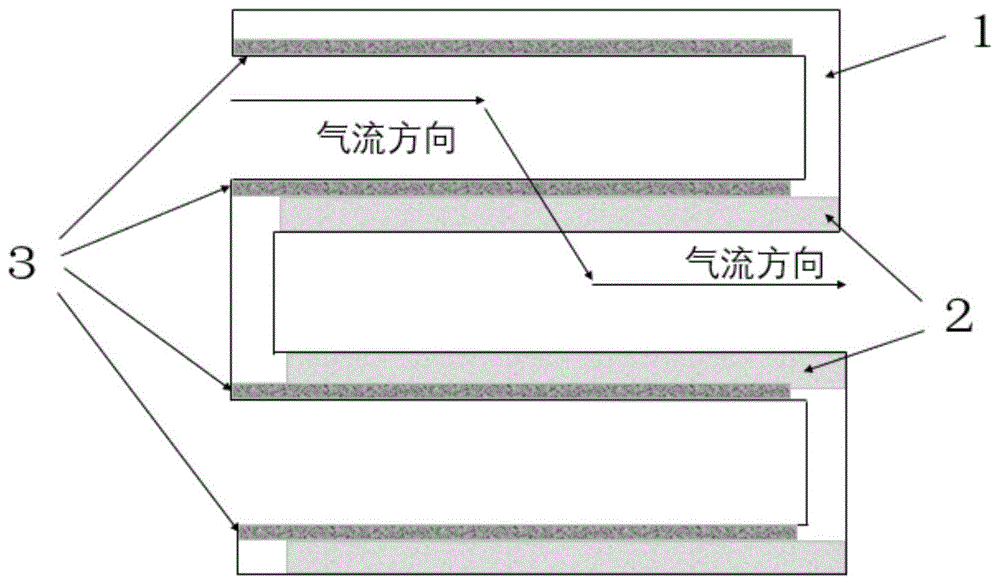
本发明涉及尾气净化材料领域,具体涉及一种汽油机颗粒捕集催化剂及其制备方法。
背景技术:
:随着能源和环境问题的日趋紧迫,为了保护环境,中国对机动车尾气的排放提出了更高的要求,中国即将在2020年实施国6排放标准,而不少区域甚至将法规提前至2019年开始实施。汽油机发动机排放的尾气中主要污染物为一氧化碳(co)、碳氢化合物(hc)、氮氧化合物(nox)和颗粒物(pm)等,且对于缸内直喷(gdi)或涡轮增压发动机(turbo)而言,其尾气中颗粒物浓度还会高于传统的自然吸气发动机(na)。对于国5及以前发动机的污染物排放标准,都主要是针对尾气中co、hc、nox的浓度限定,现有的汽车尾气净化催化剂也主要是将尾气中的co、hc、nox转化成二氧化碳(co2)、水(h2o)和氮气(n2)后再进行排放。但实施国6排放标准以后,尾气中颗粒物的浓度也成了重要限定标准,从而导致控制尾气中颗粒物的浓度成为一个新的难点。采用传统的三效催化剂(twc)只能有效的净化尾气中的co、hc和nox,却不能控制尾气中颗粒物的浓度,而汽油机颗粒捕集器催化剂(cgpf)却能显著降低尾气中颗粒物的浓度,从而使尾气达到国6的排放标准。发动机在偏浓(燃油过量,氧气不足)或者低温环境中运行时,尾气中颗粒物浓度更高,碳烟等颗粒物会在cgpf表面发生累积,随着积累量的增大,不仅会导致cgpf背压增加,造成排气阻力增大,而且可能导致碳烟发生剧烈燃烧,从而突然放出大量热量,产生的高温高热冲击会造成催化剂性能下降,甚至烧坏催化剂。因此,为了防止上述情况发生,需要提高cgpf催化剂对碳烟的燃烧能力,使碳烟可以尽早的燃烧,防止碳烟过分累积,即提高cgpf催化剂的被动再生能力。故提高cgpf催化剂的碳烟燃烧性能,是降低cgpf催化剂背压,延长cgpf催化剂的使用寿命的最佳方法,也有利于控制汽车尾气中颗粒物的排放。但在国内,cgpf催化剂通常安装在远离排气歧管的位置,尾气的温度较低,从而导致cgpf催化剂对碳烟的燃烧能力较低,容易导致cgpf表面碳烟的累积,进而影响cgpf催化剂对尾气中颗粒物的控制。技术实现要素:本发明的目的在于克服现有cgpf对碳烟的燃烧能力差的缺陷,提出一种利于碳烟燃烧的汽油机颗粒捕集催化剂及其制备方法;该汽油机颗粒捕集催化剂中的催化剂涂层采用了分层设置,不仅通过对催化剂涂层中的贵金属含量的调整,使催化剂进气端的催化剂涂层中贵金属的负载量显著高于出气端,从而能最大程度的利用催化剂涂层中高负载量贵金属对碳烟的燃烧温度的降低作用,来提高cgpf对碳烟的燃烧能力;同时,还通过对催化剂涂层中微孔孔径大小的调整,使进气端和出气端的催化剂涂层的孔径和孔容出现不同,从而降低催化剂的背压;并且,进气端催化剂涂层孔径和孔容更大,背压小,对碳烟的容纳量更大,进气端涂层与碳烟的接触面积更大,更有利于高浓度贵金属降低碳烟的催化燃烧温度,能进一步提高cgpf对碳烟的燃烧性能;本发明汽油机颗粒捕集催化剂对碳烟的燃烧能力更强,使用寿命更长,对控制汽车尾气中颗粒物的排放具有积极作用,有利于汽油机颗粒捕集催化剂大规模应用。为了实现上述发明目的,本发明提供了一种汽油机颗粒捕集催化剂,包括催化剂载体和催化剂涂层;其中,所述的催化剂涂层包括第一涂层和第二涂层;所述第一涂层位于催化剂载体出气端;所述第二涂层位于催化剂载体进气端;所述第二涂层中的微孔孔径大于所述第一涂层中的微孔孔径;所述第二涂层与第一涂层中钯的负载量之比为4-20︰1;所述第二涂层与第一涂层中铑的负载量之比为1-5︰1。优选的,所述第二涂层中的微孔孔径为3-20μm;所述第一涂层中的微孔孔径为0.01-2μm;优选的催化剂涂层孔径,催化剂对尾气的净化效果更好,对碳烟的燃烧能力更强,背压更低。优选的,所述第二涂层与第一涂层中钯的负载量之比为8-15︰1,所述第二涂层与第一涂层中铑的负载量之比为3︰1;优选的涂层贵金属负载量之比,催化剂对碳烟的燃烧温度降低效果更好,对提高cgpf对碳烟的燃烧能力效果更好。优选的,所述第一涂层中钯负载量为1-5g/ft3,铑负载量为1-5g/ft3;所述第二涂层中钯负载量为6-19g/ft3,铑负载量为1-5g/ft3;优选的涂层中贵金属负载量,使涂层的催化性能更好,对碳烟的燃烧能力更强,得到的汽油机颗粒捕集催化剂综合性能更好。为了实现上述发明目的,进一步的,本发明提供了一种汽油机颗粒捕集催化剂的制备方法,包括以下步骤:(1)制备浆料:将铈锆基复合氧化物、铝基复合氧化物、铝溶胶和去离子水混合球磨后,加入第一造孔剂,混合球磨后,再加入钯盐溶液和铑盐溶液,混合球磨得到第一涂层浆料;将铈锆基复合氧化物、铝基复合氧化物、铝溶胶和去离子水混合球磨后,加入第二造孔剂,混合球磨后,再加入钯盐溶液和铑盐溶液,混合球磨得到第二涂层浆料;所述第一造孔剂为分子量400-4000的聚乙二醇;所述第二造孔剂为分子量6000-20000的聚乙二醇;(2)涂覆:将第一涂层浆料涂覆到催化剂载体的出气端;将第二涂层浆料涂覆到催化剂载体的进气端;(3)焙烧:将涂覆好的催化剂载体进行干燥、焙烧,得到汽油机颗粒捕集催化剂。其中,优选的,步骤(1)所述第二涂层浆料中钯含量占催化剂涂层中总钯含量的75-90%;铑含量占催化剂涂层中总铑含量的10-90%;所述第一涂层浆料中钯含量占催化剂涂层中总钯含量的10-25%;铑含量占催化剂涂层中总铑含量的10-90%;优选的涂层浆料贵金属占比,使催化剂不同涂层中贵金属的负载量更好,分散更均匀,对碳烟的燃烧性能更好。其中,优选的,步骤(1)中所述的铈锆基复合氧化物中包括30-80wt%的ceo2、20-70wt%的zro2和0-15wt%的稀土金属氧化物;优选的铈锆基复合氧化物使催化剂涂层的催化性能更好,得到的汽油机颗粒捕集催化剂综合性能更好。其中,优选的,步骤(1)中所述的铝基复合氧化物包括70-100wt%的al2o3和0-30wt%的稀土金属氧化物;优选的铝基复合氧化物使催化剂涂层的催化性能更好,得到的汽油机颗粒捕集催化剂综合性能更好。其中,优选的,所述的稀土金属氧化物为la2o3、y2o3、nd2o3、zro2、pr6o11、bao或sro中的一种或多种;优选的稀土金属氧化物使催化剂涂层的催化性能更好,得到的汽油机颗粒捕集催化剂综合性能更好。其中,优选的,步骤(1)中所述铈锆基复合氧化物和铝基复合氧化物的质量比均为6︰1~1︰3;优选的铈锆基复合氧化物与铝基复合氧化物配比使催化剂涂层的催化性能更好,得到的汽油机颗粒捕集催化剂综合性能更好。其中,优选的,步骤(1)中所述铝溶胶的用量为浆料总质量的1-5%;优选的铝溶胶用量使涂层的在催化剂载体上附着性更好,不易脱落,得到的汽油机颗粒捕集催化剂综合性能更好。其中,优选的,步骤(1)中所述的钯盐为硝酸钯;所述的铑盐为硝酸铑;优选的钯盐和铑盐在涂层浆料中分散更均匀,焙烧后,得到的涂层催化性能更好,得到的汽油机颗粒捕集催化剂综合性能更好。其中,步骤(1)中所述第一造孔剂为分子量400-4000的聚乙二醇;所述第二造孔剂为分子量6000-20000的聚乙二醇;通过对造孔剂分子量的限定,使进气端和出气端的催化剂涂层的孔径和孔容出现不同,从而使催化剂背压更低;同时,进气端催化剂涂层孔径和孔容更大,对碳烟的容纳量更大,进气端涂层与碳烟的接触面积更大,有利于高浓度贵金属降低碳烟的催化燃烧温度,进而使cgpf对碳烟的燃烧性能更好。其中,优选的,步骤(1)中所述第一造孔剂和第二造孔剂的用量分别占浆料总质量的0.1-10%;优选的造孔剂用量使催化剂涂层的孔隙率更优,有利于提高催化剂的催化性能,得到的汽油机颗粒捕集催化剂综合性能更好。其中,优选的,步骤(1)中所述浆料的粒度d50不大于5μm;最优选的,浆料的粒度d50为2-3μm;优选的浆料粒度涂覆性更好,焙烧后涂层性能稳定,孔径大小更均匀,得到的汽油机颗粒捕集催化剂综合性能更好。其中,优选的,步骤(1)中所述浆料的固含量为20-40wt%;优选的浆料固含量涂覆性更好,涂覆更均匀。其中,优选的,步骤(2)中第一涂层浆料的涂覆量为10-110g/l,第二涂层的涂覆量为10-70g/l;最优选的,第一涂层浆料的涂覆量为50-90g/l,第二涂层浆料的涂覆量为10-50g/l;优选的浆料涂覆量,涂覆更均匀,其中的贵金属密度更恰当,原材料成本更低,催化剂对碳烟的燃烧性能更好。其中,优选的,步骤(3)中干燥的温度为90-150℃,时间为3-10h;优选的干燥温度和时间,使催化剂涂层性能更稳定,得到的汽油机颗粒捕集催化剂综合性能更好。其中,优选的,步骤(3)中焙烧的温度为500-600℃,时间为1-4h;优选的焙烧温度和时间,使催化剂涂层性能更稳定,得到的汽油机颗粒捕集催化剂综合性能更好。与现有技术相比,本发明的有益效果:1、本发明汽油机颗粒捕集催化剂对催化剂涂层中的贵金属含量进行了调整,使催化剂上进气端的催化剂涂层中贵金属的负载量显著高于出气端,从而最大程度的利用了催化剂涂层中高负载量贵金属对碳烟的燃烧温度的降低作用,显著提高了cgpf对碳烟的燃烧能力。2、本发明汽油机颗粒捕集催化剂对催化剂涂层中微孔孔径的大小进行了调整,使进气端和出气端的催化剂涂层的孔径和孔容出现不同,能显著降低催化剂的背压。3、本发明汽油机颗粒捕集催化剂进气端催化剂涂层孔径和孔容更大,背压小,对碳烟的容纳量更大,进气端涂层与碳烟的接触面积更大,更有利于高浓度贵金属降低碳烟的催化燃烧温度,提高了cgpf对碳烟的燃烧性能。4、本发明制备方法能提高汽油机颗粒捕集催化剂对碳烟的燃烧能力和延长使用寿命,对控制汽车尾气中颗粒物的排放具有积极作用。5、本发明汽油机颗粒捕集催化剂的制备方法简单、可靠,适用于汽油机颗粒捕集催化剂的大规模生产。附图说明图1为本发明汽油机颗粒捕集催化剂结构示意图。标记说明:1-催化剂载体;2-第一涂层;3-第二涂层。具体实施方式下面结合试验例及具体实施方式对本发明作进一步的详细描述。但不应将此理解为本发明上述主题的范围仅限于以下的实施例,凡基于本
发明内容所实现的技术均属于本发明的范围。实验使用的催化剂载体均为壁流式gpf载体,具体参数如下:尺寸为φ132.1*127,目数和壁厚分别为300cpsi和8mil,孔隙率为65%,平均孔径为19μm,体积为1.74l。实施例1(1)制备浆料:将200g铈锆基复合氧化物(由30%ceo2、60%zro2、5%la2o3和5%pr6o11组成)和40g铝基复合氧化物(由4%la2o3和96%al2o3组成)混合,然后加入铝溶胶(占浆料质量分数的2%)和去离子水,球磨搅拌30min;加入聚乙二醇(分子量为1000,占浆料质量分数的1%)球磨搅拌5min,然后加入硝酸钯溶液(占催化剂涂层中总钯含量的15%),球磨搅拌10min;加入硝酸铑溶液(占催化剂涂层中总铑含量的50%),球磨搅拌,控制浆料粒度d50=2.3μm,浆料固含量为32wt%,制备得到第一涂层浆料;将200g铈锆基复合氧化物(由30%ceo2、60%zro2、5%la2o3和5%pr6o11组成)和40g铝基复合氧化物(由4%la2o3和96%al2o3组成)混合,然后加入铝溶胶(占浆料质量分数的2%)和去离子水,球磨搅拌30min;加入聚乙二醇(分子量为10000,占浆料质量分数的1%)球磨搅拌5min,然后加入硝酸钯溶液(占催化剂涂层中总钯含量的85%),球磨搅拌10min;加入硝酸铑溶液(占催化剂涂层中总铑含量的50%),球磨搅拌,控制浆料粒度d50=2.3μm,浆料固含量为32wt%,制备得到第二涂层浆料;(2)涂覆:将第一涂层浆料涂覆到催化剂载体的出气端(保证涂层中钯负载量为1.5g/ft3,铑负载量为3g/ft3);将第二涂层浆料涂覆到催化剂载体的进气端(保证涂层中钯负载量为15g/ft3,铑负载量为3g/ft3);(3)焙烧:将涂覆好的催化剂载体在150℃的温度下干燥3h,再在600℃的温度下焙烧1h,得到汽油机颗粒捕集催化剂。实施例2(1)制备浆料:将60g铈锆基复合氧化物(由50%ceo2、40%zro2和10%pr6o11组成)和180g铝基复合氧化物(由15%la2o3、15%y2o3和70%al2o3组成)混合,然后加入铝溶胶(占浆料质量分数的5%)和去离子水,球磨搅拌60min;加入聚乙二醇(分子量为4000,占浆料质量分数的5%)球磨搅拌1min,然后加入硝酸钯溶液(占催化剂涂层中总钯含量的25%),球磨搅拌30min;加入硝酸铑溶液(占催化剂涂层中总铑含量的10%),球磨搅拌,控制浆料粒度d50=3μm,浆料固含量为40wt%,制备得到第一涂层浆料;将60g铈锆基复合氧化物(由50%ceo2、40%zro2和10%pr6o11组成)和180g铝基复合氧化物(由15%la2o3、15%y2o3和70%al2o3组成)混合,然后加入铝溶胶(占浆料质量分数的5%)和去离子水,球磨搅拌60min;加入聚乙二醇(分子量为20000,占浆料质量分数的5%)球磨搅拌1min,然后加入硝酸钯溶液(占催化剂涂层中总钯含量的75%),球磨搅拌30min;加入硝酸铑溶液(占催化剂涂层中总铑含量的90%),球磨搅拌,控制浆料粒度d50=3μm,浆料固含量为40wt%,制备得到第二涂层浆料;(2)涂覆:将第一涂层浆料涂覆到催化剂载体的出气端(保证涂层中钯负载量为4g/ft3,铑负载量为1g/ft3);将第二涂层浆料涂覆到催化剂载体的进气端(保证涂层中钯负载量为16g/ft3,铑负载量为5g/ft3);(3)焙烧:将涂覆好的催化剂载体在120℃的温度下干燥5h,再在550℃的温度下焙烧2h,得到汽油机颗粒捕集催化剂。实施例3(1)制备浆料:将160g铈锆基复合氧化物(由70%ceo2、20%zro2、5%nd2o3和5%bao组成)和80g铝基复合氧化物(由5%zro2、10%pr6o11、10%nd2o3、5%sro、和70%al2o3组成)混合,然后加入铝溶胶(占浆料质量分数的1%)和去离子水,球磨搅拌10min;加入聚乙二醇(分子量为4000,占浆料质量分数的10%)球磨搅拌10min,然后加入硝酸钯溶液(占催化剂涂层中总钯含量的10%),球磨搅拌5min;加入硝酸铑溶液(占催化剂涂层中总铑含量的90%),球磨搅拌,控制浆料粒度d50=2μm,浆料固含量为20wt%,制备得到第一涂层浆料;将160g铈锆基复合氧化物(由70%ceo2、20%zro2、5%nd2o3和5%bao组成)和80g铝基复合氧化物(由5%zro2、10%pr6o11、10%nd2o3、5%sro、和70%al2o3组成)混合,然后加入铝溶胶(占浆料质量分数的1%)和去离子水,球磨搅拌10min;加入聚乙二醇(分子量为6000,占浆料质量分数的10%)球磨搅拌10min,然后加入硝酸钯溶液(占催化剂涂层中总钯含量的90%),球磨搅拌5min;加入硝酸铑溶液(占催化剂涂层中总铑含量的10%),球磨搅拌,控制浆料粒度d50=2μm,浆料固含量为20wt%,制备得到第二涂层浆料;(2)涂覆:将第一涂层浆料涂覆到催化剂载体的出气端(保证涂层中钯负载量为1.0g/ft3,铑负载量为5g/ft3);将第二涂层浆料涂覆到催化剂载体的进气端(保证涂层中钯负载量为20g/ft3,铑负载量为1.0g/ft3);(3)焙烧:将涂覆好的催化剂载体在90℃的温度下干燥10h,再在500℃的温度下焙烧4h,得到汽油机颗粒捕集催化剂。实施例4(1)制备浆料:将180g铈锆基复合氧化物(由40%ceo2、50%zro2和10%pr6o11组成)和60g铝基复合氧化物(由4%la2o3和96%al2o3组成)混合,然后加入铝溶胶(占浆料质量分数的2%)和去离子水,球磨搅拌40min;加入聚乙二醇(分子量为5000,占浆料质量分数的3%)球磨搅拌5min,然后加入硝酸钯溶液(占催化剂涂层中总钯含量的15%),球磨搅拌15min;加入硝酸铑溶液(占催化剂涂层中总铑含量的50%),球磨搅拌,控制浆料粒度d50=2.3μm,浆料固含量为30wt%,制备得到第一涂层浆料;将180g铈锆基复合氧化物(由40%ceo2、50%zro2和10%pr6o11组成)和60g铝基复合氧化物(由20%la2o3和80%al2o3组成)混合,然后加入铝溶胶(占浆料质量分数的2%)和去离子水,球磨搅拌30min;加入聚乙二醇(分子量为15000,占浆料质量分数的3%)球磨搅拌5min,然后加入硝酸钯溶液(占催化剂涂层中总钯含量的85%),球磨搅拌15min;加入硝酸铑溶液(占催化剂涂层中总铑含量的50%),球磨搅拌,控制浆料粒度d50=2.3μm,浆料固含量为30wt%,制备得到第二涂层浆料;(2)涂覆:将第一涂层浆料涂覆到催化剂载体的出气端(保证涂层中钯负载量为5g/ft3,铑负载量为3g/ft3);将第二涂层浆料涂覆到催化剂载体的进气端(保证涂层中钯负载量为25g/ft3,铑负载量为3g/ft3);(3)焙烧:将涂覆好的催化剂载体在130℃的温度下干燥5h,再在550℃的温度下焙烧3h,得到汽油机颗粒捕集催化剂。对比例1(1)制备浆料:将200g铈锆基复合氧化物(由30%ceo2、60%zro2、5%la2o3和5%pr6o11组成)和40g铝基复合氧化物(由4%la2o3和96%al2o3组成)混合,然后加入铝溶胶(占浆料质量分数的2%)和去离子水,球磨搅拌30min;加入聚乙二醇(分子量为1000,占浆料质量分数的1%)球磨搅拌5min,然后加入硝酸钯溶液(占催化剂涂层中总钯含量的15%),球磨搅拌10min;加入硝酸铑溶液(占催化剂涂层中总铑含量的50%),球磨搅拌,控制浆料粒度d50=2.3μm,浆料固含量为32wt%,制备得到第一涂层浆料;将200g铈锆基复合氧化物(由30%ceo2、60%zro2、5%la2o3和5%pr6o11组成)和40g铝基复合氧化物(由4%la2o3和96%al2o3组成)混合,然后加入铝溶胶(占浆料质量分数的2%)和去离子水,球磨搅拌30min;加入聚乙二醇(分子量为1000,占浆料质量分数的1%)球磨搅拌5min,然后加入硝酸钯溶液(占催化剂涂层中总钯含量的85%),球磨搅拌10min;加入硝酸铑溶液(占催化剂涂层中总铑含量的50%),球磨搅拌,控制浆料粒度d50=2.3μm,浆料固含量为32wt%,制备得到第二涂层浆料;(2)涂覆:将第一涂层浆料涂覆到催化剂载体的出气端(保证涂层中钯负载量为1.5g/ft3,铑负载量为3g/ft3);将第二涂层浆料涂覆到催化剂载体的进气端(保证涂层中钯负载量为15g/ft3,铑负载量为3g/ft3);(3)焙烧:将涂覆好的催化剂载体在90-150℃的温度下干燥3-10h,再在500-600℃的温度下焙烧1-4h,得到汽油机颗粒捕集催化剂。对比例2(1)制备浆料:将200g铈锆基复合氧化物(由30%ceo2、60%zro2、5%la2o3和5%pr6o11组成)和40g铝基复合氧化物(由4%la2o3和96%al2o3组成)混合,然后加入铝溶胶(占浆料质量分数的2%)和去离子水,球磨搅拌30min;加入聚乙二醇(分子量为10000,占浆料质量分数的1%)球磨搅拌5min,然后加入硝酸钯溶液(占催化剂涂层中总钯含量的15%),球磨搅拌10min;加入硝酸铑溶液(占催化剂涂层中总铑含量的50%),球磨搅拌,控制浆料粒度d50=2.3μm,浆料固含量为32wt%,制备得到第一涂层浆料;将200g铈锆基复合氧化物(由30%ceo2、60%zro2、5%la2o3和5%pr6o11组成)和40g铝基复合氧化物(由4%la2o3和96%al2o3组成)混合,然后加入铝溶胶(占浆料质量分数的2%)和去离子水,球磨搅拌30min;加入聚乙二醇(分子量为1000,占浆料质量分数的1%)球磨搅拌5min,然后加入硝酸钯溶液(占催化剂涂层中总钯含量的85%),球磨搅拌10min;加入硝酸铑溶液(占催化剂涂层中总铑含量的50%),球磨搅拌,控制浆料粒度d50=2.3μm,浆料固含量为32wt%,制备得到第二涂层浆料;(2)涂覆:将第一涂层浆料涂覆到催化剂载体的出气端(保证涂层中钯负载量为1.5g/ft3,铑负载量为3g/ft3);将第二涂层浆料涂覆到催化剂载体的进气端(保证涂层中钯负载量为15g/ft3,铑负载量为3g/ft3);(3)焙烧:将涂覆好的催化剂载体在90-150℃的温度下干燥3-10h,再在500-600℃的温度下焙烧1-4h,得到汽油机颗粒捕集催化剂。对比例3(1)制备浆料:将200g铈锆基复合氧化物(由30%ceo2、60%zro2、5%la2o3和5%pr6o11组成)和40g铝基复合氧化物(由4%la2o3和96%al2o3组成)混合,然后加入铝溶胶(占浆料质量分数的2%)和去离子水,球磨搅拌30min;加入聚乙二醇(分子量为1000,占浆料质量分数的1%)球磨搅拌5min,然后加入硝酸钯溶液(占催化剂涂层中总钯含量的50%),球磨搅拌10min;加入硝酸铑溶液(占催化剂涂层中总铑含量的50%),球磨搅拌,控制浆料粒度d50=2.3μm,浆料固含量为32wt%,制备得到第一涂层浆料;将200g铈锆基复合氧化物(由30%ceo2、60%zro2、5%la2o3和5%pr6o11组成)和40g铝基复合氧化物(由4%la2o3和96%al2o3组成)混合,然后加入铝溶胶(占浆料质量分数的2%)和去离子水,球磨搅拌30min;加入聚乙二醇(分子量为10000,占浆料质量分数的1%)球磨搅拌5min,然后加入硝酸钯溶液(占催化剂涂层中总钯含量的50%),球磨搅拌10min;加入硝酸铑溶液(占催化剂涂层中总铑含量的50%),球磨搅拌,控制浆料粒度d50=2.3μm,浆料固含量为32wt%,制备得到第二涂层浆料;(2)涂覆:将第一涂层浆料涂覆到催化剂载体的出气端(保证涂层中钯负载量为5g/ft3,铑负载量为3g/ft3);将第二涂层浆料涂覆到催化剂载体的进气端(保证涂层中钯负载量为5g/ft3,铑负载量为3g/ft3);(3)焙烧:将涂覆好的催化剂载体在90-150℃的温度下干燥3-10h,再在500-600℃的温度下焙烧1-4h,得到汽油机颗粒捕集催化剂。对比例4(1)制备浆料:将200g铈锆基复合氧化物(由30%ceo2、60%zro2、5%la2o3和5%pr6o11组成)和40g铝基复合氧化物(由4%la2o3和96%al2o3组成)混合,然后加入铝溶胶(占浆料质量分数的2%)和去离子水,球磨搅拌30min;加入聚乙二醇(分子量为1000,占浆料质量分数的1%)球磨搅拌5min,然后加入硝酸钯溶液(占催化剂涂层中总钯含量的85%),球磨搅拌10min;加入硝酸铑溶液(占催化剂涂层中总铑含量的50%),球磨搅拌,控制浆料粒度d50=2.3μm,浆料固含量为32wt%,制备得到第一涂层浆料;将200g铈锆基复合氧化物(由30%ceo2、60%zro2、5%la2o3和5%pr6o11组成)和40g铝基复合氧化物(由4%la2o3和96%al2o3组成)混合,然后加入铝溶胶(占浆料质量分数的2%)和去离子水,球磨搅拌30min;加入聚乙二醇(分子量为10000,占浆料质量分数的1%)球磨搅拌5min,然后加入硝酸钯溶液(占催化剂涂层中总钯含量的15%),球磨搅拌10min;加入硝酸铑溶液(占催化剂涂层中总铑含量的50%),球磨搅拌,控制浆料粒度d50=2.3μm,浆料固含量为32wt%,制备得到第二涂层浆料;(2)涂覆:将第一涂层浆料涂覆到催化剂载体的出气端(保证涂层中钯负载量为15g/ft3,铑负载量为3g/ft3);将第二涂层浆料涂覆到催化剂载体的进气端(保证涂层中钯负载量为1.5g/ft3,铑负载量为3g/ft3);(3)焙烧:将涂覆好的催化剂载体在90-150℃的温度下干燥3-10h,再在500-600℃的温度下焙烧1-4h,得到汽油机颗粒捕集催化剂。对比例5(1)制备浆料:将200g铈锆基复合氧化物(由30%ceo2、60%zro2、5%la2o3和5%pr6o11组成)和40g铝基复合氧化物(由4%la2o3和96%al2o3组成)混合,然后加入铝溶胶(占浆料质量分数的2%)和去离子水,球磨搅拌30min;加入聚乙二醇(分子量为1000,占浆料质量分数的1%)球磨搅拌5min,然后加入硝酸钯溶液(占催化剂涂层中总钯含量的60%),球磨搅拌10min;加入硝酸铑溶液(占催化剂涂层中总铑含量的50%),球磨搅拌,控制浆料粒度d50=2.3μm,浆料固含量为32wt%,制备得到第一涂层浆料;将200g铈锆基复合氧化物(由30%ceo2、60%zro2、5%la2o3和5%pr6o11组成)和40g铝基复合氧化物(由4%la2o3和96%al2o3组成)混合,然后加入铝溶胶(占浆料质量分数的2%)和去离子水,球磨搅拌30min;加入聚乙二醇(分子量为10000,占浆料质量分数的1%)球磨搅拌5min,然后加入硝酸钯溶液(占催化剂涂层中总钯含量的40%),球磨搅拌10min;加入硝酸铑溶液(占催化剂涂层中总铑含量的50%),球磨搅拌,控制浆料粒度d50=2.3μm,浆料固含量为32wt%,制备得到第二涂层浆料;(2)涂覆:将第一涂层浆料涂覆到催化剂载体的出气端(保证涂层中钯负载量为5g/ft3,铑负载量为3g/ft3);将第二涂层浆料涂覆到催化剂载体的进气端(保证涂层中钯负载量为10g/ft3,铑负载量为3g/ft3);(3)焙烧:将涂覆好的催化剂载体在90-150℃的温度下干燥3-10h,再在500-600℃的温度下焙烧1-4h,得到汽油机颗粒捕集催化剂。实验例:背压测试:将实施例1-4和对比例1-5的制备的催化剂安装于冷流背压试验台上按gb18881-2017附录a进行背压测试,测试温度为室温,压缩气体流量为650kg/h,测试结果如下:组号背压(kpa)实施例19.57实施例28.34实施例310.12实施例411.43对比例115.12对比例221.34对比例310.26对比例49.83对比例59.71从上述背压测试数据可知,实施例1-4中采用本发明方法制备的催化剂,催化剂进气端涂层的微孔孔径大于出气端涂层孔径,能显著降低催化剂的背压;而对比例1中,催化剂涂层中的微孔孔径相同,催化剂的背压高,显著高于实施例1-4;对比例2中,催化剂进气端涂层的微孔孔径小于出气端涂层孔径,导致催化剂的背压反而增加,不仅高于实施例1-4,还高于对比例1。碳烟加载和碳烟燃烧试验:将实施例1-4和对比例1-5的制备得到的催化剂安装于1.8ltgdi发动机上按设计的工况进行碳烟加载,碳烟加载量为2.0g/l。控制发动机排温600℃,发动机转速从2500rpm直接进入到怠速工况,模拟断油工况,监控催化剂碳烟燃烧时的床层位置温度,温度越高表明催化剂燃烧碳烟速率越快,不同催化剂碳烟燃烧时的床层最高温度数据记载如下:组号最高温度(℃)实施例1708实施例2712实施例3715实施例4704对比例1691对比例2687对比例3675对比例4667对比例5683从上述碳烟燃烧时催化剂温度的结果可知,实施例1-4采用本发明方法制备得到的催化剂,进气口涂层贵金属含量高于出气口涂层,使催化剂展现出了更快的碳烟燃烧速率,故燃烧放热使得催化剂床温比对比例3(涂层贵金属含量相同)高30℃左右;而对比文件1中,涂层的微孔孔径相同,背压高,高浓度贵金属降低碳烟的催化燃烧温度的效果降低,对燃烧碳烟速率增加效果降低,导致催化剂床层温度降低;对比例2中,进气口涂层微孔孔径小于出气口,背压高,高浓度贵金属降低碳烟的催化燃烧温度的效果降低,对燃烧碳烟速率增加效果降低,导致催化剂床层温度降低;对比例3中,催化剂涂层中贵金属的负载量相同,不能降低碳烟的催化燃烧温度,燃烧碳烟速率较慢,催化剂床层温度显著降低;对比例4中,进气口催化剂涂层中贵金属的负载量显著低于出气口,提高了碳烟的催化燃烧温度,燃烧碳烟速率显然降低,催化剂床层温度显著降低;对比例5中,进气口涂层中贵金属的负载量与出气口的比值未达到本发明规定的范围,贵金属降低碳烟的催化燃烧温度的效果较差,对燃烧碳烟速率增加效果差,催化剂床层温度降低。当前第1页12