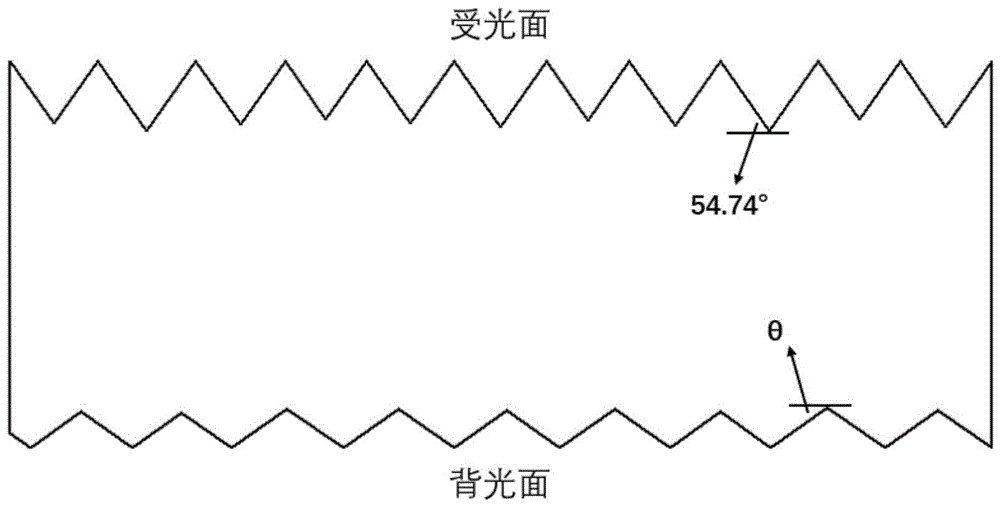
本发明属于半导体光伏领域。具体地,本发明涉及具有绒面结构的硅片及其制备方法和应用。
背景技术:
:随着化石能源的逐渐消耗和人类对于能源需求的不断提高,发展可持续的清洁能源迫在眉睫。太阳能电池是利用光伏效应将太阳光直接转变为电能的器件,是我们获取清洁能源的理想手段之一。提效降本是太阳能电池的研究目标,增加太阳能电池对光的吸收是太阳能电池提高效率的关键。为了增加太阳能电池对光线的吸收,需要在电池片表面进行制绒处理。目前单晶硅片上的绒面结构有纳米线、正金字塔、倒置金字塔等,综合陷光能力、钝化难易以及银浆填充等特性,倒置金字塔绒面结构是要优于前两者的。现有的倒置金字塔制绒工艺有金属催化刻蚀、掩模光刻等,而有希望用于产业的廉价方法是湿法的金属催化刻蚀。基于硅晶体的性质和金属催化刻蚀法的原理,在(100)硅片上所得到的倒置金字塔结构角度基本处于理论值54.74°附近。与电池片正面相比,其背光面的光照强度较小,现在常规的做法是硅片进行双面制绒后,再对制绒后的硅片背光面进行抛光处理。抛光后平整的电池片背光面更容易做到良好的背钝化,从而得到较好的电学性能。但是这种做法完全是出于对电学性能的考虑。事实上,忽略了背光面的光学结构对电池片整体的光学性能造成的影响。技术实现要素:因此,为了克服上述现有技术的缺陷,本发明综合考虑了背光面结构对电池片的光学性能和电学性能的影响,提供一种具有绒面结构的硅片,该具有绒面结构的硅片用于电池时具有更高的短路电流和转换效率。本发明还提供一种制备本发明的具有绒面结构的硅片的方法。同时,本发明还提供本发明的具有绒面结构的硅片在太阳能电池中的应用。第一方面,本发明提供一种具有绒面结构的硅片,所述硅片具有受光面和背光面,其中,所述受光面和所述背光面均具有底部边长为0.5-3.5μm的倒置金字塔结构的凹坑;所述受光面的倒置金字塔的侧壁与所述硅片宏观表面的平面的夹角为50-60°;所述背光面的倒置金字塔的侧壁与所述硅片宏观表面的平面的夹角为5-25°,可以参照图1所示的θ角。优选地,在本发明所述的具有绒面结构的硅片中,所述倒置金字塔结构的凹坑的底部边长为1-3μm。优选地,在本发明所述的具有绒面结构的硅片中,所述受光面的凹坑的底部总面积占所述受光面的总面积的60%以上;所述背光面的凹坑的底部总面积占所述背光面的总面积的60%以上。优选地,在本发明所述的具有绒面结构的硅片中,所述背光面的倒置金字塔的侧壁与所述硅片宏观表面的平面的夹角为10-23°。更优选地,在本发明所述的具有绒面结构的硅片中,所述背光面的倒置金字塔的侧壁与所述硅片宏观表面的平面的夹角为15-21°。进一步优选地,在本发明所述的具有绒面结构的硅片中,所述背光面的倒置金字塔的侧壁与所述硅片宏观表面的平面的夹角为17-19°。第二方面,本发明提供一种制备本发明的具有绒面结构的硅片的方法,包括如下步骤:(1)采用铜金属催化刻蚀的方法对硅片的受光面和背光面进行倒置金字塔制绒;(2)对经过步骤(1)制绒后的背光面进行单面刻蚀处理;所述单面刻蚀处理是通过化学刻蚀进行的。优选地,在本发明所述的方法中,所述化学刻蚀为酸化学刻蚀。优选地,在本发明所述的方法中,所述酸化学刻蚀是通过采用氢氟酸和硝酸的混合溶液进行的。优选地,在本发明所述的方法中,所述氢氟酸的浓度为1.0-3.5mol/L,所述硝酸的浓度为3.0-6.5mol/L,所述酸化学刻蚀在如下条件下进行:刻蚀温度为3-30℃,刻蚀时间为1-9min。更优选地,在本发明所述的方法中,所述氢氟酸的浓度为2.0-2.5mol/L,所述硝酸的浓度为4.5-5.0mol/L,所述酸化学刻蚀在如下条件下进行:刻蚀温度为15-25℃,刻蚀时间为3-9min。进一步优选地,在本发明所述的方法中,所述氢氟酸的浓度为2.21mol/L,所述硝酸的浓度为4.75mol/L,所述酸化学刻蚀在如下条件下进行:刻蚀温度为18-22℃,刻蚀时间为5-7min。优选地,在本发明所述的方法中,所述化学刻蚀为碱化学刻蚀。优选地,在本发明所述的方法中,所述碱化学刻蚀是通过采用氢氧化钠或氢氧化钾溶液进行的。优选地,在本发明所述的方法中,所述氢氧化钠或氢氧化钾溶液的浓度为1-10wt%,所述碱化学刻蚀在如下条件下进行:刻蚀温度为3-25℃,刻蚀时间为1-5min。第三方面,本发明提供本发明的具有绒面结构的硅片在太阳能电池中的应用。第四方面,本发明提供一种太阳能电池,包括减反射层(例如氮化硅层)、Si基底层、钝化层(例如SiO2)和金属层,其中,所述Si基底层由本发明的具有绒面结构的硅片形成。本发明具有如下有益效果:与常规背光面是抛光的结构相比,具有本发明的硅片的电池具有更高的短路电流和转换效率。不受限于任何理论,这主要得益于本发明的受光面和背光面结构的匹配所带来的整体光学性能的提升。此外,本发明提供的制备本发明的具有绒面结构的硅片的方法安全可靠、改造成本低,适用于任何类型的倒置金字塔制绒太阳能电池。附图说明以下,结合附图来详细说明本发明的实施方案,其中:图1为根据本发明一个实施方式的具有绒面结构的硅片的结构示意图;图2为包含根据本发明一个实施方式的硅片的模拟电池的结构示意图;图3为模拟电池中背光面的倒置金字塔的侧壁与硅片宏观表面的平面的夹角与光生电流的关系图;图4为模拟电池中背光面的倒置金字塔的侧壁与所述硅片宏观表面的平面的夹角分别为45°和18°时的光程增加率与波长的关系图;图5为本发明的实施例制备的具有本发明的硅片的电池的结构示意图;图6为本发明实施例1的具有绒面结构的硅片的背光面刻蚀1min后的SEM图;图7为本发明实施例2的具有绒面结构的硅片的背光面刻蚀5min后的SEM图;图8为本发明实施例3的具有绒面结构的硅片的背光面刻蚀8min后的SEM图;图9为本发明对比例1的具有绒面结构的硅片的背光面刻蚀10min后的SEM图;图10为本发明对比例2的具有绒面结构的硅片的背光面未经单面刻蚀处理的SEM图。具体实施方式下面结合具体实施方式对本发明进行进一步的详细描述,给出的实施例仅为了阐明本发明,而不是为了限制本发明的范围。为了增强光吸收,硅片正表面需要进行制绒处理,常规的倒置金字塔结构具有很好的陷光效果。进入硅片的光线在到达硅片底部后还会有内反射,为了增加对这部分内反射光线的利用,就要考虑背光面结构与正面结构的匹配问题。但常规工艺并没有考虑这方面的优化,而是进行背光面抛光以达到良好的背钝化效果。本发明人出乎意料地发现,对于倒置金字塔制绒的太阳能电池,其背光面不使用抛光面,而是使用5-25°的角度的倒置金字塔结构,可以与正面的50-60°的角度的倒置金字塔结构相匹配,从而得到更好的整体光学性能。同时本发明人出乎意料地发现,背光面的小角度倒置金字塔结构也不会对背钝化造成太大影响,最终能使电池片整体性能更优。与背光面抛光的电池片相比,具有本发明结构的电池片可以有更高的短路电流和相差不大的开路电压,得到的电池效率也更高。图1为根据本发明一个实施方式的具有绒面结构的硅片的结构示意图。本发明所提及的背光面的倒置金字塔的侧壁与硅片宏观表面的平面的夹角则可以参照图1所示的θ角。图2为包含根据本发明一个实施方式的硅片的模拟电池的结构示意图。在图2中示出的结构中,从上到下分别是:75nm厚的氮化硅层、200μm厚的Si基底、100nm厚的SiO2层。图3为模拟电池中背光面的倒置金字塔的侧壁与硅片宏观表面的平面的夹角与光生电流的关系图。图3示出了背光面的倒置金字塔结构角度θ随抛光减薄量的增加而减小,以及θ为18°时,光生电流密度达到最大值,θ为45°时,光生电流密度达到最小值。图4为模拟电池中背光面的倒置金字塔的侧壁与所述硅片宏观表面的平面的夹角分别为45°和18°时的光程增加率与波长的关系图。图4示出了在背光面倒置金字塔角度与受光面相匹配时,电池片在长波段的光程增加率会比较高,从而有更多的长波吸收。实施例1具体的电池片制作步骤如下:(1)用铜金属催化刻蚀的方法对(100)的单晶硅片进行双面制绒,其中硝酸铜的浓度为40mmol/L、HF浓度为5mol/L、双氧水浓度为0.8mol/L,在30℃下处理5min,得到受光面的倒置金字塔的侧壁与硅片宏观表面的平面的夹角约为55°,然后对制绒后的硅片进行清洗掺杂,制得pn结。(2)对经过步骤(1)制绒掺杂后的硅片的背光面进行单面刻蚀处理;所述单面刻蚀处理是通过酸刻蚀进行的;所述酸刻蚀液浓度为2.0mol/L的HF和4.5mol/L的HNO3混合水溶液;在15℃下处理1min。(3)用等离子体增强化学气相沉积(PECVD)在步骤(2)所得硅片的受光面制备80nm氮化硅钝化减反膜。(4)对步骤(3)所得硅片的背光面,先后用原子层沉积(ALD)和PECVD制备氧化铝/氮化硅钝化叠层。(5)对步骤(4)所得硅片的背光面,用激光对背面叠层膜进行开窗处理,以使得外层金属铝层能通过开窗处与硅片形成良好的欧姆接触。最后通过丝网印刷的方式印刷电极。本实施例制得的电池结构如图5所示。本实施例制得的具有绒面结构的硅片的背光面倒置金字塔结构如图6所示,特点是背光面倒置金字塔结构角度约为23°,底部边长约1-3μm。受光面的凹坑的底部总面积占所述受光面的总面积的约70%;背光面的凹坑的底部总面积占所述背光面的总面积的约70%。该电池的性能测试结果如表1所示。实施例2具体的电池片制作步骤如下:(1)用铜金属催化刻蚀的方法对(100)的单晶硅片进行双面制绒,其中硝酸铜的浓度为40mmol/L、HF浓度为5mol/L、双氧水浓度为0.8mol/L,在30℃下处理5min,得到受光面的倒置金字塔的侧壁与硅片宏观表面的平面的夹角约为55°,然后对制绒后的硅片进行清洗掺杂,制得pn结。(2)对经过步骤(1)制绒掺杂后的硅片的背光面进行单面刻蚀处理;所述单面刻蚀处理是通过酸刻蚀进行的;所述酸刻蚀液浓度为2.3mol/L的HF和4.7mol/L的HNO3混合水溶液;在20℃下处理5min。(3)用等离子体增强化学气相沉积(PECVD)在步骤(2)所得硅片的受光面制备80nm氮化硅钝化减反膜。(4)对步骤(3)所得硅片的背光面,先后用原子层沉积(ALD)和PECVD制备氧化铝/氮化硅钝化叠层。(5)对步骤(4)所得硅片的背光面,用激光对背面叠层膜进行开窗处理,以使得外层金属铝层能通过开窗处与硅片形成良好的欧姆接触。最后通过丝网印刷的方式印刷电极。本实施例制得的电池结构如图5所示。本实施例制得的具有绒面结构的硅片的背光面倒置金字塔结构如图7所示,特点是背光面倒置金字塔结构角度约为18°,底部边长约2-3μm。受光面的凹坑的底部总面积占所述受光面的总面积的约80%;背光面的凹坑的底部总面积占所述背光面的总面积的约80%。该电池的性能测试结果如表1所示。实施例3具体的电池片制作步骤如下:(1)用铜金属催化刻蚀的方法对(100)的单晶硅片进行双面制绒,其中硝酸铜的浓度为40mmol/L、HF浓度为5mol/L、双氧水浓度为0.8mol/L,在30℃下处理5min,得到受光面的倒置金字塔的侧壁与硅片宏观表面的平面的夹角约为55°,然后对制绒后的硅片进行清洗掺杂,制得pn结。(2)对经过步骤(1)制绒掺杂后的硅片的背光面进行单面刻蚀处理;所述单面刻蚀处理是通过酸刻蚀进行的;所述酸刻蚀液浓度为2.5mol/L的HF和5.0mol/L的HNO3混合水溶液;在25℃下处理8min。(3)用等离子体增强化学气相沉积(PECVD)在步骤(2)所得硅片的受光面制备80nm氮化硅钝化减反膜。(4)对步骤(3)所得硅片的背光面,先后用原子层沉积(ALD)和PECVD制备氧化铝/氮化硅钝化叠层。(5)对步骤(4)所得硅片的背光面,用激光对背面叠层膜进行开窗处理,以使得外层金属铝层能通过开窗处与硅片形成良好的欧姆接触。最后通过丝网印刷的方式印刷电极。本实施例制得的电池结构如图5所示。本实施例制得的具有绒面结构的硅片的背光面倒置金字塔结构如图8所示,特点是背光面倒置金字塔结构角度约为12°,底部边长约2-2.5μm。受光面的凹坑的底部总面积占所述受光面的总面积的约98%;背光面的凹坑的底部总面积占所述背光面的总面积的约98%。该电池的性能测试结果如表1所示。对比例1具体的电池片制作步骤如下:(1)用铜金属催化刻蚀的方法对(100)的单晶硅片进行双面制绒,其中硝酸铜的浓度为40mmol/L、HF浓度为5mol/L、双氧水浓度为0.8mol/L,在30℃下处理5min,得到受光面的倒置金字塔的侧壁与硅片宏观表面的平面的夹角约为55°,然后对制绒后的硅片进行清洗掺杂,制得pn结。(2)对经过步骤(1)制绒掺杂后的硅片的背光面进行单面刻蚀处理;所述单面刻蚀处理是通过酸刻蚀进行的;所述酸刻蚀液浓度为2.3mol/L的HF和4.7mol/L的HNO3混合水溶液;在20℃下处理10min。(3)用等离子体增强化学气相沉积(PECVD)在步骤(2)所得硅片的受光面制备80nm氮化硅钝化减反膜。(4)对步骤(3)所得硅片的背光面,先后用原子层沉积(ALD)和PECVD制备氧化铝/氮化硅钝化叠层。(5)对步骤(4)所得硅片的背光面,用激光对背面叠层膜进行开窗处理,以使得外层金属铝层能通过开窗处与硅片形成良好的欧姆接触。最后通过丝网印刷的方式印刷电极。本实施例制得的电池结构如图5所示。本实施例制得的具有绒面结构的硅片的背光面如图9所示。与前述实施例中的电池结构相比,该对比例的特点是背光面原来的倒置金字塔结构几乎完全被抛光。该电池的性能测试结果如表1所示。对比例2具体的电池片制作步骤如下:(1)用铜金属催化刻蚀的方法对(100)的单晶硅片进行双面制绒,其中硝酸铜的浓度为40mmol/L、HF浓度为5mol/L、双氧水浓度为0.8mol/L,在30℃下处理5min,得到受光面的倒置金字塔的侧壁与硅片宏观表面的平面的夹角约为55°,然后对制绒后的硅片进行清洗掺杂,制得pn结。(2)用等离子体增强化学气相沉积(PECVD)在步骤(1)所得硅片的受光面制备80nm氮化硅钝化减反膜。(3)对步骤(2)所得硅片的背光面,先后用原子层沉积(ALD)和PECVD制备氧化铝/氮化硅钝化叠层。(4)对步骤(3)所得硅片的背光面,用激光对背面叠层膜进行开窗处理,以使得外层金属铝层能通过开窗处与硅片形成良好的欧姆接触。最后通过丝网印刷的方式印刷电极。本实施例制得的电池结构如图5所示。本实施例制得的具有绒面结构的硅片的背光面倒置金字塔结构如图10所示。与前述实施例中的电池结构相比,该对比例的特点是背光面没有进行单面刻蚀处理,保留了原来角度约为55°的倒置金字塔结构。该电池的性能测试结果如表1所示。表1实施例1实施例2实施例3对比例1对比例2Uoc/V0.6770.6780.6810.6830.665Isc/A9.9329.9459.9379.8669.787FF/%81.7681.7181.3481.3681.13Eta/%22.5322.5822.5622.4721.64Uoc:开路电压;Isc:短路电流;FF:填充因子;Eta:效率。从上表的电池性能结果中可以看出,当太阳能电池背光面结构角度在所述范围10°至25°内,也就是实施例1、实施例2和实施例3,它们的短路电流和效率相比于对比例1和对比例2都有较大的提高。同时,实施例2背光面结构角度18°,也就是在所述更优选的17°至19°范围内,其最终的电池效率是上述实施例中最高的,这得益于这种正反面倒置金字塔结构组合处在光学性能和电学性能更优的平衡点。当前第1页1 2 3