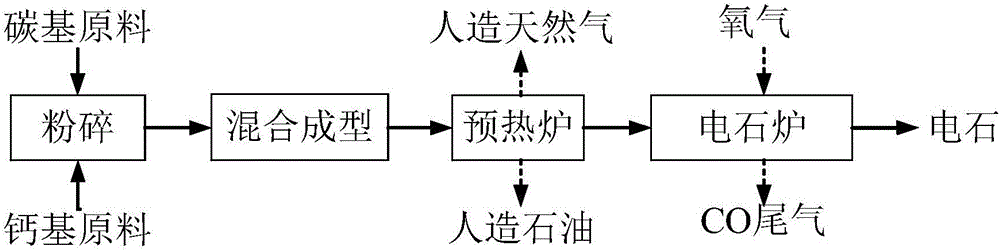
本实用新型涉及电石生产
技术领域:
,尤其涉及一种电石的制备系统。
背景技术:
:电石的生产方法有氧热法和电热法两种,目前工业上一般采用电热法生产电石,即焦炭(C)和氧化钙(CaO)在电石炉内,采用固定床依靠电弧高温(>2000℃)熔化反应而生成电石,电热法制备电石的特点是采用块状原料进料和利用电能生产电石,它存在反应速率慢、反应时间长、反应温度高,耗电量大,电石产量低、粉尘和尾气治理困难的问题。正是由于传统电石生产技术存在“高投入、高污染、高电耗”的缺点,不符合节能减排和可持续发展的要求,因此发展受限。氧热法是在氧的存在下使部分碳发生燃烧,产生的高温热量使剩余碳和钙发生反应生成电石,该法由于具有反应时间短、反应温度低、污染小的优点逐渐被重视。但是氧热法由于采用碳基原料燃烧供热,难免产生大量的灰,这不仅增加能耗而且会降低电石品质。在电热法电石炉中,灰分每增加一个百分点,电耗增加50度。技术实现要素:本实用新型期望提供一种电石的制备系统,能降低生产能耗和灰分引入。本实用新型实施例的技术方案是这样实现的:本实用新型实施例提供了一种电石的制备系统,该系统包括:原料预处理单元、送料装置、预热炉、高温输送装置以及电石炉;其中,所述原料预处理单元包括依次相连的破碎装置、混合装置和成型装置;所述破碎装置设有碳基原料入口和钙基原料入口,所述成型装置的出口与所述送 料装置的进口连通;所述送料装置的出口与所述预热炉入口相连通;所述预热炉设有固体物料出口和油气出口,固体物料出口与高温输送装置相连;所述高温输送装置出口与所述电石炉的高温固体物料入口连通;所述电石炉设有所述高温固体物料入口、氧气入口、电石出口和炉气出口,所述高温固体物料入口与所述固体物料出口相连,产品电石由所述电石出口导出,电石反应过程中产生的气体由所述炉气出口导出。上述方案中,所述预热炉为辐射管转底炉。上述方案中,所述氧气入口为氧枪接入口,位于所述电石炉的中部和/或底部。上述方案中,所述破碎装置包括气流研磨单元,用于将碳基原料和钙基原料分别进行细磨。上述方案中,所述成型装置包括:预压螺旋和对辊成型机,所述混合装置混合得到的混合物料经过所述预压螺旋预压后在所述对辊成型机中成型。上述方案中,所述高温输送装置包括:密封保温罐;或密封保温链板。上述方案中,所述送料装置为螺旋送料装置。本实用新型技术方案的有益效果在于:采用最优的氧气和碳材的配比,使 其不完全燃烧为系统提供热源同时又保证了系统的还原气氛,提高了能源利用效率;采用辐射管转底炉预热系统,实现了低阶煤的分级利用,同时降低了后续电石炉的碳材消耗量,最大限度的减少灰分引入;通过控制反应原料的粒度来降低反应温度,达到最优的反应状态。附图说明图1为本实用新型提供的电石的制备系统的组成结构示意图;图2为本实用新型提供的电石的制备方法的工艺流程示意图。具体实施方式为了更清楚地说明本实用新型实施例和技术方案,下面将结合附图及实施例对本实用新型的技术方案进行更详细的说明,显然,所描述的实施例是本实用新型的一部分实施例,而不是全部实施例。基于本实用新型的实施例,本领域普通技术人员在不付出创造性劳动的前提下所获得的所有其他实施例,都属于本实用新型保护的范围。图1为本实用新型提供的电石的制备系统的组成结构示意图,如图1所示,该制备系统包括:原料预处理单元1、送料装置2、预热炉3、高温输送装置4以及电石炉5;其中,原料预处理单元1包括依次相连的破碎装置11、混合装置12和成型装置13;所述成型装置13的出口与所述送料装置2的进口连通;送料装置2的出口与所述预热炉3入口相连通;预热炉3设有固体物料出口32和油气出口31,固体物料出口32与高温输送装置4相连;高温输送装置4出口与所述电石炉5的高温固体物料入口连通;电石炉5设有所述高温固体物料入口、氧气入口53和54、电石出口51和炉气出口52,所述高温固体物料入口与所述固体物料出口相连,产品电石由所 述电石出口51导出,电石反应过程中产生的气体由所述炉气出口52导出。进一步的,上述方案中,所述预热炉3为辐射管转底炉。进一步的,上述方案中,所述氧气入口为氧枪接入口,位于所述电石炉的中部和/或底部,即如图1所示,电石炉5设有氧枪中部接入口53和氧枪底部接入口54。进一步的,上述方案中,所述破碎装置11包括气流研磨单元,用于将碳基原料和钙基原料分别进行细磨。进一步的,上述方案中,所述成型装置13包括:预压螺旋和对辊成型机,所述混合装置混合得到的混合物料经过所述预压螺旋预压后在所述对辊成型机中成型。进一步的,上述方案中,所述高温输送装置4包括:密封保温罐;或密封保温链板。进一步的,上述方案中,所述送料装置2为螺旋送料装置。图2为本实用新型提供的电石的制备方法的工艺流程示意图,即图1所示的电石制备系统使用的工艺流程,如图2所示,该方法包括:破碎装置将碳基原料和钙基原料进行细磨,分别得到碳基原料粉末和钙基原料粉末;混合装置将含有所述碳基原料粉末和所述钙基原料粉末的混合物与粘结剂进行混合、润磨处理,得到混合物料;成型装置将所述混合物料进行成型处理,得到物料团;送料装置将所述物料团送入预热炉中进行热解,得到热解气、焦油和高温固体物料;将所述高温固体物料经过高温输送装置送至电石炉中;向所述电石炉中通入氧气,使碳材燃烧提供热量进行电石冶炼,得到电石产品和电石炉气。具体的工艺流程如下:1、将碳基原料和钙基原料进行细磨,从而可以得到粒径为0.074mm以下碳基原料粉末和粒径为0.074mm以下的钙基原料粉末。经实践验证,当二者的粒径降低到0.074mm以下时,碳化钙的起始生成温度降至1450℃,且在1850℃可以达到其最大的反应速率,通过将碳基原料和钙基原料进行细磨处理,得到超细粒级物料,可以增加物料比表面积和接触面积,进而显著降低冶炼过程还原反应活化能,从而使得还原反应可以在较低的温度下进行,由此可以显著提高电石生产效率,并且显著降低电石生产成本。2、混合成型,将以上的粉料在混料器中加入特定的成型剂混合均匀,经过预压螺旋预压后在对辊成型机中成型,得到一定粒度的型球。型球粒度可以在5~35mm之间。经实践验证,型球粒度在15mm左右时,在炉料透气性、物料传热传质方面是最优的,粒度过小会影响炉料的透气性,过大会影响物料间的传热,导致反应时间加长,降低电石反应速率。3、预热处理,根据本实用新型的实施例,陆续将上述得到的物料球团向辐射管转底炉内进行布料,随着转底炉炉底的运转,物料球团在辐射管热解炉腔内进行预热处理,在炉腔内1100℃~1400℃下,最终得到煤气、焦油和固体球料。经实践验证,在辐射管转底炉中预热处理,不仅可以得到煤气和煤焦油,同时高温固体物料热送至电石炉,可以显著提高反应物料活性,降低电石炉碳耗和氧耗,减少灰分对电石品质的影响。4、电石炉,上述得到的1200℃以上的球料直接热送至电石炉,在炉底同时通入氧气,通过和碳材反应提供热量,使钙基原料和碳基原料反应生成电石, 同时副产大量的高温CO气体。经实践验证,通过控制氧气、碳基原料和钙基原料的配比(质量比0.3~0.5:1.5:1),可以使其反应环境始终保持在还原气氛中,而且又不会有碳基原料和钙基原料的剩余。根据本实用新型电石的制备方法,通过将碳基原料和钙基原料进行细磨处理,得到超细粒级物料,可以增加物料比表面积和接触面积,进而显著降低冶炼过程反应活化能,从而提高电石生产效率。同时采用辐射管式转底炉对物料球团(此球团包括碳基原料、钙基原料和添加剂)进行预热处理,不仅可以得到干净的煤气和煤焦油,同时避免了传统氧热法直燃煤引进系统的灰分,在提高产品附加值的同时又不给后续电石冶炼增加负担。另外,高温固体产物直接热送至电石炉,减少电石炉中碳材的消耗,有效避免了灰分在电石中残留。实施例1采用气流磨将粒度在5mm以下的长焰煤以及生石灰分别进行细磨干燥处理,分别得到粒径低于0.07mm~0.05mm的颗粒占90%以上的长焰煤粉末和生石灰粉末,其中,长焰煤工业分析如表1所示,生石灰(CaO)含量为92%,然后将长焰煤粉末和生石灰粉末经气体输送至配料罐中,按照重量比为,生石灰粉末:长焰煤粉末=0.6:1进行混合,将混合的粉料气体输送至成型单元进行成型,得到粒径15×5×10mm的球团,直接由皮带转运到辐射管转底炉炉顶的料仓,采用振动布料机向转底炉炉底进行布料,布料厚度为20mm,然后随着转底炉炉底的旋转,物料球团在辐射管转底炉腔内在1200摄氏度下进行预热处理30分钟,并且利用预热炉腔内的油气回收装置回收煤气、煤焦油和高温固体球团,高温固体球团经过高温热送装置送入电石炉中,通过炉底的氧气喷枪喷入氧气,通过碳材与氧气不完全燃烧放热,在最佳反应温度1850℃下反应,得到电石产品和高热值CO尾气。对电石产品取5批样品(每批样品50g)在LJD碳化钙发气量测定装置上按照国标测量发气量,发气量范围在300~310L/kg之间,达到优质电石标准。表1长焰煤工业分析(wt%)水分(Mad)灰分(Aad)挥发分(Vad)固定碳(Cad)5.075.8029.3059.83对比例与采用传统氧热法的对比,以及与之前的超细粉热解加传统电石炉的结果对比,用数据证明有益效果。传统氧热法生产电石,由于电石反应所需热量全部由碳、氧燃烧提供,电石反应炉中吨电石所需燃料碳量要比本工艺高15%以上,相应的多引进灰分到电石产品中,降低电石发气量。本工艺比传统氧热法生产的电石产品发气量高5%~10%以上。与超细粉加传统电石炉相比,本工艺没有电石炉的高电耗,而是采用碳材不完全燃烧放热生产电石。碳材不完全燃烧相当于碳气化,其热效率可达80%以上;我国电大部分采用煤电,其热效率仅在40%左右;提供相同热量情况下,本工艺可以少耗标煤25%以上。再次说明,以上所述仅为本实用新型的实施例,并非因此限制本实用新型的专利范围,凡是利用本实用新型说明书及附图内容所作的等效结构或等效流程变换,例如各实施例之间技术特征的相互结合,或直接或间接运用在其他相关的
技术领域:
,均同理包括在本实用新型的专利保护范围内。当前第1页1 2 3