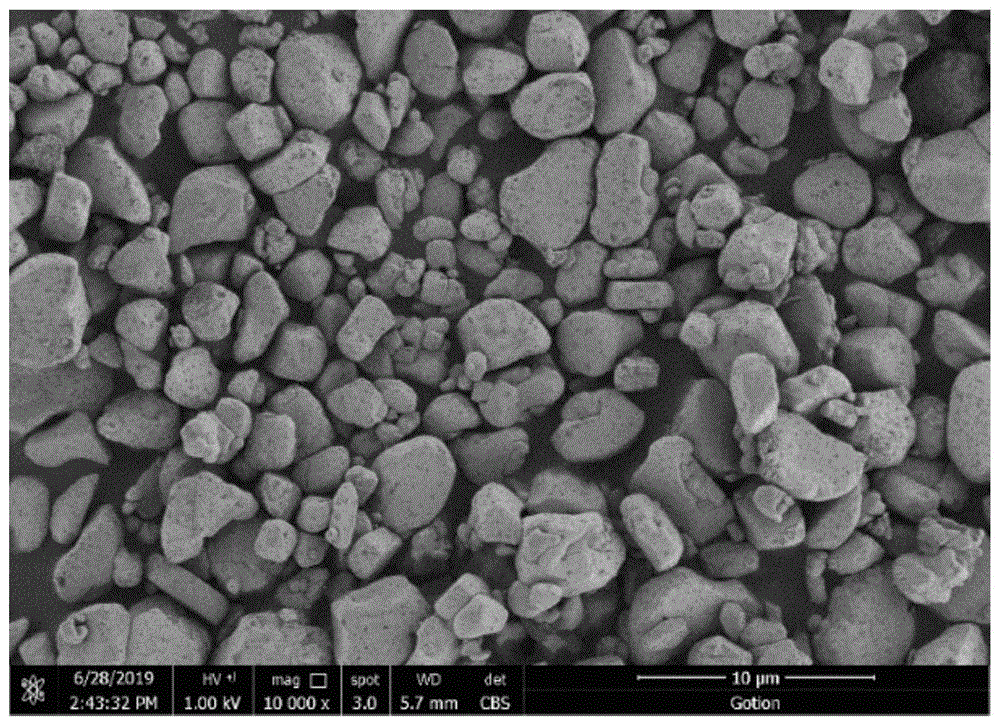
本发明属于锂离子电池正极材料领域,具体涉及一种高镍三元单晶材料及其制备方法。
背景技术:
:随着不可再生能源的日益消耗,世界上各个国家正加速对新能源行业的大力发展,在众多动力能源种类中,锂离子电池具有循环寿命长、能量密度高和绿色环保等优势,是目前为止综合性能最好的化学电源。在锂离子电池中作为最主要材料之一的正极材料,自然而然是研究的热点,其中高镍三元正极材料由于具有较高的镍含量,可以提供较高的充放电比容量,同时较低的钴含量可以有效的降低成本的特点在众多材料中脱颖而出。按照材料的形貌与粒径尺寸,三元正极材料大致可分为单晶材料和多晶材料。其中,单晶材料结构稳定、循环性能优异同时具有较高的压实强度等特点,备受动力电池厂商青睐。单晶材料可以比较有效地解决三元材料的安全问题。中低镍的三元单晶合成相对简单,已经有较多的相关专利。如中国发明专利cn103840151a,利用两步煅烧法合成了特殊形貌的单晶材料linixcoymnzmvo2,但是,0.2≤x≤0.6,属于中低镍范围。中国发明专利cn104979546a,通过合成花簇型的前驱体,与锂源共混,然后烧结合成了单晶三元材料。中国专利申请cn102593442a中公开了一种高压实密度单晶正极材料的制备方法:采用镍钴锰氧化物和碳酸锂在一定的温度和气氛下进行煅烧。中国发明专利cn101847722a通过将微米级前驱体研磨到纳米级后,经高温烧结制备了微米级单晶颗粒。这些单晶专利布局中都涉及到了高镍三元材料合成,但是方法都延续低镍单晶的合成工艺,此类单晶形貌较差、粒度不均匀、表面细粉多,导致材料性能较差。因此急需开发一种能够简单有效地合成高品质高镍大晶粒三元材料的工艺。技术实现要素:本发明所要解决的技术问题是克服
背景技术:
的技术缺陷,提供一种高镍三元单晶材料及其制备方法。本发明通过控制材料前驱体合成工艺快速合成内部疏松多孔的前驱体,并对前驱体进行粉碎分级处理后,将前驱体与锂源混合后先经过低温脱水得到预氧化物后,再经过动态回转炉高温烧结制得性能优异的高镍单晶材料。为实现上述目的,本发明采用的技术方案为:一种高镍三元单晶材料的制备方法,包括如下步骤:(1)将可溶性镍盐、可溶性钴盐、可溶性锰盐与去离子水混合,配成混合盐溶液,记为a1溶液;所述混合盐溶液中ni、co、mn的摩尔比为(1-x-y)∶x∶y,其中:0<x≤0.20,0<y≤0.20;将沉淀剂与去离子水混合,记为a2溶液;将络合剂与去离子水混合,记为a3溶液;(2)将a1溶液、a2溶液、a3溶液同时加入反应容器中进行共沉淀反应,生成粒径为10~15μm的前驱体初期籽晶,在反应容器得到含有前驱体初期籽晶的混合液;(3)去除反应容器中的部分混合液,继续向反应容器中加入a1溶液、a2溶液、a3溶液,继续进行共沉淀反应,直至制备得到粒径为20~40μm的前驱体;对共沉淀产物进行固液分离,去除残液后得到的固体依次经过水洗、烘干后,得到前驱体基材;(4)对前驱体基材进行破碎,经过筛分得到目标粒径的高镍三元单晶前驱体;(5)将高镍三元单晶前驱体与锂源进行混合得到混合物,将混合物先置于氧气气氛下进行低温烧结,得到预氧化物;预氧化物经过破碎后转移至动态回转炉中,在氧气气氛中进行高温烧结后得到最终产物,即高镍三元单晶材料。作为优选的技术方案,步骤(1)中,所述可溶性镍盐为氯化镍、硫酸镍、硝酸镍中的至少一种;所述可溶性钴盐为氯化钴、硫酸钴、硝酸钴中的至少一种;所述可溶性锰盐为氯化锰、硫酸锰、硝酸锰中的至少一种;所述沉淀剂为koh、naoh、na2co3中的至少一种;所述络合剂为氨水、乙二胺四乙酸二钠、磺基水杨酸、甘氨酸中的至少一种。进一步优选的,步骤(1)中,所述a1溶液中金属离子的浓度为1~3mol/l;所述a2溶液中沉淀剂的浓度为10~20mol/l;所述a3溶液中络合剂的浓度为15~30g/l。作为优选的技术方案,步骤(2)中,所述共沉淀反应时控制反应温度为40~100℃,反应时间为10~30h,ph为10~13,搅拌频率为200~600rpm,固含量为10~40%。作为优选的技术方案,步骤(3)中,所述共沉淀反应时控制反应温度为40~100℃,反应时间为10~30h,ph为10~13,搅拌频率为200~600rpm,固含量为20~40%;所述烘干的温度为50~150℃,所述前驱体基材的水含量≤1%。作为优选的技术方案,步骤(4)中,所述破碎为机械破碎、球磨破碎或气流破碎;所述筛分采用的筛网孔径为1000~2000目;所述高镍三元单晶前驱体的d50为3~5μm。作为优选的技术方案,步骤(5)中,所述锂源为碳酸锂、氢氧化锂、醋酸锂、草酸锂中的至少一种;所述低温烧结的温度为300~600℃,时间为2~10h;所述高温烧结的温度为700-950℃,时间为10~20h。进一步优选的,步骤(5)中,所述低温烧结是在管式炉或者辊道窑中进行的;所述高温烧结是在动态回转炉中进行的,所述动态回转炉的转速为5-10rpm/min。本发明的另一个目的是提供上述所述的制备方法制得的高镍三元单晶材料,其化学式为lini1-x-ycoxmnyo2,其中,0<x≤0.20,0<y≤0.20;所述高镍三元单晶材料以单个粒子或几个粒子团聚组成的二次颗粒形式存在,单个粒子的大小在0.5~5μm,材料中位粒径为3~8μm。本发明的基本原理如下:本发明在共沉淀反应的初期,采用常规的反应条件来合成前驱体初期籽晶。当前驱体初期籽晶的粒径生长至10~15μm后,去除反应容器中的部分混合液,目的是减少前驱体籽晶的数量,然后再次加入a1、a2、a3溶液相当于较少的籽晶对应较多的混合盐,即相对性的提高了混合盐与前驱体籽晶的用量比,这样有利于晶体快速长大,生长为内部疏松多孔的晶体,从而能够快速合成大颗粒的前驱体颗粒。然后通过破碎、筛分增加其比表面积后,使其与锂源能够充分接触,进而充分反应,提高最终产品的性能。常规合成单晶前驱体方法的主要特点是前驱体颗粒d50一般为3~5微米,粒径相对较小,合成过程速度相对较慢,形貌难以控制,本专利提供的方法有别于常规小颗粒前驱体的制备过程,先通过合成前驱体籽晶,然后提高反应物相对浓度,使其迅速长大,能够简化缩短前驱体生长过程。另外,本发明高温烧结是在动态回转炉中进行的,动态回转炉使烧结物料处于动态过程,加上氧气气氛,可以让前驱体与氢氧化锂混料在烧结的过程中扩大与氧气的接触面积,增加单位体积物料的氧分压,有助于烧结更加充分,且烧结颗粒不易粘结,省去了常规单晶材料后处理需要先后经过机械粉碎,气流粉碎等高强度处理过程。与现有技术相比,本发明的有益效果为:(1)本发明通过控制材料前驱体合成工艺合成内部疏松多孔的前驱体,并对前驱体进行粉碎筛分,以获得较大的与锂源充分接触反应的比表面积;然后将前驱体与锂源混合先经过低温烧结得预氧化物基材,再于动态回转炉中进行高温烧结得到高镍正极材料;(2)本发明方法制得的高镍单晶正极材料所需要的配锂量更少,烧结温度更低,残余li对材料的副作用较小,材料的容量与长循环性能较为优异(3)本发明方法制得的高镍单晶正极材料晶粒尺寸较大,形态饱满,同时分散均匀,避免了传统小颗粒前驱体固相烧结时,晶粒团聚严重,破碎较为困难的问题亦或需要添加助熔剂。附图说明图1为实施例1制备得到的高镍三元单晶材料的sem图;图2为对比例1制备得到的高镍三元单晶材料的sem图;图3为实施例1和对比例1制备的高镍三元单晶材料制成的扣式电池在室温、0.2c倍率下首次充放电曲线对比图;图4为实施例1和对比例1制备的高镍三元单晶材料制成的扣式电池在室温、1.0c倍率下充放电循环50周容量保持率对比图;具体实施方式为了更好地理解本发明的内容,下面结合具体实施例和附图作进一步说明。应理解,这些实施例仅用于对本发明进一步说明,而不用于限制本发明的范围。此外应理解,在阅读了本发明的内容后,该领域的技术人员对本发明作出一些非本质的改动或调整,仍属于本发明的保护范围。实施例1一种高镍三元单晶材料的制备方法,包括如下步骤:(1)制备镍钴锰盐溶液、沉淀剂溶液和络合剂溶液:将按照化学计量比83∶12∶5比例准确称量的电池级可溶性硫酸镍、硫酸钴、硫酸锰,加入去离子水后通氮气除氧得到50l2mol/l的镍钴锰盐溶液,过滤后标记为a1溶液;将电池级片状naoh粉体加入去离子水中配成10mol/l的氢氧化钠溶液,过滤后标记为沉淀剂a2溶液;将电池级氨水稀释配成18g/l的氨水溶液,过滤后标记为络合剂a3溶液;(2)将a1、a2、a3溶液并流加入反应釜中,向反应釜中通入惰性气体氮气,控制反应釜中的o2小于100ppm,搅拌速率为500r/min,精确控制溶液体系的ph为11.3,氨水浓度为15g/l,反应温度为55℃,反应时间为10h;待晶体生长至预定尺寸d50为10μm的粒度,即得到前驱体初期籽晶;在反应容器得到含有前驱体初期籽晶的混合液;(3)将反应釜中的混合液除去一半,继续加入a1、a2、a3溶液,控制搅拌速率200r/min、精确控制溶液体系的ph为10.8,氨水浓度12g/l,反应温度65℃,反应时间5h,待晶体生长至目标尺寸d50为20μm时反应结束,即得目标产物。将目标产物经过数次水洗后于120℃烘箱中烘干,烘干时控制含水量低于1%。得到前驱体基材;(4)将上述所得前驱体基材经过气流粉碎后分级得到目标粒径d50为3μm的高镍三元单晶前驱体ni0.83co0.12mn0.05(oh)2,备用。(5)将上述高镍三元单晶前驱体和电池级氢氧化锂粉末用三维混料机均匀混合,其中,前躯体中镍钴锰的总物质的量与锂的物质的量比为1∶1.05;混合均匀后,先放入具有氧气气氛的管式炉内烧结,升温至400℃,烧结时长5h,即得低温预氧化物。将预氧化物经过机械破碎,筛出杂质后转移至动态回转炉中,设定转动频率5r/min,升温至820℃,保温15h;整个烧结过程中均通入氧气且氧含量不低于99%,氧气流量10l/min;烧结完成后继续通氧至物料冷却至室温,出料后粗粉碎过筛得到高镍三元单晶材料lini0.83co0.12mn0.05o2。对比例1(1)将市售的高镍三元单晶前驱体ni0.83co0.12mn0.05(oh)2(即采用常规工艺制得的材料)、电池级氢氧化锂粉末用三维混料机均匀混合,其中,前躯体中镍钴锰的总物质的量与锂的物质的量比为1∶1.05;混合均匀后,先放入具有氧气气氛的管式炉内烧结,首先升温至400℃,烧结时长5h;然后升温至820℃,保温15h;整个烧结过程中均通入氧气且氧含量不低于99%,氧气流量10l/min;烧结完成后继续通氧至物料冷却至室温,出料后先经过机械粉碎,再经过气流粉碎分级过筛得到高镍三元单晶材料lini0.83co0.12mn0.05o2。性能检测:利用扫描电子显微镜对实施例1和对比例1制得的高镍三元单晶材料进行表征,其扫描电镜图片分别如图1和图2所示,从图1和图2可知,通过本发明方法制得的高镍三元单晶材料一次颗粒形态饱满,颗粒尺寸相对较大,即使只是经历粗粉碎所得颗粒分散程度较高,粘结团聚态相对较少,而常规方法制得的高镍三元单晶材料一次颗粒尺寸相对较小,颗粒不够饱满圆润,在经历机械粉碎,气流粉碎等一系列高强度破碎后颗粒依然呈现相互粘结且团聚状较多。以实施例1、对比例1制得的高镍三元单晶材料分别为正极材料进行组装锂离子电池。采用本领域技术人员熟知的将正极材料制备成锂离子电池的技术方案,具体方法为:将制得的正极材料、乙炔黑与聚偏氟乙烯(pvdf)按94∶3∶3质量比称取,混合均匀,加入nmp搅拌2h,成粘稠状浆料,均匀涂布在铝箔上,后80℃真空烘烤,压片,裁切直径为14mm的正极片。以直径16mm的纯锂片作为负极片,以1mol/llipf6+dec/ec(体积比1∶1)混合溶液为电解液,以聚celgard丙烯微孔膜为隔膜,在充满氩气的手套箱中进行组装成扣式电池。采用land电池测试系统(ct2001a),在2.75~4.3v的电压范围内,25℃、0.2c充放电条件下,测试上述扣式电池首次放电比容量。实施例1和对比例1中制备的材料制成的扣式电池在0.2c倍率下首次充放电曲线对比图如图3所示。可知,实施例1制备的高镍三元单晶材料制成的扣式电池25℃、0.2c条件下首次放电比容量为201.2mah/g。经测试,该正极片的压实密度为3.55g/cm3。对比例1制备的高镍三元单晶材料制备的扣式电池25℃、0.2c条件下首次放电比容量为196.7mah/g。经测试,该正极片的压实密度为3.43g/cm3。测试实施例1与对比例1中电池在1.0c充放电循环50周容量保持率,测试设备同上,结果如图4所示。测试结果为:实施例1制备的高镍三元单晶材料制备的扣式电池1.0c充放电循环50周容量保持率>93%。本发明对比例1和实施例1制备的高镍单晶正极材料的残余碱含量如下表1所示。从表1可知通过本发明方法制得的高镍三元单晶材料ph值与残留碱的总量相对较低,游离锂的含量也相对较低,有助于减少活性材料与电解液之间的副反应,提升材料的电性能。表1高镍单晶正极材料的残余碱含量数据表编号lioh(wt.%)li2co3(wt.%)freeli(wt.%)ph对比例10.30880.19080.125412.11实施例10.22780.12410.089411.98实施例2一种高镍三元单晶材料的制备方法,包括如下步骤:(1)制备镍钴锰盐溶液、沉淀剂溶液和络合剂溶液:将按照化学计量比80∶10∶10比例准确称量的电池级可溶性硫酸镍、硫酸钴、硫酸锰,加入去离子水后通氮气除氧得到50l2mol/l的镍钴锰盐溶液,过滤后标记为a1溶液;将电池级片状naoh粉体加入去离子水中配成10mol/l的氢氧化钠溶液,过滤后标记为沉淀剂a2溶液;将电池级氨水稀释配成18g/l的氨水溶液,过滤后标记为络合剂a3溶液;(2)将a1、a2、a3溶液并流加入反应釜中,向反应釜中通入惰性气体氮气,控制反应釜中的o2小于100ppm,搅拌速率为500r/min,精确控制溶液体系的ph为11.3,氨水浓度为15g/l,反应温度为55℃,反应时间为10h;待晶体生长至预定尺寸d50为12μm的粒度,即得到前驱体初期籽晶;在反应容器得到含有前驱体初期籽晶的混合液;(3)将反应釜中的混合液除去一半,继续加入a1、a2、a3溶液,控制搅拌速率200r/min、精确控制溶液体系的ph为10.8,氨水浓度12g/l,反应温度65℃,反应时间10h,待晶体生长至目标尺寸d50为30μm时反应结束,即得目标产物。将目标产物经过数次水洗后于120℃烘箱中烘干,烘干时控制含水量低于1%,得到前驱体基材;(4)将上述所得前驱体基材经过气流粉碎后分级得到目标粒径d50为3.5μm的高镍三元单晶前驱体ni0.80co0.10mn0.10(oh)2,备用。(5)将上述高镍三元单晶前驱体、电池级氢氧化锂粉末用三维混料机均匀混合,其中,前躯体中镍钴锰的总物质的量与锂的物质的量比为1∶1.07;混合均匀后,先放入具有氧气气氛的管式炉内烧结,升温至450℃,烧结时长5h,即得低温预氧化物。将预氧化物经过机械破碎,筛出杂质后转移至动态回转炉中,设定转动频率5r/min,升温至850℃,保温15h;整个烧结过程中均通入氧气且氧含量不低于99%,氧气流量10l/min;烧结完成后继续通氧至物料冷却至室温,出料后粗粉碎过筛得到高镍三元单晶材料lini0.80co0.10mn0.10o2;对比例2将市售的高镍三元单晶前驱体ni0.80co0.10mn0.10(oh)2、电池级氢氧化锂粉末用三维混料机均匀混合,其中,前躯体中镍钴锰的总物质的量与锂的物质的量比为1∶1.07;混合均匀后,先放入具有氧气气氛的管式炉内烧结,首先升温至450℃,烧结时长5h;然后升温至850℃,保温15h;整个烧结过程中均通入氧气且氧含量不低于99%,氧气流量10l/min;烧结完成后继续通氧至物料冷却至室温,出料后先经过机械粉碎,再经过气流粉碎分级过筛得到高镍三元单晶材料lini0.80co0.10mn0.10o2;采用与实施例1相同的电池组装方法和测试方法,对实施例2和对比例2制备的高镍三元单晶材料lini0.80co0.10mn0.10o2制成扣式电池,并进行测试,测试结果为:实施例2制备的高镍三元单晶材料制成的扣式电池在25℃、0.2c条件下首次放电比容量为195.6mah/g。经测试,该正极片的压实密度为3.61g/cm3。对比例2制备的高镍三元单晶材料制备的扣式电池25℃、0.2c条件下首次放电比容量为191.3mah/g。经测试,该正极片的压实密度为3.53g/cm3。测试实施例2与对比例2中电池在1.0c充放电循环50周容量保持率。测试结果为:实施例2制备的高镍三元单晶材料制备的扣式电池1.0c充放电循环50周容量保持率95.1%,实施例2的容量保持率93.3%。实施例3一种高镍三元单晶材料的制备方法,包括如下步骤:(1)制备镍钴锰盐溶液、沉淀剂溶液和络合剂溶液:将按照化学计量比70∶10∶20比例准确称量的电池级可溶性硫酸镍、硫酸钴、硫酸锰,加入去离子水后通氮气除氧得到50l2mol/l的镍钴锰盐溶液,过滤后标记为a1溶液;将电池级片状naoh粉体加入去离子水中配成10mol/l的氢氧化钠溶液,过滤后标记为沉淀剂a2溶液;将电池级氨水稀释配成18g/l的氨水溶液,过滤后标记为络合剂a3溶液;(2)将a1、a2、a3溶液并流加入反应釜中,向反应釜中通入惰性气体氮气,控制反应釜中的o2小于100ppm,搅拌速率为500r/min,精确控制溶液体系的ph为11.3,氨水浓度为15g/l,反应温度为55℃,反应时间为15h;待晶体生长至预定尺寸d50为15μm的粒度后,即得到前驱体初期籽晶;在反应容器得到含有前驱体初期籽晶的混合液;(3)将反应釜中的混合液除去一半,继续加入a1、a2、a3溶液,控制搅拌速率200r/min、精确控制溶液体系的ph为10.8,氨水浓度12g/l,反应温度65℃,反应时间8h,待晶体生长至目标尺寸d50为34μm时反应结束,即得目标产物。将目标产物经过数次水洗后于120℃烘箱中烘干,烘干时控制含水量低于1%,得到前驱体基材;(4)将上述所得前驱体基材经过气流粉碎后分级得到目标粒径d50为5μm的高镍三元单晶前驱体ni0.70co0.10mn0.20(oh)2,备用。(5)将上述高镍正极材料前驱体、电池级碳酸锂粉末用三维混料机均匀混合,其中,前躯体中镍钴锰的总物质的量与锂的物质的量比为1∶1.10;混合均匀后,先放入具有氧气气氛的管式炉内烧结,升温至500℃,烧结时长5h,即得低温预氧化物。将预氧化物经过机械破碎,筛出杂质后转移至动态回转炉中,设定转动频率5r/min,升温至900℃,保温15h;整个烧结过程中均通入氧气且氧含量不低于99%,氧气流量10l/min;烧结完成后继续通氧至物料冷却至室温,出料后粗粉碎过筛得到高镍三元单晶材料lini0.70co0.10mn0.20o2;对比例3将市售的高镍三元单晶前驱体ni0.70co0.10mn0.20(oh)2、电池级碳酸锂粉末用三维混料机均匀混合,其中,前躯体中镍钴锰的总物质的量与锂的物质的量比为1∶1.10;混合均匀后,先放入具有氧气气氛的管式炉内烧结,首先升温至500℃,烧结时长5h;然后升温至900℃,保温15h;整个烧结过程中均通入氧气且氧含量不低于99%,氧气流量10l/min;烧结完成后继续通氧至物料冷却至室温,出料后先经过机械粉碎,再经过气流粉碎分级过筛得到高镍三元单晶材料lini0.70co0.10mn0.20o2;采用与实施例1相同的电池组装方法和测试方法,对实施例3和对比例3制备的高镍三元单晶材料lini0.70co0.10mn0.20o2制成扣式电池,并进行测试,测试结果为:实施例3制备的高镍三元单晶材料制备的扣式电池25℃、0.2c条件下首次放电比容量为182.5mah/g。经测试,该正极片的压实密度为3.57g/cm3。对比例3制备的高镍三元单晶材料制备的扣式电池25℃、0.2c条件下首次放电比容量为179.6mah/g。经测试,该正极片的压实密度为3.53g/cm3。测试实施例3与对比例3于1.0c充放电循环50周容量保持率。测试结果为:实施例3制备的高镍三元单晶材料制备的扣式电池1.0c充放电循环50周容量保持率96.4%,对比例3的容量保持率为95.1%。实施例4一种高镍三元单晶材料的制备方法,包括如下步骤:(1)制备镍钴锰盐溶液、沉淀剂溶液和络合剂溶液:将按照化学计量比65∶15∶20比例准确称量的电池级可溶性硫酸镍、硫酸钴、硫酸锰,加入去离子水后通氮气除氧得到50l2mol/l的镍钴锰盐溶液,过滤后标记为a1溶液;将电池级片状naoh粉体加入去离子水中配成10mol/l的氢氧化钠溶液,过滤后标记为沉淀剂a2溶液;将电池级氨水稀释配成18g/l的氨水溶液,过滤后标记为络合剂a3溶液;(2)将a1、a2、a3溶液并流加入反应釜中,向反应釜中通入惰性气体氮气,控制反应釜中的o2小于100ppm,搅拌速率为600r/min,精确控制溶液体系的ph为11.0,氨水浓度为15g/l,反应温度为50℃,反应时间为10h;待晶体生长至预定尺寸d50为10μm的粒度,即得到前驱体初期籽晶;在反应容器得到含有前驱体初期籽晶的混合液;(3)将反应釜中的混合液除去一半,继续加入a1、a2、a3溶液,控制搅拌速率200r/min、精确控制溶液体系的ph为10.8,氨水浓度12g/l,反应温度60℃,反应时间5h,待晶体生长至目标尺寸d50为20μm时反应结束,即得目标产物。将目标产物经过数次水洗后于120℃烘箱中烘干,烘干时控制含水量低于1%,得到前驱体基材。(4)将上述所得前驱体基材经过气流粉碎后分级得到目标粒径d50为3μm的高镍三元单晶前驱体ni0.65co0.15mn0.20(oh)2,备用。(5)将上述高镍三元单晶前驱体、电池级碳酸锂粉末用三维混料机均匀混合,其中,前躯体中镍钴锰的总物质的量与锂的物质的量比为1∶1.10;混合均匀后,先放入具有氧气气氛的管式炉内烧结,升温至500℃,烧结时长5h,即得低温预氧化物。将预氧化物经过机械破碎,筛出杂质后转移至动态回转炉中,设定转动频率5r/min,升温至930℃,保温15h;整个烧结过程中均通入氧气且氧含量不低于99%,氧气流量10l/min;烧结完成后继续通氧至物料冷却至室温,出料后粗粉碎过筛得到高镍三元单晶材料lini0.65co0.15mn0.20o2;对比例4将市售的高镍三元单晶前驱体ni0.65co0.15mn0.20(oh)2、电池级碳酸锂粉末用三维混料机均匀混合,其中,前躯体中镍钴锰的总物质的量与锂的物质的量比为1∶1.10;混合均匀后,先放入具有氧气气氛的管式炉内烧结,首先升温至500℃,烧结时长5h;然后升温至930℃,保温15h;整个烧结过程中均通入氧气且氧含量不低于99%,氧气流量10l/min;烧结完成后继续通氧至物料冷却至室温,出料后先经过机械粉碎,再经过气流粉碎分级过筛得到高镍三元单晶材料lini0.65co0.15mn0.20o2;采用与实施例1相同的电池组装方法和测试方法,对实施例4和对比例4制备的高镍三元单晶材料lini0.65co0.15mn0.20o2制成扣式电池,并进行测试,测试结果为:实施例4制备的高镍三元单晶材料制备的扣式电池25℃、0.2c条件下首次放电比容量为177.5mah/g。经测试,该正极片的压实密度为3.45g/cm3。对比例4制备的高镍三元单晶材料制备的扣式电池25℃、0.2c条件下首次放电比容量为173.9mah/g。经测试,该正极片的压实密度为3.44g/cm3。测试实施例4与对比例4于1.0c充放电循环50周容量保持率。测试结果为:实施例4制备的高镍三元单晶材料制备的扣式电池1.0c充放电循环50周容量保持率98.9%,对比例4的容量保持率为96.6%。综上所述,本发明方法制得的高镍单晶三元正极材料所需要的配锂量更少,烧结温度更低,残余li较少,颗粒生长较大且分散均一,团聚较少,后处理加工相对容易同时通过该方法制备得到的高镍单晶三元正极材料具有晶型完整、结构稳定,制备的锂离子电池具有更好的容量、长循环性能更加优异,可以满足动力电池市场上对于长循环寿命和高容量性能的需求。上述说明并非对发明的限制,本发明也并不限于上述举例。本
技术领域:
的普通技术人员在发明的实质范围内,做出的变化、改型、添加或替换,也应属于本发明的保护范围。当前第1页12