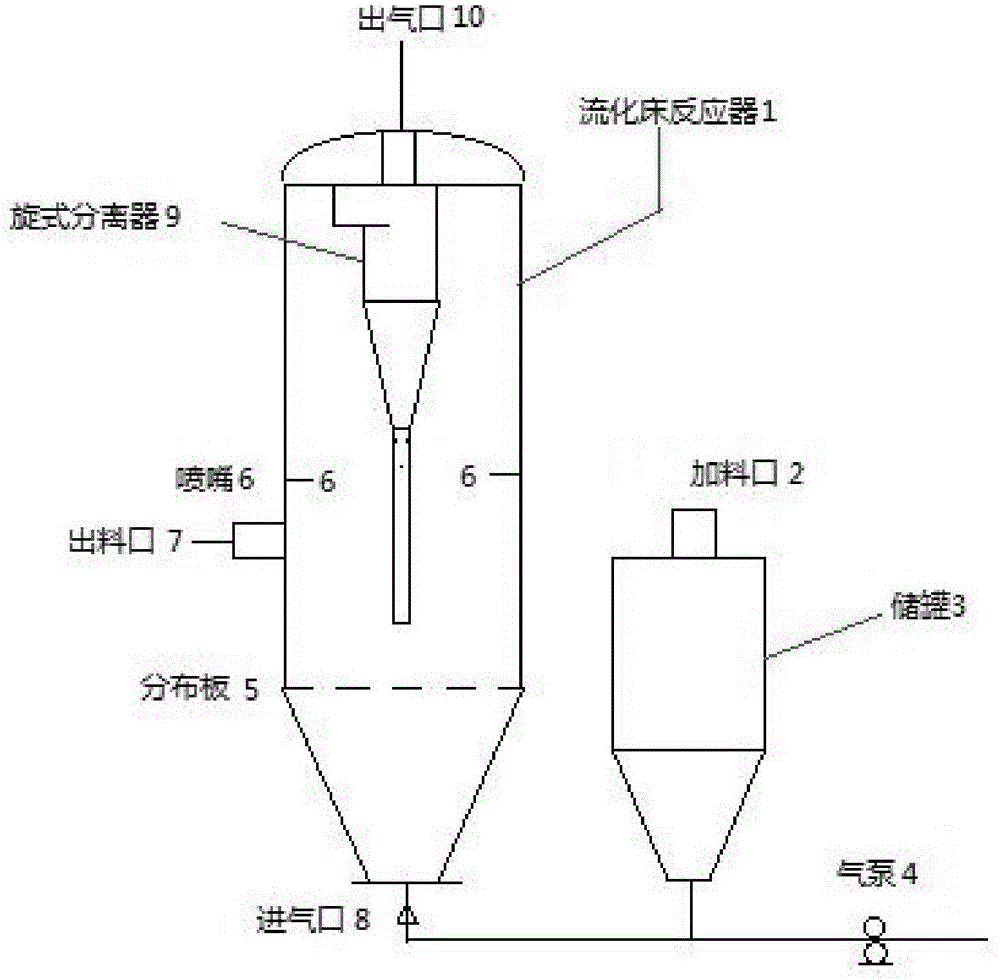
本发明属于锂离子电池
技术领域:
,涉及一种包覆改性电极材料及其制备方法,尤其涉及一种包覆改性电极材料,及先采用流化床将包覆材料前驱体和电极材料混合,再烧结制备包覆改性电极材料的方法。
背景技术:
:锂离子电池能量密度高、输出功率大,绿色环保对环境友好,不含有铅、镉、汞等有毒物质,在新能源汽车、储能方面有着广泛的应用前景。随着锂离子电池应用的快速发展,人们对锂电池的容量、循环性能、安全性能、倍率性能要求越来越高。锂电池正极材料的体相和表面相结构稳定性是影响锂电池循环性能的重要因素,如何提高正极材料的结构稳定性也成为了锂电池领域的研究热点。目前的研究结果表明,影响锂离子电池正极材料安全性和充放电循环稳定性的重要原因包括:充电态正极材料晶格失氧及相变、电解液的氧化分解反应、过渡金属离子在电解液中的溶出以及电解液副反应产生的hf对正极材料的腐蚀等。表面包覆能够有效减缓以上反应,从而提升正极材料的安全性和循环性能。cn201210221966.9公开了一种通过共沉淀法在正极材料表面包覆一层纳米氧化铝的制备方法;cn106684358a公开了一种通过溶胶凝胶法在富锂正极材料表面包覆氧化铝的改性方法。液相包覆法虽然能够在正极材料表面均匀的包覆一层金属氧化物,提升正极材料的循环性能,但是工艺复杂、处理成本较高。原子层沉积(ald)包覆方法可以实现1nm-2nm厚包覆层的均匀包覆,性能优异,但对设备和原料要求高,成本高,也不利于工业化生产。cn201710099667.5公开了一种通过气流磨的高速撞击流的方式将包覆液与正极材料进行混合得到包覆材料前驱体。这种包覆方法虽然在一定程度上能在降低包覆液的使用量的同时提高工作效率,但是高速撞击本身会对正极材料的表面包覆层造成破坏,影响材料性能。因而,有必要提供一种简单、低成本地制备包覆改性电极材料的方法,以得到均匀包覆效果,并大幅改善电极材料的循环性能。技术实现要素:针对现有技术中存在的上述问题,本发明的目的在于提供一种包覆改性电极材料及其制备方法。采用本发明的方法先将包覆材料前驱体与流态化的电极材料混合和包覆,可以在实现流态化混合的同时能提升包覆均匀性,还可以简化包覆流程,降低包覆工艺的成本。第一方面,本发明提供一种包覆改性电极材料的制备方法,所述方法先通过流化床的喷嘴向流化床反应器中喷入包覆液,与处于流态化的电极材料混合,实现包覆材料前驱体对电极材料的包覆,然后进行烧结,得到由电极材料及包覆在电极材料表面的包覆材料构成的包覆改性电极材料。流化床反应器是实现流态化过程的设备,本发明通过流化床反应器使喷入的包覆液(即包覆材料前驱体的溶液、溶胶或悬浮液)与流态化的电极材料发生作用,实现包覆材料前驱体与电极材料的混合,使包覆材料前驱体均匀地包覆在电极材料的表面,在保持包覆均匀性的同时,简化包覆流程,降低包覆工艺成本。作为本发明所述方法的优选技术方案,所述电极材料为正极材料或负极材料中的任意一种,优选正极材料,进一步优选三元镍钴锰酸锂、镍钴铝酸锂、镍钴酸锂、镍锰酸锂、钴酸锂、锰酸锂、磷酸铁锂、磷酸锰锂、磷酸锰铁锂以及上述对应的正极材料经过掺杂改性所得正极材料中的任意一种或至少两种的组合。优选地,所述流态化为散式流态化,也即平稳床。优选地,所述包覆液为包覆材料前驱体的溶液、溶胶或悬浮液中的任意一种,所述溶液、溶胶或悬浮液中的溶剂是有机溶剂或水。优选地,所述溶液、溶胶或悬浮液中的溶质为纳米金属氧化物、纳米非金属氧化物、纳米金属氢氧化物、纳米非金属氢氧化物、金属盐或非金属盐中的任意一种或至少两种的组合,优选包括纳米氧化铝、纳米氧化镁、纳米氢氧化铝、纳米氢氧化镁、纳米碳酸镁、纳米氧化钛、纳米氢氧化钛、纳米氧化锆、纳米氢氧化锆、纳米氧化钼、纳米氢氧化钼、纳米氧化钨、纳米氢氧化钨、纳米二氧化硅、纳米氧化硼、纳米五氧化二磷、纳米磷酸铝、磷酸氢二铵、磷酸二氢铵、硅酸盐或硼酸盐中的任意一种或至少两种的组合。优选地,所述包覆液为包覆材料前驱体对应的金属有机脂的有机溶液,纳米金属氧化物的悬浮分散液,纳米金属氢氧化物的悬浮分散液,纳米非金属氧化物悬浮溶液,或非金属化合物的溶液中的任意一种。优选地,所述包覆材料前驱体对应的金属有机脂的有机溶液中,金属有机脂中的包覆元素包括al、mg、zr、ti、mn、la、mo、w、si、b或p中的任意一种或至少两种的组合。优选地,所述包覆材料前驱体对应的金属有机脂的有机溶液中,作为溶质的金属有机脂为金属脂类有机物,优选包括异丙醇铝、钛酸丁酯、钛酸乙酯、硬脂酸铝、柠檬酸铝、异丙醇锆或含mo和w的有机化合物中的任意一种或至少两种的组合。优选地,所述包覆材料前驱体对应的金属有机脂的有机溶液中,作为溶剂的有机溶剂包括四氢呋喃、无水甲醇、乙醇、异丙醇、正丁醇、叔丁醇或异丁醇中的任意一种或至少两种的组合。优选地,所述包覆材料前驱体对应的金属有机脂的有机溶液中还包含润湿剂,所述润湿剂为二甲基硅油。优选地,所述包覆材料前驱体对应的金属有机脂的有机溶液中,溶质的质量分数为0.01wt%~30wt%,例如0.01wt%、0.05wt%、0.1wt%、0.3wt%、0.6wt%、1wt%、2wt%、3wt%、5wt%、8wt%、12wt%、15wt%、20wt%、22wt%、25wt%、27.5wt%或30wt%等。优选地,所述纳米金属氧化物或氢氧化物的悬浮分散液的质量分数为0.01wt%~30wt%,例如0.01wt%、0.05wt%、0.1wt%、0.3wt%、0.6wt%、1wt%、2wt%、3wt%、4wt%、5wt%、8wt%、10wt%、12wt%、15wt%、20wt%、22wt%、25wt%、27.5wt%或30wt%等。优选地,所述包覆液中金属氧化物或非金属氧化物的质量占包覆改性后的电极材料的质量比为0.01%~5%,例如0.01%、0.05%、0.1%、0.2%、0.5%、1%、1.5%、2%、2.5%、3%、3.2%、3.6%、4%、4.5%或5%等。作为本发明所述方法的优选技术方案,所述烧结的温度为200℃~900℃,例如200℃、240℃、300℃、325℃、350℃、400℃、450℃、500℃、550℃、580℃、620℃、650℃、700℃、750℃、800℃或900℃等。优选地,所述烧结的时间为2h~10h,例如2h、3h、3.5h、4h、5h、6h、6.5h、7h、8h、9h或10h等。优选地,所述烧结采用的设备为电极材料烧结设备,优选为箱式炉、辊道窑、推板窑或回转炉中的任意一种。优选地,所述烧结的气氛为干燥的压缩空气气氛或氧气气氛中的任意一种或两种的混合气氛。作为本发明所述方法的优选技术方案,所述流化床包括流化床反应器、进料口、储罐、气泵、气体分布板、喷嘴、出料口、进气口、分离器和出气口;其中,所述流化床反应器的进气口通过管道与气泵连接,所述进气口和气泵之间的管道上设置有储罐并通过储罐的出口连接,所述储罐顶部设置有加料口;所述气体分布板位于流化床反应器的下部,所述分离器位于流化床反应器的上部且与位于流化床反应器顶部的出气口连通,所述喷嘴设置在流化床反应器的侧壁、顶部或底部的任一位置,所述出料口设置在流化床反应器的侧壁上。采用此优选技术方案的流化床中,进气口和气泵之间的管道上设置有储罐,这样连通的目的是使从储罐中排出的物料在气泵产生的气流的作用下运送至流化床反应器的进气口达到气力输送物料的目的。流化床在使用过程中可能会出现腾涌、沟流和局部不流化等非正常流化现象,本发明通过设计一种气体分布板,能够有效地减少非正常流化现象的影响。优选地,所述气体分布板的形状与流化床反应器的截面形状相同,固定在流化床反应器的侧壁上。优选地,所述气体分布板的未打孔部位沿垂直板面方向增高使其形成凸起,所述凸起的形状优选为锥形,所述锥形可以是规则的锥形,也可以是不规则的类锥形。形成的凸起可以避免物料在未打孔部位堆积形成死区。优选地,所述气体分布板的开孔率为20%~80%,例如20%、25%、30%、32%、35%、40%、45%、50%、55%、60%、65%、70%或80%等。优选地,所述气体分布板上的气孔从圆心往外径向方向孔径依次逐渐增大。优选地,所述气体分布板的气孔围绕圆心成环状均匀分布,成环的气孔数量沿径向依次增加。本发明通过设计气孔从圆心往外径向方向孔径依次逐渐增大,同时未打孔部位沿垂直板面方向增高使其形成凸起,达到平衡气流分布从而减弱不利于粉体均匀混合的非正常流化现象(包括腾涌、沟流和局部不流化)的产生及分布板孔被堵塞。优选气孔围绕圆形成环状均匀分布,成环的气孔数量沿径向依次增加,可以更好地达到上述效果。作为本发明所述流化床的优选技术方案,所述喷嘴内设喷雾管道和载气管道,所述载气管道环绕在喷雾管道外周。在使用时,包覆液(比如包覆材料前驱体溶液、溶胶或悬浮液)从中间的管道以一定的速度喷出形成喷雾,中间管道周围通入的载气以一定速度将喷雾液吹入流化床反应器中,与流化态的物料进行接触混合,这样可以避免物料在喷嘴处聚集粘结。优选地,所述喷嘴的个数为至少2个,例如2个、3个、4个、5个、6个、7个、8个、9个或10个等。优选地,所述喷嘴的个数为偶数,且成对地设置在流化床反应器同一高度且对侧的侧壁上。作为本发明所述流化床的优选技术方案,所述分离器为旋式分离器。本发明的流化床中,分离器的作用是避免物料随气流离开流化床反应器,采用旋式分离器可更好地达到此效果。优选地,所述流化床还包括依次与出气口连接的气体分离系统和回收系统。优选地,所述分离系统和回收系统之间还设置有除湿系统。优选地,所述流化床还包括依次与出气口连接的除湿系统,除湿之后气体直接循环再利用。优选地,所述流化床还包括控制系统,所述控制系统分别与出气口、进料口和出料口连接。通过引入控制系统,可以实现进出料的自动化。本发明利用流化床可以实现电极材料的流态化,并解决了非正常流化现象的影响,以及工作时喷嘴被堵塞的问题,从喷嘴喷出包覆液(包覆材料前驱体溶液、溶胶或悬浮液)使包覆材料前驱体与电极材料在流化床内的高效混合,这种动态混合能够有效地提升包覆的均匀性,包覆材料前驱体均匀地包覆在电极材料的表面,而且还降低了溶剂的使用量。本发明的流化床可以实现包覆完成后得到的包覆颗粒(即包覆材料前驱体包覆电极材料形成的包覆颗粒)的半连续动态进出料,能够提高包覆材料前驱体与正极材料混合均匀性,提升包覆效果。作为本发明所述方法的进一步优选技术方案,所述方法包括以下步骤:(a)将电极材料从加料口加入储罐中,气体流通过气泵将物料从进气口送入流化床反应器并通过气体分布板;(b)调整气体流的气速,气体流稳定后实现电极材料在流化床反应器中的流态化;(c)将包覆液通过喷嘴喷雾加入到流化床反应器中,与处于流态化的电极材料混合,实现包覆材料前驱体对电极材料的包覆,得到包覆颗粒;气体流和包覆液中的溶剂蒸汽通过分离器(9)与包覆粉体分离并从出气口(10)流出;(d)喷雾结束后关闭出气口,打开出料口,增大气体流的气速,通过气体流将包覆粉体从流化床反应器中带出,在出料口处收集;(e)对收集得到的包覆粉体进行烧结,得到包覆改性电极材料。本发明的方法中,步骤(c)所述包覆液为一定浓度的包覆材料前驱体的溶液、溶胶或悬浮液。本发明的方法中,步骤(a)、(b)和(d)均涉及到控制气体流的气速的步骤,气体流的气速是通过气泵控制的。根据使用的气体流气速不同,流化态的形态也不同,流化态的形态根据气体流的气速从低到高分别有聚式流态化(即鼓泡床)、散式流态化(即平稳床)、扬析(即气力输送)。更具体地,要实现上述三种状态,分别需要进行如下气速控制:实现物料的聚式流态化对应的气体流气速范围在0.01m/s~0.3m/s,例如0.01m/s、0.05m/s、0.07m/s、0.1m/s、0.15m/s、0.2m/s、0.25m/s或0.28m/s等。实现物料的散式流态化对应的气体流气速范围在0.3m/s~1.5m/s,例如0.3m/s、0.35m/s、0.4m/s、0.5m/s、0.6m/s、0.65m/s、0.7m/s、0.8m/s、0.85m/s、0.9m/s、1m/s、1.1m/s、1.15m/s、1.2m/s、1.3m/s、1.4m/s或1.5m/s等。实现物料的扬析对应的气体流气速范围在1.5m/s~15m/s,例如1.6m/s、1.8m/s、2m/s、2.5m/s、3m/s、4m/s、4.5m/s、5.5m/s、6m/s、7m/s、7.5m/s、8m/s、9m/s、9.5m/s、10m/s、10.5m/s、11m/s、12m/s、12.5m/s、13m/s、14m/s或15m/s等。本发明的方法中,步骤(a)和(d)控制气体流的气速的目的是实现气力输送,也就是扬析;需要注意的是,步骤(a)的目的虽然也是气力输送,但其气体流的气速不能过大,若超过5m/s会导致物料从出口吹出,因此,应控制气速在5m/s以下以避免物料从出口吹出流化床反应器。本发明的方法中,步骤(b)控制气体流的气速的目的是实现平稳床,也就是散式流态化。作为本发明所述处理方法的优选技术方案,步骤(a)所述气体流的气速为1.5m/s~5m/s,例如1.6m/s、1.8m/s、2m/s、2.5m/s、2.7m/s、3m/s、3.5m/s、3.7m/s、3.8m/s、4m/s、4.2m/s、4.5m/s、4.7m/s、4.8m/s或5m/s等。优选地,步骤(a)所述气体流为压缩气流,优选为除杂干燥的压缩空气。优选地,步骤(b)调整气体流的气速至0.3m/s~1.5m/s,例如0.3m/s、0.5m/s、0.6m/s、0.7m/s、0.8m/s、1m/s、1.2m/s、1.3m/s、1.4m/s或1.5m/s等。优选地,步骤(c)还包括在喷雾的同时,从喷嘴6内设的载气通道通入载气的步骤。在此条件下,从出气口10流出的气体中还包含载气。优选地,步骤(d)增大气体流的气速至大于步骤(b)调整后的气速,且在1.5m/s~15m/s,例如1.8m/s、2m/s、2.5m/s、3m/s、4m/s、5m/s、5.5m/s、6.5m/s、8m/s、9m/s、10m/s、12m/s、13m/s或15m/s等。作为本发明所述处理方法的优选技术方案,从出气口10流出的气体依次进入气体分离器和回收系统,实现再利用。作为本发明所述处理方法的又一优选技术方案,从出气口10流出的气体依次进入气体分离系统、除湿系统和回收系统,循环再利用。本发明的方法中,从出气口10流出的气体也可以直接经过除湿系统除湿后直接循环使用,降低能耗。本发明的方法通过将电极材料气力输送到流化床反应器中,稳定气流后形成散式流态化(平稳床),通过喷嘴将包覆液以超细喷雾的形式加入到流化床反应器中,对电极材料进行包覆,喷雾结束后打开出料口,以气力输送将包覆得到的混合料(即包覆材料前驱体包覆电极材料形成的包覆颗粒)从流化床反应器吹出。该方法不仅可以在动态混合条件下实现包覆材料前驱体对电极材料的均匀包覆,均匀性好,还可以大大混合及包覆的溶剂使用量。本发明的方法混合工艺简单,进出料半自动操作方便,能耗较小。第二方面,本发明提供了一种如第一方面所述方法制备得到的包覆改性电极材料,所述包覆改性电极材料由电极材料及包覆在所述电极材料表面的包覆材料构成。第三方面,本发明提供一种锂离子电池,所述锂离子电池包含第二方面所述的包覆改性电极材料。与已有技术相比,本发明具有如下有益效果:(1)本发明提供了一种包覆改性电极的制备方法,所述制备方法采用流化床反应器实现电极材料(比如正极材料)的流态化,通过向流化床反应器中喷入包覆液,实现包覆材料前驱体与电极材料的混合过程,能够提高包覆材料前驱体与电极材料的混合均匀性,提升包覆效果,还可以实现包覆完成的混合物料的半连续动态进出料,本发明的方法还具有混合工艺简单,能耗小,在保持包覆均匀性的同时,简化了包覆流程,降低包覆工艺的成本,适合工业化生产。(2)作为更优选的技术方案,通过对流化床反应器、储罐、气泵、分离器、气体分布板和喷嘴等的设计,并通过气泵控制入料、流态化形态以及出料,解决了非正常流化现象的影响,工作时喷嘴被堵塞以及采用该流化床制备包覆型复合材料时包覆均匀性差的问题。(3)采用本发明的流化床实现电极材料与包覆材料前驱体的混合和包覆,以气力输送的方式向流化床反应器中进料,通过散式流态化(平稳床)进行包覆液与电极材料的混合,混合工作完成后打开出料口,调整气速,使反应器内材料的流化状态达到气力输送的程度,将混料(即包覆材料前驱体包覆电极材料形成的包覆颗粒)从反应器中输出,收集包覆完成的混合料继续烧结,得到包覆改性电极材料;再进行下一次混料操作,从而实现半连续的包覆操作,借助自动化程序和控制开关还可以做到包覆以及进出料的全自动操作。附图说明图1为实施例1的流化床的结构示意图,其中,1-流化床反应器,2-进料口,3-储罐、4-气泵、5-气体分布板、6-喷嘴、7-出料口、8-进气口、9-旋式分离器,10-出气口;图2为实施例1的流化床的喷嘴结构示意图;图3为实施例1的流化床的气体分布板截面俯视图;图4为实施例1、实施例2和对比例1的循环性能对比图。具体实施方式下面结合附图并通过具体实施方式来进一步说明本发明的技术方案。采用各实施例的包覆改性正极材料以及对比例中的正极材料打浆制作极片,组装2032扣式电池,电池中材料的重量比例为正极材料:sp:pvdf=96:2:2,采用金属锂片为负极,充放电电压范围3.0v-4.3v,测试常温25℃条件下0.5c循环结果。实施例1:本实施例提供一种流化床及采用该流化床先将包覆材料前驱体与正极材料混合,然后再烧结制备包覆改性电极材料的方法。(一)、所述流化床的结构示意图如图1所示,包括流化床反应器1、进料口2、储罐3、气泵4、气体分布板5、喷嘴6、出料口7、进气口8、旋式分离器9和出气口10;其中,所述流化床反应器1的进气口8通过管道与气泵4连接,所述进气口8和气泵4之间的管道上设置有储罐3并通过储罐3的出口连接,所述储罐3顶部设置有加料口2;所述气体分布板5的形状与流化床反应器1的截面形状相同,固定在流化床反应器1的侧壁上。所述气体分布板5的未打孔部位沿垂直板面方向增高使其形成锥形,以避免物料在未打孔部位堆积形成死区,所述分离器9位于流化床反应器1的上部且与位于流化床反应器1顶部的出气口10连通,两个喷嘴6和出料口7设置在流化床反应器1同一高度且对侧的侧壁上,所述出料口7设置在流化床反应器1的侧壁上;所述气体分布板5的结构示意图参见图2,气体分布板5的形状为圆形,且其上的气孔从圆心往外径向方向孔径依次逐渐增大;所述喷嘴6的结构俯视图参见图3,喷嘴6内设喷雾管道和载气管道,所述载气管道环绕在喷雾管道外周;所述分离器9为旋式分离器。(二)、制备包覆改性电极材料(具体为氧化铝包覆的正极材料)的方法,包括如下步骤:1、包覆液购买的固含量10%的纳米氧化铝的异丙醇分散液。2、包覆过程(a)称取1000g镍钴锰三元523正极材料从加料口2加入储罐3中,初始速度1.5m/s的压缩空气通过气泵4将正极材料从进气口8送入流化床反应器1,并通过气体分布板5;(b)调节气体流速为0.7m/s,使正极材料在流化床反应器1中形成平稳床(散式流态化);(c)待流化床反应器1中的正极材料呈散式流化态稳定后,将100g上述包覆液通过喷雾嘴6进行超细喷雾送入流化床反应器1,且从喷嘴6内设的载气管道中以一定速度通入载气将喷雾液吹入流化床反应器1中;气体流、载气和包覆液中的溶剂蒸汽通过分离器与包覆粉体分离,气体从出气口10流出;(d)待喷雾结束后,关闭出气口10,打开出料口7,增大气速至3m/s,通过气体流将包覆粉体(即正极材料及包覆在正极材料表面的包覆材料形成的包覆粉体)从流化床反应器中带出,在出料口7处收集喷出的混合物料(即包覆粉体);3、烧结收集到的混合物料在箱式炉中进行烧结,气氛为干燥的氧气,控制流速为0.1m3/min,控制反应器内温度500℃,烧结4h。待箱式炉冷却后取出包覆完成的正极材料(即包覆改性正极材料),粉碎、除铁、真空包装。4、循环性能实施例1中纳米氧化铝包覆三元523材料100次循环后容量保持率100%,没有衰减。实施例2:采用的流化床与实施例1相同,区别在于,制备氧化钛包覆的正极材料,且制备过程如下:1、制备包覆液称取24g钛酸四丁酯、46g无水乙醇、100g二甲基硅油混合制备包覆液。2、包覆过程(a)称取1000g镍钴锰三元523正极材料从加料口2加入储罐3中,初始速度1.7m/s的压缩空气通过气泵4将正极材料从进气口8送入流化床反应器1,并通过气体分布板5;(b)调节气体流速为0.9m/s,使正极材料在流化床反应器1中形成平稳床(散式流态化);(c)待流化床反应器1中的正极材料呈散式流化态稳定后,将170g上述包覆液通过喷雾嘴6进行超细喷雾送入流化床反应器1,且从喷嘴6内设的载气管道中以一定速度通入载气将喷雾液吹入流化床反应器1中;气体流、载气和包覆液中的溶剂蒸汽通过分离器与包覆粉体分离,气体从出气口10流出;(d)待喷雾结束后,关闭出气口10,打开出料口7,增加气速至7m/s,通过气体流将包覆粉体(即正极材料及包覆在正极材料表面的包覆材料形成的包覆粉体)从流化床反应器中带出,在出料口7处收集喷出的混合物料(即包覆粉体);3、烧结收集到的混合物料在箱式炉中进行烧结,气氛为干燥的压缩空气,控制流速为0.1m3/min,控制反应器内温度400℃,烧结3h。待箱式炉冷却后取出包覆完成的正极材料(即包覆改性正极材料),粉碎、除铁、真空包装。4、循环数据实施例2中氧化钛包覆的523材料100次循环后容量保持率94.05%。实施例3采用的流化床、包覆方法及烧结方法与实施例1相同,区别在于制备包覆改性正极材料的过程中:包覆液为硝酸铝溶液,且硝酸铝的质量分数为5wt%;步骤(a)初始速度为2m/s;步骤(b)气体流速为1m/s;步骤(c)气速为6m/s。实施例3包覆后材料100次循环后容量保持率为92.59%。实施例4采用的流化床、包覆方法及烧结方法与实施例1相同,区别在于制备包覆改性正极材料的过程中:包覆液为异丙醇锆的正丁醇溶液,且异丙醇锆的质量分数为15wt%;步骤(a)初始速度为3m/s;步骤(b)气体流速为1.2m/s;步骤(c)气速为4.5m/s。实施例4包覆后正极材料100次循环后容量保持率88.72%。实施例5采用的流化床、包覆方法及烧结方法与实施例1相同,区别在于制备包覆改性正极材料的过程中:包覆液为柠檬酸铝的四氢呋喃溶液,其中包含润湿剂二甲基硅油,且柠檬酸铝的质量分数为10wt%;步骤(a)初始速度为1.5m/s;步骤(b)气体流速为1.0m/s;步骤(c)气速为4.5m/s。实施例5包覆后材料100次循环后容量保持率94.02%。实施例6采用的流化床、包覆方法及烧结方法与实施例1相同,区别在于制备包覆改性正极材料的过程中:固含量20%的纳米氧化硼的异丁醇分散液;烧结过程中,控制反应器内温度700℃,烧结2h。实施例7采用的流化床、包覆方法及烧结方法与实施例1相同,区别在于制备包覆改性正极材料的过程中:固含量6%的纳米氧化镁的甲醇分散液;烧结过程中,控制反应器内温度350℃,烧结8h。对比例1:未包覆的镍钴锰三元523正极材料。图4为实施例1、实施例2和对比例1的循环性能对比图,由图可知,100次循环后容量保持率分别为100%,94.05%和79,23%,包覆后正极材料的循环性能明显提升。表1为实施例1-5和对比例在100次同样条件的循环测试后容量保持率数据,数据表明在进行包覆改性后正极材料的容量保持率都有一定的提升。表1正极材料包覆材料容量保持率实施例1氧化铝100%实施例2氧化钛94.05%实施例3氧化铝92.59%实施例4氧化锆88.72%实施例5氧化铝94.02%对比例无79.23%本发明中,图1示意的设计图仅作为一个可行的设计方案,仅对各个结构的作用进行说明,并不对各个部件或者结构的位置和布局进行限制,例如包覆液的喷嘴位置可以设计在流化床反应器1的顶部、侧壁或者底部以水平或呈一定角度等方式布置。申请人声明,本发明通过上述实施例来说明本发明的详细方法,但本发明并不局限于上述详细方法,即不意味着本发明必须依赖上述详细方法才能实施。所属
技术领域:
的技术人员应该明了,对本发明的任何改进,对本发明产品各原料的等效替换及辅助成分的添加、具体方式的选择等,均落在本发明的保护范围和公开范围之内。当前第1页12