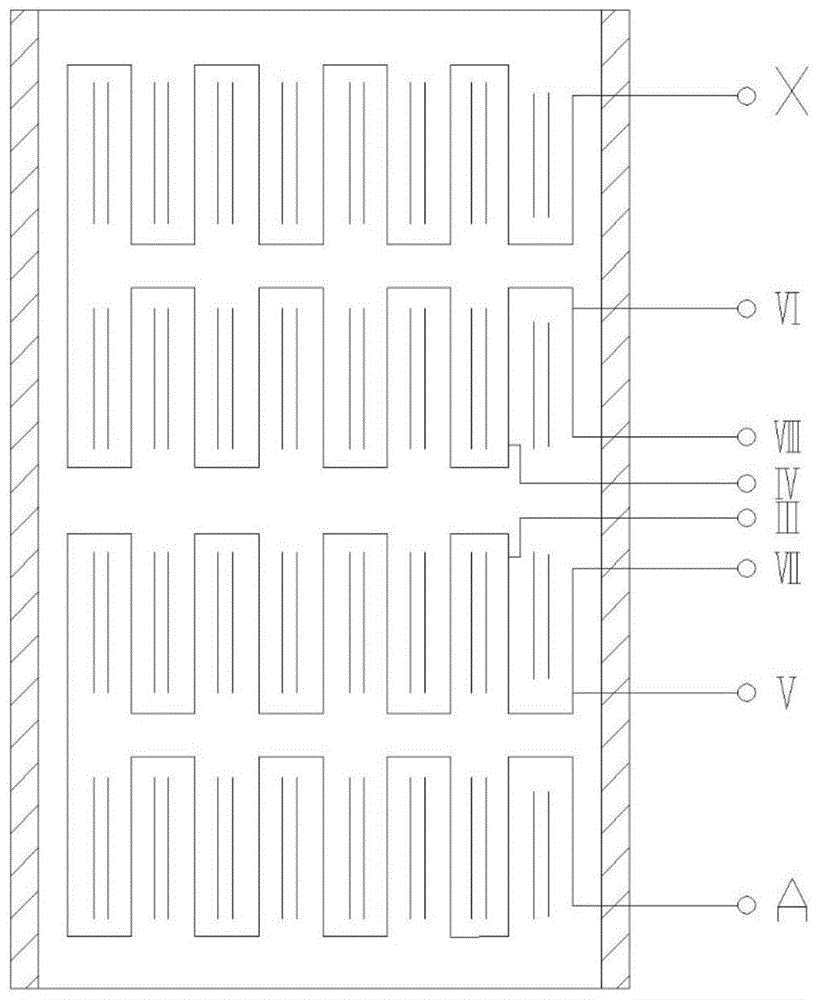
本实用新型涉及变压器领域,特别是一种干式变压器高压绕组。
背景技术:
:干变绕组通常有分段圆筒式和连续式两种绕制方法。树脂浇注干式变压器高压线圈,一般制造厂家的结构都是多段圆筒式线圈,根据电压的高低,一般10kv~35kv高压线圈分为4段至12段,减少线圈每层匝数,降低线圈层间电压。在进行绕制时,每段都相当于一个独立多层圆筒式线圈,导线层间电压高要用层间绝缘材料。如图1所示,分段圆筒式结构绕制时上层匝数与下层匝数一样或少于下层匝数,绕制上一层线段时需要打s弯升层,然后放置层间绝缘。连续式绕组绕制方法的绕组如图2所示,连续式线圈起头多从线段的外径引出,绕成一临时线段,然后用手推倒,手工将线匝进行翻叠,最后成为一个起头由外径引出的正式线段。此外,凡由双数到单数线段的段间换位均在线段外径上,因此所有的单数线段都是“反段”而且所有的双数段都是正段,正段就是一次绕制完成而不需翻叠线匝的线段。上述两种结构绕制时均比较复杂,花费工时较多,对操作人员的技术要求较高。且为满足绝缘距离和电气强度的要求,需要增加段间距离或饼间距离。然而电压越高,间距总和也就越大,这就造成干式变压器线圈的整体高度升高,体积增大,材料消耗增多,产品成本提高。技术实现要素:针对现有技术的不足,本实用新型提供了一种辐向自由排列的连续式干式变压器绕组及其加工方法,电气性能好,成本低,且具有生产效率高等优点。为实现以上目的,本实用新型通过以下技术方案予以实现:一种辐向自由排列的连续式干式变压器绕组,包括电磁线和绝缘内筒,电磁线绕在绝缘内筒上,其特征在于:绕组为电磁线沿辐向自由排列,其轴向为总体连续卷绕的结构,电磁线与绝缘内筒用树脂浇注一体。具体实施时,绕组设有上下基本段和中部的调压段,调压段从绕组的电磁线抽出分接线,分接引线折弯引出时均用聚酰亚胺胶带绑扎成型,后将分接引线套入玻璃纤维套管增强绝缘。辐向自由排列、轴向总体连续的绕组为电磁线从绕线起始端开始向另一侧绕制,由于电磁线本身有高度,因此不能像饼式线圈那样的绕组线匝沿其辐向连续绕制而成,为保证电磁线之间的最佳紧密结合,电磁线绕制和排列时有倾斜坡度,然后逐渐填满绕组的幅向位置,辐向自由排列,达到设计的幅向高度,由于该结构排列的电磁线之间的线距很小,轴向电压梯度分布均匀,电位差非常小,因此就不需要其它绝缘材料进行隔离。一种辐向自由排列的连续式干式变压器绕组及其加工方法:卧式绕线机的绕线模安装在绕线机主轴,带线盘的电磁线设在机架上,准备好绝缘内筒和设有穿孔的左右限位挡板,限位挡板的挡板处的幅向尺寸高于绕组的设计幅向尺寸,绝缘内筒和左右限位挡板的内径分别与卧式绕线机的绕线模外径相适配;把绝缘内筒和左右限位挡板套入绕线模,左右限位挡板分别位于绝缘内筒的左右侧,绝缘内筒和左右限位挡板固定在绕线模上;电磁线的绕线起始端为绝缘内筒的左侧或右侧,电磁线从绕线起始端开始向另一侧绕制,电磁线堆叠的绕组幅向高度为预先设计的幅向尺寸,电磁线沿辐向自由排列;轴向总体连续绕制,电磁线在绕线模上按自由堆叠成上述的绕组幅向高度,无需放置层间和匝间绝缘,限位挡圈上设有控制绕线机启停的激光限位器,当电磁线堆叠高度超出设计尺寸时,激光限位器输出信号,绕线机停止工作,绕线工调整电磁线的幅向高度,然后继续启动绕线机工作;在电磁线绕制时,绕线机的计数器计量电磁线绕制的匝数,进行整形,完成绕组的绕制。具体实施时,左右限位挡板的周边分别对应设有调节槽,设有定位杆能穿过左右限位挡板的相对应调节槽;绕线模一侧的绕线机主轴上同轴装有伺服电机,伺服电机能带动定位杆随电磁线的排布同步前进,控制绕组的辐向尺寸,定位杆与绝缘内筒的间距为绕组幅向高度,电磁线绕制时,定位杆起到电磁线的幅向高度定位作用。伺服电机带动定位杆移动的结构,在现有技术非常多,如齿轮传动、丝杆传动等等。具体实施时,定位杆为蜗杆,用支撑杆连接在绕线机主轴上,伺服电机输出轴连接有与蜗杆相适配的涡轮,伺服电机工作,通过涡轮蜗杆结构,能带动定位杆的移动。具体实施时,设有自动电磁线排布器,自动电磁线排布器包括排布杆和排布支柱,排布杆能在排布支柱上上下移动,排布杆与绕线模相互平行,设在绕线侧;机架上设有自动线盘导轨,线盘能在自动线盘导轨上左右移动,电磁线上套有放线环,电磁线位于排布杆下面,放线环位于排布杆的上面。具体实施时,左右限位挡板的上端和左右端一体连接有凸条,上述调节槽位于限位挡板的凸条处。具体实施时,当电磁线在绕线模上按自由堆叠,绕线工用电磁线敲板护住电磁线走向,通过定位杆的幅向定位作用,敲板配合调整绕组的绕线尺寸。具体实施时,当绕组设有分接线时,绕组设有上下基本段和中部的分接段,通过绕线机的计数器计量电磁线绕制分接处的匝数,分接处的匝数达到绕组的设计分接匝数时,完成上基本段绕制,电磁线折弯引出,然后继续绕制,中部的分接段绕制的其它分接位置同样通过绕线机的计数器计量电磁线绕制需要分接位置的处的匝数,磁线折弯引出,完成中部的分接段后,继续绕制下基本段。分接引线折弯引出时均用聚酰亚胺胶带绑扎成型,后将分接引线套入玻璃纤维套管增强绝缘。电磁线的绕线起始端为绝缘内筒的左侧或右侧,电磁线从绕线起始端开始向另一侧绕制,定位杆由模具旁的伺服电机控制,跟随电磁线一起运动。电磁线堆叠的绕组幅向高度为预先设计的幅向尺寸,电磁线沿辐向自由排列,线模旁的绕线机主轴上同轴装有伺服电机,伺服电机上安装的定位杆通过涡轮蜗杆控制前后走向,随电磁线的排布同步前进,控制绕组的辐向尺寸。限位挡圈上设有控制绕线机启停的激光限位器,当电磁线堆叠高度超出设计尺寸时,激光限位器输出信号,绕线机的伺服电机停止工作,线盘及自动电磁线排布器同步停止工作。轴向总体连续绕制,电磁线在绕线模上按自由堆叠成上述的绕组幅向高度,无需放置层间绝缘,在电磁线绕制时,绕线机的计数器计量电磁线绕制的匝数,当匝数达到绕组的设计匝数时抽出分接引线,分接引线折弯引出时均用聚酰亚胺胶带绑扎成型,后将分接引线套入玻璃纤维套管,进行整形,完成绕组的绕制。本实用新型具有以下有益效果:1、本实用新型方案提供的绕组结构和绕组方法,由于工人操作较常规绕组结构少了放置层间绝缘、打s弯升层、梯形排布、紧密绕线等工艺要求,工人只需要控制导线绕制方向,不使坡度过大即可,大大提高了生产效率。2、本实用新型方案提供的绕组结构和绕组方法,电磁线自由排布后的匝间电压远远低于传统绕组的层间电压,局部放电量远远小于传统绕组,大大提高了电气性能。3、本实用新型方案提供的绕组结构和绕组方法,取消导线每层的层间绝缘,节省了材料;同时增大了导线在绕组中的空间占有率,同样的导线截面积可以使线圈体积减小,节省了成本。4、本实用新型方案提供的绕组结构和绕组方法,其结构简单,绕制方简便,且机械性能好,耐冲击性能强,轴向电压梯度分布均匀,匝间电位差小,局部放电量小,提高了供电质量,增大了变压器的使用寿命。附图说明图1为现有技术分段圆筒式结构绕组的示意图。图2为现有技术连续式结构绕组的示意图。图3为本实用新型实施例绕组的结构示意图。图4为本实用新型实施例绕组浇注完成后的接线示意图。图5为本实用新型实施例绕组的匝数原理示意图。图6为本实用新型实施例绕组绕制时的示意图。图7为本实用新型实施例限位挡板的示意图。图中:1线盘、2限位挡板、3绕线模、4电磁线、5绝缘内筒、6定位杆、7激光限位器、8自动线盘导轨、9自动电磁线排布器、10、伺服电机、11绕线机主轴、12放线环、13涡轮、21调节槽、22凸条、23环氧树脂、91排布杆、92排布支柱、x上接线头、a下接线头、a基本段、b分接段。具体实施方式下面将结合本实用新型实施例中的附图,对本实用新型实施例中的技术方案进行清楚、完整地描述,显然,所描述的实施例仅仅是本实用新型一部分实施例,而不是全部的实施例。基于本实用新型中的实施例,本领域普通技术人员在没有做出创造性劳动前提下所获得的所有其他实施例,都属于本实用新型保护的范围。如图3-7所示,本实用新型实施例选用了型号为scb12-400/10-0.4干式变压器,提供一种辐向自由排列的连续式干式变压器绕组,包括电磁线4和绝缘内筒5,电磁线4绕在绝缘内筒5上,绕组上端为绕组电磁线4起始端连接的上接线头x,绕组下端为绕组电磁线4末端连接的下接线头a,设有上下基本段a和中部的分接段b,分接段b中从绕组的电磁线4抽出分接线,本实施例有六个分接线。绕组为电磁线4沿辐向自由排列,其轴向为总体连续卷绕的结构,电磁线4与绝缘内筒5用环氧树脂23浇注一体。辐向自由排列、轴向总体连续的绕组为电磁线4从绕线起始端开始向另一侧绕制,由于电磁线4本身有高度,且不需要像饼式线圈那样的绕组线匝沿其辐向绕制正反饼,为保证电磁线4之间的最佳紧密结合,电磁线4绕制和排列时有倾斜坡度,然后逐渐填满绕组的幅向位置,辐向自由排列,达到设计的幅向高度,由于该结构排列的电磁线4之间的线距很小,轴向电压梯度分布均匀,因此匝间电位差小,就不需要其它绝缘纸等绝缘材料进行隔离等。如图6和图7,结合图3、图4和图5所示,提供一种辐向自由排列的连续式干式变压器绕组及其加工方法:卧式绕线机的绕线模安装在绕线机主轴,带线盘的电磁线设在机架上,准备好绝缘内筒5和设有穿孔的左右限位挡板2,限位挡板2的挡板处的幅向尺寸略高于绕组的设计幅向尺寸,绝缘内筒5和左右限位挡板2的内径分别与卧式绕线机的绕线模3外径相适配;左右限位挡板2的上端和左右端一体连接有凸条22,调节槽21位于限位挡板2的凸条22处。把绝缘内筒5和左右限位挡板2套入绕线模3,左右限位挡板2分别位于绝缘内筒5的左右侧,绝缘内筒5和左右限位挡板2固定在绕线模3上;自动电磁线排布器9包括排布杆91和排布支柱92,排布杆91能在排布支柱92上上下移动,排布杆91与绕线模3相互平行,设在绕线侧;机架上设有自动线盘导轨8,线盘1能在自动线盘导轨8上左右移动,电磁线上套有放线环12,电磁线位于排布杆下面,放线环12位于排布杆91的上面。绕线模一侧的绕线机主轴上同轴装有伺服电机,伺服电机能带动定位杆6随电磁线的排布同步前进,控制绕组的辐向尺寸,定位杆6与绝缘内筒的间距为绕组幅向高度,电磁线绕制时,定位杆6起到电磁线的幅向高度定位作用。定位杆6的左右端设有外螺纹。本实用新型实施例中,定位杆6为蜗杆,用支撑杆连接在绕线机主轴上,伺服电机输出轴连接有与蜗杆相适配的涡轮13,伺服电机工作,通过涡轮蜗杆结构,能带动定位杆6的移动。绕线起始端为绝缘内筒5的左侧或右侧,电磁线4起始端抽出上接线头x,电磁线4从绕线起始端开始向另一侧绕制,定位杆6安装在伺服电机10上,定位杆6与绝缘内筒5的间距为绕组幅向高度,电磁线4绕制时,定位杆6起到电磁线4的幅向高度定位作用;将激光限位器7安装在凸条22旁,限位高度设定为绕组设计辐向高度。电磁线4堆叠的绕组幅向高度为预先设计的幅向尺寸,电磁线4在自动线盘导轨8和自动电磁线排布器9的协同动作下沿辐向自由排列,轴向总体连续绕制,电磁线4在绕线模3上按自由堆叠成上述的绕组幅向高度,无需放置层间绝缘,当电磁线4在绕线模3上按自由堆叠,绕线工用敲板护住电磁线4走向,通过定位杆6的幅向定位作用,敲板配合调整绕组的绕线尺寸。本实用新型实施例中,设有分接线时,绕组设有上下基本段a和中部的调压段b,通过绕线机的计数器计量电磁线4绕制分接处的匝数,分接处的匝数达到绕组的设计分接匝数时,完成上基本段a绕制,电磁线4折弯引出,用聚酰亚胺胶带绑扎成型,后将分接引线套入玻璃纤维套管,然后继续绕制,中部的分接段b绕制的其它分接位置同样通过绕线机的计数器计量电磁线4绕制需要分接位置的处的匝数,磁线折弯引出。完成中部的分接段b后,就要抽匝数最多的分接头ⅶ和ⅷ,将导线折弯后,按图纸要求留出工艺长度,将导线从折弯线顶部间断,分成2根单独的电磁线,将分接头ⅶ和ⅷ分开,单独对两根断开的导线进行引线包扎,用聚酰亚胺胶带绑扎成型,后将分接引线套入玻璃纤维套管,然后用玻璃纤维带将两个分接引线绑紧,使两根引线有足够的绝缘距离。再继续绕制的下基本段a,同时绕线机的计数器计量电磁线4绕制的匝数,当匝数达到绕组的设计匝数,末端抽出下接线头a,进行整形,用绝缘材料垫满绕组的末端与限位挡板2的间隙,保证绕组的高度一致性完成绕组的绕制后,拆掉激光限位器7,定位杆6根据穿过调节槽21的位置,并且用螺母紧固,左右限位挡板2、定位杆6及绕组一体卸下绕线机,检验合格后,装上外模,进行环氧树脂浇注。本实用新型为采用新型辐向自由排列、轴向总体连续的绕组,绕组采用卧式绕制,绕制时导线自由堆叠,无需按分段圆筒式、连续式等传统结构控制导线的排布。绕线工安装好模具及端部限位挡板2,绕制时只需要控制导线的辐向尺寸,不要超过线圈的外模高度即可,无需放置层间绝缘,也不需要打s弯让导线升层,更不需要像传统绕组一样为满足绕向绕完一半线段后将绕线模3掉头绕制另一半线段。由于工人操作较常规绕组结构少了放置层间绝缘、打s弯升层、梯形排布、紧密绕线、模具掉头等工艺要求,工人只需要控制导线绕制方向,不使电磁线坡度过大即可。每个绕组的生产时间比常规结构节省50%以上,熟练工人可以做到1小时一个高压线圈,一天可以绕制8-9个绕组,而传统绕组一天只能绕制3-4个,生产效率提高2倍以上。本实用新型采用的结构,由于其绕组轴向尺寸较高,散热面积增大、由于辐向尺寸较小,绕组的热传递性能较好,变压器的结构趋于瘦高,温升方面较常规结构变压器降低3k-5k左右。经过试验和对比,申请人选用容量50kva-1600kva的变压器,针对按照本实施例,制作的各种容量干式变压器的主要原材料的用量进行对比。具体见表1-表4所示。表1:本实用新型实施例与常规结构绕组铜线用量对比表表2:本实用新型实施例与常规结构硅钢片用量对比表表3:本实用新型实施例与常规结构树脂用对比表表4:本实用新型实施例与常规结构变压器重量对比表本实用新型的变压器的绕组取消了传统绕组的段间和饼间距离,轴向高度较传统绕组降低了50mm-70mm。取消了层间绝缘,辐向厚度较传统套组减小了4mm-7mm。导线排布更加密集,空间利用率更大,因此绕组体积更小,提高铁芯铁窗的利用率,硅钢材料节省3%以上。本实用新型的变压器由于采用了创新结构的绕组,变压器在温升方面拥有的优越性,使得设计方案时可选择的优化路线更多。新变压器整体体积同比传统变压器降低5%-8%,树脂用量节省3%-5%,层间绝缘材料完全节省,导线总重节省3%以上,绕组总成本节省5%以上,变压器总成本节省3%-6%。本实用新型实施例选用了型号为scb12-400/10-0.4干式变压器进行试验,其容量400千伏安、联结组标号dyn11、频率50赫兹、相数为3相,试验数据如下:电压比测量和联接组标号检定采用测量仪器为jyt-a变比测试仪。电压比测量和联接组标号检定结论:误差绝对值不大于0.4%,合格。具体见表5电压比测量和联接组标号检定试验表。表5:电压比测量和联接组标号检定试验表绕组电阻测量采用的测量仪器为jyr-10双通道变压器直流电阻测试仪,环境温度:8.5℃。绕组电阻测量结论:高、低压绕组线电阻不大于2%,如有中性点引出,分别测量相、线直流电阻,相电阻不大于4%。合格。具体见表6绕组电阻测量试验表。表6:绕组电阻测量试验表绕组对地及绕组间直流绝缘电阻测量,采用测量仪器为绝缘电阻测试仪xd2905,通过记录环境温度及湿度,按标准规定逐一进行测量,并对测试结果进行确认,然后再测量下一组,测量时,施加电压为2500v。绕组对地及绕组间直流绝缘电阻测量结论为合格。具体见表7绕组对地及绕组间直流绝缘电阻测量试验表。表7:绕组对地及绕组间直流绝缘电阻测量试验表绝缘例行(外施耐压试验),结论:在试验时间内试验电压电流稳定,变压器内无异响声,合格。具体见表8绝缘例行(外施耐压试验)试验表。表8:绝缘例行(外施耐压试验)试验表绝缘例行(感应耐压试验),采用nsw-ttcs电力变压器试验微机测控系统试验,结论:合格。具体见表9绝缘例行(感应耐压试验)试验表。表9:绝缘例行(感应耐压试验)试验表空载损耗和空载电流测量,采用nsw-ttcs电力变压器试验微机测控系统试验,结论:合格。具体见表10空载损耗和空载电流测量试验表。表10:空载损耗和空载电流测量试验表项目实测值标准值设计值空载损耗(w)762785767空载电流(%)0.361.2+0%0.59结论合格合格合格短路阻抗和负载损耗测量,采用nsw-ttcs电力变压器试验微机测控系统试验,结论:施加不低于50%额定电流,测量其负载损耗及阻抗电压合格。具体见表11短路阻抗和负载损耗测量试验表。表11:短路阻抗和负载损耗测量试验表项目实测值标准值设计值负载损耗(w)382139903867阻抗电压(%)4.014.0+10%4.15结论合格合格合格局部放电测量,结论为合格。具体见表12局部放电测量试验表。表12:局部放电测量试验表传统干变高压绕组一般采用分段圆筒式结构,层间电压在600v-1400v之间,层间绝缘厚度0.2-0.6mm,每毫米场强电压1500v以上。浇注过程稍有差池局部放电将会高于国家标准规定的10pc。本实用新型变压器绕组的轴向采用的高度较高,辐向尺寸较小,不存在层间概念,导线自由排布后的匝间电压远远低于传统绕组的层间电压,局部放电量远远小于传统绕组。试验结果显示新型结构的变压器局部放电量均可以做到5pc以下,而且对浇注过程和工人操作水平要求较常规干变的要求低,便于公司培训相关人员。尽管已经示出和描述了本实用新型的实施例,对于本领域的普通技术人员而言,可以理解在不脱离本实用新型的原理和精神的情况下可以对这些实施例进行多种变化、修改、替换和变型,本实用新型的范围由所附权利要求及其等同物限定。当前第1页12