小的值。又,如果局部凹陷存在的密度高,则当rsk为负值时,rsk的绝对值显示出较大的值。
[0048]
有时由于形状的原因导致处理或加工未对局部凹陷产生效果。或者有时处理或加工的效果小。因此,于局部凹陷容易残留异物。作为异物,可列举来自酸洗步骤所使用的酸洗液、冷轧步骤所使用的轧制油、去除轧制油的步骤所使用的脱脂液、时效处理等热处理所生成的氧化物等者。
[0049]
于局部凹陷存在异物是使铜合金的焊接性劣化的原因。因此,优选为局部凹陷存在的密度低。即,当rsk为正值的情形时,优选为rsk的绝对值大。又,当rsk为负值的情形时,优选为rsk的绝对值小。
[0050]
存在于铜合金表面的局部凹陷会对光的反射产生影响。即,入射至局部凹陷的光线会被局部凹陷吸收而不反射。或入射至局部凹陷的光线的入射角和反射角不会相同。因此,局部凹陷是使光泽度降低的原因。
[0051]
就铜合金表面的光泽度的观点,当rsk为正值的情形时,优选为rsk的绝对值大。又,当rsk为负值的情形时,优选为rsk的绝对值小。具体来说,本发明的实施方案的铜合金其表面粗糙度rsk为-0.50~0.70。如果rsk低于-0.50,则局部凹陷的存在密度变高,有时会导致光泽度降低及焊接性劣化。优选的范围的上限值并非根据金属光泽及焊接性的目的而规定,但为卡逊合金的条及箔的情形时不超过0.7。本发明的实施方案的铜合金的表面粗糙度rsk更典型为-0.20~0.65,再更典型为-0.15~0.40。
[0052]
(表面粗糙度ra)
[0053]
表面粗糙度ra可基于jis规格b0601(2013),使用非接触的激光式表面粗糙度计,例如激光科技公司制造的共焦显微镜及附属的计算软体,根据轧制材表面沿与轧制方向成直角的方向的表面粗糙度分布而算出。本实施方案的铜合金的表面粗糙度ra为0.03~0.20μm,更典型为0.06~0.07μm。如果表面粗糙度ra不在0.03~0.20μm的范围内,则有时不适合作为电子零件用的材料。再者,表面粗糙度ra可通过在冷轧中控制工作辊的表面粗糙度来调整。
[0054]
(厚度)
[0055]
本发明的实施方案的铜合金包括卡逊合金的条或箔,其厚度典型可设为0.030mm~0.15mm,更典型可设为0.030~0.120mm,进而更典型可设为0.050~0.010mm。
[0056]
(用途)
[0057]
本发明的实施方案的铜合金可适用于包括电气/电子机器、汽车等所使用的端子、
连接器、继电器、开关、插座、汇流排、引线架、散热板、电磁屏蔽板、相机零件等在内的电子机器零件的用途。
[0058]
又,本发明的实施方案的铜合金可通过根据使用目的精加工成规定的厚度,来加工成铜合金条、铜合金板、铜箔的形态。当将本发明的实施方案的铜合金加工成铜箔的情形时,通过对进行最终冷轧后的材料实施酸洗研磨处理,可获得表面外观性优异的高光泽的铜箔。
[0059]
(制造方法)
[0060]
本发明的实施方案的铜合金可利用通常的卡逊合金的制造方法来制造。在卡逊合金的通常制造方法中,首先利用熔炉将电解铜、ni、co、si等原料熔解,获得期望的组成的熔液。其次,将该熔液铸造成铸锭。然后进行热轧及冷轧而获得轧制材后,将其按照固溶处理、时效处理的顺序进行处理,由此精加工成具有期望的厚度及特性的铜合金条、铜合金板或铜箔。为了高强度化,亦可在固溶处理与时效之间或时效处理后进行冷轧。
[0061]
(时效处理中的氧化膜的厚度)
[0062]
本发明的实施方案的铜合金优选为时效处理后的表面氧化膜的厚度为15~35nm。如果表面氧化膜的厚度低于优选范围的下限,则会混合存在表面氧化膜厚的部分、薄的部分及大致不存在氧化膜的部分,因此氧化的状态变得不均。如果氧化的状态不均,则当在时效处理后进行酸洗的情形时,有时容易产生局部腐蚀、斑蚀或被称为孔蚀者,而在表面产生局部凹陷。又,如果氧化的状态不均,则有时酸洗后的研磨处理中研磨的效果也容易变得不均,而在表面产生局部凹陷。进而,如果氧化的状态不均,则有时在冷轧中轧制油的膜厚变得不均而产生被称为油坑的局部凹陷。这种局部凹陷的产生会导致表面粗糙度rsk容易显示出负值。
[0063]
如果氧化膜的厚度超过优选范围的上限,则氧化膜较脆,因此容易产生龟裂,有时会因龟裂而发生与上述相同的现象。混合存在氧化膜厚的部分、薄的部分、大致不存在氧化膜的部分的原因在于:于卡逊合金,在为母相的铜的内部存在co-si系或ni-si系的化合物相,这些化合物相的氧化速度不同,因此在氧化膜薄的初期阶段,于氧化膜的生成容易产生局部的差异。含有co-si系或ni-si系的化合物相的原因在于:卡逊合金的制造中有从高温冷却的过程,co-si系或ni-si系的化合物相会析出或结晶。时效处理后的铜合金的轧制面上形成的表面氧化膜更优选为25nm以下,优选为20nm以下。
[0064]
(氧化膜的厚度的测定方法)
[0065]
氧化膜的厚度例如可利用俄歇电子能谱法(aes)来测定。在aes分析中,交替进行氧浓度的测定和利用ar进行的溅镀,制作氧的浓度曲线。浓度曲线的横轴为溅镀时间的累计值,纵轴为氧浓度。时效处理后的卡逊合金的表层的氧浓度高。如果在氧浓度显示出最大处进一步交替进行ar溅镀和氧浓度的测定,则随着溅镀时间累计值的增加,氧浓度降低。然后,与溅镀时间的累计值无关,氧浓度显示出固定的值。根据氧的浓度曲线求出为氧浓度最大值的二分之一的值的ar溅镀时间的累计值,将该ar溅镀时间换算为长度,以此作为氧化膜的厚度。
[0066]
根据ar溅镀时间的累计值换算为长度,是以sio2的溅镀速度作为基准。例如,当sio2的溅镀速度为1nm/分、ar溅镀时间的累计值为12分钟时,换算为1
×
12=12nm。该方法为俄歇电子能谱法(aes)中通常进行的做法。优选的溅镀速度例如为1~2nm/分,1次的溅镀
时间为1~2分钟。
[0067]
(氧化膜厚度的控制方法)
[0068]
时效处理中的氧化膜厚度可通过加热装置中的环境气体的调整来控制。优选的环境为工业上所使用的还原性气体,调整组成及水分浓度即可。例如,可使用在氩气或氮气等非氧化性气体混合有氢气或一氧化碳者。例如,可使用氩气为70~90质量%,氢气为10~30质量%,露点为-40~-20℃的气体。
[0069]
再者,并不是只要为上述例所示的范围就总是能获得优选的氧化膜的厚度,由于卡逊合金需含有容易与氧反应的si,故而必须根据卡逊合金的组成调整气体的组成。然而,如果将混合的气体的种类设为最小限度,那么就可通过简单的预备试验来调整优选的组成。
[0070]
为了获得光泽度高且焊接性良好的铜合金,优选为时效处理后沿与轧制方向成直角的方向测定的卡逊合金的表面粗糙度ra为0.04~0.06。如果时效处理后沿与轧制方向成直角的方向测定的表面的表面粗糙度ra超过优选范围的上限,则在时效处理后的冷轧中,轧制油的膜厚变得不均,会产生油坑引起的凹凸,产品状态下的rsk容易显示出负值。如果ra低于优选范围的下限,则在时效处理后的冷轧中,从产品状态下的rsk的调整目的来说是优选的,但是有时轧制油不易流入轧制辊与卡逊合金之间,冷轧变得困难。表面粗糙度ra的调整可在用以将进行时效处理的铜合金调整为规定厚度的冷轧中通过控制工作辊的表面粗糙度来进行。
[0071]
时效处理后的表面粗糙度ra与上述产品表面的表面粗糙度ra的测定同样,可基于jis规格b0601(2013),使用非接触的激光式表面粗糙度计、例如激光科技公司制造的共焦显微镜及附属的计算软体,根据轧制材表面沿与轧制方向成直角的方向的表面粗糙度分布而算出。
[0072]
为了获得表面外观性优异的高光泽的铜合金,优选将最终的冷轧步骤中的轧制油的温度控制为合适的范围。于本实施方案中,优选将轧制温度设为30~70℃,更优选为40~60℃。
[0073]
若根据本发明的实施方案的铜合金及使用其的伸铜品、电子机器零件及铜合金的制造方法,可于表面发出高金属光泽,实现良好的表面外观。又,若根据本发明的实施方案的铜合金及使用其的伸铜品、电子机器零件,不论有无pb,焊接性均良好,即使在酸洗研磨后的铜合金上形成了镀敷层的情形时,也能够获得高光泽且表面外观性优异的铜合金。
[0074]
[实施例]
[0075]
以下一并揭示本发明的实施例和比较例,但这些实施例是为了更好地理解本发明及其优点而提供者,而非是要限定发明。
[0076]
利用真空熔炉将电解铜熔解,以可获得规定组成的方式添加ni、co、si及添加元素(副成分),铸造铸锭。对该铸锭依序进行热轧、冷轧,获得冷轧条。对该冷轧条进行固溶处理,然后进行冷轧、时效处理,最后进行酸洗研磨而制成产品。于酸洗研磨步骤,进行使用过氧化氢和硫酸的混酸的酸洗和抛光研磨。
[0077]
对酸洗研磨后的各材料进行以下各评价。
[0078]
<表面粗糙度ra、rsk>
[0079]
测定酸洗研磨后的各材料的表面粗糙度rsk。表面粗糙度rsk表示基于jis规格
b0601(2013),使用激光科技公司制造的共焦显微镜及附属的计算软体,根据轧制材表面沿与轧制方向成直角的方向的表面粗糙度分布而算出的结果。又,使用与表面粗糙度rsk相同的测定装置评价酸洗研磨后的表面粗糙度ra与时效处理后的表面粗糙度ra。
[0080]
<光泽度>
[0081]
基于jis z8741,使用日本电色工业股份有限公司制造的光泽度计handy gloss meter pg-1测定轧制平行方向及轧制直角方向的60度光泽度g60
rd
、g60
td
。
[0082]
<焊接性>
[0083]
使用掺pb焊料(60质量%sn-40质量%pb)及千住金属制造的无pb焊料m705系焊料,进行焊接试验。在焊料润湿性的评价中,依照jisc60068-2-54,利用可焊性测试仪(rhesca公司制造的sat-2000),按照与弧面状沾锡法(meniscograph method)相同的次序进行焊接,观察焊接部的外观。测定条件如下。作为试样的预处理,使用丙酮进行脱脂。其次,使用10vol%硫酸水溶液实施酸洗。焊料的试验温度设为245
±
5℃。助焊剂使用松香25质量%-乙醇75质量%。又,浸渍深度设为12mm,浸渍时间设为10秒,浸渍速度设为25mm/秒,试样的宽度设为10mm。关于评价基准,利用50倍的立体显微镜进行目视观察,将焊接部的整个面被焊料覆盖者记为良好(
○
),焊接部的一部分(针孔)或整个面(收缩)未被焊料覆盖者记为不良(
×
)。
[0084]
<镀敷处理>
[0085]
对酸洗研磨后的材料进行碱性电解脱脂作为预处理,酸洗后进行镀ni处理。镀镍有正常光泽镀敷、半光泽镀敷及光泽镀敷,这里利用市售的镀敷液进行光泽镀敷。将结果示于表1及表2。
[0086]
[表1]
[0087][0088]
[表2]
[0089][0090]
在时效处理后的表面粗糙度ra、氧化膜厚、轧制油温度为优选范围的实施例1~32中,沿与轧制方向平行的方向测定的表面的60度光泽度g60
rd
为200以上,沿与轧制方向成直角的方向测定的表面的60度光泽度g60
td
为150以上,获得光泽度高,表面外观性良好的铜合金,焊接性良好,镀敷后的光泽度高。
[0091]
比较例1由于时效处理后的氧化膜厚度薄,故而产品的表面粗糙度rsk低,轧制直角方向的60度光泽度g60
td
低。其结果,焊接性差,并且1μm镀敷后未显示出充分的金属光泽。
[0092]
比较例2由于时效处理后的氧化膜厚度薄,故而产品的表面粗糙度rsk低,轧制平行方向及轧制直角方向的光泽度均低。其结果,焊接性差,并且1μm镀敷后未显示出充分的金属光泽。
[0093]
比较例3虽然升高了轧制油的温度,但未能将产品的表面粗糙度rsk控制于恰当的范围内,轧制平行方向及轧制直角方向的光泽度均高。虽然1μm镀敷后显示出金属光泽,但焊接性差。
[0094]
比较例4的轧制油温度低。因此,轧制平行方向及轧制直角方向的光泽度均低。其结果,虽然焊接性良好,但1μm镀敷后未显示出充分的金属光泽。
[0095]
比较例5的时效处理后的表面粗糙度ra大。因此,产品的表面粗糙度rsk以及轧制平行方向及轧制直角方向的光泽度均低。其结果,焊接性不良,1μm镀敷后未显示出充分的金属光泽。
[0096]
比较例6及7的时效处理后的氧化膜厚。因此,产品的表面粗糙度rsk以及轧制平行方向及轧制直角方向的光泽度均低。其结果,焊接性不良,1μm镀敷后未显示出充分的金属光泽。