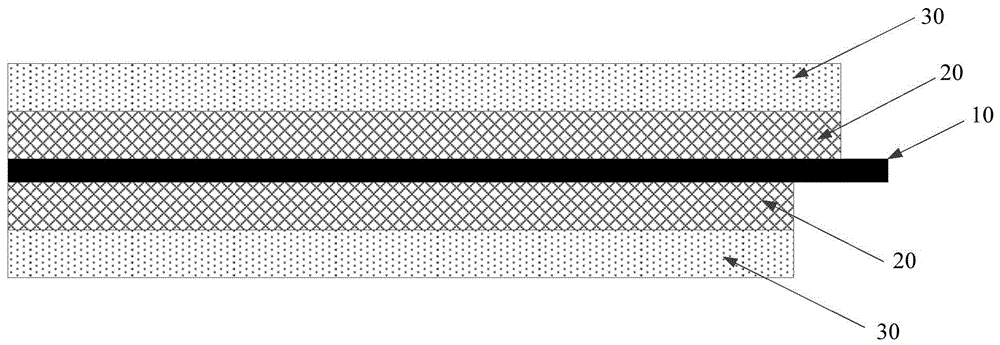
本发明涉及电池材料
技术领域:
,特别涉及一种正极片、正极片的制备方法和电池。
背景技术:
:锂离子电池因具有能量密度大、无记忆效应、寿命长等优点广泛应用于智能手机、笔记本电脑、蓝牙、穿戴设备等领域。随着锂离子电池的大规模的应用,电池的安全问题日益凸显。在一些极端情况下,如锂离子电池遭受机械破坏,例如针刺或者重物冲击等,容易触发正极片铝箔与负极石墨之间的接触,造成电池内短路,进而引发热失控,导致电池起火损毁,这表明锂离子电池存在较大的安全隐患。技术实现要素:本发明实施例的目的在于提供一种正极片、正极片的制备方法和电池,解决锂离子电池存在较大安全隐患的技术问题。为了达到上述目的,本发明实施例提供一种正极片,所述正极片包括集流体、第一活性物质层和第二活性物质层;所述集流体的至少一侧设有所述第一活性物质层,所述第一活性物质层远离所述集流体的一侧设有所述第二活性物质层;所述第一活性物质层包括第一活性物质、第一导电剂和第一粘结剂,所述第二活性物质层包括第二活性物质、第二导电剂和第二粘结剂,所述第一活性物质包括陶瓷颗粒;其中,所述第一粘结剂在所述第一活性物质层中的质量百分比高于所述第二粘结剂在所述第二活性物质层中的质量百分比。可选地,所述陶瓷颗粒包括氧化铝、勃姆石、氧化镁、氧化钛、氧化锆、氧化硅和氧化钇中的至少一种。可选地,所述陶瓷颗粒的中粒径为0.3~0.5μm,所述第一活性物质层的厚度为3~5μm。可选地,所述第一活性物质层的孔隙率与第二活性物质层的孔隙率之间的比值为1~3。可选地,所述第一活性物质层的孔隙率与第二活性物质层的孔隙率之间的比值为1.5~2.5。可选地,在所述第一活性物质层中,所述第一活性物质的质量百分比为70%~90%,所述第一导电剂的质量百分比为5%~10%,所述第一粘结剂的质量百分比为5%~20%。可选地,所述第二活性物质包括钴酸锂,所述钴酸锂的中粒径为5~20μm,所述第二活性物质层的厚度为35~60μm。、可选地,在所述第二活性物质层中,所述第二活性物质的质量百分比为90%~98%,所述第二导电剂的质量百分比为1%~6%,所述第二粘结剂的质量百分比为1%~4%。本发明实施例还提供一种正极片的制备方法,包括:提供集流体;在所述集流体的至少一侧涂覆第一活性物质层,在所述第一活性物质层远离所述集流体的一侧涂覆第二活性物质层;所述第一活性物质层包括第一活性物质、第一导电剂和第一粘结剂,所述第二活性物质层包括第二活性物质、第二导电剂和第二粘结剂,所述第一活性物质包括陶瓷颗粒;其中,所述第一粘结剂在所述第一活性物质层中的质量百分比高于所述第二粘结剂在所述第二活性物质层中的质量百分比。本发明实施例还提供一种电池,所述电池包括上述的正极片。上述技术方案中的一个技术方案具有如下优点或有益效果:本申请实施例中,在集流体和第二活性物质层之间设置第一活性物质层,且第一粘结剂在第一活性物质层中的质量百分比高于第二粘结剂在第二活性物质层中的质量百分比,以此提高第一活性物质层与集流体的粘接程度,在锂离子电池遭受机械破坏的情况下或者在锂离子电池的针刺实验中,避免正极片铝箔与负极石墨接触,防止电池内短路现象的发生,进而提高锂离子电池的安全性。附图说明图1为本发明实施例提供的正极片的结构示意图;图2为本发明实施例提供的正极片的制备方法的流程图;图3为本发明实施例提供的循环测试的测试结果示意图。附图标号说明:10、集流体;20、第一活性物质层;30、第二活性物质层。具体实施方式下面将结合本发明实施例中的附图,对本发明实施例中的技术方案进行清楚、完整地描述,显然,所描述的实施例是本发明一部分实施例,而不是全部的实施例。基于本发明中的实施例,本领域普通技术人员在没有做出创造性劳动前提下所获得的所有其他实施例,都属于本发明保护的范围。请参阅图1,图1为本发明实施例提供的正极片的结构图。本实施例中的正极片包括集流体10、第一活性物质层20和第二活性物质层30;所述集流体10的至少一侧设有所述第一活性物质层20,所述第一活性物质层20远离所述集流体10的一侧设有所述第二活性物质层30;所述第一活性物质层20包括第一活性物质、第一导电剂和第一粘结剂,所述第二活性物质层30包括第二活性物质、第二导电剂和第二粘结剂,所述第一活性物质包括陶瓷颗粒;其中,所述第一粘结剂在所述第一活性物质层20中的质量百分比高于所述第二粘结剂在所述第二活性物质层30中的质量百分比。上述集流体10可以由铝箔构成,应理解,在一些实施例中,集流体10也可以是铜箔或者其他材质。在集流体10的至少一侧设有第一活性物质层20,在第一活性物质层20远离集流体10的一侧设有第二活性物质层30。优选地,如图1所示,可以使用双层涂布装置在集流体10的相对两侧涂覆第一活性物质层20和第二活性物质层30,其中,如图1所示,集流体10相对两侧涂层的厚度相同,集流体10相对两侧涂层的长度不同;应理解,在一些实施例中,集流体10相对两侧涂层的长度相同。上述第一活性物质层20用于分隔集流体10和负极石墨,上述第一活性物质层20包括第一活性物质、第一导电剂和第一粘结剂。其中,第一活性物质包括陶瓷颗粒。可选地,陶瓷颗粒包括氧化铝、勃姆石、氧化镁、氧化钛、氧化锆、氧化硅和氧化钇中的至少一种。作为一种优先的实施方案,陶瓷颗粒为中粒径较小的氧化铝。上述第二活性物质层30用于增加电池容量,使得电池拥有更高的能量密度,上述第二活性物质层30包括第二活性物质、第二导电剂和第二粘结剂,其中,第二活性物质可以是克容量较高的钴酸锂,应理解,在其他实施例中,第二活性物质也可以是石墨等活性物质。本实施例中,第一导电剂和第二导电剂为同一导电剂,第一粘结剂和第二粘结剂为同一粘结剂。作为一种可选的实施方式,第一导电剂和所述第二导电剂包括导电石墨、超微细石墨、乙炔黑、导电炭黑、超导炭黑、碳纳米管和导电碳纤维中的至少一种;所述第一粘结剂和所述第二粘结剂包括聚偏二氟乙烯、聚四氟乙烯、羧甲基纤维素钠、丁苯橡胶、聚氨酯、聚乙烯醇、聚偏氟乙烯和偏氟乙烯-氟化烯烃的共聚物中的至少一种。在另一些实施例中,第一导电剂和第二导电剂不为同一导电剂,第一粘结剂和第二粘结剂不为同一粘结剂。例如,第一导电剂为导电石墨,第二导电剂为导电炭黑,第一粘结剂为聚偏二氟乙烯,第二粘接剂为聚氨酯。本实施例中,设置第一粘结剂在第一活性物质层20中的质量百分比高于第二粘结剂在第二活性物质层30中的质量百分比,以此提高第一活性物质层20与正极片集流体10的粘接程度,起到保护集流体10的作用。本申请实施例中,在集流体10和第二活性物质层30之间设置第一活性物质层20,且第一粘结剂在第一活性物质层20中的质量百分比高于第二粘结剂在第二活性物质层30中的质量百分比,以此提高第一活性物质层20与集流体10的粘接程度,在锂离子电池遭受机械破坏的情况下或者在锂离子电池的针刺实验中,避免正极片铝箔与负极石墨接触,防止电池内短路现象的发生,进而提高锂离子电池的安全性。在一些实施方式中,第一活性物质为钴酸锂、多孔碳或者其他粒径较大活性物质,这种情况下,由于第一活性物质的粒径较大,因此提高了由第一活性物质组成的第一活性物质层20的厚度,在正极片制备过程中,集流体10一侧涂层的总厚度不变,这样,降低了第二活性物质层30的厚度。如上所述,第二活性物质层30用于增加电池容量和能量目的,第二活性物质层30厚度的降低将减少电池的容量和能量密度。基于上述存在的技术问题,本实施例中选用粒径较小的第一活性物质构成第一活性物质层20,以降低第一活性物质层20的厚度,这样,可以增加第二活性物质层30的厚度,达到增加电池容量,提高电池能量密度的目的。可选地,所述陶瓷颗粒的中粒径为0.3~0.5μm,所述第一活性物质层20的厚度为3~5μm。本实施例中,上述陶瓷颗粒的中粒径为0.3~0.5μm,由陶瓷颗粒构成的第一活性物质层20的厚度为3~5μm。其中,中粒径为颗粒累积分布为50%的粒径,例如,一个样品的中粒径为5μm,表明组成该样品的所有粒径的颗粒中,粒径大于5μm的颗粒占50%,粒径小于等于5μm的颗粒也占50%。可选地,所述第二活性物质包括钴酸锂,所述钴酸锂的中粒径为5~20μm,所述第二活性物质层30的厚度为35~60μm。第二活性物质包括中粒径为5~20μm的钴酸锂,由钴酸锂构成的第二活性物质层30的厚度为35~60μm。应理解,第二活性物质也可以为多孔碳、石墨等导电活性物质。如上所述,陶瓷颗粒的中粒径为0.3~0.5μm,钴酸锂的中粒径为5~20μm,若第一活性物质为钴酸锂,或者其他粒径高于陶瓷颗粒的活性物质,由钴酸锂或其他粒径高于陶瓷颗粒的活性物质构成的第一活性物质层20的厚度也会大于3~5μm,这样,将降低电池的容量和能量密度。本实施例中,使用陶瓷颗粒作为第一活性物质,其中,优选使用氧化铝作为第一活性物质,利用氧化铝粒径较小的特点,降低第一活性物质层20的厚度,以此提高电池的容量和能量密度。可选地,所述第一活性物质层20的孔隙率与第二活性物质层30的孔隙率之间的比值为1~3。可选地,所述第一活性物质层20的孔隙率与第二活性物质层30的孔隙率之间的比值为1.5~2.5。应理解,可以计算活性物质层的表观体积与活性物质层的真体积之间的差值,将上述差值结果与活性物质层的表观体积相除,得到该活性物质层的孔隙率。其中,活性物质层的表观体积为该活性物质层的厚度、宽度与高度之间的乘积,再将该乘积结果与1000相除得到。其中,活性物质层的真体积可以通过检测装置,例如真密度仪测量得到。真密度仪测量真体积的原理为:真密度仪应用阿基米德原理—气体膨胀置换法,利用小分子直径的惰性气体在一定条件下的玻尔定律,通过测定由于样品测试腔放入样品所引起的样品测试腔气体容量的变化来精确测定样品的真体积。其中,活性物质层的孔隙率能够反映活性物质层中活性物质颗粒的堆积情况。本实施例中,由于第一活性物质层20设置在集流体10的表面,因此第一活性物质层20的孔隙率越高,则第一活性物质层20中各第一活性物质颗粒的堆积越密集,第一活性物质层20与集流体10的粘接程度越高。在锂离子电池遭受机械破坏的情况下或者在锂离子电池的针刺实验中,孔隙率越高的第一活性物质层20能更好的保护集流体10,避免正极片铝箔与负极石墨接触,防止电池内短路现象的发生,进而提高锂离子电池的安全性。在本实施例中,作为一种优选方案,设置第一活性物质层20的孔隙率与第二活性物质层30的孔隙率之间的比值为1.5~2.5,应理解,在一些实施例中,第一活性物质层20的孔隙率与第二活性物质层30的孔隙率之间的比值可以为1~3之内的其他数值,同样可以避免正极片铝箔与负极石墨接触,防止电池内短路现象的发生,提高锂离子电池的安全性。可选地,在所述第一活性物质层20中,所述第一活性物质的质量百分比为70%~90%,所述第一导电剂的质量百分比为5%~10%,所述第一粘结剂的质量百分比为5%~20%。可选地,在所述第二活性物质层30中,所述第二活性物质的质量百分比为90%~98%,所述第二导电剂的质量百分比为1%~6%,所述第二粘结剂的质量百分比为1%~4%。本实施例中,第一活性物质层20中第一粘结剂的质量百分比为5%~10%,第二活性物质层30中第二粘结剂的质量百分比为1%~6%,设置第一粘结剂在第一活性物质层20中的质量百分比高于第二粘结剂在第二活性物质层30中的质量百分比,以提高第一活性物质层20与正极片集流体10的粘接程度,保护集流体10。本实施例中,第二活性物质层30中第二活性物质的质量百分比为90%~98%,在第二活性物质层30中设置质量百分比较高的第二活性物质,以此提高电池的容量和能量密度。本发明实施例还提供了一种正极片的制备方法,请参阅图2,所述方法包括:s101,提供集流体。本实施例中的集流体为铜箔、铝箔或者其他材质的箔材,在此不做具体限定,上述集流体用于将活性物质产生的电流汇集起来以便形成较大的电流对外输出。s102,在所述集流体的至少一侧涂覆第一活性物质层,在所述第一活性物质层远离所述集流体的一侧涂覆第二活性物质层。本实施例中,可以使用双层涂布装置在集流体的至少一侧涂覆第一活性物质层,在第一活性物质层远离集流体的一侧涂覆第二活性物质层。优先地,可以使用双层涂布装置在集流体的相对两侧涂覆第一活性物质层,在第一活性物质层远离集流体的一侧涂覆第二活性物质层。其中,第一活性物质层用于分隔集流体和负极石墨,第一活性物质层包括第一活性物质、第一导电剂和第一粘结剂,第一活性物质包括陶瓷颗粒。第二活性物质层用于增加电池容量和能量目的,第二活性物质层包括第二活性物质、第二导电剂和第二粘结剂,第二活性物质可以是钴酸锂。第一活性物质层的厚度为3~5μm;第二活性物质层的厚度为35~60μm。本实施例中,选用粒径较小的第一活性物质构成第一活性物质层,以降低第一活性物质层的厚度,这样,可以增加第二活性物质层的厚度,达到增加电池容量,提高电池能量密度的目的。其中,第一粘结剂在第一活性物质层中的质量百分比高于第二粘结剂在第二活性物质层中的质量百分比。本实施例中,设置第一粘结剂在第一活性物质层中的质量百分比高于第二粘结剂在第二活性物质层中的质量百分比,以此提高第一活性物质层与正极片集流体的粘接程度,起到保护集流体的作用。本申请实施例中,在集流体和第二活性物质层之间设置第一活性物质层,且第一粘结剂在第一活性物质层中的质量百分比高于第二粘结剂在第二活性物质层中的质量百分比,以此提高第一活性物质层与集流体的粘接程度,在锂离子电池遭受机械破坏的情况下或者在锂离子电池的针刺实验中,避免正极片铝箔与负极石墨接触,防止电池内短路现象的发生,进而提高锂离子电池的安全性。根据上述正极片的结构,设置实施例1-3和对比例1。实施例1:将80wt%的氧化铝、5wt%的导电炭黑和15wt%的聚偏氟乙烯混合,加入n-甲基吡咯烷酮搅拌分散制成正极内层浆料,即第一活性物质层浆料。将97.8wt%的钴酸锂、1.1wt%的导电炭黑和1.1wt%的聚偏氟乙烯混合,加入n-甲基吡咯烷酮搅拌分散制成正极外层浆料,即第二活性物质层浆料。使用双层涂布设备把正极内层浆料和正极外层浆料涂布在正极片集流体上,正极内层浆料涂布至正极片集流体表面形成第一活性物质层,正极外层浆料涂布至第一活性物质层表面形成第二活性物质层。其中,第一活性物质层的孔隙率与第二活性物质层的孔隙率的比值为2.3。然后经过烘干工艺、分切工艺和制片工艺,制备得到正极片。将96.9wt%的人造石墨、0.5wt%的导电炭黑、1.3wt%的羧甲基纤维素钠和1.3wt%的丁苯橡胶混合,加入去离子水搅拌分散制成负极浆料。把负极浆料涂布在负极片集流体上,然后经过烘干工艺、分切工艺和制片工艺,制备得到负极片。将正极片、负极片、隔膜、铝塑膜经过注液工艺、陈化工艺、化成工艺和分选工艺等工序制成电池。实施例2:实施例2与上述实施例1的区别在于,实施例2中的正极内层浆料由88wt%的氧化铝、3wt%的导电炭黑和9wt%的聚偏氟乙烯制成;且第一活性物质层的孔隙率与第二活性物质层的孔隙率的比值为1.5。实施例3:实施例3与上述实施例1的区别在于,实施例3中的正极内层浆料由72wt%的氧化铝、7wt%的导电炭黑和21wt%的聚偏氟乙烯制成;且第一活性物质层的孔隙率与第二活性物质层的孔隙率的比值为3。实施例4:实施例4与上述实施例1的区别在于,实施例4中的第一活性物质层的孔隙率与第二活性物质层的孔隙率的比值为0.6。实施例5:实施例5与上述实施例1的组别在于,实施例5中的第一活性物质层的孔隙率与第二活性物质层的孔隙率的比值为5。对比例1:对比例1与上述实施例1的区别在于,对比例1不设置有第一活性物质层,集流体上只涂布第二活性物质层。对上述实施例1-实施例3和对比例1进行针刺测试和循环测试,测试结果如表一所示:表一:针刺测试通过率电池容量保持率实施例110/1085.83%实施例210/1075.90%实施例36/1086.56%实施例410/1076.59%实施例54/1069.98%对比例10/1089.62%其中,针刺测试是使用直径为3.5至4.5mm,圆锥角度为45℃至60℃,表面光洁无锈蚀、无氧化层及无油污的耐高温钢针,以25mm至35mm的速度,从垂直于电芯极板的方向贯穿,穿刺位置靠近所刺面的几何中心,且钢针停留在电芯中。在上述状态下,观察1小时,或者,电芯的表面温度为电芯的峰值温度与10的差值时,停止测试,得到测试结果。其中,循环测试是将电池放置于25℃恒温房中,以0.7c对电池放电至电池的下限电压,以1.5c对电池充电至电池的上限电压,再以1c对电池放电至下限电压,上述三个充放电操作为一个测试周期,如此循环800次计算电池的容量保持率。从表一中的针刺测试通过率可知,实施例1和2的针刺测试通过率为100%,实施例3的针刺测试通过率为60%,实施例4的针刺通过率为100%,实施例5的针刺通过率为40%,对比例1的针刺测试通过率为0%。对比例1的针刺测试通过率低,不满足锂离子电池的安全性能要求,实施例1-5的针刺实验通过率均高于对比例1,可以有效提升了锂离子电池的安全性。进一步的,请参阅图3,图3示出了实施例1-5和对比例1在循环测试的测试结果,其中,图3中的横坐标轴表征循环次数,纵坐标轴表征电池容量保持率。结合图3和表一可以得到,实施例1对应的电池容量保持率和针刺测试通过率更优,实施例1提供的电池的安全性更佳以及电池的使用寿命越长。本发明实施例还提供一种电池,该电池包括负极片、隔膜、电解液和上述的正极片,该正极片的结构可以参照上述实施例,具体在此不再赘述。由于在本实施例中,采用了上述实施例中的正极片,因此本发明实施例提供的电池具有与上述实施例中正极片相同的有益效果。以上所述,仅为本发明的具体实施方式,但本发明的保护范围并不局限于此,任何熟悉本
技术领域:
的技术人员在本发明揭露的技术范围内,可轻易想到变化或替换,都应涵盖在本发明的保护范围之内。因此,本发明的保护范围应以权利要求的保护范围为准。当前第1页12