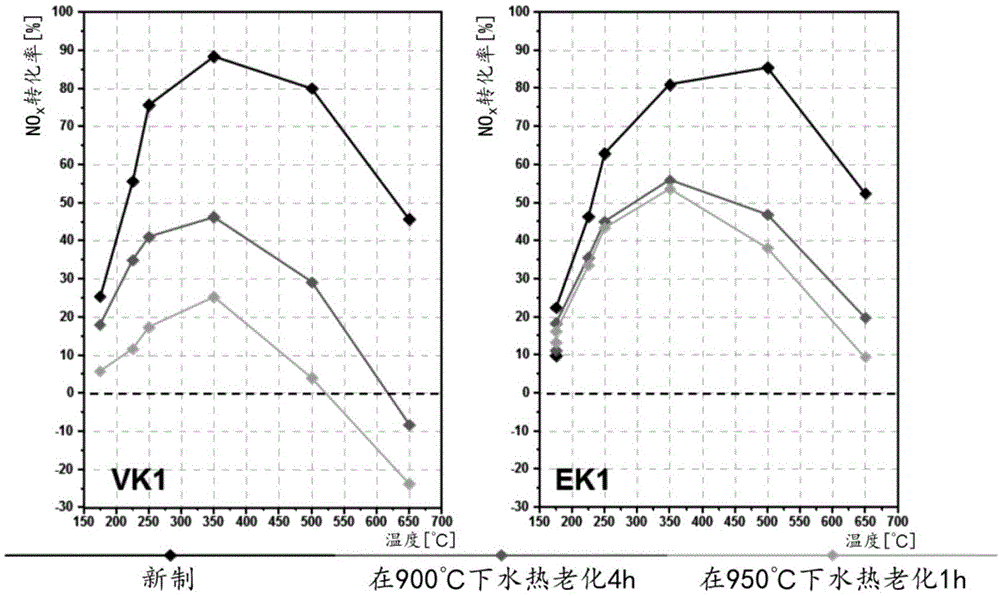
配备主要以稀燃操作的内燃机的机动车辆的废气具体地含有除了颗粒排放物之外的主要排放物一氧化碳co、碳氢化合物hc以及氮氧化物nox。由于相对较高的氧气含量为至多15体积%,因此一氧化碳和碳氢化合物可相对容易地通过氧化而变得无害。然而,氮氧化物还原成氮气变得更加困难。用于在存在氧气的情况下从废气中去除氮氧化物的一种已知方法是在合适的催化剂上借助于氨的选择性催化还原方法(scr方法)。在该方法中,利用氨将废气中待去除的氮氧化物转化为氮和水。用作还原剂的氨可通过将氨前体化合物例如尿素、氨基甲酸铵或甲酸铵给料到废气流中并且随后通过水解而可用。例如,某些金属交换沸石可用作scr催化剂。通常根据沸石最大孔开口的环尺寸将沸石细分成大孔、中孔和小孔沸石。大孔沸石具有12的最大环尺寸,并且中孔沸石具有10的最大环尺寸。小孔沸石具有8的最大环尺寸,并且例如具有插晶菱沸石(lev)结构类型。虽然基于铁交换β沸石的scr催化剂(即大孔沸石)例如已经得到使用并且仍被很大程度地用于重型卡车领域,但基于的小孔沸石的scr催化剂逐渐变得愈发重要;参见例如wo2008/106519a1、wo2008/118434a1和wo2008/132452a2。具体地讲,基于铜菱沸石和铜插晶菱沸石的scr催化剂最近是这方面的焦点。已知的scr催化剂确实能够使用氨作为还原剂来将具有高选择性的氮氧化物转化成氮和水。然而,从约350℃起,所谓的寄生氨氧化在基于铜菱沸石和铜插晶菱沸石的催化剂中开始,并且与期望的scr反应竞争。在这种情况下,还原剂氨与氧气在一系列副反应中被转化为一氧化二氮(氧化亚氮)、一氧化氮或二氧化氮,使得还原剂不能被有效利用,或者甚至由氨形成额外量的氮氧化物。这种竞争特别是在500℃至650℃的范围内的高反应温度下进行,其可发生在排气管路中scr催化剂上的柴油颗粒过滤器(dpf)的再生中。此外,必须确保催化剂材料对老化是稳定的,以便能够在机动车辆的整个使用寿命中实现高污染物转化率。为了甚至在dpf再生的反应温度下以及在使用寿命中实现高转化率,因此需要改进的scr催化剂材料的存在。wo2008/132452a2描述了与例如铜交换的小孔沸石,其可作为载体涂料涂覆到合适的整体式基材上或挤出形成基材。该载体涂料可包含选自铝氧化物、二氧化硅、(非沸石)二氧化硅铝氧化物、天然粘土、tio2、zro2和sno2的粘结剂。wo2013/060341a1描述了从酸性沸石或沸石型的物理混合物以质子形式或以铁促形式与例如cu/al2o3形成的scr活性催化剂组合物。《acscatal.》2012年第2卷第1432页至第1440页描述了nh3-scr反应期间氨在cuo/γ-al2o3上的反应途径。而含有0.5重量%的cuo/γ-al2o3的氨具体与一氧化氮反应以形成氮气,含有10重量%的cuo/γ-al2o3的氨具体与氧气反应以形成氮氧化物。现已令人惊奇地发现,基于插晶菱沸石(lev)结构类型的小孔沸石、铝氧化物以及铜的某些scr材料满足这些要求。本发明涉及一种scr活性材料,该scr活性材料包括:·插晶菱沸石(lev)结构类型的小孔沸石,·铝氧化物,以及·铜,其中铜以第一浓度存在于铝氧化物上并且以第二浓度存在于小孔沸石上,其特征在于,它包含相对于总材料的4重量%至25重量%的铝氧化物。根据插晶菱沸石(lev)结构类型的小孔沸石上存在铜的措辞,包括在本发明的范围内,作为沸石晶格骨架的一部分存在的铜,在沸石骨架的孔中存在离子交换形式的铜,以及可结合于三维沸石骨架或其表面上的任何其它形式的铜。根据铝氧化物上存在铜的措辞也涵盖铜可结合于三维铝氧化物骨架内或其表面上的所有形式。这还包括混合氧化物,诸如铝酸铜(cual2o4)。在各种情况下,术语“铜”都包括金属铜和离子形式的铜,以及氧化铜。此外,在本发明的范围内,术语“铝氧化物”不包括沸石的沸石晶格中的铝氧化物的比例。因此,“铝氧化物”仅包括根据(ii)的组分,而不是由沸石的sio2/al2o3比率(sar)产生的铝氧化物的比例。在根据本发明的scr活性材料的一个实施方案中,它包含相对于总材料的6重量%至16重量%,特别优选为6重量%至12重量%的铝氧化物。以cuo和相对于总scr活性材料计算的铜的总量具体为0.5重量%至15重量%-优选为1重量%至10重量%,并且特别优选为1.5重量%至7重量%。此处必须考虑到,与沸石相关的铜的优选量取决于沸石的sio2/al2o3比率。一般来讲,当沸石的sio2/al2o3比率增大时,可交换的铜的量减小。根据本发明,在沸石中交换到的铜与在沸石中的骨架铝的优选原子比(在下文中称为cu/al比率)具体为0.25至0.6。这对应于铜与沸石的理论交换水平为50%至120%,假定沸石中的完全电荷平衡由二价cu离子在100%的交换水平下开始。特别优选的为0.35至0.5的cu/al值,这对应于70%至100%的理论铜交换水平。cu/al比率为用于表征与铜交换的沸石的广泛使用量;参见例如wo2008/106519a1、《catalysistoday》1999年第54卷第407至418页(torreabreu等人)、《chem.commun.》2011年第47卷第800至802页(korhonen等人)或《chemcatchem》2014年第6卷第634至639(guo等人)。因此本领域的技术人员熟悉此量。cu/al比率可通过例如电感耦合等离子体发射光谱(icp-oes)法确定。该方法是本领域技术人员已知的。在本发明的一个具体实施方案中,scr活性材料包括插晶菱沸石(lev)结构类型的小孔沸石、铝氧化物以及铜,其特征在于,它包含相对于总材料的5重量%至25重量%的铝氧化物,并且铜以第一浓度存在于铝氧化物上,并且以第二浓度存在于插晶菱沸石(lev)结构类型的小孔沸石上。如果第一浓度(铝氧化物上的铜浓度)高于第二浓度(插晶菱沸石(lev)结构类型的小孔沸石上的铜浓度),则是特别有利的。第一浓度优选地比第二浓度高至少1.5倍,特别优选地高至少3倍。例如,第一浓度比第二浓度高1.5倍至20倍或3倍至15倍。可使用透射电子光谱学(tem)和能量色散x射线光谱学(edx)确定第一浓度和第二浓度的比率。为此,制备根据本发明的scr活性材料的薄段,然后使用edx确定沸石区域和铝氧化物区域内的铜浓度,并且求出比例。该方法是本领域技术人员已知的,并且在文献中有所描述。在实施方案中,根据本发明的scr活性材料不含贵金属,诸如铂、钯和铑。插晶菱沸石(lev)结构类型的小孔沸石为例如硅铝酸盐。这些沸石包括天然存在的,但优选地合成制备的小孔lev沸石。这些沸石是本领域技术人员所熟知的,例如,名称为nu-3、zk-20、lz-132、lz-133、zsm-45、rub-50、ssz-17或插晶菱沸石(levynite或levyne)。在本发明的实施方案中,它们具有5至50,优选地14至40,特别优选地20至40,非常特别优选地30至40的sar值。在本发明的范围内,术语“插晶菱沸石(lev)结构类型的小孔沸石”不仅包括上述硅铝酸盐,而且还包括所谓的硅铝酸盐(sapo)和磷酸铝(alpo)类型的沸石类材料。示例为sapo-35、sapo-67和alpo-35。对于这些材料,上述硅铝酸盐的优选sar值不适用。插晶菱沸石(lev)结构类型的小孔沸石的平均微晶尺寸(d50)为例如0.1μm至20μm,优选地0.5μm至10μm,特别优选地1μm至4μm。可通过扫描电子显微镜(sem)来确定平均微晶尺寸。该方法是本领域技术人员所熟知的。bet表面积为30m2/g至250m2/g,优选为100m2/g至200m2/g(根据iso9277确定)的铝氧化物特别适合作为铝氧化物。这种材料是本领域技术人员已知的,并且可商购获得。此外,还考虑了掺杂有其他元素以改善或调节物理或化学特性的铝氧化物。已知的元素为例如si、mg、y、la和镧系元素(例如ce、pr、nd),其可与铝形成混合氧化物化合物,并且可因此例如改变酸性或表面稳定性。铝氧化物与一种或多种元素的掺杂量应小于相对于相应的混合氧化物的15重量%,优选地小于10重量%,并且特别优选地小于5重量%。铝氧化物可以用作此类材料,但优选的为在scr活性材料生产的范围内形成铝氧化物的合适前体,诸如勃姆石或铝盐(例如硝酸铝)。在本发明的一个实施方案中,scr活性材料以其中插晶菱沸石(lev)结构类型的小孔径沸石形成芯的形式存在,并且铝氧化物形成围绕该芯的外壳。此类结构被称为核/壳结构,并且例如在wo2012/117042a2中有所描述。例如,通过干燥以及随后煅烧插晶菱沸石(lev)结构类型的小孔沸石、铜盐、铝氧化物或铝氧化物前体化合物的水性悬浮液,可制备根据本发明的scr活性材料。例如,向一个插晶菱沸石(lev)结构类型的小孔沸石中加入水,搅拌时加入可溶性铜盐,并且随后加入铝氧化物或对应的铝氧化物前体。根据本发明所得到的scr活性材料在水中的悬浮液可以进行例如过滤和/或干燥。在另一个实施方案中,lev结构类型的干燥的或潮湿的但自由流动的小孔沸石可以根据所述孔填充方法(等体积浸渍法)以浸渍的形式与铜盐溶液混合,例如,通过喷涂在合适的犁头混合机中,随后干燥并且煅烧。可在此为铝氧化物或铝氧化物前体提供干燥沸石和/或以溶液形式进行喷涂,以便获得根据本发明的scr活性材料。优选的铜盐为可溶于水的盐,诸如硫酸铜、硝酸铜和乙酸铜。特别优选的为硝酸铜和乙酸铜,非常特别优选的为乙酸铜。干燥的类型可采用不同的方法进行。例如,喷雾干燥、微波干燥、带式干燥、辊筒式干燥、冷凝干燥、滚筒干燥、冷冻干燥和真空干燥都是本领域技术人员所熟知的。优选的为喷雾干燥、带式干燥、辊筒式干燥和冷冻干燥。特别优选的为喷雾干燥。在这种情况下,通过喷雾器将悬浮液引入热气体通路中,在极短的时间(几秒至几分之一秒)内干燥以形成scr活性材料。在一个优选的实施方案中,随后将scr活性材料在空气或空气/水混合物中(优选在空气/水混合物中)进行煅烧,例如,在500℃至900℃的温度下。煅烧优选地在600℃至900℃之间的温度下发生,特别优选地在750℃至900℃下,并且非常特别优选地在800℃和900℃之间。在本发明的另一个实施方案中,这是可能的:例如,洗涤和干燥以及任选地煅烧插晶菱沸石(lev)结构类型的小孔沸石和铜盐(或用铜已经合成的lev)的水性悬浮液后,随后悬浮材料,从而得到具有铝氧化物或相应的铝氧化物前体的水溶液,再次进行干燥和煅烧,并且从而制备出根据本发明的scr活性材料。例如,随后可将该材料再悬浮于水中,任选地进行研磨,向其提供粘结剂并且将其涂覆到载体基材上。作为用于涂覆流通式基材的粘结剂,可使用例如al2o3、sio2、tio2、zro2或其前体及其混合物。过滤基材的涂覆过程中通常不需要粘结剂。为清楚起见,此处应当指出,用于制备根据本发明的scr活性材料的铝氧化物或铝氧化物前体与含铝粘结剂材料的不同之处在于:1.其使用量与本领域技术人员应使用的量相比更高,以获得载体涂料组分更高的粘合强度。2.其已经用于制备scr活性材料,并且不仅用于改善流通式基材上催化活性材料的粘合强度。3.铝氧化物表面存在一部分铜。4.将含铝氧化物或铝氧化物前体的scr活性材料先进行煅烧,再涂覆到基材上,由此丧失典型的粘结剂属性。5.如需涂覆过滤基材的多孔壁(例如,在壁流式过滤器的壁内涂覆),以便增加催化活性材料的热稳定性,则也可用铝氧化物制备根据本发明的scr活性材料。在这种情况下不需要使用粘结剂,因为当催化活性材料位于过滤器的孔中时,不需要粘结剂的粘结特性。此外,如果涂覆的催化活性材料的量原本会保持不变,则附加的粘结剂将导致过滤器上方的背压不期望地升高。6.其有助于在根据本发明的scr活性材料热老化后提高nox转化率,并且不被认为是催化活性的。在这种情况下,根据本发明的scr活性材料可以满足上文提到的点中的一个或多个或全部。例如,在第一步中,还可以干燥和任选地煅烧插晶菱沸石(lev)结构类型的小孔沸石、铜盐和部分量的铝氧化物或铝氧化物前体的水性悬浮液或湿悬浮液,并且随后在第二步中,将对应的附加部分量的铝氧化物或铝氧化物前体所获得的材料再悬浮于水溶液中,使其再次干燥和煅烧,并且从而制备根据本发明的具有al2o3的必要总量的scr活性材料。优选地25%至80%,特别优选地40%至70%的总铝氧化物或铝氧化物前体(按氧化铝计算)已在第一步期间添加。根据iso9277通过bet方法确定,根据本发明的scr活性材料的比表面积在950℃下在空气中煅烧5h后的比表面积超过400m2/g,优选地超过450g/m2,并且特别优选地450m2/g至600m2/g。根据本发明的材料特征还在于:在950℃的温度下在空气中煅烧5h后,根据iso9277确定,其具有其初始比表面积的80%以上。根据本发明的材料优选地特征在于:在1,000℃的温度下在空气中煅烧5h后,根据iso9277确定,其具有其初始比表面积的60%以上。在本发明的实施方案中,根据本发明的scr活性材料以涂层的形式存在于载体基材上。载体基材可为所谓的流通式基材或壁流式过滤器。它们可由例如碳化硅、钛酸铝、堇青石或金属组成。它们是本领域技术人员已知的,并且可商购获得。可通过本领域技术人员已知的方法将根据本发明的scr活性材料应用到载体基材上,例如,根据常用的浸涂方法或泵吸涂覆方法,随后进行热处理(煅烧),热处理优选地在350℃至600℃的温度下,特别优选地在400℃至550℃的温度下发生。本领域技术人员知道,在壁流式过滤器的情况下,它们的平均孔径和根据本发明的scr催化活性材料的平均粒度可彼此适应,使得所得的涂层位于形成壁流式过滤器的通道的多孔壁上(壁上涂层)。然而,平均孔径和平均粒度优选地彼此适应,使得根据本发明的scr活性材料定位于形成壁流式过滤器的通道的多孔壁上,因此发生内孔表面的涂层(壁内涂层)。在这种情况下,根据本发明的scr催化活性材料的平均粒度必须足够小以渗透到壁流式过滤器的孔中。如果根据本发明的scr活性材料以涂层形式存在于载体基材上,则其可作为唯一具有催化活性的涂层存在,然后优选地在载体基材的整个长度范围内延伸。然而,根据本发明的scr活性材料可也与载体基材上的其他催化活性涂层共存。在这种情况下,涂层可也在载体基材的整个长度范围内延伸或仅在其中一部分范围内延伸。本发明还涉及通过基质组分挤出scr活性材料以形成基材的实施方案。在这种情况下,载体基材是用惰性基质组分和根据本发明的scr活性材料形成的。不仅由惰性材料诸如堇青石组成而且还另外含有催化活性材料的载体基材、流通式基材和壁流式基材是本领域技术人员已知的。为了制备它们,根据本身已知的方法挤出由例如10重量%至95重量%的惰性基质组分和5重量%至90重量%的催化活性材料组成的混合物。在这种情况下,所有也用于生产催化剂基材的惰性材料都可用作基质组分。这些是例如硅酸盐、氧化物、氮化物或碳化物,其中特别优选的为硅酸镁铝。包含根据本发明的scr活性材料的挤出载体基材可用于废气净化。然而,它们可也采用与惰性载体基材相同的方式,通过常用方法涂覆附加的催化活性材料。根据本发明的scr活性材料可有利地用于净化稀燃操作的内燃机(特别是柴油发动机)的废气。其将废气中所含的氮氧化物转化为无害的化合物、氮和水,而且特别表征为具有高的老化稳定性。因此,本发明还涉及用于净化稀燃操作的内燃机的废气的方法,其特征在于,废气在根据本发明的scr活性材料上方经过。通常,该通道在还原剂存在的情况下发生。在根据本发明的方法中,氨优选地用作还原剂。例如,所需的氨可在根据本发明的scr活性材料上游的废气系统中形成,例如,借助上游氮氧化物存储催化剂(“稀nox捕集器”-lnt)。这种方法称为“被动scr”。然而,氨可也采用“活性scr方法”以尿素水溶液的形式携带,尿素水溶液根据需要通过根据本发明的scr活性材料上游的注射器给剂量。因此,本发明还涉及用于净化稀燃操作的内燃机中废气的设备,其特征在于,其包括根据本发明的scr活性材料(该scr活性材料优选地在惰性载体基材上涂覆的形式)以及提供还原剂的装置。氨通常用作还原剂。在根据本发明的设备的一个实施方案中,用于提供还原剂的装置因此为用于尿素水溶液的喷射器。该注射器通常以尿素水溶液进料,该水溶液源自携带的储水池,即,例如水箱。在另一个实施方案中,用于提供还原剂的装置为能够由氮氧化物形成氨的一种氮氧化物储存催化剂。此类氮氧化物储存催化剂是本领域技术人员已知的,并且在文献中进行了全面描述。例如,从sae-2001-01-3625中已知,如果氮氧化物存在于一氧化氮和二氧化氮的1:1或者在任何情况下接近该比率的混合物中,则与氨的scr反应进行得更快。由于稀燃操作的内燃机的废气通常具有与二氧化氮相比过量的一氧化氮,因此该文献提出借助于氧化催化剂来增加二氧化氮的比例。在一个实施方案中,根据本发明的设备因此还包括氧化催化剂。在本发明的实施方案中,载体材料上的铂用作氧化催化剂。本领域技术人员出于此目的知悉的所有材料被认为是载体材料。它们的bet表面积为30m2/g至250m2/g,优选地100m2/g至200m2/g(根据iso9277确定),并且特别是铝氧化物、氧化硅、氧化镁、氧化钛、氧化锆、氧化铈以及这些氧化物中至少两种的混合物或混合氧化物。氧化铝和铝/硅混合氧化物是优选的。如果使用铝氧化物,则特别优选地用例如氧化镧来稳定。例如,根据本发明的设备采用以下方式设计:首先在废气的流动方向上布置氧化催化剂,再布置用于尿素水溶液的喷射器,然后布置根据本发明的scr活性材料,优选地以惰性载体基材上的涂层的形式。另选地,首先在废气的流动方向上布置氮氧化物储存催化剂,然后布置按本发明的scr活性材料,优选地以惰性载体基材上的涂层的形式。在氮氧化物储存催化剂的再生过程中,在还原废气条件下,可形成氨。在这种情况下,氧化催化剂以及用于尿素水溶液的注射器是可有可无的。与常规的铜交换的小孔沸石相比,根据本发明的scr活性材料令人惊奇地具有优势。具体地讲,其特征在于显著更高的老化稳定性。本发明在接下来的实施例和附图中有更详细的解释。实施例1:在过滤基材上制备根据本发明的催化剂ek1制备了铜交换的插晶菱沸石(cu-lev,在850℃下煅烧2h)的水性悬浮液,含有32重量%的sio2/al2o3比率和3.5重量%的cu含量(按相对于沸石的cuo计算),还制备了含有20重量%的al2o3的勃姆石溶胶,使得干燥材料中铜交换的插晶菱沸石(lev)的重量百分比为88%,并且al2o3的重量百分比为12%。将悬浮液施加到可商购获得的过滤基材中,使得其在90℃下干燥和在550℃下煅烧后用干燥材料装载量为110g/l基材体积。比较例1:在过滤基材上制备比较催化剂vk1制备了铜交换的插晶菱沸石(cu-lev,在850℃下煅烧2h)的水性悬浮液,含有32重量%的sio2/al2o3比率和3.5重量%的cu含量(按相对于沸石的cuo计算)。铜交换的插晶菱沸石(lev)的重量百分比为100%。将悬浮液施加到可商购获得的过滤基材中,使得其在90℃下干燥和在550℃下煅烧后用干燥材料装载量为110g/l基材体积。与实施例1不同的是,比较例1中未加入勃姆石溶胶。比较例2:在过滤基材上制备比较催化剂vk2制备了铜交换的菱沸石(cu-cha)的水性悬浮液,含有30重量%的sio2/al2o3比率和4.0重量%的cu含量(按相对于沸石的cuo计算)。随后加入含有20重量%的al2o3的勃姆石溶胶,使得干燥材料中铜交换的菱沸石(cha)的重量百分比为92.6%,al2o3的重量百分比为7.4%。将悬浮液施加到可商购获得的过滤基材中,使得其在90℃下干燥和在550℃下煅烧后用干燥材料装载量为110g/l基材体积。实施例2:铝氧化物在根据本发明的催化剂(ek5至ek2)中含量的变化以及在流通式基材上的制备。制备了四种铜交换的插晶菱沸石(cu-lev,在850℃下煅烧2h)的水性悬浮液,含有32重量%的sio2/al2o3比率和3.5重量%的cu含量(按相对于沸石的cuo计算),还制备了含有20重量%的al2o3的勃姆石溶胶,使得干燥材料中铜交换的插晶菱沸石(cu-lev)的重量百分比x和al2o3的重量百分比y按表1变化。将悬浮液各自施加到可商购获得的流通式基材中,使得流通式基材在90℃下干燥和在550℃下煅烧后用干燥材料装载量对应于基材体积的变量z(g/l)。这是一种具有相对于铜交换的插晶菱沸石(cu-lev)的同等质量的涂层。表1:根据本发明的催化剂的名称以及变量x、y和z的值名称xcu-lev[重量%]yal2o3[重量%]z装载量[g/l]ek28812112ek39010110ek4928108ek5946106实施例3:改变al2o3加入量以形成根据本发明的材料(ek6)将含有32重量%的sio2/al2o3比率的插晶菱沸石(lev)分散于乙酸铜水溶液中,在80℃下保存3h,然后冷却到室温,再加入含有20重量%的al2o3的勃姆石溶胶。在这种情况下,选择所用反应物的量,使得干燥材料中cu含量为3.5重量%(按相对于插晶菱沸石(lev)量的cuo计算),al2o3的重量百分比(相对于总材料的氧化比例)为4%。使用在干燥并且在850℃下煅烧2h后得到的材料制得水性悬浮液,再加入含有20重量%的al2o3的勃姆石溶胶,使得根据本发明的干燥材料中al2o3的重量百分比为8%。将悬浮液施加到可商购获得的流通式基材中,使得其在90℃下干燥和在550℃下煅烧后用干燥材料装载量为108g/l基材体积。因此,这与ek4的装载量相同。与ek4相比,因此将相同总量的al2o3分两步引入到根据本发明的材料中。实施例4:制备ek7和ek8以根据bet方法进行比表面积确定将含有32重量%的sio2/al2o3比率的插晶菱沸石(lev)分散于乙酸铜水溶液中,在80℃下保存3h,然后冷却到室温,再加入含有20重量%的al2o3的勃姆石溶胶,最后将混合物进行干燥。在这种情况下,选择所用反应物的量,使得干燥材料中cu含量为3.5重量%(按cuo和相对于插晶菱沸石(lev)的量计算),al2o3的重量百分比(相对于总材料的氧化比例)为4%(ek7)或8%(ek8)。干燥后,将制备的材料ek7和ek8在950℃下在空气中煅烧5h,然后根据iso9277测定其比表面积。结果如表2所示。表2:ek7和ek8在950℃下煅烧5h后的比表面积材料比表面积[m2/g]ek8514±10ek7528±10比较实验:确定ek1、vk1、vk2、ek2至ek6的nox转化率在制备(新制)后和老化后将ek1和vk1在水热氛围(10%的h2o,10%的o2,其余为n2)中进行测定。仅在制备后和老化后将vk2以及ek2至ek6在水热氛围(10%的h2o,10%的o2,其余为n2)中进行测定。ek1、vk1和vk2的保持时间与老化温度为在900℃下保持4h和在950℃下保持1h。ek2至ek5仅在水热氛围中在950℃下仅1h就被老化。在所谓的nox转化率测试中,在模型气体反应器中确定催化剂ek1、vk1、vk2、以及ek2至ek5的nox转化率与催化剂的上游温度的函数。该nox转化率测试由包括预处理和针对各种目标温度运行的测试循环的测试程序组成。所施加的气体混合物记录在表3中。测试程序:1.在600℃下在n2中预处理10min2.针对目标温度重复测试循环a.在气体混合物1中接近目标温度b.加入nox(气体混合物2)c.加入nh3(气体混合物3),等到nh3突破20ppm,或最多30min的持续时间d.已编程的温度脱附温度最高500℃(气体混合物3)表3:nox转化率测试的气体混合物。气体混合物123n2平衡平衡平衡o210体积%10体积%10体积%nox0ppm500ppm500ppmno20ppm0ppm0ppmnh30ppm0ppm750ppmco350ppm350ppm350ppmc3h6100ppm100ppm100ppmh2o5体积%5体积%5体积%ek2至ek6测定的实例中的空速(ghsv)为60000h-1。在ek1、vk1和vk2的实例中,在500℃和60000h-1的空速(ghsv)下确定nox转化率。从500℃起,空速(ghsv)为100000h-1。对于低于500℃的每个温度点,对于测试程序范围2c确定nh3滑移为20ppm的转化率。对于高于500℃的每个温度点,在测试程序范围2c中确定平衡状态下的转化率。以各个温度点的这种nox转化率作图得到如图1、图3和图4所示的图绘。比较ek1和vk1以及vk2的催化活性:图1示出:与vk1相比,在900℃下水热老化4h后,ek1已在所考虑的温度范围内显著提升nox转化率,特别是在950℃下水热老化1h后尤为明显。这是由于通过加入al2o3制备的根据本发明的材料。图4示出:vk2在两种老化条件后的nox转化率远低于ek1和ek4的nox转化率(在950℃下水热老化1h后)。比较ek2至ek5的催化活性:图2示出:在950℃下水热老化1h后,发生nox转化率稳定在650℃,哪怕发生在根据本发明的形成材料中增加ek5至ek2的al2o3重量比例。比较ek4和ek6的催化活性:图3示出:在950℃下水热老化1h后,当在所述步骤中发生结合ek6中的根据本发明的材料所示的加入al2o3时,在高于350℃的温度范围内在ek4中得到根据本发明的材料的nox转化率的进一步稳定。当前第1页12