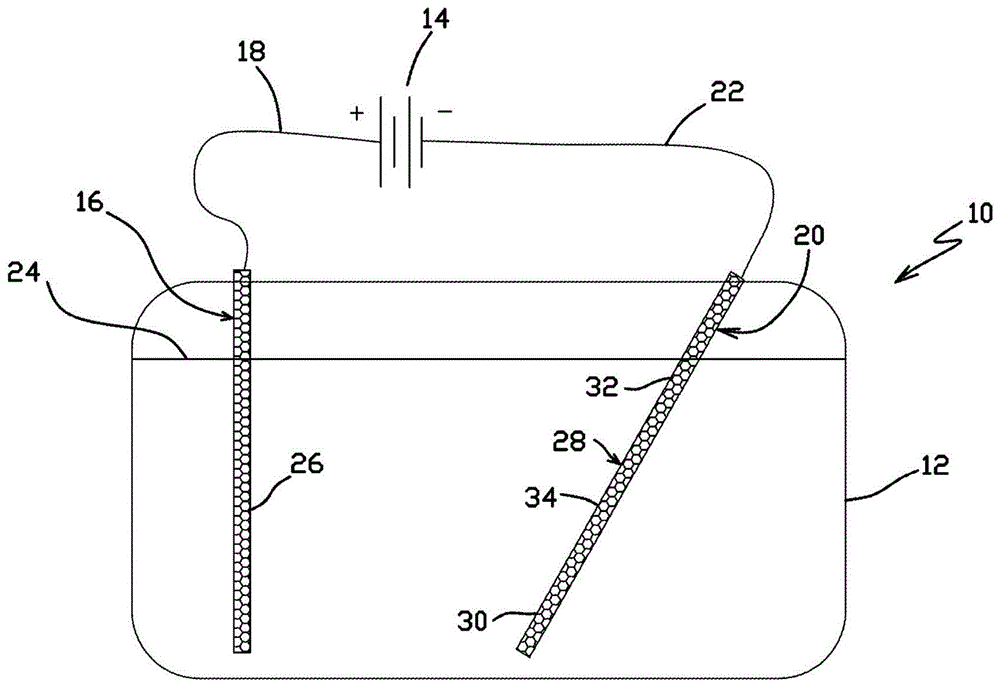
相关申请的交叉引用本申请要求享有2015年1月16日提交的临时申请第62/104,280号的优先权,该临时申请的全部内容以引用方式并入本文。本发明涉及金电镀溶液和用于电镀金的方法。更具体地,本发明涉及金电镀溶液和用于将金电镀至不锈钢表面上的方法,所述表面具有可能的图案化的金。
背景技术:
:电子装置的金属表面的镀金对于提供与金属表面的可靠的低电阻电接触经常是不可少的。这对于由天然形成氧化物钝化层的材料制成的金属表面尤其如此。此类材料包括例如不锈钢。不锈钢是“不锈的”,因为它形成了不受大多数化学品影响的大体稳定的氧化铬。这种耐化学侵蚀性也使不锈钢成为用于电镀金以及实现被镀金对不锈钢表面的良好粘着(adhesion)的具有挑战性的表面。通常,将金电镀至不锈钢使用酸/氯化物溶液将相对薄的镍“打底(strike)”层镀覆至不锈钢上。然后将金电镀在镍层上,所述镍层还也被称为“粘结”层。只要镍完全被金包封,这就会运作良好。然而,如果任何镍暴露例如在光致抗蚀剂界定的金/镍图案的边缘处,则当在后续处理步骤如常用的金属清洁工艺中金属与导电溶液接触时,将发生流电反应(galvanicreaction)。流电反应会腐蚀镍层并底切(undercut)金层。底切金层会破坏图案化的金/镍结构的完整性。因此,对需要图案化金结构的应用,期望将金直接镀覆至不锈钢表面上。所需的是与光致抗蚀剂相容的镀金工艺,其导致金层和不锈钢表面之间的良好粘着,无需引入易受腐蚀或流电溶解的“粘结”层。氰化金(i)化学知识也已被用于电镀金。然而,氰化金(i)在通常用于不锈钢的电镀溶液的低ph条件下表现不佳。例如,在ph4以下,氰化金(i)络合物开始解离(歧化),使得金开始沉淀,并且氰化物可能作为有毒气体被释放。一些形式的氯化金(iii)如四氯化氢金(iii)(haucl4)可在ph4以下稳定。然而,氯化金(iii)镀覆溶液不会产生对不锈钢具有良好粘着的电沉积金层。技术实现要素:各个实施方案涉及金电镀溶液。所述金电镀溶液包含氰化金(iii)化合物、氯化物化合物和盐酸。氰化金(iii)化合物是氰化金(iii)钾、氰化金(iii)铵和氰化金(iii)钠中的至少一种。氯化物化合物是氯化钾、氯化铵和氯化钠中的至少一种。在一些实施方案中,如果氰化金(iii)化合物为氰化金(iii)钾,则氯化物化合物为氯化钾;如果氰化金(iii)化合物为氰化金(iii)铵,则氯化物化合物为氯化铵;并且如果氰化金(iii)化合物为氰化金(iii)钠,则氯化物化合物为氯化钠。在另外的实施方案中,氰化金(iii)化合物为氰化金(iii)钾并且氯化物化合物为氯化钾。在一些实施方案中,所述溶液具有约0至约1、或约0.7至约0.9的ph值。在一些实施方案中,氰化金(iii)化合物的浓度为约1.0克金/升溶液至3.0克金/升溶液,并且氯化物阴离子的浓度为约0.30摩尔/升溶液至0.60摩尔/升溶液。在另外的实施方案中,氰化金(iii)的浓度为约1.8克金/升溶液至2.2克金/升溶液,并且氯化物阴离子的浓度为约0.45摩尔/升溶液至0.55摩尔/升溶液。在一些实施方案中,所述溶液不含乙二胺盐酸盐和/或氧化性酸,包括硝酸。各个实施方案涉及将电沉积的金图案直接产生至不锈钢表面上的方法。此类方法可包括在所述不锈钢表面上产生光致抗蚀剂图案,清洁所述不锈钢表面的未被所述光致抗蚀剂图案覆盖的部分,将所述不锈钢表面浸没在金电镀溶液中,并在所述金电镀溶液内的阳极和所述不锈钢表面之间施加电压,以产生从所述阳极至所述不锈钢表面的电流,以将金从所述金电镀溶液电镀至所述不锈钢表面上。所述金电镀溶液包含氰化金(iii)化合物、氯化物化合物和盐酸。氰化金(iii)化合物是氰化金(iii)钾、氰化金(iii)铵和氰化金(iii)钠中的至少一种。氯化物化合物是氯化钾、氯化铵和氯化钠中的至少一种。如果氰化金(iii)化合物为氰化金(iii)钾,则氯化物化合物为氯化钾;如果氰化金(iii)化合物为氰化金(iii)铵,则氯化物化合物为氯化铵;并且如果氰化金(iii)化合物为氰化金(iii)钠,则氯化物化合物为氯化钠。在一些方法中,氰化金(iii)化合物为氰化金(iii)钾并且氯化物化合物为氯化钾。此类方法还可包括向金电镀溶液中添加足够的盐酸,使得金电镀溶液具有约0至约1的ph,或使得金电镀溶液具有约0.7至约0.9的ph。此类方法还可包括维持氰化金(iii)钾在金电镀溶液中约1.0克金/升溶液至3.0克金/升溶液的浓度,和维持氯化物阴离子在金电镀溶液中约0.30摩尔/升溶液至0.60摩尔/升溶液的浓度。此类方法可进一步包括维持氰化金(iii)钾在金电镀溶液中约1.8克金/升溶液至2.2克金/升溶液的浓度,和维持氯化物阴离子在金电镀溶液中约0.45摩尔/升溶液至0.55摩尔/升溶液的浓度。在此类方法中,所述电压产生连续直流电,其中所述连续直流电在不锈钢表面产生1安培/平方分米至40安培/平方分米的电流密度。在此类方法中,所述电压产生脉冲直流电,所述脉冲直流电可在不锈钢表面产生1安培/平方分米至40安培/平方分米的时间平均电流密度。此类方法可进一步包括利用含氧的等离子体清洁工艺清洁所述不锈钢的表面。等离子体工艺可处于部分真空中或在大气压下。可将此类使电沉积金图案直接产生至不锈钢表面上的方法用于在磁盘驱动器头部悬置、光学图像稳定化悬置或医疗装置的不锈钢表面上沉积金。尽管公开了多个实施方案,但根据描述本发明的说明性实施方案的以下详细描述,本发明的其它实施方案对于本领域技术人员将变得显见。因此,详细描述被认为在本质上是说明性的而不是限制性的。附图说明图1显示评价电镀溶液的镀覆测试单元的示意性截面图。图2-3是包括金层和不锈钢(sst)层之间的镍层的分层结构的示意性图示说明。图4是根据一些实施方案的具有金图案的硬盘驱动器悬置部件的一部分的透视图。图5-6分别是根据一些实施方案的悬置柔性尾部(flexuretail)的顶部和底部侧视图,所述悬置柔性尾部具有含sst层的sst侧和含迹线层(tracelayer)的迹线侧以及电沉积在sst上的金图案。图7和图8是根据一些实施方案的具有电沉积在sst上的金图案的一部分柔性尾部的透视图,包括多个动态电测试(det)焊盘(pad)。图9是根据一些实施方案的具有电沉积在sst上的金图案的万向节的透视图。虽然本发明适于各种修改和替代形式,但是具体实施方案已通过举例方式在附图中显示,且在下面被详细描述。然而,其意图不是将本发明限定于所描述的特定实施方案。相反,本发明意在涵盖落入如由所附权利要求限定的本发明的范围内的所有修改、等同例和替代例。具体实施方式下文所述的实施方案使得能够将金层直接电镀至不锈钢表面上。所得电镀金层对不锈钢表面具有良好的粘着,不需要随后进行热处理、包覆压力或其它后处理以获得所需的粘着。一些实施方案与一些市售光致抗蚀剂相容。可通过将金离子从金电镀溶液电镀至阴极带电的不锈钢表面上,从而将金直接电沉积至不锈钢表面上。例如,可通过将金离子溶解至适合的电解液中来形成金电镀溶液。在某些实施方案中,金离子可以源自氰化金(iii),如氰化金(iii)钾(kau(cn)4)、氰化金(iii)铵(nh4au(cn)4)、氰化金(iii)钠(naau(cn)4)和其组合。氰化金(iii)钾(kau(cn)4)、氰化金(iii)铵(nh4au(cn)4)或氰化金(iii)钠(naau(cn)4)的适合浓度包括但不限于约1.0克金/升溶液至约3.0克金/升溶液、约1.8克金/升溶液至约2.2克金/升溶液或约2克金/升溶液的金电镀溶液。金电镀溶液还可以包含一种或多种酸。用于金电镀溶液中的适合的酸包括盐酸(hcl)。所述酸可与水如去离子水混合,以控制金电镀溶液的ph。金电镀溶液可具有低ph,或酸性ph。例如,所述金电镀溶液可具有小于约1且大于0的ph。更具体地,用于金电镀溶液的适合ph可以是约0.7至0.9。在一些实施方案中,将金电镀溶液维持在低ph如小于约1的ph可导致在电沉积工艺期间不锈钢表面的电清洁。这种电清洁工艺可消除来自不锈钢表面的钝化氧化物,并且可在不锈钢表面上直接产生具有良好粘着的电沉积的金层。含有金离子的金电镀溶液还可包含氯化钾(kcl)、氯化铵(nh4cl)和/或氯化钠(nacl)。在一些实施方案中,可向金电镀溶液中添加氯化钾、氯化铵或氯化钠,以控制对ph几乎没有影响的氯化物阴离子的浓度。例如,在一些实施方案中,金电镀溶液可具有约0.30摩尔/升溶液至0.60摩尔/升溶液的氯化物阴离子浓度。更具体地,金电镀溶液可具有约0.45摩尔/升溶液至0.55摩尔/升溶液的氯化物阴离子浓度。在一些实施方案中,以下组分的金电镀溶液将具有良好粘着的电沉积金层直接产生至不锈钢表面上:氰化金(iii)如氰化金(iii)钾(kau(cn)4)、氰化金(iii)铵(nh4au(cn)4)或氰化金(iii)钠(naau(cn)4);氯化物如氯化钾(kcl)或氯化铵(nh4cl);以及盐酸(hcl)。所述金电镀溶液与商业光致抗蚀剂相容,并且不在电镀阳极上产生累积。由于金(iii)和氰化物之间的强结合强度,氰化金(iii)对接近0的ph是稳定的。由于该强的结合强度,因此当与例如氰化金(i)比较时,氰化金(iii)的镀覆效率低。例如,在含有氰化金(iii)并且具有约0的ph的金电镀溶液内的电沉积期间,在电镀表面发生的反应中只有大约30%为金沉积。剩余的70%涉及对于高效镀覆通常不期望的其它化学反应,如表面上的氢与氧化物的反应。已惊讶地发现,在一些实施方案中,当电沉积至不锈钢表面上时,氢与氧化物的至少一些反应具有期望的目的:它们对不锈钢表面进行电清洁,并且可使得能够实现金与不锈钢表面的良好或改善的粘着。相比之下,其它形式的金(iii)如haucl4可在小于4的ph下稳定,但在所述金(iii)和氯化物之间的结合强度不足以相对于金沉积反应而有利于氢反应。因此,氯化金(iii)的镀覆溶液不产生对不锈钢具有良好粘着的电沉积金层。在一些实施方案中,金电镀溶液可适用于具有光致抗蚀剂或其它期望的有机材料的表面,如不锈钢表面。例如,在一些实施方案中,金电镀溶液可不含氧化性酸,如硝酸、硫酸、硝酸盐或其它组分,氧化性酸对有机材料具有腐蚀性或可组合而对有机材料具有腐蚀性。在一些实施方案中,金电镀溶液可不含乙二胺盐酸盐。在一些实施方案中,乙二胺盐酸盐可用于增强导电性并提供氯离子。然而,已发现在一些实施方案中,乙二胺可在电镀阳极上聚合,使其无效。在一些实施方案中,将电沉积金图案直接产生至不锈钢表面上可以从在衬底的不锈钢表面上产生光致抗蚀剂图案开始。可使用例如负性作用干膜光致抗蚀剂来产生光致抗蚀剂图案。可使用水溶液使此类光致抗蚀剂显影。在显影和任选地烘烤光致抗蚀剂图案之后,可任选地清洁不锈钢表面的未被光致抗蚀剂覆盖的部分,以从不锈钢表面的待被电镀金的部分去除残余有机物。也就是说,可清洁不锈钢表面以从不锈钢表面的被暴露或打算被暴露的部分去除残余有机物。可例如通过将不锈钢表面暴露于短暂的氧等离子体清洁工艺如大气压等离子体清洁或电晕清洁来进行清洁,以去除所述残余有机物。氧等离子体清洁工艺可实施为在线工艺(例如,连续卷对卷工艺),或离线工艺(例如,全板(panel)或单件零件(piece-part)工艺)。在一些实施方案中,可在等离子体清洁工艺之后进行任选的湿式清洁工艺。在湿式清洁工艺中,可将不锈钢表面先浸没在湿式清洁液中,然后再浸没在金电镀溶液中,以增加不锈钢表面的表面能,并促进在金电镀溶液中的润湿。湿式清洁液可包含一种或多种非氧化性无机酸或有机酸。在一些实施方案中,湿式清洁液可包含盐酸或柠檬酸。在清洁工艺之后,可将具有图案化的不锈钢表面的一个或多个衬底浸没在金电镀溶液中。也可将一个或多个阳极浸没在金电镀溶液中,并可在所述一个或多个的阳极和不锈钢表面之间施加电压以产生从阳极至不锈钢表面的电流,以将金从金电镀溶液电镀至不锈钢表面上。在一些实施方案中,电流是在电极之间产生的连续直流电。在其它实施例中,电流的形式可以是脉冲直流电(也被称为斩波(chopped)直流电)。在脉冲直流电中,直流电在接通和断开之间循环。电流在接通/断开循环中接通的时间段可不同于电流在所述循环中断开的时间段。所述电流接通的时间段可在循环的5%至循环的50%范围。接通/断开循环的频率可以是5hz至200hz。电流可以接通与断开循环多次,以将金沉积至期望的厚度。在一些实施方案中,所产生的连续直流电可在不锈钢表面处具有1安培/平方分米(asd)至40asd的电流密度。在其它实施方案中,不锈钢表面处的电流密度可以是约4asd。在一些实施方案中,其中电流是脉冲直流电,所述电流密度是在不锈钢表面处1asd至40asd的时间平均电流密度。在其它实施方案中,不锈钢表面(s)处的时间平均电流密度可以是约4asd。如本文所述,不锈钢的电清洁可在电镀工艺期间发生。例如,在其中ph为1或更小的情况下发生电镀的一些实施方案中,在阴极带电(带负电)的不锈钢表面处的水解离产生氢阳离子。这些氢阳离子和/或由酸内含物供应的氢阳离子然后形成氢反应性中性物,所述氢中性物与来自表面铁、镍和铬的氧化物的氧结合。金电镀溶液中的氯化物此时可与现在松散附着的铁、镍和铬络合,然后其作为不含氧化物的金属“被再电镀”至不锈钢表面。因此,在一些实施方案中,除了从不锈钢的表面去除氧化物钝化层之外,电沉积工艺还可将金属污染水平保持在低水平。在一些实施方案中,直接电镀至不锈钢上的金具有良好的粘着。所述粘着可通过本领域已知的任何适合的方法来验证,所述方法如胶带测试、划痕测试、弯曲测试、剥离测试或任何其它拉伸或剪切测试。可通过将金电镀成至少3微米的厚度来形成线和间隔(space),然后使剃刀刀片穿过一组20微米的线和间隔运行来进行更可定量的划痕测试。对不锈钢表面具有不适合的或不良粘着的电镀金将会从不锈钢表面剥离开。例如,如果在金和不锈钢之间存在任何空隙,则金层将从不锈钢表面剥离。可通过借助聚焦离子束观察金和不锈钢之间的界面来进一步验证无空隙镀覆(即,具有良好或适合的粘着)。在一些实施方案中,除了由盐酸(hcl)供应的氯离子之外,诸如氯化钾(kcl)或氯化铵(nh4cl)的氯化物也可以增加氯离子,用于络合游离的铁、镍和铬,如本文中所述的。通过调节氯化钾(kcl)或氯化铵(nh4cl),可独立于通过盐酸(hcl)调节的ph来调节总氯化物浓度。另外或备选地,与酸如盐酸(hcl)组合的氯化钾(kcl)、氯化铵(nh4cl)或氯化钠(nacl)可提供ph缓冲体系,并且可减少或消除金电镀溶液的ph在电镀工艺期间发生变化的风险。实施例在下列实施例中更具体地描述了本发明,这些实施例仅意在作为举例说明,因为在本发明的范围内的许多修改和变化对于本领域技术人员将是显而易见的。电镀测试图1显示了用于评价电镀溶液和电镀工艺条件的电镀测试单元的示意性横截面图。这种类型的测试单元也被称为赫尔(hull)单元,并且描述于例如美国专利2,149,344和美国专利3,121,053号中。赫尔单元被设计成使得在单个电镀测试中展现宽范围的电流密度。这使得例如能够确定电镀工艺质量对电流密度变化的敏感性。另外,通过改变连续电镀测试运行中目标电镀溶液组分的组分浓度,还可以确定镀覆工艺质量对组分浓度的敏感性。图1显示包括镀覆槽12、电源14、阳极16、阳极线索18、阴极20、阴极线索22和金电镀溶液24的电镀测试单元10。镀覆槽12至少部分地由电绝缘材料构造,使得镀覆槽12内的任何电压电势均不会通过镀覆槽12短路。电源14是直流电源。阳极16是由相对于金电镀溶液24至少在很大程度上化学惰性的材料例如铱和钛制成的板状电极。阳极线索18和阴极线索22是能够以足以有效电镀的水平承载电流的电线。阴极20是由不锈钢制成的板状电极。如图1中所示,金电镀溶液24填充镀覆槽12的至少一部分。阳极线索18将电源14的正端子电连接至阳极16。阴极线索22将电源14的负端子电连接至阴极20。阳极16包括阳极表面26。阳极表面26是阳极16的浸没在金电镀溶液24内并面向阴极20的表面。阴极20包括阴极表面28。阴极表面28是阴极20的浸没在金电镀溶液24内并面向阳极16的表面。阴极表面28包括近端部分30、远端部分32以及近端部分30和远端部分32之间的中间部分34。如图1中所示,阴极20相对于阳极16被设置成使得近端部分30和阳极表面26之间的距离小于远端部分32和阳极表面26之间的距离。作为阳极表面26和阴极表面28之间的这种配置的结果,电流密度沿着阴极表面28变化约40倍,在近端部分30处出现最高电流密度,在远端部分32处出现最低电流密度,在中间部分34处出现中间电流密度。在每次电镀测试期间,电流通过阳极线索18从电源14的正端子流动至阳极16。所述电流通过金电镀溶液24从阳极表面26流动至阴极20的阴极表面28。金电镀溶液24中的水在阴极表面28处解离,产生氢阳离子和氢反应性中性物,其与来自阴极表面28上的铁、镍和铬的氧化物的氧强烈地结合。金电镀溶液24中的高水平的氯化物然后与现在松散附着的铁、镍和铬络合,然后其作为不含氧化物的金属“被再电镀”至阴极表面28的不锈钢。一旦去除了来自阴极表面28的氧化物钝化层,来自金电镀溶液24中的氰化金(iii)的金被镀覆至阴极表面28上。从阴极20,电流流动通过阴极线索22返回至电源14的负端子。实施例1-3将上述电镀测试用于不同氯化物浓度的电镀实施例中,如下表中所示。在每个实施例中,横跨阴极表面的电流密度在近端部分处的高达40安培/平方分米(asd)至远端部分处的低至1asd的范围,在中间部分内具有标称的3.8asd。在每个实施例中,金电镀溶液由氰化金(iii)钾(kau(cn)4)、氯化钾(kcl)和盐酸(hcl)的水溶液组成。将kau(cn)4维持在2.0g金/升溶液(或约3.5gkau(cn)4)/升溶液)的浓度。将hcl浓度维持在0.31m,保持金电镀溶液的ph值低于1。在23℃的温度下的镀覆时间为60秒。在每个实施例中,通过改变kcl的浓度来改变氯化物浓度。降低氯化物浓度以检查金电镀溶液的电导率变化,如通过阳极和阴极之间的测得电势(电极间电势)所指示的。实施例和结果概述于下表中。表实施例氯化钾(m)总氯化物(m)电极间电势(v)10.090.403.920.180.493.730.250.563.6如表中所示,所述实施方案的氯化物浓度的变化具有小的但可测量的浴电导率的变化,如通过电极间电势所指示的。在所有三个实施例中,基于以下描述的划痕测试对不锈钢阴极表面上的电镀金的目视检查均显示其为光滑、有光泽且良好粘着的。这是在所测试的1asd至40asd的横跨电流密度范围内的情况。因此,如表的实施例中所示,实施方案是坚固稳健的,在整个宽范围的条件下都产生了良好的结果。实例结构将金层直接电镀至sst层上有助于开发可用于硬盘驱动器悬置中的有利的金图案。本文所述实施例的有利的应用涉及硬盘驱动器悬置。然而,本公开内容认识到本领域的受益于本公开内容的技术人员还可在各种其它适合的应用中利用所述金电镀溶液而将金直接电镀至sst上,所述应用例如光学图像稳定化悬挂装置(如例如,pct国际公开第wo2014/083318号中公开类型的那些)和可插入或可植入的医疗装置(如导管、起搏器、除颤器、引线和电极)。图2-3是根据本领域中的一些实施方案的包括金层110和不锈钢(sst)层115之间的镍层105的分层结构100的示意性举例图示。图2显示将金层110镀覆至镍层105上之后即刻的分层结构100。图3显示例如通过借助金属清洁工艺所促进的流电反应而腐蚀掉镍层105的分层结构100。可以看出,金层110的边缘未被支撑,其也称为闪金(goldflash),其中镍层105已被腐蚀所底切。金层110的部分更易于剥落掉并造成缺陷。相反,金电镀溶液有助于在无镍层105的情况下将金层110直接电镀至sst层115上,其中金层110被光致抗蚀剂图案化。即使在金属清洁工艺之后,金层110也直接受sst层115支撑,相对于使用插入镍层105,这改善了边缘质量并且降低了剥落的可能性。经电沉积且图案化的金层110可用于各种应用中,包括硬盘驱动器部件。图4是根据一些实施方案的具有金图案210的硬盘驱动器悬置部件200的一部分的透视图。部件200包括sst焊盘205和直接电沉积至sst焊盘205上的金图案210。具有光致抗蚀剂的金电沉积工艺能够在sst焊盘205上产生不连续的金图案210。换句话说,金图案可包括未连接的独立形状。金图案210可以被没有金的空间或间隙完全隔开,使sst焊盘205暴露。在举例图示的实施方案中,金图案210包括第一同心环215和位于第一同心环内部的第二同心环220。金图案210进一步包括间隙225,该间隙225隔开同心环215、220,使sst焊盘205的一部分暴露。如所示的,间隙225可在期望时完全隔开同心环215、220。虽然金图案210含有几个边缘,但与镍层沉积在金和sst之间时相比,所述金图案更不易于剥落。图5和图6分别是根据一些实施方案的悬置柔性尾部300的顶部和底部侧视图,所述悬置柔性尾部具有含sst层305的sst侧和含迹线层310的迹线侧,以及电沉积在sst上的金图案。电介质层317通常隔开sst层305和迹线层310。尾部300可使用各向异性导电膜(acf)在一个或多个接合区域处电连接至另一电路以形成一个或多个连接。这种类型的接合通常在接合至铜接合焊盘期间利用sst焊盘背衬而用于结构支撑。在sst焊盘上直接电镀金图案的能力允许sst焊盘除了作为结构支撑之外还可用作电接合焊盘。可能最好如图5中所见,尾部300包括具有一个或多个sst焊盘320的sst层305。在某些实施方案中,sst焊盘320各自与sst层305的其余部分以及和其它sst焊盘电绝缘。一个或多个sst焊盘320具有相应的金接合焊盘325。在某些实施方案中,通过具有光致抗蚀剂的电沉积工艺,将金接合焊盘325直接沉积至sst焊盘320上。金接合焊盘325相对于裸sst焊盘320提供了增强的电连接接口。由于改善的电性质,因此sst焊盘320上的金接合焊盘325可用作尾部300上的接合端子。在一些实施方案中,所有sst焊盘320都具有相应的金接合焊盘325。在其它实施方案(未显示)中,并非所有sst焊盘都具有相应的金接合焊盘。转至图6,尾部300包括迹线层310,迹线层310包括沿着尾部延伸的多条迹线,其中一些迹线彼此电绝缘。迹线层310的一条或多条迹线或各部分包括靠近尾部近侧的第一端,并且沿着尾部向远侧延伸至第二端或终端点。在一些实施方案中,一条或多条迹线终止于一个或多个铜接合焊盘340。在另外的实施方案中,一条或多条迹线终止于一个或多个通孔330。每个通孔330将迹线耦合至sst焊盘320或sst层305的一部分。一个或多个通孔330可耦合至铜接合焊盘340。如举例图示的实施方案中所示,一个或多个sst焊盘320具有相应的铜接合焊盘340和一个或多个相应的通孔330,通孔330将sst焊盘320与相应的铜接合焊盘340电耦合。sst焊盘320有助于在acf接合至尾部300的迹线侧期间与相应的铜接合焊盘340的接合。此外,如所示的,一个或多个sst焊盘320不具有相应的铜接合焊盘340,但具有迹线部分315。然而,对于具有金接合焊盘325的此类sst焊盘320,可将acf膜沉积至金接合焊盘325上以供acf接合至尾部300的sst侧。这种包括sst焊盘320上的金接合焊盘325的结构允许acf接合至尾部300的两侧,无需将铜引入至尾部300的sst侧的额外工艺。此外,在不存在铜接合焊盘340的情况下,这种结构能够为迹线层310的迹线沿着尾部300延伸留出更多的空间,并因此能够实现每个尾部300的更高密度的迹线和接合区域。图7和图8是根据一些实施方案的具有电沉积在sst上的金图案的一部分柔性尾部400的透视图,其包括多个动态电测试(det)焊盘405。det焊盘405使得能够从尾部400的sst侧进行测试探测。在某些实施方案中,一个或多个det焊盘405包括直接沉积在sst焊盘415上的金焊盘410。sst焊盘415也可以被认为是sst层420的一部分。sst层420设置在电介质层425的一侧上。迹线层430设置在电介质层425的另一侧上。迹线层430通过布置在迹线层430上的覆盖层435中的开口暴露。例如,可通过覆盖层435暴露一个多个铜接合焊盘440。当组装所述悬置时,柔性尾部400可通过铜接合焊盘440电耦合至所述组件的其它部分。一个或多个铜接合焊盘440可通过电介质层425中的通孔(未显示)电耦合至相应的det焊盘405。这种结构可比包括完全延伸穿过电介质层的铜det焊盘的结构更容易被制造,因为不需要背部接入步骤。图9是根据一些实施方案的具有电沉积在sst上的金图案的万向节500的透视图。如所示的,万向节500构造为接收激光二极管作为热辅助磁记录(hamr)万向节的一部分。举例示出的万向节500包括设置在电介质层510上的sst层505,sst层505至少部分由迹线层515背衬。sst层505包括与sst层505的其它部分电绝缘的sst岛520。第一组的一个或多个金接合焊盘525可直接沉积在sst岛520上。第二组的一个或多个金接合焊盘530可直接设置在sst层505的另一部分上。第一和第二组金接合焊盘525、530一起为激光二极管提供两个电端子。这种结构可比利用铜焊盘的结构更容易被制造,如本文关于其它实施方案所讨论的。可在不脱离本发明的范围的情况下对所讨论的示例性实施方案进行各种修改和补充。例如,尽管上述实施方案是指特定特征,但本发明的范围还包括具有不同特征组合的实施方案和不包括所有所描述特征的实施方案。因此,本发明的范围旨在涵盖落在权利要求的范围内的所有此类替代、修改和变化以及其所有等同形式。当前第1页12