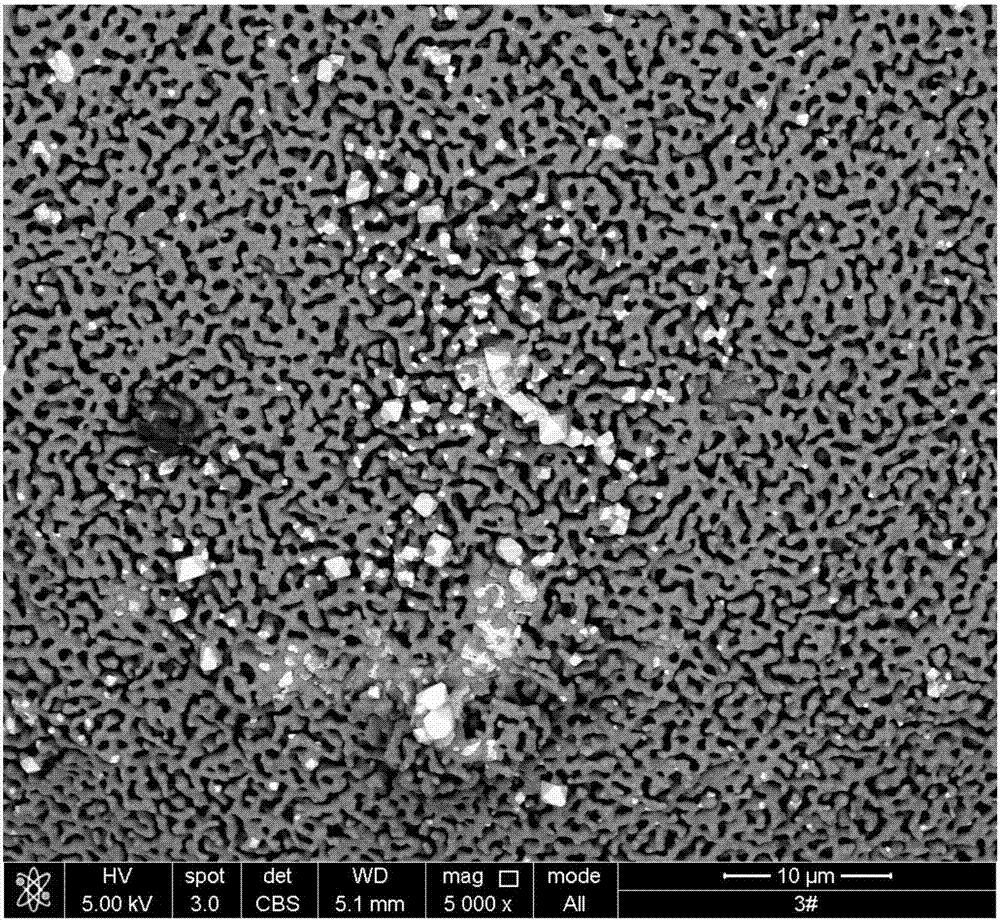
本发明涉及一种方石英及其制备方法和应用。
背景技术:
:方石英是石英的一种,为硅氧化合物,四方晶质,具有高散射性、高白度、低密度、色泽光亮、抗腐蚀、耐刻划、耐擦洗和消光效果好等良好的性质。近年来,方石英已广泛应用于精密铸造、电子材料、生物材料和航空航天等领域,且需求量逐年增加,但进口价格较高。(雷芸等,硅酸盐通报,2011)。目前已知的方石英为大多为非孔结构,硅质骨架致密,导热系数高(常温下为2.5w/m.k)(郭敬荣译,1995)。自然界中方石英的含量很少,只在火山岩中少量存在。因此,工业使用的方石英几乎均为人工合成。目前,通常采用高温煅烧(>1000℃)石英的方法制备方石英。余桂林等(方石英的制备及其对磷酸盐包埋材料性能的影响,武汉科技大学学报(自然科学版),2005年9月)将石英置于1400℃以上的温度下,发现有方石英相生成。申柯娅等(方石英的制备及其热性能测试,铸造技术,2013年3月)将石英粉体、水及添加剂混合均匀干燥后在1300℃煅烧获得石英陶瓷,再经过1500℃煅烧10h得到方石英块料。中国专利cn101041548a中提到将石英粉料与相变催化剂y2o3、na2co3和baf2放在一起升温至1300℃保温6小时得到方石英。中国专利cn101531368a公开了一种以石英坩埚为原料制备方石英材料的方法,利用已经1400-1600℃高温处理过石英坩埚,经过表面除杂、破碎和研磨工艺获得方石英材料。这些的方法显著缺点在于,第一,高温煅烧,耗能高,煅烧条件苛刻;第二,制备过程工艺复杂,成本较高。目前已知的制备多孔方石英的方法较少。专利cn103771426a公开了一种以硅藻土为原料低温烧制多孔方石英的方法,硅藻土是由硅藻生物遗骸沉积形成的天然无定形sio2,其含有丰富的大孔结构,将硅藻土加入偏硅酸钠或碱金属的硅酸盐溶液中,干燥后升温至600-800℃,煅烧后得到多孔方石英。但是该方法对原料要求苛刻,需要具有多孔结构的硅藻土。甲烷氧化偶联反应是直接以天然气为原料的方法,几十年来一直是关注的焦点,但是甲烷氧化偶联反应需要在较高温度下进行,对催化剂在高温条件下的稳定性提出了要求,因此亟需一种在高温和恶劣环境下稳定的催化剂载体。技术实现要素:本发明的目的是克服现有方石英制备技术中耗能高、工艺复杂和产品工业应用有限的不足,提供一种以二氧化硅为原料、低能耗、工艺简单和产品具有潜在工业应用价值的多孔结构的方石英及其制备方法和在甲烷氧化偶联反应中的应用。本发明的发明人发现,方石英作为一种在高温和恶劣环境下性质稳定的材料,如果能够具有多孔结构,将是理想的催化剂载体。本发明的发明人做了深入研究并发现,在采用钨酸盐作为助剂的情况下,普通的二氧化硅可以转化为多孔方石英,且反应温度明显低于现有技术教导的温度。多孔结构的方石英可以作为甲烷氧化偶联反应的催化剂载体,且具有更多潜在工业应用价值。本发明提供了一种方石英,其特征在于,该方石英具有多孔结构,所述方石英的比孔容为0.5-0.7ml/g,平均孔径为400-900nm,最可几孔径为400-850nm,该方石英含有70-99.9重量%的二氧化硅和0.1-30重量%的以氧化物计的钨组分。本发明还提供了一种方石英的制备方法,该方法包括:将二氧化硅与钨酸盐溶液接触然后干燥,将干燥后的固体在600-850℃下保持0.5-24h。本发明另外提供了上述方石英作为催化剂的载体的应用。本发明与现有技术相比的优势在于:1、本发明提供和制备的方石英除具有其他方法制备得到的方石英的固有性质外,还具有多孔的结构,且孔径分布均匀,具备潜在的工业化应用价值,有望开拓方石英新的工业应用领域;2、本发明提供的方法简单、对设备的要求低、耗能低,并且二氧化硅原料易得、储量丰富,因此生产成本低廉;3、本发明所提供和制备的方石英作为催化剂的载体具有高温下稳定的性质。本发明的其它特征和优点将在随后的具体实施方式部分予以详细说明。附图说明附图是用来提供对本发明的进一步理解,并且构成说明书的一部分,与下面的具体实施方式一起用于解释本发明,但并不构成对本发明的限制。在附图中:图1是根据实施例1制得的方石英的xrd图。图2是根据实施例1制得的方石英的sem图。图3是根据实施例1制得的方石英的孔径分布图,其中纵坐标表示压汞量对数微分。图4是在一个具体的实施方式中,根据本发明的方法所采用的原料二氧化硅的sem图。具体实施方式以下对本发明的具体实施方式进行详细说明。应当理解的是,此处所描述的具体实施方式仅用于说明和解释本发明,并不用于限制本发明。本发明提供了一种方石英,其特征在于,该方石英具有多孔结构,所述方石英的比孔容为0.5-0.7ml/g,平均孔径为400-900nm,最可几孔径为400-850nm;优选地,所述方石英的比孔容为0.6-0.7ml/g,平均孔径为500-850nm,最可几孔径为500-800nm。当根据本发明的方石英用于作为甲烷氧化偶联反应中的催化剂载体时,所述方石英的比孔容为0.5-0.7ml/g,平均孔径为400-900nm,最可几孔径为400-850nm;优选地,所述方石英的比孔容为0.6-0.7ml/g,平均孔径为500-850nm,最可几孔径为500-800nm。本发明中,测定比孔容、平均孔径和最可几孔径的方法是本领域技术人员所公知的,在此不再赘述。根据本发明的方石英,该方石英可以含有70-99.9重量%的二氧化硅和0.1-30重量%的以氧化物计的钨组分,优选含有85-99重量%的二氧化硅和1-15重量%的以氧化物计的钨组分,在本发明中,将钨组分计为wo2.5的形式。根据本发明的方石英,该方石英的颗粒大小和形状可以根据该方石英的具体应用场合在较大的范围内进行适当的选择,例如,当方石英用作甲烷氧化偶联反应的催化剂的载体时,颗粒形状可以为球形,颗粒直径可以为40-100目。本发明还提供了一种方石英的制备方法,该方法包括:将二氧化硅与钨酸盐溶液接触然后干燥,将干燥后的固体在600-850℃下保持0.5-24h。根据本发明的方法,所述二氧化硅的用量与钨酸盐溶液的用量的重量比可以为1:1-20,优选为1:1-5;所述钨酸盐溶液的浓度可以为0.01-30重量%, 优选为0.01-15重量%,更优选为0.01-8重量%。根据本发明的方法,所述二氧化硅与钨酸盐溶解接触是指将二氧化硅与钨酸盐溶液混合均匀,使二氧化硅能够充分分散在钨酸盐溶液中。所述二氧化硅与钨酸盐溶液接触的方法没有特别的限定,只要能够使二氧化硅在钨酸盐溶液中充分分散即可,例如,可以采用搅拌的方式。根据本发明的方法,所述干燥可以采用本领域常规的用于干燥的方法和设备,例如可以在90-150℃的恒温干燥烘箱中干燥0.5-5小时,优选在110-130℃的恒温干燥烘箱中干燥2-4小时。根据本发明的方法,将干燥后的固体在600-850℃下保持0.5-24h,优选地,将干燥后的固体在700-850℃下保持3-10h。该过程可以在本领域常规的能够提供高温且维持恒定温度的设备中进行,例如可以在马弗炉中进行。在本发明的一种优选的实施方式中,将干燥后的固体在马弗炉中以2-10℃/min的恒定速度升温至所需温度。根据本发明的方法,所述二氧化硅可以为致密无孔的球状或粉末状的无定形二氧化硅,例如可以选用如图4所表达的结构的二氧化硅。根据本发明的方法,所述钨酸盐溶液为钨酸钠和/或钨酸钾溶液。本发明又提供了一种由本发明的方法制备的多孔方石英。本发明另外提供了上述方石英作为催化剂的载体的应用,优选地,所述催化剂为用于甲烷氧化偶联反应的催化剂。在本发明一种优选的应用方式中,将根据本发明的方石英与硝酸盐溶液接触然后干燥,将干燥后的固体在750-950℃下焙烧7-9小时,得到以方石英为载体的催化剂;其中,所述方石英的用量与硝酸盐的用量的重量比可以为1:1-20,所述硝酸盐的浓度可以为1-5重量%,所述硝酸盐优选为硝酸锰,所述焙烧优选在马弗炉中进行。应注意到,以上提及的实施方式说明而不是限制本发明,并且在不偏离 所附权利要求的范围下,本领域技术人员能设计许多可选的实施方式。此外,在上述具体实施方式中所描述的各个具体技术特征之间也可以进行任意组合,只要其不违背本发明的思想,其同样应当视为本发明所公开的内容。为了避免不必要的重复,本发明对各种可能的组合方式不再另行说明。实施例1称取0.28g钨酸钠,加入10g蒸馏水中,溶解完全后,再加入5g二氧化硅,充分搅拌后放置120℃恒温干燥烘箱中干燥2h,干燥后的固体置于马弗炉中,以5℃/min的速率升温至700℃,在700℃保温4h,得到多孔方石英。根据物料投料量计算可知,所得多孔方石英含有95.2重量%的二氧化硅和3.6重量%的以氧化物计的钨组分。经测量,所得多孔方石英的比孔容为0.6777ml/g,平均孔径约为788.6nm,最可几孔径为568.5nm。取制得的方石英,对其进行扫描电子显微镜(sem)、x射线衍射(xrd)和孔径分布检测,检测结果分别如图1、图2和图3所示。由图1可以看出,制备得到的产品具有方石英的特征峰。由图2可以看出,方石英产品的孔结构为细长型不规则孔道且孔道分布比较均匀。由图3可以看出,孔径分布为高而窄的峰,也就是说孔径分布非常集中,证明方石英产品的孔径均匀。实施例2称取0.5g钨酸钠,加入15g蒸馏水中,溶解完全后,再加入5g二氧化硅,充分搅拌后放置110℃恒温干燥烘箱中干燥3h,干燥后的固体置于马弗炉中,以3℃/min的速率升温至750℃,在750℃保温5h,得到多孔方石英。根据物料投料量计算可知,所得多孔方石英含有91.8重量%的二氧化硅和6.2重量%的以氧化物计的钨组分。经测量,所得多孔方石英的比孔容为0.51ml/g,平均孔径约为526.4nm,最可几孔径为496.7nm。实施例3称取1g钨酸钠,加入25g蒸馏水中,溶解完全后,再加入5g二氧化硅,充分搅拌后放置130℃恒温干燥烘箱中干燥4h,干燥后的固体置于马弗炉中,以7℃/min的速率升温至800℃,在800℃保温8h,得到多孔方石英。根据物料投料量计算可知,所得多孔方石英含有84.8重量%的二氧化硅和11.5重量%的以氧化物计的钨组分。经测量,所得多孔方石英的比孔容为0.6911ml/g,平均孔径约为630nm,最可几孔径为616.7nm。实施例4称取2.7g钨酸钠,加入30g蒸馏水中,溶解完全后,再加入5g二氧化硅,充分搅拌后放置150℃恒温干燥烘箱中干燥5h,干燥后的固体置于马弗炉中,以10℃/min的速率升温至860℃,在860℃保温11h,得到多孔方石英。根据物料投料量计算可知,所得多孔方石英含有67.5重量%的二氧化硅和25重量%的以氧化物计的钨组分。经测量,所得多孔方石英的比孔容为0.5ml/g,平均孔径约为846.7nm,最可几孔径为805nm。对比例1按照cn103771426a的方法制备多孔方石英,具体为:称量0.8g九水偏硅酸钠,溶于10ml超纯水中,再加入5g硅藻土粉末,该悬浮液充分搅拌后放入烘箱中80℃烘5小时干燥,干燥后的固体置于马弗炉中,以5℃/min的速率升温至600℃,在600℃保温24小时,得到多孔方石英。所得多孔方石英不含钨组分。经测量,所得多孔方石英的比孔容为0.1ml/g,平均孔径约为280nm,最可几孔径为250nm。对比例2按照实施例1的方法制备方石英,所不同的是,助剂溶液为硅酸钠溶液。所得多孔方石英不含钨组分。经测量,所得多孔方石英的比孔容为0.12ml/g,平均孔径约为270nm,最可几孔径为253nm。应用例用实施例1-4和对比例1-2制备得到的多孔方石英作载体,称取5g,倒入10ml溶度为2%的硝酸锰溶液中,干燥后,放置马弗炉中焙烧,烧结终点温度850℃,保温8h,制备得到甲烷氧化偶联反应催化剂。称取催化剂0.2g,放置在石英管固定床反应器中,通入甲烷和氧气,空速为12000ml/(g.h),烷氧比为3。在800℃时得到甲烷转化率、碳二烃选择性和催化剂形态变化程度如表1所示。表1甲烷转化率(%)碳二烃选择性(%)催化剂形态变化程度实施例142.550.3未改变实施例243.150.2未改变实施例343.551.2未改变实施例442.850.8未改变对比例123.926.9未改变对比例223.826.7未改变对比实施例和对比例可以看出,采用本发明提供的方法制备的多孔方石英作为甲烷氧化偶联反应的催化剂载体使用时,可以在高温环境下保持形态不变,且能够实现更高的甲烷转化率和碳二烃选择性。以上详细描述了本发明的优选实施方式,但是,本发明并不限于上述实 施方式中的具体细节,在本发明的技术构思范围内,可以对本发明的技术方案进行多种简单变型,这些简单变型均属于本发明的保护范围。当前第1页12