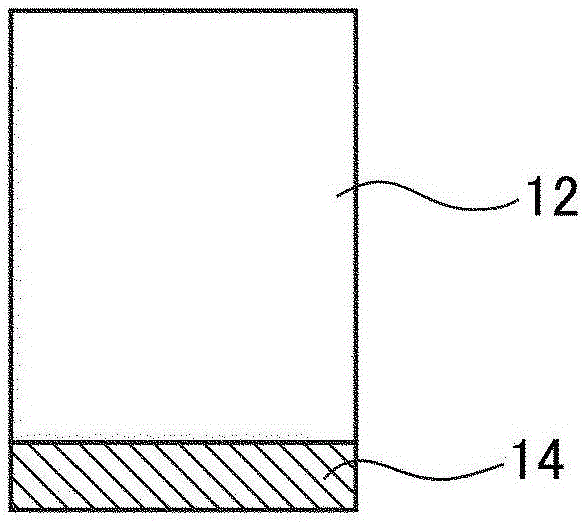
本公开涉及SiC单晶及其制造方法。
背景技术:
:SiC单晶在热学、化学方面非常稳定、机械强度优异、耐放射线方面强,而且与Si单晶相比具有高的绝缘击穿电压、高的热导率等优异的物理性质。因此,可实现Si单晶和GaAs单晶等现有半导体材料不能实现的高输出、高频、耐电压、耐环境性等,作为可进行大电力控制和节能的功率器件材料、高速大容量信息通信用器件材料、车载用高温器件材料、耐放射线器件材料等这样宽范围的新一代半导体材料的期待正在高涨。以往,作为SiC单晶的生长方法,代表性的已知有气相法、艾奇逊(Acheson)法和溶液法。在气相法中,例如在升华法中,虽然具有在生长的单晶中易于产生被称作微管缺陷的中空贯穿状的缺陷、层叠缺陷等晶格缺陷和多晶型等的缺点,但在以往,SiC块状单晶大多通过升华法制造,也进行了减少生长晶体的缺陷的尝试。在艾奇逊法中,由于使用硅石和焦炭作为原料并在电炉中进行加热,因此,因原料中的杂质等而不可能得到结晶性高的单晶。而且,溶液法为如下方法:在石墨坩埚中形成Si熔液或熔化了Si以外的金属的Si熔液,使C溶解到该熔液中,使SiC晶体层在设置于低温部的晶种基板上析出从而生长。由于溶液法与气相法相比进行在接近热平衡的状态下的晶体生长,因此最能期待低缺陷化。因此,最近,提出了一些基于溶液法的SiC单晶的制造方法(专利文献1)。现有技术文献专利文献专利文献1:日本特开2014-234342号公报技术实现要素:发明所要解决的课题但是,在专利文献1等的以往技术中,有时在生长晶体的整体中产生裂纹,或产生多晶。关于裂纹,虽然即使在距生长晶体的侧面1mm左右的范围的侧面端部产生裂纹也能允许,但有时在生长晶体的整体中产生裂纹从而生长晶体会破裂。已知的是,晶种基板与晶种保持轴之间的热膨胀差为裂纹产生的原因。另外已知的是,如果晶种基板的顶面的外形大于晶种保持轴的端面的外形,则晶种基板的顶面(被晶种保持轴保持的面)的外周部不与晶种保持轴的端面相接,自其非接触部的辐射热损失变多,在生长晶体中可能产生多晶。因此,期望不含多晶、除侧面端部外不含裂纹的SiC单晶。用于解决课题的手段本公开以SiC单晶的制造方法为对象,该制造方法是使保持于晶种保持轴的下端面的晶种基板与配置在坩埚内的具有从内部向液面温度降低的温度梯度的Si-C溶液接触从而使SiC单晶晶体生长的SiC单晶的制造方法,其中,晶种基板的顶面具有与晶种保持轴的下端面的整个面相接而被保持的中央部、和不与晶种保持轴的下端面相接的外周部,该制造方法包括:在晶种基板的顶面配置碳片材,使得覆盖中央部和外周部中的至少外周部。本公开还以SiC单晶为对象,该SiC单晶不含多晶,除侧面端部外不含裂纹,具有30mm以上的直径,并且通过X射线衍射法测定时的晶体取向的偏差为0.22°以下/50mm。发明效果根据本公开,可得到不含多晶、除侧面端部外不含裂纹的SiC单晶。附图说明图1是表示可用于本公开的方法的SiC单晶制造装置的一例的截面示意图。图2是晶种基板及具有与晶种基板相同直径的晶种保持轴的截面示意图。图3是晶种基板及具有小于晶种基板的直径的晶种保持轴的截面示意图。图4是晶种基板的顶面被碳片材覆盖的晶种基板及具有小于晶种基板的直径的晶种保持轴的截面示意图。图5是晶种基板的顶面的外周部被碳片材覆盖的晶种基板及具有小于晶种基板的直径的晶种保持轴的截面示意图。图6是示出从铅直方向上方观察时的晶种基板的顶面的外形与晶种保持轴的端面的外形的大小的关系的示意图。图7是被具有大于晶种基板的顶面的外形的碳片材覆盖的晶种基板及具有小于晶种基板的直径的晶种保持轴的截面示意图。图8是形成于晶种基板与Si-C溶液之间的弯液面的截面示意图。图9是基于实施例1的条件进行的Si-C溶液的温度梯度的模拟结果。图10是基于比较例2的条件进行的Si-C溶液的温度梯度的模拟结果。图11是基于比较例4的条件进行的Si-C溶液的温度梯度的模拟结果。附图标记说明100单晶制造装置10坩埚12晶种保持轴14晶种基板15晶种基板的中央部16晶种基板的外周部17生长晶体18隔热材料19生长晶体的生长面处的外形22高频线圈22A上段高频线圈22B下段高频线圈24Si-C溶液26石英管30碳片材34弯液面具体实施方式在本说明书中,(000-1)面等的表达中的“-1”是将原本在数字上方赋予横线而表达之处表达为“-1”。以往,在基于溶液法的SiC单晶的生长中,使用如图2所示那样的具有相同直径的晶种保持轴和晶种基板。图2是晶种保持轴12和具有与晶种保持轴12相同直径的晶种基板14的截面示意图。晶种基板14的顶面保持于晶种保持轴12的下端面。本发明人发现,如果使用如图2所示那样的具有相同直径的晶种保持轴和晶种基板,则由于晶种保持轴和晶种基板的热膨胀系数的不同,在生长晶体的整体中可能产生裂纹。特别地,还发现在为了使大口径的晶体生长而使用大直径的晶种基板的情况下,在生长晶体的整体中裂纹变得容易产生。而且,本发明人还发现,如果如图3所示的那样,使用具有小于晶种基板14的直径的直径的晶种保持轴12,则虽然可抑制在生长晶体的整体中产生那样的裂纹的发生,但在生长晶体中也可能产生多晶。图3是晶种保持轴12及具有大于晶种保持轴12的直径的晶种基板14的截面示意图。晶种基板14的顶面的中央部与晶种保持轴12的下端面的整个面相接而被保持。发现了如果如图3所示的那样,使用具有小于晶种基板14的顶面的直径的直径的端面的晶种保持轴12,则仅晶种基板14的顶面(被晶种保持轴保持的面)的中央部15与晶种保持轴12的下端面的整个面相接而被保持,晶种基板14的顶面的外周部16不与晶种保持轴12的下端面相接,自该外周部16(非接触部)的辐射热损失变多,晶种基板14的生长面附近的Si-C溶液的温度梯度变得过大,从而在生长晶体中可能产生多晶。在本申请中,将晶种基板的与晶种保持轴的下端面的整个面相接而被保持的部分称作中央部或接触部,将晶种基板的不与晶种保持轴的下端面相接的部分称作外周部或非接触部。本发明人基于上述认识发现,如果如图4和图5所示的那样,以成为非接触部的外周部不露出的方式在晶种基板14的顶面配置碳片材30,则能抑制在生长晶体中产生多晶。图4是晶种保持轴12、具有大于晶种保持轴12的直径的晶种基板14及配置于晶种基板14的顶面的中央部和外周部的碳片材30的截面示意图。在图4中,碳片材30配置于晶种基板14的顶面,顶面被碳片材30覆盖的晶种基板14保持于晶种保持轴12的下端面。图5是晶种保持轴12、具有大于晶种保持轴12的直径的晶种基板14及配置于晶种基板14的顶面的外周部的碳片材30的截面示意图。在图5中,碳片材30配置于晶种基板14的顶面的外周部上,晶种基板14保持于晶种保持轴12的下端面。碳片材30可以如图4所示那样,以介于晶种基板14的顶面与晶种保持轴12的下端面之间的方式配置,或者也可以如图5所示那样,具有在中央部具有穿过晶种保持轴的孔且仅覆盖晶种基板14的外周部的圆环(donut)形状。本公开以SiC单晶的制造方法为对象,该制造方法是使保持于晶种保持轴的下端面的晶种基板与配置在坩埚内的具有从内部向液面温度降低的温度梯度的Si-C溶液接触从而使SiC单晶晶体生长的SiC单晶的制造方法,其中,晶种基板的顶面具有与晶种保持轴的下端面的整个面相接而被保持的中央部、和不与晶种保持轴的下端面相接的外周部,该制造方法包括:在晶种基板的顶面配置碳片材,使得覆盖中央部和外周部中的至少外周部。根据本公开的制造方法,由于晶种基板14的顶面的成为非接触部的外周部被碳片材30覆盖,因此可减小自外周部的辐射热损失,故可得到不含多晶、除侧面端部外不含裂纹的SiC单晶。理所当然的是,只要晶种基板14的顶面的成为非接触部的外周部基本上被碳片材覆盖,就包含在本申请发明的范围内。本公开的SiC单晶的制造方法使用溶液法。溶液法是指使SiC晶种基板与具有从内部向表面(液面)温度降低的温度梯度的Si-C溶液接触,从而使SiC单晶生长的SiC单晶的生长方法。通过形成从Si-C溶液的内部向溶液的表面温度降低的温度梯度,使Si-C溶液的表面区域过饱和,以与Si-C溶液接触的晶种基板为基点,可使SiC单晶生长。图1中示出可用于本公开的制造方法的SiC单晶制造装置的截面示意图的一例。图示的SiC单晶制造装置100具备收容了C在Si或Si/X(X为Si以外的一种以上的金属)的熔液中溶解而成的Si-C溶液24的坩埚10,形成从Si-C溶液的内部向溶液的液面温度降低的温度梯度,将配置有碳片材30的晶种基板14保持于可在铅直方向升降的晶种保持轴12的下端面,使晶种基板14与Si-C溶液24接触,从而能以晶种基板14为基点使SiC单晶生长。作为晶种基板14,能使用通常可用于SiC单晶的制造的品质的SiC单晶作为晶种基板。例如,能使用通过升华法通常制作的SiC单晶作为晶种基板,晶种基板可以为板状、圆盘状、圆柱状、棱柱状、圆锥台状或棱锥台状等的任意形状。晶种保持轴12为在其端面保持晶种基板14的轴,可以为石墨轴,可具有圆柱状、棱柱状等的任意形状。可使用具备这样的下端面的晶种保持轴12,该下端面具有小于晶种基板14的顶面的面积的面积。优选地,如图6所示,当从铅直方向上方观察时,以晶种保持轴12的端面的外形全部进入晶种基板14的顶面的外形的内部的方式使晶种基板14的顶面保持于晶种保持轴12的下端面。晶种基板优选具有圆盘形状,晶种保持轴优选具有圆柱形状。在晶种基板具有圆盘形状、晶种保持轴具有圆柱形状时,晶种基板的直径优选为30mm以上,与晶种保持轴的轴方向垂直的方向的截面的直径(以下也称作晶种保持轴的直径)优选为25mm以下。在晶种基板的直径为30mm以上的情况下,如果晶种保持轴的直径与晶种基板的直径相同,则将晶种基板保持于晶种保持轴时的晶种基板的变形变大,但通过使晶种保持轴的直径为25mm以下,可减小因晶种基板与晶种保持轴的热膨胀差而产生的晶种基板的变形,可抑制在生长晶体的整体中产生那样的裂纹的发生。即使以30mm以上的范围增大晶种基板的直径,只要将晶种保持轴的直径设为25mm以下即可。晶种保持轴的直径的下限只要能保持晶种基板就不特别限定,但例如可设为5mm以上。晶种基板的直径的上限不特别限定,但例如可设为300mm以下。通过使圆盘形状的晶种基板的直径为30mm以上且使圆柱形状的晶种保持轴的直径为25mm以下,可得到30mm以上的大口径且变形小的SiC生长晶体,优选地,可得到从生长面通过X射线衍射法测定时的晶体取向的偏差为每50mm小于0.30°、优选0.22°以下、更优选0.17°以下、进一步优选0.11°以下的SiC生长晶体。晶体取向的偏差优选为通过衍射谱g=11-28或11-20而得到的相对晶体取向。由于这样的晶体取向的偏差小的SiC单晶的变形小,因此可抑制在所生长的SiC单晶的整体中产生那样的裂纹的发生,即使在晶体生长后进行切割等加工也不易产生裂纹和破裂。在本公开中,只要能抑制在所生长的SiC单晶的整体中产生那样的裂纹的发生即可,虽然仅在生长晶体的侧面端部产生那样的裂纹是可允许的,但优选也抑制了生长晶体的侧面端部处的裂纹的产生。在本申请中,侧面端部是指距生长晶体的侧面1mm以内的范围的端部区域。生长晶体的直径优选为30mm以上,更优选为40mm以上,进一步优选为45mm以上。生长晶体的直径的上限不特别限定,但例如为400mm以下。图5是本公开的方法中的保持晶种基板14的晶种保持轴12的一个实施方式的截面示意图。将碳片材30配置于晶种基板的顶面,使得覆盖保持于晶种保持轴12的下端面的晶种基板14的顶面的中央部以及不与晶种保持轴12的下端面相接的晶种基板14的顶面的外周部中的至少外周部。通过这样配置碳片材30,可减小来自晶种基板14的成为非接触部的外周部的辐射热损失。碳片材30可具有与晶种基板14的顶面的外形相同的外形,或大于晶种基板14的顶面的外形的外形。图7中示出顶面被具有大于晶种基板14的顶面的外形的外形的碳片材被覆的晶种基板14及具有小于晶种基板14的直径的晶种保持轴12的截面示意图。如图7所示,碳片材30优选具有大于晶种基板14的顶面的外形的外形,以覆盖晶种基板14的顶面的中央部和外周部的全部的方式配置于晶种基板的顶面。碳片材30更优选具有与所晶体生长的SiC单晶17的生长面处的外形19相同的外形或大于该外形19的外形,覆盖晶种基板14的顶面的中央部和外周部的全部,且当从铅直方向上方观察时,以覆盖所晶体生长的SiC单晶17的生长面处的外形19整体的方式配置于晶种基板14的顶面。在碳片材30具有大于晶种基板14的顶面的外形的外形的情况下,碳片材30与晶种基板的直径相比,具有优选大3~30mm、更优选大5~20mm、进一步优选大7~15mm的直径。碳片材30也可以由多个层构成,例如也可以在具有与晶种基板14的顶面相同的外形的碳片材上配置具有大于晶种基板14的外形的外形的碳片材。可使用粘接剂将碳片材30分别粘接并固定于晶种保持轴12的下端面及晶种基板14的顶面。使晶种基板14经由碳片材30保持于晶种保持轴12的下端面也可使用粘接剂来进行。在使晶种基板14经由碳片材30与晶种保持轴12接合时,与使晶种基板14直接保持于晶种保持轴12相比,能稳定且容易地保持晶种基板14,因此优选以碳片材30介于晶种基板14的顶面与晶种保持轴12的下端面之间的方式进行配置。粘接剂优选为碳粘接剂。作为碳粘接剂,可举出例如酚类粘接剂和环氧类粘接剂。也可以将由粘接剂构成的粘接层或以粘接剂为主要成分的粘接层配置于碳片材30的两面,构成粘接层/碳片材30/粘接层的层结构。作为碳片材30,只要能减小自晶种基板的外周部的辐射热损失就不特别限定,可使用市售的碳片材。碳片材例如可通过将碳纤维经历辊子以脱水来得到。由于碳片材具有柔软性,因此即使将碳片材粘接并固定于晶种基板的顶面,也不会使晶种基板或生长晶体产生变形,也能减小自晶种基板的成为非接触部的外周部的辐射热损失,也能抑制在生长晶体的整体中产生那样的裂纹的发生并抑制在生长晶体中产生多晶。虽然也可以使用在中央部具有用于穿过晶种保持轴的孔的石墨环等隔热材料来代替碳片材,但如果将石墨环等隔热材料粘接于晶种基板,则由于有时在晶种基板或生长晶体中产生变形,因此优选碳片材。已知的是,生长晶体有时从端部产生裂纹,特别是在进行30mm以上的大口径的晶体生长时,易于从生长晶体的侧面(端部)产生裂纹。认为是由于生长晶体的侧面易于被冷却。碳片材30具有与生长晶体的口径相同的面积或大于生长晶体的口径的面积,由此生长晶体的侧面被保温从而可抑制生长晶体的侧面处的裂纹的产生。碳片材的厚度只要是可得到抑制自外周部的辐射热损失的效果的厚度即可,可以例如为0.01mm以上、0.05mm以上或0.2mm以上。碳片材的厚度的上限不特别限定,但可以为例如10mm以下、5mm以下或1mm以下。Si-C溶液是指以Si或Si/X(X为Si以外的一种以上的金属)的熔液作为溶剂的C溶解而成的溶液。X为一种以上的金属,只要能与SiC(固相)形成在热力学上成为平衡状态的液相(溶液)就不特别限定。作为适合的金属X的例子,可举出Ti、Mn、Cr、Ni、Ce、Co、V、Fe等。Si-C溶液优选具有包含Si及Cr的组成。在Si-C溶液具有包含Si及Cr的组成的情况下,以按原子组成百分率计Si/(Si+Cr)=30~80%的熔液作为溶剂的Si-C溶液因C的溶解量的变动少而优选。例如,在坩埚内除了加入Si,还装入Cr等,可形成Si-Cr溶液等。通过使C溶解在将原料装入坩埚、使其加热融化而制备的Si或Si/X的熔液中来制备Si-C溶液24。通过将坩埚10设为石墨坩埚等的碳质坩埚或SiC坩埚,C因坩埚10的溶解而溶解在熔液中,可形成Si-C溶液。这样,在Si-C溶液24中不存在未溶解的C,可防止由SiC单晶在未溶解的C上的析出而引起的SiC的浪费。C的供给例如可以利用烃气的吹入或者将固体的C供给源与熔液原料一起投入等的方法,或者可以将这些方法与坩埚的溶解组合。为了保温,用隔热材料18覆盖坩埚10的外周。可以将它们一并收容在石英管26内。在石英管26的外周配置了高频线圈22作为加热装置。高频线圈22可以由上段线圈22A和下段线圈22B构成,上段线圈22A和下段线圈22B可各自独立地控制。由于坩埚10、隔热材料18、石英管26和高频线圈22成为高温,因此配置在水冷腔室的内部。为了可调整装置内的气氛,水冷腔室具备气体导入口和气体排出口。Si-C溶液24的温度通常因辐射等而形成与Si-C溶液24的内部相比表面的温度低的温度分布,但进一步地,通过调整高频线圈22的圈数及间隔、高频线圈22与坩埚10的高度方向的位置关系以及高频线圈22的输出,可在Si-C溶液24中以晶种基板14接触的溶液上部成为低温、溶液下部(内部)成为高温的方式形成垂直于Si-C溶液24的表面的方向的温度梯度。例如,使上段线圈22A的输出小于下段线圈22B的输出,可在Si-C溶液24中形成溶液上部成为低温、溶液下部成为高温的温度梯度。在Si-C溶液24中溶解的C通过扩散和对流而被分散。通过加热装置的输出控制、自Si-C溶液24表面的散热以及经由晶种保持轴12的热损失等,晶种基板14的底面附近形成了与Si-C溶液24的内部相比成为低温的温度梯度。在高温且溶解度大的溶液内部溶入的C在到达低温且溶解度低的晶种基板附近时成为过饱和状态,可以以该过饱和度为驱动力使SiC晶体在晶种基板14上生长。晶种基板14与Si-C溶液的接触可通过如下进行:使在下端面保持有晶种基板14的晶种保持轴12向着Si-C溶液24的液面下降,使晶种基板14的底面相对于Si-C溶液面24平行并使其与Si-C溶液24接触。然后,可将晶种基板14相对于Si-C溶液24的液面保持在规定位置以使SiC单晶生长。晶种基板14的保持位置可以是晶种基板14的底面的位置与Si-C溶液面一致,或可以相对于Si-C溶液面位于下侧,或者可以相对于Si-C溶液面位于上侧,但如图8所示,优选晶种基板的底面的位置相对于Si-C溶液面位于上方,使得仅使Si-C溶液24润湿晶种基板14的底面以形成弯液面34。图8是形成于晶种基板14与Si-C溶液24之间的弯液面34的截面示意图。在形成弯液面的情况下,优选将晶种基板的底面的位置相对于Si-C溶液面保持在上方0.5~3mm的位置。在将晶种基板的底面相对于Si-C溶液面保持在上方位置的情况下,一旦使晶种基板与Si-C溶液接触以使Si-C溶液与晶种基板的底面接触之后,提拉至规定位置。这样,通过形成弯液面以使晶体生长,由此使Si-C溶液不与晶种保持轴接触,可更容易地防止多晶的产生。在本公开的方法中,Si-C溶液的表面温度的下限优选为1800℃以上,上限优选为2200℃,在该温度范围内可增多C在Si-C溶液中的溶解量。Si-C溶液的温度测定可使用热电偶、辐射温度计等来进行。关于热电偶,从高温测定和防止杂质混入的观点考虑,优选在石墨保护管中放入了被覆有氧化锆或氧化镁玻璃的钨-铼线的热电偶。在一个实施方式中,在SiC单晶的生长前,可进行使晶种基板的表面层溶解在Si-C溶液中而除去该表面层的回熔。在使SiC单晶生长的晶种基板的表层有时存在位错等的加工变质层、自然氧化膜等,在使SiC单晶生长前将它们溶解并除去对于使高品质的SiC单晶生长是有效的。溶解的厚度根据晶种基板的表面的加工状态而变化,但为了充分地除去加工变质层和自然氧化膜,优选为约5~50μm。回熔可通过如下进行:在Si-C溶液中形成从Si-C溶液的内部向溶液的表面温度增加的温度梯度,即形成与SiC单晶生长反方向的温度梯度。可通过控制高频线圈等加热装置的输出来形成上述反方向的温度梯度。在一个实施方式中,也可以在预先加热晶种基板之后使晶种基板与Si-C溶液接触。如果使低温的晶种基板与高温的Si-C溶液接触,则有时在晶种中产生热冲击位错。在使晶种基板与Si-C溶液接触前预先加热晶种基板,对于防止热冲击位错并使高品质的SiC单晶生长是有效的。晶种基板的加热可与加热晶种保持轴一同进行。在该情况下,在使晶种基板与Si-C溶液接触后、在使SiC单晶生长前停止晶种保持轴的加热。另外,代替该方法,也可以在使晶种与较低温的Si-C溶液接触之后,将Si-C溶液加热至使晶体生长的温度。在该情况下,对于防止热冲击位错并使高品质的SiC单晶生长也是有效的。本公开还以SiC单晶为对象,该SiC单晶不含多晶、除侧面端部外不含裂纹,具有30mm以上的直径,并且通过X射线衍射法测定时的晶体取向的偏差为每50mm小于0.30°、优选0.22°以下、更优选0.17°以下、进一步优选0.11°以下。晶体取向的偏差优选为通过衍射谱g=11-28或11-20得到的相对晶体取向。本公开中的SiC单晶优选在侧面端部也不含裂纹。在本公开中,侧面端部是指距生长晶体的侧面1mm以内的范围。本公开中的SiC单晶具有优选30mm以上、更优选40mm以上、进一步优选45mm以上的直径。生长晶体的直径的上限不特别限定,但例如为400mm以下。实施例(实施例1)准备通过升华法制作的SiC单晶,其是直径为40mm、厚度为500μm的圆盘状4H-SiC单晶,底面具有(000-1)面,用作晶种基板。准备直径为12mm、长为40cm的圆柱形状的石墨轴作为晶种保持轴。准备厚度为0.2mm、外形形状具有与晶种基板相同直径40mm的圆形形状的碳片材30(巴工业制,GRAFOIL(注册商标))。如图4示意性地所示,使用苯酚类碳粘接剂将碳片材30粘接于晶种基板的顶面,使得完全覆盖晶种基板的顶面。进而,使用苯酚类碳粘接剂将晶种保持轴的下端面粘接于被覆了碳片材30的晶种基板的顶面的中央部。使用图1中示出的单晶制造装置100,在收容Si-C溶液的石墨坩埚10中按原子组成百分率计以Si:Cr=60:40的比例装入Si/Cr作为熔液原料。在将单晶制造装置100的内部抽真空至1×10-3Pa之后,导入氩气直至成为1个大气压,用氩置换单晶制造装置100的内部的空气。对配置于石墨坩埚10的周围的作为加热装置的高频线圈22通电以通过加热将石墨坩埚10内的原料熔化,形成Si/Cr合金的熔液。然后,使足够量的C从石墨坩埚10溶解到Si/Cr合金的熔液中,形成Si-C溶液24。调节上段线圈22A及下段线圈22B的输出来加热石墨坩埚10,使Si-C溶液24的表面处的温度升温至2000℃,并且进行控制使得在距Si-C溶液24的表面1cm范围内从溶液内部向溶液表面温度降低的平均温度梯度成为30℃/cm。利用辐射温度计进行Si-C溶液24的表面的温度测定,Si-C溶液24的温度梯度的测定使用可在铅直方向移动的热电偶来进行。使与晶种保持轴12粘接的晶种基板14的底面与Si-C溶液24的液面平行,并将晶种基板14的底面的位置配置在与Si-C溶液24的液面一致的位置,从而进行使晶种基板的底面与Si-C溶液接触的籽晶接触(seedtouch),接着将晶种保持轴12和晶种基板14提拉0.5mm以形成弯液面,在该位置保持15小时以使晶体生长。晶体生长结束后,使晶种保持轴12上升,冷却至室温,从Si-C溶液24和晶种保持轴12切离并回收晶种基板14以及以晶种基板为基点生长的SiC晶体。得到的生长晶体具有直径45mm和厚度1.0mm。得到的生长晶体的直径为生长面的直径(以下同样)。从生长面对得到的生长晶体进行显微镜拍照,结果可知,没有产生多晶,得到了SiC单晶。但是,在生长晶体的侧面端部确认出了裂纹。通过X射线衍射法(リガク制,XRT-200CCM)对生长晶体的生长面进行测定,结果,通过g=11-28衍射得到的相对晶体取向的偏差为0.11°/50mm。(实施例2)除了将晶体生长时间设为20小时以外,在与实施例1同样的条件下使SiC晶体生长并回收。得到的生长晶体具有直径49mm和厚度4.0mm。从生长面对生长晶体进行显微镜拍照,结果可知,没有产生多晶,得到了SiC单晶。但是,在生长晶体的侧面端部确认出了裂纹。通过X射线衍射法对生长晶体的生长面进行测定,结果,通过g=11-28衍射得到的相对晶体取向的偏差为0.22°/50mm。(实施例3)除了使用厚度为0.2mm且具有直径50mm的圆形形状的碳片材30(巴工业制,GRAFOIL(注册商标))以外,在与实施例1同样的条件下使SiC晶体生长并回收。得到的生长晶体具有直径46mm和厚度1.0mm。从生长面对生长晶体进行显微镜拍照,结果可知,没有产生多晶,在包括侧面端部的生长晶体的整体中没有看到裂纹,得到了良好的SiC单晶。通过X射线衍射法对生长晶体的生长面进行测定,结果,通过g=11-28衍射得到的相对晶体取向的偏差为0.17°/50mm。(比较例1)使用通过升华法制作的SiC单晶作为晶种基板,该SiC单晶是直径为30mm、厚度为500μm的圆盘状4H-SiC单晶,底面具有(000-1)面,使用直径为30mm、长度为40cm的圆柱形状的石墨轴作为晶种保持轴,并且不使用碳片材,除此以外,在与实施例1同样的条件下使SiC晶体生长并回收。得到的生长晶体具有直径42mm和厚度3.6mm。从生长面对生长晶体进行显微镜拍照,结果可知,在生长晶体的整体中产生了裂纹。通过X射线衍射法对生长晶体的生长面进行测定,结果,通过g=11-28衍射得到的相对晶体取向的偏差为1.3°/50mm。(比较例2)使用通过升华法制作的SiC单晶作为晶种基板,该SiC单晶是直径为40mm、厚度为500μm的圆盘状4H-SiC单晶,底面具有(000-1)面,使用直径为40mm、长度为40cm的圆柱形状的石墨轴作为晶种保持轴,并且不使用碳片材,除此以外,在与实施例1同样的条件下使SiC晶体生长并回收。得到的生长晶体具有直径40mm和厚度4.0mm。从生长面对生长晶体进行显微镜拍照,结果可知,没看到多晶的产生,但在生长晶体的整体中产生了裂纹。(比较例3)使用通过升华法制作的SiC单晶作为晶种基板,该SiC单晶是直径为50mm、厚度为500μm的圆盘状4H-SiC单晶,底面具有(000-1)面,使用直径为50mm、长度为40cm的圆柱形状的石墨轴作为晶种保持轴,并且不使用碳片材,除此以外,在与实施例1同样的条件下使SiC晶体生长并回收。得到的生长晶体具有直径52mm和厚度3.0mm。从生长面对生长晶体进行显微镜拍照,结果可知,没看到多晶的产生,但在生长晶体的整体中产生了裂纹。(比较例4)除了不使用碳片材以外,在与实施例1同样的条件下使SiC晶体生长并回收。得到的生长晶体具有直径44mm和厚度3.0mm。从生长面对生长晶体进行显微镜拍照,结果可知,在生长晶体的侧面端部看到了裂纹,也看到了多晶的产生。通过X射线衍射法对生长晶体的生长面进行测定,结果,通过g=11-28衍射得到的相对晶体取向的偏差为0.12°/50mm。(比较例5)使用通过升华法制作的SiC单晶作为晶种基板,该SiC单晶是直径为30mm、厚度为500μm的圆盘状4H-SiC单晶,底面具有(000-1)面,使用直径为25mm、长度为40cm的圆柱形状的石墨轴作为晶种保持轴,并且不使用碳片材,除此以外,在与实施例1同样的条件下使SiC晶体生长并回收。得到的生长晶体具有直径45mm和厚度3.1mm。从生长面对生长晶体进行显微镜拍照,结果可知,在生长晶体的侧面端部看到了裂纹,也看到了多晶的产生。通过X射线衍射法对生长晶体的生长面进行测定,结果,通过g=11-28衍射得到的相对晶体取向的偏差为0.21°/50mm。在表1中汇总了实施例1~3和比较例1~5的晶体生长条件。表1在表2中汇总了实施例1~3和比较例1~5中得到的生长晶体的直径、有无裂纹、有无多晶化及面取向的偏差。表2(Si-C溶液的温度梯度的模拟)基于实施例1、比较例2和比较例4的条件,使用CGSim(自溶液的块状晶体生长模拟软件,STRJapan制,Ver.14.1)对通过溶液法(Flux法)使SiC单晶生长时的Si-C溶液的温度梯度进行模拟。对于实施例1和比较例4,晶种基板的外周部的正下方且在距晶种基板的生长面1mm下的范围内的Si-C溶液中的铅直方向的温度梯度进行模拟,对于比较例2,晶种基板的中央部的正下方且在距晶种基板的生长面1mm下的范围内的Si-C溶液中的铅直方向的温度梯度进行模拟。在图9~11和表3中示出基于实施例1、比较例2和比较例4的条件进行的Si-C溶液的温度梯度的模拟结果。图9~11和表3中示出的数值对实施例1和比较例4而言,是显示了晶种基板的外周部之处的水平方向范围内最大值的温度梯度,对比较例2而言,是显示了晶种基板的中央部之处的水平方向范围内最大值的温度梯度。确认了对于实施例1得到的外周部正下方的Si-C溶液的温度梯度与在比较例4的条件下得到的外周部的正下方的Si-C溶液的温度梯度相比,小约30%;与在比较例2的条件下得到的中央部的正下方的温度梯度相同。表3温度梯度(℃/cm)实施例10.8比较例20.8比较例41.1当前第1页1 2 3