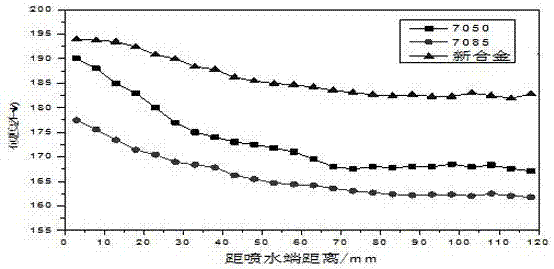
本发明属于合金材料领域,涉及一种铝合金材料的制备方法,特别是涉及一种高强高韧高淬透的铝合金材料的制备方法。
背景技术:
:高强高韧、高淬透及高抗腐蚀性能的铝合金板材,被广泛运用于航空航天工业。近年来随着飞机减重和安全性的要求,航空领域开始使用大型整体式铝合金结构件,获得了很好的减重效果,安全性也得到极大的提高。与此同时,就需要大规格高性能的铝合金板材,所需板材的厚度越来越厚。而板材越厚,沿厚度方向的性能差异就越大,往往厚板心层的性能达不到使用要求。同时,铝合金厚板用于航空工业也具有“水桶效应”,由于厚板心层性能不达标而限制了对其的使用。因此,高强高韧高淬透的7000系铝合金是飞机用大型整体式结构件制造的关键材料。大型化和整体化的飞机结构件对高性能铝合金厚板生产过程中的热变形及热处理环节提出了前所未有的挑战,其中铝合金厚板淬透性就是最致命的问题之一。而现有的技术方案,是通过优化合金成分,降低合金中淬火敏感的mg和cu元素含量,提高合金中的zn含量,提高zn/mg比值,严格控制微量元素cr、mn和ti以及杂质元素fe、si的含量,开发出以7085、7081合金为代表的新一代航空用合金,满足了厚度300mm以下厚板及锻件制造的需求。因此,现有技术的缺点主要体现在:(1)表层力学性能比起成熟牌号如7050、7055等稍显不足;(2)只能满足厚度300mm以下厚板及锻件制造的需求;(3)在板材厚度要求100mm以下的情况下不具有明显优势,还不足以完全取代7050、7055等常用合金。技术实现要素:为克服现有技术中存在的航空厚板的力学性能低、厚板厚度有限的缺点,本发明的目的是提供一种创新的生产方法来制备高强高韧高淬透铝合金材料,从而提高其力学性能,并且能制造厚板及锻件厚度超过300mm的航空用铝合金。为实现上述目的,本发明使用的技术方案为:一种铝合金材料的制备方法,包括以下步骤:s1:按重量取各金属材料,各金属材料的成分组成和重量百分比为:zn8~12wt%,mg1.0~2.4wt%,cu0.4~2.2wt%,zr0.05~0.25wt%,余量为al及不可避免的杂质,并且,4.5≤zn/mg≤6,0.65≤cu/mg≤0.95;s2:将上述的各金属材料都投至高温熔炼炉内进行熔炼,在熔炼过程中不断调整各金属材料的比例,直至满足预定的要求;s3:将步骤s2所得的金属液进行铸造,得到锭坯;s4:将步骤s3所得的锭坯进行均热处理;s5:将步骤s4所得的锭坯的头尾切除并进行铣面,锯切成400~600mm厚,1500~2000mm宽的坯料;s6:将步骤s5所得的坯料在350~450℃下预热4~20小时,得到铸锭;s7:将步骤s6所得的铸锭轧制成厚度为50~400mm的厚板;s8:将步骤s7所得的厚板送到辊底炉内进行固溶淬火处理;s9:将步骤s8所得的板材进行拉伸处理,拉伸量为1%~3%;s10:将步骤s9所得的板材进行时效处理;s11:将步骤s10所得的板材进行检验,获得合格的成品板材;s12:将步骤s11所得的合格的成品板材按需求的规格进行锯切。优选的,所述步骤s1中各金属材料的成分组成和重量百分比为:zn9~11wt%,mg1.2~2.2wt%,cu0.6~2.0wt%,zr0.10~0.20wt%,余量为al及不可避免的杂质,并且,4.5≤zn/mg≤6,0.65≤cu/mg≤0.95。优选的,所述步骤s2中的熔炼过程包括除气除渣工序和过滤工序。优选的,所述步骤s3中的铸造采用激冷的铸造技术,其中,铸造温度为670~725℃,铸造速度为30~50mm/min,铸造水流量为10~35m3/h,铸造水温为15~35℃。优选的,所述步骤s4中的均热处理采用多级逐步升温的均匀化技术。优选的,所述多级逐步升温的均匀化技术为:第一级,温度300~420℃,时间12~48h;第二级,温度425~450℃,时间12~36h;第三级,温度455~475℃,时间12~24h;第四级,温度476~495℃,时间10~20h。优选的,所述步骤s4中的均热处理采用先高温后低温再高温的均匀化技术。优选的,所述先高温后低温再高温的均匀化技术为:第一级,温度400~470℃,时间16~48h;第二级,温度250~400℃,时间24~72h;第三级,温度450~485℃,时间12~36h。优选的,所述步骤s8中的固溶淬火处理的保温温度为450~490℃,保温时间为500~1500min,淬火时,淬火室温不超过20℃。优选的,所述步骤s10中的时效处理具体为:第一级,温度40~120℃,时间2~36h;第二级,温度130~180℃,时间4~96h。与现有技术相比,本发明的有益效果是:(1)本技术设计的合金性能如强度、断裂韧性、电导率等显著提高,比现有的7085、7a85、7081等合金的性能提高5%以上;(2)利用本技术设计的合金制备得的厚板或者锻件,其厚度可达到300mm以上,且心表性能差异不超过8%。附图说明图1为本发明的工艺流程图;图2为本发明制备的新合金与7085、7050合金的淬透性曲线对比图;图3为本发明制备的新合金与7085、7050合金的硬度保留值曲线对比图。具体实施方式一种铝合金材料的制备方法,其工艺步骤如图1所示,具体为:s1:按重量取各金属材料,为了确保铝合金材料的高强高韧高淬透,各金属材料的成分组成和重量百分比为:zn8~12wt%,mg1.0~2.4wt%,cu0.4~2.2wt%,zr0.05~0.25wt%,余量为al及不可避免的杂质,同时还需要满足:4.5≤zn/mg≤6,0.65≤cu/mg≤0.95;s2:将上述的各金属材料都投至高温熔炼炉内进行熔炼,在熔炼过程中不断调整各金属材料的比例,直至满足预定的要求。同时,在熔炼过程中通过多级联合除气除渣工序降低铝熔体中的氢渣浓度,以减少铸锭中的气孔或针孔;通过过滤工序去除铝熔体中的氧化物、非金属夹杂物和其他有害金属杂质,以减少铸锭中的疏松、气孔、夹渣等缺陷。这样,就可以改善大规格铸锭的质量。s3:将步骤s2所得的金属液进行铸造,在熔铸过程通过铸造温度、铸造速度、铸造水流量的协同优化,采用激冷的铸造技术获得高质量的锭坯。其中铸造温度为670~725℃,铸造速度为30~50mm/min,铸造水流量为10~35m3/h,铸造水温为15~35℃。s4:将步骤s3所得的锭坯进行均热处理。均热处理采用多级逐步升温或先高温后低温再高温的均匀化技术。其中,多级逐步升温的均匀化技术为:第一级,温度300~420℃,时间12~48h;第二级,温度425~450℃,时间12~36h;第三级,温度455~475℃,时间12~24h;第四级,温度476~495℃,时间10~20h。而先高温后低温再高温的均匀化技术为:第一级,温度400~470℃,时间16~48h;第二级,温度250~400℃,时间24~72h;第三级,温度450~485℃,时间12~36h。通过均热处理,就可以消除残余结晶相,获得细小均匀弥散的al3zr粒子。s5:将步骤s4所得的锭坯的头尾切除并进行铣面,锯切成400~600mm厚,1500~2000mm宽的坯料;s6:将步骤s5所得的坯料在350~450℃下预热4~20小时,得到铸锭;s7:将步骤s6所得的铸锭采用强变形技术轧制成厚度为50~400mm的厚板;s8:将步骤s7所得的厚板送到辊底炉内进行固溶淬火处理。其中,固溶的保温温度为450~490℃,保温时间为500~1500min,淬火时,淬火室温不超过20℃。s9:将步骤s8所得的板材使用拉伸机来进行拉伸处理,拉伸量为1%~3%;s10:将步骤s9所得的板材进行时效处理。时效处理分成两级,其中,第一级的温度为40~120℃,时间为2~36h;第二级的温度130~180℃,时间为4~96h。经过这样的时效处理后,就可以提高板材的综合性能。s11:将步骤s10所得的板材进行检验,获得合格的成品板材;s12:将步骤s11所得的合格的成品板材按需求的规格进行锯切。实施例一生产成品规格厚度为60mm,宽度为1800mm,长度为6000mm的厚板,工序如下:(1)按重量百分比称取如下金属材料并投入至熔炼炉中:zn8~12wt%,mg1.0~2.4wt%,cu0.4~2.2wt%,zr0.05~0.25wt%,余量为al及不可避免的杂质,并且,4.5≤zn/mg≤6,0.65≤cu/mg≤0.95。(2)熔炼铝合金,经除气、过滤后,进行半连续铸造,铸出厚度为520mm的扁锭并均热。(3)将扁锭切头尾和铣面,经过预热和轧制,制备出厚度为60mm的厚板。(4)在厚板的表层切取30mm×30mm×140mm末端淬火试样。(5)将末端淬火试样在475℃固溶180min后,在末端淬火设备上进行淬火,之后经110℃/6h+150℃/12h时效后,测出淬透性曲线,并与7085和7050合金的淬透性曲线做对比,结果如图2和图3所示,从图中可以看出,本发明所制备的新合金、7085合金和7050合金两端的硬度差值分别为5.8%、8.8%和12%。实施例二生产成品规格厚度为60mm,宽度为1800mm,长度为6000mm的厚板,工序如下:(1)按重量百分比称取如下金属材料并投入至熔炼炉中:zn9~11wt%,mg1.2~2.2wt%,cu0.6~2.0wt%,zr0.10~0.20wt%,余量为al及不可避免的杂质,并且,4.5≤zn/mg≤6,0.65≤cu/mg≤0.95。(2)熔炼铝合金,经除气、过滤后,进行半连续铸造,铸出厚度为520mm的扁锭并均热。(3)将扁锭切头尾和铣面,经过预热和轧制,制备出厚度为60mm的厚板。(4)将板材在470℃固溶180min后进行淬火,之后进行变形量为2.5%的矫直,经110℃/6h+160℃/12h时效后,检测性能,并与7085和7050合金厚板性能对比,结果如表1所示。表1三种合金厚板(60mm)t7451的性能对比合金抗拉强度/mpa屈服强度/mpa延伸率/%断裂韧性/mpam1/2电导率/%iacs心表差异/%新合金5455219.53842.5470855124901134.5415.5705053250593240.58实施例三生产成品规格厚度为200mm,宽度为1800mm,长度为6000mm的超厚板,工序如下:(1)按重量百分比称取如下金属材料并投入至熔炼炉中:zn8~12wt%,mg1.0~2.4wt%,cu0.4~2.2wt%,zr0.05~0.25wt%,余量为al及不可避免的杂质,并且,4.5≤zn/mg≤6,0.65≤cu/mg≤0.95。(2)熔炼铝合金,经除气、过滤后,进行半连续铸造,铸出厚度为520mm的扁锭并均热。(3)将扁锭切头尾和铣面,经过预热和轧制,制备出厚度为200mm的超厚板。(4)将板材在470℃固溶600min后进行淬火,之后进行变形量为2.5%的矫直,经110℃/6h+160℃/12h时效后,检测性能,并与7085和7050合金厚板性能对比,如表2所示。表2三种合金超厚板(200mm)t7451的心层性能对比合金抗拉强度/mpa屈服强度/mpa延伸率/%断裂韧性/mpam1/2电导率/%iacs心表差异/%新合金53551693643.2570855004801031.542.5870504654197.52741.515实施例四生产成品规格厚度为350mm,宽度为1800mm,长度为6000mm的极厚板,工序如下:(1)按重量百分比称取如下金属材料并投入至熔炼炉中:zn9~11wt%,mg1.2~2.2wt%,cu0.6~2.0wt%,zr0.10~0.20wt%,余量为al及不可避免的杂质,并且,4.5≤zn/mg≤6,0.65≤cu/mg≤0.95。(2)熔炼铝合金,经除气、过滤后,进行半连续铸造,铸出厚度为520mm的扁锭并均热。(3)将扁锭切头尾和铣面,经过预热和轧制,制备出厚度为350mm的极厚板。(4)将板材在470℃固溶1200min后进行淬火,之后进行变形量为2.5%的矫直,经110℃/6h+160℃/12h时效后,检测性能,如表3所示。表3新合金极厚板(350mm)t7451的心层性能合金抗拉强度/mpa屈服强度/mpa延伸率/%断裂韧性/mpam1/2电导率/%iacs心表差异/%新合金5245048.534.544.56本发明的新合金在强度、断裂韧性、电导率等性能上有显著的提高,比现有的7085、7a85、7081等合金的性能提高5%以上;而其制备出的厚板或者锻件,厚度可达到300mm以上,且心表性能差异不超过8%。当前第1页12