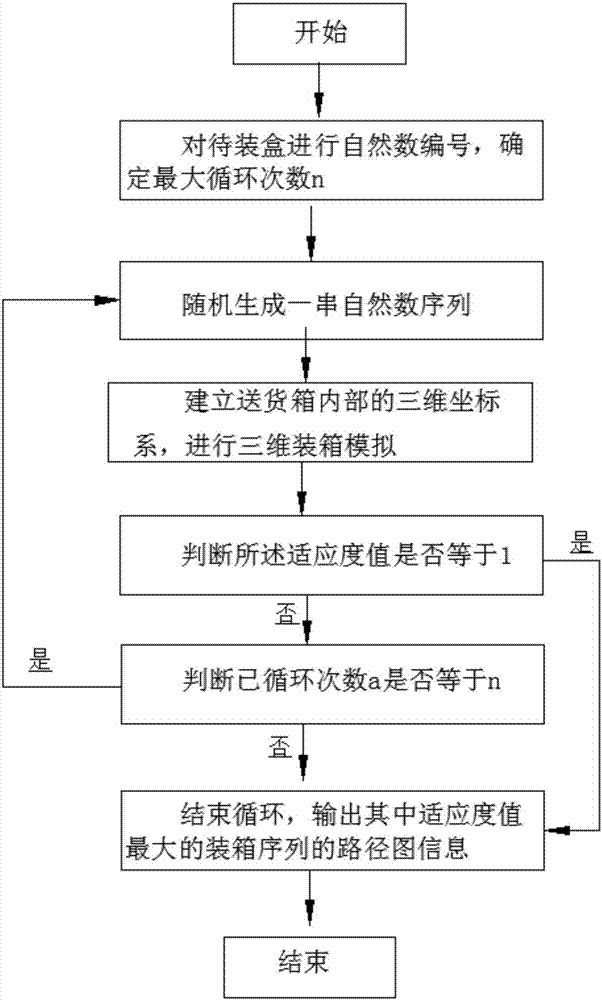
本发明涉及工业自动化包装及物流领域,特别涉及一种基于三维装箱定位与机器人抓取待装盒的装箱方法。
背景技术:
:目前,送货箱的物品装卸主要采取人工装箱的方式,或者采用三维装箱算法计算好物品装载的位置,由人工操作机械进行装载;外贸及物流行业的商品三维装箱,也主要是人工装箱的方式。可见传统的三维装箱方式存在成本高,效率低,自动化程度低,装箱方法效率不足、箱内空间未装满而浪费的问题。技术实现要素:本发明的目的在于克服现有技术中传统的三维装箱方式效率低,自动化程度低,装箱方法效率不足、箱内空间未装满而浪费的缺点,提供一种基于三维装箱定位的机器人装箱方法。为解决上述技术问题,本发明采用了以下技术措施:一种基于三维装箱定位的机器人装箱方法,包括以下步骤:s1,获取订单信息,所述订单信息包括待装盒的数量信息以及三维尺寸信息,然后根据所述待装盒的数量信息以及三维尺寸信息计算出所有待装盒的总体积,选择容积大于所述总体积的送货箱。s2,根据所述订单信息以及所选择的所述送货箱,采用最大适应度法进行三维装箱模拟,并按照以下公式计算适应度值:a=b/c;其中,a为适应度值,b为已经装箱的待装盒体积,c为所有待装盒体积。选取适应度值最大的路径图信息,所述路径图信息包括各个待装盒的装箱序列信息、放置方向信息以及其在所述送货箱中的三维坐标信息。s3,按照装箱序列以及放置方向信息将所述待装盒依次输送到传送带上;s4,根据各个所述待装盒在所述送货箱中的三维坐标信息,将传送带上的待装盒放置于所述送货箱的对应位置。本发明还可以通过以下技术措施进一步完善:作为进一步改进,在步骤s2中,所述采用最大适应度法进行三维装箱模拟,求最大适应度a的步骤包括:s21,对待装盒进行自然数编号,每一待装盒对应一个自然数,确定最大循环次数为n。s22,随机生成一串自然数序列,即生成一个所有待装盒的装箱序列。s23,建立送货箱内部的三维坐标系,定义送货箱的长宽高方向分别为y轴、x轴以及z轴,且以送货箱底部;按照所述装箱序列,考虑待装盒摆放的尺寸约束,以及待装盒摆放的表面朝向;将待装盒沿y轴方向依次装箱成条,沿x轴方向依次分条装箱成层,沿z轴方向依次分层装箱。s24,装箱完毕后,计算出此装箱序列的适应度值并存储该值;判断所述适应度值是否等于1,若是,则进入进入步骤s26;若否,则进入步骤s25。s25,定义a为所述随机生成一串自然数序列的次数;判断a是否等于n,若是,则进入步骤s26,若否,则返回步骤s22。步骤s26,结束循环,输出其中适应度值最大的装箱序列的路径图信息。作为进一步改进,在步骤s3中,按照所述放置方向信息将待装盒输送到传送带上具体包括:s31,将每一待装盒按照所述放置方向信息中设定的表面朝向放置于传送带上;步骤s4中,还包括:s41,采集所述传送带终点上所述待装盒的终点图像,并与预存的待抓取待装盒的模板图像进行模板匹配;得到待装盒中心点在传送带上坐标系中的坐标;并且通过模板匹配得到所述待装盒的相对旋转角度。s42,根据所述待装盒的中心点坐标,控制机器人爪手对所述待装盒进行抓取,并将所述待装盒水平旋转至所述相对旋转角度为零的状态。作为进一步改进,步骤s41,将所述终点图像与所述模板图像进行模板匹配,并得到所述待装盒中心点坐标及相对旋转角度的方法包括。s411,对所述待装盒的终点图像和预存的模板图像,采用sobel算子进行边缘提取,形成边缘提取后的图像。s412,对这两张边缘提取后的图像进行傅里叶变换,并按照以下公式计算两张图像的互功率谱:其中rf(u,v)和tf(u,v)分别是终点图像和模板图像的傅里叶变换,tf*(u,v)为tf(u,v)的复共轭。s413,对cc(u,v)进行傅里叶反变换,得到两张图像的相关函数,为脉冲函数,其峰值坐标(x0,y0)即为待装盒相对于模板图像的偏移量,其峰值对应为相似的程度。s414,旋转所述模板图像,循环测试每次旋转后的模板图像与待装盒图像的相关函数cc(x,y)的峰值;cc(x,y)的峰值最大时,旋转的模板图像与待装盒图像相似性也最大,模板图像的旋转角度即为待装盒图像的旋转角度。作为进一步改进,在s1中,选择容积大于所述总体积的送货箱的方法具体为:选择容积为待装盒总体积1.05倍至1.1倍之间的送货箱。作为进一步改进,在s1中,选择容积大于所述总体积的送货箱的方法具体为,选择容积大于所述待装盒总体积,且最接近所述待装盒总体积的送货箱。作为进一步改进,在步骤s26中,若最大适应度值不为1,则步骤s26之后还包括:s27,获取该装箱序列中未装箱的待装盒的数量信息以及三维尺寸信息,选择容积大于待装盒总体积1.1倍的送货箱,转步骤s22。作为进一步改进,在步骤s25与步骤s26之间还包括以下步骤;步骤s251,选取体积更大的送货箱,且更新的送货箱内部空间信息,返回步骤s21。与现有技术相比较,本发明具有以下优点:本发明的有益效果是:与传统的装箱方式相比,采用三维装箱算法的机器人智能装箱方法,无需人工操作,实现自动化装箱,提高生产效率,降低人工成本。采用最大适应度法求取装箱的最优序列和三维装箱坐标,实现待装盒的精准装箱,同时节省箱子空间,降低生产成本。采用视觉的方式确定传送带上待装盒的位置及旋转角度,实现精准抓取。附图说明图1为本发明实施例的基于三维装箱定位的机器人装箱方法的流程图。图2为本发明实施例的最大适应度法的流程图。具体实施方式为使本发明实施方式的目的、技术方案和优点更加清楚,下面将结合本发明实施方式中的附图,对本发明实施方式中的技术方案进行清楚、完整地描述,显然,所描述的实施方式是本发明一部分实施方式,而不是全部的实施方式。基于本发明中的实施方式,本领域普通技术人员在没有作出创造性劳动前提下所获得的所有其他实施方式,都属于本发明保护的范围。下面结合附图与具体实施方式对本发明作进一步详细描述:请参考图1,为本发明一种基于三维装箱定位的机器人装箱方法整体流程示意图。其包括:s1,获取订单信息,所述订单信息包括待装盒的数量信息以及三维尺寸信息,然后根据所述待装盒的数量信息以及三维尺寸信息计算出所有待装盒的总体积,选择容积大于所述总体积的送货箱。s2,根据所述订单信息以及所选择的所述送货箱,采用最大适应度法进行三维装箱模拟,并按照以下公式计算适应度值:a=b/c;其中,a为适应度值,b为已经装箱的待装盒体积,c为所有待装盒体积。选取适应度值最大的路径图信息,所述路径图信息包括各个待装盒的装箱序列信息、放置方向信息以及其在所述送货箱中的三维坐标信息。s3,按照装箱序列以及放置方向信息将所述待装盒依次输送到传送带上;s4,根据各个所述待装盒在所述送货箱中的三维坐标信息,将传送带上的待装盒放置于所述送货箱的对应位置。下面结合实施例对本发明的技术方案作进一步描述,应当注意的是,实施例仅仅是为了帮助读者更好地理解本发明的技术构思,并不用以限制本发明权利要求的保护范围。最大适应度法的三维装箱模拟,其流程图参见图2,总体实现过程包括以下步骤:根据订单信息确定待装盒的编号,读取待装盒的尺寸并进行体积加总,选择一个大于待装盒总体积的送货箱。在本实施例中,订单信息中待装盒的数量为16个,编号为1,2,3…,16,所有待装盒的长、宽和高如表1所示。表1待装盒的尺寸待装盒编号长宽高18.58.512.429.29.25.739.99.616.248.95.816.351010.125.661010.125.675.75.75.789.98.419.892915.17.51012.212.25.81114.3117.61214.3117.61314.3117.61414.3117.61514.3117.61614.3117.6选择容积大于所述总体积的送货箱,在本实施例该送货箱的长、宽和高为box=[32,32,30],单位为厘米。根据送货箱的体积和待装盒的编号及尺寸,采用基于最大适应度的三维装箱方法,计算待装盒的优化装箱序列(待装盒编号序列)。其中,确定最大循环次数n为1000。最大适应度法三维装箱模拟中,每个待装盒有六个面,并计算出待装盒放置的方向,即哪个表面朝上。通过三维对角线坐标可以得到待装盒放置的方向。同时,计算出待装盒在送货箱中放置的三维坐标,用待装盒的对角线坐标表示待装盒在送货箱中位置。例如:设某实施例待装盒的长宽高是l,w,h,放置的位置为(x0,y0,z0),放置的方向为长宽高和x,y,z轴的方向是一致的,则该待装盒在送货箱中位置表示为(x0,y0,z0,x0+l,y0+w,z0+h)。放置的方向有6种,分别是{l,w,h;l,h,w;h,w,l;h,l,w;w,l,h;w,h,l},若放置的位置为(x0,y0,z0),则按照6种放置方向放置后对应的三维对角线坐标为{(x0,y0,z0,x0+l,y0+w,z0+h),(x0,y0,z0,x0+l,y0+h,z0+w),(x0,y0,z0,x0+h,y0+w,z0+l),(x0,y0,z0,x0+h,y0+l,z0+w),(x0,y0,z0,x0+w,y0+l,z0+h),(x0,y0,z0,x0+w,y0+h,z0+l)}。同理,通过三维对角线坐标也可以得到放置的方向。在本实施例中,待装盒的优化装箱序列具体计算如下:步骤s22,随机生成一串自然数序列,即生成一个装箱序列。例如:某次循环实施例中,随机生成的装箱序列为{6,3,16,11,7,14,8,5,15,1,2,4,13,9,10,12}。步骤s23,按照这个装箱序列,考虑待装盒摆放的尺寸约束,待装盒摆放的表面朝向,按照从里到外(y轴方向),从左到右(x轴方向),从下到上(z轴方向),分条分层进行装箱。此次循环实施例中,装箱完毕后,5号待装盒和9号待装盒不能装入,可装入的序列为:{6,3,16,11,7,14,8,15,1,2,4,13,10,12}。可装入的待装盒摆放位置三维对角线坐标如表2所示。表2可装入待装盒的三维对角线坐标步骤s24,计算出此装箱序列的适应度值并存储该值,适应度值=可装箱的待装盒体积/所有待装盒体积。此次循环实施例中,计算出的适应度值为0.875。判断所述适应度值小于1,进入步骤s22,继续循环。直到循环到适应度值等于1,将路径图信息输出。在本实施例中,循环到某次时,适应度值为1,例如,该装箱序列为:{6,1,5,16,14,15,4,13,10,8,12,2,9,3,7,11}。其中待装盒摆放位置的三维对角线坐标如表3所示。表3待装盒摆放的三维对角线坐标输出这个路径图信息,其包括装箱序列,以及各个待装盒的放置方向及放置的三维对角线坐标。在其他实施例中,模拟装箱的适应度值始终小于1,则判断循环次数是否有n次,如果已经有了n次,则停止循环,输出其中适应度值最大的装箱序列的路径图信息。处理器可以获取该装箱序列中未装箱的待装盒的数量信息以及三维尺寸信息,选择容积大于待装盒总体积1.1倍的送货箱,重新进行装箱模拟。利用多个送货箱将订单内的待装盒装起,从而充分利用送货箱内的空间。在其他实施例中,模拟装箱的适应度值始终小于1,则判断循环次数是否有n次,如果已经有了n次,则停止循环,输出其中适应度值最大的装箱序列的路径图信息,并进行储存。处理器选取体积更大的送货箱,且更新的送货箱内部空间信息,重新进入步骤s21进行装箱模拟。直到出现适应度值为1的装箱序列,并输出适应度值最大的装箱序列的路径图信息。即适应度值为1时的装箱序列的路径图信息。在本实施中,得到适应度值为1时的装箱序列的路径图信息后。由机器人的控制系统按照该路径图信息进行按步骤s3与步骤s4取货装箱。其中,在步骤s3中,按照所述放置方向信息将待装盒输送到传送带上具体包括:s31,将每一待装盒按照所述放置方向信息中设定的表面朝向放置于传送带上;步骤s4中,还包括:其中包括,s31,将每一待装盒按照所述放置方向信息中设定的表面朝向放置于传送带上。s41,采集所述传送带终点上所述待装盒的终点图像,并与预存的待抓取待装盒的模板图像进行模板匹配;得到待装盒中心点在传送带上坐标系中的坐标;并且通过模板匹配得到所述待装盒的相对旋转角度。s42,根据所述待装盒的中心点坐标,控制机器人爪手对所述待装盒进行抓取,并将所述待装盒水平旋转至所述相对旋转角度为零的状态。需要说明的是,预存的待抓取待装盒的模板图像为路径图信息中,该对应待装盒放置方向信息生成的三维模板图像。具体的,步骤s41,将所述终点图像与所述模板图像进行模板匹配,并得到所述待装盒中心点坐标及相对旋转角度的方法包括:s411,对所述待装盒的终点图像和预存的模板图像,采用sobel算子进行边缘提取,形成边缘提取后的图像。s412,对这两张边缘提取后的图像进行傅里叶变换,并按照以下公式计算两张图像的互功率谱:其中rf(u,v)和tf(u,v)分别是终点图像和模板图像的傅里叶变换,tf*(u,v)为tf(u,v)的复共轭。s413,对cc(u,v)进行傅里叶反变换,得到两张图像的相关函数,为脉冲函数,其峰值坐标(x0,y0)即为待装盒相对于模板图像的偏移量,其峰值对应为相似的程度。s414,旋转所述模板图像,循环测试每次旋转后的模板图像与终点图像的相关函数cc(x,y)的峰值;cc(x,y)的峰值最大时,旋转的模板图像与终点图像相似性也最大,模板图像的旋转角度即为终点图像的旋转角度。根据位置与旋转角度信息,调整机器人抓手对传送带上的待装盒进行抓取,并根据前述方法获得的三维对角线坐标(x0,y0,z0,x1,y1,z1),控制机器人抓手,将该待装盒放置于送货箱的(x0,y0,z0)坐标处。机器人抓手继续处理传送带上流过来的下一个待装盒,按照本发明的方法抓取并放置于送货箱中,直至该订单上的所有待装盒都装入该送货箱中。优选的,选择容积大于所述待装盒总体积,且最接近所述待装盒总体积的相应规格的送货箱。其中更进一步的,选择容积为待装盒总体积1.05倍至1.1倍之间的送货箱。这个容积的送货箱更容易得到适应度值为1,且尽可能利用箱内空间。以上所述仅为本发明的较佳实施例而已,并不用以限制本发明,凡在本发明的精神和原则之内,所做的任何修改、等同替换、改进等,均应包含在本发明保护的范围之内。当前第1页12