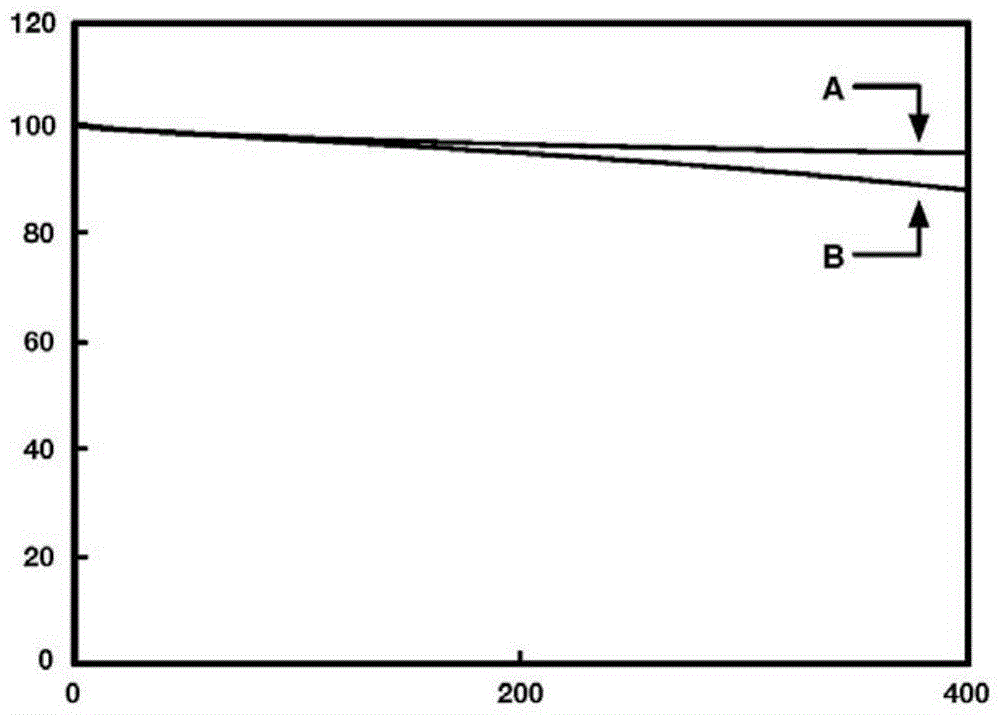
本发明涉及一种碳沉积的碱金属氧阴离子物,以及其多步骤的制备过程,以及所述的碳沉积碱金属氧阴离子物作为锂二次电池正极材料的用途。
背景技术:
:橄榄石型lifepo4具有优异的容量保持率、热稳定性、无毒性和安全性,已经成为锂离子电池的一种重要正极材料。但橄榄石型lifepo4存在明显的缺陷,例如本征电子电导率和离子电导率低。电子电导率可以通过碳包覆来提高,锂离子的扩散可以通过合成小颗粒来解决。在碳沉积磷酸亚铁锂的特定情况下,简称c-lifepo4,制造这种材料的几种工艺已经被提出,或者通过碳前驱体在lifepo4上的热分解,或者通过锂、铁、po4源与碳前驱体的同时反应制得。例如,ep1049182a3和us2002/0195591a1描述了固态热过程合成lifepo4,其反应式如下:fe(iii)po4+li-源+碳前驱体→c-life(ii)po4其中,碳前驱体是有机物,它通过热分解形成碳沉积,同时产生气体有效地还原了fe(iii)。us2007/0054187a1公开了锂金属磷酸盐limpo4的制备方法,它通过li源、至少一种m源(m可以是fe、mn、co、ni)和至少一种po4源,在100~250℃温度和1~40bar压力下水热反应得到。所公开的方法包括将limpo4与碳前驱体混合、干燥并煅烧该混合物,从而合成c-limpo4。因为包含了很多同时发生的化学、电化学、气相、气固反应,烧结反应以及碳沉积过程,该方法在工业化实施中面临着挑战。因此,具有碳沉积的碱金属氧阴离子正极材料的电化学性质取决于许多参数,例如表面特性、湿润特性、表面积、孔隙率、颗粒尺寸分布、水分含量、晶体结构、碳沉积的导电性、以及原材料的化学性质、反应进料速率、气体流量等等。在反应过程中,所有这些性质都难以以非常精准的方式控制,这会导致得到非化学计量比的产物、反应不完全或者在产物中残余杂质。因此,问题仍然是要发现一种简单的、优化的工艺,来制造应用于电池的更高质量的正极材料。技术实现要素:本发明的目的在于提供一种制造碳沉积碱金属氧阴离子物正极材料的新方法,当用本发明得到的碳沉积碱金属氧阴离子物作为锂二次电池的活性电极材料时,即使不比用现有技术得到的材料表现出的电化学性能更好,其性能表现也是类似的。此外,本发明的目的还在于提供一种制造碳沉积碱金属氧阴离子物的通用方法,该方法仅包括几个步骤,可以很容易地用于制造各种等级的高性能和低成本正极材料。而且,在每一步骤中,该工艺可以有效控制和优化前驱体、对电池运行有害的杂质、颗粒形貌以及碳沉积的品质。本发明的目的通过多步工艺制备碳沉积碱金属氧阴离子物的过程得以实现。在碳沉积磷酸亚铁锂的特定情况下,简称c-lifepo4,所述工艺过程优选包括如下步骤:(a)混合,优选研磨,包含至少一种锂源、至少一种正磷酸铁源、以及至少一种有机碳源的初始材料化合物,加热所述初始材料得到碳沉积的磷酸亚铁锂,优选地包括磷酸亚铁或焦磷酸盐相。(b)在至少一种醇基中纳米球磨步骤(a)中得到的材料;(c)干燥步骤(b)中得到的纳米研磨的悬浊液以获得固体化合物;(d)在气相有机碳源存在下加热步骤(c)中得到的固体化合物以获得碳沉积磷酸亚铁锂。本发明还提供了一种在气相有机碳源存在下通过化学气相沉积过程进行碳沉积的碳沉积碱金属氧阴离子物的方法。根据本发明,沉积碳含量低于2.5wt%,优选低于2.0wt%,更优选低于1.6wt%,更进一步优选低于1.2wt%。本发明还提供了一种通过本发明工艺获得的碳沉积碱金属氧阴离子物,其所述碳沉积碱金属氧阴离子物的沉积碳含量低于2.5wt%、硫含量低于80ppm,优选低于60ppm,更优选低于40ppm,更进一步优选低于20ppm。本发明还提供了一种通过本发明工艺获得的石墨烯状碳沉积碱金属氧阴离子物,其所述石墨烯状碳沉积碱金属氧阴离子物具有1至8层石墨烯状碳层。本发明还提供了一种通过本发明工艺获得的石墨烯状碳沉积碱金属氧阴离子物,其所述石墨烯状碳沉积碱金属氧阴离子物具有1至8层石墨烯状碳层,同时其硫含量低于80ppm,优选低于60ppm,更优选低于40ppm,更进一步优选低于20ppm。本发明还提供了一种通过本发明工艺获得的碳沉积碱金属氧阴离子物,其所述碳沉积碱金属氧阴离子物中沉积碳含量低于2.5wt%、并且碱金属氧阴离子物的一次颗粒平均粒径小于500nm,在优选实施例中小于250nm,在更优选实施例中小于150nm。在另一个优选实施例中,一次颗粒的平均粒径在25~250nm之间,优选在50~150nm之间,更优选在70~130nm之间。本发明还提供了一种通过本发明工艺获得的碳沉积碱金属氧阴离子物,其所述碳沉积碱金属氧阴离子物的沉积碳含量低于2.5wt%,并且该碳沉积碱金属氧阴离子物由平均粒径在50~250nm的一次颗粒团聚成二次球形团聚体,其bet值在3~11m2/g之间,优选3~9m2/g之间,更优选在3~7m2/g之间,更进一步优选3~5m2/g。在另一个优选实施例中,bet数值≤11m2/g,优选≤9m2/g,更优选≤7m2/g,更进一步优选≤5m2/g。本发明还提供了一种通过本发明工艺获得的碳沉积碱金属氧阴离子物,其所述碳沉积碱金属氧阴离子物的沉积碳含量低于2.5wt%、硫含量低于80ppm,优选低于60ppm,更优选低于40ppm,更进一步优选低于20ppm。并且该碳沉积碱金属氧阴离子物由平均粒径在50~250nm的一次颗粒团聚成二次球形团聚体,其bet值在3~11m2/g之间,优选3~9m2/g之间,更优选在3~7m2/g之间,更进一步优选3~5m2/g。在另一个优选实施例中,bet数值≤11m2/g,优选≤9m2/g,更优选≤7m2/g,更进一步优选≤5m2/g。本发明还提供了一种通过本发明工艺获得的石墨烯状碳沉积碱金属氧阴离子物,其所述石墨烯状碳沉积碱金属氧阴离子物具有1至8层石墨烯状碳层,同时其硫含量低于80ppm,优选低于60ppm,更优选低于40ppm,更进一步优选低于20ppm。并且该碳沉积碱金属氧阴离子物由平均粒径在50~250nm的一次颗粒团聚成二次球形团聚体,其bet值在3~11m2/g之间,优选3~9m2/g之间,更优选在3~7m2/g之间,更进一步优选3~5m2/g。在另一个优选实施例中,bet数值≤11m2/g,优选≤9m2/g,更优选≤7m2/g,更进一步优选≤5m2/g。本发明还提供了通过本发明工艺制备的碳沉积碱金属氧阴离子物用于制备锂二次电池正极的用途。本发明还提供了通过本发明工艺制备的碳沉积碱金属氧阴离子物用于制备具有优异高温电化学性能的锂二次电池正极的用途,其所述碳沉积碱金属氧阴离子的沉积碳含量小于2.5wt%、硫含量低于80ppm,优选低于60ppm,更优选低于40ppm,更进一步优选低于20ppm。本发明还提供了通过本发明工艺制备的石墨烯状碳沉积碱金属氧阴离子物用于制备具有优异高温电化学性能的锂二次电池正极的用途,其所述石墨烯状碳沉积碱金属氧阴离子具有1~8层石墨烯状沉积碳,同时其硫含量低于80ppm,优选低于60ppm,更优选低于40ppm,更进一步优选低于20ppm。本发明还提供了一种由负极、正极和电解质组成的锂二次电池,其中正极是通过本发明的工艺制造的碳沉积碱金属氧阴离子物。在结合本发明的具体实施例描述和附图说明后,这些和其它方面、以及本发明的特征对本领域的普通技术人员来说将变得显而易见。附图说明图1是循环性能图,按照对比实施例1和2制备、碳作为负极、c-lifepo4作为正极的两个液态电解质电池在60℃、c/4电流下静态循环测试。y轴表示电池容量(mah/g),x轴表示循环次数,初始容量用锂金属电池在25℃、c/5电流测试决定。电池1由包含有水中球磨纳米化步骤合成的c-lifepo4制备(曲线b),电池2由包含有异丙醇中球磨纳米化步骤合成的c-lifepo4制备(曲线a)。图2是循环性能图,按照实施例1制备、金属锂作为负极、c-lifepo4作为正极的两个液态电解质电池在60℃、c/4电流下静态循环测试。y轴表示电池容量(mah/g),x轴表示循环次数,初始容量用锂金属电池在25℃、c/5电流测试决定。电池3由包含在水中球磨纳米化步骤合成的c-lifepo4制备(曲线b),电池4由包含有异丙醇中球磨纳米化步骤合成的c-lifepo4制备(曲线a)。图3是实施例2中制备的用异丙醇作为载流液体球磨纳米化后的一次颗粒的sem图。图4是实施例2中制备的一次颗粒组成的碳沉积二次团聚体的sem图。图5是实施例2中通过气相碳源热cvd过程得到的c-lifepo4的碳沉积层的tem。图6是循环性能图,碳作为负极、c-lifepo4作为正极的5块液态电解质电池在60℃、1c电流下静态循环测试。y轴是电池容量(mah/g),x轴是循环次数,初始容量决定于25℃、c/5电流下的测试。根据实施例2,电池5b由硫含量745ppm的c-lifepo4制备(曲线e),电池6b由硫含量339ppm的c-lifepo4制备(曲线d),电池7b由硫含量71ppm的c-lifepo4制备(曲线c),电池8b由硫含量34ppm的c-lifepo4制备(曲线b)电池9b由硫含量13ppm的c-lifepo4制备(曲线a)。图7是正极容量图,碳作为负极、c-lifepo4作为正极的液态电解质电池在25℃、c/5放电倍率下测试。y轴是电池电压(相对于li+/li),x轴是容量(mah/g)。电池10是用实施例3中得到的c-lifepo4样品d1制备的。图8是循环性能图,碳作为负极、或者lco和c-lifepo4混合作为正极材料,或者纯lco作为正极材料的3块液态电解质电池在60℃、1c放电倍率下静态循环测试。y轴是电池容量(mah/g),x轴是循环次数。初始容量决定于25℃、c/5电流下的测试。根据实施例4的方法,曲线a是纯lco正极的循环性能,曲线b是c-lifepo4(硫含量33ppm)和lco混合作为正极材料的循环性能,曲线c是c-lifepo4(硫含量386ppm)和lco混合作为正极材料的循环性能。图9是混合脉冲功率性能(hppc),碳作为负极、或者nmc532和c-lifepo4混合物、或者纯nmc532作为正极材料的3块液态电解质电池在25℃、10s3c脉冲充电倍率下测试。y轴是电池电压(相对于li+/li),x轴是面积阻抗率(ω·cm2)。根据实施例4的方法,曲线a是c-lifepo4(硫含量38ppm)和nmc532作为正极材料的混合电极的输入数据,曲线c是相同混合电极在60℃、1c静态循环200周后的hppc输入数据,曲线d是c-lifepo4(硫含量251ppm)和nmc532作为正极材料的混合电极在60℃、1c静态循环200周后的hppc输入数据。具体实施方式尽管能量密度比如nmc、nca等氧化物正极材料低,但是长期来看,对安全性能优异、电化学滥用容忍度高、宽操作温度范围下效率独特、循环寿命极长、生命周期成本低(价格/kwh/循环次数)、功率/能量比极高、高温性能杰出、不使用关键原料钴的先进电池的需求,意味着碳沉积lifepo4在未来仍将是一种关键的、低成本的电极材料,其应用市场快速增长,比如直接替代铅酸电池、微混48v汽车电池、大规模储能、电动巴士、电动卡车、自动驾驶汽车、叉车、混合以及纯电动火车、或者混合以及纯电动船用电池系统(装有大型船用兆瓦级电池的渡船)。发明人发现,通过前驱体烧结、醇基纳米研磨、以及化学气相碳沉积的多步工艺过程合成碳沉积碱金属氧阴离子物,如c-lipopo4,为了确保其在最苛刻的条件下(高温循环和储存)仍具有优异的性能,非常有必要在每一步都将杂质和副反应控制到出乎意料地低水平。在一个非限制性实施例中,碱金属氧阴离子物是一种对应于通用标称公式aamm(xo4)x的化合物,其中:a代表单独或部分被na和/或k原子取代至多20%的li;m包括至少95%原子比的fe(ⅱ)或mn(ⅱ)或它们的混合;xo4代表单独或部分被从选自so4和sio4中的至少一个基团取代至多30%的po4;a、m、x是这样的:0<a≤8,1≤m≤3,0<x≤3,并且其中选择的m、x、a、m和x是可以维持所述化合物电中性的。在另一个非限制实施例中,碱金属氧阴离子物是一种对应于一般名义公式aamm(xo4)x的化合物,其中:a代表单独或部分被na和/或k原子取代至多20%的li;m选自含有fe(ⅱ)、mn(ⅱ)、或它们混合的基团,单独或部分被至多5%原子比的一种或多种金属取代,该取代金属含有ni、或co、或等化合价或异化合价的选自mg、mo、nb、ti、al、ta、ge、la、in、y、yb、cu、sm、sn、pb、ag、v、ce、hf、cr、zr、bi、zn、ca、cd、ru、ga、sr、ba、b、w金属组合。xo4代表单独或部分被从选自so4和sio4中的至少一个基团取代至多30%的po4;a、m、x是这样的:0<a≤8,1≤m≤3,0<x≤3,并且其中选择的m、x、a、m和x是可以维持所述化合物电中性的。在另一个非限制性实施例中,碱金属氧阴离子物是具有橄榄石结构的化合物,对应于通用标称公式limpo4,其中m包含至少95%原子比,优选至少97%原子比,更优选至少99%原子比的fe(ⅱ)或mn(ⅱ)、或它们的混合。一种或多种其它金属可选来进行金属平衡,其选自ni、或co,或选自等化合价或异化合价的mg、mo、nb、ti、al、ta、ge、la、in、y、yb、cu、sm、sn、pb、ag、v、ce、hf、cr、zr、bi、zn、ca、cd、ru、ga、sr、ba、b、w金属的组合。在另一个非限制性实施例中,碱金属氧阴离子物是具有橄榄石结构的化合物,对应于通用标称公式limpo4,其中m包括至少65%原子比的mn(ⅱ)和至少25%原子比的fe(ⅱ),单独或部分被至多5%的一种或多种其它原子取代,取代原子选自ni、或co,或选自等化合价或异化合价的mg、mo、nb、ti、al、ta、ge、la、in、y、yb、cu、sm、sn、pb、ag、v、ce、hf、cr、zr、bi、zn、ca、cd、ru、ga、sr、ba、b、w金属的组合。在另一个非限制性实施例中,碱金属氧阴离子物是具有橄榄石结构的化合物,对应于通用标称公式limpo4,其中m包括至少97%原子比,优选至少98%原子比,更优选至少99%原子比的fe(ⅱ),一种或多种其它金属可选来进行金属平衡,其选自ni、或co,或选自等化合价或异化合价的mg、mo、nb、ti、al、ta、ge、la、in、y、yb、cu、sm、sn、pb、ag、v、ce、hf、cr、zr、bi、zn、ca、cd、ru、ga、sr、ba、b、w金属的组合。在另一个非限制性实施例中,碱金属氧阴离子物是具有橄榄石结构的化合物,对应于通用标称公式lifepo4。“通用标称公式”表示本发明的材料的化学计量比可以有偏移化学计量比几个百分点的变化,这是由于结构中存在取代或其它包括反位结构缺陷在内的缺陷,例如,但不限于,lifepo4晶体结构中铁位和锂位之间的阳离子无序,参见maier等[defectchemistryoflifepo4,journaloftheelectrochemicalsociety,155,4,a339-a344,2008]和nazar等[proofofsupervalentdopinginolivinelifepo4,chemistryofmaterials,2008,20(20),6313-6315]论文中的例子。a)前驱体的烧结步骤优选地,合成地橄榄石结构碱金属氧阴离子物是limpo4,其中m包含至少95%原子比,优选至少97%原子比,更优选至少99%原子比的fe(ⅱ)或mn(ⅱ)、或它们的混合。一种或多种其它金属可选来进行金属平衡(以后称为“外加金属”),其选自ni、或co,或选自等化合价或异化合价的mg、mo、nb、ti、al、ta、ge、la、in、y、yb、cu、sm、sn、pb、ag、v、ce、hf、cr、zr、bi、zn、ca、cd、ru、ga、sr、ba、b、w金属的组合。用来合成limpo4的初始材料化合物,包括至少一种锂源、至少一种金属铁源和/或金属锰源、任选地至少一种外加金属源、至少一种磷源以及至少一种有机碳源。这些初始材料经过至少一次混合、优选干法或湿法研磨步骤。所述源可以是具有不止一种源元素的化合物形式。湿法研磨在载流液体存在下实施。例如水或有机溶剂以及它们的混合物。优选地载流液体选自水或醇类以及它们的混合物。在一个非限制性实施例中,水优选软化水,流体载体的脱气可以通过本领域普通技术人员熟知的任何方法在湿法研磨步骤之前进行。在本工艺的开发过程中,发明人意识到,当使用水作为载流液体时,会引发一些有害的副反应,这取决于不同的前驱体。例如,以li2co3和fepo4合成lifepo4时,在水中研磨可能会产生一些不希望的含铁杂质,比如,但不限于,fe(oh)3、feo(oh)、或fe(oh)2,对本发明的碳沉积正极材料的电化学性能产生潜在的负面影响。同时,当不用载流液体进行干法研磨时,在一些实施例中的研磨效率可能相对较低,特别是在大规模研磨时。而且,在一些实施例中干法研磨可能导致前驱体局部过热,形成潜在的不希望的杂质。反之,湿法研磨其中的载流液体能有助于排除热量。这是为什么在一个优选的实施例中,研磨是在有醇类载流液体存在下进行的湿法研磨。醇是优选自具有1至10个碳原子的脂肪族醇,如甲醇、乙醇、丙醇如正丙醇或异丙醇、丁醇如正丁醇或异丁醇、以及它们的混合物。可应用任何已知的干法或湿法研磨技术,例如,但不限于,球磨或珠磨、行星式球磨、胶体磨、振动磨、搅拌磨、转子-定子磨、摇动球磨机、盘式磨、砂磨机、卵石磨、罐磨机、超声波和超声波辅助磨、潜式篮研机、篮式砂磨机、高动能转子球磨机、搅拌珠磨、搅拌磨、以及等同研磨设备。干法或湿法研磨优选地是球磨或珠磨,更优选地是高能球磨或珠磨。可用的工业设备可用于进行至少一个干法和/或湿法高能球磨或珠磨步骤。适合的高能研磨设备可来自unionprocess(阿克伦,俄亥俄州44313)、zozgmbh(维登,德国)、耐驰-feinmahltechnikgmbh(塞尔布,德国)、retschgmbh(哈恩,德国)、fritschgmbh(伊达尔奥伯施泰因,德国)、布勒ag(乌兹维尔,瑞士)、spexsampleprep(n.j.梅塔钦,08840)、山东龙兴化工机械集团有限公司(山东烟台)等等其它可能的供应商。这样合适的高能研磨设备的具例包括,但不限于此,7.6l处理容积的1-s、200l处理容量的sd-30、300l处理容积的sd-50(unionprocess)、simoloyercm08(zoz)、mastermill30潜篮式球磨机(耐驰),centextmt3搅拌磨(布勒),lmj-37篮式砂磨机(山东龙兴)、spex8000d混合/研磨机(spexsampleprep)。本领域技术人员将能够选择合适的设备来进行湿法研磨和/或干法研磨,而不脱离本发明的精神。在一个非限制性实施例中,本发明的研磨步骤的持续时间是5分钟到4小时之间,优选10分钟到2小时之间,更优选15分钟到1小时之间。在另一个非限制性实施例中,研磨步骤操作时间小于2小时,优选小于1小时,更优选小于30分钟,更进一步优选小于15分钟。研磨后,如果是湿法研磨的,可选择进行干燥步骤,研磨后物料经过至少一次热处理。可选地,可以增加至少一个压实步骤,这可以用机械压实,例如用辊压机或片压机,也可以用滚动、堆积或造粒、或用任何其他适合本领域技术人员的技术方法。在广泛的非限制性实施例中,在化学反应器中加热研磨后物料,以控制气氛和/或热处理温度。在一个非限制性实施例中,研磨后物料加热温度在300~800℃之间,在优选实施例中温度在500~700℃之间,在另一个优选实施例中温度在550~650℃之间,在进一步优选的实施例中温度在575~625℃之间。在实验室规模的非限制性实施例中,本发明过程方便地在管式炉中或放置于加热炉里的密闭金属容器中实施。两者都有进气口和出气口,可以控制与研磨后物料接触的气氛。在工业规模的非限制性实施例中,本发明过程优选连续地、有助于研磨后物料与气相平衡的反应器中实施。可以控制气体成分和循环的反应器,例如来自这些:回转窑、推板窑、辊道窑、网带窑、皮带驱动窑炉、流化床等。在一个非限制性实施例中,在保护性气氛中加热研磨后物料,优选在非氧化性或惰性气氛中,例如,但不限于,氮气、氩气、二氧化碳、氦气、其它惰性气体以及它们的混合物。除了从有机碳源热分解产生的还原性气氛,如果需要的话,可以任意地选择外加还原性气氛,以参与还原或防止二价铁和/或锰继续氧化且防止完全还原成元素状态。外加还原性气氛包括气体,例如但不限于co、h2、nh3、hc、其中hc是指气体或蒸汽形式的任何碳氢化合物及其衍生物或含碳产物;气氛也包括惰性气体,例如但不限于氮气、氩气、二氧化碳、氦气、其它惰性气体以及它们的混合物。在另一个非限制性实施例中,本发明的加热步骤持续时间在10分钟到4小时之间,优选20分钟到2小时之间,更优选30分钟到1小时之间。在进一步的非限制性实施例中,本发明的研磨、可选的干燥、以及加热步骤的总时间小于180分钟,优选小于150分钟,更优选小于120分钟,更进一步优选小于90分钟。在广泛的非限制性实施例中,本发明的研磨步骤持续时间、加热步骤的温度和持续时间根据前驱体性质和其它参数的函数来选择,例如合理的时间限制。本领域技术人员将能够在不偏离本发明的情况下,在不需要特别努力的情况下识别合适的可选参数。铁和/或锰金属来源通常是全部或部分以它们的氧化态fe(ⅲ)和/或mn(ⅲ)的形式,为了确保最终正极材料的品质,在热处理过程中全部铁和/或锰被还原至fe(ⅱ)和/或mn(ⅱ)氧化态。然而,初始原料化合物优选不完全转化为橄榄石结构的锂金属磷酸盐,从而方便微调晶粒大小,并优化热处理的能量效率。同时,部分转变可以避免即使经过后续的热cvd步骤,材料中仍残留不希望形成的杂质。例如在lifepo4中,众所周知,在还原条件下热处理温度越高和/或反应时间越长会导致磷化物杂质(fep、fe2p、fe3p)形成,对正极材料有潜在的有害影响,特别是其高温循环性能。在后续的热cvd步骤中,合适化学计量比的剩余物相将被转化为理想的橄榄石结构的锂金属磷酸盐。由于其中的物料预先纳米化了,所以增强了反应动力学。例如在lifepo4中,剩余物相含有磷酸亚铁fe3(po4)2和li3po4(1:1摩尔比)或者在较低的加热温度下包括焦磷酸亚铁fe2p2o7和li2co3(1:1摩尔比),在随后的热cvd步骤中转化为橄榄石结构的lifepo4。这就是为什么本发明的另一个目的在于热处理步骤中研磨后初始原料化合物变为橄榄石结构limpo4的转化率为30~99mol%之间,优选为40~90mol%之间,更优选为50~80mol%之间,其中在热处理的材料中所有铁和/或锰原子是fe(ⅱ)和/或mn(ⅱ)氧化态。有机碳源用来提供还原气氛,并通过避免或限制前驱体的烧结来控制晶粒大小,同时在材料中留下残余碳。在后续的纳米研磨步骤中,残余碳将从材料表面磨掉作为低质量碳组分存在,因此最好限制上述碳残留的数量。这就是为什么本发明的另一个目的在于热处理后的初始原料化合物包含低于1wt%的残余碳,优选低于0.7wt%,更优选低于0.4wt%,更进一步优选低于0.1wt%。在本发明的其他优选模型中,残余碳优选在0.01至1wt%范围内,更优选在0.05至0.75wt%范围内,更进一步优选在0.1至0.5wt%范围内。在一个非限制性实施例中,锂源化合物是选自,例如氧化锂、氢氧化锂、碳酸锂、中性磷酸锂li3po4、lipo3、磷酸氢锂lih2po4、li2hpo4、草酸锂、乙酸锂、聚丙烯酸锂、硬脂酸锂、以及它们的混合物之一。本领域的技术人员在不脱离本发明精神的情况下,将能够选择任何可选的合适化合物或选择以上任何来源化合物。优选地,在氢氧化锂和碳酸锂中选择锂源,更优选地锂源为碳酸锂。在一个非限制性实施例中,锂源以粒子形式存在,或者以粒子的团聚体或块体形式存在,其d90优选小于40μm,更优选小于20μm,进一步优选小于10μm,更进一步优选小于5μm。在另一个非限制实施例中,金属源和磷源优选地由同一个源提供,并且是选自化合物例如含水或脱水fepo4、mnpo4、(fe,mn)po4、fehpo4、mnhpo4、(fe,mn)hpo4、fe3(po4)2、mn3(po4)2、(fe,mn)3(po4)2、fe2p2o7、mn2p2o7、(fe,mn)p2o7、nh4fepo4、nh4mnpo4、nh4(fe,mn)po4、以及它们的一种混合物。本领域的技术人员在不脱离本发明精神的情况下,将能够选择任何可选的合适化合物或选择以上任何来源化合物。金属磷酸盐来源优选含水或脱水fepo4、mnpo4、(fe,mn)po4以及它们的混合物。当limpo4是lifepo4时,来源优选自磷酸铁fe(ⅲ)po4和水合磷酸铁fe(ⅲ)po4·xh2o(x≤4,优选x=2)之中。金属磷酸盐来源可以是无定形态、非晶化或晶化态(包括但不限于strengite,metastrengitei,metastrengiteii,或者正交晶体结构)。在一个非限制性实施例中,上述金属磷酸盐来源是颗粒、团聚体或颗粒聚集体、或片状形貌,其d90优选小于40μm,更优选小于20μm,进一步优选小于10μm,更进一步优选小于5μm。在另一个非限制性实施例中,金属磷酸盐来源于平均粒径小于500nm的一次粒子的团聚体或聚集体,优选一次粒子的平均粒径小于200nm,更优选小于100nm,进一步优选小于50nm。在进一步的非限制性实施例中,外加金属源是一种没有任何限制的化合物,它以外加金属的碳酸盐、草酸盐、乙酸盐、硬脂酸盐、硝酸盐、磷酸盐、氢氧化物、氧化物、有机金属物、甚至非优选的卤化物或硫酸盐、以及它们的混合物。外加金属不排除作为其它来源的一部引入,例如2%mg取代fe的(fe,mg)po4,本领域的技术人员在不脱离本发明精神的情况下将能够选择任何可选的合适组合。本领域的技术人员在不脱离本发明精神的情况下,将能够通过选择合适的碱、金属、氧阴离子源化合物而生产其它的碱金属氧阴离子物。在进一步的非限制性实施例中,没有任何限制地,有机碳源可以选自任何含有碳原子的液相、半固相、蜡状、或固体有机物,例如可选自多环芳香物质(如焦油和沥青)、多羟基化合物(如糖和碳水化合物)、乳糖、甘油、脂肪酸、氨基多羧酸(如乙二胺四乙酸)、乙二醇、低聚物、聚合物、共聚物、嵌段共聚物、纤维素、淀粉及其酯和醚、以及上述有机碳源的任意衍生物、以及它们的混合物。作为聚合物或低聚物的例子,可以提及包括聚烯烃、聚丁二烯、聚乙二醇、聚乙烯醇、聚乙烯吡咯烷酮、聚乙烯醇缩丁醛、聚乙二醇、聚乙二醇、聚乙烯、聚丙烯、聚丙烯酸酯等的聚合物或低聚物、酚类缩合物(包括与醛反应得到的缩合物),由糠醇、环氧乙烷和/或环氧丙烷、马来酸酐、苯乙烯、二乙烯基苯、萘、戊二烯、丙烯腈、丙烯酸酯、丙烯酰胺、乙烯基、乙烯基醚、乙烯、丙烯、丁烯、丁二烯、乙酸乙烯酯衍生的聚合物或低聚物,以及上述聚合物或低聚物的任何衍生物,以及它们的混合物。不排除用外部气相有机碳源替代全部或部分液体、半固体或固体有机碳源。b)纳米研磨步骤步骤a)获得的物料(称为“物料a”)在载流液体的存在下经过至少一种液相珠磨纳米化加工步骤。在这个工艺的开发过程中,发明人意识到当用水作为载流液体时,在一些实施例中,载流液体中可能含有铁和/或锰的金属性杂质(在100ppm级别或更多),这对碳沉积正极材料的电化学性能产生负面影响。不受任何理论束缚,发明人相信杂质的形成可能是因为在高能水基珠磨纳米化加工步骤中,物料a部分溶出。这就是为什么纳米研磨使用醇基作为载流液体。步骤a)获得的物料(称为“物料a”)经过至少一种醇基纳米研磨加工步骤。本文所使用的“纳米研磨”是指自上而下的研磨化合物的步骤,以获得平均一次粒径(对应于d50)小于500nm的化合物颗粒,在优选的实施例中小于250nm,在更优选的实施例中小于150nm。在另一个实施例中,纳米研磨的一次粒子具有25至250nm之间的平均粒径,优选在50至150nm之间,更优选在70至130nm之间。在一个非限制性实施例中,本发明纳米研磨物料a的粒径分布特征在于,跨度(定义为(d90-d10)/d50)小于2.5,优选小于1.5,更优选小于1,更进一步优选小于0.75。本文所使用的“醇基纳米研磨”是指在有醇类载流液体存在下进行的湿法研磨。醇是优选自具有1至10个碳原子的脂肪族醇,如甲醇、乙醇、丙醇如正丙醇或异丙醇、丁醇如正丁醇或异丁醇、以及它们的混合物。甲醇、乙醇和异丙醇是优选的载流液体。在一个非限制性实施例中,纳米研磨在惰性气氛中操作,例如但不限于氮气、氩气、二氧化碳、氦气、其它惰性气体、以及它们的混合物之一。术语“惰性气氛”通常指含有少量或不含氧的气体混合物。在另一个非限制性实施例中,醇基载流液体的脱气是在纳米研磨步骤之前,采用本领域普通技术人员熟知的任何方法进行,例如降压、脱除器、膜脱气和惰性气体替代的方法。在另一个非限制性实施例中,湿法珠磨设备可以选自本领域技术人员熟知的搅拌珠磨机,它能将颗粒尺寸降低至纳米范围。特别地,可以提及日本神通工业株式会社的ultraapex研磨机、德国耐驰公司的高速耐驰zeta和neos搅拌珠磨机、日本细川公司的hosokawaalpineahm研磨机、布勒中国公司的卧式纳米磨phn系列、中国山东龙兴公司的纳米磨zbw/5l、以及瑞士布勒公司的l&x系列磨机。在进一步的非限制性实施例中,研磨腔和研磨单元由保护材料层和/或由耐磨及耐腐蚀性材料制成,以避免配方污染,尤其避免金属性污染。优选地,进行无金属研磨设备部件的材料是聚合物或含有聚合物的,例如聚氨酯或聚乙烯;或者是陶瓷或含有陶瓷的,例如氧化锆、碳化钨、氮化硅或碳化硅。在另一个非限制性实施例中,输入悬浊液的研磨能耗优选设定在200~2500kwh/t,其中参考质量(t)是指悬浊液中物料a的质量。输入能量产生热量,所以该悬浊液必须用合适的冷却设备冷却。研磨珠可以例如由氧化铝、氧化锆、钇或铈稳定的氧化锆或碳化物制成。氧化锆也可以包含铪氧化物hfo2(zro2+hfo2)。在优选的实施例中,研磨珠由钇或铈稳定的氧化锆制成,任选地含有铪氧化物hfo2。在一个非限制性实施例中,根据本发明的醇基珠磨纳米化加工步骤使用的研磨珠的平均直径为50至800μm。在优选的实施例中,研磨珠的平均直径为100至400μm。在另一个优选的实施例中,研磨珠的平均直径为100至200μm。由于搅拌介质研磨是一个能量集中的过程,应该优化能量效率,使用更小的研磨珠可以使研磨过程效率更高,降低研磨能耗(kwh/t)、缩短研磨时间、而且可以降低粒径分布范围。降低研磨能耗和/或缩短研磨时间有助于提高本发明正极材料的品质,可以限制伴随苛刻高能研磨过程的潜在有害副反应。研磨腔中的研磨介质填充比例对研磨效果有重要影响。随着填充率提升,介质间的接触次数增加,单个研磨介质间的距离减小,从而改善了研磨效果。但是研磨介质的填充率超过一定比例会产生负面的研磨效果,因为过小的研磨介质距离会限制运行的自由度。研磨珠填充的优化可以优化加工效率,也可以缩小粒径分布。这就是为什么本发明的另一个目的在于在一个优选的实施例中,研磨腔与研磨珠的填充率在50~90vol%;在另一个优选的实施例中,填充率在60~85vol%;在另一个优选的实施例中,填充率在70~85vol%。在没有任何限制的情况下,纳米研磨可以用四种模式的其中一种操作,即单通道模式、多通道模式(其中悬浊液多次流经同一研磨机)、级联模式(其中悬浊液流经两台相连的研磨机)、以及循环模式(其中悬浊液可以连续地多次由泵输送流过研磨机)。级联模式允许使用两台装有不同大小研磨介质的研磨机,第一台装有大尺寸研磨介质的研磨机将粗大的来料研磨至允许进入小尺寸研磨介质研磨机的颗粒大小,从而最终达到理想的颗粒尺寸。除了优化工艺过程(研磨能耗、研磨时间、粒径分布)外,级联模式可以减少昂贵的细磨珠的磨损。在优选的实施例中,第一台研磨机使用平均直径在300~800μm的磨珠,第二台研磨机使用平均直径在100~300μm的磨珠。根据本发明,该工艺的灵活性允许生产各种等级的纳米化的物料a和细小的正极材料。例如,有可能生产存储在生产罐中的不同粒径分布的、以及/或具有不同化学组分的悬浊液,并有可能在干燥步骤c)之前混合它们以改变正极材料的特性。在一个非限制性实施例中,为了优化正极材料的压实密度,混合平均粒度50~200nm(占总重10~90wt%)的第一种纳米化的物料a悬浊液和平均粒度250~500nm的第二种纳米化的物料a悬浊液。在进一步的非限制性实施例中,混合至少两种具有不同化学组分的纳米化物料a。任意地,例如平均粒径78nm(占总量的87wt%)的纳米化life0.25mn0.73mg0.01po4与平均粒径134nm的纳米化lifepo4正极材料混合,以优化正极材料的能量密度。不排除与其它正极材料混合,如锂金属氧化物。任何其它的组合也是本发明的一部分,例如核壳结构的产物,包括通过后续干燥步骤中的包覆得到的组合,例如lifepo4包覆富锰limpo4或反向核壳结构。可以选择在至少一种还原剂存在情况下进行醇基纳米研磨,以避免物料a最终部分氧化。在一个非限制性实施例中,可选的还原剂是选自肼或其衍生物、羟基胺或其衍生物、抗坏血酸、柠檬酸、草酸、甲酸、硫醇、二硫代磷酸酯、硫代硫酸盐、亚磷酸盐、次磷酸盐、亚磷酸、醇、吡咯、多酚、氢醌、含有易氧化双键的化合物及其混合物。在一个非限制性实施例中,在纳米研磨中,可选的还原剂相对于被研磨物料a的用量小于10000ppm,在一个优选的实施例中小于5000ppm,在另一个优选的实施例中小于2500ppm,在更优选的实施例中小于1000ppm。还原剂可以在纳米研磨过程前加入或过程中连续地加入。在纳米研磨过程中,优选加入至少一种稳定剂,通过增加颗粒分散来润滑悬浊液以提高研磨效率,同时主要通过颗粒表面电荷改性和增加颗粒之间的斥力来抵消范德华力以减少颗粒团聚。因此,可能通过稳定分散和控制纳米团聚,研磨更高浓度的悬浮液,增加单位产量,减少研磨能耗,并减少纳米颗粒粒径分布。在进一步的非限制性实施例中,所述至少一种稳定剂是一种有机化合物,其可选自有机静电或电空间稳定剂、表面活性剂、分散剂和密封剂,其中许多来源于市售。所述至少一种稳定剂的用量相对于悬浊液中的物料a重量通常在0.05~2wt%之间,优选在0.1~1wt%之间,更优选在0.1~0.5wt%之间,更进一步优选在0.1~0.25wt%之间。在进一步的非限制性实施例中,所述至少一种稳定剂,例如,可以选自脂肪酸盐(例如油酸、硬脂酸和它们的锂盐)、脂肪酸酯、脂肪醇酯、烷氧基醇类、烷氧基胺类、脂肪醇硫酸盐或磷酸酯、咪唑和季铵盐、环氧乙烷/环氧丙烷共聚物、环氧乙烷/环氧丁烷共聚物、以及反应性表面活性剂。脂肪酸的一些衍生物也是特别令人感兴趣的。首先,糖酯化合物由亲水糖部分(特别是蔗糖、山梨糖醇和山梨糖醇)、疏水脂肪酸部分以及任选的聚氧化乙烯段构成。例如,可以提到croda公司生产的吐温,尤其是吐温20(聚氧乙烯山梨糖醇单月桂酸酯)、吐温80(聚氧乙烯山梨糖醇单油酸酯)和吐温85(聚氧乙烯山梨糖醇三油酸酯)。醇酸醇可以选自从由环氧乙烷和/或环氧丙烷获得的醇类。最常见的醇类前体是脂肪醇和烷基酚(例如辛基或壬基酚),特别是以商品名igepal(solvay公司)和brij(croda公司)出售的烷氧基醇。烷氧基胺类来自huntsman,商品名为jeffamine和surfonamine。脂肪醇硫酸盐或磷酸酯,包括它们的四维电子的形式,例如可以从stepan公司获得。环氧乙烷/环氧丙烷共聚物表面活性剂主要是巴斯夫生产的pruron。改变eo/po比和分子量,为获得不同溶解度、表面张力和润湿性等可调特性的表面活性剂提供了大量低价高效的选择。聚乙烯醇缩丁醛,聚乙烯醇,聚乙烯吡咯烷酮、聚乙二醇、羧酸、磺酸或膦酸及其盐、酒石酸及其盐、乙醇酸及其盐、聚丙烯酸及其盐、乙二胺四乙酸及其盐也可用作表面活性剂,如它们的任何衍生物和它们的混合物。当使用盐时,优选它们的锂盐。在一个非限制性实施例中,所述至少一种稳定剂可以选自有机硅表面活性剂(例如来自evonik或dowcorning),能将极性液体表面张力降低至用有机表面活性剂达到的一般水平以下。在进一步的非限制性实施例中,所公开的稳定剂也可部分或全部作为前驱体烧结步骤a)的有机碳源。在一个非限制性实施例中,悬浊液的固含量在20~70wt%之间,在优选的实施例中为30~65wt%之间,在更优选的实施例中为40~60wt%,在进一步优选的实施例中为45~55wt%。在一个非限制性实施例中,本文描述的纳米研磨步骤操作时间选自如下时间范围:约5分钟至约4小时、约10分钟至约4小时、约30分钟至约4小时、约60分钟至约4小时、约90分钟至约4小时、约120分钟至约4小时、约150分钟至约4小时、约180分钟至约4小时、约210分钟至约4小时、约230分钟至约4小时。本领域技术人员将能够在不偏离本发明精神的情况下选择任何合适的时间段或采用上述范围内的任何时间段。在另一个非限制性实施例中,纳米研磨步骤操作时间少于4小时,优选少于2小时,更优选少于1小时,更进一步优选少于30分钟。纳米研磨设备昂贵,还需要定期更换昂贵的细磨珠以保持高效率。在本发明的开发过程中,发明人发现在一些情况下,物料a经过低价高效的湿法或干法微米磨珠预研磨,对纳米研磨过程有好处。这种预研磨降低了纳米磨珠的磨耗,能够增加产出、降低研磨时间,还能够提高纳米化颗粒品质,特别是能得到更窄的粒径分布,并能减少材料暴露在严苛的高能球磨过程时间。而且,由于纳米研磨过程中大量输入的能量消耗成热量,预研磨显著提高了整个过程的能量效率。预研磨的应用也可以降低工艺对合成物料a粒度测量的要求,特别是对同等操作条件下纳米研磨步骤后的粒径分布。在一个非限制性实施例中,本文描述的预研磨是醇基高能研磨,优选以分批、单通道、多通道、循环或连续的方式在搅拌球磨机中操作。搅拌机可以使用低价高效预研磨设备,具体实例包括但不限于,unionprocess公司的34~2200l处理腔的attritorsl系列、attritorq或ol系列循环磨、attritorc、h或cls系列连续磨,以及其他供应商的同等设备。优选地,搅拌磨局部有内衬或由耐磨耐腐蚀材料制成,以避免杂质特别是金属污染,例如氧化铝、碳化物、氧化锆和聚氨酯。研磨珠由例如氧化铝、滑石、硅酸锆、氧化锆、钇或铈稳定的氧化锆或碳化物制成。在一个优选实施例中,研磨珠由铈或钇稳定的氧化锆制成,优选的磨珠直径2~20mm。这里使用的“微米研磨”是指研磨化合物的步骤,从而获得粒径分布中d90为1~5μm,优选1~3μm,更优选1~2μm的化合物。在另一个非限制性实施例中,预研磨步骤时间少于1小时,优选少于30分钟,更优选少于15分钟。预研磨可以选择在至少一种还原剂和/或至少一种稳定剂存在条件下实施。在一个非限制性实施例中,纳米研磨在惰性气氛中操作,例如氮气、氩气、二氧化碳、氦气。而在另一个非限制性实施例中,在纳米研磨前脱除醇基液体中的气体。在一个非限制性实施例中,输入搅拌磨的研磨能量优选设定在30kwh/t~300kwh/t,更优选在50kwh/t~200kwh/t,进一步优选在50kwh/t~150kwh/t,其中参考质量(t)是指在搅拌磨中的物料a的质量。输入能量会产生热量,因此可能需要合适的冷却设备冷却搅拌磨。而在另一个非限制性实施例中,预微米研磨是在一个连接有储罐的搅拌磨中以循环模式进行的。在预研磨完成后,将储罐连接到纳米设备上。在一个非限制性实施例中,根据本发明,还可以在纳米研磨配方中加入功能性添加剂,以提高正极材料的质量。具体实例包括但不限于,导电添加剂和表面处理剂。在纳米研磨之前、之中或之后,可以在配方中加入添加剂,在没有任何限制的情况下,在纳米研磨之前或之中加入添加剂。导电添加剂可以选自碳颗粒、碳纤维、碳纳米纤维、碳纳米管、石墨烯、氧化石墨烯、以及它们的混合物。在一个非限制性实施例中,导电添加剂是容易分散的颜料形式,其表面附着有稳定化基团。优选地,离子种类例如羧酸(-co2m)和磺酸(-so3m)盐,其中m优选自h、li、na或k,更优选自h或li之中。易分散的碳颗粒通常用于油墨或绘画颜料,是一种经济有效的解决方案。所公开的碳颗粒的平均粒径小于200nm,优选小于100nm,更优选小于50nm,更进一步优选小于25nm。例如,可以提及cabot公司生产的litx200和litx300、orion工程碳有限公司生产的色素碳黑fw200、tokaicarbon公司生产的tokabess#8500/f、三菱化学公司生产的highcolorfurnace#2650。根据本发明,除了潜在地改善正极材料的电化学性能,特别是在高电流密度和低温运行下,这样的碳颗粒可以提高正极材料的压实密度。在一个非限制性实施例中,导电添加剂优选易分散的碳颗粒,其用量相对于纳米研磨物料a总质量低于4wt%,优选低于2wt%,更优选低于1wt%,更进一步优选低于0.5wt%。表面处理剂可以选自有机金属化合物,比如包括钛、锆、铝的金属醇盐,包括硅醇盐的有机硅烷,及它们的混合物。根据本发明,表面处理剂可以作为钝化剂作用于纳米研磨过程中产生的新鲜的、高反应活性的表面,从而改善正极材料的电化学性能。在一个非限制性实施例中,表面处理剂的用量相对于纳米研磨物料a总质量低于2wt%,优选低于1wt%,更优选低于0.5wt%,更进一步优选低于0.25wt%。在一个非限制性实施例中,高能纳米研磨步骤可以在化学添加剂存在下进行,该化学添加剂能够有效地与物料a中意外存在的杂质发生反应,比如铁颗粒、铁氧化物、锂、过渡金属、以及含磷杂质。例如,铁颗粒或铁氧化物可以在lih2po4存在下通过机械合成法发生反应,产生具有合适li:fe:p平衡比例的化合物。在一个具体实例中,一批c-lifepo4中意外含有高的磁性杂质,这与fepo4·2h2o中存在fe2o3杂质有关。因此,在初步实验中,在化学计量比的lih2po4存在下,纳米研磨同批次的物料a可以获得约含有300ppb而不是4000ppm磁性杂质的c-lifepo4。c)干燥步骤纳米研磨后,从悬浊液中除去载流液体以获得纳米化物料a的固体化合物。本质上可以使用任何过程。例如,压滤、冷冻干燥、蒸发、闪蒸、盘式干燥、桨叶干燥、流化床干燥、锥形螺杆干燥、介质搅拌干燥、喷雾干燥都可以除去熔剂。喷雾干燥是一种广泛使用的方法,它利用热气体快速干燥悬浊液生产干粉,是本发明中优选的干燥设备。首先将悬浊液雾化产生液滴,随后在喷雾干燥室中液滴与热气体相接触,离开干燥室后,水分含量可在第二阶段干燥过程中进一步降低,例如在流化床或振动床干燥机中干燥。悬浊液雾化使用旋转雾化器、液压喷嘴、气动喷嘴、悬浊液和气体喷雾介质加压的组合式液压气动喷嘴、或者超声雾化器。喷嘴可以选择例如单流体喷嘴、双流体喷嘴、四流体喷嘴、在线混合喷嘴、喷墨喷嘴、双喷气动喷嘴、组合喷嘴以及超声波喷嘴。喷雾干燥室可以设计成同流、混流或逆流雾化。喷雾气体介质为惰性气体,比如氮气。不同于水基载流液体使用空气,使用惰性气体作为喷雾介质的额外成本,在同等操作条件下部分地通过醇溶剂优良的蒸发速率来补偿。甲醇、乙醇或异丙醇的蒸发速率一般是水的2~3倍。而且,用惰性气体喷雾干燥醇基悬浊液有助于干燥物料的纯化。众多喷雾干燥机的设计能满足多种产品规格,可以控制颗粒形貌从轻微团聚的一次粒子到一次粒子的二次团聚体,优选地,以一次粒子的二次球性团聚体形式。在进行喷雾干燥步骤之前,可以对步骤b)中获得的纳米悬浊液进行分散处理。这种处理可以采用任何市售的分散设备来进行,比如转子/定子分散机或胶体磨。在喷雾干燥前,为了防止雾化器堵塞,降低雾化前悬浊液的粘度,可以对悬浊液进行再凝聚。任何合适的添加剂也可以任选地添加在喷雾干燥之前的分散处理过程中,例如先前定义的表面处理剂和导电添加剂。在一个非限制性实施例中,在喷雾干燥机的进气口设备温度120~500℃下进行悬浊液的干燥操作,通常温度在200~370℃。出口温度通常在60~150℃范围,优选80~120℃。用任何市售的气固分离系统可以从气体里分离出固体产物,比如旋风分离器、静电沉淀器或过滤器、优选带有脉冲射流除尘系统的布袋过滤器。任选地,可以在喷雾干燥后增加至少一种分级工艺步骤,例如筛查、筛选或筛分。特别地,筛分和/或过筛步骤可以用30~40μm公称筛网。任选地,可以在喷雾干燥后增加至少一种压实工艺步骤,该步骤可以是机械压实,例如通过碾压机或压片机来进行,但是也可以用辊压、堆积、造粒、或通过其它任何本领域技术人员知道的合适技术方法实现本目的。在本工艺开发过程中,发明人还发现根据本发明,在一些实施过程中,即使纳米化的物料a干燥后湿分含量低,也可能对正极材料的电化学性能产生有害的影响。因此,在一个非限制性实施例中,干燥后、化学气相碳沉积前的物料含湿量小于4000ppm,优选小于2000ppm,更优选小于1000ppm,更进一步优选小于500ppm。d)化学气相碳沉积化学气相沉积(cvd)是一种化学过程,用于在各种基体上生成沉积碳,基体暴露于一种或多种气相碳源中,比如含碳气体或者有机物的热分解产物。本发明中,热cvd过程用于在步骤c)获得的纳米化颗粒上产生连续均匀吸附、高结晶度、低阻抗的碳沉积,优选石墨烯状沉积碳。这里使用的“石墨烯状碳沉积”是指id/ig比例小于0.9的碳沉积,优选小于0.8,更优选小于0.7,更进一步优选小于0.6。id/ig比例通常是拉曼分析中1360cm-1峰(id,与无定形碳相关)与1580cm-1峰(ig,与结晶碳相关)的强度比值。在一个非限制性实施例中,本发明中通过热cvd过程获得的沉积碳由至少99.5wt%的碳组成,优选至少99.7wt%,更优选至少99.9wt%,进一步更优选至少99.95wt%。在另一个非限制性实施例中,为了确保所有的颗粒表面都暴露于气相碳源中,优选地将粉体在回转炉中搅拌和旋转、或者在流化床中通过气相悬浮,任选地借助脉动辅助技术有效地使纳米颗粒流体化(特别感兴趣的是产生均匀的碳沉积的一次粒子。炉子与物料接触的部分被可以消除金属污染的材料包覆或制备,比如回转炉内的陶瓷炉管或碳炉管。锂金属磷酸盐的拉曼光谱分析显示多峰,比如900~1200cm-1对应于lifepo4谱图(称为iv)。沉积碳的品质可以通过iv/(id+ig)比监测,因为当表面被沉积碳完全包覆时,在900~1200cm-1范围就没有峰出现。这是为什么本发明的另一个目的在于在气相碳源存在下,通过化学气相沉积工艺获得碳沉积正极材料,其中iv/(id+ig)比在0至0.05的范围内,优选在0至0.03,更优选在0至0.01。不受任何限制,作为热cvd过程的碳源可以使用气体比如甲烷、乙烷、丙烷、丁烷、乙烯、丙烯、丁烯、天然气、液化石油气(lpg)或乙炔;汽化液体比如烷烃化合物,如戊烷、己烷或环己烷、芳香族化合物如苯、甲苯、二甲苯或乙苯;或醇比如甲醇、乙醇、丙醇或丁醇;汽化固体比如苯酚、醌、羟基醌、萘、蒽、联苯或联苯;以及以上物质的组合。碳源还可以是通过有机物裂解生成的复杂分解产物的气流,不受任何限制,可以使用任何含碳有机物比如聚丙烯、聚乙烯、聚苯乙烯、聚乙烯醇、聚烯烃、聚丁二烯、焦油、淀粉、碳水化合物、或纤维素及其衍生物。在一个非限制性实施例中,碳源由碳和氢构成。优选碳源是苯、丙烯或乙炔。任选地,添加氮(如尿素、氨、脂肪族胺或腈)或硼(如硼烷或硼酸)的衍生物允许合成氮或硼掺杂的沉积碳。任选地,碳沉积过程可以是等离子体增强cvd或激光激活cvd。在本发明的开发过程中,发明人还发现当使用有机物裂解得到的碳源时,提高芳烃化合物浓度的气相催化重整有助于提高碳沉积特性,特别是id+ig比降低和导电率提升。可以进行气流的升级,没有任何限制,例如用沸石催化剂(如y沸石或沸石zsm-5催化剂)在温度400℃到700℃之间进行气流升级。这是为什么本发明的另一个目的在于通过有机物裂解获得的热cvd碳源,用至少一种催化剂进行进一步的重整步骤以提高芳香族化合物的浓度。不排除对其它碳源应用催化重整步骤以提高芳香族化合物含量。碳沉积热cvd过程可以在一步或多步热过程中进行,例如,在一个非限制性实施例中,使用相同的或不同的碳源,cvd可以在第一个回转炉中进行,而热处理可以在第二个连续的炉中进行(例如在惰性气氛中);或者首次cvd在第一个回转炉中进行,而第二次cvd在第二个连续的炉中进行。总反应时间通常在10分钟到4小时,优选在10分钟到2小时,更优选在10分钟到1小时,更进一步优选在20到40分钟。在一个非限制性实施例中,在一步或至少一步的多步过程中,反应温度优选在600℃到750℃之间,在一个优选的实施例中反应温度在625℃到725℃之间,在另一个优选的实施例中反应温度在625℃到700℃之间,在一个更优选的实施例中反应温度在625℃到675℃之间。在一个非限制性实施例中,首次cvd步骤温度在200℃到600℃之间,优选在300℃到500℃之间,更优选在300℃到400℃之间。采用首次低温步骤可能有几个好处,例如可以限制纳米化颗粒的烧结,还可以限制对电化学性能有害影响的杂质形成。在本发明的开发过程中,发明人还发现,当使用脱氢时间短(在400℃小于1分钟)的化合物作为碳源时,比如苯,首次低温热cvd过程有利于获得具有较低缺陷密度的有序化石墨烯状沉积碳。然后,在600℃到750℃之间的温度下进行第二热处理,在一个优选的实施例中温度在625℃到725℃之间,在一个更优选的实施例中温度在625℃到700℃之间,在更进一步优选的实施例中温度在625℃到675℃之间。在一个非限制性实施例中,本发明的方法任选地包括在最终产品上进行后续闪蒸热处理,以改善碳沉积的石墨化程度,同时避免材料部分分解。闪蒸热处理温度在750℃到950℃之间,优选在800℃到900℃之间。闪蒸热处理持续时间优选地在10秒至10分钟之间,更优选在1分钟到5分钟之间。沉积碳的厚度和含量可以通过纳米化颗粒在气相碳源中的暴露时间控制,和/或通过调节炉内气相碳源的流量控制,和/或通过调节气相有机碳源浓度控制。为了控制气流中的碳源浓度,有机物可以与惰性载气混合,比如氮气、氩气、co2、氦气或还原性气体,比如co或h2,或者以上这些的任意组合。用于热cvd步骤的合适气相碳源流量通常取决于特定的环境(反应器类型、负载、停留时间和初始材料的类型),它可以由本领域技术人员使用本文所包含的信息来确定。在一些实施例中,虽然准确的流量取决于反应器类型、待处理材料和其他工艺参数,但是流速约为0.1~5l/min,或者约为0.1~3l/min,或者约为0.1~2l/min,任选地结合惰性载气,流速约为0.5~10l/min,约为0.5~8l/min,约为1~5l/min,或者约为1~3l/min时可以获得良好的结果。在其它实施例中,预先制备的气相碳源与氮气或氩气载气的混合物可用于热cvd步骤。例如,在流化床反应器中用更高流速来进行包覆,例如使用流速约为1~50l/min、10~25l/min、或者20~25l/min。在一些实施例中,气相碳源与混合物中惰性载气的比例为1:20到1:5。热cvd步骤通常在微正压下进行。因此,在特定的实施例中,热cvd步骤的气压在大气压之上0~80mbar、0~60mbar、0~50mbar、10~60mbar、10~50mbar、或者0~40mbar。在一个非限制性实施例中,根据本发明的碳沉积正极材料中来自热cvd的沉积碳含量少于总重的2.5wt%,优选少于2.0wt%,更优选少于1.6wt%,更进一步优选少于1.2wt。在本发明的其它优选实施例中,根据本发明的碳沉积正极材料中来自热cvd的沉积碳含量范围优选在0.2~1.2wt%,更优选0.5~1wt%,更进一步优选在0.6~0.95wt%。在另一个非限制性实施例中,碳沉积厚度约在0.3~3.7nm,优选地在0.8~2.2nm。在另一个非限制性实施例中,碳沉积是石墨烯状沉积碳形式,具有1~8层、优选2~5层所述石墨烯状沉积碳。在进一步的非限制性实施例中,通过本发明方法得到的以一次粒子形成二次球形团聚体的碳沉积正极材料,且沉积碳含量小于2.5wt%,其bet值在3~11m2/g之间,优选在3~9m2/g之间,更优选在3~7m2/g之间,更进一步优选在3~5m2/g之间。在另一个优选实施例中,bet值≤11m2/g,优选≤9m2/g,更优选≤7m2/g,更进一步优选≤5m2/g。在一个非限制性实施例中,通过本发明方法得到的沉积碳含量小于2.5wt%的碳沉积正极材料,以平均粒径在50~250nm的一次粒子团聚成二次球形团聚体的形式,其bet值在3~11m2/g之间,优选3~9m2/g之间,更优选在3~7m2/g之间,更进一步优选3~5m2/g。在另一个优选实施例中,bet数值≤11m2/g,优选≤9m2/g,更优选≤7m2/g,更进一步优选≤5m2/g。以一次粒子团聚成二次球形团聚体的形式存在的正极材料优选具有最小孔隙率,以允许二次电池电解液中溶剂化锂离子穿透团聚体并到达一次粒子,特别是支持大充放电电池,但过大的孔隙率对电极密度是有害的。这就是为什么孔隙率优选在5~40%之间,更优选在10~35%之间,更进一步优选在15~30%之间。通过压汞孔隙度测量法可以得到孔径分布,在一个非限制性实施例中,正极材料优选平均孔径为50~500nm的。在一个非限制性实施例中,本发明中以一次粒子的二次球形团聚体形式存在的碳沉积正极材料的d50在2~30μm之间,优选在3~20μm之间,更优选在3~10μm之间,更进一步优选在3~7μm之间。在另一个非限制性实施例中,本发明中以一次粒子的二次球形团聚体形式存在的碳沉积正极材料的粒径分布的特征在于,其跨度(定义为(d90-d10)/d50)小于3,优选小于2.5,更优选小于2,更进一步优选小于1.5。在进一步的非限制性实施例中,本发明中以一次粒子的二次球形团聚体形式存在的碳沉积正极材料的粒径分布的特征在于,d30/d70比值大于0.45,优选大于0.6,更优选大于0.75。控制粒径分布特性可以优化本发明正极材料的堆积密度,得到更高的压实密度。如已讨论的,碳沉积,最好是石墨烯状碳沉积,电阻率低,因此,根据本发明的方法获得的碳沉积正极材料的粉末电阻率约小于20ω·cm,优选小于10ω·cm,更优选小于7ω·cm,更进一步优选小于4ω·cm。粉末电阻率的下限值超过0.05ω·cm,优选超过0.5ω·cm,更优选超过1ω·cm。本发明材料的粉末电阻率低,有利于其应用于高功率/能量比性能优异的电池中。材料压实密度或多或少地与电极的密度或所谓活性物质的密度有关,它最终也和电池容量有关。压实密度越高,电池容量也越高。在一个非限制性实施例中,通过本发明工艺获得的碳沉积正极材料的压实密度超过2g/cm3,优选超过2.2g/cm3,更优选超过2.4g/cm3。在一个非限制性实施例中,本发明中以一次粒子的二次球形团聚体形式存在的碳沉积正极材料的粉末压实密度在2.4~3g/cm3之间,优选在2.5~2.9g/cm3之间,更优选在2.6~2.8g/cm3之间。在一个非限制性实施例中,本发明中以一次粒子的二次球形团聚体形式存在的碳沉积正极材料优选地为球形,其长径比(l/d)为0.7~1.5,优选地为0.8~1.3,更优选地为0.9~1.1,更进一步优选地为0.95~1.05。正极材料的压实密度随长径比提高而降低,特别是当长径比超过1.5时。根据本发明的碳沉积正极材料显示出优异的体积和振实密度,以改善这些材料在电极制造过程中的加工性能。这是因为用于制造电极的机器可以用被加工的材料填充至更大程度,从而可以获得更高的产出量。材料的体积密度在1~1.4g/cm3范围内。材料的振实密度在1.4~2g/cm3范围内。在本发明的开发过程中,发明人还发现,令人惊讶的是,即使硫杂质含量非常低也会对碳沉积正极材料在高温下(60℃循环和85℃循环)的电化学性能产生有害的影响,该碳沉积正极材料上有来自于热cvd过程的碳沉积,特别的是石墨烯状沉积碳。因此,在高温下制备性能优异的碳沉积正极材料,材料中硫含量小于80ppm,优选小于60ppm,更优选小于40ppm,更进一步优选小于20ppm。不受任何理论约束,发明人认为,令人惊讶的是,甚至从热cvd过程获得的碳沉积中,特别是在石墨烯状碳沉淀中痕量的硫,也可引起碳沉积正极材料表面与电池电解液的电催化反应。痕量的硫也可能引起bet值的增加,这可能是由于更多的无序碳沉积。这是为什么本发明的另一个目的在于一种低硫碳沉积正极材料,其通过在气相有机碳源存在下的化学气相沉积过程获得,其中碳沉积含量小于2.5wt%,硫含量小于80ppm,优选小于60ppm,更优选小于40ppm,更进一步优选小于20ppm。这是为什么本发明的另一个目的在于一种低硫碳沉积正极材料,其中碳沉积是以1~8层石墨烯状碳沉积,其中硫含量小于80ppm,优选小于60ppm,更优选小于40ppm,更进一步优选小于20ppm。这是为什么本发明的另一个目的在于一种低硫碳沉积正极材料,优选石墨烯状沉积碳,其中碳沉积含量低于1.2wt%,硫含量与碳沉积含量的比例(称为“s/c”)小于0.8%,优选小于0.6%,更优选小于0.4%,更进一步优选小于0.2%。这是为什么本发明的另一个目的在于通过本发明方法获得一种碳沉积正极材料,其碳沉积含量低于2.5wt%;其硫含量小于80ppm,优选小于60ppm,更优选小于40ppm,更进一步小于20ppm;其以一次粒子的二次球形团聚体形式存在,一次粒子的平均粒径在50~250nm之间;其bet值在3~11m2/g之间,优选3~9m2/g之间,更优选在3~7m2/g之间,更进一步优选3~5m2/g。在另一个优选实施例中,bet数值≤11m2/g,优选≤9m2/g,更优选≤7m2/g,进一步优选≤5m2/g。这是为什么本发明的另一个目的在于通过本发明方法得到一种石墨烯状碳沉积正极材料,其具有1~8层所述石墨烯状碳沉积;其硫含量低于80ppm,优选低于60ppm,更优选低于40ppm,更优选低于20ppm;其以一次粒子的二次球形团聚体形式存在,一次粒子的平均粒径在50~250nm之间;其bet值在3~11m2/g之间,优选3~9m2/g之间,更优选在3~7m2/g之间,更进一步优选3~5m2/g。在另一个优选实施例中,bet数值≤11m2/g,优选≤9m2/g,更优选≤7m2/g,进一步优选≤5m2/g。这是为什么本发明的另一个目的在于一种通过本发明方法得到的碳沉积正极材料在高温电化学性能优异的锂二次电池正极材料制备中的应用,其正极材料碳沉积含量低于2.5wt%;且其硫含量小于80ppm,优选低于60ppm,更优选低于40ppm,更进一步优选低于20ppm。这是为什么本发明的另一个目的在于通过本发明方法得到的石墨烯状碳沉积正极材料在高温电化学性能优异的锂二次电池正极材料制备中的应用,其正极材料具有1~8层所述石墨烯状碳沉积;且其硫含量小于80ppm,优选低于60ppm,更优选低于40ppm,更进一步优选低于20ppm。任选地,可以增加至少一种颗粒分级工艺步骤,以除去本发明的碳沉积正极材料的粗粉或细粉部分。这可以通过任何商业上可用的颗粒分类设备进行,例如旋风分离器、空气分级机、筛网、筛子、筛分器或它们的组合。在本发明的一个实施例中,二次球性团聚体碳沉积正极材料中粒径小于2μm、优选小于1μm的部分,采用分级工艺去除。在本发明的另一个实施例中,碳沉积正极材料在超声和空气刷联合清洁的筛网筛分机上进行筛分,筛网标称网孔30~40μm,优选40μm。细粉仍作为产品,粗粉不能。不能作为产品的粗和/或细粉可以作为原料在工艺中循环使用。配备集成分级机的气流磨通常是一种降低碳沉积正极材料粒径分布的方便工具。但是当正极材料是二次球性团聚体形式时,为了不破坏这种团聚体,优选地不使用气流磨。可选地,可以增加至少一个压实步骤,这可以用机械压实,例如用辊压机或片压机,也可以用滚动、堆积或造粒、或用其它任何适合本领域技术人员的技术方法。在优选的操作模式下,热cvd步骤后,碳沉积正极材料,优选石墨烯状碳沉积,其含水量小于200ppm,优选小于100ppm,更优选小于50ppm,更进一步优选小于25ppm。然而,任选地,通过后续的干燥步骤可以减少所获得材料的水分含量,这是有用的。不受任何限制,可以使用真空干燥设备、旋风真空干燥机、旋转真空干燥器、锥形桨叶干燥机、流化床干燥机、振动床干燥机、或锥形螺杆干燥机。本领域技术人员将能够在不脱离本发明、在不过度努力的情况下识别合适的替代干燥装置。在进一步的非限制性实施例中,从步骤a)到d)的总持续时间少于8小时,优选少于6小时,更优选小于4小时。在热cvd过程之后的任何步骤,比如分级、压实、气流磨、干燥、混合、搬运或存储,在干燥气氛下操作,优选惰性气氛,以保持产品品质直到包装于合适的密闭容器中,特别是在铝塑箔包装袋中。本发明方法允许合成几乎没有金属或磁性杂质的碳沉积正极材料,非常低的硫杂质和水分含量有利于它的实现。在一些实施例中,任选地在任何步骤过程中使用一个或多个除磁器,以进一步除掉潜在的残留磁性杂质。这是为什么本发明的另一个目的在于使用通过本发明方法得到的一种碳沉积正极材料。该正极材料碳含量低于2.5wt%;其硫含量小于80ppm,优选低于60ppm,更优选低于40ppm,更进一步优选低于20ppm;其水分含量低于100ppm;磁性杂质含量低于300ppb,优选低于200ppb,更优选低于100ppb,更进一步优选低于50ppb。这是为什么本发明的另一个目的在于使用通过本发明方法得到的一种石墨烯状碳沉积正极材料。该正极材料具有1~8层所述石墨烯状碳沉积,其硫含量小于80ppm,优选低于60ppm,更优选低于40ppm,更进一步优选低于20ppm;其水分含量低于100ppm;磁性杂质含量低于300ppb,优选低于200ppb,更优选低于100ppb,更进一步优选低于50ppb。根据本发明的碳沉积正极材料中的铁磁杂质与它们的比磁化强度水平有关,极低的硫杂质含量和水分有利于实现低比磁化强度特性。这是为什么本发明的另一个目的在于使用通过本发明方法得到的一种碳沉积正极材料。其碳含量低于2.5wt%;其硫含量小于80ppm,优选低于60ppm,更优选低于40ppm,更进一步优选低于20ppm;其水分含量低于100ppm;其比磁化强度小于0.1emu/g,优选小于0.01emu/g,更优选小于0.001emu/g,更进一步优选小于0.0001emu/g。这是为什么本发明的另一个目的在于使用通过本发明方法得到的一种石墨烯状碳沉积正极材料。该正极材料具有1~8层所述石墨烯状碳沉积,其硫含量小于80ppm,优选低于60ppm,更优选低于40ppm,更进一步优选低于20ppm;其水分含量低于100ppm;其比磁化强度小于0.1emu/g,优选小于0.01emu/g,更优选小于0.001emu/g,更进一步优选小于0.0001emu/g。碳沉积物中的硫杂质会产生吸湿性物质,因此极低的硫含量有利于限制水的吸收。这是为什么本发明的另一个目的在于使用通过本发明方法得到的一种石墨烯状碳沉积正极材料。该正极材料具有1~8层所述石墨烯状碳沉积,其水分含量低于100ppm;其硫含量小于80ppm,优选低于60ppm,更优选低于40ppm,更进一步优选低于20ppm。碳沉积物中的硫杂质会生成离子,这些离子会在碳沉积物表面形成对ph敏感的物质造成有害影响,比如导致非最佳电极孔隙率、弯曲度、密度、电阻率或循环性能。这可以用zeta电位法(测量材料的表面电荷)测定。不受任何理论束缚,本发明人相信,当碳沉积、优选石墨烯状碳沉积正极材料的颗粒分散在水和/或有机溶液中时,颗粒间会发生排斥现象,这与颗粒彼此非常接近时在水和/或有机溶液中的粒子表面电荷有关。事实上,当碳沉积正极材料的粒子彼此变得非常接近时,它们的表面电荷开始通过排斥相邻粒子而起作用,从而阻止粒子的紧密堆积,从而限制电极的最大压实。极低硫含量允许碳沉积正极材料,优选二次球性团聚体的形式,对环境ph不太敏感,因此更适合通过溶剂系浆料涂覆加工,包括水性浆料涂覆。这是为什么本发明的另一个目的在于使用通过本发明方法得到的一种碳沉积正极材料。其碳含量低于2.5wt%;优选二次球性团聚体的形式;其硫含量小于80ppm,优选低于60ppm,更优选低于40ppm,更进一步优选低于20ppm;同时其在中性ph水溶液中的zeta电位绝对值小于20mv,优选小于15mv,更优选小于10mv,更进一步优选小于5mv。这是为什么本发明的另一个目的在于使用通过本发明方法得到的一种石墨烯状碳沉积正极材料。该正极材料具有1~8层所述石墨烯状碳沉积;优选二次球性团聚体的形式;其硫含量小于80ppm,优选低于60ppm,更优选低于40ppm,更进一步优选低于20ppm;同时其在中性ph水溶液中的zeta电位绝对值小于20mv,优选小于15mv,更优选小于10mv,更进一步优选小于5mv。含锂金属复合氧化物正极材料(称为“氧化物正极”),例如层状结构或尖晶石结构氧化物,已经被报道其表面修饰和包覆提高了它们的性能,例如限制容量衰减、阻抗增大、过渡金属溶解、表面非晶化和钝化。用锂金属磷酸盐(优选碳沉积的)包覆氧化物正极来改善它们的热稳定性和电化学性能,特别应该提到的是包覆材料为碳沉积lifepo4的。在本发明开发过程中,发明人还发现,本发明的碳沉积正极材料包覆氧化物正极以及极低的硫杂质含量,特别有利于保持优异的高温性能,包括循环性能和最佳面积比阻抗(asi)。这是为什么本发明的另一个目的在于一种锂二次电池的正极,其包含至少一种氧化物正极和至少一种通过本发明方法得到的碳沉积正极材料,其碳含量小于2.5wt%,其硫含量小于80ppm,优选小于60ppm,更优选小于40ppm,更进一步优选小于20ppm。它用于制备高温电化学性能优异、热稳定性改善的锂二次电池正极,该正极中含有氧化物正极。这是为什么本发明的进一步目的在于一种锂二次电池的正极,其包含至少一种氧化物正极和至少一种通过本发明得到的石墨烯状碳沉积正极材料,其含有1~8层所述的石墨烯状碳沉积,其其硫含量小于80ppm,优选小于60ppm,更优选小于40ppm,更进一步优选小于20ppm;它用于制备高温电化学性能优异、热稳定性改善的锂二次电池正极,该正极中含有氧化物正极。在一个非限制性实施例中,相对于氧化物的质量,本发明的碳沉积正极材料的占比在0.5~30wt%之间,优选在2~20wt%之间,更优选在4~10wt%之间。在进一步的非限制性实施例中,氧化物正极的d50在5~20μm之间,碳沉积正极材料由一次粒子组成,任选地,以二次球性团聚体形式,其一次粒子地平均粒径在25~250nm之间,优选50~150nm之间,更优选70~130nm之间。而且,氧化物正极的比表面积在0.01~1m2/g,优选在0.05~0.7m2/g,更优选在0.1~0.4m2/g。除了硫杂质含量低外,本发明人还发现,碳沉积、特别是石墨烯状碳沉积的高电导率,对于制备锂二次电池的正极是有益的,所述锂二次电池包括至少一个涂覆有本发明的碳沉积正极材料和至少一个氧化物正极。不受任何理论束缚,发明人相信碳沉积的高电导率允许电流更均匀地通过,从而避免形成过大的界面反应阻抗;发明人还相信碳沉积的高电导率允许最优面积比阻抗(asi),从而可以通过本质上安全的磷酸盐正极材料保持其热安全性上的有益影响。氧化物正极,比如licoo2、lini1/3mn1/3co1/3o2或lini0.8co0.15al0.05的电导率在10-4到10-2s/cm,在本发明的碳沉积正极材料中,导电率超过5.10-2s/cm,优选超过10-1s/cm。这是为什么本发明的进一步目的在于一种锂二次电池的正极,其包括至少一种氧化物(粉末电导率σ_ox)以及至少一种通过本发明方法得到的碳沉积正极材料(粉末电导率σ_碳),其粉末电导率比值(σ_碳/σ_ox)范围为1至104,优选范围为10至103。在氧化物正极的非限制性实施例中,可使用的氧化物正极包括licoo2、nmc111(lini1/3mn1/3co1/3o2)、nmc433、nmc532、nmc622、nmc811、nca(lini0.8co0.15al0.05)、lini0.5co0.5o2、lini0.5mn1.5o4、limn2o4、limn1.9al0.1o4、lini0.43mn1.57o4、富锂和富锰层状氧化物xli2mno3·(1-x)li(ni,mn,co)o2(0≤x≤0.15)、缺锂的li1-x(ni,mn,co)o2、linio2、稳定的linio2基正极材料(例如camxpowerllcc公司开发的am-7platform)、lixmgynio2(0.9<x<1.3,0.01<y<0.1,0.91<x+y<1.3)、晶界富co的li1.01mg0.024ni0.88co0.12o2.03或li1.01mg0.023ni0.93co0.07o2.03、富ni层状复合氧化物li(ni1-y-zcoymnz)o2(1-y-z≥0.8),还有核-壳结构或有浓度梯度分布的核-壳结构,比如核是lixmgynio2(0.9<x<1.3,0.01<y<0.1,0.91<x+y<1.3)和壳是liacobo2(0.7<a<1.3,and0.9<b<1.2)的核-壳结构、核是富镍li(ni0.89co0.01mn0.1)o2和壳是缺ni富mnli(ni0.61co0.09mn0.3)o2的全浓度梯度分布(fcg)li(ni0.65co0.08mn0.27)o2、或者fcg的li(ni0.77co0.12mn0.11)o2。氧化物正极还可以有涂覆层,比如陶瓷涂层,例如al2o3、alf3、lialf4、zro2、以及tio2;比如功能化有机涂层,例如有机硅。涂覆能通过例如液相、溶胶凝胶、机械工艺、溅射、以及原子层沉积实现。在用合适的混合技术预先混合过程中,或在电极涂覆的制备过程中,可以获得碳沉积正极材料涂覆的氧化物正极。碳沉积正极材料还可以以任意比例和任意其它正极活性材料混合,优选地与含锂金属复合氧化物混合,其目的在于获得可能比任何单独的化合物更平衡的性能。本发明的低硫高导电性碳沉积的正极材料特别有益于使用这种正极材料的锂二次电池,以及优选的实施例。例如,本发明的c-lifepo4可以与nmc811(占总正极材料含量的50wt%)共混,用于高能量密度、高功率、循环寿命改善的、低温度性能好、安全的sli(气动-照明-点火)锂二次电池的研制。本发明的c-lifepo4还可以与nmc622(占总正极材料含量的20wt%)共混,用于高能量密度、低充电态(soc)下充放电脉冲功率性能(以更低的asi值测量)提高的、高温循环性能改善的锂二次电池的研制,该电池应用于phev。同时,本发明的c-life0.3mn0.7po4可以与li(ni0.45co0.1mn1.45)o4(占总正极材料含量的50wt%)共混,用于氧化物锰溶解稳定性、在更高放电倍率(超过1c,相对纯c-life0.3mn0.7po4)下能量密度、功率密度、振实密度以及高温循环性能都改善的锂二次电池的研制,该电池应用于3c市场。本发明的另一个目的在于由至少两种电极和至少一种电解质构成的锂二次电池,其特征在于至少这些电极的其中之一,优选正极,含有至少一种本发明的碳沉积碱金属聚氧阴离子物。锂二次电池的非限制性实施例包括锂金属二次电池、锂离子二次电池、锂金属聚合物二次电池和锂离子聚合物二次电池。根据本发明的制造正极的方法没有特别限制,并且可以使用本领域已知的任何常规方法进行。在一个实施例中,在集流体上敷加包含至少一种碳沉积碱金属氧阴离子物的正极浆料,然后干燥所敷的浆料,来制造本发明的正极。在这种情况下,可以加入少量的导电剂和/或粘合剂。正极还可以通过干燥混合的和/或涂覆的组分来制备,包括挤压、压实、机械加工、层压、喷涂和电喷雾技术。在一个非限制性实施例中,导电剂是碳材料,例如但不限于,碳颗粒、碳纤维和碳纳米纤维、气相生长碳纤维、碳纳米管、石墨烯、氧化石墨烯、或任何它们的衍生物,包括有助于分散的有机功能团嫁接物(如羧酸酯、磺酸、膦酸酯离子基团),以及以上任意的混合物。根据一种有利的方法,电解质是固定在微孔分离器中并在溶液中含有一种或多种金属盐的极性液体。优选地,这些金属盐中的至少一种是锂盐。在另一个实施方案中,电解质是聚合物,它是溶剂化或不溶剂化的,任选地,它被含有一种或多种金属盐的极性液体在溶液中塑化或凝胶化。用于粘合电极的或作为电解质的聚合物,有利地是聚醚、聚烯烃、聚酯、基于丙烯酸酯的聚合物、苯乙烯、环氧乙烷、环氧丙烷、乙烯基或乙烯基醚单元、丙烯腈基聚合物、含偏二氟乙烯的聚合物(cf2=ch2)、六氟丙烯(cf2=cf-cf3)、或者三氟乙烯(cf2=chf)单体,和它们的任意衍生物。根据另一个有利的方法,至少一个负电极是金属锂、锂合金,特别是铝、锑、锌、锡的锂合金,可能是锂氧化物与纳米分子的混合物,或碳基插入化合物,特别是合成或天然石墨,或者锂和铁、钴或锰的双氮化合物、或硅基插入化合物,任选地嵌入碳基体中,或钛酸锂(li4ti5o12),及其它们的任意衍生物。锂二次电池的电解质含有溶剂,其包含碳酸乙烯酯或碳酸丙烯酯、碳酸氟乙烯、碳酸二氟乙烯、双(2,2,2-三氟乙基)碳酸酯、2,2,3,4,4,4-六氟丁基碳酸甲酯、偏碳酸乙烯酯,还有具有1至4个碳原子的碳酸烷基酯、碳酸二甲酯、γ-丁内酯、丙酸甲酯、乙酸甲酯、丁酸甲酯、二氟乙酸乙酯、亚硫酸亚乙酯、硫酸乙烯酯、三(三甲基硅)亚磷酸酯、四烷基磺酰胺,还有分子量小于或等于5000的单、二、三、四或低聚乙二醇的α-ω二烷基醚,还有磺内酯,例如丙烷磺内酯,以及上述溶剂的任意混合物。电解质通常还含有lipf6,其全部或部分被阴离子盐所取代,优选锂盐,从而改善锂二次电池性能,特别是安全性、低温性能、高温循环性能、抑制内阻增加、促进负极钝化层形成。锂盐优选自双草酸硼酸锂、lipo2f2、lin(so2f)2、lin(so2f)(so2cnf2n+1)(n为1~4,优选1和2)、lin(so2cnf2n+1)(so2cmf2m+1)(n和m分别为1~4)、反应性阴离子和包含它们的聚合物,例如,没有任何限制,苯乙烯-so2n(li)so2cnf2n+1(n为0~4,优选为0~2)。除了锂金属聚合物电池不使用外,lipf6可以被1~30mol%的那些盐取代,优选5~25mol%,更优选10~20mol%。优选地,lipf6取代选择自lipo2f2、lin(so2f)2、lin(so2f)(so2cf3)、lin(so2cf3)2、lin(so2c2f5)2,进一步优选自lipo2f2和lin(so2f)2,更进一步优选自lin(so2f)2。在本发明的碳沉积正极材料与高电压含锂金属复合氧化物混合的锂离子二次电池高温测试中,其中包含至少95at%的选自镍、钴、锰及其混合物的一种金属,发明人意识到,在一些情况下过量的硫杂质可能改变电解液的性质,对电极产气和阻抗产生负面影响。该电解液含有被至少一种fe2po2-或fso2-自由基的离域阴离子部分取代的lipf6,特别是lipo2f2和lin(so2f)2。这是为什么本发明的另一个目的在于一种含有至少一种含锂金属复合氧化物的锂离子二次电池,以及通过本发明方法得到的至少一种碳沉积正极材料,其用于制备高温电化学性能改善的锂离子二次电池。其中包含至少95at%的选自镍、钴、锰及其混合物的一种金属,其中电解液包含至多30%被至少一种选自lipo2f2和lin(so2f)2之中的锂盐取代的lipf6;同时,通过本发明方法得到的至少一种碳沉积正极材料,其碳含量少于2.5wt%,其硫含量小于80ppm,优选小于60ppm,更优选小于40ppm,更进一步优选小于20ppm。这是为什么本发明的进一步目的在于一种含有至少一种含锂金属复合氧化物的锂离子二次电池,以及通过本发明方法得到的石墨烯状碳沉积正极材料,其用于制备高温电化学性能改善的锂离子二次电池。其中包含至少95at%的选自镍、钴、锰及其混合物的一种金属,其中电解液包含至多30%被至少一种选自lipo2f2和lin(so2f)2之中的锂盐取代的lipf6;同时,通过本发明方法得到的石墨烯状碳沉积正极材料,其具有1~8层所述石墨烯状碳沉积,其硫含量小于80ppm,优选小于60ppm,更优选小于40ppm,更进一步优选小于20ppm。此外,虽然根据上述方法得到的二次电池外形不限于任何特定形状,但可以是圆柱形、多边形、软包或一种有利的形状。本公开和要求的所有组合物和/或方法可以根据本公开而无需过度实验而被制造和执行。虽然本发明的组成和方法已在优选实施例中描述,但对于本领域的技术人员来说,显而易见的是,在不脱离本发明的概念、精神和范围的情况下,本文所描述的组成和/或方法、以及本方法的步骤或后续步骤可以有变化。对本领域的技术人员来说,所有类似的取代和修改被认为是在所附权利要求所定义的本发明的精神、范围和概念之内。此处前后所有的参考文献均已并入参考部分。下面更详细地阐述用于确定本文所述产品的各种性能和参数的合适方法。测量方法:·bet面积按照diniso9277进行测定。·粒径分布在此使用马尔文型号为mastersizers的激光粒度仪通过激光衍射测定。为了测定psd,少量含碳材料样品与几滴湿润剂和少量水混合。如此制备的样品加入仪器的存样器中(mastersizers),100%强度的超声处理5分钟后,泵速和搅拌速度设定在40%,开始测量。参考:iso13320(2009)/iso14887·碳含量可以用所谓的leco方法测量,使用leco公司(美国密歇根州圣约瑟夫)的lecocr12碳分析仪,或用eltra测量法,使用eltracs2000型号的c/s分析仪。·硫含量使用用eltracs2000型号的c/s分析仪测定。·水分含量用arizona设备公司的型号为vaporxl的仪器测定。·raman分析使用horiba公司的labram-aramis的显微拉曼光谱仪用632.8nmhene激光测定。id/ig比例基于所谓d峰和g峰强度的比值。这些峰是碳材料的特征峰,分别在1350cm-1和1580cm-1位置。·磁性杂质含量测试是取150g碳沉积正极材料,加入干净的1升塑料瓶中,加入400g异丙醇,再加入一个彻底洗净的直径约1.5cm、长约5cm的、特氟龙包覆的超过5000高斯强度的fe-nd-b磁棒。然后密封该塑料瓶并放置在滚动机上以100rpm速度滚动30分钟。之后,在不与污染物质接触情况下,从瓶中取出磁棒,用异丙醇简单冲洗后转移至一个可密封的、干净的50mlpp或pe试管中。在试验管中用异丙醇进一步冲洗棒磁铁,最后用异丙醇填充并密封,然后放在超声浴中,在至少50khz的超声频率和在20w至40w每升水的特定超声功率下处理20min,从而轻柔而不破坏特氟龙涂覆层地彻底清洗磁棒表面。在试管内用异丙醇对磁棒进行漂洗后,试管在超声浴中再次处理20min,进行最后冲洗,然后倒出异丙醇。这次处理的目的是除去所有通过表面作用附着在磁棒或磁性颗粒上的顺磁性锂过渡金属磷酸盐颗粒,但不除去紧密附着在磁棒上的反磁性污染物颗粒,同时不暴露磁棒以避免来自环境的磁性粒子污染。然后试管连同其中的磁棒用4.5ml35%的盐酸和1.5ml65%硝酸的混合酸在80~90℃加热回流2小时。冷却后,从提取液中移出磁棒,并用软化水冲洗到试管内,最后用软化子水填充至50ml刻度。然后加入合适的稀释液用icp-oes测定提取液中的铁含量,相对于150g起始样品以ppm或ppb表示。·压实密度和粉末电阻率同时用三菱mcp-pd51型号的压片机测定。该仪器带有loresta-gp、mcp-t610阻抗计,其安装在氮气手套箱,以避免氧气和湿度的潜在干扰。压片机的液压操作用手动液压机enerpacpn80-apj(最大10000psi/700bar)。在上述设备的制造商推荐设置条件下测量4g本发明的样品。粉末电阻率根据以下公式计算:粉末电阻率[ω·cm]=电阻[ω]×厚度[cm]×rcf其中rcf值是决定于仪器的值,已根据制造商的建议对每个样品进行了测定。压实密度根据以下公式计算:r=样品片的直径·hppc(混合脉冲功率容量)测试是国际化标准方法,它由美国能源部(doe)规定(freedomcarbatterytestmanualforpower-assisthybridelectricvehicles,doe/id-11069,2003)。本发明将通过以下非限制性实施例进一步说明。实施例对比实施例1在连接有循环罐、装有400μm钇稳定氧化锆球的耐驰minicer型号的搅拌磨中,以去离子除氧水作为载流液体,纳米研磨碳沉积lifepo4(北大先行科技产业有限公司,p600a型号产品,碳含量1.37wt%,d90为4.9μm)。为避免金属污染,该搅拌磨配有陶瓷研磨腔。水中含有相对p600a占比0.5wt%的吐温20(聚氧乙烯山梨糖醇单月桂酸酯,croda公司产品)表面活性剂。以0.46kwh每公斤p600a(热量通过与研磨组件外壁的冷却水排出)的研磨能量研磨120分钟后,用psd分析仪测量浆料(ac-1)样品,得到平均粒度为184nm的lifepo4颗粒,用tem分析证实在纳米研磨过程中初始碳沉积从lifepo4表面磨掉了,并以碳渣形式存在于物料中。纳米化的lifepo4在真空旋转下蒸发水分后,在真空炉中100℃烘干过夜,然后再用实验实的旋转磨中解团聚(装有“无铁”转换配件的fritschpulverisette14)。按实施例5公开的方法装配金属锂负极的液态电解质电池,正极组成是lifepo4/粘结剂/科琴黑ec-300j为70/10/20wt%,为了确保含有纳米化的低电导率lifepo4的导电网络的渗透性,有必要增加较多高表面积的碳。该电池正极的装载量是2.77mg/cm2,用每cm2的正极面积上的活性物质mg数来表示。在25℃、c/25进行电化学测量时,实现122mah/g的可逆比容量。将30g纳米化lifepo4放置于可旋转管式炉中(郑州cy科学设备公司,型号cy-r1200x-100ic),如在us2002/0195591a1(实施例2)中公开的方法处理混合物,炉管通干燥氩气,以10℃/min速度加热至200℃,保持该温度30min,然后用94%氩气和6%丙烯的混合气体通入炉管进行热cvd过程。在以10℃/min速度加热至675℃后,保温1小时,获得碳沉积lifepo4,用leco法测量其碳含量为2.65wt.%。按实施例5公开的方法装配金属锂负极的液态电解质电池,正极组成是c-lifepo4/粘结剂/碳为88/6/6wt%,装载量为4.6mg/cm2。在25℃、c/5进行电化学测量时,实现158mah/g的初始放电比容量。按实施例5公开的方法还装配了碳负极和相同正极的液态电解质锂离子电池(电池1)。对比实施例2按对比实施例1所述重复p600a纳米研磨过程,但用异丙醇代替液体水作为载流液体,得到浆料ac-2,其中lifepo4颗粒的d50为186nm。然后用丙烯气体进行热cvd过程以形成碳沉积的lifepo4,其中碳含量2.73wt%。按实施例5公开的方法装配金属锂作为负极的液态电解质电池,正极组成时c-lifepo4/粘结剂/碳为88/6/6wt%,装载量为4.6mg/cm2。在25℃、c/5进行电化学测量时,实现157mah/g的初始放电比容量。按实施例5公开的方法还装配了碳负极和相同正极的液态电解质锂离子电池(电池2)。然后在c/4、60℃、2~3.6v之间静态循环测试电池1和电池2,循环曲线如图1所示。结果表明包含异丙醇(曲线a)而不是水(曲线b)纳米研磨步骤的c-lifepo4在60℃下容量衰减降低了。实施例1称量fepo4·2h2o(200g,来自长沙合康化工公司,电池级,d90为2.92μm)、li2co3(摩尔比2:1,来自成都化学化工公司,电池级,d90为2.84μm)、brij35(占fepo4·2h2o的3.5wt%,来自croda)、以及脱氧异丙醇(占fepo4·2h2o的50wt%),加入装有5mm氧化锆球的氧化锆圆柱形容器中,其中球/粉体料的重量比为2:1。在retsch型号为pm100的行星式球磨机中,转速400rpm、氩气气氛下球磨30分钟。研磨后,浆料在80℃下蒸发干燥。然后,按us2002/0195591a1公开的方法,混合物在通有干燥除氧氮气气流的管式炉(郑州cy科学仪器公司)中,以10℃/min加热速率升温至600℃,并在该温度下保温60min。得到了碳含量为0.38wt%(用leco测定)的碳沉积材料,用xrd分析测定其组成含有75.2wt%的lifepo4、残余有摩尔比为1:1的li3po4和fe3(po4)2相,用谱分析其中没有fe(ⅲ)。lifepo4的含量可以用转化率表示,即已得到的lifepo4除以理论量的比值,在本例中转化率即为75.2%。该材料称为材料-a1。重复合成过程,在氮气气氛下,转速为300rmp条件下,前驱体在retsch型号pm100的行星式球磨机中干法研磨60min。球磨机中装有球料比为3:1的10mm碳化钨球。然后经过类似的热处理过程,获得碳沉积材料,用leco测定其碳含量为0.33wt%,用xrd分析测定其lifepo4的转化率为75.2wt%,还残留有摩尔比为1:1的li3po4和fe3(po4)2相。该材料称为材料-a1-1。按实施例5公开的方法装配金属锂负极的液态电解质电池,正极组成是材料-a1/粘结剂/碳为88/6/6wt%,装载量为4.5mg/cm2。在25℃、c/5进行电化学测量时(假设容量等于lifepo4的理论容量),实现67mah/g的初始放电比容量,中值放电电压为2.85v。该结果表明材料-al电化学性能差。材料-a1是在水中纳米化,以水作为载流液体,如在对比实施例1中,使用300μm的钇稳定氧化锆球(吐温20为表面活性剂、纳米研磨90分钟,研磨能量0.48kwh每公斤材料-a1,得到平均一次粒子粒径为186nm的无碳沉积的纳米化颗粒,浆料a),材料-a1也是在异丙醇中纳米化,以异丙醇作为载流液体,如在对比实施例2中,使用300μm的钇稳定氧化锆球(吐温20为表面活性剂、纳米研磨90分钟,研磨能量0.44kwh每公斤材料-a1,得到平均一次粒子粒径为192nm的无碳沉积的纳米化颗粒,浆料b)。在这两种情况下,来自lifepo4表面的磨损碳都以碳渣形式残存在组分中。浆料a和浆料b用压缩氮气通过二流体喷嘴喷雾干燥(上海雅程仪器,配有惰性环的yc-015a型号喷雾干燥机),在喷雾干燥过程中,气体入口温度为200℃,气体出口温度为96℃。然后,在喷雾干燥后的浆料a和b的纳米颗粒上进行气相碳沉积得到样品c-a和c-b,如在对比实施例1中所述,但是在此使用97%氮气和3%乙炔气体的混合物而不是丙烯/氩气混合物。最后得到了碳沉积量(通过leco测量)如表1所示的碳沉积橄榄石lifepo4(通过xrd测定)。热cvd前后通过进行leco测量可以得到碳沉积量,从而很容易地纠正材料-a1中的残碳量。表1样品c-ac-bc-沉积wt%1.251.15id/ig比0.840.78在含有不同浓度的乙烯、丙烯、汽化苯的氮气中,在不同气流量下,样品b(喷雾干燥的在异丙醇为载流液体中纳米化的材料-a1)重复进行热cvd过程。leco测量表明,获得了碳沉积量在0.21~2.49wt%的c-lifepo4。按实施例5公开的方法装配金属锂负极的液态电解质电池,正极组成是材料-a1/粘结剂/碳为88/6/6wt%。通过c/5电化学测量得到的电极容量和初始放电比容量(第一次放电)如表2所示。还按实施例5公开的方法装配了碳为负极、相同正极的液态锂离子电池(样品c-a的电池3,样品c-b的电池4)。然后在c/4、60℃、2~3.6v之间静态循环测试电池3和电池4,循环曲线如图2所示。结果表明包含异丙醇(曲线a)而不是水(曲线b)纳米研磨步骤的c-lifepo4在60℃下容量衰减降低了。用合适的前驱体和化学计量比同样重复材料-a1的合成过程,通过后续的纳米研磨和热cvd步骤,得到了c-life0.97mg0.03po4(fepo4·2h2o、li2co3、以及mghpo4,转化率为74%,含碳0.35wt.%)、c-life0.3mn0.7po4(fe0.3mn0.7po4·2h2o、li2co3,转化率为75%,含碳0.38wt.%),c-limnpo4(mn3(po4)2、li3po4,转化率为69%,含碳0.27wt.%)表2样品c-ac-b电池34装载量(mg/cm2)4.84.71st放电容量(mah/g)162163如材料c-b一样(在异丙醇载流液体中纳米研磨、喷雾干燥、接着在乙炔碳源中热cvd)加工处理通过前驱体干法研磨得到的材料-a1-1,从而获得一个具有类似特点的材料,进一步用于负极是碳的液态电解质锂离子电池(正极装载量为4.8mg/cm2,1st放电容量为164mah/g)的正极材料。电池在c/4、60℃、2~3.6v条件下静态循环。循环400周后,前驱体通过干法研磨步骤得到的正极材料相比湿法研磨的,容量比初始放电容量低7%。实施例2如实施例1,重复材料-a1的合成过程,不同批的fepo4·2h2o(每次合成用500gfepo4·2h2o),然后在醇基中用200μm的钇稳定氧化锆球纳米研磨90min,接着喷雾干燥悬浊液。对于每一批,300g纳米化物料放置于回转窑(郑州cy科学仪器公司,型号cy-r200x-100ic)的炉管中,炉管中通入干燥氮气,以10℃/min加热速率升温至200℃,保温60min,然后连续通入汽化苯和氩气的混合气体(含体积比3%的苯)。以20℃/min速率升温至640℃后,保温1小时,获得碳沉积lifepo4。每批中的硫含量和碳含量通过碳/硫分析仪(leco公司)用燃烧分析法测定,结果见表3。按实施例5公开的方法装配负极为碳的液态电解质电池(电池5a-9a以及电池5b-9b),其中使用表3的c-lifepo4样品作为正极材料,正极组成是c-lifepo4/粘结剂/碳为88/6/6wt%。电池5a-9a进行高温存储测试,可以加速电池组件老化,并可以进行关键参数的影响评估。通过在c/5、25℃下的电化学测量,测定存储前的初始放电比容量,如表3所示。接着在25℃、c/10充电至3.6v后,电池在85℃存储3天,存储后再在25℃、c/5倍率下恢复放电容量,结果见表3。表3样品c1c2c3c4c5纳米化平均一次粒子粒径140142141139142c-lifepo4d50(μm)7.27.47.67.37.5c-lifepo4硫含量(ppm)745339713413c-沉积wt.%1.261.111.021.031.04s/c比(%)5.913.050.700.330.12bet7.86.86.26.16.1电池5a/b6a/b7a/b8a/b9a/b装载量(mg/cm2)4.74.64.64.64.7存储前比容量(mah/g)162162163163164存储后恢复容量(mah/g)93102142144146结果表明本发明的c-lifepo4中极低水平的硫杂质是确保c-lifepo4电化学性能优异的关键。对于样品c5,纳米化的一次粒子的sem图如图3所示,一次粒子的二次团聚体c-lifepo4的sem图如图4所示,碳沉积的tem图如图5所示。用拉曼分析样品c5的碳沉积纯度超过99.9%。电池5b-9b在c/1、60℃、2~3.6v条件下静态循环,循环曲线见图6(曲线a为样品c5,b为c4,c为c3,d为c2,e为c1)。该结果证明,为了得到高温性能优异的本发明碳沉积正极材料,材料中硫杂质含量必须极低。本实例获得的所有样品水分含量都小于100ppm,并在300℃真空下进一步干燥48小时使得水分含量低于10ppm,然后暴露于增湿器(owlstone公司,美国)10%相对湿度气氛中,同时监测样品重量。暴露于湿气气氛中120s后,水分含量结果如表4所示。表4样品c1c2c3c4c5水分含量(ppm)411256816343结果表明在本发明的c-lifepo4中极低水平的硫杂质有利于限制材料的吸水性。不受任何理论束缚,发明人相信与硫杂质的存在有关的吸湿性物质增加了表面的亲水性。在400ml异丙醇中,在有特氟龙包覆的fe-nb-b磁棒存在下,加入150gc-lifepo4样品搅拌,然后在酸性介质中预矿化磁棒吸出物,由icp-oes分析吸出物中的磁性物质含量,从而测定c-lifepo4样品的磁性杂质。选定的c-lifepo4样品的磁化强度由m-h曲线测定。磁性杂质以铁占样品总量ppb的形式表示,自发的磁化强度见表5。表5样品c1c2c3c4c5磁性杂质(ppb)7325091336842磁化强度(emu/g)0.019/0.0013/0.0006结果表明本发明的c-lifepo4中极低水平的硫杂质有利于限制磁性杂质含量。含有5wt.%固体c-lifepo4样品的水性悬浊液,在中性ph值下用zetaprobe(美国colloidaldynamics公司)进行zeta电位测量,结果见表6。表6样品c1c2c3c4c5zeta电位(mv)-32-29-14-9-5结果表明在本发明的c-lifepo4中极低水平的硫杂质有利于降低本发明的碳沉积材料的zeta电位绝对值。用合适的前驱体和化学计量比同样重复不同硫杂质含量的碳沉积材料的合成过程,得到了c-life0.97ca0.03po4(fepo4·2h2o、li2co3、以及cahpo4,碳沉积量在0.86~1.01wt.%,硫含量在10~686ppm)、c-life0.29mn0.68zn0.03po4(fe0.29mn0.68zn0.03po4·2h2o、li2co3,碳沉积量在0.91~0.96wt.%,硫含量在9~734ppm),c-limnpo4(mn3(po4)2、li3po4,碳沉积量在0.89~0.96wt.%,硫含量在12~603ppm)。高温存储和循环、吸水性测量、磁性杂质含量、自发磁化强度、以及zeta电位结果同样推断出,硫杂质含量小于80ppm以及优选地s/c比小于0.8%都对本发明的碳沉积材料的性能有利。作为对比实验,制备了十批lifepo4,在25℃、搅拌条件下,将0.3mlioh·h2o水溶液加到0.1mfeso4·7h2o和0.1mh3po4的50vol%水与50vol%dmso的溶液中。然后提高溶液温度至溶液的沸点,108到110℃,lifepo4开始沉淀。一个小时以后,过滤沉淀并用水洗涤沉淀。最后进行热处理,干燥的沉淀在弱还原性n2/h2(95/5)气流中,在500℃处理3小时。然后,将得到的十批样品在回转炉(郑州cy科学设备公司,型号cy-r200x-100ic)中进行热cvd步骤。炉管中通入干燥氮气,以10℃/min加热至200℃,保温60min,然后连续通入汽化苯和氩气的混合气体(含有3%体积比的苯)。以20℃/min加热至640℃之后,保温1小时,得到碳沉积的lifepo4。每批中的硫含量和碳含量用碳/硫分析仪(leco公司)通过燃烧分析法测定。得到了碳沉积量在0.92~1.08wt.%以及硫杂质含量在24~682ppm之间的c-lifepo4样品批。高温存储和循环测试结果同样推断出,硫杂质含量小于80ppm以及优选地s/c比小于0.8%都对通过气相碳源的热cvd工艺获得的碳沉积lifepo4的性能有利。实施例3如实施例1,用高纯的fepo4·2h2o(100kg)、电池级的li2co3(摩尔比1:2)、pluronicp-123(相对于fepo4·2h2o2wt.%;聚乙二醇-聚丙二醇-聚乙二醇三嵌段共聚物,basf产)重复材料-a1的合成过程。使用mastermill18型篮式研磨机(耐驰产),在200l脱气甲醇中研磨前驱物。溶剂蒸发后,将材料(称为材料-a3)置于陶瓷坩埚中,放入通入在干燥无氧氮气的辊道窑中,在600℃处理60分钟,然后在氮气中冷却、存储。得到了碳含量为0.35wt%(用leco测定)的碳沉积材料,用xrd分析测定其组成含有73.7wt%的lifepo4、残余有摩尔比为1:1的li3po4和fe3(po4)2相,用谱分析其中没有fe(ⅲ)。2kg的一批材料-a3进一步在脱气异丙醇载流液体中纳米研磨,使用连接有循环罐的耐驰alpha8neos搅拌磨。为避免金属污染,该搅拌磨配有陶瓷研磨腔,其中填充有100μm的钇稳定氧化锆球。异丙醇中含有相对于p600a总量为1wt.%的carbowax聚乙二醇4000表面活性剂(陶氏化学产)。以0.34kwh每公斤材料-a3的研磨能量纳米研磨60分钟,热量通过与研磨组件外壁的冷却水排出。浆料使用压缩氮气在装配combi-nozzle喷嘴的闭环mobileminor干燥机(geaniro产)中喷雾干燥。在喷雾干燥过程中,气体入口温度为275℃,气体出口温度为105℃。然后,喷雾干燥的材料在真空100℃干燥24小时并保存在氮气中。在回转窑中连续进行气相碳沉积操作。该回转窑装配有碳炉管,并连续通入丙烯和氮气的混合气体(含有体积比10%的丙烯),加热区温度为640℃,通过可控的螺旋喂料器输入喷雾干燥的物料,然后物料囤积在氮气保护的窑炉出口处,就得到了具有表7所示特性的碳沉积lifepo4。表7样品d1纳米研磨的平均一次粒子粒径92纳米研磨的颗粒psd跨度1.42c-lifepo4d50(μm)7.2c-lifepo4孔隙率(%)26c-lifepo4硫含量(ppm)29c-沉积wt.%0.95id/ig比0.75s/c比(%)0.31l/d1.05bet(m2/g)7.6电导率(s.cm-1)0.12含水量(ppm)82磁性杂质(ppb)86振实密度(g/cm3)1.67压实密度(g/cm3)2.65初始比容量(mah/g)(a)165.6(a)由如实施例1所公开的锂金属电池所确定使用配置了rj-5双喷嘴的nl-5型喷雾干燥机(ohkawarakakohki公司产)重复喷雾干燥实验,进气口温度在200~250℃之间,产生的一次颗粒组成的二次团聚体颗粒d50在约2~20μm之间,l/d球形度在约0.95~1.05之间。电池10在25℃下,以c/5倍率充电,c/5、c、5c以及10c倍率静态放电进行ragone测试,结果见表8。表8c-倍率c/5c5c10c正极比容量(mah/g)164.8147.9139.2113.6在c/5放电倍率下的放电曲线如图7所示。在-20℃下,以c/5倍率充电,以c/5倍率静态放电,电池11的正极比容量为112.1mah/g。重复样品d1的合成,但是材料-a3的纳米研磨过程在甲醇和乙醇而不是异丙醇的载流液体中进行,得到具有同等性能的碳沉积正极材料。在2kg的大量材料-a3上重复纳米研磨、喷雾干燥、热cvd过程,但是改变工艺参数,比如纳米研磨珠尺寸、时间、醇的化学组成、有效能量、表面活性剂、喷雾干燥进/出口温度、喷嘴、以及热cvd碳源等,从而制备具有不同特性的c-lifepo4。所有这些实验表明有可能不受任何限制地实现:一次粒子平均粒径在25~250nm、一次粒子粒径分布跨度小于2.5~0.5、c-lifepo4碳沉积量0.2~2.5wt.%、碳沉积的id/ig小于0.9~0.6、具有1~8层石墨烯状碳沉积、粉末电导率超过5.10-2~5.10-1s.cm-1、硫杂质含量小于80~20ppm、磁性杂质小于300~50ppb、水分含量小于200~20ppm、一次颗粒的二次团聚体的bet小于11~5m2/g、孔隙率5~40%、d50在2~30μm、跨度小于3~1、粉末压实超过2.4~2.8g/cm3。使用本发明中的不同批次c-lifepo4作为正极材料的电池品质表明,在25℃下,有可能实现c/5倍率放电容量159~169mah/g,1c倍率放电容量145~155mah/g,5c倍率放电容量130~145mah/g;在-20℃下,有可能实现c/5倍率放电容量100~140mah/g。重复样品d1的合成,但是作为热cvd碳源的丙烯被聚乙烯(pe)裂解产生的气流所替代。该聚乙烯块在氮气气流下,在600℃的热解反应器中裂解。进一步的实验在催化反应器中进行额外的重整步骤,其中裂解的聚乙烯气流进一步通过600℃的y型沸石催化床,总芳香族含量从约0.5wt.%增加到约39wt.%。结果如表9所示。表9热cvd碳源pe裂解pe裂解+重整碳源中芳香族含量(wt.%)0.4239.3c-沉积含量(wt.%)1.111.14c-沉积id/ig比0.820.70c-沉积电导率(s.cm-1)0.0730.134重复样品d1的合成,在纳米研磨步骤前,额外添加相对于材料-a32wt.%的色素碳黑fw200(orion工程碳有限公司产)。在喷雾干燥和热cvd步骤后,得到的c-lifepo4粉末压实密度提高8.7%,类似于电池11的锂离子电池显示在-20℃下、c/5静态倍率放电时,正极比容量提升了6.8%。重复样品d1的合成,在纳米研磨步骤前,额外添加相对于材料-a30.25wt.%的苯基三甲氧基硅烷。在喷雾干燥和热cvd步骤后,用使用样品d1为正极材料的锂离子电池为基准,使用该材料的类似于电池10的锂离子电池显示,在2~3.6v、60℃、1c静态循环时,2000次循环后的容量衰减降低了9.3%。额外添加1wt.%的tyzornpz(正丙醇中的锆酸正丙酯,dorfketal化学品公司产)进行重复实验,显示在60℃循环2000次后也能有效地降低容量衰减。重复样品d1的合成,但是在纳米研磨步骤之前,材料-a3在q-03无金属的循环搅拌磨(unionprocess公司产)中预研磨15分钟,该搅拌磨中填充由6mm钇稳定氧化锆球。d90从初始22μm降低至1.1μm,接着浆料在耐驰alpha8neos搅拌磨中的纳米研磨40分钟。得到类似的平均粒径为94nm的纳米化颗粒,但是颗粒分布跨度降低至1.03。而且,通过预研磨步骤使总比研磨能量降低了28%,同时昂贵细纳米研磨珠的磨损(用icp-oes分析法测量纳米研磨后的浆料中锆的含量来确定)降低了36%,对工艺成本有良好的影响。在经过类似于样品d1的合成过程(喷雾干燥和热cvd)之后,用类似于电池10的锂离子电池进行ragone测试,结果表明纳米化的颗粒降低了颗粒粒径分布跨度,提高了材料功率性能,例如,在10c倍率放电下,正极容量提升约17%。通过优化纳米研磨过程参数(比如研磨球大小、填充量、材料-a装载量、进行多步纳米研磨、预研磨阶段、表面活性剂选择、纳米化材料平均粒径或者研磨能量),发明人证明有可能在跨度0.3~3之间合成纳米化材料-a。重复样品d1的合成,但是在压滤机中回收纳米化材料-a3(有效研磨能量为0.49kwh每公斤材料-a3),滤饼在真空100℃干燥24小时,并保存于氮气气氛。得到平均一次粒子粒径为81nm的弱团聚纳米化颗粒,进一步在650℃用苯蒸汽/氮气作为碳源的混合气体中进行热cvd步骤。得到的c-lifepo4命名为样品d2,其中碳沉积含量1.4wt.%,bet为13.3m2/g,硫含量33ppm,id/ig比为0.68,导电率为0.14s.cm-1,压实密度为2.44g/cm3,水分含量为34ppm,磁性杂质含量为96ppb。用合适的前驱体和合适化学计量比同样重复材料-a3的合成过程,并进行相关的实验,通过后续的纳米研磨和热cvd过程,得到了c-life0.97zn0.03po4、c-life0.3mn0.7po4、c-life0.33mn0.64mg0.03po4、c-life0.08mn0.88co0.04po4、c-limnpo4,从而确认了本发明的碳沉积材料的益处。实施例4按实施例5公开的方法制备混合电极涂层(称为涂层4.1)。使用实施例3中的c-lifepo4样品d2与licoo2(lco983ha,北大先行产,d5014.3μm,占总正极材料的95wt.%)混合物作为正极活性材料。正极组成(lco:c-lifepo4)/粘结剂/碳为88/6/6wt.%。同时还制备了仅用lco983ha为正极活性材料的类似参考电极涂层(称为涂层4.2)。进一步地还制备了一个具有相同正极组成的混合电极涂层(称为涂层4.3),只是其中正极活性物质是除了硫含量386ppm不同,其余都类似样品d2的c-lifepo4(称为涂层d3)。按实施例5公开的方法装配碳作为负极的液态电解质锂离子电池。电池在c/1、60℃、2.6~4.35v之间静态循环测试。涂层4.1(曲线b)、4.2(曲线a)以及4.3(曲线c)的循环曲线如图8所示。结果表明,本发明的碳沉积正极材料用作氧化物正极涂层,其中极低的硫杂质含量有利于在高温下保持优异的性能。含有涂层4.1(混合正极)和涂层4.2(纯lco正极)的类似电池(3),在充电至4.3v(c/10倍率)后,在60℃进行针刺测试(1m/min),有混合电极的电池通过测试(0/3失败),那些纯lco的电池快速着火,没有通过测试(3/3失败)。将lco983ha替换为具有licoo2包覆层的核-壳li1.05mg0.025nio2(称为核-壳取代lno,根据实施例7中us7381496方法制备,5mol%licoo2,样品d2和d3的混合电极全部正极材料的92wt.%),制备了类似的电极涂层及其相应的锂离子电池。含有c-lifepo4样品d2和d3的混合电极表现出更好的循环性能(c/1、60℃、2.8~4.3v之间静态循环测试),相较于单纯使用核-壳取代lno正极材料的电极,混合电池在300周循环后的容量衰减减少了88%(样品d2)和72%(样品d3)。重复实施例3中样品d2的合成过程,但是压滤后得到的纳米化材料-a3在水中与6wt.%的乳糖混合,而不是进行热cvd步骤。干燥后,通过在氮气气流下,700℃1小时的热处理过程进行碳沉积,得到c-lifepo4(称为样品dref),其中碳沉积含量为1.32wt.%,电导率约为10-3s.cm,该材料用于制备同样的混合电极涂层和锂离子电池。分别使用c-lifepo4样品d2和样品dref,装配成类似的(lco:c-lifepo4)混合电极涂层的锂离子电池,用于进行交流阻抗测试。测试在25℃,3.7v电压下,增加放电电流倍率。相对于3.7v下纯lco983ha的类似锂离子电池的dc阻抗,结果见表10所示,同时表1中还有样品d2和样品dref相对于lco983ha的电导率比值(σ_carbon/σ_ox)。表10c-倍率1c5c10c20c30cσ_carbon/σ_ox相对dc阻抗d2(%)<2<3-4-6-22>10相对dc阻抗dref(%)6183498234<10-1结果表明,本发明的碳沉积正极材料用作氧化物正极涂层,有利于提高电导率,有利于改善使用该混合电极的电池的功率特性。将lco983ha替换为全浓度梯度分布(fcg)的nmc811氧化物正极材料(posco公司产,占含有样品d2的混合电极全部正极材料的92wt.%),制备了类似的电极涂层及其相应的锂离子电池。这些电池按实施例2公开的过程(25℃、c/10充电至4.35v后),在85℃存储3天进行存储测试。相对于使用纯fcgnmc811正极材料的电极,混合电极表现出更好的存储性能,存储后混合电极的容量损失减小了71%。用c-lifepo4样品d3(硫含量356ppm)代替样品d2(硫含量33ppm)的混合电极进行了同样的存储测试,结果证实硫杂质含量低是有益处的。使用表面处理后的fcgnmc811可以改善锂离子电池的性能,例如用原子层沉积获得氧化铝包覆层(在间歇性流化床反应器中从前驱体三甲基铝得到约15nm厚的al2o3沉积),同时还保持了具有本发明的极低硫碳沉积材料的混合电极在高温存储方面的优势。如实施例5,制备了一种用于phev电池的混合电极。其正极材料使用c-lifepo4与nmc532的混合物。其中c-lifepo4是如在实施例3中公开的、用nl-5喷雾干燥机(ohkawarakakohki公司产)干燥的c-lifepo4样品(d50为3.7um,硫含量为38ppm),nmc532(ecopro公司产)占总正极材料的88wt.%。正极组成(nmc532:c-lifepo4)/粘结剂/碳为88/6/6wt.%。同时还制备了以纯nmc532作为正极材料的同样的参比电极涂层。进一步地,还制备了具有相同正极组成地混合电极涂层,只是其中含有除了硫含量251ppm不同,其余都类似的c-lifepo4样品(d50为3.6μm)如实施例5公开的锂离子电池进行hppc脉冲功率特性试验(25℃,3c,10s充电脉冲)。hppc结果(用ω.cm2表示的面积比阻抗asi,与电池电压)如图9所示,混合电极(低硫正极材料)和纯nmc532电极测试结果分别在曲线a和曲线b上显示,高硫正极材料的混合电极的结果与低硫的相似。在60℃循环200周后(在2.8~4.4v之间c/1倍率静态循环),重复进行hppc试验,结果在图9中混合电极的曲线c(低硫)和曲线d(高硫)上显示。结果表明,极低硫杂质含量对本发明的碳沉积正极材料有益处,从而保持高温下优异的性能,同时由于测量到更低的asi值,碳沉积的高电导率改善了低充电态(soc)下的充放电脉冲功率特性。实施例5金属锂液态电解质电池的制备根据下述步骤制备金属锂液态电解质电池。至少一种本发明的正极材料、hfp-vf2共聚物(kynar的hsv900,atochem公司产)以及ebn-1010石墨粉(superior石墨公司产)一起在n-甲基吡咯烷酮(nmp)中用装有氧化锆球的罐磨机球磨10小时制备料浆,获得由正极/hfp-vf2/石墨组成重量比为80/10/10的分散体。获得的混合物随后使用gardner设备涂覆在涂碳铝箔(exopackadvancedcoating公司产)上,涂覆极片在80℃真空干燥24小时,然后保存于手套箱中。在手套箱中组装并封装“纽扣”型电池,由含有本发明的正极材料涂层的涂碳铝箔作为电池正极,锂片作为负极,以及浸润于ec/dec的1mlipf6混合液中的25μm厚的隔膜(celgard公司产)组成。锂离子液态电解质电池的制备根据以下步骤制备液态电解质锂离子电池。至少一种本发明的正极材料、hfp-vf2共聚物(kynar的hsv900,atochem公司产)以及ebn-1010石墨粉(superior石墨公司产)一起在n-甲基吡咯烷酮(nmp)中用装有氧化锆球的罐磨机球磨10小时制备料浆,获得由正极/hfp-vf2/石墨组成重量比为80/10/10的分散体。获得的混合物随后使用gardner设备涂覆在涂碳铝箔(exopackadvancedcoating公司产)上,涂覆极片在80℃真空干燥24小时,然后保存于手套箱中。在手套箱中组装并封装“纽扣”型电池,由含有本发明的正极材料涂层的涂碳铝箔作为电池正极,锂片作为负极,以及浸润于ec/dec的1mlipf6混合液中的25μm厚的隔膜(celgard公司产)组成。以上实施例仅用以说明本发明的技术方案而非对其进行限制,本领域的普通技术人员可以对本发明的技术方案进行修改或者等同替换,而不脱离本发明的精神和范围,本发明的保护范围应以权利要求书所述为准。当前第1页12