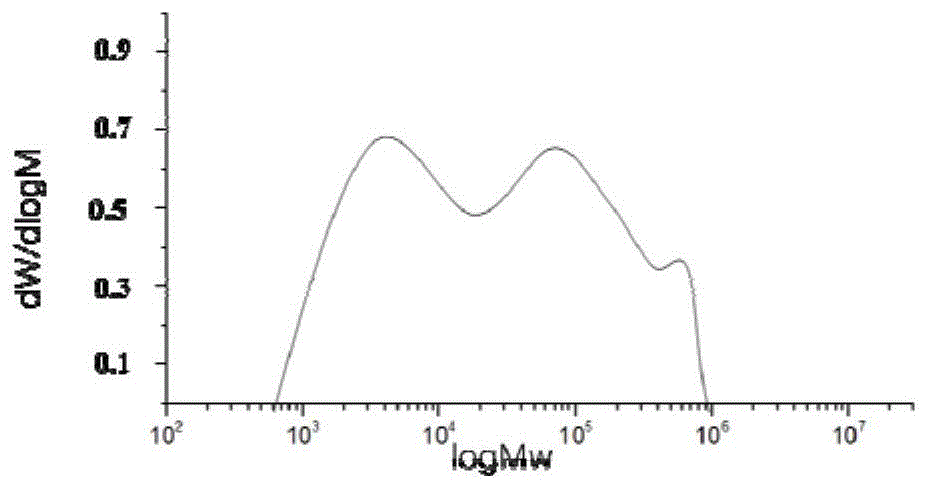
本发明属于催化剂领域,特别涉及一种负载型三中心催化剂及其制备方法和应用。
背景技术:
:聚乙烯作为一种通用的塑料,由于其优良的力学性能、电绝缘性、耐化学腐蚀性及耐低温性能,广泛应用于工业、农业、汽车、通讯以及日常生活的各个领域,而这些优良的性能主要取决于聚乙烯的生产工艺、催化剂技术以及后加工技术等,其中催化剂技术又是其中最为关键的技术,因此受到工业和学术界广泛的关注和研究。目前,工业上广泛应用的聚乙烯催化剂主要包含如下三大类:ziegler~natta钛系催化剂、铬基催化剂(主要包括无机铬phillip催化剂和有机铬s~2催化剂)以及茂金属催化剂。在上述三大类催化剂的基础上,研究人员又开发出一些新型的催化剂,如复合型双中心催化剂,即将两种催化剂共混或者共负载于某一载体,其研究的出发点在于使该类催化剂能够同时具备两种活性中心的特性,甚至利用两种活性中心间的协同效应,表现出更为优异的催化特性。但是实际研究过程中人们发现该类催化剂的开发难度较大,主要是复合之后,两种活性中心通常表现为反协同作用,即互相毒化使催化性能削弱。通过大量的筛选,前期我们开发了一系列负载型铬、钒双金属中心聚乙烯催化剂,其双金属中心间在大多数条件下表现出优良的催化协同效应,使催化剂的聚合活性、共聚性能等方面在原来单金属催化剂的基础上有明显改善,且合成聚合物的分子量呈宽峰或者双峰分布,共聚单体也集中分布于高分子量组分,因此该系列催化剂在单釜法合成高性能双峰聚乙烯方面拥有巨大优势,有可能部分取代工业上常用的合成高性能双峰聚乙烯料的双釜串联工艺,因为相对于后者,利用双中心催化技术于单一反应釜中合成高性能双峰聚乙烯的设备投资更低,操作难度更小,能耗也更低。另一方面,近些年德国的利安德~巴塞尔公司以及日本的三井油化公司开发了三釜串联工艺,该工艺使用单金属中心催化剂通过改变三个聚合釜的工艺条件,如共聚单体浓度和氢气分压以实现分子量呈三峰分布聚乙烯的生产(如图1所示),其聚合物包含较低分子量乙烯均聚物a,中等分子量乙烯共聚物b以及高分子量或超高分子量乙烯共聚物c,其中a组分主要提供聚合物较高的刚性和加工性能,b组分提供聚合物良好的韧性和长期力学性能,在此基础上c组分使聚合物的耐蠕变性以及长期力学性能又有进一步的提高,a、b、c组分的相对含量可通过催化剂在各反应釜的相对停留时间调整。该工艺合成的分子量呈三峰分布的聚乙烯相比于市场上现有的聚乙烯,在生产更高等级的管材以及薄膜方面展现出明显的优势。现有技术中还没有通过三中心催化剂利用单一反应釜合成高性能三峰分布聚乙烯的报道。技术实现要素:为了克服上述现有技术的缺点与不足,本发明的首要目的在于提供一种负载型三中心催化剂。其可用于乙烯均聚以及乙烯与α-烯烃的共聚,其合成的聚合物分子量分布较宽,部分呈三峰分布,包含较低分子量乙烯均聚物、中等分子量乙烯共聚物以及高分子量或超高分子量乙烯共聚物。本发明另一目的在于提供上述负载型三中心催化剂的制备方法。本发明再一目的在于提供上述负载型三中心催化剂在催化烯烃聚合中的应用。本发明的目的通过下述方案实现:一种负载型三中心催化剂,其包括多孔无机载体和三种催化剂活性中心,即有机铬活性组分、无机铬活性组分和无机钒活性组分;或者,该催化剂除了包括多孔无机载体、有机铬活性组分、无机铬活性组分和无机钒活性组分外,还可以包括催化剂改性组分。所述的多孔无机载体为氧化硅、氧化铝、硅铝酸盐、无机粘土、氧化钛、氧化锆、氧化镁、氧化钙、氧化铁、氧化锡、氧化锌、氧化硼、氧化钨、氧化铌中的至少一种;所述无机粘土优选为蒙脱石,所述的氧化硅优选为无定型多孔硅胶。所述的多孔无机载体的比表面积为50~800m2/g,孔体积为0.1~5.0cm3/g,平均孔径在1~50nm;所述的有机铬活性组分为有机铬活性组分前驱体经有机金属助催化剂或聚合单体活化后得到,而所述有机铬活性组分前驱体由含有环戊二烯基配体、茚基配体、芴基配体、环戊二烯基衍生物配体、茚基衍生物配体、芴基衍生物配体中至少一种配体的有机铬铬源负载于多孔无机载体表面获得;所述的无机铬活性组分为无机铬活性组分前驱体经有机金属助催化剂或聚合单体活化后的得到,而所述无机铬活性组分前驱体为铬源在多孔无机载体表面的高温焙烧产物;所述的无机钒活性组分为无机钒活性组分前驱体经有机金属助催化剂或聚合单体活化后的得到,而所述无机钒催化剂前驱体为钒源在多孔无机载体表面的高温焙烧产物;所述的催化剂改性组分为含硫、磷或卤素元素的化合物在多孔无机载体表面的高温焙烧产物,其中含硫、磷或卤素元素的化合物简称为q组分;所述聚合单体为乙烯或常见α-烯烃,常见α-烯烃包括丙烯、1-丁烯、1-己烯等。所述的有机金属助催化剂包括有机铝化合物、有机锂化合物、有机硼化合物等常用作烯烃聚合反应助催化剂中的任何一种或者是它们的组合。有机铝化合物可以包括三烷基铝alr3、二烷基烷氧基铝alr2or、二烷基卤化铝alr2x、铝氧烷、乙基倍半铝氯化物等等,其中r是烷基,例如具有1-12个碳原子的烷基,例如是甲基、乙基、正丙基、异丙基、正丁基、异丁基、正戊基、正己基、正庚基、正辛基、正壬基、正十二烷基等,x是卤素,例如氟、氯、溴和碘,优选氯。所述铝氧烷可以包括甲基铝等所有烷基铝与水的反应物。所述作为有机金属助催化剂的有机铝化合物可以单独使用或两种或两种以上组合使用。作为具体例子,所述铝化合物可以为三乙基铝、三异丁基铝、二乙基乙氧基铝、一氯二乙基铝和甲基铝氧烷等中的至少一种。有机铬活性组分前驱体由有机铬铬源负载于多孔无机载体表面获得,所述的有机铬铬源的结构简式可表示如下:crcp*1cp*2,其中cp*1与cp*2均可为环戊二烯基及其衍生物、茚基及其衍生物、芴基及其衍生物中的一种,且cp*1与cp*2结构是否相同不受限制。具体地,cp*1与cp*2的结构可为如下结构中的一种:其中,r为1~20个碳原子的烃基,烃基可以是饱和或是不饱和的,包括脂肪族、脂环族和芳香族,如甲基、乙基、丙基、丁基、戊烷基、环戊烷基、烯丙基、苯基和萘基等;n,取整数值0~5;芳香环上连接的多个r相互独立,可以相同,也可以不同;ra和ra'为1~10个碳原子的烃基,烃基可以是饱和或是不饱和的,包括脂肪族、脂环族和芳香族,如甲基、乙基、丙基、丁基、戊烷基、环戊烷基、烯丙基、苯基和萘基等;m,取整数0~4;x,取整数0~3;芳香环上连接的多个ra以及多个ra'均相互独立,可以相同,也可以不同;rb和rb'为1~10个碳原子的烃基,烃基可以是饱和或是不饱和的,包括脂肪族、脂环族和芳香族,如甲基、乙基、丙基、丁基、戊烷基、环戊烷基、烯丙基、苯基和萘基等官能团;m'、m",取整数值0~4;y可以为h、rb或rb';z,取值0或1;芳香环上连接的多个rb以及多个rb'均相互独立,可以相同,也可以不同。无机铬活性组分前驱体为铬源(含铬化合物)在无机载体表面的高温焙烧产物;所述的铬源(含铬化合物)选自三氧化铬、硝酸铬、醋酸铬、氯化铬、硫酸铬、铬酸铵、重铬酸铵、碱式醋酸铬、其它合适的可溶性铬盐以及它们之间的任意的组合。无机钒活性组分前驱体为钒源(含钒化合物)在无机载体表面的高温焙烧产物;所述的钒源(含钒化合物)可选自如下:六氟钒酸铵、硝酸钒、草酸氧钒、偏钒酸铵、硫酸氧钒、硫酸氧化钒(ⅳ)水合物、硫酸钒(ⅲ)、三氯代氧化钒、原钒酸钠、偏钒酸钠等,以及非水溶性含钒盐:如双乙酰丙酮氧化钒、三异丙醇氧钒、三丙醇氧化钒、乙酰丙酮钒、氧化三乙氧基钒、氯化氧钒、硅化三钒、其它合适的可溶性钒盐以及它们的任意组合。催化剂改性组分为q组分在无机载体表面的高温焙烧产物;所述的q组分可选自如下:硫酸、过硫酸、焦硫酸、亚硫酸、牛磺酸、硫酸铵、亚硫酸铵、过硫酸铵、硫酸钛、硫酸锆、硫酸钒、硫酸铁、硫酸亚铁、硫酸亚铁铵、硫酸镍、硫酸锌、硫酸铝、硫酸锡、硫酸锑、磷酸、焦磷酸、过磷酸、亚磷酸、次磷酸、偏磷酸、磷酸铵、焦磷酸铵、过磷酸铵、亚磷酸铵、次磷酸铵、偏磷酸铵、磷酸钛、磷酸锆、磷酸铁、磷酸镍、磷酸锌、磷酸铝、磷酸锡、磷酸锑、氢氟酸、氟化铵、氟硅酸、氟硼酸、氟硼酸铵、氟化氢铵、六氟硅酸铵、三氟化硼、氟化铝、氟化锑、六氟磷酸铵、六氟钛酸铵、盐酸、氯磺酸、氯化铵、氯化亚铁、氯化铁、氯化铝、四氯化钛、氢溴酸、溴化铵、溴化铁、溴化亚铁或溴化铝以及它们的任意组合。所述的负载型三中心催化剂的活性中心前驱体结构如下所示,其中a结构为无机铬活性组分前驱体,b结构为无机钒活性组分前驱体,c组分为有机铬活性组分前驱体(其中l为环戊二烯基及其衍生物、茚基及其衍生物、芴基及其衍生物中的一种):所述的负载型三中心催化剂中,有机铬活性组分中cr的含量为催化剂总重量的0.1~12wt%(按cr的重量计);无机铬活性组分中cr的含量为催化剂总重量的0.05~12wt%,(按cr的重量计);无机钒活性组分中v的含量为催化剂总重量的0.05~10wt%,(按v的重量计);催化剂改性组分中硫、磷和卤素元素的含量为催化剂总重量的0.1~20wt%(按硫、磷和卤素元素的总重量计)。一种上述负载型三中心催化剂的制备方法,包括负载型三中心催化剂前驱体的制备以及负载型三中心催化剂前驱体的活化,当负载型三中心催化剂中包括多孔无机载体、有机铬活性组分、无机铬活性组分、无机钒活性组分和催化剂改性组分时,负载型三中心催化剂前驱体的制备包括以下步骤:(1.1)通过浸渍、干燥和高温焙烧程序将铬源、钒源以及q组分分别转化为负载于多孔无机载体表面的无机铬活性组分前驱体、无机钒活性组分前驱体以及催化剂改性组分,得到负载型两中心催化剂前驱体,其中无机铬活性组分前驱体、无机钒活性组分前驱体以及催化剂改性组分这三种组分的负载顺序是任意的;(1.2)通过浸渍、干燥程序将有机铬铬源转化为负载于步骤(1)中负载型两中心催化剂表面的有机铬活性组分前驱体,即得到负载型三中心催化剂前驱体;当负载型三中心催化剂中包括多孔无机载体、有机铬活性组分、无机铬活性组分和无机钒活性组分时,负载型三中心催化剂前驱体的制备包括以下步骤:(2.1)通过浸渍、干燥和高温焙烧程序将铬源和钒源分别转化为负载于多孔无机载体表面的无机铬活性组分前驱体和无机钒活性组分前驱体,得到负载型两中心催化剂前驱体,其中无机铬活性组分前驱体和无机钒活性组分前驱体这两种组分的负载顺序是任意的;(2.2)通过浸渍、干燥程序将有机铬催化剂铬源转化为负载于步骤(1)中负载型两中心催化剂前驱体表面的有机铬活性组分前驱体,即得到负载型三中心催化剂前驱体;负载型三中心催化剂前驱体的活化包括以下步骤:取上述两种方法中任意一种方法制备的负载型三中心催化剂前驱体,加入有机金属助催化剂对其进行预处理活化,然后干燥即得目标催化剂;或取上述负载型三中心催化剂前驱体,聚合前置于反应釜中与有机金属助催化剂反应原位形成目标催化剂;或取上述负载型三中心催化剂前驱体置于高压聚合单体中,经聚合单体原位活化形成目标催化剂。上述两种制备三中心催化剂前驱体的方法中,所述的负载顺序是任意的是指以任何顺序负载这几种活性成分前驱体都是可以的,例如步骤(1.1)中,可以通过共浸渍的方法将铬源、钒源以及q组分同时负载到多孔无机载体表面,然后通过干燥和高温焙烧得到负载型两中心催化剂前驱体;也可以通过共浸渍的方法将铬源、钒源以及q组分中的任意两种组分同时负载到多孔无机载体表面,然后通过干燥和高温焙烧得到负载有相应活性组分前驱体或改性组分的多孔无机载体,再通过浸渍、干燥和高温焙烧程序将剩下一种组分转化为负载于改性多孔无机载体表面的相应活性组分前驱体或改性组分,即得到目标催化剂前驱体;也可以通过浸渍、干燥和高温焙烧程序将铬源、钒源以及q组分中的任意一种转化为负载于多孔无机载体表面的活性组分前驱体或改性组分,再通过共浸渍的方法将剩下两种组分负载到改性的多孔无机载体上,然后再通过干燥和高温焙烧程序将剩下两种组分转化为负载于多孔无机载体表面的活性组分前驱体,即得到目标催化剂前驱体;还可以通过浸渍、干燥和高温焙烧程序依次将铬源、钒源以及q组分分别转化为负载于多孔无机载体表面的无机铬活性组分前驱体、无机钒活性组分前驱体以及催化剂改性组分,即得到目标催化剂前驱体;步骤(1.1)和步骤(2.1)中,铬源、钒源以及q组分均以惰性溶剂为介质,通过浸渍搅拌的方法进入多孔无机载体孔道,并吸附于其表面,其中惰性溶剂为水、甲醇、乙醇、正己烷、正庚烷、正辛烷、苯、甲苯、二甲苯等中的至少一种;铬源、钒源以及q组分的用量满足:无机铬活性组分中cr的含量为催化剂总重量的0.05~12wt%,(按cr的重量计);无机钒活性组分中v的含量为催化剂总重量的0.05~10wt%,(按v的重量计);催化剂改性组分中硫、磷和卤素元素的含量为催化剂总重量的0.1~20wt%,(按硫、磷和卤素元素的总重量计);所述的浸渍的温度为20~120℃,优选为45~90℃,所述的浸渍时间为1~24h,优选为4~12h;浸渍结束后通过高温将体系中的溶剂蒸发脱除以达到干燥的目的,所述的干燥是指在60~150℃干燥,优选在80~130℃干燥,所述的干燥时间为2~24h,优选为6~16h;铬源、钒源以及q组分在多孔无机载体表面的高温焙烧过程是在氮气,或惰性气体如氩气和氦气,或者含氧气氛如氧气、干空气中进行,所述的高温焙烧的温度为300~900℃,优选为400~800℃,焙烧过程的升温速率为0.1~5℃/min,优选0.5~2℃/min,焙烧时间为2~24h,优选为4~12h;焙烧过程中,当温度升至150℃之前,焙烧在氮气或惰性气氛如氩气和氦气下进行,当焙烧温度超过150℃后,焙烧在含氧气氛如氧气或干空气中进行,当焙烧结束并且温度降至300~400℃以下后,将含氧气氛替换为惰性气氛;步骤(1.1)和步骤(2.1)中,所述的焙烧过程一般在流化状态或非流化状态下均可进行,但优选在流化状态下进行,焙烧主要分为四个阶段,其中第一阶段为室温至150℃,该阶段主要使物理吸附于无机载体表面的水组分脱除;第二阶段为150℃至焙烧温度,该阶段主要使无机载体表面的羟基缩合,并使形成的水分脱除,同时使浸渍吸附于其表面的铬源、钒源或q组分部分分解;第三阶段为焙烧温度,该阶段使铬源、钒源或q组分几乎完全分解,并分别形成无机铬活性组分前驱体、无机钒活性组分前驱体以及催化剂改性组分;第四阶段为冷却阶段,该阶段无机铬活性组分前驱体、无机钒活性组分前驱体或催化剂改性组分已在无机载体表面形成,但是需要继续通入气体使催化剂冷却至室温,以便于收集。其中第一阶段在惰性气体中进行以便使所含水分被充分脱除,第二和第三阶段在含氧气氛中进行,第四阶段当温度降低至300~400℃时将工作气氛由含氧气氛切换至惰性气体。步骤(1.2)和步骤(2.2)中,有机铬铬源以惰性有机溶剂为介质,通过浸渍搅拌的方法与多孔无机载体表面的剩余羟基反应从而负载于其表面,其中有机铬铬源的用量满足:有机铬活性组分中cr的含量为催化剂总重量的0.1~12wt%(按cr的重量计);惰性有机溶剂可选用常用的有机烃类化合物,如正己烷、正庚烷、正辛烷、苯、甲苯、二甲苯等,浸渍温度为20~120℃,优选为45~80℃,浸渍时间1~24h,优选为4~8h;浸渍结束后通过高温将体系中的有机溶剂蒸发脱除以达到干燥的目的,干燥温度为60~150℃,优选为80~130℃,干燥时间为2~24h,优选为6~16h;整个过程在氮气或惰性气体如氩气以及氦气保护下进行。负载型三中心催化剂前驱体的活化步骤中,所述有机金属助催化剂对该负载型三活性中心催化剂前驱体进行预还原活化处理是在惰性气氛下进行,所述的有机金属助催化剂的摩尔量和负载型三中心催化剂前驱体中铬元素的总摩尔量的比值为0~1000,优选为0-100,更优选0-50;所述的预还原活化处理温度在室温~100℃之间,优选室温~60℃之间,还原活化处理时间0.5~20小时,优选0.5~10小时,还原活化处理采用搅拌方式,优选连续搅拌,处理完毕后再在60~120℃之间干燥2~8小时,干燥在氮气或惰性气体气氛下进行,例如在氮气、氦气、氩气等气氛下进行,优选在氮气气氛下进行,该干燥过程也可在真空条件下进行,得到的经过预还原活化的负载型三活性中心催化剂在惰性气体气氛下保存待用。负载型三中心催化剂前驱体的活化步骤中,负载型三中心催化剂前驱体与有机金属助催化剂反应原位形成目标催化剂是指在溶剂介质中进行原位还原活化处理,所述的溶剂介质可以选自异戊烷、正戊烷、正己烷、异己烷、正庚烷、正辛烷、甲苯、二甲苯,优选异戊烷、正己烷、异己烷和正庚烷中的至少一种;所述的有机金属助催化剂中金属元素的摩尔量和负载型三中心催化剂前驱体中铬元素的总摩尔量的比值为0~1000,优选为0-100,更优选0-50;所述的原位还原活化处理的温度为20~120℃,原位还原活化处理的时间为0.5~5h;负载型三中心催化剂前驱体的活化步骤中,负载型三中心催化剂前驱体经聚合单体原位活化形成目标催化剂是指在溶剂介质中进行原位还原活化处理,溶剂介质可选自异戊烷、正戊烷、正己烷、异己烷、正庚烷、正辛烷、甲苯、二甲苯,优选异戊烷、正己烷、异己烷和正庚烷中的至少一种;聚合单体的分压为1-5mpa,优选1.5-3.5mpa;所述的原位还原活化处理的温度为50~120℃;本发明提供制备负载型三中心催化剂的方法,其中一种方法包含如下步骤:(i)将多孔无机载体浸渍于含铬源和钒源的溶液,然后干燥,接着在高温300~900℃下焙烧活化;(ii)将(i)中所得焙烧产物浸渍于含有机铬铬源的溶液,然后干燥,得到所述催化剂前驱体保存备用。(iii)称取一定量(ii)中所得催化剂前驱体置于高压聚合釜中,原位通过聚合单体的活化作用形成具有催化剂活性的目标催化剂,随后开始聚合反应。根据一个优选的制备负载型三活性中心乙烯聚合催化剂的方法包含步骤:a)将含铬源和钒源的溶液通过共浸渍的方法吸附于多孔无机载体表面,浸渍时间为1~24h,优选4~12h,浸渍温度为20~120℃,优选45~90℃,然后在60~150℃之间干燥,优选80~130℃,干燥时间2~24h,优选6~16h,干燥过程中也可以采用真空,然后将干燥后混合物置于惰性气体或者含氧气氛中进行高温焙烧活化,焙烧温度在300~900℃,优选400~800℃,焙烧时间为2~24h,优选4~12h,然后进行冷却,在冷却至300~400℃时将气氛切换成惰性气体,自然冷却至室温后保存备用。b)将上述焙烧产物置于含有机铬催化剂前驱体的溶液中进行浸渍反应,浸渍反应时间为1~24h,优选4~8h,浸渍温度为20~120℃,优选45~80℃,然后在60~150℃之间干燥,优选80~130℃,干燥时间2~24h,优选6~16h,干燥过程中也可以采用真空,干燥结束后即得所述催化剂前驱体。c)称取一定量(ii)中所得催化剂前驱体置于装有一定量溶剂的高压聚合釜中,原位通过乙烯单体的活化作用形成具有催化剂活性的目标催化剂,随后开始乙烯聚合反应,溶剂介质可选自异戊烷、正己烷、正庚烷、正辛烷和甲苯,优选异戊烷或正己烷,催化剂活化与聚合温度为50-110℃,优选60-80℃,乙烯单体压力为1-5mpa,优选1-3mpa。作为一个实例,制备本发明催化剂的具体操作包括:将多孔无定形硅胶浸渍在一定浓度的偏钒酸铵和碱式醋酸铬的水溶液中,钒和铬的负载量相对于催化剂总重量符合本发明的要求(例如v为0.1~10wt%,cr为0.1~2wt%);在连续搅拌一定时间(例如4~8小时)后,升温干燥;然后在流化床内进行高温焙烧,其中焙烧第一阶段为升温阶段(例如100~150℃),在氮气气氛中焙烧脱除载体中吸附的物理水;焙烧第二阶段为升温阶段(例如150~800℃),在干燥空气中焙烧脱除硅胶表面的部分羟基,同时偏钒酸铵和碱式醋酸铬部分氧化分解;焙烧第三阶段为恒温阶段(例如800℃下恒温4~12h),在干燥空气中焙烧,以进一步脱除硅胶表面的羟基,同时使偏钒酸铵和碱式醋酸铬几乎完全氧化分解;焙烧第四阶段为自然降温冷却阶段,在冷却至300~400℃时切换为氮气保护,在氮气保护下转移保存备用。将上述焙烧产物浸渍于一定浓度的二茂铬正己烷溶液中,有机铬的负载量相对于催化剂总重量符合本发明要求(例如cr为0.5~2wt%),浸渍温度为45~50℃,浸渍时间为4~8h,浸渍结束后进行升温干燥,干燥温度为75~90℃,干燥时间为4~8h,整个浸渍和干燥过程可施加搅拌,干燥结束后在氮气保护下将催化剂前驱体转移至无水无氧条件下保存。往容积为2l的高压聚合釜中导入1l正己烷,随后在氮气保护下往聚合釜中加入0.1g催化剂前驱体,同时导入2mpa的乙烯分压,并在90℃下进行催化剂前驱体的原位活化和后续的聚合反应。本发明提供制备负载型三中心催化剂的方法,其中一种方法包含如下步骤:(i)将多孔无机载体浸渍于含钒源的溶液,然后干燥,接着在高温300~900℃下焙烧活化;(ii)将(i)中所得焙烧产物浸渍于含铬源的溶液,然后干燥,接着在高温300~900℃下焙烧活化;(iii)将(ii)中所得焙烧产物浸渍于含有机铬铬源的溶液,然后干燥,得到所述催化剂前驱体保存备用。(iv)称取一定量(iii)中所得催化剂前驱体置于高压聚合釜中,通过聚合单体的原位活化作用形成具有催化剂活性的目标催化剂,随后开始聚合反应。根据一个优选的制备负载型三活性中心乙烯聚合催化剂的方法包含步骤:a)将含钒源的溶液通过浸渍的方法吸附于多孔无机载体表面,浸渍时间为1~24h,优选4~12h,浸渍温度为20~120℃,优选45~90℃,然后在60~150℃之间干燥,优选80~130℃,干燥时间2~24h,优选6~16h,干燥过程中也可以采用真空,然后将干燥后混合物置于惰性气体或者含氧气氛中进行高温焙烧活化,焙烧温度在300~900℃,优选400~600℃,焙烧时间为2~24h,优选4~12h,然后自然冷却至室温后保存备用。b)将上述焙烧产物浸渍于含铬源的溶液,浸渍时间为1~24h,优选4~12h,浸渍温度为20~120℃,优选45~90℃,然后在60~150℃之间干燥,优选80~130℃,干燥时间2~24h,优选6~16h,干燥过程中也可以采用真空,然后将干燥后混合物置于惰性气体或者含氧气氛中进行高温焙烧活化,焙烧温度在300~900℃,优选400~800℃,焙烧时间为2~24h,优选4~12h,然后进行冷却,在冷却至300~400℃时将气氛切换成惰性气体,自然冷却至室温后保存备用。c)将上述焙烧产物置于含有机铬铬源的溶液中进行浸渍反应,浸渍反应时间为1~24h,优选4~8h,浸渍温度为20~120℃,优选45~80℃,然后在60~150℃之间干燥,优选80~130℃,干燥时间2~24h,优选6~16h,干燥过程中也可以采用真空,干燥结束后即得所述催化剂前驱体。d)称取一定量(c)中所得催化剂前驱体置于装有一定量溶剂的高压聚合釜中,原位通过乙烯单体的活化作用形成具有催化剂活性的目标催化剂,随后开始乙烯聚合反应,溶剂介质可选自异戊烷、正己烷、正庚烷、正辛烷和甲苯,优选异戊烷或正己烷,催化剂活化与聚合温度为50-110℃,优选60-80℃,乙烯单体压力为1-5mpa,优选1-3mpa。作为一个实例,制备本发明催化剂的具体操作包括:将多孔无定形氧化铝浸渍在一定浓度的偏钒酸铵水溶液中,钒的负载量相对于催化剂总重量符合本发明的要求(例如v为0.1~10wt%);在连续搅拌一定时间(例如4~8小时)后,升温干燥;然后在流化床内进行高温焙烧,其中焙烧第一阶段为升温阶段(例如100~150℃),在氮气气氛中焙烧脱除载体中吸附的物理水;焙烧第二阶段为升温阶段(例如150~500℃),在干燥空气中焙烧脱除硅胶表面的部分羟基,同时偏钒酸铵部分氧化分解;焙烧第三阶段为恒温阶段(例如500℃下恒温4~12h),在干燥空气中焙烧,以进一步脱除硅胶表面的羟基,同时使偏钒酸铵几乎完全氧化分解;焙烧第四阶段为自然降温冷却阶段,冷却至室温时将焙烧产物收集备用。将上述焙烧产物浸渍在一定浓度的硝酸铬水溶液中,铬的负载量相对于催化剂总重量符合本发明的要求(例如铬为0.2~1wt%);在连续搅拌一定时间(例如4~8小时)后,升温干燥;然后在流化床内进行高温焙烧,其中焙烧第一阶段为升温阶段(例如100~150℃),在氮气气氛中焙烧脱除载体中吸附的物理水;焙烧第二阶段为升温阶段(例如150~800℃),在干燥空气中焙烧脱除硅胶表面的部分羟基,同时硝酸铬部分氧化分解;焙烧第三阶段为恒温阶段(例如800℃下恒温4~12h),在干燥空气中焙烧,以进一步脱除硅胶表面的羟基,同时使硝酸铬几乎完全氧化分解;焙烧第四阶段为自然降温冷却阶段,在冷却至300~400℃时切换为氮气保护,在氮气保护下转移保存备用。将上述焙烧产物浸渍于一定浓度的二茂铬正己烷溶液中,有机铬的负载量相对于催化剂总重量符合本发明要求(例如cr为0.5~2wt%),浸渍温度为45~50℃,浸渍时间为4~8h,浸渍结束后进行升温干燥,干燥温度为75~90℃,干燥时间为4~8h,整个浸渍和干燥过程可施加搅拌,干燥结束后在氮气保护下将催化剂转移至无水无氧条件下保存。往容积为2l的高压聚合釜中导入1l异戊烷,随后在氮气保护下往聚合釜中加入0.1g催化剂前驱体,同时导入3mpa的乙烯分压,并在100℃下进行催化剂前驱体的原位活化和后续的聚合反应。本发明提供制备负载型三中心催化剂的方法,其中一种方法包含如下步骤:(i)将多孔无机载体浸渍于含铬源的溶液,然后干燥,接着在高温300~900℃下焙烧活化;(ii)将(i)中所得焙烧产物浸渍于含钒源的溶液,然后干燥,接着在高温300~900℃下焙烧活化;(iii)将(ii)中所得焙烧产物浸渍于含有机铬铬源的溶液,然后干燥,得到所述催化剂前驱体保存备用;(iv)将(iii)中所得催化剂前驱体浸渍于金属有机助催化剂溶液中进行预还原活化,得到所述催化剂。根据一个优选的制备负载型三活性中心乙烯聚合催化剂的方法包含步骤:a)将含铬源的溶液通过浸渍的方法吸附于多孔无机载体表面,浸渍时间为1~24h,优选4~12h,浸渍温度为20~120℃,优选45~90℃,然后在60~150℃之间干燥,优选80~130℃,干燥时间2~24h,优选6~16h,干燥过程中也可以采用真空,然后将干燥后混合物置于惰性气体或者含氧气氛中进行高温焙烧活化,焙烧温度在300~900℃,优选400~600℃,焙烧时间为2~24h,优选4~12h,然后自然冷却至室温后保存备用。b)将上述焙烧产物浸渍于含钒源的溶液,浸渍时间为1~24h,优选4~12h,浸渍温度为20~120℃,优选45~90℃,然后在60~150℃之间干燥,优选80~130℃,干燥时间2~24h,优选6~16h,干燥过程中也可以采用真空,然后将干燥后混合物置于惰性气体或者含氧气氛中进行高温焙烧活化,焙烧温度在300~900℃,优选400~800℃,焙烧时间为2~24h,优选4~12h,然后进行冷却,在冷却至300~400℃时将气氛切换成惰性气体,自然冷却至室温后保存备用。c)将上述焙烧产物置于含有机铬铬源的溶液中进行浸渍反应,浸渍反应时间为1~24h,优选4~8h,浸渍温度为20~120℃,优选45~80℃,然后在60~150℃之间干燥,优选80~130℃,干燥时间2~24h,优选6~16h,干燥过程中也可以采用真空,干燥结束后即得所述催化剂前驱体。d)将上述催化剂前驱体置于含有有机金属助催化剂的溶液中进行浸渍反应,浸渍是在惰性气体保护下以有机溶剂为介质进行,预还原活化处理的温度为室温~100℃之间,优选室温~60℃之间;预还原活化处理的时间为0.5~20h,优选0.5~10h;预还原活化处理采用搅拌方式,优选连续搅拌,处理完毕后再在60~120℃之间干燥2~8h,干燥也在氮气或惰性气体气氛下进行,例如在氮气、氦气、氩气等气氛下进行,优选在氮气气氛下进行,该干燥过程也可在真空条件下进行;有机金属助催化剂的加入量满足有机金属助催化剂/总铬摩尔比在0~1000之间,优选0~100,更优选0~50;作为一个实例,制备本发明催化剂的具体操作包括:将多孔无定形sio2/al2o3载体浸渍在一定浓度的醋酸铬水溶液中,铬的负载量相对于催化剂总重量符合本发明的要求(例如cr为0.2~0.8wt%);在连续搅拌一定时间(例如4~8小时)后,升温干燥;然后在流化床内进行高温焙烧,其中焙烧第一阶段为升温阶段(例如100~150℃),在氮气气氛中焙烧脱除载体中吸附的物理水;焙烧第二阶段为升温阶段(例如150~500℃),在干燥空气中焙烧脱除硅胶表面的部分羟基,同时醋酸铬部分氧化分解;焙烧第三阶段为恒温阶段(例如500℃下恒温4~12h),在干燥空气中焙烧,以进一步脱除硅胶表面的羟基,同时使醋酸铬几乎完全氧化分解;焙烧第四阶段为自然降温冷却阶段,冷却至室温时将焙烧产物收集备用。将上述焙烧产物浸渍在一定浓度的偏钒酸铵水溶液中,钒的负载量相对于催化剂总重量符合本发明的要求(例如v为0.5~3wt%);在连续搅拌一定时间(例如4~8小时)后,升温干燥;然后在流化床内进行高温焙烧,其中焙烧第一阶段为升温阶段(例如100~150℃),在氮气气氛中焙烧脱除载体中吸附的物理水;焙烧第二阶段为升温阶段(例如150~800℃),在干燥空气中焙烧脱除硅胶表面的部分羟基,同时偏钒酸铵部分氧化分解;焙烧第三阶段为恒温阶段(例如800℃下恒温4~12h),在干燥空气中焙烧,以进一步脱除硅胶表面的羟基,同时使偏钒酸铵几乎完全氧化分解;焙烧第四阶段为自然降温冷却阶段,在冷却至300~400℃时切换为氮气保护,在氮气保护下转移保存备用。将上述焙烧产物浸渍于一定浓度的二茚铬正庚烷溶液中,有机铬的负载量相对于催化剂总重量符合本发明要求(例如cr为0.5~2wt%),浸渍温度为45~60℃,浸渍时间为4~8h,浸渍结束后进行升温干燥,干燥温度为90~100℃,干燥时间为4~8h,整个浸渍和干燥过程可施加搅拌,干燥结束后在氮气保护下将催化剂转移至1mol/l的三乙基铝正己烷溶液中,并且铝与总铬含量的摩尔比为5/1,预还原活化处理的温度为50℃;预还原活化处理的时间为2h;预还原活化处理采用连续搅拌加强反应,处理完毕后再在80℃下氮气氛围中干燥4h,最终得到所述目标催化剂。本发明提供制备负载型三中心催化剂的方法,其中一种方法包含如下步骤:(i)将多孔无机载体浸渍于含铬源、钒源和q组分的溶液,然后干燥,接着在高温300~900℃下焙烧活化;(ii)将(i)中所得焙烧产物浸渍于含有机铬铬源的溶液,然后干燥,得到所述催化剂前驱体保存备用。(iii)将(ii)中所得催化剂前驱体浸渍于金属有机助催化剂溶液中进行预还原活化,得到所述催化剂。根据一个优选的制备负载型三活性中心乙烯聚合催化剂的方法包含步骤:a)将含铬源、钒源和q组分的溶液通过共浸渍的方法吸附于多孔无机载体表面,浸渍时间为1~24h,优选4~12h,浸渍温度为20~120℃,优选45~90℃,然后在60~150℃之间干燥,优选80~130℃,干燥时间2~24h,优选6~16h,干燥过程中也可以采用真空,然后将干燥后混合物置于惰性气体或者含氧气氛中进行高温焙烧活化,焙烧温度在300~900℃,优选400~800℃,焙烧时间为2~24h,优选4~12h,然后进行冷却,在冷却至300~400℃时将气氛切换成惰性气体,自然冷却至室温后保存备用。b)将上述焙烧产物置于含有机铬铬源的溶液中进行浸渍反应,浸渍反应时间为1~24h,优选4~8h,浸渍温度为20~120℃,优选45~80℃,然后在60~150℃之间干燥,优选80~130℃,干燥时间2~24h,优选6~16h,干燥过程中也可以采用真空,干燥结束后即得所述催化剂前驱体。c)将上述催化剂前驱体置于含有有机金属助催化剂的溶液中进行浸渍反应,浸渍是在惰性气体保护下以有机溶剂为介质进行,预还原活化处理的温度为室温~100℃之间,优选室温~60℃之间;预还原活化处理的时间为0.5~20h,优选0.5~10h;预还原活化处理采用搅拌方式,优选连续搅拌,处理完毕后再在60~120℃之间干燥2~8h,干燥也在氮气或惰性气体气氛下进行,例如在氮气、氦气、氩气等气氛下进行,优选在氮气气氛下进行,该干燥过程也可在真空条件下进行;有机金属助催化剂的加入量满足有机金属助催化剂/总铬摩尔比在0~1000之间,优选0~100,更优选0~50;作为一个实例,制备本发明催化剂的具体操作包括:将多孔无定形sio2/tio2载体浸渍在一定浓度的硝酸钒、碱式醋酸铬和硫酸的水溶液中,钒、铬和硫的负载量相对于催化剂总重量符合本发明的要求(例如v为0.1~10wt%,cr为0.1~2wt%,s为1~5wt%);在连续搅拌一定时间(例如4~8小时)后,升温干燥;然后在流化床内进行高温焙烧,其中焙烧第一阶段为升温阶段(例如100~150℃),在氮气气氛中焙烧脱除载体中吸附的物理水;焙烧第二阶段为升温阶段(例如150~800℃),在干燥空气中焙烧脱除硅胶表面的部分羟基,同时硝酸钒、碱式醋酸铬和硫酸部分氧化分解;焙烧第三阶段为恒温阶段(例如800℃下恒温4~12h),在干燥空气中焙烧,以进一步脱除硅胶表面的羟基,同时使硝酸钒、碱式醋酸铬和硫酸几乎完全氧化分解;焙烧第四阶段为自然降温冷却阶段,在冷却至300~400℃时切换为氮气保护,在氮气保护下转移保存备用。将上述焙烧产物浸渍于一定浓度的二茂铬正己烷溶液中,有机铬的负载量相对于催化剂总重量符合本发明要求(例如cr为0.3~1wt%),浸渍温度为45~50℃,浸渍时间为4~8h,浸渍结束后再加入1mol/l的一氯二乙基铝的正己烷溶液,使铝与总铬含量的摩尔比为3/1,预还原活化处理的温度为50℃;预还原活化处理的时间为2h;预还原活化处理采用连续搅拌加强反应,处理完毕后再在80℃下氮气氛围中干燥4h,最终得到所述目标催化剂。本发明提供制备负载型三中心催化剂的方法,其中一种方法包含如下步骤:(i)将多孔无机载体浸渍于含钒源和q组分的溶液,然后干燥,接着在高温300~900℃下焙烧活化;(ii)将(i)中所得焙烧产物浸渍于含铬源的溶液,然后干燥,接着在高温300~900℃下焙烧活化;(iii)将(ii)中所得焙烧产物浸渍于含有机铬铬源的溶液,然后干燥,得到所述催化剂前驱体保存备用。(iv)将(iii)中所得催化剂前驱体浸渍于金属有机助催化剂溶液中进行预还原活化,得到所述催化剂。根据一个优选的制备负载型三活性中心乙烯聚合催化剂的方法包含步骤:a)将含钒源和q组分的溶液通过浸渍的方法吸附于多孔无机载体表面,浸渍时间为1~24h,优选4~12h,浸渍温度为20~120℃,优选45~90℃,然后在60~150℃之间干燥,优选80~130℃,干燥时间2~24h,优选6~16h,干燥过程中也可以采用真空,然后将干燥后混合物置于惰性气体或者含氧气氛中进行高温焙烧活化,焙烧温度在300~900℃,优选400~600℃,焙烧时间为2~24h,优选4~12h,然后自然冷却至室温后保存备用。b)将上述焙烧产物浸渍于含铬源的溶液,浸渍时间为1~24h,优选4~12h,浸渍温度为20~120℃,优选45~90℃,然后在60~150℃之间干燥,优选80~130℃,干燥时间2~24h,优选6~16h,干燥过程中也可以采用真空,然后将干燥后混合物置于惰性气体或者含氧气氛中进行高温焙烧活化,焙烧温度在300~900℃,优选400~800℃,焙烧时间为2~24h,优选4~12h,然后进行冷却,在冷却至300~400℃时将气氛切换成惰性气体,自然冷却至室温后保存备用。c)将上述焙烧产物置于含有机铬铬源的溶液中进行浸渍反应,浸渍反应时间为1~24h,优选4~8h,浸渍温度为20~120℃,优选45~80℃,然后在60~150℃之间干燥,优选80~130℃,干燥时间2~24h,优选6~16h,干燥过程中也可以采用真空,干燥结束后即得所述催化剂前驱体。d)将上述催化剂前驱体置于含有有机金属助催化剂的溶液中进行浸渍反应,浸渍是在惰性气体保护下以有机溶剂为介质进行,预还原活化处理的温度为室温~100℃之间,优选室温~60℃之间;预还原活化处理的时间为0.5~20h,优选0.5~10h;预还原活化处理采用搅拌方式,优选连续搅拌,处理完毕后再在60~120℃之间干燥2~8h,干燥也在氮气或惰性气体气氛下进行,例如在氮气、氦气、氩气等气氛下进行,优选在氮气气氛下进行,该干燥过程也可在真空条件下进行;有机金属助催化剂的加入量满足有机金属助催化剂/总铬摩尔比在0~1000之间,优选0~100,更优选0~50;作为一个实例,制备本发明催化剂的具体操作包括:将多孔无定形sio2/nb2o5载体浸渍在一定浓度的偏钒酸铵和硫酸铵水溶液中,钒和硫的负载量相对于催化剂总重量符合本发明的要求(例如v为0.1~10wt%,s为1~3wt%);在连续搅拌一定时间(例如4~8小时)后,升温干燥;然后在流化床内进行高温焙烧,其中焙烧第一阶段为升温阶段(例如100~150℃),在氮气气氛中焙烧脱除载体中吸附的物理水;焙烧第二阶段为升温阶段(例如150~500℃),在干燥空气中焙烧脱除硅胶表面的部分羟基,同时偏钒酸铵和硫酸铵部分氧化分解;焙烧第三阶段为恒温阶段(例如500℃下恒温4~12h),在干燥空气中焙烧,以进一步脱除硅胶表面的羟基,同时使偏钒酸铵和硫酸铵几乎完全氧化分解;焙烧第四阶段为自然降温冷却阶段,冷却至室温时将焙烧产物收集备用。将上述焙烧产物浸渍在一定浓度的硝酸铬水溶液中,铬的负载量相对于催化剂总重量符合本发明的要求(例如铬为0.2~1wt%);在连续搅拌一定时间(例如4~8小时)后,升温干燥;然后在流化床内进行高温焙烧,其中焙烧第一阶段为升温阶段(例如100~150℃),在氮气气氛中焙烧脱除载体中吸附的物理水;焙烧第二阶段为升温阶段(例如150~800℃),在干燥空气中焙烧脱除硅胶表面的部分羟基,同时硝酸铬部分氧化分解;焙烧第三阶段为恒温阶段(例如800℃下恒温4~12h),在干燥空气中焙烧,以进一步脱除硅胶表面的羟基,同时使硝酸铬几乎完全氧化分解;焙烧第四阶段为自然降温冷却阶段,在冷却至300~400℃时切换为氮气保护,在氮气保护下转移保存备用。将上述焙烧产物浸渍于一定浓度的二茚基铬正己烷溶液中,有机铬的负载量相对于催化剂总重量符合本发明要求(例如cr为0.5~2wt%),浸渍温度为45~50℃,浸渍时间为4~8h,浸渍结束后再加入1mol/l的甲基铝氧烷的甲苯溶液,使铝与总铬含量的摩尔比为300/1,预还原活化处理的温度为50℃;预还原活化处理的时间为2h;预还原活化处理采用连续搅拌加强反应,处理完毕后再在120℃下氮气氛围中干燥4h,最终得到所述目标催化剂。本发明提供制备负载型三中心催化剂的方法,其中一种方法包含如下步骤:(i)将多孔无机载体浸渍于含铬源和q组分的溶液,然后干燥,接着在高温300~900℃下焙烧活化;(ii)将(i)中所得焙烧产物浸渍于含钒源的溶液,然后干燥,接着在高温300~900℃下焙烧活化;(iii)将(ii)中所得焙烧产物浸渍于含有机铬铬源的溶液,然后干燥,得到所述催化剂前驱体保存备用。(iv)往高压聚合釜中依次引入一定量溶剂、有机金属助催化剂溶液和乙烯单体,随后称取一定量(iii)中所述催化剂前驱体,并导入聚合釜中,助催化剂原位还原催化剂前驱体得到所述目标催化剂,随后催化乙烯聚合。根据一个优选的制备负载型三活性中心乙烯聚合催化剂的方法包含步骤:a)将含铬源和q组分的溶液通过浸渍的方法吸附于多孔无机载体表面,浸渍时间为1~24h,优选4~12h,浸渍温度为20~120℃,优选45~90℃,然后在60~150℃之间干燥,优选80~130℃,干燥时间2~24h,优选6~16h,干燥过程中也可以采用真空,然后将干燥后混合物置于惰性气体或者含氧气氛中进行高温焙烧活化,焙烧温度在300~900℃,优选400~600℃,焙烧时间为2~24h,优选4~12h,然后自然冷却至室温后保存备用。b)将上述焙烧产物浸渍于含钒源的溶液,浸渍时间为1~24h,优选4~12h,浸渍温度为20~120℃,优选45~90℃,然后在60~150℃之间干燥,优选80~130℃,干燥时间2~24h,优选6~16h,干燥过程中也可以采用真空,然后将干燥后混合物置于惰性气体或者含氧气氛中进行高温焙烧活化,焙烧温度在300~900℃,优选400~800℃,焙烧时间为2~24h,优选4~12h,然后进行冷却,在冷却至300~400℃时将气氛切换成惰性气体,自然冷却至室温后保存备用。c)将上述焙烧产物置于含有机铬铬源的溶液中进行浸渍反应,浸渍反应时间为1~24h,优选4~8h,浸渍温度为20~120℃,优选45~80℃,然后在60~150℃之间干燥,优选80~130℃,干燥时间2~24h,优选6~16h,干燥过程中也可以采用真空,干燥结束后即得所述催化剂前驱体。d)往高压聚合釜中依次导入一定量溶剂、有机金属助催化剂、乙烯单体和(c)所述催化剂前驱体开始催化剂活化以及乙烯聚合反应,溶剂介质可选自异戊烷、正己烷、正庚烷、正辛烷和甲苯,优选异戊烷或正己烷,有机金属助催化剂可选自烷基铝及其衍生物、烷基锂、烷基硼,优选烷基铝,有机金属助催化剂与铬总量的摩尔比为0-1000,优选10-30,催化剂活化与聚合温度为50-110℃,优选60-80℃,乙烯单体压力为0.5-5mpa,优选1-3mpa。作为一个实例,制备本发明催化剂的具体操作包括:将多孔无定形sio2/al2o3载体浸渍在一定浓度的醋酸铬和硅氟酸铵水溶液中,铬和氟的负载量相对于催化剂总重量符合本发明的要求(例如cr为0.2~0.8wt%,f为0.5~2wt%);在连续搅拌一定时间(例如4~8小时)后,升温干燥;然后在流化床内进行高温焙烧,其中焙烧第一阶段为升温阶段(例如100~150℃),在氮气气氛中焙烧脱除载体中吸附的物理水;焙烧第二阶段为升温阶段(例如150~500℃),在干燥空气中焙烧脱除硅胶表面的部分羟基,同时醋酸铬和硅氟酸铵部分氧化分解;焙烧第三阶段为恒温阶段(例如500℃下恒温4~12h),在干燥空气中焙烧,以进一步脱除硅胶表面的羟基,同时使醋酸铬和硅氟酸铵几乎完全氧化分解;焙烧第四阶段为自然降温冷却阶段,冷却至室温时将焙烧产物收集备用。将上述焙烧产物浸渍在一定浓度的偏钒酸铵水溶液中,钒的负载量相对于催化剂总重量符合本发明的要求(例如v为0.5~3wt%);在连续搅拌一定时间(例如4~8小时)后,升温干燥;然后在流化床内进行高温焙烧,其中焙烧第一阶段为升温阶段(例如100~150℃),在氮气气氛中焙烧脱除载体中吸附的物理水;焙烧第二阶段为升温阶段(例如150~800℃),在干燥空气中焙烧脱除硅胶表面的部分羟基,同时偏钒酸铵部分氧化分解;焙烧第三阶段为恒温阶段(例如800℃下恒温4~12h),在干燥空气中焙烧,以进一步脱除硅胶表面的羟基,同时使偏钒酸铵几乎完全氧化分解;焙烧第四阶段为自然降温冷却阶段,在冷却至300~400℃时切换为氮气保护,在氮气保护下转移保存备用。将上述焙烧产物浸渍于一定浓度的二茚铬正庚烷溶液中,有机铬的负载量相对于催化剂总重量符合本发明要求(例如cr为0.5~2wt%),浸渍温度为45~60℃,浸渍时间为4~8h,浸渍结束后进行升温干燥,干燥温度为90~100℃,干燥时间为4~8h,整个浸渍和干燥过程可施加搅拌,干燥结束后在氮气保护下将催化剂转移至无水无氧条件下保存。随后在氮气保护下依次往容积为2l的高压聚合釜中导入1l异戊烷、一定量1mol/l三异丁基铝正己烷溶液、3mpa乙烯分压和一定量催化剂前驱体,使铝与铬总量的摩尔比为10/1,并在100℃下进行催化剂前驱体的原位活化和后续的聚合反应。本发明提供制备负载型三中心催化剂的方法,其中一种方法包含如下步骤:(i)将多孔无机载体浸渍于含钒源的溶液,然后干燥,接着在高温300~900℃下焙烧活化;(ii)将(i)中所得焙烧产物浸渍于含铬源和q组分的溶液,然后干燥,接着在高温300~900℃下焙烧活化;(iii)将(ii)中所得焙烧产物浸渍于含有机铬铬源的溶液,然后干燥,得到所述催化剂前驱体。(iv)往高压聚合釜中依次引入一定量溶剂、有机金属助催化剂溶液和乙烯单体,随后称取一定量(iii)中所述催化剂前驱体,并导入聚合釜中,助催化剂原位还原催化剂前驱体得到所述目标催化剂,随后催化乙烯聚合。根据一个优选的制备负载型三活性中心乙烯聚合催化剂的方法包含步骤:a)将含钒源的溶液通过浸渍的方法吸附于多孔无机载体表面,浸渍时间为1~24h,优选4~12h,浸渍温度为20~120℃,优选45~90℃,然后在60~150℃之间干燥,优选80~130℃,干燥时间2~24h,优选6~16h,干燥过程中也可以采用真空,然后将干燥后混合物置于惰性气体或者含氧气氛中进行高温焙烧活化,焙烧温度在300~900℃,优选400~600℃,焙烧时间为2~24h,优选4~12h,然后自然冷却至室温后保存备用。b)将上述焙烧产物浸渍于含铬源和q组分的溶液,浸渍时间为1~24h,优选4~12h,浸渍温度为20~120℃,优选45~90℃,然后在60~150℃之间干燥,优选80~130℃,干燥时间2~24h,优选6~16h,干燥过程中也可以采用真空,然后将干燥后混合物置于惰性气体或者含氧气氛中进行高温焙烧活化,焙烧温度在300~900℃,优选400~800℃,焙烧时间为2~24h,优选4~12h,然后进行冷却,在冷却至300~400℃时将气氛切换成惰性气体,自然冷却至室温后保存备用。c)将上述焙烧产物置于含有机铬铬源的溶液中进行浸渍反应,浸渍反应时间为1~24h,优选4~8h,浸渍温度为20~120℃,优选45~80℃,然后在60~150℃之间干燥,优选80~130℃,干燥时间2~24h,优选6~16h,干燥过程中也可以采用真空,干燥结束后即得所述催化剂前驱体。d)往高压聚合釜中依次导入一定量溶剂、有机金属助催化剂、乙烯单体和(c)所述催化剂前驱体开始催化剂活化以及乙烯聚合反应,溶剂介质可选自异戊烷、正己烷、正庚烷、正辛烷和甲苯,优选异戊烷或正己烷,有机金属助催化剂可选自烷基铝及其衍生物、烷基锂、烷基硼,优选烷基铝,有机金属助催化剂与铬总量的摩尔比为0-1000,优选10-30,催化剂活化与聚合温度为50-110℃,优选60-80℃,乙烯单体压力为0.5-5mpa,优选1-3mpa。作为一个实例,制备本发明催化剂的具体操作包括:将多孔无定形硅胶浸渍在一定浓度的偏钒酸铵水溶液中,钒的负载量相对于催化剂总重量符合本发明的要求(例如v为0.1~10wt%);在连续搅拌一定时间(例如4~8小时)后,升温干燥;然后在流化床内进行高温焙烧,其中焙烧第一阶段为升温阶段(例如100~150℃),在氮气气氛中焙烧脱除载体中吸附的物理水;焙烧第二阶段为升温阶段(例如150~500℃),在干燥空气中焙烧脱除硅胶表面的部分羟基,同时偏钒酸铵部分氧化分解;焙烧第三阶段为恒温阶段(例如500℃下恒温4~12h),在干燥空气中焙烧,以进一步脱除硅胶表面的羟基,同时使偏钒酸铵几乎完全氧化分解;焙烧第四阶段为自然降温冷却阶段,冷却至室温时将焙烧产物收集备用。将上述焙烧产物浸渍在一定浓度的硝酸铬和磷酸铵水溶液中,铬和磷的负载量相对于催化剂总重量符合本发明的要求(例如铬为0.2~1wt%,p为0.5~2wt%);在连续搅拌一定时间(例如4~8小时)后,升温干燥;然后在流化床内进行高温焙烧,其中焙烧第一阶段为升温阶段(例如100~150℃),在氮气气氛中焙烧脱除载体中吸附的物理水;焙烧第二阶段为升温阶段(例如150~800℃),在干燥空气中焙烧脱除硅胶表面的部分羟基,同时硝酸铬和磷酸铵部分氧化分解;焙烧第三阶段为恒温阶段(例如800℃下恒温4~12h),在干燥空气中焙烧,以进一步脱除硅胶表面的羟基,同时使硝酸铬和磷酸铵几乎完全氧化分解;焙烧第四阶段为自然降温冷却阶段,在冷却至300~400℃时切换为氮气保护,在氮气保护下转移保存备用。将上述焙烧产物浸渍于一定浓度的二芴基铬正己烷溶液中,有机铬的负载量相对于催化剂总重量符合本发明要求(例如cr为0.5~2wt%),浸渍温度为45~50℃,浸渍时间为4~8h,浸渍结束后进行升温干燥,干燥温度为75~90℃,干燥时间为4~8h,整个浸渍和干燥过程可施加搅拌,干燥结束后在氮气保护下将催化剂转移至无水无氧条件下保存。随后在氮气保护下依次往容积为2l的高压聚合釜中导入1l异戊烷、一定量1mol/l三乙基基铝正己烷溶液、1mpa乙烯分压和一定量催化剂前驱体,使铝与铬总量的摩尔比为4/1,并在100℃下进行催化剂前驱体的原位活化和后续的聚合反应。本发明提供制备负载型三中心催化剂的方法,其中一种方法包含如下步骤:(i)将多孔无机载体浸渍于含铬源的溶液,然后干燥,接着在高温300~900℃下焙烧活化;(ii)将(i)中所得焙烧产物浸渍于含钒源和q组分的溶液,然后干燥,接着在高温300~900℃下焙烧活化;(iii)将(ii)中所得焙烧产物浸渍于含有机铬铬源的溶液,然后干燥,得到所述催化剂前驱体。(iv)往高压聚合釜中依次引入一定量溶剂、有机金属助催化剂溶液和乙烯单体,随后称取一定量(iii)中所述催化剂前驱体,并导入聚合釜中,助催化剂原位还原催化剂前驱体得到所述目标催化剂,随后催化乙烯聚合。根据一个优选的制备负载型三活性中心乙烯聚合催化剂的方法包含步骤:a)将含铬源的溶液通过浸渍的方法吸附于多孔无机载体表面,浸渍时间为1~24h,优选4~12h,浸渍温度为20~120℃,优选45~90℃,然后在60~150℃之间干燥,优选80~130℃,干燥时间2~24h,优选6~16h,干燥过程中也可以采用真空,然后将干燥后混合物置于惰性气体或者含氧气氛中进行高温焙烧活化,焙烧温度在300~900℃,优选400~600℃,焙烧时间为2~24h,优选4~12h,然后自然冷却至室温后保存备用。b)将上述焙烧产物浸渍于含钒源和q组分的溶液,浸渍时间为1~24h,优选4~12h,浸渍温度为20~120℃,优选45~90℃,然后在60~150℃之间干燥,优选80~130℃,干燥时间2~24h,优选6~16h,干燥过程中也可以采用真空,然后将干燥后混合物置于惰性气体或者含氧气氛中进行高温焙烧活化,焙烧温度在300~900℃,优选400~800℃,焙烧时间为2~24h,优选4~12h,然后进行冷却,在冷却至300~400℃时将气氛切换成惰性气体,自然冷却至室温后保存备用。c)将上述焙烧产物置于含有机铬铬源溶液中进行浸渍反应,浸渍反应时间为1~24h,优选4~8h,浸渍温度为20~120℃,优选45~80℃,然后在60~150℃之间干燥,优选80~130℃,干燥时间2~24h,优选6~16h,干燥过程中也可以采用真空,干燥结束后即得所述催化剂前驱体。d)往高压聚合釜中依次导入一定量溶剂、有机金属助催化剂、乙烯单体和(c)所述催化剂前驱体开始催化剂活化以及乙烯聚合反应,溶剂介质可选自异戊烷、正己烷、正庚烷、正辛烷和甲苯,优选异戊烷或正己烷,有机金属助催化剂可选自烷基铝及其衍生物、烷基锂、烷基硼,优选烷基铝,有机金属助催化剂与铬总量的摩尔比为0-1000,优选10-30,催化剂活化与聚合温度为50-110℃,优选60-80℃,乙烯单体压力为0.5-5mpa,优选1-3mpa。作为一个实例,制备本发明催化剂的具体操作包括:将多孔无定形sio2/al2o3载体浸渍在一定浓度的醋酸铬水溶液中,铬的负载量相对于催化剂总重量符合本发明的要求(例如cr为0.2~0.8wt%);在连续搅拌一定时间(例如4~8小时)后,升温干燥;然后在流化床内进行高温焙烧,其中焙烧第一阶段为升温阶段(例如100~150℃),在氮气气氛中焙烧脱除载体中吸附的物理水;焙烧第二阶段为升温阶段(例如150~500℃),在干燥空气中焙烧脱除硅胶表面的部分羟基,同时醋酸铬部分氧化分解;焙烧第三阶段为恒温阶段(例如500℃下恒温4~12h),在干燥空气中焙烧,以进一步脱除硅胶表面的羟基,同时使醋酸铬几乎完全氧化分解;焙烧第四阶段为自然降温冷却阶段,冷却至室温时将焙烧产物收集备用。将上述焙烧产物浸渍在一定浓度的偏钒酸铵和硅氟酸铵水溶液中,钒和氟的负载量相对于催化剂总重量符合本发明的要求(例如v为0.5~3wt%,f为1~3wt%);在连续搅拌一定时间(例如4~8小时)后,升温干燥;然后在流化床内进行高温焙烧,其中焙烧第一阶段为升温阶段(例如100~150℃),在氮气气氛中焙烧脱除载体中吸附的物理水;焙烧第二阶段为升温阶段(例如150~800℃),在干燥空气中焙烧脱除硅胶表面的部分羟基,同时偏钒酸铵和硅氟酸铵部分氧化分解;焙烧第三阶段为恒温阶段(例如800℃下恒温4~12h),在干燥空气中焙烧,以进一步脱除硅胶表面的羟基,同时使偏钒酸铵和硅氟酸铵几乎完全氧化分解;焙烧第四阶段为自然降温冷却阶段,在冷却至300~400℃时切换为氮气保护,在氮气保护下转移保存备用。将上述焙烧产物浸渍于一定浓度的二茂铬正庚烷溶液中,有机铬的负载量相对于催化剂总重量符合本发明要求(例如cr为0.5~2wt%),浸渍温度为45~60℃,浸渍时间为4~8h,浸渍结束后进行升温干燥,干燥温度为90~100℃,干燥时间为4~8h,整个浸渍和干燥过程可施加搅拌,干燥结束后在氮气保护下将催化剂转移至无水无氧条件下保存。随后在氮气保护下依次往容积为2l的高压聚合釜中导入1l异戊烷、一定量1mol/l三异丁基铝正己烷溶液、1mpa乙烯分压和一定量催化剂前驱体,使铝与铬总量的摩尔比为15/1,并在95℃下进行催化剂前驱体的原位活化和后续的聚合反应。本发明提供制备负载型三中心催化剂的方法,其中一种方法包含如下步骤:(i)将多孔无机载体浸渍于含q组分的溶液,干燥,接着在300~900℃下焙烧活化;(ii)将(i)中所得焙烧产物浸渍于含钒源的溶液,然后干燥,接着在300~900℃下焙烧活化;(iii)将(ii)中所得焙烧产物浸渍于含铬源的溶液,干燥,接着在300~900℃下焙烧活化;(iv)将(iii)中所得焙烧产物浸渍于含有机铬铬源的溶液,然后干燥,得到所述催化剂前驱体。(v)往高压聚合釜中依次引入一定量溶剂、有机金属助催化剂溶液和乙烯单体,随后称取一定量(iv)中所述催化剂前驱体,并导入聚合釜中,助催化剂原位还原催化剂前驱体得到所述目标催化剂,随后催化乙烯聚合。根据一个优选的制备负载型三活性中心乙烯聚合催化剂的方法包含步骤:a)将含q组分的溶液通过浸渍的方法吸附于多孔无机载体表面,浸渍时间为1~24h,优选4~12h,浸渍温度为20~120℃,优选45~90℃,然后在60~150℃之间干燥,优选80~130℃,干燥时间2~24h,优选6~16h,干燥过程中也可以采用真空,然后将干燥后混合物置于惰性气体或者含氧气氛中进行高温焙烧活化,焙烧温度在300~900℃,优选350~500℃,焙烧时间为2~24h,优选4~12h,然后自然冷却至室温后保存备用。b)将上述焙烧产物与含钒源的溶液进行浸渍,浸渍时间为1~24h,优选4~12h,浸渍温度为20~120℃,优选45~90℃,然后在60~150℃之间干燥,优选80~130℃,干燥时间2~24h,优选6~16h,干燥过程中也可以采用真空,然后将干燥后混合物置于惰性气体或者含氧气氛中进行高温焙烧活化,焙烧温度在300~900℃,优选400~600℃,焙烧时间为2~24h,优选4~12h,然后自然冷却至室温后保存备用。c)将上述焙烧产物浸渍于含铬源的溶液,浸渍时间为1~24h,优选4~12h,浸渍温度为20~120℃,优选45~90℃,然后在60~150℃之间干燥,优选80~130℃,干燥时间2~24h,优选6~16h,干燥过程中也可以采用真空,然后将干燥后混合物置于惰性气体或者含氧气氛中进行高温焙烧活化,焙烧温度在300~900℃,优选400~800℃,焙烧时间为2~24h,优选4~12h,然后进行冷却,在冷却至300~400℃时将气氛切换成惰性气体,自然冷却至室温后保存备用。d)将上述焙烧产物置于含有机铬铬源的溶液中进行浸渍反应,浸渍反应时间为1~24h,优选4~8h,浸渍温度为20~120℃,优选45~80℃,然后在60~150℃之间干燥,优选80~130℃,干燥时间2~24h,优选6~16h,干燥过程中也可以采用真空,干燥结束后即得所述催化剂前驱体。e)往高压聚合釜中依次导入一定量溶剂、有机金属助催化剂、乙烯单体和(d)所述催化剂前驱体开始催化剂活化以及乙烯聚合反应,溶剂介质可选自异戊烷、正己烷、正庚烷、正辛烷和甲苯,优选异戊烷或正己烷,有机金属助催化剂可选自烷基铝及其衍生物、烷基锂、烷基硼,优选烷基铝,有机金属助催化剂与铬总量的摩尔比为0-1000,优选10-30,催化剂活化与聚合温度为50-110℃,优选60-80℃,乙烯单体压力为0.5-5mpa,优选1-3mpa。作为一个实例,制备本发明催化剂的具体操作包括:将多孔无定形sio2载体浸渍在一定浓度的磷酸铵水溶液中,磷的负载量相对于催化剂总重量符合本发明的要求(例如磷为1~2wt%);在连续搅拌一定时间(例如4~8小时)后,升温干燥;然后在流化床内进行高温焙烧,其中焙烧第一阶段为升温阶段(例如100~150℃),在氮气气氛中焙烧脱除载体中吸附的物理水;焙烧第二阶段为升温阶段(例如150~500℃),在干燥空气中焙烧脱除硅胶表面的部分羟基,同时磷酸铵分解为催化剂改性组分;焙烧第三阶段为恒温阶段(例如500℃下恒温4~12h),在干燥空气中焙烧,以进一步脱除硅胶表面的羟基,同时使磷酸铵进一步分解;焙烧第四阶段为自然降温冷却阶段,冷却至室温时将焙烧产物收集备用。将上述焙烧产物浸渍在一定浓度的偏钒酸铵水溶液中,钒的负载量相对于催化剂总重量符合本发明的要求(例如v为0.5~3wt%);在连续搅拌一定时间(例如4~8小时)后,升温干燥;然后在流化床内进行高温焙烧,其中焙烧第一阶段为升温阶段(例如100~150℃),在氮气气氛中焙烧脱除载体中吸附的物理水;焙烧第二阶段为升温阶段(例如150~500℃),在干燥空气中焙烧脱除硅胶表面的部分羟基,同时偏钒酸铵部分氧化分解;焙烧第三阶段为恒温阶段(例如500℃下恒温4~12h),在干燥空气中焙烧,以进一步脱除硅胶表面的羟基,同时使偏钒酸铵几乎完全氧化分解;焙烧第四阶段为自然降温冷却阶段,冷却至室温时保存在干燥环境下备用。将上述焙烧产物浸渍在一定浓度的碱式醋酸铬水溶液中,铬的负载量相对于催化剂总重量符合本发明的要求(例如cr为0.5~1wt%);在连续搅拌一定时间(例如4~8小时)后,升温干燥;然后在流化床内进行高温焙烧,其中焙烧第一阶段为升温阶段(例如100~150℃),在氮气气氛中焙烧脱除载体中吸附的物理水;焙烧第二阶段为升温阶段(例如150~500℃),在干燥空气中焙烧脱除硅胶表面的部分羟基,同时碱式醋酸铬部分氧化分解;焙烧第三阶段为恒温阶段(例如500℃下恒温4~12h),在干燥空气中焙烧,以进一步脱除硅胶表面的羟基,同时使碱式醋酸铬几乎完全氧化分解;焙烧第四阶段为自然降温冷却阶段,在冷却至200~300℃时切换为氮气保护,在氮气保护下转移保存备用。将上述焙烧产物浸渍于一定浓度的二茚基铬正庚烷溶液中,有机铬的负载量相对于催化剂总重量符合本发明要求(例如cr为0.5~2wt%),浸渍温度为45~60℃,浸渍时间为4~8h,浸渍结束后进行升温干燥,干燥温度为90~100℃,干燥时间为4~8h,整个浸渍和干燥过程可施加搅拌,干燥结束后在氮气保护下将催化剂转移至无水无氧条件下保存。随后在氮气保护下依次往容积为2l的高压聚合釜中导入1l异戊烷、一定量1mol/l三异丁基铝正己烷溶液、2mpa乙烯分压和一定量催化剂前驱体,使铝与铬总量的摩尔比为10/1,并在105℃下进行催化剂前驱体的原位活化和后续的聚合反应。上述的负载型三中心催化剂乙烯在催化烯烃聚合中的应用,尤其是在催化乙烯的均聚或乙烯与α-烯烃的共聚中的应用。所述的烯烃一般包含乙烯单体,还可以包含共聚单体;所述共聚单体可以是具有3~20个碳原子的α-烯烃,例如丙烯、1-丁烯、1-戊烯、1-己烯、1-庚烯、1-辛烯、1-壬烯、1-癸烯、1-十二碳烯、1-甲基-1-戊烯、4-甲基-1-己烯等,这些可以单独使用或两种或更多种组合使用。所述共聚单体优选为1-丁烯、1-己烯、1-辛烯和1-癸烯中的至少一种;当共聚单体存在时,共聚单体的量一般为0~30vol%,优选0~10vol%,共聚单体的加入量是基于聚合时其相对于溶剂的体积浓度计算。当所述的负载型三中心催化剂用于催化乙烯的均聚或乙烯与α-烯烃的共聚时,所生产的聚乙烯产品具有如下特点:进行乙烯均聚时分子量分布较宽,部分呈三峰分布;进行乙烯与α-烯烃的共聚时,分子量分布较宽,部分呈三峰分布,且含有较低分子量乙烯均聚物、中高分子量乙烯与α-烯烃共聚物以及高分子量或超高分子量乙烯与α-烯烃的共聚物。所述的负载型三中心催化剂乙烯在催化烯烃聚合中的应用,聚合过程中可根据需要添加有机金属助催化剂以及分子量调节剂等;所述有机金属助催化剂可以为有机铝化合物,如三乙基铝、三异丁基铝、二乙基乙氧基铝、一氯二乙基铝和甲基铝氧烷等。所述有机金属铝化合物的用量满足:铝元素和总铬元素的摩尔比为0-1000,优选0-70,更优选0-50;所述的分子量调节可为氢气;所述的负载型三中心催化剂在催化烯烃聚合中的应用,其对聚合的方法没有任何特别的限制,当用于催化乙烯的均聚或乙烯与α-烯烃的共聚时,聚合方法可以包括气相聚合工艺、淤浆聚合工艺、悬浮聚合工艺、本体聚合工艺、溶液聚合工艺等,另外还包括各种形式组合的双釜串联聚合工艺。如本领域技术人员所理解的那样,对采用本发明催化剂的生产烯烃聚合物的方法没有特别限制,可以采用本领域已知的气相聚合工艺、淤浆聚合工艺、悬浮聚合工艺、本体聚合工艺、溶液聚合工艺以及各种形式组合的双釜串联聚合工艺等在常规实施方案和聚合条件下实施。优选的,当使用淤浆聚合工艺进行聚合时,包括向反应釜内加入乙烯,然后加入溶剂和助催化剂(有机铝化合物)并任选地加入氢气和共聚单体,最后加入本发明的负载型三中心催化剂开始聚合。其中所使用的溶剂一般为本领域所公知的用于烯烃聚合的任何溶剂,可为具有3~20个碳原子的烷烃,例如丙烷、正丁烷、异丁烷、正戊烷、异戊烷、新戊烷、正己烷、环己烷、正庚烷、正辛烷等;这些溶剂可以单独使用或可以两种或更多种组合使用。所使用的溶剂优选为异丁烷、异戊烷、正己烷、环己烷、正庚烷等。更优选的,当采用传统的淤浆聚合工艺实施聚合时,具体操作如下:先将聚合反应釜进行真空加热除杂,然后置换为高纯氮气,反复操作三次,再用少量乙烯单体置换一次,并最后将反应釜内充满乙烯至微正压(0.12mpa);向反应釜内加入脱水脱氧处理后的精制溶剂如正庚烷,一定量的烷基铝作为助催化剂,在氢调和共聚实验中还需分别加入一定量的氢气和共聚单体,待乙烯压力调至1mpa,最后加入本发明的催化剂开始聚合反应;反应过程中在线采集单体乙烯的瞬时消耗量并由电脑记录,在一定温度下(例如35℃-100℃)反应进行一定时间(例如1小时)后,加入盐酸/乙醇混合溶液终止反应;聚合物经洗涤,真空干燥后称重并分析。本发明相对于现有技术,具有如下的优点及有益效果:本发明开发了一种负载型的三中心催化剂并用于乙烯聚合。该催化剂中三种活性中心能够较好地表现各自的催化性能,甚至表现出良好的催化协同效应,其相比于传统的单、双中心催化剂而言,主要特征表现为聚合物分子量分布更宽,呈三峰或多峰分布,包含由有机铬活性中心合成的较低分子量乙烯均聚物a,由无机铬活性中心合成的中等分子量乙烯共聚物b以及由无机钒活性中心合成的高分子量或超高分子量乙烯共聚物c,且a、b、c三种组分的相对含量可主要地通过调整催化剂中三种活性中心的相对含量进行调节,可通过改变助催化剂用量、聚合温度、分子量调节剂等聚合条件方便地调整乙烯均聚物和乙烯/α-烯烃共聚物的分子量和分子量分布以及共聚单体含量及分布。显然,相比于三釜串联工艺,利用本发明的负载型三中心催化剂于单釜或串联双釜中合成分子量呈宽峰或三峰分布聚乙烯更加经济、绿色、高效。本发明所述负载型三活性中心催化剂相比于现有的大多数催化剂而言具有如下特点,即本发明的催化剂可在单一反应器或两个串联反应器中生产分子量分布较宽,甚至呈三峰分布的乙烯均聚物和乙烯/α-烯烃共聚物,其含有较低分子量的乙烯均聚物、中高分子量乙烯与α-烯烃共聚物以及高分子量或超高分子量乙烯与α-烯烃的共聚物。该催化剂还具有较高的乙烯均聚和乙烯与α-烯烃共聚反应活性。附图说明图1为三釜串联技术制备三峰聚乙烯产品的高温gpc曲线;图2为本发明实施例16制备的负载型三中心催化剂聚乙烯产品的高温gpc曲线;图3为本发明实施例31与32所得聚合物的gpc-ftir表征曲线;图4为本发明实施例28-2所得聚合物的gpc-ftir表征曲线;图5为本发明实施例30所得聚合物的gpc-ftir表征曲线;图6为本发明实施例14、对比实施例1、对比实施例2和对比实施例3所得聚合物的高温gpc曲线。具体实施方式下面结合实施例和附图对本发明作进一步详细的描述,但本发明的实施方式不限于此。实施例中所用试剂如无特殊说明均可从市场常规购得。实施例中的各种聚合物性质根据以下方法测量:高温凝胶色谱(ht-gpc)重均分子量和分子量分布用高温凝胶色谱测定:本实验采用pl-220型高温凝胶渗透色谱仪(polymerlaboratories公司)来测定聚乙烯分子量及其分子量分布。对于需要分析短支链分布的情况,将采用红外检测器(ir4,polymerchar公司)与ht-gpc联用测定。实验中以1,2,4-三氯苯为溶剂,在160℃下测定。采用窄分布聚苯乙烯作为标样的普适校正法处理数据。13c高温核磁共振谱(ht-13cnmr)聚合物的短支链含量采用高温核磁碳谱测定:本实验采用brukeravanceiii500型核磁共振仪来测定聚乙烯短支链含量。实验中以氘代对二氯苯为溶剂,在110℃下测定,采用聚乙烯主链上的碳信号(位移在30.00ppm)为内标计算短支链含量。实施例1:取10g硅胶(比表面积500m2/g,孔容1.3ml/g,孔径20nm)浸渍在草酸氧钒和碱式醋酸铬的水溶液中(v与cr的负载量相对于催化剂总重量分别为0.25wt%和0.7wt%),连续搅拌浸渍约4h,浸渍温度为60℃,随后升温至120℃,继续搅拌干燥8h。将干燥的混合物置于流化床中从室温开始进行升温焙烧,升温速率为1℃/min,当达到600℃时恒温4h,焙烧结束后开始自然冷却至室温,并转移至无水无氧条件下保存。上述过程中室温至150℃采用氮气气氛,150~600℃的升温阶段采用干空气气氛,600℃的恒温阶段,采用干空气气氛,自然冷却时由600℃降低至300℃时为干空气气氛,当低于300℃时切换至氮气气氛。将上述焙烧产物浸渍于二茂铬的正己烷溶液中(cr的负载量相对于催化剂总重量为1.5wt%),浸渍温度为45℃,浸渍时间为6h,随后进行升温干燥,干燥温度为80℃,干燥时间为4h,浸渍和干燥过程施加搅拌,干燥结束后将催化剂前驱体在氮气保护下转移至无水无氧条件下保存。实施例2:取10gsio2/al2o3(比表面积600m2/g,孔容1.1ml/g,铝含量为5wt%,孔径17nm)浸渍在乙酰丙酮氧钒的乙醇溶液中(v负载量相对于催化剂总重量为0.25wt%),连续搅拌浸渍约4h,浸渍温度为40℃,随后升温至100℃,继续搅拌干燥8h。将干燥的混合物置于流化床中从室温开始进行升温焙烧,升温速率为1℃/min,当达到500℃时恒温4h,焙烧结束后开始自然冷却至室温并保存至干燥环境中待用。上述过程中室温至150℃采用氮气气氛,150~500℃采用干空气气氛,自然冷却时由500℃降低至300℃时为干空气气氛,当低于300℃时切换至氮气气氛。将上述焙烧产物浸渍于碱式醋酸铬的水溶液中(cr负载量相对于催化剂总重量为0.7wt%),连续搅拌浸渍约4h,浸渍温度为45℃,随后升温至120℃,继续搅拌干燥8h。将干燥的混合物置于流化床中从室温开始进行升温焙烧,升温速率为1℃/min,当达到600℃时恒温6h,焙烧结束后开始自然冷却至室温,并转移至无水无氧条件下保存。上述过程中室温至150℃采用氮气气氛,150~600℃采用干空气气氛,自然冷却时由600℃降低至300℃时为干空气气氛,当低于300℃时切换至氮气气氛。将上述焙烧产物浸渍于二茂铬的正己烷溶液中(cr的负载量相对于催化剂总重量为1.5wt%),浸渍温度为45℃,浸渍时间为6h,随后进行升温干燥,干燥温度为80℃,干燥时间为4h,浸渍和干燥过程施加搅拌,干燥结束后将催化剂前驱体在氮气保护下转移至无水无氧条件下保存。实施例3:取10gsio2/tio2(比表面积500m2/g,孔容1.2ml/g,钛含量为5wt%,孔径25nm)浸渍在硝酸铬水溶液中(cr负载量相对于催化剂总重量为0.7wt%),连续搅拌浸渍约4h,浸渍温度为40℃,随后升温至120℃,继续搅拌干燥8h。将干燥的混合物置于流化床中从室温开始进行升温焙烧,升温速率为1℃/min,当达到450℃时恒温4h,焙烧结束后开始自然冷却至室温,并转移至干燥条件下保存。上述过程中室温至150℃采用氮气气氛,150-450℃采用干空气气氛,自然冷却时由450℃降低至300℃时为干空气气氛,当低于300℃时切换至氮气气氛。将上述焙烧产物浸渍于偏钒酸铵水溶液中(v负载量相对于催化剂总重量为0.27wt%),连续搅拌浸渍约4h,浸渍温度为45℃,随后升温至120℃,继续搅拌干燥8h。将干燥的混合物置于流化床中从室温开始进行升温焙烧,升温速率为1℃/min,当达到600℃时恒温6h,焙烧结束后开始自然冷却至室温,并转移至无水无氧条件下保存。上述过程中室温至150℃采用氮气气氛,150~600℃采用干空气气氛,自然冷却时由600℃降低至300℃时为干空气气氛,当低于300℃时切换至氮气气氛。将上述焙烧产物浸渍于二茂铬的正己烷溶液中(cr的负载量相对于催化剂总重量为1.5wt%),浸渍温度为45℃,浸渍时间为6h,随后进行升温干燥,干燥温度为80℃,干燥时间为4h,浸渍和干燥过程施加搅拌,干燥结束后将催化剂前驱体在氮气保护下转移至无水无氧条件下保存。实施例4:取10gsio2/al2o3(比表面积600m2/g,孔容1.1ml/g,铝含量为5wt%,孔径17nm)浸渍在草酸氧钒、碱式醋酸铬和六氟硅酸铵的水溶液中(v、cr和f的负载量相对于催化剂总重量分别为0.25wt%、0.7wt%和2wt%),连续搅拌浸渍约4h,浸渍温度为60℃,随后升温至120℃,继续搅拌干燥8h。将干燥的混合物置于流化床中从室温开始进行升温焙烧,升温速率为1℃/min,当达到600℃时恒温4h,焙烧结束后开始自然冷却至室温,并转移至无水无氧条件下保存。上述过程中室温至150℃采用氮气气氛,150~600℃采用干空气气氛,自然冷却时由600℃降低至300℃时为干空气气氛,当低于300℃时切换至氮气气氛。将上述焙烧产物浸渍于二茂铬的正己烷溶液中(cr的负载量相对于催化剂总重量为1.5wt%),浸渍温度为45℃,浸渍时间为6h,随后进行升温干燥,干燥温度为80℃,干燥时间为4h,浸渍和干燥过程施加搅拌,干燥结束后将催化剂前驱体在氮气保护下转移至无水无氧条件下保存。实施例5:取10gsio2/al2o3(比表面积600m2/g,孔容1.1ml/g,铝含量为5wt%,孔径17nm)浸渍在乙酰丙酮氧钒和甲基磺酸的乙醇溶液中(v和s负载量相对于催化剂总重量分别为0.25wt%和1.7wt%),连续搅拌浸渍约4h,浸渍温度为40℃,随后升温至100℃,继续搅拌干燥8h。将干燥的混合物置于流化床中从室温开始进行升温焙烧,升温速率为1℃/min,当达到500℃时恒温4h,焙烧结束后开始自然冷却至室温并保存至干燥环境中待用。上述过程中室温至150℃采用氮气气氛,150~500℃采用干空气气氛,自然冷却时由500℃降低至300℃时为干空气气氛,当低于300℃时切换至氮气气氛。将上述焙烧产物浸渍于碱式醋酸铬的水溶液中(cr负载量相对于催化剂总重量为0.7wt%),连续搅拌浸渍约4h,浸渍温度为45℃,随后升温至120℃,继续搅拌干燥8h。将干燥的混合物置于流化床中从室温开始进行升温焙烧,升温速率为1℃/min,当达到600℃时恒温6h,焙烧结束后开始自然冷却至室温,并转移至无水无氧条件下保存。上述过程中室温至150℃采用氮气气氛,150-600℃采用干空气气氛,自然冷却时由600℃降低至300℃时为干空气气氛,当低于300℃时切换至氮气气氛。将上述焙烧产物浸渍于二茂铬的正己烷溶液中(cr的负载量相对于催化剂总重量为1.5wt%),浸渍温度为45℃,浸渍时间为6h,随后进行升温干燥,干燥温度为80℃,干燥时间为4h,浸渍和干燥过程施加搅拌,干燥结束后将催化剂前驱体在氮气保护下转移至无水无氧条件下保存。实施例6取10gsio2/tio2(比表面积500m2/g,孔容1.2ml/g,钛含量为5wt%,孔径25nm)浸渍在硝酸铬和磷酸铵水溶液中(cr和p负载量相对于催化剂总重量分别为0.7wt%和2.2wt%),连续搅拌浸渍约4h,浸渍温度为40℃,随后升温至120℃,继续搅拌干燥8h。将干燥的混合物置于流化床中从室温开始进行升温焙烧,升温速率为1℃/min,当达到450℃时恒温4h,焙烧结束后开始自然冷却至室温,并转移至干燥条件下保存。上述过程中室温至150℃采用氮气气氛,150-450℃采用干空气气氛,自然冷却时由450℃降低至300℃时为干空气气氛,当低于300℃时切换至氮气气氛。将上述焙烧产物浸渍于偏钒酸铵水溶液中(v负载量相对于催化剂总重量为0.25wt%),连续搅拌浸渍约4h,浸渍温度为45℃,随后升温至120℃,继续搅拌干燥8h。将干燥的混合物置于流化床中从室温开始进行升温焙烧,升温速率为1℃/min,当达到600℃时恒温6h,焙烧结束后开始自然冷却至室温,并转移至无水无氧条件下保存。上述过程中室温至150℃采用氮气气氛,150~600℃采用干空气气氛,自然冷却时由600℃降低至300℃时为干空气气氛,当低于300℃时切换至氮气气氛。将上述焙烧产物浸渍于二茂铬的正己烷溶液中(cr的负载量相对于催化剂总重量为1.6wt%),浸渍温度为45℃,浸渍时间为6h,随后进行升温干燥,干燥温度为80℃,干燥时间为4h,浸渍和干燥过程施加搅拌,干燥结束后将催化剂前驱体在氮气保护下转移至无水无氧条件下保存。实施例7:取10gsio2/al2o3(比表面积600m2/g,孔容1.1ml/g,铝含量为5wt%,孔径17nm)浸渍在乙酰丙酮氧钒的乙醇溶液中(v负载量相对于催化剂总重量为0.25wt%),连续搅拌浸渍约4h,浸渍温度为40℃,随后升温至100℃,继续搅拌干燥8h。将干燥的混合物置于流化床中从室温开始进行升温焙烧,升温速率为1℃/min,当达到500℃时恒温4h,焙烧结束后开始自然冷却至室温并保存至干燥环境中待用。上述过程中室温至150℃采用氮气气氛,150~500℃采用干空气气氛,自然冷却时由500℃降低至300℃时为干空气气氛,当低于300℃时切换至氮气气氛。将上述焙烧产物浸渍于碱式醋酸铬和硫酸的水溶液中(cr和s负载量相对于催化剂总重量分别为0.7wt%和2.7wt%),连续搅拌浸渍约4h,浸渍温度为45℃,随后升温至120℃,继续搅拌干燥8h。将干燥的混合物置于流化床中从室温开始进行升温焙烧,升温速率为1℃/min,当达到600℃时恒温6h,焙烧结束后开始自然冷却至室温,并转移至无水无氧条件下保存。上述过程中室温至150℃采用氮气气氛,150~600℃采用干空气气氛,自然冷却时由600℃降低至300℃时为干空气气氛,当低于300℃时切换至氮气气氛。将上述焙烧产物浸渍于二茂铬的正己烷溶液中(cr的负载量相对于催化剂总重量为1.5wt%),浸渍温度为45℃,浸渍时间为6h,随后进行升温干燥,干燥温度为80℃,干燥时间为4h,浸渍和干燥过程施加搅拌,干燥结束后将催化剂前驱体在氮气保护下转移至无水无氧条件下保存。实施例8:取10gsio2/tio2(比表面积500m2/g,孔容1.2ml/g,钛含量为5wt%,孔径25nm)浸渍在硝酸铬水溶液中(cr负载量相对于催化剂总重量为0.7wt%),连续搅拌浸渍约4h,浸渍温度为40℃,随后升温至120℃,继续搅拌干燥8h。将干燥的混合物置于流化床中从室温开始进行升温焙烧,升温速率为1℃/min,当达到450℃时恒温4h,焙烧结束后开始自然冷却至室温,并转移至干燥条件下保存。上述过程中室温至150℃采用氮气气氛,150~450℃采用干空气气氛,自然冷却时由450℃降低至300℃时为干空气气氛,当低于300℃时切换至氮气气氛。将上述焙烧产物浸渍于偏钒酸铵和磷酸铵水溶液中(v和p负载量相对于催化剂总重量分别为0.25wt%和4wt%),连续搅拌浸渍约4h,浸渍温度为45℃,随后升温至120℃,继续搅拌干燥8h。将干燥的混合物置于流化床中从室温开始进行升温焙烧,升温速率为1℃/min,当达到600℃时恒温6h,焙烧结束后开始自然冷却至室温,并转移至无水无氧条件下保存。上述过程中室温至150℃采用氮气气氛,150~600℃采用干空气气氛,自然冷却时由600℃降低至300℃时为干空气气氛,当低于300℃时切换至氮气气氛。将上述焙烧产物浸渍于二茂铬的正己烷溶液中(cr的负载量相对于催化剂总重量为1.5wt%),浸渍温度为45℃,浸渍时间为6h,随后进行升温干燥,干燥温度为80℃,干燥时间为4h,浸渍和干燥过程施加搅拌,干燥结束后将催化剂前驱体在氮气保护下转移至无水无氧条件下保存。实施例9:取10gsio2/zro2(比表面积550m2/g,孔容1.4ml/g,锆含量为5wt%,孔径13nm)浸渍在硫代硫酸铵水溶液中(s负载量相对于催化剂总重量为2wt%),连续搅拌浸渍约4h,浸渍温度为40℃,随后升温至120℃,继续搅拌干燥8h。将干燥的混合物置于流化床中从室温开始进行升温焙烧,升温速率为1℃/min,当达到450℃时恒温4h,焙烧结束后开始自然冷却至室温,并转移至干燥条件下保存。上述过程中室温至150℃采用氮气气氛,150~450℃采用干空气气氛,自然冷却时由450℃降低至300℃时为干空气气氛,当低于300℃时切换至氮气气氛。将上述焙烧产物浸渍于硝酸铬水溶液中(cr负载量相对于催化剂总重量为0.7wt%),连续搅拌浸渍约4h,浸渍温度为40℃,随后升温至120℃,继续搅拌干燥8h。将干燥的混合物置于流化床中从室温开始进行升温焙烧,升温速率为1℃/min,当达到450℃时恒温4h,焙烧结束后开始自然冷却至室温,并转移至干燥条件下保存。上述过程中室温至150℃采用氮气气氛,150~450℃采用干空气气氛,自然冷却时由450℃降低至300℃时为干空气气氛,当低于300℃时切换至氮气气氛。将上述焙烧产物浸渍于偏钒酸铵水溶液中(v的负载量相对于催化剂总重量为0.25wt%),连续搅拌浸渍约4h,浸渍温度为45℃,随后升温至120℃,继续搅拌干燥8h。将干燥的混合物置于流化床中从室温开始进行升温焙烧,升温速率为1℃/min,当达到600℃时恒温6h,焙烧结束后开始自然冷却至室温,并转移至无水无氧条件下保存。上述过程中室温至150℃采用氮气气氛,150~600℃采用干空气气氛,自然冷却时由600℃降低至300℃时为干空气气氛,当低于300℃时切换至氮气气氛。将上述焙烧产物浸渍于二茂铬的正己烷溶液中(cr的负载量相对于催化剂总重量为1.5wt%),浸渍温度为45℃,浸渍时间为6h,随后进行升温干燥,干燥温度为80℃,干燥时间为4h,浸渍和干燥过程施加搅拌,干燥结束后将催化剂前驱体在氮气保护下转移至无水无氧条件下保存。实施例10取10g硅胶(比表面积500m2/g,孔容1.3ml/g,孔径20nm)浸渍在草酸氧钒和碱式醋酸铬的水溶液中(v与cr的负载量相对于催化剂总重量分别为0.25wt%和0.7wt%),连续搅拌浸渍约4h,浸渍温度为60℃,随后升温至120℃,继续搅拌干燥8h。将干燥的混合物置于流化床中从室温开始进行升温焙烧,升温速率为1℃/min,当达到600℃时恒温4h,焙烧结束后开始自然冷却至室温,并转移至无水无氧条件下保存。上述过程中室温至150℃采用氮气气氛,150~600℃采用干空气气氛,自然冷却时由600℃降低至300℃时为干空气气氛,当低于300℃时切换至氮气气氛。将上述焙烧产物浸渍于二茂铬的正己烷溶液中(cr的负载量相对于催化剂总重量为1.5wt%),浸渍温度为45℃,浸渍时间为6h,随后进行升温干燥,干燥温度为80℃,干燥时间为4h,浸渍和干燥过程施加搅拌,干燥结束后将催化剂在氮气保护下转移至三异丁基铝正己烷溶液中,三异丁基铝与催化剂中cr元素的摩尔比al/cr=7,搅拌浸渍反应2h,浸渍反应温度为30℃,随后进行升温干燥,干燥温度为80℃,干燥时间为4h,干燥结束后将经过三异丁基铝预还原的催化剂前驱体转移至无水无氧条件下保存待用。实施例11取10g硅胶(比表面积500m2/g,孔容1.3ml/g,孔径20nm)浸渍在草酸氧钒和碱式醋酸铬的水溶液中(v与cr的负载量相对于催化剂总重量分别为0.25wt%和0.7wt%),连续搅拌浸渍约4h,浸渍温度为60℃,随后升温至120℃,继续搅拌干燥8h。将干燥的混合物置于流化床中从室温开始进行升温焙烧,升温速率为1℃/min,当达到600℃时恒温4h,焙烧结束后开始自然冷却至室温,并转移至无水无氧条件下保存。上述过程中室温至150℃采用氮气气氛,150~600℃的升温阶段采用干空气气氛,600℃的恒温阶段,采用干空气气氛,自然冷却时由600℃降低至300℃时为干空气气氛,当低于300℃时切换至氮气气氛。将上述焙烧产物浸渍于二茚基铬的正己烷溶液中(cr的负载量相对于催化剂总重量为1.0wt%),浸渍温度为45℃,浸渍时间为6h,随后进行升温干燥,干燥温度为80℃,干燥时间为4h,浸渍和干燥过程施加搅拌,干燥结束后将催化剂前驱体在氮气保护下转移至无水无氧条件下保存。实施例12取10g硅胶(比表面积500m2/g,孔容1.3ml/g,孔径20nm)浸渍在草酸氧钒和碱式醋酸铬的水溶液中(v与cr的负载量相对于催化剂总重量分别为0.25wt%和0.7wt%),连续搅拌浸渍约4h,浸渍温度为60℃,随后升温至120℃,继续搅拌干燥8h。将干燥的混合物置于流化床中从室温开始进行升温焙烧,升温速率为1℃/min,当达到600℃时恒温4h,焙烧结束后开始自然冷却至室温,并转移至无水无氧条件下保存。上述过程中室温至150℃采用氮气气氛,150~600℃的升温阶段采用干空气气氛,600℃的恒温阶段,采用干空气气氛,自然冷却时由600℃降低至300℃时为干空气气氛,当低于300℃时切换至氮气气氛。将上述焙烧产物浸渍于二芴基铬的正己烷溶液中(cr的负载量相对于催化剂总重量为1.5wt%),浸渍温度为45℃,浸渍时间为6h,随后进行升温干燥,干燥温度为80℃,干燥时间为4h,浸渍和干燥过程施加搅拌,干燥结束后将催化剂前驱体在氮气保护下转移至无水无氧条件下保存。实施例13-1至13-6:取10g硅胶(比表面积500m2/g,孔容1.3ml/g,孔径20nm)浸渍在草酸氧钒和碱式醋酸铬的水溶液中(v与cr的负载量相对于催化剂总重量分别为0.25wt%和0.7wt%),连续搅拌浸渍约4h,浸渍温度为60℃,随后升温至120℃,继续搅拌干燥8h。将干燥的混合物置于流化床中从室温开始进行升温焙烧,升温速率为1℃/min,当达到600℃时恒温4h,焙烧结束后开始自然冷却至室温,并转移至无水无氧条件下保存。上述过程中室温至150℃采用氮气气氛,150~600℃采用干空气气氛,自然冷却时由600℃降低至300℃时为干空气气氛,当低于300℃时切换至氮气气氛。将上述焙烧产物浸渍于二茂铬的正己烷溶液中,cr的负载量相对于催化剂总重量为0.2wt%、0.5wt%、1wt%、1.5wt%、2wt%或3wt%,分别记为实施例13-1、13-2、13-3、13-4、13-5和13-6,浸渍温度为45℃,浸渍时间为6h,随后进行升温干燥,干燥温度为80℃,干燥时间为4h,浸渍和干燥过程施加搅拌,干燥结束后将催化剂前驱体在氮气保护下转移至无水无氧条件下保存。实施例14称取实施例1中催化剂前驱体100mg,并混合于10ml经过精制的正庚烷溶液中形成催化剂前驱体悬浊液进行聚合实验。将2l不锈钢高压聚合反应釜进行真空加热除杂,并用高纯氮气抽排三次,最后向反应釜内充微量精制乙烯至0.12mpa。接着依次向反应釜内加入900ml精制的正庚烷溶剂,加入用量为al/cr(cr为总铬摩尔量)=10的三异丁基铝(tiba)作助催化剂,再加入100ml脱水脱氧精制后的正庚烷溶剂。调节乙烯压力至1mpa,待釜内温度恒定在80℃后,利用高压氮气将催化剂前驱体悬浊液压入聚合釜中开始反应。反应过程中在线采集单体乙烯的瞬时消耗量并由电脑记录。1h后加入盐酸/乙醇混合溶液终止反应。过滤后将所得聚合物在真空干燥箱中60℃下干燥4h后称重并分析。实施例15称取实施例2中催化剂前驱体100mg,并混合于10ml经过精制的正庚烷溶液中形成催化剂前驱体悬浊液进行聚合实验。将2l不锈钢高压聚合反应釜进行真空加热除杂,并用高纯氮气抽排三次,最后向反应釜内充微量精制乙烯至0.12mpa。接着依次向反应釜内加入900ml精制的正庚烷溶剂,加入用量为al/cr(cr为总铬摩尔量)=10的三异丁基铝(tiba)作助催化剂,再加入100ml脱水脱氧精制后的正庚烷溶剂。调节乙烯压力至1mpa,待釜内温度恒定在80℃后,利用高压氮气将催化剂前驱体悬浊液压入聚合釜中开始反应。反应过程中在线采集单体乙烯的瞬时消耗量并由电脑记录。1h后加入盐酸/乙醇混合溶液终止反应。过滤后将所得聚合物在真空干燥箱中60℃下干燥4h后称重并分析。实施例16称取实施例3中催化剂前驱体100mg,并混合于10ml经过精制的正庚烷溶液中形成催化剂前驱体悬浊液进行聚合实验。将2l不锈钢高压聚合反应釜进行真空加热除杂,并用高纯氮气抽排三次,最后向反应釜内充微量精制乙烯至0.12mpa。接着依次向反应釜内加入900ml精制的正庚烷溶剂,加入用量为al/cr(cr为总铬摩尔量)=10的三异丁基铝(tiba)作助催化剂,再加入100ml脱水脱氧精制后的正庚烷溶剂。调节乙烯压力至1mpa,待釜内温度恒定在80℃后,利用高压氮气将催化剂前驱体悬浊液压入聚合釜中开始反应。反应过程中在线采集单体乙烯的瞬时消耗量并由电脑记录。1h后加入盐酸/乙醇混合溶液终止反应。过滤后将所得聚合物在真空干燥箱中60℃下干燥4h后称重并分析。所得聚烯烃产品的高温gpc曲线如图2所示。实施例17称取实施例4中催化剂前驱体100mg,并混合于10ml经过精制的正庚烷溶液中形成催化剂前驱体悬浊液进行聚合实验。将2l不锈钢高压聚合反应釜进行真空加热除杂,并用高纯氮气抽排三次,最后向反应釜内充微量精制乙烯至0.12mpa。接着依次向反应釜内加入900ml精制的正庚烷溶剂,加入用量为al/cr(cr为总铬摩尔量)=10的三异丁基铝(tiba)作助催化剂,再加入100ml脱水脱氧精制后的正庚烷溶剂。调节乙烯压力至1mpa,待釜内温度恒定在80℃后,利用高压氮气将催化剂前驱体悬浊液压入聚合釜中开始反应。反应过程中在线采集单体乙烯的瞬时消耗量并由电脑记录。1h后加入盐酸/乙醇混合溶液终止反应。过滤后将所得聚合物在真空干燥箱中60℃下干燥4h后称重并分析。实施例18称取实施例5中催化剂前驱体100mg,并混合于10ml经过精制的正庚烷溶液中形成催化剂前驱体悬浊液进行聚合实验。将2l不锈钢高压聚合反应釜进行真空加热除杂,并用高纯氮气抽排三次,最后向反应釜内充微量精制乙烯至0.12mpa。接着依次向反应釜内加入900ml精制的正庚烷溶剂,加入用量为al/cr(cr为总铬摩尔量)=10的三异丁基铝(tiba)作助催化剂,再加入100ml脱水脱氧精制后的正庚烷溶剂。调节乙烯压力至1mpa,待釜内温度恒定在80℃后,利用高压氮气将催化剂前驱体悬浊液压入聚合釜中开始反应。反应过程中在线采集单体乙烯的瞬时消耗量并由电脑记录。1h后加入盐酸/乙醇混合溶液终止反应。过滤后将所得聚合物在真空干燥箱中60℃下干燥4h后称重并分析。实施例19称取实施例6中催化剂前驱体100mg,并混合于10ml经过精制的正庚烷溶液中形成催化剂前驱体悬浊液进行聚合实验。将2l不锈钢高压聚合反应釜进行真空加热除杂,并用高纯氮气抽排三次,最后向反应釜内充微量精制乙烯至0.12mpa。接着依次向反应釜内加入900ml精制的正庚烷溶剂,加入用量为al/cr(cr为总铬摩尔量)=10的三异丁基铝(tiba)作助催化剂,再加入100ml脱水脱氧精制后的正庚烷溶剂。调节乙烯压力至1mpa,待釜内温度恒定在80℃后,利用高压氮气将催化剂前驱体悬浊液压入聚合釜中开始反应。反应过程中在线采集单体乙烯的瞬时消耗量并由电脑记录。1h后加入盐酸/乙醇混合溶液终止反应。过滤后将所得聚合物在真空干燥箱中60℃下干燥4h后称重并分析。实施例20称取实施例7中催化剂前驱体100mg,并混合于10ml经过精制的正庚烷溶液中形成催化剂前驱体悬浊液进行聚合实验。将2l不锈钢高压聚合反应釜进行真空加热除杂,并用高纯氮气抽排三次,最后向反应釜内充微量精制乙烯至0.12mpa。接着依次向反应釜内加入900ml精制的正庚烷溶剂,加入用量为al/cr(cr为总铬摩尔量)=10的三异丁基铝(tiba)作助催化剂,再加入100ml脱水脱氧精制后的正庚烷溶剂。调节乙烯压力至1mpa,待釜内温度恒定在80℃后,利用高压氮气将催化剂前驱体悬浊液压入聚合釜中开始反应。反应过程中在线采集单体乙烯的瞬时消耗量并由电脑记录。1h后加入盐酸/乙醇混合溶液终止反应。过滤后将所得聚合物在真空干燥箱中60℃下干燥4h后称重并分析。实施例21称取实施例8中催化剂前驱体100mg,并混合于10ml经过精制的正庚烷溶液中形成催化剂前驱体悬浊液进行聚合实验。将2l不锈钢高压聚合反应釜进行真空加热除杂,并用高纯氮气抽排三次,最后向反应釜内充微量精制乙烯至0.12mpa。接着依次向反应釜内加入900ml精制的正庚烷溶剂,加入用量为al/cr(cr为总铬摩尔量)=10的三异丁基铝(tiba)作助催化剂,再加入100ml脱水脱氧精制后的正庚烷溶剂。调节乙烯压力至1mpa,待釜内温度恒定在80℃后,利用高压氮气将催化剂前驱体悬浊液压入聚合釜中开始反应。反应过程中在线采集单体乙烯的瞬时消耗量并由电脑记录。1h后加入盐酸/乙醇混合溶液终止反应。过滤后将所得聚合物在真空干燥箱中60℃下干燥4h后称重并分析。实施例22称取实施例9中催化剂前驱体100mg,并混合于10ml经过精制的正庚烷溶液中形成催化剂前驱体悬浊液进行聚合实验。将2l不锈钢高压聚合反应釜进行真空加热除杂,并用高纯氮气抽排三次,最后向反应釜内充微量精制乙烯至0.12mpa。接着依次向反应釜内加入900ml精制的正庚烷溶剂,加入用量为al/cr(cr为总铬摩尔量)=10的三异丁基铝(tiba)作助催化剂,再加入100ml脱水脱氧精制后的正庚烷溶剂。调节乙烯压力至1mpa,待釜内温度恒定在80℃后,利用高压氮气将催化剂前驱体悬浊液压入聚合釜中开始反应。反应过程中在线采集单体乙烯的瞬时消耗量并由电脑记录。1h后加入盐酸/乙醇混合溶液终止反应。过滤后将所得聚合物在真空干燥箱中60℃下干燥4h后称重并分析。实施例23称取实施例10中催化剂前驱体100mg,并混合于10ml经过精制的正庚烷溶液中形成催化剂前驱体悬浊液进行聚合实验。将2l不锈钢高压聚合反应釜进行真空加热除杂,并用高纯氮气抽排三次,最后向反应釜内充微量精制乙烯至0.12mpa。接着依次向反应釜内加入1000ml精制的正庚烷溶剂,调节乙烯压力至1mpa,待釜内温度恒定在80℃后,利用高压氮气将催化剂前驱体悬浊液压入聚合釜中开始反应。反应过程中在线采集单体乙烯的瞬时消耗量并由电脑记录。1h后加入盐酸/乙醇混合溶液终止反应。过滤后将所得聚合物在真空干燥箱中60℃下干燥4h后称重并分析。实施例24称取实施例11中催化剂前驱体100mg,并混合于10ml经过精制的正庚烷溶液中形成催化剂前驱体悬浊液进行聚合实验。将2l不锈钢高压聚合反应釜进行真空加热除杂,并用高纯氮气抽排三次,最后向反应釜内充微量精制乙烯至0.12mpa。接着依次向反应釜内加入900ml精制的正庚烷溶剂,加入用量为al/cr(cr为总铬摩尔量)=10的三异丁基铝(tiba)作助催化剂,再加入100ml脱水脱氧精制后的正庚烷溶剂。调节乙烯压力至1mpa,待釜内温度恒定在80℃后,利用高压氮气将催化剂前驱体悬浊液压入聚合釜中开始反应。反应过程中在线采集单体乙烯的瞬时消耗量并由电脑记录。1h后加入盐酸/乙醇混合溶液终止反应。过滤后将所得聚合物在真空干燥箱中60℃下干燥4h后称重并分析。实施例25称取实施例12中催化剂前驱体100mg,并混合于10ml经过精制的正庚烷溶液中形成催化剂前驱体悬浊液进行聚合实验。将2l不锈钢高压聚合反应釜进行真空加热除杂,并用高纯氮气抽排三次,最后向反应釜内充微量精制乙烯至0.12mpa。接着依次向反应釜内加入900ml精制的正庚烷溶剂,加入用量为al/cr(cr为总铬摩尔量)=10的三异丁基铝(tiba)作助催化剂,再加入100ml脱水脱氧精制后的正庚烷溶剂。调节乙烯压力至1mpa,待釜内温度恒定在80℃后,利用高压氮气将催化剂前驱体悬浊液压入聚合釜中开始反应。反应过程中在线采集单体乙烯的瞬时消耗量并由电脑记录。1h后加入盐酸/乙醇混合溶液终止反应。过滤后将所得聚合物在真空干燥箱中60℃下干燥4h后称重并分析。实施例26-1至26-6以实施例13-1、13-2、13-3、13-4、13-5或13-6制备催化剂前驱体为研究对象,分别记为实施例26-1、26-2、26-3、26-4、26-5或26-6。称取催化剂前驱体100mg,并混合于10ml经过精制的正庚烷溶液中形成催化剂前驱体悬浊液进行聚合实验。将2l不锈钢高压聚合反应釜进行真空加热除杂,并用高纯氮气抽排三次,最后向反应釜内充微量精制乙烯至0.12mpa。接着依次向反应釜内加入900ml精制的正庚烷溶剂,加入用量为al/cr(cr为总铬摩尔量)=10的三异丁基铝(tiba)作助催化剂,再加入100ml脱水脱氧精制后的正庚烷溶剂。调节乙烯压力至1mpa,待釜内温度恒定在80℃后,利用高压氮气将催化剂前驱体悬浊液压入聚合釜中开始反应。反应过程中在线采集单体乙烯的瞬时消耗量并由电脑记录。1h后加入盐酸/乙醇混合溶液终止反应。过滤后将所得聚合物在真空干燥箱中60℃下干燥4h后称重并分析。实施例27称取实施例4中催化剂前驱体100mg,并混合于10ml经过精制的正庚烷溶液中形成催化剂前驱体悬浊液进行聚合实验。将2l不锈钢高压聚合反应釜进行真空加热除杂,并用高纯氮气抽排三次,最后向反应釜内充微量精制乙烯至0.12mpa。接着依次向反应釜内加入900ml精制的正庚烷溶剂,分别加入用量为al/cr(cr为总铬摩尔量)=0,5,10,15,20的三异丁基铝(tiba)作助催化剂(依次对应于实施例27-1,27-2,27-3,27-4,27-5),再加入100ml脱水脱氧精制后的正庚烷溶剂。调节乙烯压力至1mpa,待釜内温度恒定在80℃后,利用高压氮气将催化剂前驱体悬浊液压入聚合釜中开始反应。反应过程中在线采集单体乙烯的瞬时消耗量并由电脑记录。1h后加入盐酸/乙醇混合溶液终止反应。过滤后将所得聚合物在真空干燥箱中60℃下干燥4h后称重并分析。实施例28称取实施例4中催化剂前驱体100mg,并混合于10ml经过精制的正庚烷溶液中形成催化剂前驱体悬浊液进行聚合实验。将2l不锈钢高压聚合反应釜进行真空加热除杂,并用高纯氮气抽排三次,最后向反应釜内充微量精制乙烯至0.12mpa。接着依次向反应釜内加入900ml精制的正庚烷溶剂,加入用量为al/cr(cr为总铬摩尔量)=10的三异丁基铝(tiba)作助催化剂,然后再分别加入10ml、30ml、50ml和100ml的1-己烯(共聚单体1-己烯占加入的溶剂总体积的百分率依次为1%、3%、5%和10%,依次对应于实施例28-1,28-2,28-3,28-4),再加入100ml脱水脱氧精制后的正庚烷溶剂。调节乙烯压力至1mpa,待釜内温度恒定在80℃后,利用高压氮气将催化剂前驱体悬浊液压入聚合釜中开始反应。反应过程中在线采集单体乙烯的瞬时消耗量并由电脑记录。1h后加入盐酸/乙醇混合溶液终止反应。过滤后将所得聚合物在真空干燥箱中60℃下干燥4h后称重并分析。实施例29称取实施例4中催化剂前驱体100mg,并混合于10ml经过精制的正庚烷溶液中形成催化剂前驱体悬浊液进行聚合实验。将2l不锈钢高压聚合反应釜进行真空加热除杂,并用高纯氮气抽排三次,最后向反应釜内充微量精制乙烯至0.12mpa。接着依次向反应釜内加入900ml精制的正庚烷溶剂,加入用量为al/cr(cr为总铬摩尔量)=10的三异丁基铝(tiba)作助催化剂,然后加入30ml的1-己烯,再加入100ml脱水脱氧精制后的正庚烷溶剂,随后分别压入0.3bar、0.5bar、1bar和1.5bar的氢气(依次对应于实施例29-1,29-2,29-3,29-4),最后调节乙烯分压为1mpa,待釜内温度恒定在80℃后,利用高压氮气将催化剂前驱体悬浊液压入聚合釜中开始反应。反应过程中在线采集单体乙烯的瞬时消耗量并由电脑记录。1h后加入盐酸/乙醇混合溶液终止反应。过滤后将所得聚合物在真空干燥箱中60℃下干燥4h后称重并分析。实施例30称取实施例4中催化剂前驱体100mg,并混合于10ml经过精制的正庚烷溶液中形成催化剂前驱体悬浊液进行聚合实验。将2l不锈钢高压聚合反应釜进行真空加热除杂,并用高纯氮气抽排三次,最后向反应釜内充微量精制乙烯至0.12mpa。接着向反应釜内加入1000ml精制的正庚烷溶剂,随后压入0.3bar的氢气,再将乙烯分压调节为1mpa,待釜内温度恒定在80℃后,利用高压氮气将催化剂前驱体悬浊液压入聚合釜中开始反应。反应过程中在线采集单体乙烯的瞬时消耗量并由电脑记录。0.5h后利用高压氮气加入用量为al/cr(cr为总铬摩尔量)=5的三异丁基铝(tiba)和30ml的1-己烯,继续反应0.5h,同时利用电脑在线采集单体乙烯的瞬时消耗量。反应结束后往聚合物淤浆液中加入盐酸/乙醇混合溶液终止反应。过滤后将所得聚合物在真空干燥箱中60℃下干燥4h后称重并分析。实施例31称取实施例4中催化剂前驱体100mg,并混合于10ml经过精制的正庚烷溶液中形成催化剂前驱体悬浊液进行聚合实验。将2l不锈钢高压聚合反应釜进行真空加热除杂,并用高纯氮气抽排三次,最后向反应釜内充微量精制乙烯至0.12mpa。接着向反应釜内加入1000ml精制的正庚烷溶剂,随后将乙烯分压调节为3.5mpa,待釜内温度恒定在80℃后,利用高压氮气将催化剂前驱体悬浊液压入聚合釜中开始反应。反应过程中在线采集单体乙烯的瞬时消耗量并由电脑记录。反应1h后往聚合物淤浆液中加入盐酸/乙醇混合溶液终止反应。过滤后将所得聚合物在真空干燥箱中60℃下干燥4h后称重并分析。实施例32称取实施例4中催化剂前驱体100mg,并混合于10ml经过精制的正庚烷溶液中形成催化剂前驱体悬浊液进行聚合实验。将2l不锈钢高压聚合反应釜进行真空加热除杂,并用高纯氮气抽排三次,最后向反应釜内充微量精制乙烯至0.12mpa。接着向反应釜内加入1000ml精制的正庚烷溶剂,随后将乙烯分压调节为3.5mpa,待釜内温度恒定在80℃后,利用高压氮气将催化剂前驱体悬浊液压入聚合釜中开始反应。反应过程中在线采集单体乙烯的瞬时消耗量并由电脑记录。反应2h后往聚合物淤浆液中加入盐酸/乙醇混合溶液终止反应。过滤后将所得聚合物在真空干燥箱中60℃下干燥4h后称重并分析。对比实施例1取10g硅胶(比表面积500m2/g,孔容1.3ml/g)浸渍在草酸氧钒和碱式醋酸铬的水溶液中(v与cr的负载量相对于催化剂总重量分别为0.25wt%和0.7wt%),连续搅拌浸渍约4h,浸渍温度为60℃,随后升温至120℃,继续搅拌干燥8h。将干燥的混合物置于流化床中从室温开始进行升温焙烧,升温速率为1℃/min,当达到600℃时恒温4h,焙烧结束后开始自然冷却至室温,并转移至无水无氧条件下保存。上述过程中室温至150℃采用氮气气氛,150~600℃采用干空气气氛,自然冷却时由600℃降低至300℃时为干空气气氛,当低于300℃时切换至氮气气氛。称取上述催化剂前驱体100mg,并混合于10ml经过精制的正庚烷溶液中形成催化剂前驱体悬浊液进行聚合实验。将2l不锈钢高压聚合反应釜进行真空加热除杂,并用高纯氮气抽排三次,最后向反应釜内充微量精制乙烯至0.12mpa。接着依次向反应釜内加入900ml精制的正庚烷溶剂,加入用量为al/cr(cr为总铬摩尔量)=10的三异丁基铝(tiba)作助催化剂,再加入100ml脱水脱氧精制后的正庚烷溶剂。调节乙烯压力至1mpa,待釜内温度恒定在80℃后,利用高压氮气将催化剂前驱体悬浊液压入聚合釜中开始反应。反应过程中在线采集单体乙烯的瞬时消耗量并由电脑记录。1h后加入盐酸/乙醇混合溶液终止反应。过滤后将所得聚合物在真空干燥箱中60℃下干燥4h后称重并分析。对比实施例2取10g硅胶(比表面积500m2/g,孔容1.3ml/g)浸渍在碱式醋酸铬的水溶液中(cr的负载量相对于催化剂总重量为0.7wt%),连续搅拌浸渍约4h,浸渍温度为60℃,随后升温至120℃,继续搅拌干燥8h。将干燥的混合物置于流化床中从室温开始进行升温焙烧,升温速率为1℃/min,当达到600℃时恒温4h,焙烧结束后开始自然冷却至室温,并转移至无水无氧条件下保存。上述过程中室温至150℃采用氮气气氛,150-600℃采用干空气气氛,自然冷却时由600℃降低至300℃时为干空气气氛,当低于300℃时切换至氮气气氛。将上述焙烧产物浸渍于二茂铬的正己烷溶液中(cr的负载量相对于催化剂总重量为1.5wt%),浸渍温度为45℃,浸渍时间为6h,随后进行升温干燥,干燥温度为80℃,干燥时间为4h,浸渍和干燥过程施加搅拌,干燥结束后将催化剂前驱体在氮气保护下转移至无水无氧条件下保存。称取上述催化剂前驱体100mg,并混合于10ml经过精制的正庚烷溶液中形成催化剂前驱体悬浊液进行聚合实验。将2l不锈钢高压聚合反应釜进行真空加热除杂,并用高纯氮气抽排三次,最后向反应釜内充微量精制乙烯至0.12mpa。接着依次向反应釜内加入900ml精制的正庚烷溶剂,加入用量为al/cr(cr为总铬摩尔量)=10的三异丁基铝(tiba)作助催化剂,再加入100ml脱水脱氧精制后的正庚烷溶剂。调节乙烯压力至1mpa,待釜内温度恒定在80℃后,利用高压氮气将催化剂前驱体悬浊液压入聚合釜中开始反应。反应过程中在线采集单体乙烯的瞬时消耗量并由电脑记录。1h后加入盐酸/乙醇混合溶液终止反应。过滤后将所得聚合物在真空干燥箱中60℃下干燥4h后称重并分析。对比实施例3取10g硅胶(比表面积500m2/g,孔容1.3ml/g)浸渍在草酸氧钒的水溶液中(v的负载量相对于催化剂总重量为0.25wt%),连续搅拌浸渍约4h,浸渍温度为60℃,随后升温至120℃,继续搅拌干燥8h。将干燥的混合物置于流化床中从室温开始进行升温焙烧,升温速率为1℃/min,当达到600℃时恒温4h,焙烧结束后开始自然冷却至室温,并转移至无水无氧条件下保存。上述过程中室温至150℃采用氮气气氛,150-600℃采用干空气气氛,自然冷却时由600℃降低至300℃时为干空气气氛,当低于300℃时切换至氮气气氛。将上述焙烧产物浸渍于二茂铬的正己烷溶液中(cr的负载量相对于催化剂总重量为1.5wt%),浸渍温度为45℃,浸渍时间为6h,随后进行升温干燥,干燥温度为80℃,干燥时间为4h,浸渍和干燥过程施加搅拌,干燥结束后将催化剂前驱体在氮气保护下转移至无水无氧条件下保存。称取上述催化剂前驱体100mg,并混合于10ml经过精制的正庚烷溶液中形成催化剂前驱体悬浊液进行聚合实验。将2l不锈钢高压聚合反应釜进行真空加热除杂,并用高纯氮气抽排三次,最后向反应釜内充微量精制乙烯至0.12mpa。接着依次向反应釜内加入900ml精制的正庚烷溶剂,加入用量为al/cr(cr为总铬摩尔量)=10的三异丁基铝(tiba)作助催化剂,再加入100ml脱水脱氧精制后的正庚烷溶剂。调节乙烯压力至1mpa,待釜内温度恒定在80℃后,利用高压氮气将催化剂前驱体悬浊液压入聚合釜中开始反应。反应过程中在线采集单体乙烯的瞬时消耗量并由电脑记录。1h后加入盐酸/乙醇混合溶液终止反应。过滤后将所得聚合物在真空干燥箱中60℃下干燥4h后称重并分析。对比实施例4取10g硅胶(比表面积500m2/g,孔容1.3ml/g)浸渍在碱式醋酸铬的水溶液中(cr的负载量相对于催化剂总重量分别为0.7wt%),连续搅拌浸渍约4h,浸渍温度为60℃,随后升温至120℃,继续搅拌干燥8h。将干燥的混合物置于流化床中从室温开始进行升温焙烧,升温速率为1℃/min,当达到600℃时恒温4h,焙烧结束后开始自然冷却至室温,并转移至无水无氧条件下保存。上述过程中室温至150℃采用氮气气氛,150~600℃采用干空气气氛,自然冷却时由600℃降低至300℃时为干空气气氛,当低于300℃时切换至氮气气氛。称取上述催化剂前驱体100mg,并混合于10ml经过精制的正庚烷溶液中形成催化剂前驱体悬浊液进行聚合实验。将2l不锈钢高压聚合反应釜进行真空加热除杂,并用高纯氮气抽排三次,最后向反应釜内充微量精制乙烯至0.12mpa。接着依次向反应釜内加入900ml精制的正庚烷溶剂,加入用量为al/cr(cr为总铬摩尔量)=5的三异丁基铝(tiba)作助催化剂,再加入100ml脱水脱氧精制后的正庚烷溶剂。调节乙烯压力至1mpa,待釜内温度恒定在80℃后,利用高压氮气将催化剂悬浊液压入聚合釜中开始反应。反应过程中在线采集单体乙烯的瞬时消耗量并由电脑记录。1h后加入盐酸/乙醇混合溶液终止反应。过滤后将所得聚合物在真空干燥箱中60℃下干燥4h后称重并分析。对比实施例5取10g硅胶(比表面积500m2/g,孔容1.3ml/g)浸渍在偏钒酸铵的水溶液中(v的负载量相对于催化剂总重量分别为0.25wt%),连续搅拌浸渍约4h,浸渍温度为60℃,随后升温至120℃,继续搅拌干燥8h。将干燥的混合物置于流化床中从室温开始进行升温焙烧,升温速率为1℃/min,当达到600℃时恒温4h,焙烧结束后开始自然冷却至室温,并转移至无水无氧条件下保存。上述过程中室温至150℃采用氮气气氛,150~600℃采用干空气气氛,自然冷却时由600℃降低至300℃时为干空气气氛,当低于300℃时切换至氮气气氛。称取上述催化剂前驱体100mg,并混合于10ml经过精制的正庚烷溶液中形成催化剂前驱体悬浊液进行聚合实验。将2l不锈钢高压聚合反应釜进行真空加热除杂,并用高纯氮气抽排三次,最后向反应釜内充微量精制乙烯至0.12mpa。接着依次向反应釜内加入900ml精制的正庚烷溶剂,加入用量为al/cr(cr为总铬摩尔量)=5的三异丁基铝(tiba)作助催化剂,再加入100ml脱水脱氧精制后的正庚烷溶剂。调节乙烯压力至1mpa,待釜内温度恒定在80℃后,利用高压氮气将催化剂前驱体悬浊液压入聚合釜中开始反应。反应过程中在线采集单体乙烯的瞬时消耗量并由电脑记录。1h后加入盐酸/乙醇混合溶液终止反应。过滤后将所得聚合物在真空干燥箱中60℃下干燥4h后称重并分析。对比实施例6取10g硅胶(比表面积500m2/g,孔容1.3ml/g)置于流化床中从室温开始进行升温焙烧,升温速率为1℃/min,当达到600℃时恒温4h,焙烧结束后开始自然冷却至室温,并转移至无水无氧条件下保存。上述过程整个过程在氮气氛围下进行。将上述焙烧产物浸渍于二茂铬的正己烷溶液中(cr的负载量相对于催化剂总重量为1.5wt%),浸渍温度为45℃,浸渍时间为6h,随后进行升温干燥,干燥温度为80℃,干燥时间为4h,浸渍和干燥过程施加搅拌,干燥结束后将催化剂前驱体在氮气保护下转移至无水无氧条件下保存。称取上述催化剂前驱体100mg,并混合于10ml经过精制的正庚烷溶液中形成催化剂前驱体悬浊液进行聚合实验。将2l不锈钢高压聚合反应釜进行真空加热除杂,并用高纯氮气抽排三次,最后向反应釜内充微量精制乙烯至0.12mpa。接着依次向反应釜内加入900ml精制的正庚烷溶剂,加入用量为al/cr(cr为总铬摩尔量)=10的三异丁基铝(tiba)作助催化剂,再加入100ml脱水脱氧精制后的正庚烷溶剂。调节乙烯压力至1mpa,待釜内温度恒定在80℃后,利用高压氮气将催化剂悬前驱体浊液压入聚合釜中开始反应。反应过程中在线采集单体乙烯的瞬时消耗量并由电脑记录。1h后加入盐酸/乙醇混合溶液终止反应。过滤后将所得聚合物在真空干燥箱中60℃下干燥4h后称重并分析。表1不同制备方式制得的负载型三中心催化剂乙烯聚合结果实施例聚合活性(g聚合物/g催化剂)重均相对分子量×10-5相对分子量分布1-丁基短支链含量(mol%)实施例1498743.7340实施例15108303.5420实施例16112173.7380实施例17141204.5330实施例18156063.2540实施例19142663.1610实施例20145823.2470实施例21145132.8380实施例22139813.2450实施例23128363.5340实施例14与实施例15~16的主要区别在于前者的铬、钒是共浸渍的,而后两者是分步浸渍的,可发现分步浸渍法比共浸渍法制得的催化剂其乙烯聚合活性略高,而聚合物分子量与分子量分布却相当。分别对比实施例15与16或实施例18与20可发现催化剂各组分的负载顺序对其乙烯聚合性能影响甚微。实施例14~16与实施例17~23的主要区别在于后者在催化剂制备过程中引入了催化剂改性组分,可发现在相同聚合条件下加入改性组分的催化剂其活性普遍有所提高,且聚合物的相对分子量整体有所降低,相对分子量分布有所拓宽。表2不同配比组成的催化剂乙烯聚合结果实施例聚合活性(g聚合物/g催化剂)重均相对分子量×10-5相对分子量分布1-丁基短支链含量(mol%)实施例26-174067.7250实施例26-278996.5290实施例26-389854.8310实施例26-498743.7340实施例26-5118492.9370实施例26-6138242.1430实施例26-1至26-6的主要区别在于其所采用的催化剂中有机二茂铬组分加入量的不同,其按照cr质量计算分别占催化剂总质量的0.2wt%、0.5wt%、1wt%、1.5wt%、2wt%与3wt%。由上表2可知随着二茂铬加入量的增加,催化剂的聚合活性逐渐提升,而聚合物相对分子量逐渐降低,分子量分布则有所提升。这主要是因为二茂铬组分负载后形成的活性中心趋向于聚合乙烯形成较低分子量聚乙烯。表3不同助催化剂浓度下催化剂的乙烯聚合结果实施例聚合活性(g聚合物/g催化剂)重均相对分子量×10-5相对分子量分布1-丁基短支链含量(mol%)实施例27-173422.7210实施例27-2120023.9300实施例27-3141204.5370实施例27-4131314.9400实施例27-5124255.1420实施例3151342.5560实施例3290943.9270实施例27-1至27-5的主要区别在于其聚合过程中助催化剂三异丁基铝的加入量不同,其加入量按助催化剂与金属中心的摩尔比al/cr分别为0、5、10、15、20。由表3可知,当加入助催化剂后,催化体系的活性有明显提高,但是当al/cr的值大于某一定值后,其催化活性开始有所下降,即对于特定组成的负载型三中心催化剂,其具有最优的al/cr比使其聚合活性最高。同时可知随着al/cr值的提高,聚合物的相对分子量逐渐提高,而其聚合物相对分子量分布也相应有所提高。实施例31与32为未加入有机金属助催化剂条件下的聚合结果,其中前者的聚合时间是1h,后者的聚合时间是2h。显然,未加入助催化剂时本发明的三中心催化剂依然具有一定的乙烯聚合活性,但是相比于加入助催化剂的情况则活性有明显降低,这体现了一定量助催化剂对催化剂中心,特别是无机铬、无机钒活性中心的活性促进作用(见图3,其中a代表实施例31,b代表实施例32)。表4不同1-己烯加入量下催化剂的乙烯聚合结果实施例聚合活性(g聚合物/g催化剂)重均相对分子量×10-5相对分子量分布1-丁基短支链含量(mol%)实施例28-1155324.1370.45实施例28-2129903.8410.77实施例28-3122843.7430.98实施例28-4115783.6401.16实施例28-1至28-4的主要区别在于其聚合过程中共聚单体1-己烯的加入量不同,其加入量按1-己烯占溶剂体积分率百分比分别为1%、3%、5%、10%。由上表4可知,随着1-己烯加入量的加入,催化剂的活性呈现先上升后降低的趋势,这在大多数烯烃聚合催化体系均有所报道,即所谓的共聚单体效应。此外随着1-己烯的加入,聚合物的相对分子量有所降低,且分子量分布有所拓宽,这是由于1-己烯对催化剂的链转移反应有一定的促进作用所致。同时,由聚合物中1-丁烯短支链的含量可知,当加入1-己烯后,其能有效地插入至聚乙烯链中。同时通过gpc-ftir表征结果(见图4)可知聚合物的短支链呈逆分布,即短支链主要集中分布于高分子量部分。这是由于催化剂中v活性组分相比于其他两种活性组分具有明显更优的共聚性能。表5不同氢气分压下催化剂的乙烯聚合结果实施例聚合活性(g聚合物/g催化剂)重均相对分子量×10-5相对分子量分布1-丁基短支链含量(mol%)实施例29-1134143.5270实施例29-2127082.9210实施例29-3117192.4180实施例29-4110131.8160实施例29-1至29-4的主要区别在于其聚合过程中加入的氢气分压不同,其依次为0.3bar、0.5bar、1bar和1.5bar氢气。由上表5可知其聚合过程中加入氢气后催化剂的聚合活性依次降低,但是聚合物的相对分子量明显降低,说明该催化剂具有较优异的氢调敏感性。同时随着氢气分压的增加,聚合物的分子量分布随之变窄。表6负载型三中心催化剂两段乙烯聚合结果实施例聚合活性(g聚合物/g催化剂)重均相对分子量×10-5相对分子量分布1-丁基短支链含量(mol%)实施例3098843.1510.65实施例30采用两段聚合的形式模拟工业上常用的串联聚合工艺进行乙烯聚合。第一段聚合未加入助催化剂和共聚单体,因此主要由有机铬活性组分(该催化剂组分无需助催化剂活化即有乙烯聚合活性)聚合乙烯得到分子量较低的乙烯均聚物。第二段聚合加入助催化剂和共聚单体后,无机铬、无机钒活性组分前驱体被助催化剂大量活化,进行乙烯-1己烯共聚,形成大量较高分子量共聚物,同时有机铬活性组分因其较差的共聚性能而主要继续进行乙烯均聚。因此采用该种串联聚合工艺可灵活地对聚合物的分子量以及共聚单体的分布进行调控。如实施例30与实施例28-2的共聚单体加入量相同,尽管后者的共聚单体插入量更高,但是前者的聚合物共聚单体更加集中分布于较高分子量组分(如图4和图5所示),这更有利于改善聚合物的长期力学性能。表7负载型三中心与双中心、单中心催化剂乙烯聚合结果实施例聚合活性(g聚合物/g催化剂)重均相对分子量×10-5相对分子量分布1-丁基短支链含量(mol%)对比实施例174068.5210对比实施例283932.6350对比实施例352334.91070对比实施例431604180对比实施例59872440对比实施例62469130将实施例14与对比实施例1-3对比可知,在相同聚合条件下,相比于负载型双中心催化剂,负载型三中心催化剂的乙烯聚合活性明显更高,同时聚合物的相对分子量及分子量分布均明显不同,并可通过高温gpc曲线观测到(见图6,其中a、b、c、d依次为实施例14、对比实施例1、对比实施例2和对比实施例3所得聚合物的高温gpc曲线),即当只负载本发明所述三中心催化剂中的两种催化剂活性组分前驱体,其经有机金属助催化剂活化后所得双中心催化剂的聚乙烯产物分子量只能呈单、双峰分布,而本发明所述负载型三中心催化剂的聚合物分子量可呈三峰分布,其主要是因为三种活性中心的乙烯插入和链转移反应能垒有较大差异,其聚乙烯产物的分子量有较大差别。但是其相比于双中心催化剂而言,在调节聚合物分子量分布方面显然操作空间更大。同时比较对比实施例1-6和实施14可知本发明的三中心负载型催化剂其乙烯聚合活性明显高于单、双中心催化剂,且约高出三种单中心催化剂乙烯聚合活性加和的50%,充分说明三中心负载型催化剂中各活性中心间的催化协同效应。上述实施例为本发明较佳的实施方式,但本发明的实施方式并不受上述实施例的限制,其他的任何未背离本发明的精神实质与原理下所作的改变、修饰、替代、组合、简化,均应为等效的置换方式,都包含在本发明的保护范围之内。当前第1页12