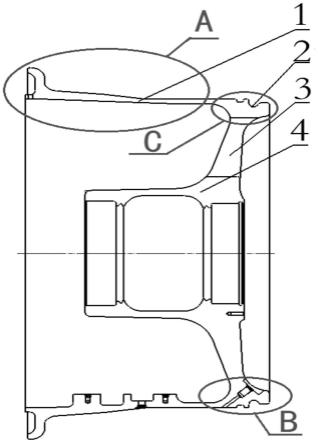
1.本发明涉及航空机轮结构设计领域,具体是一种高承载能力民用支线飞机机轮轮毂。
背景技术:2.飞机机轮轮毂作为飞机重要承力部件,其重量和强度直接关系到飞机的安全和性能。机轮轮毂单位质量承载能力,即每千克重量能承受的极限载荷大小,是目前国内外机轮轮毂结构设计的一个重要参考指标。
3.根据调研,目前国内外轮胎规格在30英寸~35英寸之间的民用支线飞机机轮,其单位质量承载能力在8~10kn/kg之间。而随着民用支线飞机经济利益最大化和成本最低化要求,飞机机轮需要满足更高的单位质量承载能力要求。
技术实现要素:4.为克服现有机轮轮毂结构不能满足规定的单位质量承载能力要求的不足,本发明提出了一种高承载能力的机轮轮毂结构。
5.本发明为单腹板结构,采用常规的双筒形结构,包括机轮轮毂轮辋、卡环槽、轮毂腹板和轮毂毂部。所述轮辋内环截面为一锥形,锥形角度为a1。从轮缘圆角至轮辋钢丝接触处的内环截面有一弧形鼓包,该弧形鼓包的半径为r1、高度为h1。所述轮辋外环截面形状为一锥形。在所述轮辋内圆周方向均布9个导轨安装凸台。所述轮辋根部与腹板结合部位为一圆弧面,圆弧半径r3=15~20mm。所述卡环槽分布在轮辋与腹板连接部位的外侧,为一半圆形截面的环状凹槽。
6.所述锥形角a1=2
°
~4
°
;所述弧形鼓包半径r1=50~100mm,弧形鼓包高度h1=3~5mm;
7.所轮辋外环截面的锥形由三段线组成:一段为轮毂轮辋5
°
线,一段为斜线,一段为轮毂外环水平线;其中,该斜线与轮毂外环水平线夹角为a2,a2=7
°
~10
°
;该水平线与活动轮缘互相接触。所述斜线与轮毂外环水平线之间通过半径r2的圆弧面结合,r2=50~100mm。
8.所述轮辋根部和腹板结合部位圆弧面外侧有安装气门嘴组件的气门嘴孔。该圆弧面与气门嘴孔之间的最小材料厚度为h2;h2=7~10mm。
9.所述腹板的圆周上均布9个腹板孔。所述各腹板孔与轮毂毂部轴承孔之间的厚度为h3,h3=30~45mm;各腹板孔与卡环槽之间的厚度为h4,h4=15~25mm;各腹板内表面与竖直面之间的夹角为a3,a3=13
°
~18
°
;各腹板外表面与竖直面之间的夹角为a4,a4=0
°
~3
°
。
10.所述腹板截面形状近似为梯形,靠近卡环槽处为梯形短边,靠近轮毂毂部处为梯形长边。所述腹板内表面与刹车壳体之间的最短距离h5=2~5mm。
11.所述轮毂毂部与腹板结合部位为一大圆弧面,圆弧半径为r4;r4=35~50mm。
12.本发明通过增加轮毂外载荷施加区域轮缘圆角至轮辋钢丝接触部位处的厚度,大幅度提高了轮毂的整体刚度,经试验验证,轮毂变形量减小了10%;减少轮毂腹板孔内表面与刹车壳体之间的距离,使得轮毂外载荷作用点与轮毂固支点轴承孔处的距离缩短,由力矩计算公式m=f
×
l可知,当力一定时,力臂l越短力矩m越小,因而降低了轮毂毂部所受的弯曲力矩;加大轮毂最危险部位轮毂毂部和腹板结合处的圆角半径,加厚腹板孔与轮毂毂部轴承孔之间的厚度,由应力集中原理可知,增大过渡圆角半径及增大高应力区材料厚度会大幅度降低该危险部位应力水平。同时减薄轮毂腹板孔与卡环槽之间的厚度,减薄轮毂轮辋5
°
线与轮毂外环水平线之间的轮毂筒壁厚度,在轮毂重量不变的基础上降低轮毂危险部位的应力水平,使本发明轮毂的单位质量承载能力大幅度提高。
13.某型号飞机机轮轮胎规格34英寸,其单位质量承载能力达到12kn/kg,远高于目前国内外相同轮胎规格机轮单位质量承载能力。
附图说明
14.图1是一种飞机轮毂剖面图。
15.图2是图1的左视图。
16.图3是轮毂轮辋结构示意图。
17.图4是轮辋根部与腹板结合部位。
18.图5是轮毂卡环槽结构示意图。
19.图6是轮毂腹板的结构尺寸示意图。
20.图7是轮毂腹板截面形状图。
21.1.轮毂轮辋;2.卡环槽;3.轮毂腹板;4.轮毂毂部;5.刹车壳体。
具体实施方式
22.本实施例是某型飞机的机轮轮毂,包括轮辋1、卡环槽2、腹板3和轮毂毂部4。
23.如图3所示,轮辋1内环截面为一锥形,锥形角度a1为2
°
~4
°
。从轮缘圆角至轮辋钢丝接触处的内环截面有一弧形鼓包,该弧形鼓包半径r1为50~100mm,弧形鼓包高度h1为3~5mm。所述轮毂轮辋外环截面形状为一锥形,该锥形由三段线组成,一段为轮毂轮辋5
°
线,一段为斜线,该斜线与轮毂外环水平线夹角a2为7
°
~10
°
,一段为轮毂外环水平线,该水平线与活动轮缘互相接触。上述斜线与轮毂外环水平线之间通过圆弧面结合,圆弧面半径r2为50~100mm。在所述轮辋内圆周方向均布9个导轨凸台,用于安装导轨,承受刹车力矩作用。
24.本实施例中,锥形角度a1为3
°
;弧形鼓包半径r1为80mm、高度h1为4mm;斜线与轮毂外环水平线夹角a2为8
°
;斜线与轮毂外环水平线之间的圆弧面的半径r2为100mm;
25.如图4所示,所述轮辋1根部与腹板3结合部位为一圆弧面,圆弧半径r3为15~20mm。所述轮辋根部和腹板结合部位圆弧面外侧。安装有气门嘴孔,用于安装气门嘴组件。该圆弧面与气门嘴孔之间的最小材料厚度为h2;h2=7~10mm。所述圆弧表面与气门嘴孔之间的距离h2为7~10mm。
26.本实施例中,圆弧半径r3为20mm;圆弧表面与气门嘴孔之间的距离h2为8mm。
27.如图5所示,所述卡环槽2采用现有技术,分布在轮毂轮辋1与轮毂腹板3连接部位
的外侧,为一半圆形截面的环状凹槽,用于与活动轮缘、半卡环相配合。
28.如图6所示,所述腹板3在沿着圆周方向均布9个腹板孔。腹板孔与轮毂毂部4轴承孔之间的厚度h3为30~45mm,腹板孔与卡环槽2之间的厚度h4为15~25mm。所述腹板内表面与竖直面之间的夹角a3为13
°
~18
°
,腹板外表面与竖直面之间的夹角a4为0
°
~3
°
。
29.本实施例中,腹板孔与轮毂毂部4轴承孔之间的厚度h3为35mm,腹板孔与卡环槽2之间的厚度h4为15mm。所述腹板内表面与竖直面之间的夹角a3为18
°
,腹板外表面与竖直面之间的夹角a4为3
°
。
30.如图7所示,所述腹板3截面形状近似为梯形,靠近卡环槽2处为梯形短边,靠近轮毂毂部4处为梯形长边。所述腹板内表面距离刹车壳体之间的最短距离h4为2~5mm。所述轮毂毂部4为常规结构,轮毂毂部有两个轴承孔,用于和轴承相配合。所述轮毂毂部4与腹板3结合部位为一大圆弧面,圆弧半径为r4为35~50mm。
31.本实施例中,所述腹板内表面距离刹车壳体5之间的最短距离h4为3mm,轮毂毂部4与腹板3结合部位圆弧的半径为r4为40mm
32.机轮受极限载荷作用时,通过增加轮毂极限载荷施加区域轮缘圆角至轮辋钢丝接触部位处的厚度,大幅度提高了轮毂的整体刚度;减少轮毂腹板孔内表面与刹车壳体5之间的距离,使得轮毂外载荷作用点与轮毂固支点轴承孔处的距离缩短,降低了轮毂毂部所受的弯曲力矩;加大轮毂最危险部位轮毂毂部和腹板结合处的圆角半径,加厚腹板孔与轮毂毂部轴承孔之间的厚度,大幅度降低该危险部位应力水平。同时减薄轮毂腹板孔与卡环槽之间的厚度,减薄轮毂轮辋5
°
线与轮毂外环水平线之间的轮毂筒壁厚度,在轮毂重量不变的基础上降低轮毂危险部位的应力水平,使本发明轮毂的单位质量承载能力大幅度提高。某型飞机机轮轮毂采用上述结构,在重量不变的基础上机轮轮毂能承受的极限载荷提高了25%以上,该机轮轮毂单位质量承载能力提高25%以上;某型飞机机轮轮毂采用上述结构,在极限载荷不变基础上,机轮轮毂重量从34.6kg减至27.3kg,机轮轮毂重量减重约22%,该机轮轮毂单位质量承载能力提高约22%。试验结果表明本发明提出的机轮轮毂结构能显著提高轮毂的单位质量承载能力。