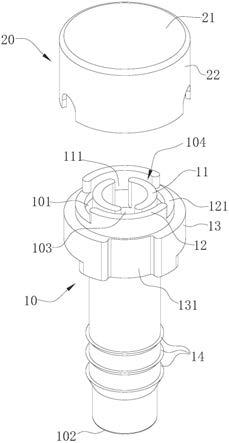
[0001]
本实用新型涉及车辆技术领域,具体涉及一种排气装置及驱动桥。
背景技术:[0002]
驱动桥是车辆的重要部件,通常需要在驱动桥中部设置桥壳空腔用于安装减速器,为了将桥壳内的气体及时排出,以确保桥壳空腔内的齿轮油压力保持在正常范围内,需要在桥壳空腔外壁上安装排气装置,现有的排气装置包括排气管、垫片、弹簧以及端盖,端盖连接在排气管的外侧端部,垫片封盖于排气管的外侧端的开口处,弹簧至于垫片和端盖之间,通过弹簧的弹性应力,将垫片压紧在排气管外侧端的开口外侧,以封堵排气管外侧端的开口,避免外部的泥水、灰尘经由排气管进入桥壳空腔内污染齿轮油,在桥壳空腔内部的气体压力过大时,则垫片被向外推动,使气体能够经由排气管的外侧开口、端盖与排气管的间隙排出,以保证桥壳空腔内外的气压平衡,此种结构对弹簧的精度要求较高,即弹簧所产生的弹性应力应保持在一个精确的范围内,才能确保排气装置能够正常工作,如弹簧的弹性应力过大时,桥壳空腔内的气体不能及时排除,导致桥壳空腔内压力过大,致使齿轮油从桥壳空腔的密封部位泄漏,如弹簧的弹性应力过小,则外界的空气会经由排气管倒灌进入到桥壳空腔内,对齿轮油造成污染。
技术实现要素:[0003]
针对现有技术的不足,本实用新型的目的一是提供一种排气装置,其无需使用弹簧,能够及时排放气体,同时又能够防止空气倒灌。
[0004]
本实用新型的目的二是提供一种驱动桥。
[0005]
为实现上述目的一,本实用新型采用如下技术方案:
[0006]
一种排气装置,包括通气塞、端盖;
[0007]
通气塞包括顶端面和底端面,且通气塞上设置有由底端面延伸至顶端面的通气孔;端盖包括位于顶端面上方的端壁、以及由端壁的周缘向下延伸的侧壁,该侧壁套设于通气塞的外侧面并与通气塞的外侧面贴合;
[0008]
顶端面和端壁之间设置有环绕于通气孔顶部开口外围的第一环形挡壁、以及环绕于第一环形挡壁外围的第二环形挡壁,该第一环形挡壁、第二环形挡壁的底部与顶端面密闭配合、顶部与端壁密闭配合,且第一环形挡壁和第二环形挡壁之间形成第一间隙、第二环形挡壁与侧壁之间形成第二间隙;
[0009]
在第一环形挡壁上设置有将第一间隙与通气孔连通的第一缺口,第二环形挡壁上设置有将第二间隙与第一间隙连通的第二缺口,第一缺口与第二缺口沿通气孔的周向相互错开;
[0010]
侧壁与通气塞的外表面之间设置有导气槽,该导气槽通过位于其顶部的第一开口与第二间隙连通、通过位于其底部的第二开口与外界环境连通,且第一开口与第二缺口沿通气孔的周向相互错开。
[0011]
第一环形挡壁和第二环形挡壁一体成型于顶端面上。
[0012]
通气塞的外侧面设置有向外凸出的凸块,侧壁套设在凸块的外周面并与凸块的外周面过盈配合,导气槽开设在凸块上,第一开口位于凸块的上端面、第二开口位于凸块的下端面。
[0013]
侧壁的底部设置有向着内侧弯折的挂接部,该挂接部卡设于凸块的下端面。
[0014]
通气塞上设置有导油槽,该导油槽由通气孔的内壁延伸至顶端面,且导油槽底面为一斜面,该斜面由外向内逐渐向下倾斜。
[0015]
导油槽位于第一缺口的正下方,并且导油槽的顶部与第一缺口的底部衔接。
[0016]
第二缺口由第二环形挡壁的顶端部向下延伸,且第二缺口的底面高于顶端面。
[0017]
通气塞的外侧面设置有多条沿通气塞的周向延伸的凸筋。
[0018]
通气孔的底部呈孔径由下至上逐渐减小的锥状。
[0019]
为实现上述目的二,本实用新型采用如下技术方案:
[0020]
驱动桥,包括壳体,壳体内部形成桥壳空腔,该驱动桥还包括上述的排气装置,排气装置的通气塞的底部连接于壳体上,且通气塞的通气孔与桥壳空腔连通。
[0021]
本实用新型的有益效果在于:
[0022]
相比于现有的排气装置,本实用新型通过在端盖与通气塞配合的位置处设置多个环形的通道以及缺口,使通气孔始终保持与外界环境处于连通的状态,可及时、快速的将气体排出,且可防止外部空气倒灌进入通气孔;同时,气体中夹杂的齿轮油能够被有效的阻挡并最终通过通气孔回流,防止齿轮油外泄。
附图说明
[0023]
图1为本实用新型的结构示意图;
[0024]
图2为本实用新型的安装示意图;
[0025]
图3为图1的a-a剖视图;
[0026]
图4为图1的b-b剖视图。
具体实施方式
[0027]
下面,结合附图和具体实施方式,对本实用新型作进一步描述:
[0028]
如图1、2、3、4所示,为本实用新型的一种排气装置,其包括通气塞10以及端盖20,其中,通气塞10可以是橡胶材质,端盖20采用金属材质,通气塞10大致圆柱状构造,其包括顶端面101和与顶端面101相对的底端面102,在通气塞10上设置有通气孔103,该通气孔103由底端面102贯穿的延伸至顶端面101;端盖20包括位于其顶部的端壁21、以及由端壁21的周缘向下延伸且呈环形的侧壁22,端盖20扣设在通气塞10的顶部,使端壁21位于顶端面101的上方,侧壁22套设在通气塞10的外侧面,并且该侧壁22与通气塞10的外侧面贴合,使侧壁22与通气塞10的外侧面呈密闭配合状态,可以是将侧壁22与通气塞10的外侧面过盈配合,以实现其二者配合处的密闭性,当然侧壁22与通气塞10的外侧面也可以采用其他的密闭配合方式进行连接。
[0029]
在本实用新型的其中一个优选实施例中,在通气塞10上设置第一环形挡壁11和第二环形挡壁12,该第一环形挡壁11和第二环形挡壁12均是由顶端面101向上延伸而成,其
中,第一环形挡壁11环绕在通气孔103位于顶端面101上的开口外围,第二环形挡壁12环绕于第一环形挡壁11的外围,并且第二环形挡壁12的内径大于第一环形挡壁11的外径,在其二者之间形成第一间隙104,侧壁22的内径大于第二环形挡壁12的外径,在其二者之间形成第二间隙105,在将端盖20与通气塞10扣紧时,第一环形挡壁11、第二环形挡壁12的顶端部抵顶于端壁21的下表面,即第一环形挡壁11、第二环形挡壁12的顶部与端壁21密闭配合,同时,由于第一环形挡壁11、第二环形挡壁12是一体成型于顶端面101上的,因此,第一环形挡壁11、第二环形挡壁12的底部与顶端面101之间是密闭的,同时基于侧壁22与通气塞10的外侧面密闭配合,使得第一间隙104和第二间隙105在通气塞10与端盖20之间分别形成一个环形的通道;在第一环形挡壁11上开设有第一缺口111,该第一缺口111由第一环形挡壁11的外侧面贯穿延伸至内侧面,以将通气孔103与第一间隙104连通,同时,在第二环形挡壁12上开设有第二缺口121,该第二缺口121由第二环形挡壁12的外侧面贯穿延伸至内侧面,以将第一间隙104与第二间隙105连通,并且,第一缺口11与第二缺口121沿通气孔103的周向相互错开。此外,在侧壁22与通气塞10的外表面之间设置有通气槽131,该通气槽131的顶部形成第一开口、底部形成第二开口,通气槽131的第一开口与第二间隙105连通,其第二开口延伸至通气塞10的表面或端盖20的表面与外界环形连通,并且第一开口与第二缺口121沿通气孔103的周向相互错开。
[0030]
本实用新型的排气装置安装于驱动桥的壳体上,具体的,将通气塞10的底部连接在壳体上,使通气孔103与壳体内部的卡壳空腔连通,当桥壳空腔内气体压力增大时,通过排气装置排气,气体经过通气孔103向外排出的过程中,经过第一缺口111进入到第一间隙104内,第一间隙104内流动后经过第二缺口121进入到第二间隙105中,在第二间隙105内流动后进入通气槽131排至外界环境中,利用该排气装置,使桥壳空腔内的压力始与外界环境的大气压力保持平衡,同时,在排气的过程中,通过第一环形挡壁11的阻挡,气体中携带的一部分齿轮油附着于第一环形挡壁11上后经过通气孔回流至桥壳空腔,另一部分齿轮油随着气体进入第一间隙104,通过第二环形挡壁12的阻挡,沉积在第一间隙104中后,经过第一缺口111回流到通气孔103,最终回流至桥壳空腔内,另外,极小部分的齿轮油随着气体从第二缺口121流入第二间隙105,随着气体在第二间隙105内流动,这些极小部分的齿轮油最终也会附着在第二环形挡壁105和侧壁22上,如此,避免齿轮油外泄。
[0031]
相比于现有的排气装置,本实用新型通过在端盖与通气塞配合的位置处设置多个环形的通道以及缺口,使通气孔始终保持与外界环境处于连通的状态,可及时、快速的将气体排出,且可防止外部空气倒灌进入通气孔;同时,气体中夹杂的齿轮油能够被有效的阻挡并最终通过通气孔回流,防止齿轮油外泄。
[0032]
为了方便安装,同时确保上述的通气槽131具有足够的尺寸以实现及时、快速的排气,本实用新型在通气塞10的外侧面设置有向外凸出的凸块13,该凸块13的顶端面衔接于第二环形挡壁12的底端部,侧壁22套设在凸台13的外周面上,并且侧壁22与凸块13是过盈配合的,导气槽131开设在凸块13上,其是由凸块131的上端面延伸至下端面,即导气槽131在凸块上端面形成第一开口,在凸块13的下端面形成第二开口。相比于将导气槽131开设在通气塞10的外侧面上,将导气槽131开设在上述凸块13上,可使导气槽131具有相对较大的深度,从而确保气体能够经导气槽131及时、快速的排出。当然,也可以是将导气槽131设置在侧壁22上,例如,在侧壁22上通过冲压工艺压设向外凸出的凸筋,侧壁22上未设置凸筋的
部分与凸块13的外周面或通气塞的外侧面密闭贴合,设置凸筋的位置由于是向外拱起,与凸块13的外周面或通气塞10的外侧面之间间隔一定距离,如此利用凸筋形成通气槽13。在设置上述凸块13的前提下,可以在侧壁22的底部设置向内弯折的挂接部23,该挂接部23卡设在凸块13的下端面,该挂接部23可以是通过冲压工艺在侧壁22加工成型,在通气塞10与端盖20安装到位后,将挂接部23向内弯折,使挂接部23置于凸块13的下端面,将凸块13压紧,如此,防止端盖20从通气塞10上脱离。
[0033]
在另一个优选实施例中,为了使沉积在第一间隙104内的齿轮油能够快速的回流到通气孔103中,本实用新型在通气塞10上设置有导油槽14,该导油槽14由通气孔103的内壁延伸至顶端面101,并且导油槽14的底面被设置成斜面141,该斜面141由外向内逐渐向下倾斜,沉积在第一间隙104内的齿轮油可经过顺延斜面141快速的回流至通气孔103中;为了便于加工,可将导油槽14与第一缺口111一次成型于通气塞10上,具体的,导油槽14位于第一缺口111的正下方,并且导油槽14的顶部与第一缺口111衔接,可以将导油槽14和第一缺口111视为一个由第一环形挡壁11顶部向下延伸至顶端面101的开口结构。
[0034]
本实用新型的上述第二缺口121由第二环形挡壁12的顶端部向下延伸形成,并且第二缺口121的底面高于顶端面101,这样,第一间隙104内沉积的齿轮油不会经由第二缺口121进入第二间隙105,同时可确保气体能够从第一间隙104经由第二缺口121进入第二间隙105。
[0035]
上述方案中,可以是在第一环形挡壁11设置两个相对的第一缺口111,在第二环形挡壁12上设置两个相对的第二缺口121,第一缺口111和第二缺口121在通气孔103的周向错开的90
°
角,同样的,在凸块13上可以是设置两个相对的通气槽131,通气槽131与第二缺口121在通气孔103的轴向错开90
°
角。当然,也可以是在仅设置一个第一缺口111、第二缺口121和通气槽131,第一缺口111与第二缺口121相互错开的角度为180
°
,第二缺口121与通气槽131相互错开的角度同样为180
°
。
[0036]
在其他实施例中,本实用新型可以是将第一环形挡壁11、第二环形挡壁12设置在端盖20上,在该实施例中,端盖20与通气塞10应选择适当的材质,在端盖20与通气塞10扣合安装后,第一环形挡壁11和第二环形挡壁12的底端部压紧于通气塞10的顶端面101上,并与顶端面101密闭配合,同时,使第一环形挡壁11环绕于通气孔103的顶部外围。
[0037]
此外,将通气孔103的底部设置为孔径由下至上逐渐减小的锥状,使通气孔103的底部形成一个喇叭状的开口,当气体经过该喇叭状开口时,通过锥状的内壁可阻挡气体中夹杂的齿轮油。
[0038]
本实用新型在通气塞10的外侧面上还设置有多条凸筋14,凸筋14顺延通气塞10的周向延伸,在与驱动桥的壳体安装时,将通气塞10插入到壳体上开设的安装孔内,多个凸筋14被安装孔的内壁挤压形变,从而确保通气塞10与壳体配合处具有较佳的密封性。
[0039]
需要指出的是,本实用新型的排气装置不仅能够如上述安装在驱动桥的壳体上,其还可以是应用在其他具有排气需求、同时又要避免油液外泄的机构上。
[0040]
以上实施例仅用以说明本实用新型的技术方案,而非对其限制;尽管参照前述实施例对本实用新型进行了详细的说明,本领域的普通技术人员应当理解,其依然可以对前述各实施例所记载的技术方案进行修改,或者对其中部分技术特征进行等同替换,而这些修改或者替换,并不使相应技术方案的本质脱离本实用新型各实施例技术方案的精神和范围。