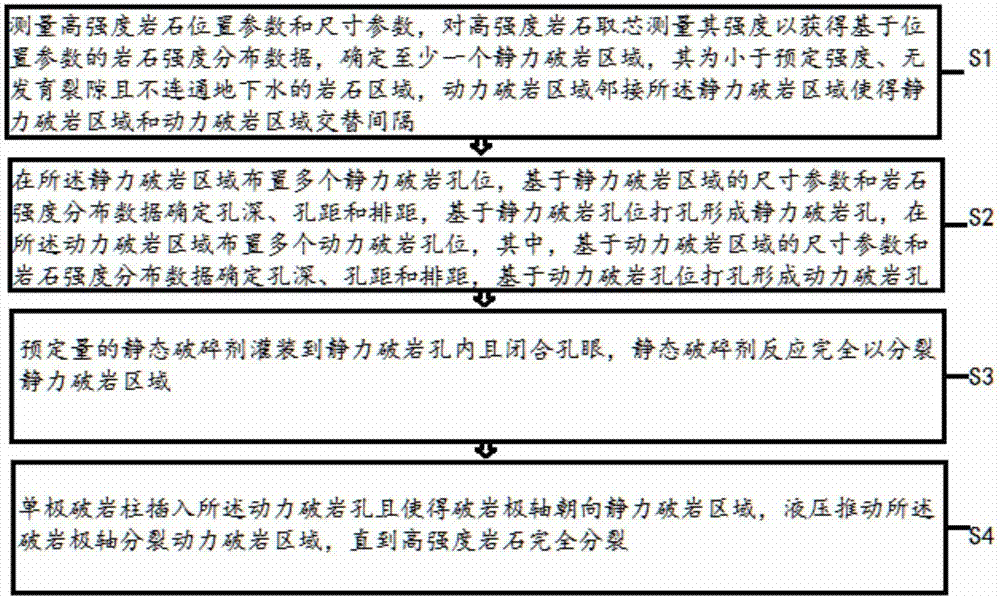
本发明涉及岩石非爆破裂
技术领域:
,特别是一种基于静动力交替耦合的高强度岩石分裂方法和分裂装置。
背景技术:
:目前,爆破仍是破碎岩石最经济、快捷的方法,但爆破过程中,可能产生爆破震动、爆破飞石、有毒气体等有害效应,当这些爆破危害失控时,可能对爆破点周围环境、人员或设备造成影响。近年来,随着人们自我保护意识和环境保护意识的加强,人们越来越关注爆破危害,尤其是当爆破区域距建(构)筑物很近时,为了确保周围建筑物的安全,减少因爆破引起的纠纷,一些施工单位不使用常规的爆破方法,而趋向于应用非爆破开挖的破岩工艺。这些需求也促使人们对非爆破破岩方法进行深入研究。目前,非爆破的破岩工艺经过了多年的不断研究已有了长足的发展,与传统爆破方法相比,非爆破方法具有安全性高、噪声小、无污染等优点。目前常用的非爆方法有:二氧化碳致裂技术是一种高压气体爆破技术,是利用液态二氧化碳吸热气化时体积急剧膨胀产生高压,致使煤(岩)体破碎或开裂。可广泛应用于煤矿及非煤矿山、水泥、采石等诸多行业。特别适用于煤与瓦斯突出矿并,替代炸药,可用于爆破落煤、瓦斯综合治理、冲击地压治理、消突、顶煤弱化、石门揭煤,巷道底鼓治理、煤仓清堵等。高频破碎锤是一种主要应用在岩石的破碎、旧城改造项目、混凝土构件的拆毁施工中的新型液压工程设备。近年来,随着国家对城市噪声污染和爆破采石工法危害性的控制,高频破碎锤凭借其工作的灵活性、载体设备的多样性及其高效的工作效率,高频破碎锤得到了快速发展。随着人们对环境和安全越来越重视,非爆破破岩方法得到了较大的发展,与常规爆破方法相比,非爆破法破碎岩石成本高出很多,但它安全,无污染、无危害。因此在距建筑物较近的地点实施破岩时,应结合爆区周围环境的特点,综合应用这两种手段,合理划分爆破区域与非爆破区域,达到既安全又经济的目的。但对于大体积岩体,单纯的静态破碎法需要耗费大量试剂,且爆破周期长,对坚硬岩石效果差。二氧化碳致裂器虽然属于非爆方法,但实施过程中仍会产生冲击波,影响周围岩体,对于对地层扰动要求严格的区域仍不能使用。高频破碎锤对大体积岩石的破裂仍然有效率慢等缺点。随着人们对环境和安全越来越重视,非爆破破岩方法得到了较大的发展,与常规爆破方法相比,非爆破法破碎岩石成本高出很多,但它安全,无污染、无危害。但上述的非爆方法破碎效率低且能分裂强度低于50mpa的岩石,对于强度超过100mpa的超高强度岩石尚缺少较好的施工方法。在
背景技术:
部分中公开的上述信息仅仅用于增强对本发明背景的理解,因此可能包含不构成在本国中本领域普通技术人员公知的现有技术的信息。技术实现要素:发明要解决的问题如上所述,本发明需要提供一种基于静动力交替耦合的高强度岩石分裂方法和分裂装置,其能够对强度超过100mpa的超高强度岩石进行分裂,且施工效率高,操作方便且安全可靠。解决问题的方案本发明人等为了达成上述目的而进行了深入研究,具体而言,本发明提供一种基于静动力交替耦合的高强度岩石分裂方法包括下述步骤:第一步骤中,测量高强度岩石位置参数和尺寸参数,对高强度岩石取芯测量其强度以获得基于位置参数的岩石强度分布数据,确定至少一个静力破岩区域,其为小于预定强度、无发育裂隙且不连通地下水的岩石区域,动力破岩区域邻接所述静力破岩区域使得静力破岩区域和动力破岩区域交替间隔,第二步骤中,在所述静力破岩区域布置多个静力破岩孔位,其中,基于静力破岩区域的尺寸参数和岩石强度分布数据确定孔深、孔距和排距,基于静力破岩孔位打孔形成静力破岩孔,在所述动力破岩区域布置多个动力破岩孔位,其中,基于动力破岩区域的尺寸参数和岩石强度分布数据确定孔深、孔距和排距,基于动力破岩孔位打孔形成动力破岩孔,第三步骤中,预定量的静态破碎剂灌装到静力破岩孔内且闭合孔眼,静态破碎剂反应完全以分裂静力破岩区域,第四步骤中,单极破岩柱插入所述动力破岩孔且使得破岩极轴朝向静力破岩区域,液压推动所述破岩极轴分裂动力破岩区域,直到高强度岩石完全分裂。本发明中的高强度岩石指的是强度超过100mpa的岩石。在所述的基于静动力交替耦合的高强度岩石分裂方法中,第一步骤中,所述预定强度为30-40mpa,岩石强度分布数据包括岩石强度走向图。在所述的基于静动力交替耦合的高强度岩石分裂方法中,第二步骤中,静破岩孔位梅花状布满静力破岩区域和/或动破岩孔位梅花状布满动力破岩区域高,潜孔钻基于破岩孔位打孔形成破岩孔,静破岩孔位的孔距m400mm~450mm。在所述的基于静动力交替耦合的高强度岩石分裂方法中,第二步骤中,动破岩孔的孔深为岩石深度的0.4-0.6倍,动破岩孔位的孔距m以及其与静力破岩区孔位的距离l由以下方法确定:m=2m,其中f为单个破岩极轴对岩体施加的力的大小,r为静力破岩孔的半径,r为动力破岩孔半径,为岩体压力扩散角,m为静破岩孔位孔距,σ为岩石单轴饱和抗压强度。在所述的基于静动力交替耦合的高强度岩石分裂方法中,相邻的静力破岩区域和动力破岩区域中,每两个静力破岩孔与一个动力破岩孔对应且分置于动力破岩孔两侧。在所述的基于静动力交替耦合的高强度岩石分裂方法中,第三步骤中,静态破碎剂包括氧化钙,所述预定量为4.5-5kg,第四步骤中,所述单极破岩柱的直径为破岩孔半径r的92%-98%。根据本发明的另一方面,一种实施所述基于静动力交替耦合的高强度岩石分裂方法的分裂装置包括,测量单元,其配置成测量高强度岩石位置参数和尺寸参数,强度检测单元,其基于所述位置参数生成岩石强度分布数据,钻孔单元,其基于破岩孔位打孔形成破岩孔,分裂单元,用于分裂高强度岩石的分裂单元包括释放静态破碎剂的静力分裂单元和动力分裂岩石的动力分裂单元,动力分裂单元包括,液压源,其提供分裂单元分裂的动力,单极破岩柱,插入所述破岩孔的单极破岩柱经由输油管连接所述液压源,破岩极轴,其经由液压驱动可伸缩布置在所述单极破岩柱,所述破岩极轴朝向静力破岩区域,处理单元,其一端连接所述测量单元和强度检测单元,另一端连接钻孔单元和分裂单元,响应于岩石强度分布数据,处理单元确定岩石的至少一个静力破岩区域,以及邻接所述静力破岩区域的动力破岩区域响应于所述尺寸参数和岩石强度分布数据,处理单元确定静力破岩孔和动力破岩孔的孔位、孔深、孔距和排距,使得钻孔单元基于破岩孔位打孔形成预定孔深、孔距和排距的破岩孔,响应于岩石强度分布数据,处理单元确定所述预定量以释放静态破碎剂于静力破岩孔,以及确定液压作用力,使得破岩极轴分裂高强度岩石。在所述的分裂装置中,所述测量单元包括gps导航设备,所述强度检测单元包括用于取芯的钻机和强度测量单元,所述钻孔单元包括潜孔钻。在所述的分裂装置中,液压源包括液压油泵、增压器和用于控制液压的控制器,所述单极破岩柱的一侧纵向排列至少六个所述破岩极轴。在所述的分裂装置中,处理单元包括数字信号处理器、专用集成电路asic或现场可编程门阵列fpga,处理单元包括存储器,所述存储器可以包括一个或多个只读存储器rom、随机存取存储器ram、快闪存储器或电子可擦除可编程只读存储器eeprom。本发明具有以下特点:施工方便,钻孔采用常用的潜孔钻钻孔,成孔简单、应用灵活、操作方便,对操作人员技能无特殊要求。静态破碎剂不属于危险物品,因而在购买、运输、保管、使用中,不受任何限制。施工过程安全,不存在炸药爆破时产生的震动、空气冲击波、飞石、噪音、有毒气体和粉尘的危害。需破则破,需留则留。按照要求,设计适当的参数,可达到有计划地分裂、切割岩石和混凝土的目的。单极破岩柱结构简单,施工过程中安全系数较高。节约时间、减少隐患,所用静态破碎剂在对岩体进行预裂之后,后续动力破岩可以极大提高工作效率,相比传统静态破碎施工方法每循环可节省预裂时间5小时。很大程度上减少了因预裂时间间隔长造成破碎解小设备(液压破碎锤)空闲时间增加了设备的利用率提高了开挖效率。上述说明仅是本发明技术方案的概述,为了能够使得本发明的技术手段更加清楚明白,达到本领域技术人员可依照说明书的内容予以实施的程度,并且为了能够让本发明的上述和其它目的、特征和优点能够更明显易懂,下面以本发明的具体实施方式进行举例说明。附图说明[图1]示出了本发明一个实施例的基于静动力交替耦合的高强度岩石分裂方法的步骤示意图。[图2]示出了本发明一个实施例的所述基于静动力交替耦合的高强度岩石分裂方法静力破岩区域和动力破岩区域分布示意图。[图3]示出了本发明一个实施例的所述基于静动力交替耦合的高强度岩石分裂方法的破碎过程示意图。[图4]示出了本发明一个实施例的所述基于静动力交替耦合的高强度岩石分裂方法的破岩形态示意图。[图5]示出了本发明一个实施例的所述基于静动力交替耦合的高强度岩石分裂方法与现有技术的效果比较示意图。[图6]示出了本发明一个实施例的所述基于静动力交替耦合的高强度岩石分裂方法的静力破岩孔和动力破岩孔的分布示意图。[图7]示出了本发明一个实施例的所述基于静动力交替耦合的高强度岩石分裂方法的破岩孔位位置示意图。[图8]示出了本发明一个实施例的实施所述基于静动力交替耦合的高强度岩石分裂方法的分裂装置结构示意图。[图9]示出了本发明一个实施例的实施所述基于静动力交替耦合的高强度岩石分裂方法的分裂装置的动力分裂单元的结构示意图。具体实施方式下面将参照附图更详细地描述本发明的具体实施例。虽然附图中显示了本发明的具体实施例,然而应当理解,可以以各种形式实现本发明而不应被这里阐述的实施例所限制。相反,提供这些实施例是为了能够更透彻地理解本发明,并且能够将本发明的范围完整的传达给本领域的技术人员。需要说明的是,在说明书及权利要求当中使用了某些词汇来指称特定组件。本领域技术人员应可以理解,技术人员可能会用不同名词来称呼同一个组件。本说明书及权利要求并不以名词的差异来作为区分组件的方式,而是以组件在功能上的差异来作为区分的准则。如在通篇说明书及权利要求当中所提及的“包含”或“包括”为一开放式用语,故应解释成“包含但不限定于”。说明书后续描述为实施本发明的较佳实施方式,然所述描述乃以说明书的一般原则为目的,并非用以限定本发明的范围。本发明的保护范围当视所附权利要求所界定者为准。为便于对本发明实施例的理解,下面将结合附图以几个具体实施例为例做进一步的解释说明,且各个附图并不构成对本发明实施例的限定。具体而言,如图1所示基于静动力交替耦合的高强度岩石分裂方法的步骤示意图。一种基于静动力交替耦合的高强度岩石分裂方法包括下述步骤:第一步骤s1中,测量高强度岩石位置参数和尺寸参数,对高强度岩石取芯测量其强度以获得基于位置参数的岩石强度分布数据,确定至少一个静力破岩区域1,其为小于预定强度、无发育裂隙且不连通地下水的岩石区域,动力破岩区域2邻接所述静力破岩区域1使得静力破岩区域1和动力破岩区域2交替间隔,图2示出了本发明一个实施例的所述基于静动力交替耦合的高强度岩石分裂方法静力破岩区域和动力破岩区域分布示意意图,参见图2。第二步骤s2中,在所述静力破岩区域1布置多个静力破岩孔位,其中,基于静力破岩区域1的尺寸参数和岩石强度分布数据确定孔深、孔距和排距,基于静力破岩孔位打孔形成静力破岩孔3,在所述动力破岩区域2布置多个动力破岩孔位,其中,基于动力破岩区域2的尺寸参数和岩石强度分布数据确定孔深、孔距和排距,基于动力破岩孔位打孔形成动力破岩孔4,第三步骤s3中,预定量的静态破碎剂灌装到静力破岩孔3内且闭合孔眼,静态破碎剂反应完全以分裂静力破岩区域1,第四步骤s4中,单极破岩柱5插入所述动力破岩孔4且使得破岩极轴6朝向静力破岩区域1,液压推动所述破岩极轴5分裂动力破岩区域2,直到高强度岩石完全分裂。图3示出了本发明一个实施例的所述基于静动力交替耦合的高强度岩石分裂方法的破碎过程示意图,参见图3。为了进一步理解本发明,在一个实施例中,本方法在某地铁站深基坑开挖过程中的应用。由于车站基坑地质情况错综复杂,岩石岩石体积较大,完整性高,且紧邻高铁线,环境要求高,为了满足工期要求,车站基坑开挖工期紧,且不能采取爆破开挖,现有技术开挖都无法满足要求。本方法及时地解决了硬质岩石不能爆破情况下的开挖效果,开挖效率高,无震动、无扬尘,环境适应性强,为下道工序的喷锚支护节约了大量时间,降低了因破碎锤刷坡时间长造成的边坡稳定性的安全隐患,边坡平整度检测结果符合设计规及范要求。本发明的一个实施例中,测量高强度岩石位置参数和尺寸参数,对高强度岩石取芯测量其强度以获得基于位置参数的岩石强度分布数据,确定静力破岩区一、静力破岩区二,其为小于预定强度、无发育裂隙且不连通地下水的岩石区域,动力破岩区一、动力破岩区二邻接所述静力破岩区一、静力破岩区二使得静力破岩区域和动力破岩区域交替间隔,破岩区内均为一排破岩孔组成。破岩过程中,静力破岩区一和静力破岩区二内的破岩孔由静态破碎剂预裂,产生岩石裂面,进而在动力破岩区一吊装单极破岩柱,其破岩极轴朝向静力破岩区一;在动力破岩区二吊装单极破岩柱,其破岩极轴朝向静力破岩区二。由静力破岩产生的岩石裂面会诱导由动力破岩产生裂面的方向,最终使由静力破岩和动力破岩产生的岩石裂面相互贯通,使岩石分裂,为用器械对岩石进行松动和解小提供基础。本发明的一个实施例中,场地内地下水类型主要为岩溶裂隙水,渗透系数为15.5m/d。平均水位埋深10.44m,水位埋深浅,基坑涌水量8628m/d,对基坑施工不利,施工时拟采用坑内排水沟+集水井明排。基坑场地下伏基岩为寒武系石灰岩,基本区位于背斜的核部,南侧岩层倾向南东,倾角最大约为30°,中部岩层较为平缓,北侧倾向北西,倾角最大约为50°。根据地质详勘及现场实际,基坑内除表层土外中下部为中风化石灰岩,饱和单轴抗压强度为60-100mpa,天然密度2.71kg/m3,按土壤及岩石分类属特坚石。坑内石灰岩强度高、方量大、工期紧,且不能采用常规爆破开挖。在勘探作业中,发现开挖区域有大量大体积岩石,且岩体完整,无较发育裂隙。破岩施工前,预计施工过程中天气晴朗,无阴雨天气。地质条件和天气均适合采用静态破碎剂破岩。设计裂石孔布置方式和位置。静力破岩区孔径为42mm,孔距300mm,孔深1.5m,动力破岩区孔径250mm,孔距600mm,排距600mm,与相邻静力破岩区距离500mm,均采用梅花状布置,即邻排的动力破岩孔之间错开布置。与动力破岩区相邻的静力破岩区,每两个静力破岩孔与一个动力破岩孔对应,分置于动力破岩孔两侧。同排孔位应相互平行,避免歪斜,否则直接影响破碎效果。孔间距、排距越小,破碎效果越好,但钻孔工程量也相应增加。具体参数可以根据现场实际情况适当调整。用潜孔钻按照设计的破岩孔位打孔,并将孔内杂物、岩屑清除干净。按设计剂量拌合静态破碎剂并按照4.8kg每孔的剂量灌装到静力破岩孔内,同一排孔位尽量同时装入膨胀剂,在孔眼上部做覆盖措施。其在破岩过程中数据统计如表1。表1本方法破岩孔位参数表岩石中风化石灰岩岩石强度100mpa静力孔孔径42mm动力孔孔径250mm静力孔孔距0.3m动力孔孔距0.6m孔深1.5m动力孔排距0.6m钻孔速度3孔/h*台破碎剂4.8kg/孔装药完成后,应有专人在安全位置观察装药部位的变化,提醒通过人员注意安全。膨胀剂的作用生效时间,依照使用产品的不同而变化。产品一定,环境温度一定,破裂时间相对稳定。装药后2-3h,装药部位产生裂隙,6h后裂缝宽度基本稳定,12h内药剂的胀裂能量释放完毕。其在破岩过程中数据统计如表2。表2本方法静力破岩数据统计表待静态破碎剂反应完全后,于动力破岩孔4内吊装直径为240mm的单极破岩柱5,调整破岩柱方向,使破岩极轴6朝向相邻的静力破岩孔3。运行超高压油泵站,产生超高油压流经输油管形成推力驱动破岩极轴6,涨裂岩石。动力涨裂后最大的三条裂缝宽度统计如表3。最后用器械对破裂后的岩石进行松动和解小,装运出场地。图4示出了本发明一个实施例的所述基于静动力交替耦合的高强度岩石分裂方法的破岩形态示意图。表3动力破岩裂缝数据统计表通过单独使用静态破碎剂、动力破岩和动静耦合对比,测量其最大裂缝宽度的平均值。设计裂石孔布置方式和位置。静力破岩区孔径为42mm,孔距300mm,排距300mm,孔深1.5m,采用梅花状布置。按设计剂量拌合静态破碎剂并按照4.8kg每孔的剂量灌装到静力破岩孔3内,同一排孔位尽量同时装入膨胀剂,在孔眼上部做覆盖措施。装药后2-3h,装药部位产生裂隙,6h后裂缝宽度基本稳定,12h内药剂的胀裂能量释放完毕。动力破岩区孔径250mm,孔距600mm,排距600mm,孔深1.5m,采用梅花状布置。同排孔位应相互平行,避免歪斜,否则直接影响破碎效果。于动力破岩孔4内吊装直径为240mm的单极破岩柱,调整破岩柱方向,使破岩极轴朝向相邻的静力破岩孔。运行超高压油泵站,产生超高油压流经输油管形成推力驱动破岩极轴6,涨裂岩石。将单独采用静态破碎剂和动力破岩所形成的裂缝宽度进行统计后,和动静耦合进行对比,图5示出了本发明一个实施例的所述基于静动力交替耦合的高强度岩石分裂方法与现有技术的效果比较示意图。由图5可得,动静耦合破岩工法相对于单独采用静态破碎剂或者动力破岩具有较好的效果。近年来,随着城市地下空间发、高程建筑和深基础工程越来越多,城市内由于建、构筑物管线复杂,对施工技术的要求也越来越高,城市环保大气环境要求越来越高。特别石质基坑不能采用爆破开挖,各种硬质岩石的基坑、路堑等,都难免或多或少的要求不能采用爆破施工,本方法可以为类似施工环境下石方开挖,提供很好的借鉴,具有很好的参考价值。本发明的方法通过确定至少一个静力破岩区域,动力破岩区域邻接所述静力破岩区域使得静力破岩区域和动力破岩区域交替间隔,基于静力破岩区域的尺寸参数和岩石强度分布数据确定孔深、孔距和排距,基于静力破岩孔位打孔形成静力破岩孔,在所述动力破岩区域布置多个动力破岩孔位,静态破碎剂反应完全以分裂静力破岩区域,单极破岩柱插入所述动力破岩孔且使得破岩极轴朝向静力破岩区域,静力破碎和动力破碎交替耦合破碎既提高了破碎效率且能够破碎现有技术中无法非爆破碎的高强度岩石,相比现有技术可节省大量的时间成本且施工简便,避免了环境污染,可实现快速对超大体积高强度岩石进行分裂,施工效率高、污染小、风险低、技术难度低、实施方便快捷且安全可靠。在一个实施例中,基于静动力交替耦合的高强度岩石分裂方法包括,第一步骤:勘探岩体并清理表面覆土和其他杂物。第二步骤:根据地下水分布和其他地质条件以及天气因素判定是否可以采用本方法。所述能否采用本方法的适用条件为:静力破岩孔布置区域是否有较为发育的裂隙,是否与地下水连通,天气是否为阴雨。若岩体无较为发育裂隙,与地下水无连通,且天气晴朗,则可以采用本方法。第三步骤:若满足本方法适用条件,则选取破岩方向,设计裂石孔布置方式和位置,根据岩石大小、强度设计孔深、孔距、排距和静态破碎剂用量。第四步骤:用潜孔钻按照设计的破岩孔位打孔,并将孔内杂物、岩屑清除干净。第五步骤:按设计剂量拌合静态破碎剂并灌装到静力破岩孔内,在孔眼上部做覆盖措施。第六步骤:待静态破碎机反应完全后,于动力破岩孔内吊装单极破岩柱,调整破岩柱方向,使破岩极轴朝向相邻的静力破岩孔。运行超高压油泵站,产生超高油压流经输油管形成推力驱动破岩极轴,涨裂岩石。第七步骤:用器械对破裂后的岩石进行松动和解小,装运出场地。本发明所述的基于静动力交替耦合的高强度岩石分裂方法的优选实施方式中,第一步骤中,所述预定强度为30-40mpa,岩石强度分布数据包括岩石强度走向图。本发明所述的基于静动力交替耦合的高强度岩石分裂方法的优选实施方式中,第二步骤中,静破岩孔位梅花状布满静力破岩区域1和/或动破岩孔位梅花状布满动力破岩区域2,潜孔钻基于破岩孔位打孔形成破岩孔,静破岩孔位的孔距m400mm~450mm。图6示出了本发明一个实施例的所述基于静动力交替耦合的高强度岩石分裂方法的破岩孔位分布示意图,参见图6。本发明所述的基于静动力交替耦合的高强度岩石分裂方法的优选实施方式中,第二步骤中,动破岩孔的孔深为岩石深度的0.4-0.6倍,动破岩孔位的孔距m以及其与静力破岩区孔位的距离l由以下公式确定:m=2m,其中f为单个破岩极轴对岩体施加的力的大小,r为静力破岩孔的半径,r为动力破岩孔半径,为岩体压力扩散角,m为静破岩孔位孔距,σ为岩石单轴饱和抗压强度,图7示出了本发明一个实施例的所述基于静动力交替耦合的高强度岩石分裂方法的破岩孔位位置对比示意图,参见图7。同排孔位应相互平行,避免歪斜,否则直接影响破碎效果。孔间距、排距越小,破碎效果越好,但钻孔工程量也相应增加。具体参数可以根据现场实际情况适当调整。所述破岩孔位采用梅花状布置。邻排的动力破岩孔之间错开布置。与动力破岩区相邻的静力破岩区,每两个静力破岩孔与一个动力破岩孔对应,分置于动力破岩孔两侧。考虑到破岩孔内壁平整度和单极破岩柱下放问题,所述单极破岩柱的直径为破岩孔直径的92%-98%。本发明所述的基于静动力交替耦合的高强度岩石分裂方法的优选实施方式中,相邻的静力破岩区域和动力破岩区域中,每两个静力破岩孔与一个动力破岩孔对应且分置于动力破岩孔两侧。本发明所述的基于静动力交替耦合的高强度岩石分裂方法的优选实施方式中,第三步骤中,静态破碎剂包括氧化钙,所述预定量为4.5-5kg,第四步骤中,所述单极破岩柱的直径为破岩孔半径r的92%-98%。图8示出了本发明一个实施例的实施所述基于静动力交替耦合的高强度岩石分裂方法的分裂装置结构示意图,如图所示,一种实施所述基于静动力交替耦合的高强度岩石分裂方法的分裂装置包括,测量单元7,其配置成测量高强度岩石位置参数和尺寸参数,强度检测单元8,其基于所述位置参数生成岩石强度分布数据,钻孔单元9,其基于破岩孔位打孔形成破岩孔,分裂单元10,用于分裂高强度岩石的分裂单元10包括释放静态破碎剂的静力分裂单元11和动力分裂岩石的动力分裂单元12,动力分裂单元12包括,液压源13,其提供动力分裂单元分裂的动力,单极破岩柱5,插入所述破岩孔的单极破岩柱5经由输油管连接所述液压源13,破岩极轴6,其经由液压驱动可伸缩布置在所述单极破岩柱5,所述破岩极轴6朝向静力破岩区域1,处理单元14,其一端连接所述测量单元7和强度检测单元8,另一端连接钻孔单元9和分裂单元10,响应于岩石强度分布数据,处理单元14确定岩石的至少一个静力破岩区域1,以及邻接所述静力破岩区域1的动力破岩区域2,响应于所述尺寸参数和岩石强度分布数据,处理单元14确定静力破岩孔3和动力破岩孔4的孔位、孔深、孔距和排距,使得钻孔单元9基于破岩孔位打孔形成预定孔深、孔距和排距的破岩孔,响应于岩石强度分布数据,处理单元14确定所述预定量以释放静态破碎剂于静力破岩孔3,以及确定液压作用力,使得破岩极轴6分裂高强度岩石。本发明所述的分裂装置的优选实施例,所述测量单元7包括gps导航设备,所述强度检测单元8包括用于取芯的钻机和强度测量单元,所述钻孔单元包括潜孔钻。本发明所述的分裂装置的优选实施例,图9示出了本发明一个实施例的实施所述基于静动力交替耦合的高强度岩石分裂方法的分裂装置的动力分裂单元的结构示意图,液压源13包括液压油泵、增压器和用于控制液压的控制器,所述单极破岩柱5的一侧纵向排列至少六个所述破岩极轴6。本发明所述的分裂装置的优选实施例,处理单元14包括数字信号处理器、专用集成电路asic或现场可编程门阵列fpga,处理单元包括存储器,所述存储器可以包括一个或多个只读存储器rom、随机存取存储器ram、快闪存储器或电子可擦除可编程只读存储器eeprom。工业实用性本发明的所述基于静动力交替耦合的高强度岩石分裂方法及分裂装置可以在岩石非爆破碎领域制造并使用。尽管以上结合附图对本发明的实施方案进行了描述,但本发明并不局限于上述的具体实施方案和应用领域,上述的具体实施方案仅仅是示意性的、指导性的,而不是限制性的。本领域的普通技术人员在本说明书的启示下和在不脱离本发明权利要求所保护的范围的情况下,还可以做出很多种的形式,这些均属于本发明保护之列。当前第1页12