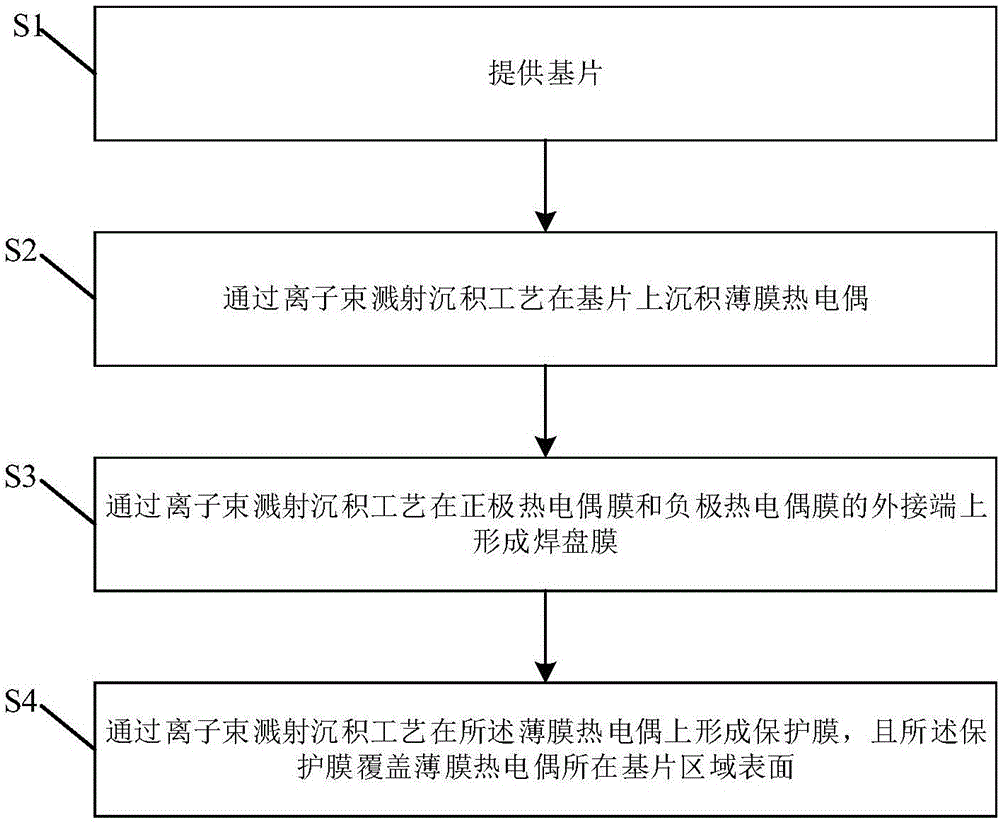
本发明涉及传感器
技术领域:
,尤其涉及一种薄膜温度传感器及制备方法。
背景技术:
:传感器技术是与通信技术和计算机技术构成现代信息产业的三大支柱,是一项当今世界令人瞩目的迅猛发展的高新技术,同时又是一项相对通信和计算机技术整体落后的瓶颈工业。传统的传感器因功能、特性、体积等难以满足现代计算机技术和通信技术对传感器的精度、可靠性、抗环境性、信息处理能力等要求而被逐渐淘汰。温度传感器是感受温度并转换成可用输出信号的传感器,主要包括热电阻、热敏电阻、热电偶以及集成P-N温度传感器。随着技术的发展,红外辐射和光纤温度等温度传感器也得到了越来越多的应用。然而,传统的热电偶传感芯片以正负极热电偶丝焊接形成热电偶接点进行测温,由于热偶丝式热电偶材料为块体材料,其热电偶接点的厚度较厚,对温度的响应时间较长,且热电偶封装以后具有较大的体积。因此,亟待开发一种响应时间快且体积小的高性能薄膜温度传感器。技术实现要素:本发明要解决的技术问题是,针对现有薄膜温度传感器的响应时间慢且体积大的缺陷,提供一种薄膜温度传感器及制备方法。为了解决上述技术问题,本发明提供了一种薄膜温度传感器,至少包括:基片;薄膜热电偶,其通过离子束溅射沉积技术在所述基片上形成;所述薄膜热电偶包括正极热电偶膜和负极热电偶膜,所述正极热电偶膜和负极热电偶膜的内端对接形成热电偶接点;焊盘膜,其通过离子束溅射沉积技术在正极热电偶膜和负极热电偶膜的外端上形成,用于与外接引线连接;保护膜,其通过离子束溅射沉积技术覆盖在所述薄膜热电偶上,并覆盖薄膜热电偶所在基片区域表面。在根据本发明优选实施例所述的薄膜温度传感器中,所述薄膜热电偶的厚度为0.5~0.8μm。在根据本发明优选实施例所述的薄膜温度传感器中,所述薄膜热电偶从以下一组热电偶材料中选择:镍铬10-镍硅3、铂铑30-铂铑6、钨铼5-钨铼26、钨铼3-钨铼25、镍铬-铜镍、铁-铜镍、镍铬硅-镍硅、铂铑13-铂、铂铑10-铂和铜-铜镍。在根据本发明优选实施例所述的薄膜温度传感器中,所述薄膜热电偶中正极热电偶膜和负极热电偶膜分别采用镍铬和镍硅热电偶材料,其中镍铬热电偶材料的薄膜沉积时间t1通过以下公式计算:t1=m-3×10-8x3+6×10-5x2-0.0255x+4.6282;]]>镍硅热电偶材料的薄膜沉积时间t2通过以下公式计算:t2=m1×10-10x4-4×10-7x3+0.0003x2-0.1072x+13.69;]]>其中m为预设薄膜厚度,x为离子束的离子能量,且离子束流设置为100mA。在根据本发明优选实施例所述的薄膜温度传感器中,所述薄膜温度传感器还包括通过离子束溅射沉积技术形成于所述薄膜热电偶以及保护膜之间的五氧化二钽绝缘过渡膜。本发明还提供了一种薄膜温度传感器的制备方法,该制备方法包括以下步骤:S1、提供基片;S2、通过离子束溅射沉积技术在基片上沉积薄膜热电偶;所述薄膜热电偶包括正极热电偶膜和负极热电偶膜,所述正极热电偶膜和负极热电偶膜的内端对接形成热电偶接点;S3、通过离子束溅射沉积技术在正极热电偶膜和负极热电偶膜的外接端上形成焊盘膜;S4、通过离子束溅射沉积技术在所述薄膜热电偶上形成保护膜,且所述保护膜覆盖薄膜热电偶所在基片区域表面。实施本发明的薄膜温度传感器及制备方法,具有以下有益效果:本发明使用离子束溅射沉积技术制备薄膜温度传感器,制备的各层薄膜密度高、附着力强,镀覆的薄膜热电偶厚度小,对温度的响应时间快,并且热电偶封装以后体积小,测量精度高。附图说明图1为根据本发明优选实施例的薄膜温度传感器结构示意图;图2为根据本发明优选实施例的薄膜温度传感器的制备方法流程图;图3为六靶台双离子束反应溅射沉积设备的结构示意图。具体实施方式为使本发明实施例的目的、技术方案和优点更加清楚,下面将结合本发明实施例中的附图,对本发明实施例中的技术方案进行清楚、完整地描述,显然,所描述的实施例是本发明的一部分实施例,而不是全部的实施例。基于本发明中的实施例,本领域普通技术人员在没有做出创造性劳动的前提下所获得的所有其他实施例,都属于本发明保护的范围。在附图中示出了根据本公开实施例的各种结构示意图。这些图并非是按比例绘制的,其中为了清楚表达的目的,放大了某些细节,并且可能省略了某些细节。图中所示出的各种区域、层的形状以及它们之间的相对大小、位置关系仅是示例性的,实际中可能由于制造公差或技术限制而有所偏差,并且本领域技术人员根据实际所需可以另外设计具有不同形状、大小、相对位置的区域/层。在本公开的上下文中,当将一层/元件称作位于另一层/元件“上”时,该层/元件可以直接位于该另一层/元件上,或者它们之间可以存在居中层/元件。另外,如果在一种朝向中一层/元件位于另一层/元件“上”,那么当调转朝向时,该层/元件可以位于该另一层/元件“下”。请参阅图1,为根据本发明优选实施例的薄膜温度传感器结构示意图。如图1所示,该薄膜温度传感器至少包括:基片1、薄膜热电偶、焊盘膜5和保护膜7。其中,基片1优选但不限于碳化硅质基片。薄膜热电偶采用离子束溅射沉积技术在基片1上形成。该薄膜热电偶包括正极热电偶膜2和负极热电偶膜3,其中正极热电偶膜2和负极热电偶膜3的内端对接形成热电偶接点4。薄膜热电偶的厚度为0.5~0.8μm。在本发明的优选实施例中,薄膜热电偶优选但不限于使用表格1所示的热电偶材料,具体的选择根据薄膜温度传感器的使用温度及信号输出要求决定。表格1分度号BCDEJ材料铂铑30-铂铑6钨铼5-钨铼26钨铼3-钨铼25镍铬-铜镍铁-铜镍分度号KNRST材料镍铬10-镍硅3镍铬硅-镍硅铂铑13-铂铂铑10-铂铜-铜镍焊盘膜5通过离子束溅射沉积技术在正极热电偶膜2和负极热电偶膜3的外接端上沉积而成,用于与外接引线连接。焊盘膜5优选但不限于。在本实施例中,引线膜4由金Au制成。虽然本实施例给出了一种具体的焊盘膜材料,但本发明不限于此,而是可以采用其它适用的电极材料,例如铝钴合金。焊盘膜5表面可以涂覆有耐高温无机胶状材料,如无机硅铝酸盐材料。保护膜7则通过离子束溅射沉积技术覆盖在薄膜热电偶上,并覆盖薄膜热电偶所在基片区域表面。该保护膜7优选但不限于二氧化硅材料。所述保护膜7能阻挡空气中的氧和水汽对传感器的侵蚀,提高薄膜温度传感器的可靠性和稳定性。在本发明优选的实施例中,薄膜温度传感器还包括通过离子束溅射沉积技术形成于薄膜热电偶以及保护膜7之间的五氧化二钽绝缘过渡膜6。该Ta2O5绝缘过渡膜6是为了缓减后续制备的保护层7与基片1及热电偶材料的晶格参数和热膨胀系数的不匹配性,过渡膜的厚度约为150~180nm。请参阅图2,为根据本发明优选实施例的薄膜温度传感器的制备方法流程图。如图2所示,本发明还提供了一种薄膜温度传感器的制备方法,可以用于制备上述薄膜温度传感器。该制备方法包括以下步骤:首先,在步骤S1中,提供基片1。随后,在步骤S2中,通过离子束溅射沉积技术在基片1上薄膜热电偶。该薄膜热电偶包括正极热电偶膜2和负极热电偶膜3,该正极热电偶膜2和负极热电偶膜3的内端对接形成热电偶接点4。该步骤S2进一步包括:S2-1、在基片1上制作正极热电偶膜光刻胶,并固定在工件台上;S2-2、设置离子束的离子能量为500~700eV,设置离子束流密度为0.4~0.55mA/cm2;并使真空仓的本底压强抽到并保持在3×10-3Pa及以下;设置工件台自转速度为7~9rpm,沉积角度为45°;S2-3、利用离子源轰击正极热电偶靶材,使正极热电偶靶材溅射出来的粒子沉积在基片上,形成正极热电偶膜;随后去除正极热电偶膜光刻胶;S2-4、在基片上制作负极热电偶膜光刻胶,并固定在工件台上;S2-5、利用离子源轰击负极热电偶靶材,使负极热电偶靶材溅射出来的粒子沉积在基片上,形成负极热电偶膜;随后去除负极热电偶膜光刻胶。随后,在步骤S3中,通过离子束溅射沉积技术在正极热电偶膜2和负极热电偶膜3的外接端上形成焊盘膜5。随后,在步骤S4中,通过离子束溅射沉积技术在薄膜热电偶上形成保护膜7,且保护膜7覆盖薄膜热电偶所在基片区域表面。在本发明的优选实施例中,还包括在步骤S3和步骤S4之间执行的步骤S3’,通过离子束溅射沉积技术在薄膜热电偶上沉积五氧化二钽绝缘过渡膜6。该五氧化二钽绝缘过渡膜6也覆盖薄膜热电偶所在基片区域表面。之后在五氧化二钽绝缘过渡膜6上镀覆所述保护膜7。在本发明的另一项优选实施例中,步骤S2~S4中离子源在轰击靶材前还包括靶材清洗步骤,该步骤中采用低能离子束对靶材表面轰击2~4分钟,以去除靶材表面杂质,该低能离子束的离子能量Ei=200~500eV,离子束流密度为Jb=0.2~0.4mA/cm2。更优选地,在步骤S2~S4中离子源在轰击靶材前还包括预处理步骤,该步骤中采用低能离子束对需要镀膜的工件表面轰击2~4分钟,以增大工件表面附着力,该低能离子束的离子能量Ei=200~500eV,离子束流密度为Jb=0.2~0.4mA/cm2。在本发明的优选实施例中,薄膜热电偶中的正极热电偶膜2和负极热电偶膜3分别采用镍铬和镍硅热电偶材料。镍铬-镍硅热电偶,即镍铬10-镍硅3热电偶,分度号为K,是目前用量最大的廉金属热电偶。正极镍铬热电偶材料的化学成分为:Ni:Cr=90:10,负极镍硅热电偶材料的化学成分为:Ni:Si=97:3,其使用温度为-200~1300℃。K型热电偶具有线性度好,热电动势较大,灵敏度高,稳定性和均匀性较好,抗氧化性能强,价格便宜等优点,能用于氧化性惰性气氛中。本发明中通过离子束溅射沉积技术能够使得沉积的薄膜热电偶中正极热电偶膜2和负极热电偶膜3的厚度均达到0.5~0.8μm。鉴于目前常用的薄膜制备工艺无法精确控制薄膜沉积厚度,而薄膜温度传感器对厚度的要求较高,本发明通过大量实验及经验总结,并结合离子束溅射沉积工艺中离子束的离子能量及离子束流对薄膜沉积速率的影响,得出了镍铬和镍硅热电偶材料薄膜沉积时间的最佳计算公式。其中步骤S2中选取的镍铬热电偶材料的薄膜沉积时间t1通过以下公式(1)计算:t1=m-3×10-8x3+6×10-5x2-0.0255x+4.6282;---(1)]]>步骤S2中选取的镍硅热电偶材料的薄膜沉积时间t2通过以下公式(2)计算:t2=m1×10-10x4-4×10-7x3+0.0003x2-0.1072x+13.69;---(2)]]>公式(1)和公式(2)中m为预设薄膜厚度,即需要沉积的薄膜热电偶的厚度,单位为nm。x为离子束的离子能量,单位为eV。计算获得的薄膜沉积时间t1和t2的单位为min。且在使用该公式精确设置薄膜沉积时间,以控制薄膜达到预设薄膜厚度时,需要在离子束溅射沉积过程中将离子束流设置为标准值,即100mA。本发明还对上述公式(1)和(2)进行了验证。以离子束能量分别为400eV、450eV、500eV、550eV、600eV和700eV,预设的薄膜热电偶的厚度分别为0.8μm、0.7μm、0.6μm和0.5μm,分别计算出最佳的薄膜沉积时间t1和t2。并通过实验,分别在基片1上使用离子束溅射沉积技术镀膜,设置离子束流为100mA,溅射角θs=45°,沉积角θs=17°,离子束能量分别为400eV、450eV、500eV、550eV、600eV和700eV,采用上述计算出的薄膜沉积时间t1和t2分别沉积镍铬热电偶材料和镍硅热电偶材料,并测量所得薄膜厚度。通过与预设厚度对比可知,当采用离子能量为450~550eV时,本发明可以将沉积的薄膜厚度精确控制在±2%的范围内。当采用离子能量为600~700eV时,本发明可以将沉积的薄膜厚度精确控制在±5%的范围内。请参阅图3,为六靶台双离子束反应溅射沉积设备的结构示意图。如图3所示,本发明的薄膜温度传感器的制备方法优选但不限于采用该六靶台双离子束反应溅射沉积设备制备。该六靶台双离子束反应溅射沉积设备包括主离子源21、辅离子源26、工件台28和可旋转的六靶台24。主离子源21和辅离子源26位于真空室29的两侧相对设置,两者的发射轴平行且间隔预定距离。六靶台24位于真空室中部主离子源的离子束22发射方向上,具有六个靶面,可分别用于固定钽靶材、二氧化硅靶材、正负热电偶靶材和焊盘膜靶材。工件台28用于固定基片1,位于辅离子源的离子束27发射方向上,同时位于六靶台24工作靶面的离子束溅射粒子25沉积的方向上。该工件台28上还设有用于遮挡工件台28上工件的可开关的挡板20。如图所示,六靶台24与主离子源21呈45度设置,工件台28与辅离子源26呈45度设置。下面结合图3的设备对薄膜温度传感器的制备过程进行具体描述。该实施例中以碳化硅制备基片1,依次镀上NiCr、NiSi、Au、Ta2O5、SiO2五种薄膜。一、环境准备:1、工作气体用纯度为99.99%的Ar,反应气体用纯度为99.99%的O2。工件台自转速度为8rpm。2、将长×宽=10×5mm的基片1固定在工件台28上作为工件,将NiCr、NiSi、Au、Ta和SiO2的靶材23依次固定在六靶台24的各个靶面上。3、关闭真空仓21,先用机械泵单机粗抽,当真空度达到10Pa时,启动分子泵双机精抽,将本底真空度抽到并保持在:3×10-3Pa。二、提供基片1,对表面进行清洗:1、用机械抛光和常规化学清洗先对基片1去油、去污、去氧化物。2、打开工件台的挡板20,用辅离子源26产生的低能Ar离子束轰击基片1表面3min,在基片1表面轰出的小坑将很大程度提高基片1与NiCr正极热电偶膜和NiSi负极热电偶膜以及Au焊盘膜的附着力。该低能Ar离子束的离子能量Ei=400eV,离子束流密度Jb=0.35mA/cm2。三、沉积NiCr正极热电偶膜:1、旋转六靶台24选择NiCr靶材;在基片1上制作正极热电偶膜光刻胶。2、关闭工件台的挡板20,用主离子源21产生的低能Ar离子束轰击NiCr靶材表面3min,去除靶材表面杂质。该低能Ar离子束的离子能量Ei=400eV,离子束流密度为Jb=0.35mA/cm2;3、打开工件台的挡板20,用主离子源21产生的高能Ar离子束轰击NiCr靶材,NiCr靶材溅射出来的粒子沉积在基片1上,生成NiCr正极热电偶膜。该高能Ar离子束的离子能量Ei=700eV,离子束流密度为Jb=0.55mA/cm2。四、沉积NiSi负极热电偶膜:1、旋转六靶台24选择NiSi靶材;清除工件上剩余的光刻胶,在基片1上制作负极热电偶膜光刻胶。2、关闭工件台的挡板20,用主离子源21产生的低能Ar离子束轰击NiSi靶材表面3min,去除靶材表面杂质。该低能Ar离子束的离子能量Ei=400eV,离子束流密度为Jb=0.35mA/cm2;3、打开工件台的挡板20,用主离子源21产生的高能Ar离子束轰击NiSi靶材,NiSi靶材溅射出来的粒子沉积在基片1上,生成NiSi负极热电偶膜。该高能Ar离子束的离子能量Ei=700eV,离子束流密度为Jb=0.55mA/cm2。五、沉积Au焊盘膜1、旋转六靶台24选择Au靶材,清除工件上剩余的光刻胶,在工件上制作焊盘膜光刻胶。2、关闭工件台的挡板20,用主离子源21产生的低能Ar离子束轰击Au靶材表面3min,去除靶材表面杂质。该低能Ar离子束的离子能量Ei=400eV,离子束流密度Jb=0.35mA/cm2。3、打开工件台的挡板20,用辅离子源26产生的低能Ar离子束轰击工件台3min,增强现有薄膜表面附着力。该低能Ar离子束的离子能量Ei=400eV,离子束流密度Jb=0.35mA/cm2。4、用主离子源21产生的高能Ar离子束轰击Au靶材,Au靶材溅射出来的粒子沉积在NiCr正极热电偶膜和NiSi负极热电偶膜的外接端上,生成Au焊盘膜。该高能Ar离子束的离子能量Ei=700eV,离子束流密度Jb=0.55mA/cm2。六、沉积Ta2O5绝缘过渡膜:1、旋转六靶台24选择Ta靶材;清除工件上剩余的光刻胶,并制作绝缘过渡膜光刻胶。2、关闭工件台的挡板20,用主离子源21产生的低能Ar离子束轰击Ta靶材表面3min,去除靶材表面杂质。该低能Ar离子束的离子能量Ei=400eV,离子束流密度为Jb=0.35mA/cm2。3、打开工件台的挡板20,用主离子源21产生的高能Ar离子束轰击Ta靶材,Ta靶材溅射出来的粒子与辅离子源26产生的O2离子束发生反应,形成Ta2O5化合物沉积在薄膜热电偶及薄膜热电偶所在基片区域表面上,生成Ta2O5绝缘过渡膜。该高能Ar离子束的离子能量Ei=700eV,离子束流密度为Jb=0.55mA/cm2。七、沉积SiO2保护膜:1、旋转六靶台24选择SiO2石英玻璃靶材;清除工件上剩余的光刻胶,并制作保护膜光刻胶。2、关闭工件台的挡板20,用主离子源21产生的低能Ar离子束轰击SiO2靶材表面3min,去除靶材表面杂质。该低能Ar离子束的离子能量Ei=400eV,离子束流密度为Jb=0.35mA/cm2。3、打开工件台的挡板20,用辅离子源26产生的低能Ar离子束轰击工件台3min,增强Ta2O5绝缘过渡膜表面附着力。该低能离子束的离子能量Ei=400eV,离子束流密度为Jb=0.35mA/cm2。4、用主离子源21产生的高能Ar离子束轰击SiO2靶材,靶材溅射出来的粒子形成SiO2化合物沉积在Ta2O5绝缘过渡膜上,形成SiO2保护膜。该高能Ar离子束的离子能量Ei=700eV,设置离子束流密度Jb=0.55mA/cm2。5、打开真空仓29,取出工件台28,清除工件表面剩余的光刻胶,制成薄膜温度传感芯片。本发明采用的双离子束反应溅射沉积(DoubleIonBeanReactiveSputteringDeposition,简称DIBRSD)技术,是先用低能量的工作气体离子束对靶材和衬底进行清洗,以充入工作气体的主离子源产生的主离子束轰击靶材,靶材溅射出来的粒子与充入反应气体的辅离子源产生的辅离子束进行化学反应,产生稳定的化合物沉积在衬底上,生成化合物薄膜。其具有以下显著特点:1、薄膜的均匀度好,薄膜的应力小且附着力高,光学性质更加重复稳定;工作参数独立控制自由度大,可以纳米级控制薄膜生长、薄膜微结构和薄膜晶格取向;2、靶材粒子能量高,沉积的薄膜膜层密度高、杂质少,与衬底的结合力高;对靶材和衬底进行预清洗,能提高薄膜和衬底的附着力;3、适用除有机材料和易分解材料以外的众多材料,无环境污染干法镀膜,可制备合金薄膜、氧化物薄膜、高熔点薄膜和绝缘薄膜。因此,采用六靶台双离子束反应溅射沉积技术,制成的高性能薄膜温度传感芯片体积小、精度高、响应时间快、温漂小、稳定性好、可靠性高、使用寿命长、抗振抗扰抗冲击能力强,适用于恶劣环境,并且制作工艺简单,不用高温老化,生产时间短,综合指标优于磁控溅射制备的同类产品。最后应说明的是:以上实施例仅用以说明本发明的技术方案,而非对其限制;尽管参照前述实施例对本发明进行了详细的说明,本领域的普通技术人员应当理解:其依然可以对前述各实施例所记载的技术方案进行修改,或者对其中部分技术特征进行等同替换;而这些修改或者替换,并不使相应技术方案的本质脱离本发明各实施例技术方案的精神和范围。当前第1页1 2 3