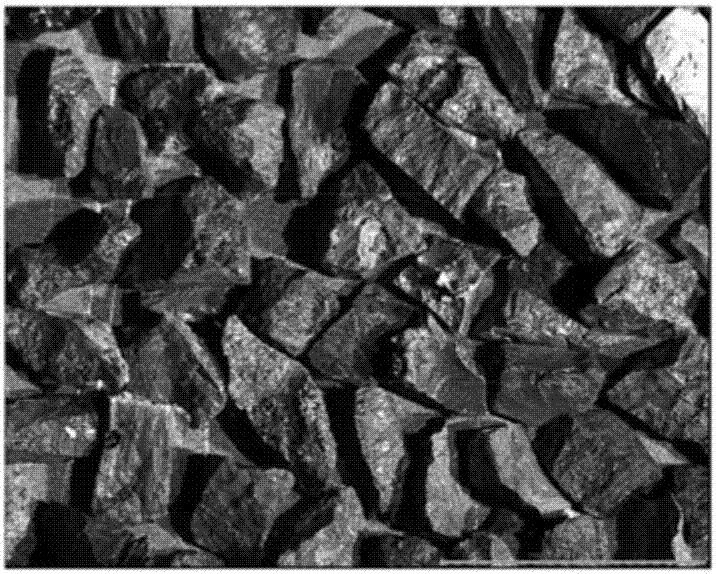
本发明涉及制备烧结的陶瓷颗粒的方法,用作陶瓷颗粒,用作由陶瓷磨损部件的三维互联网络形成的开孔的陶瓷结构,以及用作粉碎(减小)设备和粉碎设备的应用。本发明涉及尤其但非专门用于含有陶瓷颗粒的磨损部件的陶瓷颗粒,尤其是在碾磨、破碎和运输各种研磨材料的车间中使用的磨损部件,这些研磨材料用于工业应用,尤其是水泥厂;采矿;金属工业,例如炼钢工业;铸造;发电站;回收活动;采石场;清淤;地面作业;油砂回收。
背景技术:
:us3,454,385涉及适于重负荷荒磨(heavydutysnagging)的研磨组合物,其包括30%至70%的氧化铝、15%至60%氧化锆和5%至15%的铁、钛、锰和硅的一种或多种氧化物。在煅烧之前将该材料预制成最终需要的形状,煅烧成一定尺寸并作为磨矿媒介或作为在有机粘合的碾磨砂轮中使用的研磨颗粒以未粉碎的状态使用。ep152768(a)涉及用于研磨应用的陶瓷体。该陶瓷体含有α氧化铝亚微米晶粒并且已通过在低于1400℃的温度下烧结制成。描述了其中在酸性条件下使氧化铝胶凝的制造方法。将该凝胶干燥然后进行辊式破碎,之后过筛,然后煅烧以产生所需的最终粒度。也存在用于制备陶瓷颗粒的其他方法,例如流化床或优化的挤压造粒,等等。尤其是,磨损部件和研磨切割工具经常处于宏观中(inthebulk)的高机械应力下并且在工作面上受到高磨损。因此,这些组分呈现高耐磨性和一些韧性是合乎需要的,以允许其能够承受机械应力,例如挤压、研磨、摩擦、侵蚀和/或腐蚀。考虑到在同一种材料中这两种性质难以彼此兼顾,因此已提出了具有由合金制成的核的复合材料部件,其中包埋了有具有良好耐磨性的分离的陶瓷刀片。通常,该合金比陶瓷刀片具有更好的韧性。ep0575685(a)涉及金属基质中的陶瓷刀片的复合材料磨损部件。该文献中所描述的制造方法具有许多局限性,尤其是在所制造的磨损部件的尺寸方面。ep0930948(a)涉及由金属基质构成的磨损部件,该金属基质的磨损表面包含具有良好耐磨性质的刀片(insert),这些刀片由陶瓷材料制成,该陶瓷材料本身是复合材料,由20%至80%的al2o3和80%至20%的zro2的固溶体或均相组成,百分比均以成分的重量计。优选地,该刀片的al2o3含量为至少55wt.%。实例示出了由分别具有25wt.%和40wt.%的zro2含量的电熔的颗粒制成的陶瓷垫(刀片)。尽管由这样的陶瓷垫制成的磨损部件满足了各种碾磨应用中的用途,但本发明人认为需要替代性的,尤其是可在具体应用中提供优势的改进的磨损部件,或者为磨损部件本身提供进一步改进的磨损部件。尤其是,本发明人注意到,电熔的颗粒仍会具有之前已存在的因用于获得颗粒的工艺形成的裂纹的问题,这对磨损部件的操作寿命是不利的,或者这会导致较高的产品报废率,或储存期间颗粒的损坏。还存在改进制造陶瓷-金属磨损部件或其一部分(例如陶瓷材料)的方法的需求。尤其是,提供在更小能耗、更少耗时、更少耗材或降低报废率(不满足所要求的规格的产品部分)方面得到改进的方法。技术实现要素:本申请的一个目的是提供在用于材料粉碎的陶瓷-金属磨损复合材料部件中使用的新型陶瓷材料,其具有令人满意的刚性和硬度以提供已知陶瓷材料的替代品,分别称为磨损部件,尤其是提供较少受到在磨损部件的陶瓷材料或金属相中形成裂纹影响的陶瓷材料。本发明的进一步目的是提供用于制备陶瓷颗粒的方法,尤其是满足上述要求中的一种或多种的方法。本发明的进一步目的是提供用于研磨应用中的新型陶瓷材料,例如,尤其但不限于碾磨砂轮和砂纸。下文的描述将使所达到的一个或多个其他目的显而易见。发明人发现了适于达到本发明深层次的一个或多个目的的用于制备陶瓷颗粒的具体技术。因此本发明涉及用于制备陶瓷颗粒的方法,所述方法包括:-制备包含无机粒子以及胶凝剂的浆料;-制备所述浆料的液滴;-将所述液滴引入到液体胶凝反应介质中,其中所述液滴被胶凝化;-在胶凝化之前、期间或之后使所述液滴变形;-干燥胶凝化的变形的液滴,从而获得干燥的颗粒并烧结所述干燥的颗粒,从而获得所述陶瓷颗粒。进一步地,本发明涉及可通过根据本发明的方法获得的烧结的陶瓷颗粒。进一步地,本发明涉及烧结的陶瓷颗粒-优选可通过本发明的方法获得的烧结的陶瓷颗粒-所述颗粒包含α-氧化铝,所述颗粒的α-氧化铝含量的范围为50-90wt.%,所述颗粒进一步含有形成少于所述颗粒总重量30wt.%的非晶相,所述颗粒含有二氧化硅,其可以非晶相或以结晶相存在。进一步地,本发明涉及根据本发明的陶瓷颗粒的三维互联网络形成的开孔的陶瓷结构,所述颗粒用粘结剂相连,其中所述颗粒的堆积体在所述颗粒之间提供开孔,其孔可由液态金属填充。进一步地,本发明涉及金属-陶瓷复合材料磨损部件,所述部件由根据本发明的开孔的陶瓷结构和至少一部分所述陶瓷结构周围的金属基质制成。进一步地,本发明涉及用于制备根据本发明的磨损部件的方法,所述方法包括:-提供根据本发明的陶瓷结构;-用液态金属填充所述陶瓷结构的开孔;以及-使所述液态金属固化,从而形成所述磨损部件。进一步地,本发明涉及粉碎设备,所述粉碎设备包括根据本发明的磨损部件。进一步地,本发明涉及用于处理材料的方法,所述方法包括将所述材料引入到根据本发明的装置中并使该材料进行粉碎步骤,其中所述磨损部件与所述材料接触,尤其是,粉碎步骤选自碾磨和破碎的组中。进一步地,本发明涉及研磨切割工具、复合装甲,分别为由根据本发明的陶瓷颗粒或开孔的陶瓷结构制成的挖泥泵。进一步地,本发明涉及柔性涂层研磨制品,例如砂纸,所述制品具有提供根据本发明的颗粒的研磨表面。本发明能够制备具有令人满意性质的陶瓷颗粒,其特别用作粉碎设备的陶瓷-金属磨损部件中的陶瓷部件,例如在选自以下的粉碎设备中:磨,尤其是卧式管式磨和立式碾磨磨;破碎设备,尤其是卧式轴式破碎机;以及冲击机设备,尤其是立式轴式冲击机。该磨损部件尤其可在粉碎设备中提供,该粉碎设备在碾磨、破碎和运输各种研磨材料的车间中使用,其用于例如水泥厂、采矿、冶金、发电站、回收活动、采石、清淤、油砂回收的产业中。在进一步的实施方式中,该颗粒在研磨切割工具,例如研磨切割砂轮、砂纸中提供或在复合装甲中提供。本发明提供了许多过程相关的优点。例如,其能够不需要破碎操作制造颗粒。而且,多个颗粒通常具有尺寸上的高均一性,而不需要使多个颗粒进行基于尺寸的分离步骤,例如过筛。而且,根据本发明的方法能够以令人满意的能量效率来操作,至少相比于一些已知的技术在这方面得到了改善。相比于所制造的具有相同组成的陶瓷颗粒,例如在通过这样制备颗粒工艺中,其中通过首先熔融成份,然后淬灭该熔融物以形成融合的陶瓷并破坏融合的陶瓷以获得颗粒,本发明的优点尤其是能够制造具有较低弱点(尤其是裂纹)发生率,或者基本上无弱点(尤其是裂纹)的颗粒。这在图2.1中示出,其示出了粒径为约1.6mm的根据本发明的颗粒的抛光截面。在根据本发明的这些颗粒中不存在明显裂纹。图2.2示出了根据us3,181,939的教导制备的可对比的粒状产物,其通过熔融(电熔)、淬火和破碎来制造。能够观察到沿着该颗粒的宽度的显著部分可见裂纹(深色线)。本发明进一步的优点在于,其能够提供具有令人满意的耐磨性的颗粒,从而使由该颗粒制造的磨损部件具有令人满意的预期寿命,其类似于由通过例如电熔制造的可对比的粒状产物制成的磨损部件,相比之得到了改善。本发明进一步的优点在于,其能够提供具有低粉化倾向的颗粒,这允许(在进一步使用前)产物的脱落百分比降低而且对于磨损部件的寿命也是有利的。本发明方法的进一步优点在于,该颗粒制备工艺是易控制的,这能够制造在形式、机械性能和/或尺寸方面以及相当大体积方面具有相对较高均一性的(多个)颗粒。不受理论的束缚,据信颗粒的相对较大均一性尤其是在材料性质(例如刚性和硬度)方面,以及弱点的低发生率方面有助于良好预期寿命,并且即使常规用来改善耐磨性的陶瓷成分的含量低的话也是如此。发明人因此得出结论认为,能够提供具有相对较高硬度或刚性的陶瓷颗粒,同时考虑到其他产品性质,例如材料组成、堆积密度(陶瓷材料与大量颗粒总体积的体积比)或颗粒的陶瓷材料密度。尤其是,发明人发现,根据本发明能够提供具有相对较低材料密度、令人满意的硬度和令人满意的刚性的用于碾磨、破碎或其他粉碎设备的磨损部件中的颗粒。例如,为了节约材料使用,使用具有相对较低密度的材料是有用的。尤其是,可根据本发明获得的颗粒可通过具有带条纹的表面的圆形外观来表征。在该表面处存在波纹(ripples),参见例如图1.1,这与会导致颗粒尖锐并且具有边缘(图1.2)的通过破碎电熔的原材料块形成的颗粒不同。此外,本发明的粒子可以具有更偏向球形的外观,而通过破碎形成的颗粒则具有更偏向多边形截面的外观。此外,根据本发明的颗粒的形式倾向于比常规破碎的颗粒更加平滑。应该理解,在现有技术中,平滑形式通常被认为在陶瓷-金属复合材料中是不利的,除非在陶瓷和金属之间提供化学键,因为通常认为陶瓷会相对容易脱落。尽管如此,根据本发明的磨损部件在这方面仍具有令人满意的性质。显然,表面处的不规则和沟槽(即粗糙度)为颗粒在陶瓷-金属复合材料中提供了充分的抓持(hold)从而赋予了该复合材料充分的磨损特性(wearingcharacteristics)。发明人考虑了本发明的颗粒具有对于其堆积行为有利的形状。该颗粒比常规破碎的颗粒具有更高的堆积行为,从而允许耐磨材料(陶瓷材料)能够在陶瓷-金属复合材料中获得更高的体积百分比。如在本文中使用的,除非另外说明,术语“或”意指“和/或”。如在本文中使用的,除非另外说明,术语“一个”或“一种”意指“至少一个/至少一种”。术语“基本上”或“实质上”在本文中通常用于指明具体所指的对象具有一般特征或功能。当指代可量化的特征时,这些术语尤其用于指明其为该特征最大值的至少75%,更加尤其是至少90%,甚至更加尤其是至少95%。当以单数指代“名词”(例如,化合物、添加剂等)时,除非另外说明,意在包括复数。当指代百分比时,除非另外说明,其通常是基于组合物总重量的重量百分比(wt.%)。出于清楚和简要描述的目的,本文中所述的特征作为相同或单独实施方式的部分,然而,应该理解本发明的范围可以包括具有所有或一些所述特征的组合的实施方式。当指代浓度或数量时,除非另外说明,该浓度/数量是基于所指代的材料或产品(例如,陶瓷、颗粒)的总重量。可利用x-射线荧光(xrf)来确定陶瓷的化学组成。可利用x-射线衍射来确定陶瓷的晶体组成和非晶相的量。在本发明的方法中,浆料由无机非金属粒子和胶凝剂制成。该粒子通常为适合作为陶瓷产品的起始材料的粒子。通常,该无机非金属的粒子包含选自无机氧化物、硅酸盐、碳酸盐、碳化物、硼化物和氮化物的组中的一种或多种材料。尤其是,使用无机氧化物粒子已经获得了良好的结果。该无机氧化物可以是单一无机氧化物或混和的无机氧化物。优选的无机氧化物粒子是包含选自氧化铝、氧化锆和稀土元素的组中的一种或多种金属氧化物的粒子。此外,一种或多种无机氧化物可尤其选自氧化钛和氧化铁。碳酸钙为优选的碳酸盐。优选的硅酸盐粒子包括硅酸锆、粘土、滑石。无机粒子和胶凝剂通常分散在水性液体中,即,至少基本上由水组成的液体。优选地,除了胶凝剂之外,还使用分散剂。该分散剂有助于微粒在液体中的分散并且避免该粒子的絮凝。用于提供无机微粒,尤其是无机氧化物微粒的浆料的适合的分散剂和有效浓度通常是本领域已知的,并且包括阴离子表面活性剂,例如羧酸表面活性剂,如dolapixce64tm。可以使用阴离子聚电解质分散剂,例如聚(甲基)丙烯酸。可商购的聚甲基丙烯酸为darvanctm。无机粒子通常是微粒,尤其是具有最大直径的微粒,如通过沉淀确定为100μm或更小,优选0.1至30μm的微粒。微粒的d50优选小于2μm。微粒优选通过碾磨获得。在有利的实施方式中,将无机粒子的原料(具有比用于制备颗粒的微粒更大尺寸的典型粒子物)与水混和并碾磨以获得具有所需尺寸的微粒。单个微粒可由单一相或多个相组成。浆料可由相同材料形成的可被浆料化的微粒制成,例如不同材料的相同无机氧化物或粒子,例如不同的无机氧化物。优选地,至少50wt.%的无机粒子是金属氧化物粒子,更优选地60-95wt.%,尤其是75-90wt.%。优选地,余量的无机粒子由一种或多种硅酸盐、一种或多种碳酸盐、一种或多种碳化物或它们的组合形成。碳酸钙,即方解石,可尤其被用于提供钙。尤其是,利用包含α-氧化铝粒子的浆料已获得了良好的结果。氧化铝尤其有利于良好的硬度。在进一步有利的实施方式中,浆料另外还包含选自氧化锆粒子和硅酸盐粒子(例如滑石、长石、粘土和锆石)的组中的一种或多种粒子。尖晶石、钙长石、钇土和硅石也是可加入到浆料中的适合的无机粒子的实例。氧化锆是结晶氧化物,其具有作为主要金属元素的锆。氧化锆的若干结晶相是已知的,例如单斜氧化锆、立方氧化锆和四方氧化锆。除非另外具体说明,当本文中指代氧化锆时,其意指任意晶型的氧化锆。氧化锆粒子通常含有氧化铪(hfo2),其在大多数氧化锆矿物中以痕量天然存在,通常形成达到矿物的5wt.%,尤其是1wt.%至2wt.%。颗粒中的氧化锆在其结晶结构中可进一步包含一种或多种其他金属元素,例如一种或多种稀土金属氧化物,或选自氧化钙、氧化镁、氧化钽和氧化铌的组中的氧化物。它们可存在于用于制备颗粒的原料氧化锆中,或者在本发明的制备工艺过程中结合到氧化锆晶体结构中。氧化锆能够尤其有助于有利的刚性。而且,可以使用稀土氧化物或氧化钙、氧化镁、氧化钽、氧化铌的粒子,尤其是与氧化锆粒子组合使用。稀土氧化物或氧化钙、氧化镁、氧化钽、氧化铌的存在对于稳定氧化锆和减少单斜相的量是尤其有利的。优选的硅酸盐粒子为硅酸锆粒子。取决于温度和构成,硅酸锆可形成氧化锆或莫来石或含有二氧化硅的非晶相或其他相(取决于该组成中存在其他元素)。如果分别存在钙和镁,在烧结过程中也可以形成钙长石或尖晶石。不同类型的粒子的量可根据需要而不同,这取决于想要形成的陶瓷颗粒的组成。在一种具体的实施方式中,加入一定量的硬质相,如碳化物、硼化物、氮化物;如果使用的话,其量通常达到基于总无机物的45wt.%,尤其是0.5-25wt.%。该碳化物可尤其被用于增加硬度。适合的硬质相的实例为碳化钛、碳化硅、碳化钨、碳化钒、碳化铌、碳化钽、碳化锆、碳化铪、氮化硅、硼化钛和氮化钛。基于浆料的重量,浆料中的无机粒子的总浓度通常为40-80wt.%,尤其是50-75wt.%,更加尤其是55-70wt.%。可将胶凝剂与其他成分一起形成浆料或者将胶凝剂加入到无机粒子的预形成浆料中。优选地,在碾磨无机原材料之后再加入该胶凝剂。胶凝剂通常为聚合胶凝剂,其包含能够化学交联、光交联或热交联的官能团。优选地,该胶凝剂为阴离子聚合物。阴离子聚合胶凝剂是尤其优选的,因为其能够通过与多价阳离子(例如二价金属阳离子或三价阳离子)的相互作用胶凝化,从而在聚合物的两种阴离子基团之间形成(电价)交联。已经发现,可以使用多价阳离子而不会对颗粒性质造成不可接受程度的不利影响。至少在一些实施方式中,该多价阳离子以有利的方式有助于产品质量。用于交联阴离子胶凝剂的适合的多价金属离子包括多价过渡金属离子–尤其是锌、铁、铬、镍、铜或稀土元素(例如钇)的离子,以及碱土金属离子(例如钡或钙的离子)。能够与多价金属离子一起形成交联的聚合胶凝剂的阴离子基团的实例为羧酸根、烷氧基、膦酸根和磺酸根。优选地,阴离子多糖被用作胶凝剂,尤其是包含羧基的多糖。使用海藻酸盐已获得了尤其好的结果。胶凝剂以在胶凝反应介质中以有效引起胶凝化的浓度存在于浆料中,并且在该浓度下浆料保持流体(并且因此不会胶凝化)且可由其形成液滴。一般而言,当制备液滴时,浆料的粘度低于20,000mpa.s,尤其是在50-10,000mpa.s的范围内,更加尤其是在1,000-7,000的范围内,如以1.25s-1的剪切速率确定的。一般而言,胶凝剂的浓度通常在无机氧化物粒子总重量的0.2-5wt.%的范围内,优选在无机氧化物粒子总重量的0.3-3wt.%的范围内。然后,由浆料制备液滴。这可以本身已知的方式用喷嘴进行。可通过改变喷嘴尺寸来改变液滴尺寸,其通常在0.01至10mm的范围内。原则上可在胶凝化期间或胶凝化之后使液滴变形,即,当在没有施加外力的情况下液滴保持尺寸稳定,但仍会发生变形而不破坏液滴时,例如通过用压型器(stamp)等进行模制或压制使液滴变形。优选地,变形在胶凝化期间发生。尤其是,利用其中发生变形时液滴仍基本上保持流体的方法已获得了良好的结果。更加尤其是,利用其中液滴表面被胶凝化而液滴核为流体的方法已获得了良好的结果。将液滴引入到胶凝反应介质中。一个选择是将液滴注入到胶凝反应介质中。尤其是,利用其中远离胶凝反应介质形成液滴并且允许该液滴在其进入胶凝反应介质之前能够通过空气或其他气相下落,优选自由下落的方法已获得了良好的结果。优选地,该液滴随着其进入胶凝反应介质或者在胶凝反应介质中在胶凝反应介质的表面处或附近(通常在该表面的1cm之内)发生变形。该变形优选在已经发生实质胶凝化之前(即,当至少液滴的核仍基本为流体时)发生。这尤其被认为是为了获得具有带条纹的表面的颗粒的优点,例如图1.1所示。变形可以任何方式实现。该变形可以包括冲击(shock)处理或者机械变形,例如,可通过将液滴撞击到障碍物上或迫使其穿过变形设备(例如挤出机)来实现变形。该变形优选包括将液滴撞击到胶凝反应介质表面处或胶凝反应介质中存在的变形机构上。图6a(正视图)和图6b(侧视图)图示出了用于实施根据本发明方法的装置,其中该变形是通过撞击来实现的。在本文中,浆料通过喷嘴(2)从贮器(1)泵送,浆料的液滴能够从该喷嘴下落。变形机构优选包含用于接收下落液滴(3)的接收面。安排该接收面是为了使液滴变形。有利的是,该接收面包含穿孔(perforation)、凹陷(indentation)和/或凸起以使撞击到该接收面上的液滴发生变形。可进一步通过在胶凝反应介质中要胶凝化的穿孔来处理液滴(在图6中,该介质存在于池子4中)。或者,当存在少量凸起或者没有凸起时,可例如通过拍打动作(swipingaction)、通过震动或者通过接收面的倾斜从接收面除去液滴。有利的是,该接收面具有倾斜位置,即,该接收面被定位成相对于下落方向成一定角度,有利的是,该角度在大约10度至大约80度之间,更有利的是在大约20度至大约60度之间,并且更有利的是为大约40度。通过提供接收面的倾斜位置。通过穿孔下落的液滴可继续下落到胶凝反应介质中,其他液滴可借助于重力下落到接收面并且之后继续下落到胶凝反应介质中。在一种优选的实施方式中,该接收面为平面并且可以是板的上表面。在一种优选的实施方式中,变形机构选自格栅(grating)、网孔(mesh)、网格(grid)和倾斜板。网孔或格栅可基本上处于水平的或者是倾斜的。在一种实施方式中,倾斜板是打孔的。在一种优选的实施方式中,该倾斜板具有凸起(例如格栅)或者具有凹陷。变形的程度尤其受到速度的影响,在该速度下液滴与变形机构撞击。在其中液滴能够下落以产生与变形机构冲击的速度的方法中,能够通过在与该机构冲击之前调节液滴的下落距离或者通过调节液滴从喷嘴或其他喷射机构喷射的速度(流速)来容易地调整该冲击速度。液滴的胶凝化在液态胶凝反应介质中发生,通常是多价阳离子的水溶液,优选多价阳离子的无机盐在水中的溶液。含有多价阳离子的无机盐的浓度通常选自0.05-10wt.%的范围,优选在0.1-2wt.%的范围内。原则上,可以使用在给定条件下以所需浓度可溶的任何盐。尤其是,适合的盐包括无机盐,例如氯盐和硝酸盐。根据胶凝剂的类型(化学、热、光学)诱发胶凝化反应。如上文所述,优选借助于多价阳离子的阴离子聚合物的胶凝化。原则上,可以使用能够与聚合物的两个阴离子基团形成连接的任何阳离子,尤其是上文所述的任意阳离子。尤其是,使用含有钙离子的反应介质已经取得了良好的结果,尤其是在其中颗粒制成为包含氧化硅的实施方式中。包含氧化硅的颗粒中存在钙被认为有助于在颗粒中产生非晶相或者与降低优选的烧结温度以提供具有有利性质的陶瓷颗粒有关。降低烧结温度对于节约能源消耗是尤其有利的。进一步有利的是,不需要从胶凝化的液滴除去钙,并且因此能够省去胶凝化液滴的洗涤步骤。在胶凝反应介质中的停留时间通常为至少足以提供胶凝化的粒子,即,在不存在施加的外力的情况下尺寸稳定的粒子。停留时间可基于一般通用知识和本文中披露的信息常规地确定。如所指出的,对于其中使用阴离子胶凝剂和阳离子来引起胶凝化的方法,停留时间通常为至少5分钟,尤其是至少20分钟,更加尤其是至少30分钟。通常在一天内从反应介质除去胶凝化的粒子,尤其是在6小时内,有利的是在1小时内。将胶凝化的变形液滴干燥,通常在从反应介质分离之后;尤其是,在已利用阴离子聚合物作为胶凝剂和多价阳离子进行胶凝化的情况下。如果需要的话,用水洗涤该颗粒,例如除去在烧结过程中会反应形成氯的氯化物。在一种有利的实施方式中,在不洗涤胶凝化的变形液滴的情况下进行干燥。这样可以节约材料(水)、省时而且节能。干燥优选在从烧结步骤分离的方法步骤中进行。干燥通常是在低于用于烧结的高温炉中的温度下进行,尤其是因为这是更加有效的。干燥优选在低于100℃的温度下进行,尤其是在40℃至80℃之间的温度下进行,例如在空气中进行。优选进行干燥直至残余水含量少于5wt.%,尤其是约3wt.%或更少。烧结温度通常为在1200-1600℃的范围内。本发明的烧结的颗粒通常具有的尺寸范围为约0.5mm至约6mm,尤其是在约1至约5mm的范围内,更加尤其是1-3mm的范围内。优选地,10vol%或更少的多个根据本发明的颗粒的尺寸为0.7mm或更小。在现有技术中这部分颗粒也被称为‘d10’。更优选地,d10的范围为0.9-1.8mm,尤其是1.0-1.6。优选地,50vol%或更少多个根据本发明的颗粒的尺寸小于1.3mm。在现有技术中这部分颗粒被称为‘d50’。更优选地,d50的范围为1.3-2.2mm,尤其是1.4-2.0mm。优选地,90vol%或更少的多个根据本发明的颗粒的尺寸小于5mm。在现有技术中这部分颗粒也被称为‘d90’。更优选地,d90的范围为1.6-3mm,尤其是1.8-2.5mm。在一种具体的实施方式中,颗粒的d10为1.3-1.5,d50为1.6-1.8且d90为1.8-2.1,如通过所确定的。如本文中所使用的,d10、d50和d90是通过可确定的。如上文所述,该方法能够制备具有高尺寸均一性的颗粒,而不需对颗粒进行过筛。因此,颗粒的多分散性相对较低。根据本发明的均一性的测量值为d10与d90的比值。如果d10与d90之比在0.60:1至1:1的范围内,则该颗粒特别考虑为均一的。尤其是,本发明提供了(多个)颗粒,其中d10与d90之比在0.65:1至0.85:1的范围内,更加尤其是在0.70:1至0.80:1的范围内。原则上,本发明能够制备任何陶瓷前驱体材料的陶瓷颗粒。尤其是,已经发现本发明可用于提供包含氧化铝、氧化锆或二者的陶瓷氧化物。可采用任意范围的锆和铝(表示为其氧化物)的重量之比,尤其是在5:95至95:5,更加尤其是在20:80至90:10的范围内。使用这样的粒子已经取得了良好的结果,其中,锆和铝(一起考虑且表示为其氧化物)形成陶瓷组合物的70-100wt.%,优选77-98wt.%,更优选80-97wt.%。该颗粒的化学组成优选如下:-颗粒的铝含量(表示为al2o3)为30-95wt.%,更优选为35-90wt.%,更优选为50-90wt.%,尤其是55-85wt.%;更加尤其是60-80wt.%、65-80wt.%或70-80wt.%。-颗粒的锆含量(表示为zro2)通常为0-50wt.%,优选为7-40wt.%,更优选为10-30wt.%;尤其是10-25wt.%,更加尤其是12-20wt.%。在其中颗粒包含氧化锆和氧化铝的实施方式中,(一种或多种)其他组分的含量通常为0-30wt.%,尤其是3-20wt.%,更加尤其是5-20wt.%。在根据本发明的粒子中,除了锆和铝之外,尤其优选的元素为硅、稀土元素,尤其是钇和钙。如果存在的话,硅含量(表示为sio2)通常为1-15wt.%,尤其是4-10wt.%。如果存在的话,钙含量(表示为cao)通常为0.1-3wt.%,尤其是0.5-2wt.%。如果存在的话,总稀土金属含量(表示为氧化物)通常在0.1-6wt.%的范围内,尤其是0.3-5wt.%的范围内,更尤其是在0.5-3wt.%的范围内。尤其是,利用钇已经获得了良好的结果。如果存在的话,钇含量(表示为y2o3)通常为至少0.1wt.%,优选至少0.3wt.%,尤其是至少0.5wt.%,更尤其是至少0.6wt.%。通常,钇含量(表示为y2o3)为6wt.%或更少,优选5wt.%或更少,尤其是3wt.%或更少。另外的稀土元素(可选地存在的)为铈。如果存在的话,其含量通常小于5wt.%。优选地,铈含量为0-2wt.%,更优选0-1wt.%,更优选0-0.5wt.%。用基本上不含铈的陶瓷颗粒已获得了良好的结果。在一种实施方式中,烧结的陶瓷颗粒包含α-氧化铝(结晶相)和非晶相。如果存在的话,非晶相含量通常为颗粒的至少0.1wt.%,优选至少1wt.%,尤其是至少3wt.%。非晶相含量通常为80wt.%或更少,优选50wt.%或更少,尤其是30wt.%或更少,更加尤其是20wt.%或更少。在其中颗粒包含α-氧化铝的实施方式中,本发明的颗粒的α-氧化铝含量通常为至少5wt.%,优选至少10wt.%,更优选为14wt.%或更多,更优选为20wt.%或更多,尤其是30wt.%或更多,更加尤其是35wt.%或更多。在一种具体实施方式中,α-氧化铝的量为50wt.%或更多。α-氧化铝含量通常为90wt.%或更少,优选80wt.%或更少,尤其是75wt.%或更少,更加尤其是70wt.%或更少,更加尤其是61wt.%或更少。颗粒中存在氧化锆是有利的。其有助于陶瓷颗粒的刚性。然而,本发明能够以相对较低的氧化锆含量制备用于金属-陶瓷磨损部件中的具有令人满意的刚性的颗粒。氧化锆通常具有tqc比–即,[四方zro2+四方-’(prime)+立方氧化锆]的重量和除以[四方zro2+单斜zro2+四方-’(prime)zro2+立方氧化锆乘以100%]的重量和–在10-100%的范围内,尤其是25-100%,更加尤其是35-95%。莫来石相含量通常为80wt.%或更少,优选为50wt.%或更少,尤其是30wt.%或更少,更加尤其是25wt.%或更少,或20wt.%或更少。在一种具体实施方式中,莫来石相含量为9-17wt.%。尖晶石含量通常为0-5wt.%,尤其是0.1-4wt.%。在一种具体实施方式中,颗粒包含:-50-75wt.%,尤其是53-70wt.%,更加尤其是53-61wt.%的α-氧化铝;-5-25wt.%,尤其是10-20wt.%,更加尤其是11-17wt.%的氧化锆;-0-25wt.%,尤其是5-20wt.%,更加尤其是9-17wt.%的莫来石;-0-5wt.%,尤其是0.1-4wt.%的尖晶石;以及-0-25wt.%,尤其是0.1-15wt.%,更加尤其是1-10wt.%的非晶相。在此具体实施方式中,α-氧化铝、不同类型的氧化锆、莫来石和非晶相的总和优选形成颗粒的90-100wt.%,尤其是95-100wt.%。尤其是,利用由根据本发明的陶瓷结构制成的金属-陶瓷复合材料磨损部件已经在耐磨性方面获得了良好的结果,其以如下量(基于陶瓷总重量)包含铝、锆、硅、钇以及可选地钙:-铝含量(表示为al2o3)60-80wt.%,尤其是65-75wt.%-锆含量(表示为zro2)10-30wt.%;尤其是13-20wt.%-硅含量(表示为sio2)3-15wt.%,尤其是5-10wt.%-钇含量(表示为y2o3)0.3-6wt.%,尤其是0.5-3wt.%-钙含量(表示为cao)0-3wt.%,尤其是0.3-3wt.%-余量,由其他组分形成:0-5wt.%,尤其是0-1wt.%。制成磨损部件的陶瓷结构的晶体组成优选如下(至少在铸造之前;所有的量均是基于陶瓷的总重量):-50-70wt.%,尤其是53-61wt.%的α-氧化铝;-7-30wt.%,尤其是10-20wt.%,更加尤其是11-17wt.%的氧化锆(包括除锆之外的可形成部分氧化锆晶体结构的元素,例如hf和y);-5-20wt.%,尤其是9-17wt.%的莫来石;-1-40wt.%,尤其是5-30wt.%,更加尤其是10-20wt.%的非晶相。在该具体的实施方式中,α-氧化铝、氧化锆、莫来石、尖晶石和非晶相的总和优选形成颗粒的90-100wt.%,尤其是95-100wt.%。已经发现,这样的陶瓷-金属磨损部件在粉碎设备(例如研磨设备)中尤其具有良好的耐磨性。已发现本发明尤其适合提供具有(平均)球度(各向异性)–定义为最短投影尺寸比最长投影尺寸–在0.65-0.9的范围内,尤其是在0.70-0.80的范围内,更加尤其是在0.71-0.77的范围内的颗粒,如通过所确定的。优选地,根据本发明的烧结的陶瓷颗粒的密度为3-6kg/l,由维氏(vickers)压痕在98n确定的硬度为900-1600。烧结的颗粒尤其用于制备能够用于金属-陶瓷复合材料的陶瓷相的开孔的陶瓷结构。该陶瓷结构是由通过粘结剂粘合的陶瓷颗粒的三维互联网络形成的开孔的陶瓷结构,其中该颗粒的堆积体在颗粒之间具有开孔,该孔可由液态金属填充。图5示出了根据本发明的陶瓷结构的实例。在一种有利的实施方式中,该开孔的陶瓷结构包含供给通道,其与该孔相连接,允许该孔经由该供给通道被液态金属填充。通过在陶瓷结构中提供供给通道,存在更多的通向陶瓷结构的入口,并因此向孔供应液态金属以填充这些孔。而且,当供给通道在陶瓷结构中作为凹陷提供时,其与颗粒的接触面积以及因此通向孔的入口数量相比于没有供给通道的结构更大,从而液态金属能够更深地填充这些孔并因此使其能够更深补强到陶瓷结构的核中,并且可能朝向面向模制表面的陶瓷结构的表面越过核。有利的是,供给通道是贯通通道,其能够从两侧填充该陶瓷结构,从而增加液态金属的渗透深度和/或减少用液态金属填充该孔的时间。提供供给通道的一种有利的实施方式是将颗粒围绕一个或多个柱状或锥形开放空间(其起到供给通道的作用以使液态金属流入到该陶瓷结构的孔中)安排成蜂巢状结构。该供给通道可以具有圆的(圆形、椭圆)或多边形横截面。该供给通道与孔流体连通,允许液态金属能够从供给通道进入到孔中。陶瓷结构能够以本身已知的方式制造,例如,在ep-a930948中所描述的。在有利的实施方式中,颗粒以用于陶瓷结构的预期形状排布并且与粘结剂粘合。颗粒通常涂布有粘结剂在水或其他液体中的分散体。在排布颗粒之后,通常进行干燥步骤从而使液体蒸发并且粘结剂在颗粒之间形成紧密粘合(solidbond)。粘结剂优选为无机粘结剂。适合的无机粘结剂通常选自水玻璃、矿物粘土、沸石、硅酸钠和硅酸铝。尤其是,使用硅酸钠已经获得了良好的结果,这在与氧化铝粉末组合使用时是有利的。本发明的颗粒,尤其是包含本发明颗粒的陶瓷结构尤其适合用于制备陶瓷-金属复合材料,例如金属-陶瓷磨损部件。陶瓷-金属复合材料能够以本身已知的方法制备,优选通过经典制造或离心铸造来制备,例如epa930948中所描述的。在一种优选的实施方式中,金属为铁,优选为其合金。尤其是,优选为含白铬铁(whitechromiumiron)和马氏体钢(martensiticsteel)。在另外的实施方式中,金属为铝。本发明进一步涉及在材料尤其是地质材料的粉碎(减少)方面使用根据本发明的金属-陶瓷复合材料磨损部件。要经过根据本发明的粉碎过程的优选材料选自石灰石、煤、矿石、油砂、水泥、混凝土、石油焦、生物质、熔渣和集料的组中。根据本发明的粉碎设备优选选自破碎机、冲击机和磨的组中,尤其是选自卧式轴式破碎机、立式轴式冲击机和立式磨的组中。在一种具体的实施方式中,磨损部件为卧式破碎机的锤头。根据本发明的材料粉碎能够以本身已知的方式进行。在一种具体的实施方式中,磨损部件为研磨切割工具的磨损部件,由根据本发明的陶瓷颗粒或开孔的陶瓷结构制成。在一种具体的实施方式中,由本发明的颗粒或陶瓷结构制成的陶瓷金属复合材料为复合装甲。在一种具体的实施方式中,由本发明的颗粒或陶瓷结构制成的陶瓷金属复合材料为挖泥泵的磨损部件。在一种具体的实施方式中,本发明的颗粒用来提供柔性涂层研磨料制品(砂纸)。具体实施方式现在将通过以下实施例来举例说明本发明。对比例通过熔融、淬火然后破碎制造的批次陶瓷颗粒可商购自saint-gobain(ce),其包含:75wt.%氧化铝和23wt.%氧化锆(包括hfo2)。参考例1使用ep930948的方法提供颗粒。其具有如下组成:实施例1颗粒制备如下(条件为室温,通常为约20-30℃,除非另外具体说明)。制备具有如下组成的金属氧化物粒子和硅酸盐粒子的原料混合物。制备该原料混合物在水中的浆料。水中含有约1wt.%的分散剂dolapixce64tm。原料的含量为约72wt.%。浆料中的粒子在磨碎机(attritor)中碾磨,直至获得浆料,其中粒子的d50为约0.6μm。基于该浆料的总干重,将5wt.%的胶凝剂(海藻酸钠)水溶液加入到浆料中,以获得含有约0.7wt.%海藻酸盐和约65wt.%无机粒子的浆料。将所得到的浆料通过喷嘴(3mm孔径)泵送,该喷嘴位于胶凝反应介质(0.3wt.%脱水氯化钙的水溶液)上方10cm高处。反应池中存在胶凝介质,其中提供有在其上表面上具有网格的倾斜板,浆料液滴冲击该上表面。该板部分浸没于液体介质中,以使下落的液滴冲击在该板上并且能够滑入该液体介质中。在约1小时后从反应介质除去胶凝的粒子,并在热空气(高达80℃)中干燥直至残余水含量为约1%。将干燥的粒子烧结。下表中示出了烧结后的颗粒组成。颗粒的化学组成wt.%al2o375zro2(+hfo2)15.5y2o31.5sio27.5cao0.5在下表中示出了烧结温度和保压时间。用来确定所产生的颗粒(ex1)和对比颗粒(ce)样品的粒径分布(d10、d50、d90)和球度。颗粒的硬度如下通过由维氏(vickers)压痕以49n负载确定(astmc1327)确定。可通过x-射线衍射(xrd)来确定晶体组成,基于理论单个衍射谱和和不同结晶相的原子结构通过衍射图谱的重构(rietveld方法)。下表中示出了结果。1已经利用rietveld方法通过向样品中添加已知量的参考结晶材料(石英)测量了非晶相。用颗粒来制作整个颗粒的双目视照片(图1.1)、抛光截面的光学显微镜图像(图2.1)以及电子显微镜图像(图3.1,比例尺为10μm;图4.1;比例尺为10μm)。由对比例的颗粒制成的对比图像(分别为图1.2、图2.2、图3.2和图4.2)。在通过以下程序蚀刻该颗粒之后,制作电子显微镜图像:对包埋在树脂基质中的颗粒进行镜面抛光。从树脂除去一些颗粒,然后在电炉中进行热蚀刻(在空气下,以低于烧结温度50℃至100℃的温度)。发白的部分为氧化锆。较深色部分为氧化铝/莫来石/尖晶石/钙长石/非晶相。实施例23d-开孔的陶瓷结构(具有图5中示出的结构)由实施例1、2和参考例1(每种类型的粒子两种结构)的颗粒制成。程序如下:将颗粒与包含硅酸钠、氧化铝粉末和水的4wt.%的矿物胶混和。将颗粒和胶一起倒入所需设计的模具中。将该模具和内容物加热到100℃直至所有的水都被蒸发。然后从模具去除该陶瓷结构。实施例3如下制造陶瓷金属磨损部件(立式轴式冲击机的叶轮):将根据实施例2获得的陶瓷结构单个置于砂模中,将液态金属倒在该结构上并使其冷却。实施例4对以根据本发明(ex1)的颗粒制成的叶轮对和以参考例的颗粒制备的叶轮对进行称重,并且之后将其安装在同一台立式轴式冲击机破碎机上,以确保所有的叶轮在相同条件下进行测试。该破碎机用来破碎斑岩石(porphyrystone)。在操作19小时以及2,470公吨破碎材料之后,拆下叶轮并再次称重。根据本发明的叶轮具有明显可见的更小磨损。而且,重量损失的比较表明根据本发明的叶轮的磨损降低了15%。实施例5用于制备vsi破碎机的砧的两个3d-开孔的陶瓷结构由基于如实施例1中所述的方法制备的颗粒制成。颗粒具有以下组成:如下制备陶瓷结构:将颗粒与包含硅酸钠、氧化铝粉末和水的4wt.%的矿物胶混和。将颗粒和胶一起倒入所需设计的模具中。将该模具和内容物加热到100℃直至所有的水都被蒸发。然后从模具去除该陶瓷结构。参考例2使用ep930948的方法提供颗粒。其具有如下组成:利用相同的方法,使用参考例的颗粒制备与实施例5具有相同设计的两种陶瓷结构。实施例6根据实施例5的陶瓷结构和参考例2的陶瓷结构,制备陶瓷金属磨损部件(用于立式轴式冲击机的砧)如下:将陶瓷结构单个置于砂模中,将液态金属(铁合金)倒在该结构上并使其冷却。另外两个砧由具有相同冶金学组成的金属制成,而不是陶瓷的(全金属砧)。将全部六个砧称重并且然后将其安装在vsi破碎机的同一环上,以确保所有的砧在相同条件下进行测试。该破碎机用于粉碎河砾石。在操作60小时之后,除去砧并且再次称重。在此测试中,对于以来自参考例1的颗粒制备的砧,相比于全金属砧,没有观察到其在耐磨性方面的改进。然而,显著地观察到以根据本发明的颗粒(实施例4)制成的砧更少被磨损。而且,重量损失的比较表明根据本发明的砧的磨损比参考例的砧或全金属砧低50%。当前第1页12