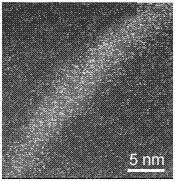
本发明涉及燃料电池领域,特别涉及聚合物电解质膜燃料电池中离子交换膜的处理方法。
背景技术:
:燃料电池作为一种将化学能转换为电能的特殊装置,由于具有能量转换效率高、低污染、储能物质选择范围宽、低噪音等多种其他能量发生装置不可比拟的优越性,被认为是最有希望的、环境友好的新型化学电源之一。其中,聚合物电解质膜燃料电池具有快速启动和对负荷变化的快速响应等优点,受到越来越多的关注,成为了最近的研究热点。聚合物电解质膜燃料电池以聚合物电解质膜为固体电解质,起到分割阴阳两极及传导质子(h+)或氢氧根离子(oh-)的作用,是聚合物电解质燃料电池中的一个关键部件。聚合物电解质膜的性能好坏对聚合物电解质膜燃料电池的发电性能起到了决定性的作用,因而高性能聚合物电解质膜的研究与开发就显得尤为重要。聚合物电解质膜燃料电池通常根据传导离子的不同,可分为使用质子交换膜的酸性聚合物电解质膜燃料电池和使用碱性阴离子交换膜的碱性聚合物电解质膜燃料电池。目前,商业化的质子交换膜如美国杜邦公司生产的全氟磺酸(nafion)膜,由于具有高导电率、优良的化学、电化学及机械稳定性,是目前商业应用于燃料电池中最多的聚合物电解质膜。但是nafion膜制备工艺复杂、价格高昂、制备过程对环境造成危害、必须使用贵金属催化剂等问题,限制了质子交换膜燃料电池进一步的商业化使用。而另一方面,相对于质子交换膜燃料电池,碱性阴离子交换膜燃料电池具有一系列独特优点:由于其碱性环境,燃料电池具有更快的反应动力学、可以使用非贵金属催化剂以及便于运输的甲醇或乙醇等有机燃料。直接硼氢化钠燃料电池是直接利用硼氢化钠水溶液为燃料,氧或空气作为氧化剂的一种新型燃料电池。它的工作原理是:在阳极区,负极活性物质硼氢化钠水溶液经阳极流场板均匀分配后,通过阳极扩散层扩散并进入阳极催化层中(即阳极电化学活性反应区域),在碳载铂电催化剂的作用下发生电化学氧化反应,生成质子、电子和偏硼酸根。产生的质子通过全氟磺酸膜聚合物电解质迁移到阴极,电子通过外电路传递到阴极,偏硼酸根从阳极出口排出;阴极区,正极活性物质氧气或空气经阴极流场板均匀配后,通过阴极扩散层扩散并进入阴极催化层中(即阴电化学活性反应区域),在碳载铂电催化剂的作用下与从阳极迁移过来的质子发生电化学还原反应生成水随反应尾气从阴极出口排出。其电极反应如下:阳极反应:bh4-+2h2o→bo2-+8h++8e;阴极反应:2o2+8h++8e→4h2o;总反应:bh4-+2o2→bo2-+2h2o。硼氢化钠在室温下为液态,具有很高的能量密度。然而燃料渗透是影响直接硼氢化钠燃料电池性能的关键问题。当硼氢化钠透过膜到阴极后,会产生混合电势降低电池总电压损害电池发电效率。专利(公开号105884948a)公开了一种阻断甲醇渗透的燃料电池阴离子膜,采用异丁烯、1-氯异戊烯和交联单体2-三氟甲基-6-甲基-5-庚烯乙酸酯,经过阳离子预聚、胺化、季铵化、脱水烯键,最后自由基聚合致密交联为聚异丁烯阴离子膜。由于是饱和的叔烷基主链,不会强碱降解。具有优异的耐碱性和甲醇阻断能力,室温膜电导率能达到≥80ms/cm。专利(公开号105826584a)采用在nafion中参杂磺化石墨烯的方法,降低nafion膜的甲醇渗透率。专利(授权号zl03137306.2)公开了属于燃料电池材料制备技术范围的用于直接甲醇燃料电池的含磺酸侧基的芳杂环聚合物与无机材料进行掺杂制备质子交换膜的一种抗甲醇渗透质子交换膜的制备方法。将膜基体含磺酸侧基的芳杂环聚合物加到溶剂中,形成均匀混合物后,加入无机物,形成悬浮物。通过纳米破碎技术对该悬浮物进行破碎,得到分散均匀的浆料,用浇注法制膜。其形成的膜结构均匀、相当致密。它不但能良好地抗甲醇渗透,还具有良好的化学稳定性和质子传导性,甲醇渗透率小于5%。如上所述,目前已有一些关于降低甲醇渗透率的离子交换膜制备方法,然而关于降低硼氢化钠燃料渗透率的离子交换膜处理方法鲜有报道。甲醇渗透机理与硼氢化钠渗透机理不同,前者是分子扩散,后者是离子传导。适用于降低甲醇渗透率的方法不一定适用于硼氢化钠体系。因此很有必要开发一种降低硼氢化钠渗透率的离子交换膜处理方法。技术实现要素:针对上述所提及的现有技术中离子交换膜存在的问题,本发明旨在提供一种降低硼氢化钠渗透率的离子交换膜处理方法。本发明提供了一种降低离子交换膜对硼氢化钠燃料渗透原位处理离子交换膜的方法,包括如下步骤:(1)将离子交换膜与电极、流场、夹板等部件组装电池,先不通入燃料和氧气,而是先在阴极通入过渡金属盐溶液,并保持过渡金属盐溶液填满阴极流场5~30分钟,使过渡金属盐中的过渡金属离子渗入离子交换膜中的微孔道,之后排空该过渡金属盐溶液;(2)然后在阳极通入硼氢化钠溶液,在阴极通入氧气,即可正常启动电池工作,对外发电。其中优选步骤(1)中的过渡金属盐溶液浓度为1m~5m。其中优选过渡金属盐为氯化钴、氯化铜、硫酸钴或氯化铁。本发明的核心思路是:目前无论何种离子交换膜均存在燃料渗透问题,其根本原因是高分子聚合膜基体无可避免地存在微孔道,如果能够堵住这些微孔道,则可以显著减少燃料渗透。在阴极预先通入过渡金属盐溶液使过渡金属离子吸附扩散在膜微孔道内,之后当阳极通入硼氢化钠燃料时,硼氢化钠也将通过微孔道企图渗透到阴极。当硼氢化钠与过渡金属离子相遇时将反应生成不可溶的过渡金属硼化物从而将过渡金属离子固定在微孔道内并堵塞住微孔道使后续硼氢化钠无法继续渗透,实现降低渗透率效果。本发明的技术关键是:过渡金属离子渗入膜微孔道的量。如果渗入微孔道的过渡金属离子含量不足则在后续反应中无法生成足够的硼化物完全填充微孔道以达到降低渗透率效果。本发明通过控制过渡金属盐溶液浓度和渗透时间来保障渗入膜微孔道的离子含量。本发明的有益效果:1)根据本发明处理的离子交换膜由于过渡金属离子阻塞了微孔道而显著降低燃料渗透率,从而避免了渗透的燃料在阴极产生混合电势降低电池电压,保障电池发挥出优良的性能;2)本发明的处理方法简便易行,且是原位进行,无需精密设备,容易实现。附图说明图1为未处理前离子交换膜横截面微孔道附近的碳元素面分布的能谱测试结果,图片中白亮点表示碳元素信号点。图2为使用实施例1所处理的离子交换膜横截面微孔道附近的钴元素面分布的能谱测试结果,图片中白亮点表示钴元素信号点。具体实施方式目前无论何种离子交换膜均存在燃料渗透问题,其根本原因是作为离子交换膜的高分子聚合膜基体无可避免地存在微孔道,如附图1为目前常规使用的离子交换膜(未经过本发明处理方法处理)的横截面微孔道附近的碳元素面分布的能谱测试结果,图片中白亮点表示碳元素信号点,从这个测试结果反映出微孔道的在离子交换膜中普遍存在。下面通过具体的实施例对本发明做进一步的说明。实施例1:(1)将离子交换膜与电极、流场、夹板等部件组装电池,先不通入燃料和氧气而是先在阴极持续通入5m浓度的氯化钴溶液并保持溶液填满阴极流场5分钟,之后排空该氯化钴溶液;(2)然后在阳极通入硼氢化钠溶液,在阴极通入氧气,即可正常启动电池工作,对外发电。实施例2:与实施例1的区别在于步骤(1)中氯化钴为氯化铜替代,其他参数相同。实施例3:与实施例1的区别在于步骤(1)中氯化钴为硫酸钴替代,其他参数相同。实施例4:与实施例1的区别在于步骤(1)中氯化钴为氯化铁替代,其他参数相同。实施例5:与实施例1的区别在于步骤(1)中氯化钴的浓度为1m,保持时间为30分钟,其他参数相同。对比例1:与实施例1的区别:步骤(1)中保持时间为1分钟,其他参数相同。对比例2:与实施例1的区别:步骤(1)中氯化钴浓度为0.1m,其他参数相同。对比例3:与实施例1的区别:不包含步骤(1),其他参数相同。上述实施例和对比例所用电池有效面积为6cm2,阳极使用ni-pd催化剂,担载量为10mg/cm2,阴极使用pt/c催化剂,担载量为5mg/cm2,硼氢化钠溶液为5wt.%nabh4和10wt.%naoh混合水溶液,氧化剂为纯氧气,压力为0.2mpa,测试温度为30摄氏度。通过测试不同放电电流下的电压获得电池最大输出功率密度。通过恒电流放电,测试电池电压随时间的变化从而评价电池性能衰减率。具体各测试获得的实验结果如表1所示。此外,将实施例1的离子交换膜取出超薄切片并用透射电镜配合能谱仪测试膜横截面的过渡金属离子分布,如附图2所示。表1各实施例和对比例原位处理后的电池最大输出功率密度,衰减率和开路电压。样品开路电压(v)最大输出功率密度(mw/cm2)衰减率(300ma持续放电24小时)实施例11.12893.2实施例21.15923.5实施例31.10883.1实施例41.26933.5实施例51.13903.7对比例11.07677.4对比例21.05718.6对比例31.02659.4从表1的开路电压可以看出,经本发明处理后的电池开路电压普遍高于对比例的开路电压,这正是得益于本发明所提出的自阻塞效应思路使得燃料难以再通过膜微孔道渗透到阴极而降低电池开路电压。同时本发明处理后的电池电压衰减率也低于对比例的衰减率,这是由于本发明所提出的自阻塞效应思路降低了燃料渗透,减弱了对阴极的损害效应,保障了电池性能稳定。由于渗透被抑制,一方面使电池总电压较高,另一方面电池性能稳定,从而保障电池发挥出良好的发电性能,因此本发明的实施例所获得的最大功率密度显著高于对比例。从实施例1~4可见常见的过渡金属离子均能与硼氢化钠反应生成不溶的硼化物产生自堵塞效果,而不同的阴离子对于该处理方法影响不大。从实施例1,5与对比例1,2的对比可见,过渡金属离子的渗透程度很关键,过渡金属盐浓度太低或者处理时间太短均无法达到充分的自堵塞效果。从实施例1~5与对比例3的对比可见,相比于对比例3所示的电池直接测试,在测试前增加本发明所提出的步骤(1)能够显著改善电池性能。当前第1页12