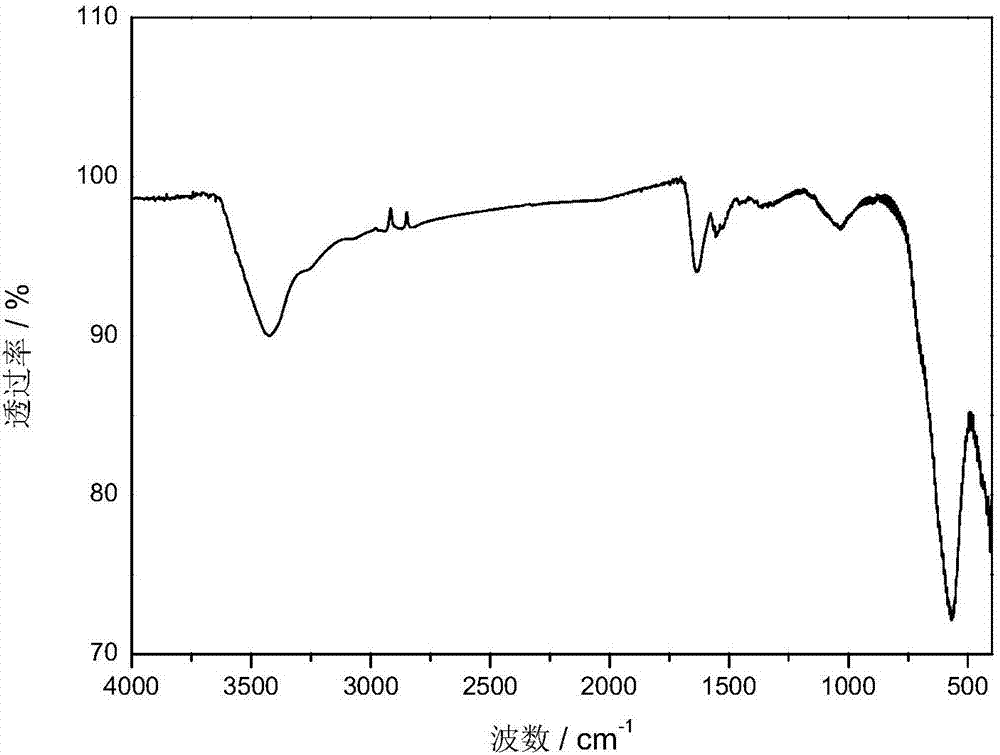
本发明涉及功能化材料领域,具体涉及一种粒径均匀的树枝状高分子修饰的磁性微球及其制备方法和应用。
背景技术:
:磁性微球包括磁性纳米粒子和微米粒子,由于其特殊的物理化学性质,使其在材料、生物等领域存在广泛的应用前景,如磁分离、药物磁靶向运输等方面。为了适应不同的用途,采用各种各样的改性磁性微球及其复合结构,如功能化硅包覆的磁性微球,聚合物接枝改性的磁性微球等材料被广泛的制备出来并且得到实际的应用。通常制备的功能化磁性微球表面基团含量较低,需要用高灵敏的检测方法进行检测和表征,如荧光等[参见chem.eur.j.2006,12,6341]。因此,发展制备表面功能基团丰富的磁性微球的方法对于提高磁性微球的应用效果和应用范围具有重要的意义。树枝状高分子具有高度支化、带有多功能基团且具有良好溶解性等特点,在纳米材料制备和生物医用等方面存在广泛的应用前景。树枝状高分子修饰的磁性微球的制备方法已有报道[cn101955231b,cn103157447b],但通常采用的是后修饰法,步骤多,耗时长。cn102092795a报道了一种有机高分子修饰的四氧化三铁多级球的制备方法,但由于其粒径不均匀,在具体应用时会影响其性能,如重现性差等。技术实现要素:针对上述问题,本发明公开了一种粒径均匀的,一步法制备的树枝状高分子修饰的磁性微球及其制备方法和应用,以满足不同应用领域的需要。为这样的目的,我们以树枝状高分子为修饰剂,以乙二醇为反应溶剂,并在反应体系中加入无水乙酸钠以增加静电稳定作用,防止磁性纳米颗粒团聚,采用水热法制备粒径均匀的树枝状高分子修饰的磁性微球。本发明的提供了一种粒径均匀的树枝状高分子修饰磁性微球,所述磁性微球通过在磁性载体表面引入树枝状高分子得到;所述磁性载体为磁性纳米粒子,或者磁性微米粒子。优选的,所述树枝状高分子为末端基团为氨基的树枝状高分子。更优选的,所述树枝状高分子为聚酰胺-胺树枝状高分子。进一步优选的,所述的树枝状高分子为第0代至第七代中的任何一代。本发明还提供了一种粒径均匀的树枝状高分子修饰磁性微球的制备方法,所述方法包括下述步骤:s100、配制合成磁性微球的溶液s200、将树枝状高分子均匀分散在合成磁性微球的溶液中;s300、通过水热合成一锅法将步骤s200获得的混合溶液合成树枝状高分子修饰的磁性微球。其中,所述合成磁性微球的溶液为:均匀溶解于20.0-50.0重量份乙二醇溶液中的1.0-5.0重量份生成磁性载体的铁化合物、2-10重量份无水乙酸钠。或者,所述合成磁性微球的溶液为:均匀溶解于20.0-50.0重量份乙二醇溶液中的2.0-10.0重量份的钴化合物、2-10重量份无水乙酸钠。所述树枝状高分子的用量为0.5-5.0重量份。优选的,所述水热合成一锅法可以包括下述步骤:s301、将所述混合溶液转移至水热反应釜,水热反应温度180至250℃,反应时间为6-10小时;s302、将制备得到的磁性微球,甲醇清洗3-5次,乙醇清洗3-5次,水清洗3-5次,再乙醇清洗3-5次;s303、将清洗后的磁性微球于50℃真空干燥12小时备用。优选的,所述水热合成一锅法还可以包括下述步骤:s311、将所述混合溶液转移至水热反应釜,水热反应温度200至350℃,反应时间为6-10小时;s312、将制备得到的磁性微球,甲醇清洗3-5次,乙醇清洗3-5次,水清洗3-5次,再乙醇清洗3-5次;本发明还提供了一种树枝状高分子修饰磁性微球的应用,将前述树枝状高分子修饰磁性微球应用于磁分离、污水处理与药物磁靶向输运。同现有技术相比,本发明的树枝状高分子修饰的磁性微球制备方法步骤少,简单易行,粒径均匀。制得的树枝状高分子修饰的磁性微球在水溶液或醇溶液中分散性和稳定性好。在污水处理、药物磁靶向输运与磁分离等各方面存在着巨大的应用前景。附图说明图1第四代的pamam树枝状高分子修饰的磁性四氧化三铁微球的透射电镜图;图2本发明一个实施例中关于第四代的pamam树枝状高分子修饰的磁性四氧化三铁微球的红外示意图;图3第四代的pamam树枝状高分子修饰的磁性四氧化三铁微球修饰硼酸后对腺苷的萃取量(图3中3),与背景文献chem.eur.j.2006,12,6341.文献中制备的氨基功能化磁性微球修饰硼酸后对腺苷的萃取量(图3中1)、背景文献cn103157447b中后修饰法制备的第四代的pamam树枝状高分子修饰的磁性微球修饰硼酸后对腺苷的萃取量(图3中2)对比示意图。具体实施方式下面结合附图1-3所示和实施例对本公开作进一步的详细说明。可以理解的是,此处所描述的具体实施例仅用于解释相关内容,而非对本公开的限定。另外还需要说明的是,为了便于描述,附图1-3中仅示出了与本公开相关的部分。下面将参考附图1-3并结合实施例来详细说明本公开。本发明提供的一个实施方式为一种粒径均匀的树枝状高分子修饰磁性微球,所述磁性微球通过在磁性载体表面引入树枝状高分子得到;所述磁性载体为磁性纳米粒子,或者磁性微米粒子。本发明的一方面,所述树枝状高分子为末端基团为氨基的树枝状高分子,优选为聚酰胺-胺树枝状高分子。更优选的,所述的树枝状高分子为第0代至第七代中的任何一代。本发明还提供了一种粒径均匀的树枝状高分子修饰磁性微球的制备方法,所述方法包括下述步骤:s100、配制合成磁性微球的溶液;s200、将树枝状高分子均匀分散在合成磁性微球的溶液中;s300、通过水热合成一锅法将步骤s200获得的混合溶液合成树枝状高分子修饰的磁性微球。如图1第四代的pamam树枝状高分子修饰的磁性四氧化三铁微球的透射电镜图;如图3第四代的pamam树枝状高分子修饰的磁性四氧化三铁微球修饰硼酸后对腺苷的萃取量(图3中3),与背景文献chem.eur.j.2006,12,6341.文献中制备的氨基功能化磁性微球修饰硼酸后对腺苷的萃取量(图3中1)、背景文献cn103157447b中后修饰法制备的第四代的pamam树枝状高分子修饰的磁性微球修饰硼酸后对腺苷的萃取量(图3中2)对比示意图。本发明的另一方面,所述合成磁性微球的溶液可以为:均匀溶解于20.0-50.0重量份乙二醇溶液中的1.0-5.0重量份生成磁性载体的铁化合物、2-10重量份无水乙酸钠。本发明的另一方面,所述合成磁性微球的溶液还可以为:均匀溶解于20.0-50.0重量份乙二醇溶液中的2.0-10.0重量份的钴化合物、2-10重量份无水乙酸钠。本发明的一个方面,所述树枝状高分子的用量为0.5-5.0重量份。本发明的另一方面,所述水热合成一锅法可以包括下述步骤:s301、将所述混合溶液转移至水热反应釜,水热反应温度180至250℃,反应时间为6-10小时;s302、将制备得到的磁性微球,甲醇清洗3-5次,乙醇清洗3-5次,水清洗3-5次,再乙醇清洗3-5次;s303、将清洗后的磁性微球于50℃真空干燥12小时备用。本发明的另一方面,所述水热合成一锅法还可以包括下述步骤:s311、将所述混合溶液转移至水热反应釜,水热反应温度200至350℃,反应时间为6-10小时;s312、将制备得到的磁性微球,甲醇清洗3-5次,乙醇清洗3-5次,水清洗3-5次,再乙醇清洗3-5次;如图2本发明一个实施例中关于第四代的pamam树枝状高分子修饰的磁性四氧化三铁微球的红外示意图。本发明还提供了一种树枝状高分子修饰磁性微球的应用,将前述树枝状高分子修饰磁性微球应用于磁分离、污水处理与药物磁靶向输运。以下通过具体实施例更加详细阐述本发明,以下实施例的说明只是用于帮助理解本发明的方法及其核心思想。实施例1:按照下述制备方法获得了四氧化三铁磁性微球:1.0重量份的六水合氯化铁,2.0重量份无水乙酸钠,1重量份第四代的pamam树枝状高分子,依次溶解于35.0重量份乙二醇溶液中,混合均匀,转移至水热反应釜,水热反应温度200℃。反应时间为6小时。将制备得到的磁性微球,甲醇清洗3-5次,乙醇清洗3-5次,水清洗3-5次,乙醇清洗3-5次。于50℃真空干燥12小时备用。如图1所示,图1为该第四代的pamam树枝状高分子修饰的磁性四氧化三铁微球的透射电镜图,从图上可以看出其粒径均匀,约为100nm。图2为第四代的pamam树枝状高分子修饰的磁性四氧化三铁微球的红外图,580cm-1是fe-o的特征吸收峰证明生成了磁性四氧化三铁微球,特征吸收峰1642cm-1,1549cm-1与1048cm-1证明了pamam修饰到磁性四氧化三铁微球表面了。实施例2:制备氧化钴磁性微球:2.0重量份的六水合氯化钴,10重量份无水乙酸钠,2重量份树枝状高分子,依次溶解于45重量份乙二醇溶液中,混合均匀,转移至水热反应釜,水热反应温度300℃。反应时间为8小时。将制备得到的磁性微球,甲醇清洗3-5次,乙醇清洗3-5次,水清洗3-5次,乙醇清洗3-5次。于50℃真空干燥12小时备用。实施例3:磁性分离应用实验将根据实施例1的方法制备的第四代的pamam树枝状高分子修饰的磁性四氧化三铁微球与4-甲酰基苯硼酸反应修饰上苯硼酸,对腺苷溶液进行萃取(硼酸功能化材料可以萃取腺苷),计算材料对腺苷的萃取量(图3中的3),同时与背景文献(cn103157447b)中氨基功能化磁性材料修饰硼酸后对腺苷的萃取量(图3中的1)和后修饰法制备的第四代的pamam树枝状高分子修饰的磁性四氧化三铁微球对腺苷的萃取量(图3中的2)进行对比,从图3可以看出,本发明方法制备的磁性微球修饰上苯硼酸后,对腺苷的萃取量增加58%,而且制备过程相对现有技术更加简单易行,更加快捷。对比例1:采用cn102092795a公开的方法制备了有机高分子修饰的四氧化三铁多级球。实施例1和对比例1相比区别如下:实施例1对比例1制备时间6小时12-72小时粒径(100±5)nm(250±50)nm颗粒均匀程度均匀不均匀通过比较可以发现采用本发明的方法制备的树枝状高分子修饰磁性微球比对比例1所需时间更短,粒径更均匀,而采用对比例1的方法制备的磁性微球需要的时间长,从文献cn102092795a的附图1可看出其粒径均匀程度较差。以上对本发明进行了详细介绍,本文中应用了具体个例对本发明的原理及实施方式进行了阐述,以上实施例的说明只是用于帮助理解本发明的方法及其核心思想;同时,对于本领域技术人员,依据本发明的思想,在具体实施方式及应用范围上均会有改变之处,综上所述,本说明书内容不应理解为对本发明的限制。当前第1页12