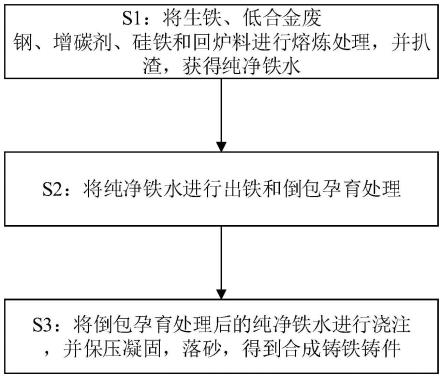
1.本发明涉及铸铁生产技术领域,具体为一种利用低合金废钢生产合成铸铁及方法。
背景技术:2.合成铸铁是利用高比例废钢经感应电炉,在熔得的铁液中加入石墨电极和碳化硅增碳增硅后获得的灰铸铁。目前,合成铸铁所使用的废钢均为低碳钢,低碳钢合金元素低,并且废钢纯净,杂质含量都很低,对铸铁的工艺性能与机械性能几乎无影响。因此,配料仅仅需要按照标准成分配料即可达到各项要求。
3.但是随着社会上对材料的强度、轻量化要求越来越高,合金钢和低合金废钢在钢材中所占比例逐渐增大,因此,废钢中的合金钢和低合金废钢比例越来越大。随着废钢比例的改变,现有合成铸铁工艺已经不能满足生产的需求。
4.因此,急需一种成本低、低合金废钢利用率高且性能稳定的合成铸铁工艺来满足生产需求。
技术实现要素:5.针对现有技术中存在的合成铸铁低合金废钢应用比例低,成本高导致的现有合成铸铁工艺无法满足当前生产需求的问题,本发明提供一种利用低合金废钢生产合成铸铁及方法。
6.为达到上述目的,本发明采用以下技术方案予以实现:
7.本发明提供一种利用低合金废钢生产的合成铸铁,按质量分数计包括以下原料组分:20%~30%的生铁、40%~50%的低合金废钢、1.23%~1.52%的增碳剂和0.7%~0.8%的硅铁,余量为回炉料。
8.优选地,所述低合金废钢的成分按质量百分比计为:0.18%~0.22%的c、0.17%~0.26%的si、0.70%~0.90%的mn、0.40%~0.60%的cr、0.40%~0.70%的ni和0.15%~0.25%的mo,余量为fe。
9.优选地,所述增碳剂的理化指标质量百分比为:c≥98.5%,s≤0.1%,n≤300ppm,水份≤0.5%,挥发份≤0.5%,灰份≤1%,增碳剂的粒度为1mm~5mm。
10.优选地,所述硅铁化学成分质量百分比为:72%~80%的si、0~1%的al,0~≤0.54%的cr,0~0.04%的p,余量为fe;硅铁的粒度为50mm~100mm。
11.优选地,该合金铸铁的成分质量百分比为:3.1%~3.5%的c、1.5%~2.3%的si、0.5%~0.85%的mn、0~0.1%的s、0~0.1%的p、0.16~0.35%的cr、0.15~0.30%的ni和0.06~0.10%的mo,余量为fe。
12.本发明还提供一种如上述的利用低合金废钢生产的合成铸铁的方法,包括以下步骤:
13.s1:将生铁、低合金废钢、增碳剂、硅铁和回炉料进行熔炼处理,并扒渣,获得纯净
铁水;
14.s2:将纯净铁水进行出铁和倒包孕育处理;
15.s3:将倒包孕育处理后的纯净铁水进行浇注,并保压凝固,落砂,得到合成铸铁铸件。
16.进一步地,s1的方法为:
17.步骤1)将生铁和低合金废钢混合进行熔炼,当生铁与低合金废钢熔化1/3~1/2时,加入增碳剂,并继续熔炼直至铁水化清;
18.步骤2)铁水化清后,向化清后的铁水中加入硅铁,并进行第一次升温,取样测试;
19.步骤3)根据测试结果,调节铁水的化学成分,并加入回炉料,进行第二次升温,加入聚渣剂,并扒渣获得纯净铁水。
20.优选地,第一次升温的温度大于1400℃;第二次升温的温度为1580℃~1600℃。
21.进一步地,步骤3)中调节铁水的化学成分按质量百分比计为:3.3%~3.5%的c、1.4%~1.7%的si、0.5%~0.85%的mn、0~0.1%的s、0~0.1%的p、0.16~0.35%的cr、0.15~0.30%的ni和0.06~0.10%的mo,余量为fe。
22.进一步地,s3中保压凝固的条件为:保压时间为8min~10min,保压范围为-0.02mpa~-0.04mpa。
23.与现有技术相比,本发明具有以下有益效果:
24.本发明一种利用低合金废钢生产合成铸铁,该合成铸铁按质量分数计包括以下原料组分:20%~30%的生铁、40%~50%的低合金废钢、1.23%~1.52%的增碳剂和0.7%~0.8%的硅铁,余量为回炉料。可使低合金废钢的利用达50%,提升低合金废钢的利用,使铸铁工艺的成本降低,经检验,所述合金铸铁的抗拉强度和硬度值等均满足冶金质量各项指标的要求,满足当前废钢比例变化合成铸铁工艺的需求。
25.本发明还提供一种合成铸铁的生产方法,该方法通过将生铁、低合金废钢、增碳剂、硅铁和回炉料进行熔炼处理,并扒渣,获得纯净铁水;将纯净铁水进行出铁和倒包孕育处理;将倒包孕育处理后的纯净铁水进行浇注,并保压凝固,落砂,得到合成铸铁铸件,经检验所生产的铸铁件铸态珠光体≥90%,本体硬度均值达192.6hb,本体抗拉强度均值达289mpa,微观组织石墨分布为a型,石长4级,珠光体数量为珠90,其性能和组织完全满足ht200的要求。通过对批量试制的成分、硬度和单铸试棒的数据统计,计算出利用低合金废钢生产合成铸铁的冶金质量各项指标,成熟度rg=1.1231,相对强度rz=138%,硬化度hg=0.911;相对硬度rh=0.845;品质系数qi=1.329,以上各项冶金参数优良。本生产方法所生产的铸铁既能达到必需的强度指标,又能保证铸铁具有良好的工艺性能,在提升低合金废钢的利用率,同时保持铸铁工艺性能的稳定性,满足当前铸铁工艺的需求,降低了生产成本,生产方法简单,无需设备改造,改造成本低。
附图说明
26.图1为本发明的一种利用低合金废钢生产合成铸铁的生产方法流程图。
27.图2为本发明的一种利用低合金废钢生产合成铸铁的生产方法工艺流程图。
28.图3为实施例1的利用低合金废钢生产合成铸铁的金相图片,其中a为未腐蚀之前铸件的金相图片,b为经腐蚀后铸件的金相图片。
29.图4为实施例2的利用低合金废钢生产合成铸铁的金相图片,其中a为未腐蚀之前铸件的金相图片,b为经腐蚀后铸件的金相图片。
30.图5为实施例中单铸试棒检测硬度及抗拉强度统计结果分布图,其中,a为硬度统计分布图,b为抗拉强度统计分布图。
具体实施方式
31.为使本发明实施例的目的、技术方案和优点更加清楚,下面将结合本发明实施例中的附图,对本发明实施例中的技术方案进行清楚、完整地描述,显然,所描述的实施例是本发明一部分实施例,而不是全部的实施例。通常在此处附图中描述和示出的本发明实施例的组件可以以各种不同的配置来布置和设计。
32.因此,以下对在附图中提供的本发明的实施例的详细描述并非旨在限制要求保护的本发明的范围,而是仅仅表示本发明的选定实施例。基于本发明中的实施例,本领域普通技术人员在没有作出创造性劳动前提下所获得的所有其他实施例,都属于本发明保护的范围。
33.应注意到:相似的标号和字母在下面的附图中表示类似项,因此,一旦某一项在一个附图中被定义,则在随后的附图中不需要对其进行进一步定义和解释。
34.在本发明实施例的描述中,需要说明的是,若出现术语“上”、“下”、“水平”、“内”等指示的方位或位置关系为基于附图所示的方位或位置关系,或者是该发明产品使用时惯常摆放的方位或位置关系,仅是为了便于描述本发明和简化描述,而不是指示或暗示所指的装置或元件必须具有特定的方位、以特定的方位构造和操作,因此不能理解为对本发明的限制。此外,术语“第一”、“第二”等仅用于区分描述,而不能理解为指示或暗示相对重要性。
35.此外,若出现术语“水平”,并不表示要求部件绝对水平,而是可以稍微倾斜。如“水平”仅仅是指其方向相对“竖直”而言更加水平,并不是表示该结构一定要完全水平,而是可以稍微倾斜。
36.在本发明实施例的描述中,还需要说明的是,除非另有明确的规定和限定,若出现术语“设置”、“安装”、“相连”、“连接”应做广义理解,例如,可以是固定连接,也可以是可拆卸连接,或一体地连接;可以是机械连接,也可以是电连接;可以是直接相连,也可以通过中间媒介间接相连,可以是两个元件内部的连通。对于本领域的普通技术人员而言,可以根据具体情况理解上述术语在本发明中的具体含义。
37.下面结合具体的实施例对本发明做进一步的详细说明,所述是对本发明的解释而不是限定。
38.本发明公开了一种利用低碳合金生产的合成铸铁,按质量分数计包括以下原料组分:20%~30%的生铁、40%~50%的低合金废钢、1.23%~1.52%的增碳剂和0.7%~0.8%的硅铁,余量为回炉料。
39.其中,所述低合金废钢的成分按质量百分比计为:0.18%~0.22%的c、0.17%~0.26%的si、0.70%~0.90%的mn、0.40%~0.60%的cr、0.40%~0.70%的ni和0.15%~0.25%的mo,余量为fe;所述增碳剂为煅烧无烟煤、煅烧石油焦、天然石墨和人造石墨中的一种或多种,从环保、质量、工艺、来源和经济方面考虑,优选为人造石墨,所述增碳剂的理化指标质量百分比为:c≥98.5%,s≤0.1%,n≤300ppm,水份≤0.5%,挥发份≤0.5%,灰
份≤1%,增碳剂的粒度为1mm~5mm;所述硅铁化学成分质量百分比为:72%~80%的si、0~1%的al,0~≤0.54%的cr,0~0.04%的p,余量为fe;硅铁的粒度为50mm~100mm;所述回炉料为同牌号回炉料,包括同一车间铸件的浇冒口和有铸造缺陷的废弃铸件等。
40.该合成铸铁的成分质量百分比为:3.1%~3.5%的c、1.5%~2.3%的si、0.5%~0.85%的mn、0~0.1%的s、0~0.1%的p、0.16~0.35%的cr、0.15~0.30%的ni和0.06~0.10%的mo,余量为fe。
41.参见图1和图2,本发明提供一种如上所述的合成铸铁的生产方法,包括以下步骤:
42.s1:将生铁、低合金废钢、增碳剂、硅铁和回炉料进行熔炼处理,并扒渣,获得纯净铁水,具体操作为:
43.步骤1)将生铁和低合金废钢混合进行熔炼,当生铁与低合金废钢熔化1/3~1/2时,加入增碳剂,并继续熔炼直至铁水化清;
44.步骤2)铁水化清后,向化清后的铁水中加入硅铁,并进行第一次升温,升温至1400℃以上,取样测试,利用直读光谱仪检测铁水成分;
45.步骤3)根据测试结果,调节铁水的化学成分按质量百分比计为:3.3%~3.5%的c、1.4%~1.7%的si、0.5%~0.85%的mn、0~0.1%的s、0~0.1%的p、0.16~0.35%的cr、0.15~0.30%的ni和0.06~0.10%的mo,余量为fe。并加入回炉料,进行第二次升温,在额定功率1500kw升温至1580℃~1600℃,加入聚渣剂,并扒渣获得纯净铁水,所述聚渣剂为20目~30目的珍珠岩保温覆盖剂。
46.s2:将纯净铁水进行出铁和倒包孕育处理,将s1中获得的纯净铁水倒入浇注包内,并在倾倒纯净铁水的过程中随流均匀加入孕育剂,孕育剂的加入量为纯净铁水的0.54%,优选地,所述倒包孕育的孕育剂化学成分按质量百分比计为:68%~72%的si、4.0%~6.0%的ba、1.0%~2.0%的ca和0~2.0%的al,孕育剂的粒度为10mm~20mm,孕育剂优选为粒度为10mm~20mm的basife孕育剂。
47.s3:将倒包孕育处理后的纯净铁水进行浇注,并保压凝固,落砂,得到合成铸铁铸件,将倒包孕育处理后的纯净铁水在1470℃~1520℃的温度下浇入准备好的模型簇中,浇注过程确保负压范围-0.03mpa~-0.07mpa;浇注完成后,持续保压,保压时间为8min~10min,保压范围-0.02mpa~-0.04mpa;保压凝固后,砂箱按照正常生产节拍运转至落砂工位,落砂后铸件温度控制在100℃以下。
48.优选地,为防止孕育衰退,从出铁至浇注结束时间控制在12min以内
49.实施例1
50.某变速器壳体一,1吨中频炉熔炼为例,按质量百分比将202kg的q10生铁和455kg的低合金废钢混合进行熔炼,当生铁与低合金废钢熔化1/3时,加入15.2kg的人造石墨,并继续熔炼直至铁水化清;
51.铁水化清后,向化清后的铁水中加入7.1kg的75#硅铁,并升温至1410℃,取样测试,利用直读光谱仪检测铁水成分;
52.根据测试结果,调节铁水的化学成分按质量百分比计为:3.319的c、1.561%的si、0.737%的mn、0.018%的s、0.024%的p、0.274%的cr、0.252%的ni和0.097%的mo,余量为fe。并加入320.7kg回炉料,在额定功率1500kw升温至1586℃,加入20目~30目的珍珠岩保温覆盖剂,并扒渣获得纯净铁水。
53.将纯净铁水倒入浇注包内,并在倾倒纯净铁水的过程中随流均匀加入5.3kg孕育剂。
54.将倒包孕育处理后的纯净铁水在1512℃的温度下浇入准备好的模型簇中,浇注过程确保负压范围-0.03mpa~-0.07mpa;浇注完成后,持续保压,保压时间为10min,保压范围-0.02mpa~-0.04mpa;保压凝固后,砂箱按照正常生产节拍运转至落砂工位,落砂后铸件温度控制在100℃以下。
55.经检测,最终得到的铸件化学成分按质量百分比为:c为3.303%,si为1.928%,mn为0.749%,s为0.017%,p为0.023%,cr为0.227%,ni为0.222%,mo为0.078%,余量为fe。铸态本体取样,测得本体样品硬度分别为184hb、193hb、182hb、189hb、185hb、187hb和195hb;单铸试棒检测抗拉强度,测得抗拉强度分别为289mpa和288mpa;参见图3,附铸试块检测金相,所得铸件为石墨分布为a型,石长4级,珠光体数量为珠90。
56.实施例2
57.某离合器壳体二,2吨中频炉熔炼为例,按质量百分比将505kg的q10生铁和845kg的低合金废钢混合进行熔炼,当生铁与低合金废钢熔化1/3时,加入25.2kg的人造石墨,并继续熔炼直至铁水化清;
58.铁水化清后,向化清后的铁水中加入15.6kg的75#硅铁,并升温至1433℃,取样测试,利用直读光谱仪检测铁水成分;
59.根据测试结果,调节铁水的化学成分按质量百分比计为:3.399%的c、1.5061%的si、0.735%的mn、0.031%的s、0.024%的p、0.326%的cr、0.242%的ni和0.086%的mo,余量为fe。并加入609.2kg回炉料,在额定功率1500kw升温至1590℃,加入20目~30目的珍珠岩保温覆盖剂,并扒渣获得纯净铁水。
60.将纯净铁水倒入浇注包内,并在倾倒纯净铁水的过程中随流均匀加入10.8kg孕育剂。
61.将倒包孕育处理后的纯净铁水在1508℃的温度下浇入准备好的模型簇中,浇注过程确保负压范围-0.03mpa~-0.07mpa;浇注完成后,持续保压,保压时间为8min,保压范围-0.02mpa~-0.04mpa;保压凝固后,砂箱按照正常生产节拍运转至落砂工位,落砂后铸件温度控制在98℃以下。
62.经检测,最终得到的铸件化学成分按质量百分比为:c为3.326%,si为1.861%,mn为0.745%,s为0.024%,p为0.023%,cr为0.327%,ni为0.241%,mo为0.086%,余量为fe。铸态本体取样,测得本体样品硬度分别为200hb、204hb、195hb、201hb、202hb、207hb、201hb和204hb;单铸试棒检测抗拉强度,测得抗拉强度分别为290mpa、297mpa和291mpa;参见图4,附铸试块检测金相,所得铸件为石墨分布为a型,石长4级,珠光体数量为珠90。
63.实施例3
64.某离合器壳体三,1吨中频炉熔炼为例,按质量百分比将210kg的q10生铁和470kg的低合金废钢混合进行熔炼,当生铁与低合金废钢熔化1/3时,加入16.2kg的人造石墨,并继续熔炼直至铁水化清;
65.铁水化清后,向化清后的铁水中加入8kg的75#硅铁,并升温至1450℃,取样测试,利用直读光谱仪检测铁水成分;
66.根据测试结果,调节铁水的化学成分按质量百分比计为:3.421%的c、1.491%的
si、0.668%的mn、0.02%的s、0.0177%的p、0.237%的cr、0.245%的ni和0.1%的mo,余量为fe。并加入335kg回炉料,在额定功率1500kw升温至1586℃,加入20目~30目的珍珠岩保温覆盖剂,并扒渣获得纯净铁水。
67.将纯净铁水倒入浇注包内,并在倾倒纯净铁水的过程中随流均匀加入5.4kg孕育剂。
68.将倒包孕育处理后的纯净铁水在1470℃的温度下浇入准备好的模型簇中,浇注过程确保负压范围-0.03mpa~-0.07mpa;浇注完成后,持续保压,保压时间为8min,保压范围-0.02mpa~-0.04mpa;保压凝固后,砂箱按照正常生产节拍运转至落砂工位,落砂后铸件温度控制在100℃以下。
69.经检测,最终得到的铸件化学成分按质量百分比为:3.391%的c、1.845%的si、0.678%的mn、0.022%的s、0.0197%的p、0.247%的cr、0.235%的ni和0.096%的mo,余量为fe。铸态本体取样,测得本体样品硬度分别为195hb、198hb、190hb、200hb、204hb、198hb、195hb和202hb;单铸试棒检测抗拉强度,测得抗拉强度分别为294mpa、298mpa和288mpa;由金相结果可知,所得铸件为石墨分布为a型,石长4级,珠光体数量为珠90。
70.实施例4
71.某变速器壳体四,2吨中频炉熔炼为例,按质量百分比将405kg的q10生铁和885kg的低合金废钢混合进行熔炼,当生铁与低合金废钢熔化1/3时,加入29.5kg的人造石墨,并继续熔炼直至铁水化清;
72.铁水化清后,向化清后的铁水中加入13.5kg的75#硅铁,并升温至1490℃,取样测试,利用直读光谱仪检测铁水成分;
73.根据测试结果,调节铁水的化学成分按质量百分比计为:3.383%的c、1.452%的si、0.677%的mn、0.0204%的s、0.0172%的p、0.227%的cr、0.234%的ni和0.0977%的mo,余量为fe。并加入753kg回炉料,在额定功率1500kw升温至1593℃,加入20目~30目的珍珠岩保温覆盖剂,并扒渣获得纯净铁水。
74.将纯净铁水倒入浇注包内,并在倾倒纯净铁水的过程中随流均匀加入10.6kg孕育剂。
75.将倒包孕育处理后的纯净铁水在1508℃的温度下浇入准备好的模型簇中,浇注过程确保负压范围-0.03mpa~-0.07mpa;浇注完成后,持续保压,保压时间为10min,保压范围-0.02mpa~-0.04mpa;保压凝固后,砂箱按照正常生产节拍运转至落砂工位,落砂后铸件温度控制在100℃以下。
76.经检测,最终得到的铸件化学成分按质量百分比为:3.343%的c、1.824%的si、0.752%的mn、0.0207%的s、0.0165%的p、0.213%的cr、0.219%的ni和0.0917%的mo,余量为fe。铸态本体取样,测得本体样品硬度分别为200hb、197hb、194hb、199hb、202hb、201hb、203hb和200hb;单铸试棒检测抗拉强度,测得抗拉强度分别为290mpa、295mpa和286mpa;由金相结果可知,所得铸件为石墨分布为a型,石长4级,珠光体数量为珠90。
77.综上,经过批量生产验证,铸件化学成分控制在::c 3.1%~3.5%,si 1.5%~2.3%,mn 0.5%~0.85%,s≤0.1%,p≤0.1%,cr 0.16%~0.30%,ni0.15%~0.30%,mo 0.06~0.10%,余量为fe。铸态本体取样,测得本体硬度分布图见图5a,批量试制本体硬度均值为192.6hb w10/3000,所有样本均符合标准要求;单铸试棒检测抗拉强度,测得抗拉
强度分布见图5b,批量试制样本抗拉强度均值为289.111mpa,所有样本均符合标准要求;附铸试块检测金相,石墨分布为a型,石长4级,珠光体数量为珠90。通过对批量试制的成分、硬度和单铸试棒的数据统计,计算出利用低合金废钢生产合成铸铁的冶金质量各项指标,成熟度rg=1.1231,相对强度rz=138%,硬化度hg=0.911;相对硬度rh=0.845;品质系数qi=1.329,以上各项冶金参数优良,本发明生产的铸铁既能达到必需的强度指标,又能保证铸铁具有良好的工艺性能。
78.以上所述的仅仅是本发明的较佳实施例,并不用以对本发明的技术方案进行任何限制,本领域技术人员应当理解的是,在不脱离本发明精神和原则的前提下,该技术方案还可以进行若干简单的修改和替换,这些修改和替换也均属于权利要求书所涵盖的保护范围之内。