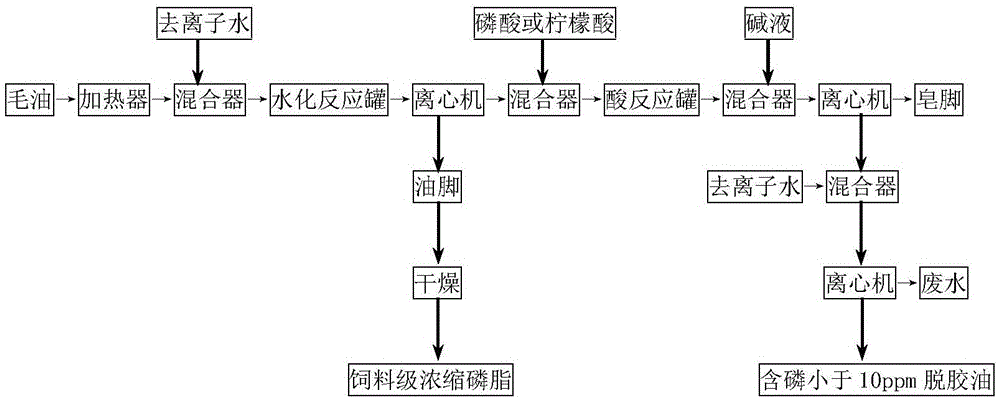
本发明涉及一种植物油脂脱胶的方法,属于食用油加工
技术领域:
。
背景技术:
:通过压榨或浸出方法生产的植物油脂中都含有一定胶质,其主要成分为磷脂,磷脂含量通过检测油脂的含磷量确定。磷脂的存在会使油脂在高温时颜色变深并产生絮状沉淀,影响产品的外观和保存,所以在生产高品质的食用油脂时,必须通过脱胶精炼工艺将其去除。植物油中的磷脂根据其亲水性,可分为水化磷脂和非水化磷脂,水化磷脂由于具有亲水性,在脱胶过程中通过加水混合搅拌会吸水膨胀析出,再通过离心分离从油中去除;非水化磷脂没有吸水性,一般先加入磷酸或柠檬酸反应,使之转变成水化磷脂后再通过离心分离方法去除。现有的脱胶工艺有两种:第一种工艺(工艺流程如图1所示)是将毛油加热至70~85℃,加水反应后再通过离心机进行分离,重相是脱胶产生的油脚,可以用来生产饲料级浓缩磷脂,轻相为脱胶油(还含有200ppm左右的磷脂);然后在脱胶油里再加入一定量的磷酸或柠檬酸混合后在酸反应罐中反应一定时间,再加入一定量的碱液混合后,通过离心机进行分离,重相为胶质和皂的混合物,称为皂脚,轻相为脱皂油再加入一定量的去离子水混合后,通过离心机进行分离,重相为水洗后的水以及油中的残皂,轻相为中和油,轻相进入下一道脱色工序。第二种工艺(工艺流程如图2所示)是将毛油加热到70~85℃,加入一定量的磷酸或柠檬酸混合后在酸反应罐中反应一定时间,再加入一定量的碱液混合后,通过离心机进行分离,重相为胶质和皂的混合物,称为皂脚,轻相为脱皂油,轻相再加入一定量的去离子水混合后,通过离心机进行分离,重相为水洗后的水以及油中的残皂,轻相为中和油,轻相进入下一道脱色工序。上述两种现有工艺具有一定的缺陷:(1)现有工艺中磷酸或柠檬酸加入后多采用刀式混合器,混合强度低,酸用量大,生产成本高,非水化磷脂的转化率低;(2)脱胶过程需加入碱液,一方面会增加成本;另一方面加入碱液使油脂形成皂化损失,降低成品油的得率,此外碱液加入后必须水洗去除残皂,增加水的使用量,同时会产生难处理的生产废水,增加污水处理成本;(3)油中的一部分磷脂生产成了皂脚,游离脂肪酸也生产了皂脚,副产品的附加值比较低;(4)工艺复杂,需要使用的设备多,固定资产的投入大,耗电量也较多。申请公布号为cn102533441a的中国发明专利申请公开了一种食用植物油脱胶工艺,该工艺包括以下步骤:(1)转化:将温度为50~70℃的毛油与占毛油重量0.05%~0.5%的柠檬酸、磷酸、苹果酸或草酸混合后,在酸反应罐中搅拌反应15~30min,得到转化混合物;(2)水化:将转化混合物与20~50℃重量为毛油中磷脂重量的1.5~2倍的软水混合后,调温至20~45℃,在水化反应罐中搅拌反应45~150min,完成水化反应,得到水化混合物;(3)离心分离:将水化混合物加热至75~90℃后经离心分离,得到的轻相分离物经真空脱溶干燥后获得脱胶油。该脱胶工艺的方法在生产过程中需要降温再升温,其工艺复杂,能耗较高,成本较高。技术实现要素:本发明提供一种植物油脂脱胶的方法。该方法操作简单,在保证得油率较高的前提下可以降低生产成本。为实现上述目的,本发明的技术方案是:一种植物油脂脱胶的方法,包括如下步骤:(1)将毛油加热至72~90℃,再加入磷酸或柠檬酸进行酸化反应,所述酸化反应包括在加入磷酸或柠檬酸后进行高强度混合的步骤;所述高强度混合为在转速为2900~14000转/min的条件下进行混合;(2)酸化反应后加水进行水化反应;(3)水化反应完成后进行离心分离得轻相,得到的轻相进行脱色、脱臭,即得。该方法中将毛油加热至72~90℃可以加快磷酸或柠檬酸与毛油中非水化磷脂的反应速度,此外本发明的油脂脱胶方法不需要加入碱液,简化了工艺流程,副产品的附加值高,在降低生产成本的同时提高了植物油的得油率,脱胶油的残磷量可达到10ppm以下,完全可以满足直接进入脱色精炼工序的要求。步骤(1)中所述的酸化反应是加入磷酸或柠檬酸进行高强度混合后再进行搅拌反应,搅拌反应的搅拌转速为40~80转/min。在40~80转/min的搅拌转速下可以使磷酸或柠檬酸与毛油中的非水化磷脂充分接触,保证非水化磷脂的转化率较高。所述搅拌反应的时间为1~45min。该反应时间可以使磷酸或柠檬酸与毛油充分反应,提高转化率。步骤(1)中磷酸或柠檬酸的加入量为毛油重量的0.02~0.1%。该磷酸或柠檬酸的使用量能保证非水化磷脂的转化率较高。步骤(2)中加水的量为毛油重量的1.5~2.5%。加水量在1.5~2.5%,可以有效地使水化磷脂彻底析出,提高分离和脱胶效果。加水所用的水温度为90~95℃。水温在90~95℃时可以使水化反应更充分。步骤(2)中水化反应的时间为20~60min。水化反应时间在20~60min可以使水化磷脂在脱胶的过程中充分地吸水进而膨胀析出。步骤(2)中水化反应时进行搅拌,搅拌的转速为30~80转/min。水化反应过程中进行转速为30~80转/min的搅拌可以使水化反应更充分,进而有效地使轻相和重相分离。附图说明图1为现有技术中的一种植物油脂脱胶方法的工艺流程图;图2为现有技术中的另一种植物油脂脱胶方法的工艺流程图;图3为本发明实施例2的植物油脂脱胶方法的工艺流程图。具体实施方式下面结合附图对本发明的具体实施方式作进一步说明。植物油脂脱胶的方法的实施例1本实施例的植物油脂脱胶的方法,包括以下步骤:(1)将毛油加热至72℃,然后加入毛油重量0.02%的磷酸进行酸化反应,酸化反应采用高强度混合器(离心混合器)进行,离心混合器的转速为2900转/min,酸化反应时间为0.1min;(2)酸化反应后再加入毛油重量2%的去离子水进行水化反应,水化反应时进行搅拌,搅拌的转速为30转/min,加入的去离子水的温度为90℃,水化反应的时间为30min;(3)水化反应后进行离心分离,离心分离的转速为4750转/min,离心时间为0.5min;离心后得到的重相为胶质,称为油脚,胶质的主要成分为磷脂、油、水和杂质,油脚可进一步生产成饲料级浓缩磷脂,轻相为脱胶油;(4)将脱胶油加热到105℃,再加入毛油重量1.0%的白土,混合30min,过滤得到脱色油;(5)将脱色油再升温到250℃,在真空度为1mbar下进行脱臭反应,脱臭反应时间为60min,通过热油与冷油的多次换热,再经过水冷降温得到一级油。该实施例中,步骤(3)水化反应后进行离心分离,离心分离的转速为3000~5000转/min均可。该实施例中,步骤(3)水化反应后进行离心分离,离心分离的时间为0.1~0.5min均可。该实施例中,步骤(4)脱胶油加热后和白土混合20~30min均可。该实施例中,步骤(5)将脱色油升温到235~250℃均可。植物油脂脱胶的方法的实施例2本实施例的植物油脂脱胶的方法,该方法的工艺流程图如图3所示,该方法包括以下步骤:(1)将毛油加热至80℃,然后加入毛油重量0.025%的磷酸进行酸化反应得混合物,酸化反应采用高强度混合器(离心混合器)进行,离心混合器的转速为10000转/min,酸化反应时间为0.1min;(2)酸化反应后的混合物置于酸反应罐进行搅拌反应得酸化产物,搅拌反应的搅拌转速为40转/min,搅拌反应的时间为45min;(3)搅拌反应后的酸化产物置于混合器中,再向混合器中加入毛油重量2.5%的去离子水进行混合,混合后转移至水化反应罐中进行水化反应,水化反应时进行搅拌,搅拌的转速为50转/min,加入的去离子水的温度为93℃,水化反应的时间为60min;(4)水化反应后进行离心分离,离心分离的转速为3000转/min,离心时间为0.1min;离心后得到的重相为胶质,称为油脚,可进一步生产成饲料级浓缩磷脂,轻相为脱胶油;(5)将脱胶油加热到105℃,再加入毛油重量1.0%的白土,混合25min,过滤得到脱色油;(6)将脱色油再升温到240℃,在真空度为1mbar下进行脱臭反应,脱臭反应时间为60min,通过热油与冷油的多次换热,再经过水冷降温得到一级油。该实施例中,步骤(4)水化反应后进行离心分离,离心分离的转速为3000~5000转/min均可。该实施例中,步骤(4)水化反应后进行离心分离,离心分离的时间为0.1~0.5min均可。该实施例中,步骤(5)脱胶油加热后和白土混合20~30min均可。该实施例中,步骤(6)将脱色油升温到235~250℃均可。植物油脂脱胶的方法的实施例3本实施例的植物油脂脱胶的方法,包括以下步骤:(1)将毛油加热至90℃,然后加入毛油重量0.1%的柠檬酸进行酸化反应得混合物,酸化反应采用高强度混合器(均质机)进行,离心混合器的转速为14000转/min,酸化反应时间为0.1min;(2)酸化反应后的混合物置于酸反应罐进行搅拌反应,搅拌反应的搅拌转速为80转/min,搅拌反应的时间为1min;(3)搅拌反应后再加入毛油重量1.5%的去离子水进行水化反应,水化反应时进行搅拌,搅拌的转速为80转/min,加入的去离子水的温度为95℃,水化反应的时间为20min;(4)水化反应后进行离心分离,离心分离的转速为5000转/min,离心时间为0.5min;离心后得到的重相为胶质,称为油脚,可进一步生产成饲料级浓缩磷脂,轻相为脱胶油;(5)将脱胶油加热到105℃,再加入毛油重量1.0%的白土,混合20min,过滤得到脱色油;(6)将脱色油再升温到235℃,在真空度为1mbar下进行脱臭反应,脱臭反应时间60min,通过热油与冷油的多次换热,再经过水冷降温得到一级油。该实施例中,步骤(4)水化反应后进行离心分离,离心分离的转速为3000~5000转/min均可。该实施例中,步骤(4)水化反应后进行离心分离,离心分离的时间为0.1~0.5min均可。该实施例中,步骤(5)脱胶油加热后和白土混合20~30min均可。该实施例中,步骤(6)将脱色油升温到235~250℃均可。对比例1本对比例的植物油脂脱胶的方法如图2所示,包括以下步骤:(1)将毛油在加热器中加热到70℃,然后加入毛油重量0.03%的磷酸混合,混合后通过刀式混合器反应后,再在酸反应罐中反应20min;(2)反应完成后再加入毛油重量0.4%的碱液进行混合,通过刀式混合器以后,进入中和反应罐进行中和反应;(3)中和反应后通过离心机进行分离,重相为胶质和皂的混合物,称为皂脚,轻相为脱皂油;(4)再向轻相中加入毛油重量4.5%的去离子水混合,通过刀式混合器后,再通过离心机进行分离,重相为水洗后的水以及油中的残皂,轻相为中和油;(5)轻相经脱色、脱臭即得。对比例2本对比例的植物油脂脱胶的方法如图2所示,包括以下步骤:(1)将毛油在加热器中加热到85℃,然后加入毛油重量0.05%的磷酸混合,混合后通过刀式混合器反应后,再在酸反应罐中反应20min;(2)反应完成后再加入毛油重量0.6%的碱液进行混合,通过刀式混合器以后,进入中和反应罐进行中和反应;(3)中和反应后通过离心机进行分离,重相为胶质和皂的混合物,称为皂脚,轻相为脱皂油;(4)再向轻相中加入毛油重量5%的去离子水混合,通过刀式混合器混合后,再经过离心机进行分离,重相为水洗后的水以及油中的残皂,轻相为中和油;(5)轻相经脱色、脱臭即得。试验例1本试验例以
背景技术:
中现有工艺的第二种工艺(如图2所示)为例和本发明的工艺进行对比,如表1所示,从表1可以看出,本发明的工艺得油率高、用酸和水量少、辅料使用少、工艺环节少、副产品的附加值高,总体效果明显优于现有工艺。表1现有工艺与本发明工艺的对比项目现有工艺本发明的工艺得率(%)94.5~9595~95.5磷酸或柠檬酸用量(公斤/吨)0.3~0.50.2~0.3碱用量(公斤/吨)4~80电用量(度/吨)106水用量(公斤/吨)45~8015~25废水量(公斤/吨)45~8015~25副产品价值(元/吨)146179白土用量(公斤/吨)1012固定资产投入(万元)1400700试验例2本试验例以本发明的实施例1中的植物油脱胶方法对600吨大豆毛油进行脱胶,每年可产生的效益(以年加工300天计算)如表2所示,从表2可以看出,本发明的制备工艺总效益更好。表2每年可产生的效益序号项目数量效益(元)备注1出油增加量900吨4950000油的价格5500元/吨2耗酸减少量18吨90000酸的价格5000元/吨3耗碱减少量720吨936000碱的价格1300元/吨4耗电减少量720000度576000电的价格0.8元/度5耗水减少量3600吨14400水的价格4元/吨6少出废水量3600吨36000废水处理成本10元/吨7多耗白土量360吨-900000白土的价格2500元/吨8副产品价差5940000合计11642400当前第1页12