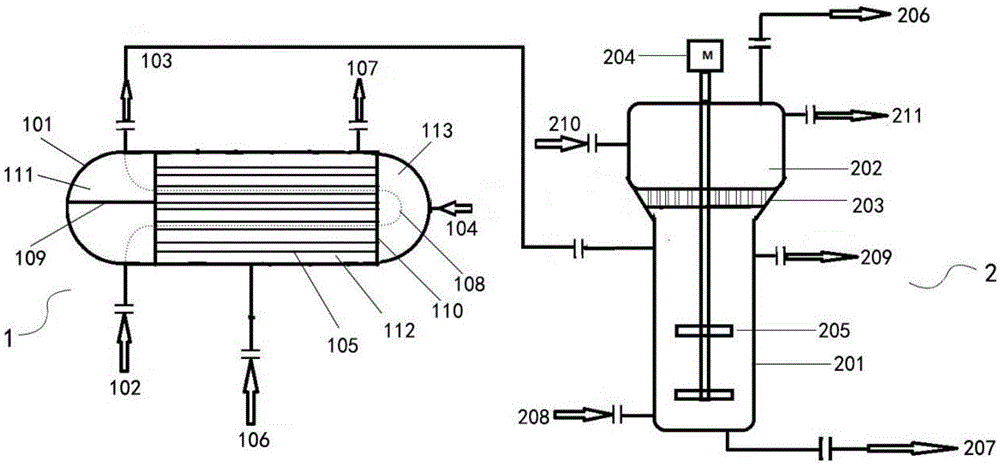
本发明涉及聚合反应领域,具体地,涉及一种用于制备轻烃交替共聚微球的反应装置及制备轻烃交替共聚微球的方法。
背景技术:
:聚合物的生产一般包括原料处理、催化剂单元、聚合、分离及回收利用等单元,在这诸多单元中,聚合单元是其中较为核心和重要的单元,聚合单元直接决定了聚合反应的运行和所得聚合产物的质量。不同于小分子反应,聚合反应有其自身的特殊性,诸如反应过程粘度的升高,反应过程伴随较为强烈的放热等。通常聚合反应器应该满足以下普适性工艺要求:能有效的去除反应的聚合热,较好的控制聚合反应温度;提供反应物料必要的停留时间;提供必要的物料混合条件,保证反应器内浓度分布较为均匀;操作费用较低等。通常情况下,聚合反应器按反应方法可分为悬浮聚合反应器、淤浆聚合反应器、乳液聚合反应器、溶液聚合反应器和本体聚合反应器,按反应器的结构形式可以分为搅拌釜式反应器、管式反应器、塔式反应器及流化床反应器等。随着聚合反应技术的进步,聚合反应器的结构和形式变得越来越复杂(合成橡胶工业,1994,17(1):47-51)。通常情况下,生产不同聚合物的反应器有其特定性。生产聚合物颗粒的反应器通常有间歇搅拌反应釜、螺带式搅拌反应釜、环管式反应器等(合成橡胶工业,1994,17(5):299-303),这些聚合反应器在不同的聚合物生产中,其结构差别通常较大(合成橡胶工业,1995,18(2):114-117)。开发新的聚合物生产工艺,通常需要进行新的反应器设计,以满足特定聚合反应的控制要求。针对通过马来酸酐与c2-4不饱和烃的自稳定沉淀聚合反应得到特定性质的反应产物,现有技术中没有公开相关的反应装置和反应方法。技术实现要素:本发明的目的是为了克服现有技术的存在上述的问题,提供一种用于制备轻烃交替共聚微球的反应装置及制备轻烃交替共聚微球的方法,该反应装置具有能够提高反应的转化率,并且能够控制轻烃交替共聚微球的形态。为了实现上述目的,本发明一方面提供一种用于制备轻烃交替共聚微球的反应装置,该反应装置包括反应器和气液分离器;所述反应器包括:反应器壳体,两个导流挡板,其设置在反应器壳体内部,将反应器壳体的内部分割为二者之间的换热腔和两侧的第一反应腔和第二反应腔,多根中空的导流管,其平行设置在所述两个导流挡板之间,且两端开口分别开口于第一反应腔和第二反应腔,折流挡板,其设置在所述第一反应腔的内部,将所述第一反应腔分割为上部反应腔和下部反应腔;物料第一导入口,其设置在所述第一反应腔的下部反应腔上,物料第二导入口,其设置在第二反应腔上,物料导出口,其设置在所述第一反应腔的上部反应腔上,以及物料通道,其为依次连接物料第一导入口、第一反应腔的下部反应腔、第二反应腔、第一反应腔的上部反应腔和物料导出口的物料通路;其中,所述物料第二导入口位于所述物料通道全长的40-60%处;所述反应器通过物料导出口与所述气液分离器连接。优选地,所述换热腔上还设置有控温介质导入口和控温介质导出口,以及设置在所述换热腔的内部且位于所述导流管外部的控温介质腔。优选地,所述气液分离器包括壳体,所述壳体被具孔挡板分为位于上部的气体区和位于下部的气液分离区,所述气体区连接气体导出口,所述气液分离区的上部与物料导出口连接,下部设置有液体导出口,内部设置有搅拌部件。优选地,所述气体区外部设置有降温部件,所述气液分离区的外部设置有升温部件。本发明第二方面提供一种利用上述本发明的反应装置制备轻烃交替共聚微球的方法,该方法包括如下步骤:(1)在物料第一导入口将含有c2-4不饱和烃、马来酸酐和引发剂的混合物导入到反应器使得物料在所述物料通道中进行第一聚合反应,在物料第二导入口将二乙烯基苯导入到反应器使得物料在所述物料通道中进行第二聚合反应,并从物料导出口导出反应产物;(2)将所述反应产物导入气液分离器进行气液分离。优选地,所述c2-4不饱和烃包括1-丁烯、异丁烯、1,3-丁二烯、1,2-丁二烯、乙烯基乙炔、顺2-丁烯和反2-丁烯中的一种或多种。优选地,所述混合物中还包括c2-4烷烃。优选地,所述c2-4烷烃包括正丁烷和/或异丁烷。优选地,所述c2-4不饱和烃和c2-4烷烃包括1-丁烯1-99重量%、异丁烯1-99重量%、1,3-丁二烯0-99重量%、1,2-丁二烯0-50重量%、正丁烷0-99重量%、异丁烷1-99重量%、乙烯基乙炔5-20重量%、顺2-丁烯0-99重量%和反2-丁烯1-99重量%。优选地,所述c2-4不饱和烃和c2-4烷烃包括1-丁烯0.1-2重量%、异丁烯10-30重量%、1,3-丁二烯0.01-0.1重量%、正丁烷0.5-5重量%、异丁烷30-40重量%、顺2-丁烯20-40重量%、反2-丁烯5-20重量%。优选地,所述c2-4不饱和烃和c2-4烷烃包括1-丁烯5-15重量%、异丁烯0.5-3重量%、正丁烷20-30重量%、顺2-丁烯15-30重量%、反2-丁烯35-45重量%。优选地,所述引发剂为过氧化二苯甲酰、过氧化二异丙苯、过氧化二特丁基、过氧化十二酰、过氧化苯甲酸特丁酯、过氧化二碳酸二异丙基酯、过氧化二碳酸二环己酯、偶氮二异丁腈和偶氮二异庚腈中的一种或多种。优选地,所述引发剂为偶氮二异丁腈和/或过氧化二苯甲酰。优选地,在所述混合物中,马来酸酐的含量为5-25重量%,优选为10-20重量%。优选地,所述c2-4不饱和烃中的端烯烃、马来酸酐与二乙烯基苯的摩尔比为1:0.8-7:0.008-0.07。优选地,所述混合物包括有机溶剂。优选地,所述有机溶剂为有机酸烷基酯、烷烃、芳香烃和卤代芳香烃中的一种或多种。优选地,所述有机酸烷基酯为甲酸甲酯、甲酸乙酯、甲酸丙酯、甲酸丁酯、甲酸异丁酯、甲酸戊酯、乙酸甲酯、乙酸乙酯、乙酸丙酯、乙酸丁酯、乙酸异丁酯、乙酸仲丁酯、乙酸戊酯、乙酸异戊酯、乙酸苄酯、丙酸甲酯、丙酸乙酯、丙酸丁酯、丁酸甲酯、丁酸乙酯、丁酸丁酯、丁酸异丁酯、丁酸异戊酯、异戊酸异戊酯、苯甲酸甲酯、苯甲酸乙酯、苯甲酸丙酯、苯甲酸丁酯、苯甲酸异戊酯、苯乙酸甲酯和苯乙酸乙酯中的一种或多种。更优选地,所述有机酸烷基酯为乙酸异戊酯。优选地,所述烷烃为丙烷、正丁烷、异丁烷、正戊烷、异戊烷、正己烷、异己烷、环己烷、正庚烷、正辛烷和异辛烷中一种或多种。优选地,所述芳香烃为苯、甲苯和二甲苯中一种或多种。优选地,所述卤代芳香烃为氯苯和/或溴苯。优选地,所述反应器中的反应条件包括:第一共聚反应时间为0.5-3h,第二共聚反应时间为0.5-3h。优选地,第一共聚反应时间为1-2h,第二共聚反应时间为1-2h。优选地,反应温度为50-100℃,反应压力为0.2-2mpa。优选地,反应温度为70-90℃,反应压力为0.5-1mpa。优选地,所述搅拌部件的转速为5-100rpm。优选地,该方法还包括将所述液相产物进行固液分离;优选地,所述固液分离的方式为离心。通过上述技术方案,本发明的用于制备轻烃交替共聚微球的反应装置和制备轻烃交替共聚微球的方法能够实现马来酸酐与c2-4不饱和烃的自稳定沉淀聚合,实现反应热的有效去除,精确控制反应温度,实现对停留时间的有效要求,控制反应物的浓度分布,最终生产出均匀的超细聚合物粉末,并且能够有效提高反应的转化率。附图说明图1是本发明的用于制备轻烃交替共聚微球的反应装置的结构示意图。附图标记说明1、反应器2、气液分离器101、反应器壳体102、物料第一导入口103、物料导出口104、物料第二导入口105、导流管106、控温介质导入口107、控温介质导出口108、物料通道109、折流挡板110、导流挡板111、第一反应腔112、换热腔113、第二反应腔201、气液分离区202、气体区203、具孔挡板204、电机205、搅拌部件206、气体导出口207、液体导出口208、升温介质导入口209、升温介质导出口210、冷却介质导入口211、冷却介质导出口具体实施方式在本文中所披露的范围的端点和任何值都不限于该精确的范围或值,这些范围或值应当理解为包含接近这些范围或值的值。对于数值范围来说,各个范围的端点值之间、各个范围的端点值和单独的点值之间,以及单独的点值之间可以彼此组合而得到一个或多个新的数值范围,这些数值范围应被视为在本文中具体公开。在本发明中,在未作相反说明的情况下,使用的方位词如“上、下、左、右”通常是指附图中的上、下、左、右。例如上部反应腔和下部反应腔中的“上”“下”仅表示附图中的上方和下方。所述压力均为表压。本发明提供一种用于制备轻烃交替共聚微球的反应装置,如图1所示,该反应装置包括反应器1和气液分离器2;所述反应器1包括:反应器壳体101,两个导流挡板110,其设置在反应器壳体101内部,将反应器壳体101的内部分割为二者之间的换热腔112和两侧的第一反应腔111和第二反应腔113,多根中空的导流管105,其平行设置在所述两个导流挡板110之间,且两端开口分别开口于第一反应腔111和第二反应腔113,折流挡板109,其设置在所述第一反应腔111的内部,将所述第一反应腔111分割为上部反应腔和下部反应腔;物料第一导入口102,其设置在所述第一反应腔111的下部反应腔上,物料第二导入口104,其设置在第二反应腔113上,物料导出口103,其设置在所述第一反应腔111的上部反应腔上,以及物料通道108,其为依次连接物料第一导入口102、第一反应腔111的下部反应腔、第二反应腔113、第一反应腔111的上部反应腔和物料导出口103的物料通路;其中,所述物料第二导入口104位于所述物料通道108全长的40-60%处;所述反应器1通过物料导出口103与所述气液分离器2连接。在本发明中,通过适当地设置物料第二导入口104的位置,可以在恰当的反应阶段添加反应物,从而控制交替共聚反应的进行;通过在所述换热腔112的内部导入控温介质,可以方便地调节本发明的反应器中的反应温度,控制反应的进行。因此利用本发明的反应器可以方便地进行马来酸酐与c2-4不饱和烃的共聚反应,得到粒径为200-2000nm(优选600-1500nm)、颗粒形状均匀的轻烃交替共聚微球。根据本发明,所述物料第二导入口104的位置可以配合反应器使用的反应条件适当调节,优选位于所述物料通道108全长的42-58%处,更优选为45-55%。图1中的物料通道108仅为示出物料的可能流动方式之一,物料可以在全部的导流管105中流动。在本发明中,所述导流挡板110、所述折流挡板109的设置方式和设置位置没有特别的限定,只要能够达到分离液流的目的即可。如图1所示,所述反应器壳体101水平设置,所述导流挡板110和所述折流挡板109均垂直设置。在本发明中,所述导流管105用于控制反应在适当的温度下进行,其长度、数量和直径可以根据反应适当设置。优选地,所述导流管105的长度为反应器壳体101长度的60-90%,优选为65-75%。优选地,所述导流管105的数量为4根以上,优选为10根以上,直径为20-90cm,优选为30-60cm。通过如上设置流挡板110、所述折流挡板109和所述导流管105,延长了反应物料在反应器中的反应时间,并在导流管105中以适当的温度进行反应,同时可以保证物料与通过物料第二导入口104添加的物料均匀混合,使得反应物料在反应器1中稳定反应。在本发明中,所述反应器壳体101能够提供所需的交替共聚反应条件即可,例如可以采用现有的用于聚合反应的反应器壳体。优选地,所述反应器壳体101为夹套结构,其内部也可以通入上述控温介质,从而进一步便于对反应物料进行温度控制。根据本发明的一个优选的实施方式,所述换热腔112上还设置有控温介质导入口106和控温介质导出口107,以及设置在所述换热腔112的内部且位于所述导流管105外部的控温介质腔。根据本发明,所述换热腔112中可以导入控温介质,从而调节反应器1中的反应温度。所述控温介质的通入方式没有特别的限定,从便于控制反应温度的角度考虑,如图1所示,例如可以将换热腔112的一侧连接控温介质导入口106,另一侧连接控温介质导出口107,并通过控温介质导入口106导入控温介质,使控温介质填充所述控温介质腔,与导热管105内部的物料充分换热,调节反应器内部的反应物料的温度。优选控温介质的流动方向与物料的流动方向相同。作为本发明中的控温介质,可以采用现有的用于调节反应物温度的任意介质,为适当温度的温水等。在本发明中,所述气液分离器2只要能够完成反应器1中的反应产物的气液分离即可,其实施方式没有特别的限定。例如可以使反应产物降压降温,从而使气体液体分离即可。根据本发明的一个优选的实施方式,所述气液分离器2包括壳体,所述壳体被具孔挡板203分为位于上部的气体区202和位于下部的气液分离区201,所述气体区202连接气体导出口206,所述气液分离区201的上部与物料导出口103连接,下部设置有液体导出口207,内部设置有搅拌部件205。所述具孔挡板203用于阻挡搅拌导致的液体喷溅,从而保证液体不进入气体区202,所述具孔挡板203例如可以为不锈钢制具孔挡板。根据本发明,所述搅拌部件205部件例如可以采用搅拌桨,如图1所示,所述搅拌部件205在电机204的带动下旋转,所述电机例如可以设置在气液分离器2的顶部。根据本发明的上述气液分离器2,所述气液分离区201用于分离气相和液相,所述气体区202用于使气体冷却。通过在气液分离区201调整压力,并结合搅拌部件205的搅拌作用使反应产物中的气体和液体分离,气体进一步上升进入气体区202进行冷却后通过气体导出口206导出,液体通过液体导出口207导出。为了进一步提高气液分离效率,优选地,所述气体区202外部设置有降温部件,所述气液分离区201的外部设置有升温部件。作为上述降温部件和升温部件,可以使用夹套结构,并可以在夹套结构中导入冷却介质或升温介质。例如图1所示,所述壳体的气液分离区201设置为夹套结构,底部设置有升温介质导入口208,顶部设置有升温介质导出口209;所述壳体的气体区202设置为夹套结构,并设置有冷却介质导入口210和冷却介质导出口211。作为上述冷却介质或升温介质,可以使用适当温度的冷却水或温水。根据本发明,为了分离得到轻烃交替共聚微球,所述液体导出口可以进一步连接固液分离装置(图未示出)。通过固液分离装置,可以将制得的轻烃交替共聚微球与溶剂等分离。所述固液分离装置能够使用现有的能够用于分离上述c2-4不饱和烃和马来酸酐等与轻烃交替共聚微球任意装置,例如离心机等。所述离心的条件可以包括:转速为4000rpm以上,时间为20min以上;优选地,转速为4000-8000rpm,时间为20-30min。本发明第二方面提供一种利用上述本发明的反应装置制备轻烃交替共聚微球的方法,该方法包括如下步骤:(1)在物料第一导入口102将含有c2-4不饱和烃、马来酸酐和引发剂的混合物导入到反应器1使得物料在所述物料通道108中进行第一聚合反应,在物料第二导入口104将二乙烯基苯导入到反应器1使得物料在所述物料通道108中进行第二聚合反应,并从物料导出口103导出反应产物;(2)将所述反应产物导入气液分离器2进行气液分离。优选地,在气液分离器2中,利用搅拌部件205的旋转使得所述反应产物中的气体和液体分离,并从液体导出口207得到液相产物。通过采用本发明的用于制备轻烃交替共聚微球的反应装置进行c2-4不饱和烃和马来酸酐的共聚反应,并适时地加入二乙烯基苯,从而能够高效率制得粒径为200-2000nm(优选600-1500nm)、颗粒形状均匀的轻烃交替共聚微球。在本发明中,所述c2-4不饱和烃是碳原子数为2-4的具有碳碳双键的烃类即可,没有特别的限定,优选为c4烯烃,例如可以包括1-丁烯、异丁烯、1,3-丁二烯、1,2-丁二烯、乙烯基乙炔、顺2-丁烯和反2-丁烯中的一种或多种。根据本发明,优选地,所述混合物中还包括c2-4烷烃,优选为c4烷烃。作为所述c2-4烷烃,例如可以为正丁烷和/或异丁烷。也就是说,所述混合物可以为含有混合碳四、马来酸酐和引发剂的混合物。所述混合碳四为石油炼制过程产生的液化燃料(碳四馏分)、石脑油裂解产生的裂解气、甲醇制烯烃产生的气体等,其主要组分通常有正丁烷、异丁烷、异丁烯、丁二烯、1-丁烯和2-丁烯等,不同来源的混合碳四中各组分的含量也有差异。根据本发明,所述第一聚合反应和第二聚合反应可以实现选择性地将物料中的c2-4端烯烃与马来酸酐进行共聚反应,因此本发明的装置和方法可以用于将c2-4端烯烃(即α-烯烃)与c2-4内烯烃分离。在本发明的所述物料中,所述c2-4内烯烃为2-丁烯,包括顺2-丁烯和反2-丁烯。根据本发明的一个更优选的实施方式,所述c2-4不饱和烃和c2-4烷烃包括1-丁烯1-99重量%、异丁烯1-99重量%、1,3-丁二烯0-99重量%、1,2-丁二烯0-50重量%、正丁烷0-99重量%、异丁烷1-99重量%、乙烯基乙炔5-20重量%、顺2-丁烯0-99重量%和反2-丁烯1-99重量%。根据本发明的一个更优选的实施方式,所述c2-4不饱和烃和c2-4烷烃包括1-丁烯0.1-2重量%、异丁烯10-30重量%、1,3-丁二烯0.01-0.1重量%、正丁烷0.5-5重量%、异丁烷30-40重量%、顺2-丁烯20-40重量%、反2-丁烯5-20重量%。根据本发明的一个更优选的实施方式,所述c2-4不饱和烃和c2-4烷烃包括1-丁烯5-15重量%、异丁烯0.5-3重量%、正丁烷20-30重量%、顺2-丁烯15-30重量%、反2-丁烯35-45重量%。根据本发明,作为所述引发剂,例如可举出过氧化二苯甲酰、过氧化二异丙苯、过氧化二特丁基、过氧化十二酰、过氧化苯甲酸特丁酯、过氧化二碳酸二异丙基酯、过氧化二碳酸二环己酯、偶氮二异丁腈和偶氮二异庚腈中的一种或多种。优选地,所述引发剂为偶氮二异丁腈和/或过氧化二苯甲酰。根据本发明,在所述混合物中,马来酸酐的含量为5-25重量%,优选为10-20重量%。根据本发明,所述混合物还包括有机溶剂。优选地,所述有机溶剂为有机酸烷基酯、烷烃、芳香烃和卤代芳香烃中的一种或多种。作为所述有机酸烷基酯,例如可以为甲酸甲酯、甲酸乙酯、甲酸丙酯、甲酸丁酯、甲酸异丁酯、甲酸戊酯、乙酸甲酯、乙酸乙酯、乙酸丙酯、乙酸丁酯、乙酸异丁酯、乙酸仲丁酯、乙酸戊酯、乙酸异戊酯、乙酸苄酯、丙酸甲酯、丙酸乙酯、丙酸丁酯、丁酸甲酯、丁酸乙酯、丁酸丁酯、丁酸异丁酯、丁酸异戊酯、异戊酸异戊酯、苯甲酸甲酯、苯甲酸乙酯、苯甲酸丙酯、苯甲酸丁酯、苯甲酸异戊酯、苯乙酸甲酯和苯乙酸乙酯中的一种或多种,其中优选为乙酸异戊酯;作为所述烷烃,例如可以为丙烷、正丁烷、异丁烷、正戊烷、异戊烷、正己烷、异己烷、环己烷、正庚烷、正辛烷和异辛烷中一种或多种;作为所述芳香烃,例如可以为苯、甲苯和二甲苯中一种或多种;作为所述卤代芳香烃,例如可以为氯苯和/或溴苯。在本发明中,将c2-4不饱和烃、马来酸酐和引发剂等均匀混合得到的混合物后导入所述反应器1,并在物料通道中进行反应,然后与通过物料第二导入口104加入的二乙烯基苯反应,从而得到所需的轻烃交替共聚微球。根据本发明,为了提高得到的轻烃交替共聚微球的尺寸均一性,优选地,所述c2-4不饱和烃中的端烯烃、马来酸酐与二乙烯基苯的摩尔比为1:0.8-7:0.008-0.07,更优选为1:1-4:0.01-0.04。根据本发明,所述反应器1的反应条件可以根据反应器的设置等进行适当调整,例如,所述反应器1中的反应条件可以包括:第一共聚反应时间为0.5-3h,第二共聚反应时间为0.5-3h;优选地,第一共聚反应时间为1-2h,第二共聚反应时间为1-2h。通过分别控制第一共聚反应时间和第二共聚反应时间在上述范围内,可以使得到的轻烃交替共聚微球尺寸分布更为均匀,并且提高反应的转化率。优选地,所述反应器1中的反应条件可以包括:反应温度为50-100℃,反应压力为0.2-2mpa;优选地,反应温度为70-90℃,反应压力为0.5-1mpa。上述反应优选在惰性气体气氛中进行,例如氮气、氩气等。通过控制在上述条件下进行聚合反应,可以提高得到的轻烃交替共聚微球的尺寸均一性。为了控制上述反应条件,通过控温介质导入口106导入的控温介质(如温水)的温度可以为55-100℃,优选为75-95℃。经过在反应器1中的反应,得到的反应产物通过物料导出口103导入气液分离器2。反应产物在气液分离器2中压力降低至例如常压,并通过搅拌部件205旋转加速气体与液体的分离,优选地,所述搅拌部件205的转速为5-100rpm,更优选为10-50rpm。根据本发明,该方法还包括将所述气液分离得到的所述液相产物进行固液分离。所述固液分离能够使用现有的能够用于分离上述c2-4不饱和烃和马来酸酐等与轻烃交替共聚微球任意方法进行,例如离心等。所述离心的条件可以为转速为4000rpm以上,时间为20min以上;优选地,转速为4000-8000rpm,时间为20-30min。通过离心,将所述液相产物分离为上层清液和下层固体;所述清液为有机溶剂,可以回用于所述共聚反应。以下将通过实施例对本发明进行详细描述。以下实施例中,混合碳四的组成通过安捷伦的7890a气相色谱仪分析。实施例1使用如图1所示的用于制备轻烃交替共聚微球的反应装置进行。该反应装置包括依次连接的反应器1、气液分离器2和离心机(图未示出)。所述反应器1包括:水平设置的截面为圆形的反应器壳体101,两个导流挡板110,其垂直设置在反应器壳体101内部,将反应器壳体101的内部分割为二者之间的换热腔112和两侧的第一反应腔111和第二反应腔113,8根中空的导流管105,长度为反应器壳体101长度的70%,直径为50cm,其平行均匀设置在所述两个导流挡板110之间,且两端开口分别开口于第一反应腔111和第二反应腔113,折流挡板109,其垂直设置在所述第一反应腔111的内部,将所述第一反应腔111分割为容积相等的上部反应腔和下部反应腔;物料第一导入口102,其设置在所述第一反应腔111的下部反应腔上,物料第二导入口104,其设置在第二反应腔113上,物料导出口103,其设置在所述第一反应腔111的上部反应腔上,以及物料通道108,其为依次连接物料第一导入口102、第一反应腔111的下部反应腔、导流管105、第二反应腔113、导流管105、第一反应腔111的上部反应腔和物料导出口103的物料通路;所述物料第二导入口104位于所述物料通道108全长的50%处。换热腔112的一侧连接控温介质导入口106,另一侧连接控温介质导出口107,并通过控温介质导入口106导入控温介质(温水)。所述反应器壳体101为夹套结构,内部导入上述控温介质(温水)。所述气液分离器2包括壳体,所述壳体被不锈钢制具孔挡板203分为位于上部的气体区202和位于下部的气液分离区201,所述气体区202连接气体导出口206,所述气液分离区201的上部与物料导出口103连接,下部设置有液体导出口207,内部设置有搅拌部件205(搅拌桨),该搅拌部件205能够在设置在气液分离器2的顶部的电机204的带动下旋转。所述壳体的气液分离区201设置为夹套结构,底部设置有升温介质导入口208,顶部设置有升温介质导出口209;所述壳体的气体区202设置为夹套结构,并设置有冷却介质导入口210和冷却介质导出口211。制备使用的混合碳四a组成(重量百分数)为:1,2-丁二烯8.92%;1,3-丁二烯14.14%;1-丁烯8.38%;反2-丁烯5.84%;顺2-丁烯31.7%;乙烯基乙炔10.99%;异丁烷1.3%;异丁烯12.78%;正丁烷2.58%,其他3.37%。制备方法包括如下步骤:(1)将14kg的混合碳四a与20kg马来酸酐、2.4kg偶氮二异丁腈、100l乙酸异戊酯混合得到有机反应液在物料第一导入口102导入反应器1,液态物流的流速为0.1m/min,使得物料在所述物料通道108中进行第一聚合反应;在物料第二导入口104将二乙烯基苯0.26kg(流速为0.01kg/min)导入到反应器1使得物料在所述物料通道108中进行第二聚合反应。在控温介质导入口和反应器壳体101的夹套结构中通入温水,控制反应温度,使得共聚反应压力为0.9mpa,共聚反应温度为70℃,第一共聚反应时间为2h,第二共聚反应时间为2h。(2)将所述反应产物通过物料导出口103导入气液分离器2,利用搅拌部件205的旋转(转速为20rpm)使得所述反应产物中的气体和液体分离,并从液体导出口207得到液相产物。在升温介质导入口208导入温水控制气液分离区201内部温度为80℃,在冷却介质导入口210导入冷却水控制气体区202温度为0℃。(3)将所述液相产物进行在4000rpm离心20min,得到固体共聚物颗粒粉末a。实施例2按照实施例1的方法进行,不同的是:使用混合碳四b代替混合碳四a,混合碳四b组成(重量百分数)为:1,3-丁二烯0.06%、反2-丁烯12.67%、异丁烷37.09%、异丁烯19.48%、顺2-丁烯27.79%、1-丁烯1.02%、其它1.89%;有机反应液由13.5kg混合碳四b、20kg马来酸酐、4kg过氧化二苯甲酰和100l乙酸异戊酯组成;共聚反应压力为1mpa,共聚反应温度为80℃,第一共聚反应时间为2.5h,第二共聚反应时间为2.5h;离心条件为4000rpm、20min;从而制得固体共聚物颗粒粉末b。实施例3按照实施例1的方法进行,不同的是:使用混合碳四c代替混合碳四a,混合碳四c组成(重量百分数)为:反2-丁烯20.83%、顺2-丁烯18.18%、正丁烷24.29%、1-丁烯9.52%、异丁烯22.78%、其它4.4%。有机反应液由15kg的混合碳四c、20kg马来酸酐、4.5kg过氧化二苯甲酰、0.26kg二乙烯基苯和100l乙酸异戊酯组成;共聚反应压力为1.5mpa,共聚反应温度为80℃,第一共聚反应时间为1.5h,第二共聚反应时间为3h;从而制得固体共聚物颗粒粉末c。实施例4-7采用实施例1的方法进行,不同的是:所述物料第二导入口104分别位于所述物料通道108全长的40%、45%、55%和60%处。从而制得固体共聚物颗粒粉末d、e、f和g。实施例8-9采用实施例1的方法进行,不同的是:导入二乙烯基苯的量分别为0.13kg、0.52kg。从而制得固体共聚物颗粒粉末h和i。实施例10采用实施例1的方法进行,不同的是反应物料的流动速率为0.5m/min。从而制得固体共聚物颗粒粉末j。对比例1采用实施例1的方法进行,不同的是,不使用本发明的用于制备轻烃交替共聚微球的反应装置,而使用普通的反应釜进行,并将二乙烯基苯与有机反应液直接混合后进行反应。从而制得固体共聚物颗粒粉末da1。对比例2采用实施例1的方法进行,不同的是,不使用本发明的用于制备轻烃交替共聚微球的反应装置,而使用普通的反应釜进行,将有机反应液反应2h(即第一聚合反应时间)后,加入二乙烯基苯,再反应2h(即第二聚合反应时间)。从而制得固体共聚物颗粒粉末da2。对比例3-4采用实施例1的方法进行,不同的是:所述物料第二导入口104分别位于所述物料通道108全长的30%和70%处。从而制得固体共聚物颗粒粉末da3和da4。测试例1将上述实施例和对比例制得的固体共聚物颗粒粉末进行如下测试:聚合物颗粒的形貌的测试:将聚合物粉末洒在铺有导电胶的样品台上,喷金,通过扫描电子显微镜hitachis4800进行聚合物形貌的分析。聚合物颗粒的粒径的测试:聚合物粒子的粒径通过扫描电子显微镜hitachis4800的自带软件进行分析。聚合转化率的测试:测试结果如下述表1所示。表1实施方式形貌粒径(微米)分散性转化率实施例1球型1.3良好85%实施例2球型1.8良好80%实施例3球型1.5良好72%实施例4球型1.3良好75%实施例5球型1.3良好76%实施例6球型1.3良好76%实施例7球型1.3良好75%实施例8球型1.2良好70%实施例9球型1.5良好77%实施例10球型1.2良好72%对比例1不规则粒子0.8差35%对比例2不规则粒子0.6差32%对比例3不规则粒子1.3差41%对比例4不规则粒子1.4差43%通过上述结果可以看出,采用本发明的实施例1-10具有较高的反应转化率,所得聚合物具有良好的球型形貌,物料分散状态良好,相对于传统反应器和反应方法的对比例具有明显更好的效果。以上详细描述了本发明的优选实施方式,但是,本发明并不限于此。在本发明的技术构思范围内,可以对本发明的技术方案进行多种简单变型,包括各个技术特征以任何其它的合适方式进行组合,这些简单变型和组合同样应当视为本发明所公开的内容,均属于本发明的保护范围。当前第1页12