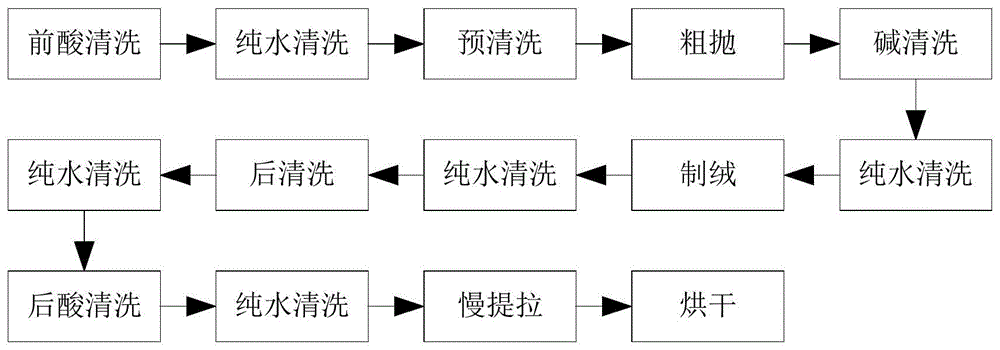
本发明涉及一种单晶硅制绒工艺及装置,属于晶硅太阳电池制造
技术领域:
。
背景技术:
:目前太阳电池朝着高效低成本方向发展,电池效率不断提高。太阳电池要获得良好的光电转换效率就需要有更多的太阳光进入到太阳电池内部而不被反射掉。因此就需要制备反射率更低,且符合后道工序的绒面结构。目前产业上单晶硅的绒面制备方法大多为碱制绒,但是制绒过程中会出现白点、齿印,脏污清洗不干净,绒面反射率较大,金字塔尺寸不均匀及制绒工序时间较长等缺点。技术实现要素:本发明要解决的技术问题是:解决了如何减少在制绒过程中硅片表面的脏污,降低绒面的反射率,使得金字塔尺寸均匀及减少制绒工序时间的问题。为了解决上述技术问题,本发明的技术方案是提供了一种单晶硅制绒工艺,其特征在于,包括以下步骤:步骤(1)、将需要制绒的原始硅片放入到前酸洗槽进行前酸清洗;步骤(2)、将步骤(1)酸洗后的硅片放入到第一纯水清洗槽进行纯水清洗;步骤(3)、在前清洗槽将步骤(2)纯水清洗后的硅片进行表面预清洗处理;步骤(4)、在粗抛槽将步骤(3)预清洗处理后的硅片进行粗抛处理;步骤(5)、在碱清洗槽将步骤(4)粗抛后的硅片进行清洗处理;步骤(6)、将步骤(5)碱清洗处理后的硅片放入到第二纯水清洗槽进行纯水清洗;步骤(7)、在制绒槽将步骤(6)纯水清洗后的硅片进行制绒处理;步骤(8)、将步骤(7)制绒后的硅片放入到第三纯水清洗槽进行纯水清洗;步骤(9)、在后清洗槽将步骤(8)纯水清洗后的硅片进行表面后清洗处理;步骤(10)、将步骤(9)表面后清洗的硅片放入到第四纯水清洗槽进行纯水清洗;步骤(11)、将步骤(10)纯水清洗处理后的硅片放入到后酸洗槽进行后酸清洗处理;步骤(12)、将步骤(11)后酸清洗处理后的硅片放入到第五纯水清洗槽进行纯水清洗;步骤(13)、将步骤(12)纯水清洗后的硅片放入到慢提拉槽进行预脱水;步骤(14)、将步骤(13)预脱水后的硅片放入到烘干槽进行烘干。优选地,所述的步骤(1)和步骤(11)中,前酸洗槽和后酸洗槽内的溶液为hf/hcl溶液;所述hf/hcl溶液中,hf的体积浓度为4-8%,hcl的体积浓度5-10%,其余为纯水;酸清洗温度为20-30℃,时间为60-120s,同时进行循环鼓泡。优选地,所述的步骤(3)、步骤(5)和步骤(9)中,前清洗槽、碱洗槽和后清洗槽内的溶液为碱性溶液与h2o2的混合溶液;所述碱性溶液与h2o2的混合溶液中,碱性溶液的质量浓度为0.4-0.6%,h2o2的质量浓度为1.5-2.5%;碱性溶液为koh或naoh或nh4oh;清洗的温度为60-65℃,时间为60-120s,同时进行循环鼓泡。优选地,所述的步骤(4)中,粗抛槽内的溶液为koh与第一添加剂的混合溶液或naoh与第一添加剂的混合溶液;koh或naoh的质量浓度为1-2%,第一添加剂的体积浓度为0.3-0.5%;第一添加剂包括表面活性剂和去泡剂;粗抛槽内的温度为65-80℃,粗抛的时间为60-120s,同时进行循环鼓泡。优选地,所述的步骤(7)中,制绒槽内的溶液为koh与第二添加剂的混合溶液或naoh与第二添加剂的混合溶液;koh或naoh的质量浓度为0.8-1%,第二添加剂的体积浓度为1-1.2%;第二添加剂包括表面活性剂、去泡剂及去污剂;制绒槽内的温度为85-95℃,制绒的时间为350-450s,同时进行循环鼓泡。优选地,所述的步骤(13)中,慢提拉槽内设有纯水,慢提拉槽内的温度为60-80℃,预脱水的时间为30-60s。优选地,所述的步骤(14)中,烘干槽内设有氮气,烘干槽内的温度为60-80℃,烘干的时间为180-360s。优选地,所述的步骤(2)、(6)、(8)、(10)、(12)中,纯水清洗的时间为60~120s,清洗的温度为20-25℃。一种使用单晶硅制绒工艺的装置,其特征在于,包括对原始硅片进行前酸清洗的前酸洗槽、对前酸清洗后的硅片进行第一次纯水清洗的第一纯水清洗槽、对第一次纯水清洗后的硅片进行表面预清洗处理的前清洗槽、对预清洗处理后的硅片进行粗抛处理的粗抛槽、对粗抛后的硅片进行碱清洗处理的碱清洗槽、对碱清洗处理后的硅片进行第二次纯水清洗的第二纯水清洗槽、对第一次纯水清洗后的硅片进行制绒处理的制绒槽、对制绒后的硅片进行第三次纯水清洗的第三纯水清洗槽、对第三次纯水清洗后的硅片进行表面后清洗处理的后清洗槽、对表面后清洗的硅片进行第四次纯水清洗的第四纯水清洗槽、对第四次纯水清洗后的硅片进行后酸清洗处理的后酸洗槽、对后酸清洗处理后的硅片进行第五次纯水清洗的第五纯水清洗槽、对第五次纯水清洗后的硅片进行预脱水的慢提拉槽、对预脱水后的硅片进行烘干处理的烘干槽。本发明公开了一种单晶硅制绒工艺,将硅片依次进行前酸清洗→纯水清洗→预清洗→粗抛→碱清洗→纯水清洗→制绒→纯水清洗→后清洗→纯水清洗→后酸清洗→纯水清洗→慢提拉→烘干处理。本发明分别使用酸溶液以及多次纯水处理,可以有效解决绒面脏污问题,通过碱溶液分别进行粗抛和制绒,制备的金字塔大小均匀、尺寸一致且密集分布于硅片表面,绒面反射率低。而且制绒工序整体时间短,提高了产量。附图说明图1为一种单晶硅制绒工艺的流程图;图2为一种单晶硅制绒装置的示意图。具体实施方式为使本发明更明显易懂,兹以优选实施例,并配合附图作详细说明如下。实施例1如图1所示,一种单晶硅制绒工艺,包括以下步骤:步骤(1)、将需要制绒的原始硅片放入到酸洗槽进行前酸清洗处理。hf体积浓度为4%。hcl体积浓度5%,其余为纯水。酸清洗的温度为20℃,时间为60s,同时进行循环鼓泡。步骤(2)、将步骤(1)酸洗后的硅片放入到第一纯水清洗槽进行纯水清洗。纯水清洗的时间为60s,温度为25℃。步骤(3)、在前清洗槽将步骤(2)纯水清洗后的硅片进行表面预清洗处理。前清洗槽内的溶液为naoh与h2o2的混合溶液;naoh与h2o2的混合溶液中,naoh的质量浓度为0.4%,h2o2的质量浓度为2%。前清洗槽内的温度为60℃,时间为80s,同时进行循环鼓泡。步骤(4)、在粗抛槽将步骤(3)预清洗处理后的硅片进行粗抛处理。粗抛槽溶液为naoh与第一添加剂的混合溶液;naoh与第一添加剂的混合溶液中,naoh的质量浓度为1%,第一添加剂的体积浓度为0.3%。第一添加剂主要由表面活性剂和去泡剂组成。粗抛槽内的温度为70℃,时间为100s,同时进行循环鼓泡。步骤(5)、在碱清洗槽将步骤(4)粗抛后的硅片进行清洗处理。碱洗槽溶液为naoh与h2o2的混合溶液;naoh与h2o2的混合溶液中,naoh的质量浓度为0.4%,h2o2的质量浓度为2.5%。碱洗槽温度为65℃,时间为120s,同时进行循环鼓泡。步骤(6)、将步骤(5)碱清洗处理后的硅片放入到第二纯水清洗槽进行纯水清洗。纯水清洗的时间为60s,温度为25℃。步骤(7)、在制绒槽将步骤(6)纯水清洗后的硅片进行制绒处理。制绒槽溶液为naoh与第二添加剂的混合溶液;naoh与第二添加剂的混合溶液中,naoh的质量浓度为0.8%,第二添加剂的体积浓度为1%。第二添加剂主要由表面活性剂、去泡剂及去污剂组成。制绒槽内的温度为85℃,时间为420s,同时进行循环鼓泡。步骤(8)、将步骤(7)制绒后的硅片放入到第三纯水清洗槽进行纯水清洗。纯水清洗的时间为60s,温度为25℃。步骤(9)、在后清洗槽将步骤(8)纯水清洗后的硅片进行表面后清洗处理。后清洗槽溶液为naoh与h2o2的混合溶液;naoh与h2o2的混合溶液中,naoh的质量浓度为0.5%,h2o2的质量浓度为2.5%。后洗槽内的温度为65℃,时间为120s,同时进行循环鼓泡。步骤(10)、将步骤(9)后清洗的硅片放入到第四纯水清洗槽进行纯水清洗。纯水清洗的时间为80s,温度为25℃。步骤(11)、将步骤(10)纯水清洗处理后的硅片放入到酸洗槽进行后酸清洗处理;hf体积浓度为4%。hcl体积浓度5%,其余为纯水。酸清洗温度为20℃,时间为60s,同时进行循环鼓泡。步骤(12)、将步骤(11)后酸清洗处理后的硅片放入到第五纯水清洗槽进行纯水清洗。纯水清洗的时间为120s,温度为25℃。步骤(13)、将步骤(10)纯水清洗后的硅片放入到慢提拉槽进行预脱水。慢提拉槽内的温度为60℃,预脱水的时间为60s。步骤(14)、将步骤(11)预脱水后的硅片放入到烘干槽进行烘干。烘干槽内的温度为80℃的氮气烘干,烘干的时间为200s。实施例1中的制绒工艺后表面干净无污染,无齿痕、手印、白斑等,外观干净。经3d显微镜形貌观测后表面金字塔均匀,密集分布于硅片表面。金字塔尺寸在0.5-1.8um之间。平均金字塔尺寸在1.5um左右。400-1000nm波长范围内的综合反射率为9.3825%。如图2所示,一种使用单晶硅制绒工艺的装置,包括对原始硅片进行前酸清洗的前酸洗槽、对前酸清洗后的硅片进行第一次纯水清洗的第一纯水清洗槽、对第一次纯水清洗后的硅片进行表面预清洗处理的前清洗槽、对预清洗处理后的硅片进行粗抛处理的粗抛槽、对粗抛后的硅片进行碱清洗处理的碱清洗槽、对碱清洗处理后的硅片进行第二次纯水清洗的第二纯水清洗槽、对第一次纯水清洗后的硅片进行制绒处理的制绒槽、对制绒后的硅片进行第三次纯水清洗的第三纯水清洗槽、对第三次纯水清洗后的硅片进行表面后清洗处理的后清洗槽、对表面后清洗的硅片进行第四次纯水清洗的第四纯水清洗槽、对第四次纯水清洗后的硅片进行后酸清洗处理的后酸洗槽、对后酸清洗处理后的硅片进行第五次纯水清洗的第五纯水清洗槽、对第五次纯水清洗后的硅片进行预脱水的慢提拉槽、对预脱水后的硅片进行烘干处理的烘干槽。实施例2一种单晶硅制绒工艺,包括以下步骤:步骤(1)、将需要制绒的原始硅片放入到酸洗槽进行前酸清洗处理。。hf体积浓度为4%。hcl体积浓度5%,其余为纯水。酸清洗温度为25℃,时间为60s,同时进行循环鼓泡。步骤(2)、将步骤(1)酸洗后的硅片放入到第一纯水清洗槽进行纯水清洗。纯水清洗的时间为80s,温度为20℃。步骤(3)、在前清洗槽将步骤(2)纯水清洗后的硅片进行表面预清洗处理。前清洗槽溶液为naoh与h2o2的混合溶液;naoh与h2o2的混合溶液中,naoh的质量浓度为0.4%,h2o2的质量浓度为2%。前清洗槽内的温度为60℃,时间为100s,同时进行循环鼓泡。步骤(4)、在粗抛槽将步骤(3)预清洗处理后的硅片进行粗抛处理。粗抛槽溶液为naoh与第一添加剂的混合溶液;naoh与第一添加剂的混合溶液中,naoh的质量浓度为2%,第一添加剂的体积浓度为0.3%。第一添加剂主要由表面活性剂和去泡剂组成。粗抛槽内的温度为70℃,时间为120s,同时进行循环鼓泡。步骤(5)、在碱清洗槽将步骤(4)粗抛后的硅片进行清洗处理。碱洗槽溶液为naoh与h2o2的混合溶液;naoh与h2o2的混合溶液中,naoh的质量浓度为0.4%,h2o2的质量浓度为2.5%。碱洗槽内的温度为65℃,时间为120s,同时进行循环鼓泡。步骤(6)、将步骤(5)碱清洗处理后的硅片放入到第二纯水清洗槽进行纯水清洗。纯水清洗的时间为80s,温度为25℃。步骤(7)、在制绒槽将步骤(6)纯水清洗后的硅片进行制绒处理。制绒槽溶液为naoh与第二添加剂的混合溶液;naoh与第二添加剂的混合溶液中,naoh的质量浓度为0.8%,第二添加剂的体积浓度为1%。第二添加剂主要由表面活性剂、去泡剂及去污剂组成。制绒槽温度为90℃,时间为420s,同时进行循环鼓泡。步骤(8)、将步骤(7)制绒后的硅片放入到第三纯水清洗槽进行纯水清洗。纯水清洗的时间为80s,温度为25℃。步骤(9)、在后清洗槽将步骤(8)纯水清洗后的硅片进行表面后清洗处理。后清洗槽溶液为naoh与h2o2的混合溶液;naoh与h2o2的混合溶液中,naoh的质量浓度为0.5%,h2o2的质量浓度为2.5%。后洗槽内的温度为65℃,时间为120s,同时进行循环鼓泡。步骤(10)、将步骤(9)后清洗的硅片放入到第四纯水清洗槽进行纯水清洗。纯水清洗的时间为80s,温度为25℃。步骤(11)、将步骤(10)纯水清洗处理后的硅片放入到酸洗槽进行后酸清洗处理;hf体积浓度为4%。hcl体积浓度5%,其余为纯水。酸清洗温度为20℃,时间为60s,同时进行循环鼓泡。步骤(12)、将步骤(11)后酸清洗处理后的硅片放入到第五纯水清洗槽进行纯水清洗。纯水清洗的时间为120s,温度为25℃。步骤(13)、将步骤(10)纯水清洗后的硅片放入到慢提拉槽进行预脱水。慢提拉槽内的温度为60℃,预脱水的时间为60s。步骤(14)、将步骤(11)预脱水后的硅片放入到烘干槽进行烘干。烘干槽内的温度为80℃的氮气烘干,烘干的时间为200s。实施例2中的制绒工艺后表面干净无污染,无齿痕、手印、白斑等,外观干净。经3d显微镜形貌观测后表面金字塔均匀,密集分布于硅片表面。金字塔尺寸在0.5-1.8um之间。平均金字塔尺寸在1.5um左右。400-1000nm波长范围内的综合反射率为9.3735%。其他与实施例1相同。实施例3一种单晶硅制绒工艺,包括以下步骤:步骤(1)、将需要制绒的原始硅片放入到酸洗槽进行前酸清洗处理。hf体积浓度为4%。hcl体积浓度5%,其余为纯水。酸清洗温度为20℃,时间为60s,同时进行循环鼓泡。步骤(2)、将步骤(1)酸洗后的硅片放入到第一纯水清洗槽进行纯水清洗。纯水清洗的时间为120s,温度为20℃。步骤(3)、在前清洗槽将步骤(2)纯水清洗后的硅片进行表面预清洗处理。前清洗槽溶液为naoh与h2o2的混合溶液;naoh与h2o2的混合溶液中,naoh的质量浓度为0.4%,h2o2的质量浓度为2%。前清洗槽内的温度为60℃,时间为120s,同时进行循环鼓泡。步骤(4)、在粗抛槽将步骤(3)预清洗处理后的硅片进行粗抛处理。粗抛槽溶液为koh与第一添加剂的混合溶液;koh与第一添加剂的混合溶液中,koh的质量浓度为2%,第一添加剂体积浓度为0.3%。第一添加剂主要由表面活性剂和去泡剂组成。粗抛槽内的温度为80℃,时间为120s,同时进行循环鼓泡。步骤(5)、在碱清洗槽将步骤(4)粗抛后的硅片进行清洗处理。碱洗槽溶液为naoh与h2o2的混合溶液;naoh与h2o2的混合溶液中,naoh的质量浓度为0.4%,h2o2的质量浓度为2.5%。碱洗槽内的温度为65℃,时间为120s,同时进行循环鼓泡。步骤(6)、将步骤(5)碱清洗处理后的硅片放入到第二纯水清洗槽进行纯水清洗。纯水清洗的时间为120s,温度为25℃。步骤(7)、在制绒槽将步骤(6)纯水清洗后的硅片进行制绒处理。制绒槽溶液为naoh与第二添加剂的混合溶液;naoh与第二添加剂的混合溶液中,naoh的质量浓度为0.8%,第二添加剂体积浓度为1%。第二添加剂主要由表面活性剂、去泡剂及去污剂组成。制绒槽内的温度为95℃,时间为350s,同时进行循环鼓泡。步骤(8)、将步骤(7)制绒后的硅片放入到第三纯水清洗槽进行纯水清洗。纯水清洗的时间为120s,温度为25℃。步骤(9)、在后清洗槽将步骤(8)纯水清洗后的硅片进行表面后清洗处理。后清洗槽溶液为naoh与h2o2的混合溶液;naoh与h2o2的混合溶液中,naoh的质量浓度为0.5%,h2o2的质量浓度为2.5%。后洗槽内的温度为65℃,时间为120s,同时进行循环鼓泡。步骤(10)、将步骤(9)后清洗的硅片放入到第四纯水清洗槽进行纯水清洗。纯水清洗的时间为80s,温度为25℃。步骤(11)、将步骤(10)纯水清洗处理后的硅片放入到酸洗槽进行后酸清洗处理;hf体积浓度为4%。hcl体积浓度5%,其余为纯水。酸清洗温度为20℃,时间为60s,同时进行循环鼓泡。步骤(12)、将步骤(11)后酸清洗处理后的硅片放入到第五纯水清洗槽进行纯水清洗。纯水清洗的时间为120s,温度为25℃。步骤(13)、将步骤(10)纯水清洗后的硅片放入到慢提拉槽进行预脱水。慢提拉槽内的温度为60℃,预脱水的时间为60s。步骤(14)、将步骤(11)预脱水后的硅片放入到烘干槽进行烘干。烘干槽内的温度为80℃的氮气烘干,烘干的时间为360s。实施例3中的制绒工艺后表面干净无污染,无齿痕、手印、白斑等,外观干净。经3d显微镜形貌观测后表面金字塔均匀,密集分布于硅片表面。金字塔尺寸在0.5-1.8um之间。平均金字塔尺寸在1.5um左右。400-1000nm波长范围内的综合反射率为9.3360%。其他与实施例1相同。实施例4一种单晶硅制绒工艺,包括以下步骤:步骤(1)、将需要制绒的原始硅片放入到酸洗槽进行前酸清洗处理。hf的体积浓度为8%,hcl的体积浓度10%,其余为纯水;酸清洗温度为30℃,时间为120s,同时进行循环鼓泡。步骤(2)、将步骤(1)酸洗后的硅片放入到第一纯水清洗槽进行纯水清洗。纯水清洗的时间为120s,温度为20℃。步骤(3)、在前清洗槽将步骤(2)纯水清洗后的硅片进行表面预清洗处理。前清洗槽溶液为koh与h2o2的混合溶液;koh与h2o2的混合溶液中,koh的质量浓度为0.6%,h2o2的质量浓度为2%。前清洗槽内的温度为60℃,时间为120s,同时进行循环鼓泡。步骤(4)、在粗抛槽将步骤(3)预清洗处理后的硅片进行粗抛处理。粗抛槽溶液为koh与第一添加剂的混合溶液;koh与第一添加剂的混合溶液中,koh的质量浓度为1%,第一添加剂体积浓度为0.5%。第一添加剂主要由表面活性剂和去泡剂组成。粗抛槽内的温度为65℃,粗抛的时间为60s,同时进行循环鼓泡。步骤(5)、在碱清洗槽将步骤(4)粗抛后的硅片进行清洗处理。碱洗槽溶液为nh4oh与h2o2的混合溶液;nh4oh与h2o2的混合溶液中,nh4oh的质量浓度为0.6%,h2o2的质量浓度为2.5%。碱洗槽内的温度为65℃,时间为120s,同时进行循环鼓泡。步骤(6)、将步骤(5)碱清洗处理后的硅片放入到第二纯水清洗槽进行纯水清洗。纯水清洗的时间为120s,温度为25℃。步骤(7)、在制绒槽将步骤(6)纯水清洗后的硅片进行制绒处理。制绒槽溶液为koh与第二添加剂的混合溶液;koh与第二添加剂的混合溶液中,koh的质量浓度为1%,第二添加剂体积浓度为1.2%。第二添加剂主要由表面活性剂、去泡剂及去污剂组成。制绒槽内的温度为95℃,时间为450s,同时进行循环鼓泡。步骤(8)、将步骤(7)制绒后的硅片放入到第三纯水清洗槽进行纯水清洗。纯水清洗的时间为120s,温度为25℃。步骤(9)、在后清洗槽将步骤(8)纯水清洗后的硅片进行表面后清洗处理。后清洗槽溶液为naoh与h2o2的混合溶液;naoh与h2o2的混合溶液中,naoh的质量浓度为0.5%,h2o2的质量浓度为2.5%。后洗槽内的温度为65℃,时间为120s,同时进行循环鼓泡。步骤(10)、将步骤(9)后清洗的硅片放入到第四纯水清洗槽进行纯水清洗。纯水清洗的时间为80s,温度为25℃。步骤(11)、将步骤(10)纯水清洗处理后的硅片放入到酸洗槽进行后酸清洗处理;hf体积浓度为4%。hcl体积浓度5%,其余为纯水。酸清洗温度为20℃,时间为60s,同时进行循环鼓泡。步骤(12)、将步骤(11)后酸清洗处理后的硅片放入到第五纯水清洗槽进行纯水清洗。纯水清洗的时间为80s,温度为20℃。步骤(13)、将步骤(10)纯水清洗后的硅片放入到慢提拉槽进行预脱水。慢提拉槽内的温度为80℃,预脱水的时间为30s。步骤(14)、将步骤(11)预脱水后的硅片放入到烘干槽进行烘干。烘干槽内的温度为60℃的氮气烘干,烘干的时间为180s。实施例4中的制绒工艺后表面干净无污染,无齿痕、手印、白斑等,外观干净。经3d显微镜形貌观测后表面金字塔均匀,密集分布于硅片表面。金字塔尺寸在0.5-1.8um之间。平均金字塔尺寸在1.5um左右。400-1000nm波长范围内的综合反射率为9.3300%。其他与实施例1相同。常规制绒工艺与实施例1、2、3、4之间的综合反射率对比如表1。表1制绒工艺绒面反射率/%(400-1000nm)综合反射率提升/%常规制绒11.05730实施例19.38251.6748实施例29.37351.6838实施例39.33601.7213实施例49.33001.7273当前第1页12