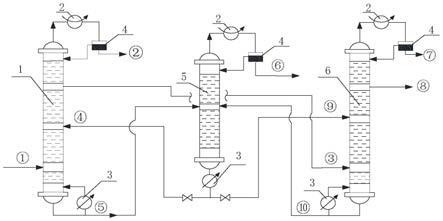
一种分离异丙苯
‑
对甲基苯乙烯
‑
苯乙酮
‑
苄醇
技术领域
1.本发明涉及化工分离方法,特别涉及一种分离异丙苯
‑
对甲基苯乙烯
‑
苯乙酮
‑
苄醇。
背景技术:2.过氧化二异丙苯(简称dcp),是一种最常用的对称二叔烷基过氧化物。通常用作聚乙烯(pe)、氯化聚乙烯(cpe)、聚苯乙烯(ps)的交联剂,生产可发性聚苯乙烯(eps)的引发剂,聚乙烯醋酸乙烯酯(eva)的发泡剂;还用作三元乙丙橡胶(epdm)、丁腈橡胶和硅橡胶等的硫化剂,俗称“工业味精”。由于dcp具有优良的交联性能,几十年来,一直被广泛应用于电线电缆等橡胶制品生产中,交联的聚乙烯用作电缆绝缘材料,不仅具有优良的绝缘性和加工性能,而且可提高其耐热性。硫化剂dcp可使乙烯
‑
醋酸乙烯共聚物(eva)泡沫材料形成细微均匀的泡孔,同时提高制品的耐热性和耐候性随着高分子材料的进步与发展;在制备dcp的过程中过氧化氢异丙苯(chp)作为其重要的中间产物,chp同样也是制备苯酚的重要中间体,目前全世界大约95%的苯酚都是采用异丙苯氧化生产所得。chp除用于合成苯酚外,还广泛应用于烯烃环氧化试剂及链式自由基反应的起始剂,橡胶硫化的促进剂,chp与dcp的应用将日益开拓其领域。
3.dcp生产主要由氧化、还原和缩合三个步骤构成,第一步以异丙苯为原料、高氯酸或高锰酸钾为催化剂催化氧化制备过氧化氢异丙苯(chp),第二步在亚硫酸钠存在条件下通过固定床进行异相还原制得苄醇(ca),第三步由chp和ca在高氯酸条件下缩合制得过氧二异丙苯(dcp),在上述反应过程由于存在诱导期长、反应速率慢、反应温度高及反应压力大等原因,chp分解生成副产物苯乙酮和对甲基苯乙烯,经过减压精馏得到dcp,同时生成异丙苯、chp、对甲基苯乙烯及ca混合副产物。
4.目前,工业上一般采用多次精馏法分离异丙苯
‑
对甲基苯乙烯
‑
苯乙酮
‑
苄醇混合物,由于苯乙酮与苄醇沸点差仅为2.7℃,见表1所示,很难采用普通精馏法进行分离,多次精馏使得操作过程复杂、能耗大,苯乙酮和苄醇的纯度均难达到99%以上。
5.表1原料异丙苯
‑
对甲基苯乙烯
‑
苯乙酮
‑
苄醇混合物的组成及性质
[0006][0007]
技术实现要素:[0008]
发明目的:本发明目的是提供一种收率高的分离异丙苯
‑
对甲基苯乙烯
‑
苯乙酮
‑
苄醇方法。
[0009]
技术方案:本发明提供一种分离异丙苯
‑
对甲基苯乙烯
‑
苯乙酮
‑
苄醇,包括如下步骤:
[0010]
(1)混合原料
①
加入第一侧线减压萃取精馏塔t101分离,同时加入混合萃取剂
④
,萃取分离后,塔顶、侧线和塔底分别得到沸程馏分
②
、侧线馏分
③
和塔底馏分
⑤
,塔底馏分
⑤
送至再生t103处理,t103塔底出料
④
循环至t101;
[0011]
(2)步骤(1)所得到的侧线馏分
③
进入二次上侧线出料减压萃取精馏装置t102,同时加入混合萃取剂
⑨
,萃取分离后,塔顶为对甲基苯乙烯和苯乙酮混合馏分
⑦
,侧线出料为馏分
⑧
,塔底为含有萃取溶剂的苄醇馏分
⑩
;
[0012]
(3)在第一侧线萃取精馏和第二侧线萃取精馏所得到的馏分
⑩
与馏分
⑤
,同时送至溶剂再生塔t103处理,溶剂再生塔t102塔顶为苄醇
⑥
,塔釜为混合萃取剂,再循环至二次侧线出料减压萃取精馏塔t103使用。
[0013]
进一步地,所述步骤(1)的馏分
②
对甲基苯乙烯含量达98.5%,侧线馏分
③
中苯乙酮的含量为89%以上,t103塔顶得到99.5%以上苄醇
⑥
。
[0014]
进一步地,所述步骤(3)溶剂再生塔t102塔顶为含99.5%以上苄醇
⑥
。
[0015]
进一步地,所述混合原料
①
成分包括:质量百分含量分别为1.1~1.3%异丙苯、78.5~80.2%对甲基苯乙烯、8.0~9.0%苯乙酮和10.0~11.0%苄醇。
[0016]
进一步地,所述步骤(1)中,塔顶和塔底温度分别控制在96.8~98.1℃和175.8~176.9℃,原料、塔顶和侧线和萃取剂进出料量控制为10.0~12.0kg/h、8.0~10.0kg/h、0.9~1.0kg/h和3.0~3.5kg/h,回流比2~3,塔板数、原料进料、萃取剂进料及侧线出料位置分别为50块、第40块、第32块及第13块,经第一上侧线减压萃取精馏塔处理,塔顶得到98.5%对甲基苯乙烯、侧线得到89.02%苯乙酮。
[0017]
进一步地,所述步骤(2)中,所述第(2)步骤中,原料和混合萃取剂进料量分别控制为0.9~1.0kg/h和0.7~0.9kg/h、塔顶底温度分别为111.1~112.7℃和213.8~215.6℃,回流比2~3,塔板数为50块,原料、萃取剂及侧线进出料位置分别在第42块、第35块和第15块,经第二上侧线减压萃取精馏塔处理,塔顶和侧线分别得到58.9%的苯乙酮混合物和馏分99.5%的苯乙酮。
[0018]
进一步地,所述步骤(3)中,控制塔顶底温度为132.2~134.7℃和216.9~219.7℃,塔板数为30块,进料位置在第15块,回流比在1~2,塔顶得到含量为99.5%苄醇馏分
⑥
,塔釜馏分为混合萃取剂再循环至第一和第二侧线萃取精馏塔,循环使用。
[0019]
进一步地,二次侧线出料萃取精馏均采用同一萃取剂。
[0020]
进一步地,萃取剂均为甘油和邻二甲苯二丁酯混合萃取剂,其中邻苯二甲酸丁甲酯按质量占比为35~40%。
[0021]
有益效果:本发明与传统的多塔精馏分离工艺相比,本发明将传统多塔精馏改为二次连续侧线出料萃取精馏,经过二次连续侧线减压萃取精馏,对甲基苯乙烯含量和收率分别达到98.5%和99.23%,苄醇含量和收率均达99.5%以上,苯乙酮含量和收率分别达到99.51%和99.5%和89.0%以上。克服了传统精馏法难以将苄醇和苯乙酮产品提高至99.5%以上的问题。
附图说明
[0022]
图1为本发明方法的工艺流程图。
具体实施方式
[0023]
本实施例的连续侧线精馏和萃取精馏集成分离乙醛
‑
乙酸甲酯
‑
甲醇
‑
丁醇
‑
水体系的方法,参照图1所示工艺和表3所示参数,其中1为第一上侧线出料减压萃取精馏塔塔t101、6为第二上侧线出料减压萃取精馏塔塔t102、5为溶剂回收塔t103。原料混合液
①
中异丙苯、对甲基苯乙烯、苯乙酮及苄醇的质量百分含量分别为1.2%、79.4%、8.5%和10.9%,流量为10kg/h。
[0024]
塔内径均为φ100mm,采用φ7
×
7拉丝环填料,经用标准体系测定,该填料等板高度hetp=110mm,塔釜采用调压器电热棒加热,通过气
‑
质联用色谱仪对原料和各馏分进行定量和定性分析。
[0025]
分离方法包括以下步骤:
[0026]
(1)原料混合液
①
加入第一侧线出料减压萃取精馏塔t101,控制塔的压力为0.01~0.015mpa,塔釜通过调压器控制电热棒加热,通过计量泵控制原料进料量为10.0kg/h、萃取剂进料量为2.0kg/h,塔顶、侧线和塔底出料量分别为8.0kg/h、0.95kg/h和3.05kg/h,塔顶温度在96.8~98.1℃,塔釜温度175.8~176.9℃,回流比2~3,理论塔板数为50,萃取剂和原料分别在第34块和42块位置处进料,经第一连续侧线出料萃取精馏塔预处理,塔顶温度为96.8~98.1℃,得到含98.5%对甲基苯乙烯的馏分馏分
②
,侧线温度为138.4~140.5℃,得到含89.02%苯乙酮的馏分
③
,塔底温度为175.8~176.9℃。(2)步骤(1)所得到的连侧线馏分
③
进入第二侧线出料减压萃取精馏塔t103,控制原料
③
和混合萃取剂
⑨
分别为0.95kg/h和0.80kg/h,第二侧线出料减压萃取精馏塔塔顶温度在111.1~112.7℃,塔釜温度在213.8~215.6℃,回流比2~3,理论塔板数为50,进料位置在第42块塔板处,萃取剂进料位置在第35块,侧线出料在第15块,经第二上侧线减压萃取精馏塔处理,塔顶和侧线分别得到馏分
⑦
的58.9%对苯乙酮和馏分
⑧
的99.5%苯乙酮。
[0027]
(3)在步骤(1)和(2)中的得到的馏分
⑤
和馏分
⑩
送至再生t103处理。控制t103再生塔的顶、底温度分别为132.2~134.7℃和216.9~219.7℃,t103塔顶得到99.5%以上苄醇
⑥
,t103塔底出料分别按
④
为2.0kg/h和
⑨
为0.8kg/h循环至t101和t102。
[0028]
上述方法中各塔的工艺条件及分离结果分别见下表3和表4。
[0029]
表3分离过程的工艺条件
[0030][0031]
表4分离过程各个馏分的组成及含量
[0032][0033]
实施例2,与实施例1基本相同,但是所述第(1)步骤中的塔的压力控制为0.02~0.025mpa,在表5条件下,得到表6所示结果,在苄醇和苯乙酮收率不变的情况下,苄醇和苯乙酮的含量均达99.8%以上;从表5结果看,整个分离过程压力提高,第一、二上测线萃取精馏塔的塔顶底温度均有明显提高。
[0034]
表5分离过程的工艺条件
[0035][0036]
表6分离过程各个馏分的组成及含量
[0037][0038]
实施例3,与实施例1基本相同,但是所述第(1)步骤中的萃取剂进料量为3.0kg/h、侧线
③
出料量为0.85kg/h,经第一连续侧线出料萃取精馏塔预处理,馏分
③
中苯乙酮含量和收率均达98.5%,第一上侧线出料萃取精馏塔t101塔底馏分送至再生塔t102处理,塔t102塔顶苄醇的含量和收率分别为94.73%和99.98%。