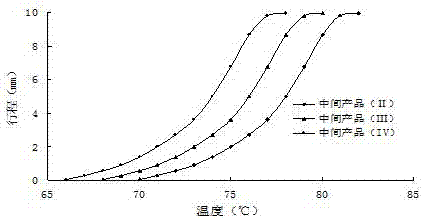
本发明属于特种蜡生产技术领域,特别是涉及一种节温器用介质的制备方法。
背景技术:蜡质温控阀以蜡类物质作为感应温度变化的介质,当环境温度变化时,蜡类物质的体积产生变化,进而控制阀门开度,从而调节物流流量,达到调整、控制温度的目的。蜡质温控阀所用蜡类物质称作温敏介质。蜡质温控阀的研制始于二十世纪初,其目的是代替内燃机冷却系统所用的波纹管元件进行控温。蜡质温控阀是集感应、放大、执行、反馈、定值等功能于一体的自力式温度和流量的自动控制装置,具有温度特性不随系统压力而明显变化、机械强度高、化学稳定性好、容易批量生产以及易于安装、成本低、温控稳定可靠等优点,因而得到广泛应用。节温器又称调温器,其作用是根据冷却水温度的高低自动调节进入散热器的水量,改变水的循环范围,以调节冷却系统的散热能力,保证发动机在合适的温度范围内工作。常用的节温器是蜡式节温器,属蜡质温控阀。蜡式节温器一般采用套管式结构,控温范围10~12℃,根据发动机的最佳工作温度区域,又按标称温度分成70、72、76、80、82等规格。对节温器行程要求为:常温~标称温度+2℃的行程小于1mm,控温范围内(标称温度~标称温度+10℃或标称温度+12℃)行程大于8mm。如标称温度为72℃的节温器的控温区间为72℃~82℃,要求74℃时行程小于1mm,72℃~82℃行程大于8mm。蜡式节温器是依靠其所用的蜡类温敏介质随温度变化产生体积变化作为输出动作的原动力。当冷却水温度低于规定值时,节温器感温体内的蜡类温敏介质呈固态,节温器阀在弹簧的作用下关闭发动机与散热器之间的通道,冷却水经水泵返回发动机,进行发动机内小循环;当冷却水温度达到规定值后,蜡类温敏介质产生固→液相变,体积膨胀,并压迫橡胶管使其收缩。在橡胶管收缩的同时对推杆作用以向上的推力,推杆对阀门有向下的反推力使阀门开启。这时冷却水经由散热器和节温器阀,再经水泵流回发动机,进行大循环。这样蜡式节温器就能根据冷却水温度的变化自动调节进入散热器的水量,从而保证发动机在合适的温度范围内工作。为保证发动机在合适的温度范围内工作,需要蜡式节温器对冷却水温度的变化做出快速的反应以及时调节冷却水的流量,这要求蜡式节温器所用的温敏介质有较高的导热性,但石油蜡的导热系数很低,只有约6×10-4J·(m·℃·h)-1。为提高蜡类温敏介质的导热性,通常加入导热剂,常用的导热剂是金属粉末;但是由于金属粉末的密度远大于蜡类温敏介质,在蜡类温敏介质处于液态时金属粉末在重力作用下产生沉降,使用一段时间后导热性能产生变化,导致蜡式节温器推杆行程—温度关系产生变化,影响发动机的正常工作。为解决导热剂的沉降问题,还要加入其它添加剂。为使发动机能够长时间正常工作,应该保持发动机运行过程的平稳,这就要求蜡式节温器在控温范围内推杆的行程最好是均匀线性的,即节温器阀的开度随冷却水温度的变化进行均匀调节,这有利于发动机的平稳工作。同时,蜡式节温器制备过程的技术要求很高,一般需要后续的精细调整过程。为了便于后期调整,通常期望在标称温度-2℃~标称温度+2℃范围内有比较小的行程;同时为使发动机能够平稳工作,在标称温度+2℃~标称温度+10℃(或+12℃)的范围内推杆的行程最好是均匀线性的。以标称温度为70℃的节温器为例,推杆理想的行程应该是:在常温~68℃范围内行程为0,68℃~72℃范围内行程较小(小于1mm),在72℃~80℃范围内行程均匀线性,且70℃~80℃范围内行程要大于8mm。这种要求如摘要附图中的理想性能曲线所示。从蜡式节温器的工作原理可以看出,蜡类温敏介质是其接收环境温度变化进而输出相应动作的主体,所以蜡类温敏介质的性质是蜡式节温器性能的决定因素。一般蜡类温敏介质处于液体状态时,其膨胀系数约为6.7×10-4,固态时的膨胀系数比液态时稍大,而在固←→液相变范围内膨胀系数远大于此值。对节温器用蜡类温敏介质的要求就是相变过程的体积膨胀应与节温器的控温范围一致,反映在推杆行程上就是要在节温器的控温范围内大于8mm,而在控温范围以外行程要很小。石油蜡是原油经过炼制加工后从含蜡馏分油中制得的各类蜡产品的总称,包括液体石蜡、石蜡和微晶蜡。液体石蜡常温下为液态,通常石蜡的熔点为52℃~74℃,微晶蜡的滴熔点为65℃~92℃。商品石油蜡是多种碳数的正构烷烃、异构烷烃、环烷烃等的烃类混合物,其碳数分布较宽,正构烷烃含量较低。商品石油蜡直接用作节温器的温敏介质时,会导致大循环开启过早(常温~标称温度+2℃范围内推杆的行程大于1mm),使发动机预热时间延长;同时由于在节温器的控温范围内推杆行程较小(标称温度~标称温度+10℃或标称温度+12℃的范围内行程小于8mm),会导致发动机正常工作时大循环的水量不足,会引起发动机过热。所以商品石油蜡必须经分离提纯以缩小碳数分布范围并提高正构烷烃含量,才能用作节温器的蜡类温敏介质。由于石油蜡必须经严格地分离提纯才能用作节温器的蜡类温敏介质,导致其膨胀在很窄的范围内变化很大,这类似纯净物的熔化过程。对于节温器,其控温范围只有10~12℃,要作到行程的均匀线性是十分困难的。在石油蜡生产工艺方面常用的石油蜡分离加工手段主要有蒸馏、发汗脱油、溶剂脱油等。蒸馏是利用不同分子量烃类的沸点不同达到分离提纯的目的,减小蒸馏的沸程可以有效降低产物碳分布的宽度,但对提高正构烷烃含量影响不大,同时由于蒸馏过程需要将石油蜡加热到沸点以上,消耗大量的能量。溶剂脱油方法是利用正构烷烃与异构烷烃在溶剂中的溶解度不同达到分离提纯的目的,可以有效提高产物中的正构烷烃含量,但对碳分布宽窄的影响不大,同时溶剂脱油生产设备投资大;生产过程中需要大量使用溶剂,回收溶剂需要消耗大量的能量;溶剂中含有苯系物,会对环境造成影响;溶剂易燃,容易造成生产事故。发汗脱油方法是利用蜡中各种烃类组分熔点不同的性质进行分离提纯的。石油蜡中各种组分的分子量和结构的不同都会使其熔点不同。同为正构烷烃时,分子量较大的正构烷烃的熔点较高,而分子量较小的正构烷烃的熔点较低;分子量相同时,异构烷烃和环烷烃的熔点要低于正构烷烃,且异构程度越高熔点就越低。所以发汗脱油即能降低产物碳分布的宽度又能提高正构烷烃含量。与蒸馏分离方法相比,由于各种烃类的熔点温度远低于沸点温度,所以发汗分离过程的能耗远低于蒸馏分离;与溶剂分离方法相比,发汗分离过程不使用溶剂,所以发汗分离过程对环境无影响。而且发汗法即能降低产物碳分布的宽度又能提高正构烷烃含量,所以对制备节温器用蜡类温敏介质而言,发汗脱油分离过程在生产过程和产品性能两方面都有优势。普通的发汗分离过程主要包括以下步骤:(1)准备工作:垫水,用水充满发汗装置皿板下部空间;(2)装料:原料加热至熔点以上呈液态时装入发汗装置;(3)降温结晶:将原料以不大于4℃/h的降温速率缓慢冷却到其熔点以下10~20℃。在冷却过程中,熔点最高的组分先以粗的纤维状晶体形态结晶出来,随着蜡层温度继续降低,其它组分按熔点由高到低的顺序依次结晶形成固体;(4)升温发汗:当蜡层温度达到预设的降温终止温度之后,放掉垫水;再将原料缓慢地加热到预设的发汗终止温度。在升温发汗过程中,随着蜡层温度缓慢升高,熔点较低的环烷烃、异构烷烃和分子量较低的正构烷烃按熔点由低到高的顺序先后熔化成液态并流出(蜡下),最后得到的发汗装置内的剩余物(蜡上)就是熔点高、碳分布窄、正构烷烃含量高的蜡;(5)粗产品收集:升温发汗过程结束后继续升高温度,以熔化取出蜡上,即为粗产品;(6)产品精制、成型、包装:精制过程通常采用白土精制:将粗产品熔化后升温至预定温度,加入白土并恒温搅拌至预定时间后过滤;再经成型、包装即为目的产品。普通发汗脱油工艺可以生产熔点在40℃~60℃的皂蜡和低熔点石蜡,不适宜生产熔点在70℃左右的节温器用蜡类温敏介质。有试验表明,普通发汗脱油工艺生产熔点在70℃左右的节温器用蜡类温敏介质产品时,发汗后期蜡上的碳分布宽度和正构烷烃含量与收率无关,即蜡上的碳分布宽度不随收率的下降而下降,正构烷烃含量也不随收率的下降而提高,所以普通发汗分离工艺不适宜制备熔点在70℃左右的节温器用蜡类温敏介质。多年来,发汗脱油工艺在生产设备和工艺方面得到了一些发展,如CN89214332(立式方形多段隔板发汗罐)、CN98233254.8(石蜡发汗罐)、CN201320127680.4(管式石蜡脱油装置)等,在发汗脱油生产设备上作了改进;CN91206202(一种高效石蜡发汗罐)在发汗脱油工艺上作了改进。但这些改进仍不能生产熔点在70℃左右的节温器用蜡类温敏介质。现有技术中的蜡类温敏介质制备手段,有采用溶剂法的,如:DD241,829、DD241,830等专利介绍以溶剂萃取的方法制备80~90℃范围内控温的蜡类温敏介质。DD247,572、SU1,084,289、RU2,009,171、US5,223,122等专利介绍的制备方式,均以溶剂萃取为主。这些专利介绍的溶剂法制备方式对环境有污染。现有技术中的蜡类温敏介质制备手段,也有采用(多段)发汗或(与蒸馏方法)组合发汗的,如:CN02109670.8(淋浴自动调温阀用蜡质感温介质)、CN02109668.6(采暖控温阀用蜡介质及其制备方法)、CN200310104909.3(一种蜡质控温阀用温敏介质及其制备方法)等,这些专利的目的产品的熔点都在50℃以下;CN201110353409.8(一种控温阀用蜡质感温介质的制备方法)、CN201110353410.0(一种摩托车自动加浓阀用热感应蜡介质的制备方法)、CN02109670.8(淋浴自动调温阀用蜡质感温介质)等,这些专利的目的产品熔点也在50℃以下,且控温范围宽,不适合用作节温器用蜡类温敏介质。为解决蜡质温控阀使用过程中因导热剂沉降导致导热性变差的问题,专利CN02125845.7(一种低熔点热敏蜡)采用加入0.5~30(wt)%的增粘剂的方法进行改进,所选的增粘剂为石蜡、聚异丁烯、松香、氢化松香、聚乙烯、聚丙烯中的一种或一种以上。该专利选用的增粘剂都是与基础材料相溶性非常好的有机物,为起到防止金属粉末的沉降需要加入大量的增粘剂,这会导致体系粘度很大,影响后续的加工过程。发汗工艺具有投资少、生产过程简单、操作费用低、处理量适中、产品质量指标易于调整等优点,更重要的是,发汗脱油工艺能耗低,又是目前已知用于工业规模生产石蜡产品的唯一无溶剂脱油方法,在提倡绿色低碳、环保节能的今天,采用发汗脱油工艺生产节温器用蜡类温敏介质的需求更加迫切;同时采用适当的手段解决节温器推杆行程不线性的现象及采用不影响后续的加工过程的方法有效解决导热剂沉降的现象,也是本领域急需解决的问题。
技术实现要素:针对现有技术的不足,本发明提供一种节温器用介质的制备方法,具体地说包括蜡介质中间产品的制备、行程均匀线性蜡介质的制备和节温器用介质的制备三部分。其中蜡介质中间产品的制备是采用发汗装置,在普通发汗方法的基础上,在冷却降温过程中的适当温度增加高温恒温阶段,并增加在冷却过程结束后的低温恒温阶段和升温发汗过程的恒温阶段;在冷却过程结束后在蜡层表面均匀铺满混合的金属颗粒,并在升温发汗过程中强制气流通过蜡层,携带出处于液态的组分(油和较低熔点的蜡),从而加快了固态组分(较高熔点的蜡)与液态组分的分离速度,并增强了固态组分与液态组分的分离效果,使发汗脱油这种无溶剂脱油方法可以生产出系列的节温器用蜡介质的中间产品;行程均匀线性蜡介质的制备是将这些中间产品进行调配制得;节温器用介质的制备是将行程均匀线性蜡介质与导热剂和不影响后续加工的稳定剂调配制得。本发明方法具有装置投资低、生产过程简单、操作费用低、无溶剂污染,而且以该介质生产的节温器推杆的行程均匀线性且导热性能稳定等优点。本发明一种节温器用介质的制备方法包括:蜡介质中间产品的制备:以商品石蜡为原料,加热熔化后装入发汗装置,以1.0℃~3.0℃/h的速率冷却降温至适当温度后,高温恒温一段时间;再以0.5℃~2.5℃/h的速率冷却降温至原料熔点以下5℃~20℃,并低温恒温一段时间;以0.5℃~2.5℃/h的速率升温发汗,并恒温一段时间;升温发汗过程中强制气流通过蜡层;蜡层达到预定温度并恒温一段时间后停止发汗过程。蜡上经精制后即为蜡介质中间产品;行程均匀线性蜡介质的制备:再将系列的中间产品进行调配就可得到行程均匀线性蜡介质;节温器用介质的制备:行程均匀线性蜡介质再与导热剂和稳定剂混合均匀,成型、包装后即可得到行程均匀线性且导热性能稳定的蜡式节温器用介质产品。本发明的一种节温器用介质的制备方法,具体包括以下内容:(1)在发汗装置中垫水;(2)以商品石蜡为原料,加热熔化后装入发汗装置;(3)以1.0℃/h~3.0℃/h的速率将蜡层降温至适当温度,高温恒温一段时间;再以0.5℃/h~2.5℃/h的速率降温至原料熔点以下5℃~20℃的降温终止温度,并低温恒温一段时间;(4)排出发汗装置中的垫水;然后以0.5℃/h~2.5℃/h的速率升温,蜡层达到预定温度后恒温一段时间,然后停止发汗;其中在升温过程中强制气流通过蜡层;(5)收集蜡上;(6)蜡上经精制、成型后即得到蜡介质中间产品;(7)改变原料,重复上述步骤(1)至(6),即可得到标称温度相近的系列的节温器用蜡介质的中间产品;这些中间产品可以满足节温器的一般要求,即:常温~标称温度+2℃的行程小于1mm,控温范围内(标称温度~标称温度+10℃或标称温度+12℃)行程大于8mm;再将系列的中间产品进行调配即得到行程均匀线性蜡介质;(8)行程均匀线性蜡介质再与导热剂和稳定剂混合均匀,成型、包装后即可得到节温器用介质产品。本发明的节温器用介质的制备方法中,所述商品石蜡的熔点一般为节温器用蜡类温敏介质的标称温度±10℃,优选为标称温度±5℃。本发明的节温器用介质的制备方法中,优选在步骤(3)原料降温结晶以后、而在步骤(4)升温发汗过程前(此时蜡层处于固体状态),在蜡层的表面均匀铺满10~100目,优选20~50目的固体颗粒。固体颗粒的密度一般大于4g/cm3,可以是非金属、金属及合金等材质,优选密度为6~12g/cm3的金属及合金颗粒,如锌、铁、铜、铅及其合金等化学性质较稳定的低价格金属材质。可以选择两种或两种以上的不同密度的固体颗粒,密度相邻的两种固体颗粒材质的密度差为1~5g/cm3。各种固体颗粒可按重量份数相近的比例混合。此处所述的密度是指构成固体颗粒的材质的密度,如金属颗粒的密度是指金属的密度,而非颗粒的堆密度。发汗过程结束后可以回收固体颗粒并清洗以重复使用。本发明的节温器用介质的制备方法中,所述的发汗装置一般为发汗皿,并在蜡层以上增加可拆卸的密封系统及加压装置和/或在蜡层以下增加真空装置。所述的强制气流通过蜡层采用在蜡层上方施加压力(气压)和/或在蜡层下方降低压力(气压),使蜡层上下形成压力差实现。所述的压力差一般为0.1~5.0个大气压,优选为0.2~2.0个大气压,用以强制气流通过蜡层。本发明的节温器用介质的制备方法中,所述的降温过程,在高温恒温阶段之前的降温速率优选1.5℃/h~2.5℃/h。本发明的节温器用介质的制备方法中,所述的降温过程的高温恒温段的适当温度是原料石蜡熔点-1.0℃~熔点+2.0℃,优选为原料石蜡熔点~熔点+1.0℃;冷却降温过程的高温恒温段的时间为0~4.0小时,优选为1.0~4.0小时。本发明的节温器用介质的制备方法中,所述的降温过程,在高温恒温段之后的降温速率优选1.0℃/h~2.0℃/h。本发明的节温器用介质的制备方法中,所述的降温终止温度优选为原料石蜡熔点以下8℃~15℃。本发明的节温器用介质的制备方法中,所述的冷却降温至预设温度后,增加恒温阶段以使固体结晶更充分,冷却降温过程的低温恒温阶段的时间为0~3.0小时,优选为1.0~3.0小时。本发明的节温器用介质的制备方法中,所述的升温发汗过程的升温速率优选1.0℃/h~2.0℃/h。本发明的节温器用介质的制备方法中,步骤(4)中所述原料蜡层升温的预定温度为节温器用蜡类温敏介质的标称温度±10℃,优选为标称温度±5℃。本发明的节温器用介质的制备方法中,所述的升温发汗至制取(中间)产品的预设温度后,增加恒温阶段以使固态组分与液态组分分离更充分,恒温阶段的时间为0~5.0小时,优选为1.0~5.0小时。本发明的方法中,所述蜡层的升温速率和降温速率,可以通过空气浴、水浴、油浴或者其他可行的方式进行控制,优选采用水浴或油浴进行控制。采用水浴或油浴等方式控制升温速率和降温速率时,可在发汗皿外增加夹套,夹套与可移动盘管及循环系统相连,循环系统具有程序降温/加热功能,循环系统加入水或油等物质作为循环介质;装料后将盘管浸没在蜡层中,可使蜡层升/降温过程更快、蜡层温度更均匀。本发明的节温器用介质的制备方法中,所述的强制气流通过蜡层可以在升温发汗过程任意阶段实施,优选在升温发汗初期实施。本发明的节温器用介质的制备方法中,所述的强制气流通过蜡层是采用在蜡层上方增加气压实现的,如在蜡层上方施加的压力(气压)为0.2~1.5个大气压(表压),而蜡层下方保持为常压。本发明的节温器用介质的制备方法中,所述的强制气流通过蜡层是采用在蜡层下方降低气压实现的,如在蜡层上方保持为常压,而在蜡层下方的压力(气压)维持为-0.2~-0.8个大气压(表压)。本发明的节温器用介质的制备方法中,所述的中间产品的调配是利用2~5种中间产品进行的,这些中间产品的标称温度应在目的产品的标称温度±6℃的范围内选择;优选3种中间产品进行调配,优选的3种中间产品的标称温度分别为目的产品标称温度-2℃、目的产品标称温度、目的产品标称温度+2℃;优选的3种中间产品的调配比例为5%~25%:45%~85%:10%~30%(重量)。本发明的节温器用介质的制备方法中,所述的稳定剂为无机类的微粉、超微粉、表面改性的微粉以及其混合物。所述的微粉选自碳酸钙、炭黑、石墨、膨胀石墨、碳纤维、矿粉、三氧化二锑、硫酸钙、硫酸钡、二氧化钛、碳化硅、二氧化硅、氧化锌和氧化铝微粉构成的一组物质;所述的超微粉选自超微细碳酸钙、气相二氧化硅、纳米氧化锌、单壁碳纳米管、多壁碳纳米管;所述的表面改性的微粉为有机化蒙脱土、表面处理的超微细碳酸钙等。所述稳定剂的平均粒径为200目以上,优选的平均粒径为1000目~3000目。本发明的节温器用介质的制备方法中,所述的导热剂为金属粉末及其混合物。导热剂优选超细的金属粉,如超细的铝粉、铜粉、锌粉、铁粉等等。所述的导热剂的平均粒径为200目~2000目,优选的平均粒径为500目~1000目。本发明的节温器用介质的制备方法中,所得到的节温器用介质的组成为(以重量计):蜡类温敏介质5%~60%、导热剂10%~90%、稳定剂5%~30%。优选的比例为蜡类温敏介质15%~30%、导热剂50%~80%、稳定剂8%~15%。商品石油蜡直接用作节温器的蜡介质时,易于引起大循环开启过早和大循环的水量不足等情况。这是由商品石油蜡的化学组成引起的,即商品石油蜡的碳数分布较宽且含有较多的异构烷烃和环烷烃。由于商品石油蜡碳数分布较宽,即含有较多的低分子量的成分,低分子量成分的熔点低于节温器的控温范围,这些成分会提前熔化而产生体积膨胀,导致大循环开启过早;同时由于商品石油蜡含有较多的异构烷烃和环烷烃(一般异构烷烃和环烷烃的膨胀系数小于正构烷烃),这就会使在节温器控温范围内推杆的行程较小,导致发动机正常工作时大循环的水量不足。所以商品石油蜡必须经分离提纯以缩小碳数分布范围并提高正构烷烃含量,才能用作节温器的蜡类温敏介质。普通发汗脱油方法是利用蜡和油熔点不同的性质进行分离生产石油蜡产品的,但是对于熔点在70℃左右的石油蜡产品,由于原料中环烷烃和异构烷烃等物质增多,化学组成复杂,导致结晶时晶体结构更加细小致密,对液态组分的排出形成巨大的滤流阻力,这就造成仅靠重力自然分离的普通发汗过程中固态组分与液态组分难以完全分离。因此普通发汗脱油工艺不能生产符合标称温度在70℃左右的节温器标准的蜡类温敏介质产品。本发明为了使发汗脱油这种无溶剂生产石油蜡的方法可以制备节温器用蜡介质,通过对节温器用蜡介质使用性能与其化学组成的关系和普通发汗过程的深入研究,针对普通石油蜡产品化学组成中碳数分布较宽且正构烷烃含量较低是造成普通石油蜡产品不能满足节温器用蜡介质产品技术要求的原因,通过采用发汗法降低碳数分布宽度同时提高正构烷烃含量;针对普通发汗过程中固态组分与液态组分难以分离原因,通过在升温发汗过程中采用气流通过蜡层强制携带出液态组分的方法,同时还优选在冷却降温过程中增加高温恒温阶段,并在冷却降温过程结束后(即升温发汗过程前)在蜡层表面均匀铺满固体颗粒(优选金属颗粒)的方法进行改进;同时增加冷却降温过程的低温恒温阶段和升温发汗至预设温度后的恒温阶段等过程,这些措施有效地降低了产物碳分布的宽度并提高正构烷烃含量,使中间产物的性能能够满足节温器用蜡介质的一般技术要求。中间产物再经进一步调配,即可得到行程均匀线性的节温器用蜡介质产品。行程均匀线性的节温器用蜡介质再与导热剂和稳定剂混合均匀,成型、包装后即可得到行程均匀线性且导热性能稳定的节温器用介质产品。针对石油蜡发汗过程的研究表明,发汗过程中,液态组分是顺着结晶部分逐渐排出的,类似于液体在毛细管中流动的情况。由于熔点在70℃左右的石油蜡细小致密的结晶结构,会使对液态组分形成的滤流阻力急剧增大,这就造成仅靠重力自然分离的普通发汗过程中固态组分与液态组分难以完全分离,导致普通发汗方法不能生产标称温度在70℃左右的节温器用蜡类温敏介质产品。在发汗脱油的冷却降温过程中增加高温恒温阶段可以使石油蜡的结晶更大,利于升温发汗过程中液态组分的排出。针对石油蜡结晶过程的研究表明,其化学组成是决定结晶形态的最主要原因,同时冷却过程的条件也会影响结晶形态,尤其是在熔点附近的温度下的冷却条件对结晶形态的影响最明显。熔点在70℃左右的石油蜡在冷却到熔点附近时,较大分子量的正构烷烃已形成结晶析出,这部分结晶体可以作为后续形成结晶的晶核,此时增加高温恒温阶段,可以使晶核能够充分增长,形成更大尺寸的晶体,这种更大尺寸的晶体虽然不如低熔点石蜡的结晶那样粗大,但这种增大的晶体结构对发汗阶段排出液态组分也是十分有利的。在冷却降温过程结束后在蜡层表面均匀铺满固体颗粒同时在升温发汗过程中强制气流通过蜡层也有利于升温发汗过程中液态组分的排出。在冷却降温过程结束后(即升温发汗过程前),此时蜡层处于固体状态,在蜡层表面均匀铺满固体颗粒,在升温发汗过程中,随着蜡层温度升高,蜡层变软,固体颗粒由于密度较大,在重力作用下将以较慢的速度沉降,在蜡层内形成上下贯穿的细小通道,降低了滤流阻力,有利于液态组分的快速排出。不同密度和粒径的固体颗粒的沉降速度不同,采用混合的固体颗粒可以保证在发汗脱油的全过程中在蜡层的不同高度都有较多的排出液态组分的通道。同时强制气流通过蜡层,携带出液态组分,从而增强了固态组分与液态组分的分离效果。再辅以冷却过程的低温恒温阶段使固体结晶更充分,以及发汗过程的恒温阶段使固态组分与液态组分分离更充分等方法,使发汗脱油工艺可以生产碳数分布范围窄且正构烷烃含量高的节温器用蜡介质的中间产品,再将系列的中间产品进行调配就可得到行程均匀线性的节温器用蜡类温敏介质产品。同时,针对固体颗粒在液体中沉降过程的研究表明,固体颗粒的沉降速度与颗粒粒径、颗粒密度和液体密度、液体粘度等因素有关,固体颗粒粒径越大、固体颗粒密度和液体密度之差越大,沉降速度越快;而液体粘度越大,沉降速度越慢。由于导热剂通常为金属材质,这些金属颗粒的密度远大于液态蜡类温敏介质的密度(约为0.8×103Kg/m3),因此采用选择密度较低的金属材质(如铝)或粒径较小的金属颗粒等办法,不仅会导致成本增加,而且更重要的是这些手段只能减缓导热剂颗粒的沉降速度,而不能杜绝导热剂颗粒沉降的现象,所以增加液态蜡介质的粘度就是唯一可行的方式。加入与蜡介质相溶性非常好的有机物作为增粘剂,只有在液态下体系粘度非常大的情况下才能有效防止导热剂颗粒的沉降,但是这会使得蜡介质与增粘剂的均匀混合及蜡介质与导热剂的均匀混合带来很大的困难。本发明方法中,特别选择加入无机微粉用于取代增粘剂作为稳定剂。本发明中加入的无机微粉有非常大的比表面积,加入适量的无机微粉就可以吸附液态的蜡介质,使蜡类温敏介质在液态下呈膏体状态,失去流动性,因此可以有效防止导热剂颗粒的沉降;同时膏体状态的蜡介质几乎没有强度,不会影响蜡介质与导热剂的均匀混合。与现有技术相比较,本发明的优点是:通过在升温发汗过程中混合固体颗粒沉降,形成的上下贯穿蜡层的细小通道,利于液态组分的快速排出;并采用强制气流通过蜡层携带出液态组分的方法,加快了固态组分与液态组分的分离速度,并增强了固态组分与液态组分的分离效果。从而使发汗脱油工艺可以生产碳数分布范围较窄且正构烷烃含量较高的石油蜡产品,这些产品可以用作节温器用蜡介质;再经进一步调配,即可得到行程均匀线性的节温器用蜡介质。行程均匀线性的节温器用蜡介质再与导热剂和稳定剂混合均匀,成型、包装后即可得到节温器用介质产品。本发明方法装置投资低、生产过程简单、操作费用低、无溶剂污染环境,由其制备的节温器的推杆行程均匀线性且导热性能稳定。附图说明图1是本发明实施例1的中间产品(Ⅰ)和中间产品(Ⅱ)制备的节温器的推杆行程性能曲线。图2是本发明实施例1的中间产品(Ⅱ)、(Ⅲ)、(Ⅳ)制备的节温器的推杆行程性能曲线。图3是本发明实施例1的行程均匀线性的节温器用蜡介质制备的节温器的推杆行程性能曲线(Ⅴ)和理想的推杆行程性能曲线。图4是本发明实施例1的节温器用介质制备的节温器的推杆行程性能曲线(Ⅵ)及其经500次高—低温循环后其推杆的行程性能曲线(Ⅶ)和理想的推杆行程性能曲线。图5是本发明对比例中行程均匀线性的节温器用蜡介质制备的节温器的推杆行程性能曲线(Ⅴ)及其经500次高—低温循环后其推杆的行程性能曲线(Ⅷ)和理想的推杆行程性能曲线。图1-5中横坐标为温度,纵坐标为节温器推杆行程。具体实施方式发汗皿上部连接可拆卸的密封装置并与缓冲罐和压缩机连接,和/或在发汗皿下部连接缓冲罐和真空泵;发汗皿外增加夹套,夹套与可移动盘管和循环系统相连,循环系统具有程序降温/加热功能;以熔点适宜的石蜡为原料,加热熔化后装入发汗皿,将盘管浸没在原料中并固定;在夹套和盘管内通入低温介质以降低蜡层温度至原料熔点温度附近并恒温一段时间;在蜡层表面均匀铺满混合固体颗粒;加热循环介质提高蜡层温度;连接密封装置并启动压缩机以在蜡层以上形成正压,和/或启动真空泵以在蜡层以下形成负压,用以强制气流通过蜡层;蜡层温度达到预设温度并恒温一段时间后停止发汗过程。蜡上经精制后即为节温器用蜡介质,再经进一步调配,即可得到行程均匀线性的节温器用蜡介质。行程均匀线性的节温器用蜡介质再与导热剂和稳定剂混合均匀,成型、包装后即可得到节温器用介质产品。以下通过实施例1具体说明本发明节温器用介质的制备方法。实施例1本实施例包括:节温器用蜡介质中间产品(Ⅰ)、(Ⅱ)、(Ⅲ)、(Ⅳ)的制备、行程均匀线性的节温器用蜡介质的制备和节温器用介质的制备,共六部分。A:中间产品(Ⅰ)的制备本部分包括:(A1)准备工作、(A2)装料、(A3)降温—高温恒温—降温—低温恒温结晶、(A4)升温—恒温发汗、(A5)中间产品(Ⅰ)粗产品收集、(A6)中间产品(Ⅰ)精制等过程。(A1)准备工作将发汗皿上部的密封系统与缓冲罐和压缩机连接好。发汗皿皿板下部垫水。将发汗皿的夹套与可移动盘管和具有程序制冷/加热功能的循环系统相连,以水为导热介质。启动循环系统的加热功能,使循环水介质升温至75℃。(A2)装料以70号半炼蜡(大连石化公司生产,其性质为:熔点70.35℃;含油量0.81%;正构烷烃含量70.37%)为原料,加热熔化后加入发汗皿。将盘管浸没在原料蜡层中并固定。(A3)降温—高温恒温—降温—低温恒温结晶启动循环系统的制冷功能,以2.0℃/h的降温速率使蜡层温度下降至71.0℃并恒温2.0小时进行高温恒温,以使结晶充分增长;再以1.5℃/h的降温速率使蜡层温度下降至60.0℃并恒温2.0小时进行低温恒温,以使结晶更充分。关闭循环系统的制冷功能。(A4)升温—恒温发汗排出发汗皿垫水。发汗皿出口连接蜡下储罐;连接发汗皿上部密封装置;启动压缩机并保持缓冲罐内压力稳定在1.0~1.2个大气压(表压),发汗皿皿板下方保持常压;启动循环系统加热功能,以1.5℃/h的升温速率使蜡层温度升高到72.0℃并恒温2.0小时;以1.5℃/h的升温速率使蜡层温度升高到74.0℃并恒温4.0小时以使蜡层中的固态组分与液态组分充分分离。停压缩机,终止发汗脱油过程。(A5)中间产品(Ⅰ)粗产品收集发汗皿出口换接粗产品储罐(Ⅰ)以接收蜡上;继续升高循环水的温度到90℃,以熔化取出蜡上,即为中间产品(Ⅰ)粗产品。(A6)中间产品(Ⅰ)精制粗产品经白土精制、成型后即为节温器用蜡介质中间产品(Ⅰ)。节温器用蜡介质中间产品(Ⅰ)性质:熔点75.8℃;含油量0.40%;正构烷烃含量83.68%。节温器用蜡介质中间产品(Ⅰ)的收率为12.5%(相对于原料70号半炼蜡)。由蜡介质中间产品(Ⅰ)制备的节温器推杆的行程—温度关系如图1中的中间产品(Ⅰ)所示。从图1可以看出,节温器推杆行程在74℃时行程小于1mm,72℃~82℃间行程大于8mm,符合标称温度为72℃节温器的技术要求。B:中间产品(Ⅱ)的制备本实施例包括:(B1)准备工作、(B2)装料、(B3)降温—高温恒温—降温—低温恒温结晶、(B4)升温—恒温发汗、(B5)中间产品(Ⅱ)粗产品收集及混合金属颗粒回收、(B6)中间产品(Ⅱ)精制等过程。(B1)准备工作筛分出20目~40目的铅颗粒、铜颗粒和铁颗粒,按重量比为1:1:1混合均匀。将发汗皿上部的密封系统与缓冲罐和压缩机连接好。发汗皿皿板下部垫水;在发汗皿底部铺双层中速滤纸。将发汗皿的夹套与可移动盘管和具有程序制冷/加热功能的循环系统相连,以水为导热介质。启动循环系统的加热功能,使循环水介质升温至75℃。(B2)装料以70号半炼蜡(性质同A2)为原料,加热熔化后加入底部铺好滤纸的发汗皿。将盘管浸没在原料蜡层中并固定。(B3)降温—高温恒温—降温—低温恒温结晶启动循环系统的制冷功能,以2.0℃/h的降温速率使蜡层温度下降至71.0℃并恒温2.0小时进行高温恒温,以使结晶充分增长;再以1.5℃/h的降温速率使蜡层温度下降至60.0℃并恒温2.0小时进行低温恒温,以使结晶更充分。在蜡层表面铺满前述的铅、铜和铁的混合颗粒。关闭循环系统的制冷功能。(B4)升温—恒温发汗排出发汗皿垫水。发汗皿出口连接一蜡下(第一部分发汗流出物,下同)储罐;连接发汗皿上部密封装置;启动压缩机并保持缓冲罐内压力稳定在1.0~1.2个大气压(表压),发汗皿皿板下方保持常压;启动循环系统加热功能,以1.5℃/h的升温速率使蜡层温度升高到72.0℃并恒温2.0小时以使蜡层中的固态组分与液态组分充分分离。发汗皿出口换接二蜡下储罐;保持缓冲罐内压力稳定在1.0~1.2个大气压(表压),发汗皿皿板下方保持常压;以1.5℃/h的升温速率使蜡层温度升高到74.0℃并恒温4.0小时以使蜡层中的固态组分与液态组分充分分离。停压缩机,终止发汗脱油过程。(B5)中间产品(Ⅱ)粗产品收集及混合金属颗粒回收发汗皿出口换接粗产品储罐(Ⅱ)以接收蜡上;继续升高循环水的温度到90℃,以熔化取出蜡上,即为中间产品(Ⅱ)粗产品。收集滤纸上的混合金属颗粒,清洗、干燥以备重复使用。(B6)中间产品(Ⅱ)精制中间产品(Ⅱ)粗产品经白土精制、成型后即为节温器用蜡介质中间产品(Ⅱ)。节温器用蜡介质中间产品(Ⅱ)性质:熔点76.1℃;含油量0.23%;正构烷烃含量87.16%。节温器用蜡介质中间产品(Ⅱ)的收率为12.3%(相对于原料70号半炼蜡)。由节温器用蜡类温敏介质中间产品(Ⅱ)制备的节温器产品推杆的行程—温度关系如图1和图2中的中间产品(Ⅱ)所示。从图1和图2可以看出,节温器推杆行程在74℃时行程小于1mm,72℃~82℃间行程大于8mm,符合标称温度为72℃节温器的技术要求。C:中间产品(Ⅲ)的制备本部分包括:(C1)准备工作、(C2)装料、(C3)降温—高温恒温—降温—低温恒温结晶、(C4)升温—恒温发汗、(C5)中间产品(Ⅲ)粗产品收集及混合金属颗粒回收、(C6)中间产品(Ⅲ)精制等过程。(C1)准备工作将前述B部分中二蜡下产物(其性质为:熔点72.8℃;含油量0.52%;正构烷烃含量74.83%。相对于原料70号半炼蜡的收率14.50%。二蜡下产物性质符合72#半炼蜡的相关技术要求)经白土精制、成型,待用。筛分出30目~50目的铅颗粒和铁颗粒,按重量比为1:1混合均匀。在发汗皿下部安装缓冲罐并连接真空泵。发汗皿皿板下部垫水;在发汗皿底部铺双层中速滤纸。将发汗皿的夹套与可移动盘管和具有程序制冷/加热功能的循环系统相连,以水为导热介质。启动循环系统的加热功能,使循环水介质升温至76℃。(C2)装料以前述精制后的B部分中的二蜡下产物为原料,加热熔化后加入底部铺好滤纸的发汗皿。将盘管浸没在原料蜡层中并固定。(C3)降温—高温恒温—降温—低温恒温结晶启动循环系统的制冷功能,以1.5℃/h的降温速率使蜡层温度下降至73.0℃并恒温2.0小时进行高温恒温,以使结晶充分增长;再以1.0℃/h的降温速率使蜡层温度下降至65.0℃并恒温2.0小时进行低温恒温,以使结晶更充分。在蜡层表面铺满前述的铅和铁的混合颗粒。关闭循环系统的制冷功能。(C4)升温—恒温发汗排出发汗皿垫水。发汗皿出口连接蜡下储罐;开启真空泵并保持缓冲罐内压力稳定在-0.4~-0.6个大气压(表压),蜡层上方保持常压;以1.0℃/h的升温速率使蜡层温度升高到73.0℃并恒温4.0小时以使蜡层中的固态组分与液态组分充分分离。停真空泵,终止发汗脱油过程。(C5)中间产品(Ⅲ)粗产品收集及混合金属颗粒回收发汗皿出口换接粗产品储罐(Ⅲ)以接收蜡上;继续升高循环水的温度到90℃,以熔化取出蜡上,即为中间产品(Ⅲ)的粗产品。收集滤纸上的混合金属颗粒,清洗、干燥以备重复使用。(C6)中间产品(Ⅲ)精制中间产品(Ⅲ)粗产品经白土精制、成型后即为中间产品(Ⅲ)。中间产品(Ⅲ)的性质:熔点74.0℃;含油量0.38%;正构烷烃含量85.58%。中间产品(Ⅲ)的收率为8.62%(相对于原料70号半炼蜡)。由节温器用蜡类温敏介质中间产品(Ⅲ)制备的节温器推杆的行程—温度关系如图2中的中间产品(Ⅲ)所示。从图2可以看出,节温器推杆行程在72℃时行程小于1mm,70℃~80℃间行程大于8mm,符合标称温度为70℃节温器的技术要求。D:中间产品(Ⅳ)的制备本部分包括:(D1)准备工作、(D2)装料、(D3)降温—高温恒温—降温—低温恒温结晶、(D4)升温—恒温发汗、(D5)中间产品粗产品收集及混合金属颗粒回收、(D6)中间产品(Ⅳ)精制等过程。(D1)准备工作筛分出30目~50目的铅颗粒、铜颗粒和铁颗粒,按重量比为1:1:1混合均匀。将发汗皿上部的密封系统与缓冲罐和压缩机连接好。发汗皿皿板下部垫水;在发汗皿底部铺双层中速滤纸。将发汗皿的夹套与可移动盘管和具有程序制冷/加热功能的循环系统相连,以水为导热介质。启动循环系统的加热功能,使循环水介质升温至70℃。(D2)装料以66号半炼蜡(大连石化公司生产,其性质为:熔点66.4℃;含油量0.95%;正构烷烃含量73.62%)为原料,加热熔化后加入底部铺好滤纸的发汗皿。将盘管浸没在原料蜡层中并固定。(D3)降温—高温恒温—降温—低温恒温结晶启动循环系统的制冷功能,以2.0℃/h的降温速率使蜡层温度下降至67.0℃并恒温2.0小时进行高温恒温,以使结晶更充分;再以1.5℃/h的降温速率使蜡层温度下降至58.0℃并恒温2.0小时进行低温恒温。在蜡层表面铺满前述的铅、铜和铁的混合颗粒。关闭循环系统的制冷功能。(D4)升温—恒温发汗排出发汗皿垫水。发汗皿出口连接蜡下储罐;连接发汗皿上部密封装置;启动压缩机并保持缓冲罐内压力稳定在1.0~1.2个大气压(表压),发汗皿皿板下方保持常压;启动循环系统加热功能,以1.5℃/h的升温速率使蜡层温度升高到68.0℃并恒温4.0小时以使蜡层中的固态组分与液态组分充分分离。停压缩机,终止发汗脱油过程。(D5)中间产品粗产品收集及混合金属颗粒回收发汗皿出口换接粗产品储罐(Ⅳ)以接收蜡上;继续升高循环水的温度到90℃,以熔化取出蜡上,即为中间产品(Ⅳ)粗产品。收集滤纸上的混合金属颗粒,清洗、干燥以备重复使用。(D6)中间产品(Ⅳ)精制中间产品(Ⅳ)粗产品经白土精制、成型后即为中间产品(Ⅳ)。中间产品(Ⅳ)的性质:熔点72.9℃;含油量0.32%;正构烷烃含量91.67%。中间产品(Ⅳ)的收率为17.6%(相对于原料66号半炼蜡)。由节温器用蜡介质中间产品(Ⅳ)制备的节温器推杆的行程—温度关系如图2中的中间产品(Ⅳ)所示。从图2可以看出,节温器推杆行程在70℃时行程小于1mm,68℃~78℃间行程大于8mm,符合标称温度为68℃节温器的技术要求。E:行程均匀线性的节温器用蜡介质的制备将中间产品(Ⅱ)、(Ⅲ)、(Ⅳ)按重量比为15%:65%:20%加热熔融并混合均匀,既为行程均匀线性的节温器用蜡介质。由该介质制备的节温器推杆的行程—温度关系如图3中的性能曲线(Ⅴ)所示。从图3可以看出,由行程均匀线性的蜡介质制备的节温器,其推杆行程在常温~68℃范围内行程为0;68℃~72℃范围内行程为0.56mm(小于1mm);70℃~80℃范围内行程为8.45mm(大于8mm),符合标称温度为70℃的节温器的技术要求,且行程性能曲线均匀线性,与理想性能曲线基本吻合。F:节温器用介质的制备以铜金粉(苏州钻石金属粉有限公司生产,800目)为导热剂;纳米活性碳酸钙(河北承德化工有限公司生产,白色粉末,平均粒径为1500目)为稳定剂。将(E)部分制备的行程均匀线性的节温器用蜡介质、导热剂、稳定剂按重量比为25:65:10称量备用。将蜡介质加热至85℃,熔化后加入稳定剂和导热剂,混合均匀后成型、包装即为节温器用介质产品。由上述介质制备的节温器产品,其推杆的行程—温度关系如图4中(Ⅵ)所示。从图4中曲线(Ⅵ)可以看出,节温器推杆在常温~68℃范围内行程为0;68℃~72℃范围内行程小于1mm;70℃~80℃范围内行程大于8mm,符合标称温度为70℃的节温器的技术要求,且行程性能曲线均匀线性,与理想性能曲线基本吻合。将上述制备的节温器产品进行高—低温循环(高温90℃水浴中放置15min,再在低温50℃水浴中放置15min为一次循环),经500次循环后,其推杆的行程—温度关系如图4中曲线(Ⅶ)所示。从图4中曲线(Ⅵ)与曲线(Ⅶ)的对比可以看出,由本发明节温器用介质制备的节温器产品经500次高—低温循环后推杆的行程—温度关系基本无变化。对比例以实施例1(E)部分制备的蜡介质与铜金粉按重量比为25%:75%混合后制备节温器产品,其推杆的行程—温度关系如图5中(Ⅴ)所示;该节温器经500次高—低温循环后,其推杆的行程—温度关系如图5中(Ⅷ)所示。从图5中曲线(Ⅴ)与曲线(Ⅷ)的对比可以看出,不加稳定剂时,节温器经500次高—低温循环后其推杆的行程随温度变化有明显的变化。通过实施例1可以看出,本发明节温器用介质的制备方法通过在升温发汗过程中混合金属颗粒沉降而形成的上下贯穿蜡层的细小通道,并在升温发汗过程中强制气流通过蜡层的方法,增强了固态组分与液态组分分离效果,制备出碳数分布范围较窄且正构烷烃含量较高的石油蜡产品,可以用作节温器用蜡介质,蜡介质再进一步调配,即可得到行程均匀线性的节温器用蜡介质;蜡介质与导热剂和稳定剂混合后得到的节温器用介质,制备的节温器产品的导热性能稳定性好且行程均匀线性。