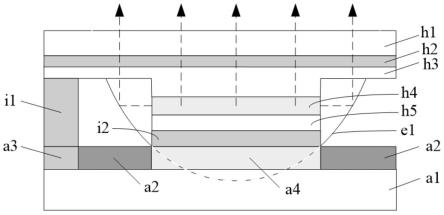
发光准直的microled显示器件及其制备方法
技术领域
1.本发明涉及显示技术领域,特别是一种发光准直的microled显示器件及其制备方法。
背景技术:2.microled(微小发光二极管)是业界公认的新一代显示技术,除用于平板显示外,硅基上的microled微显示器件还可以用于投影显示、vr/ar(虚拟显示/增强现实)等近眼显示。在投影显示和近眼显示产品上,microled像素发出的光需要耦合到光学成像系统以得到放大的图像,而为了获得清晰的图像,microled显示器件须安装在光学成像系统的焦平面位置,加上受物理装配尺寸的限制,通常显示器件与光学成像系统之间有一定的距离;另一方面,常规microled显示器件的像素发光角度接近180度,因而大部分光不能耦合进光学成像系统而导致光的泄漏损失,最终导致投影显示或近眼显示产品的亮度不够,功耗较大。
3.为了减小microled像素的光发射角,实现准直发光,有业内公司或研究机构提出在microled显示器件的发光表面增加微透镜阵列的技术方案,但该技术方案难以保证微透镜阵列的制作精准度,且微透镜阵列对光有较大衰减,导致microled显示器件的发光亮度降低。
技术实现要素:4.为解决现有技术中存在的问题,本发明的目的是提供一种发光准直的microled显示器件及其制备方法,本发明可以使microled像素的发光角度显著减小,沿像素发光面的垂直方向以近乎0度准直发光,从而极大地提高microled显示器件与光学成像系统之间的光耦合效率,且可以提高microled出光效率,进而提高投影或近眼显示等整机产品的亮度,降低功耗。
5.为实现上述目的,本发明采用的技术方案是:一种发光准直的microled显示器件,包括若干按行列排列的发光像素单元,每一个所述发光像素单元包括驱动背板和发光二极管,所述发光二极管与驱动背板键合在一起,还包括设于所述驱动背板上的类抛物镜,所述类抛物镜用于反射所述发光二极管所发出的光,使其准直发出。
6.作为本发明的进一步改进,所述驱动背板包括驱动芯片、绝缘层、像素公共电极和像素驱动电极,所述像素公共电极布置在驱动芯片的周边,并与驱动芯片的接地端相连;所述像素驱动电极与驱动芯片内的驱动晶体管的输出电极相连,所述绝缘层覆盖在驱动芯片上,用于分隔相邻的像素驱动电极。
7.作为本发明的进一步改进,所述类抛物镜为制作在绝缘层和驱动电极上的类抛物面的台面,类抛物镜在所述绝缘层的一侧为非金属绝缘材料层,非金属绝缘材料层在抛物面底部与驱动电极接触处设有开口,使驱动电极外露,所述非金属绝缘材料层上设有高反光金属层,所述高反光金属层在抛物面底部与所述驱动电极电连接。
8.作为本发明的进一步改进,所述发光二极管包括n型电极和沿发光方向依次设置
的p型电极、p型半导体层、发光层、n型半导体层、缓冲层以及衬底,所述n型电极设于发光二极管的周边,n型电极的一侧与所述n型半导体层电连接,n型电极的另一侧与所述驱动背板的像素公共电极电连接,所述p型电极的一侧与p型半导体层电连接,p型电极的另一侧与所述类抛物镜的高反光金属层在驱动电极处电连接。
9.作为本发明的进一步改进,所述n型半导体层朝向所述发光层一侧的中部设有台阶,使发光层位于所述类抛物镜的焦平面位置。
10.作为本发明的进一步改进,所述驱动背板为硅基cmos驱动背板。
11.本发明还公开了一种发光准直的microled显示器件的制备方法,包括以下步骤:
12.步骤1、制备驱动芯片,然后在驱动芯片的周边制作像素公共电极,在所述像素公共电极之间制作至少一个像素驱动电极,再在像素驱动电极的周边制作绝缘层;
13.步骤2、先后沉积绝缘材料层和涂覆光刻胶;
14.步骤3、用图案开口与像素电极一一对应的掩模板覆盖在光刻胶之上,并对光刻胶曝光、显影;
15.步骤4、显影后对绝缘材料层进行各向同性刻蚀,掩模板遮挡部分被保留下来形成像素隔离柱,曝光部分被刻蚀后形成类抛物面,控制刻蚀深度,使类抛物面底部露出像素公共电极和像素驱动电极;
16.步骤5、沉积高反光金属膜,高反光金属膜覆盖在像素隔离柱及像素公共电极和像素驱动电极上,并与像素公共电极和像素驱动电极电连接;
17.步骤6、涂覆光刻胶并用图案开口与像素隔离柱一一对应的掩模板进行曝光;
18.步骤7、经显影、刻蚀,去除覆盖在像素隔离柱顶部的金属膜,再剥离掉类抛物面上残留的光刻胶;高反光金属膜的类抛物面为各像素的发光限定区,类抛物面底部分别与像素公共电极和像素驱动电极电连接,隔离柱用于分隔各像素并遮光防串扰;
19.步骤8、在衬底上外延制备发光二极管的各叠层,包括缓冲层、n型半导体层、发光层和p型半导体层;
20.步骤9、光刻形成发光二极管像素阵列并经过镀膜、光刻、刻蚀制作n型电极和至少一个p型电极,其中n型电极为所有像素的公共电极且布置在像素阵列的周边;
21.步骤10、将发光二极管倒置后与驱动背板键合在一起,使所述发光二极管的n型电极与驱动背板的像素公共电极电连接,至少一个p型电极经类抛物面底部的反光金属膜与至少一个像素驱动电极电连接。
22.作为本发明的进一步改进,在步骤1中,所述像素公共电极和像素驱动电极通过镀膜、光刻、刻蚀的方式制作于所述驱动芯片上,所述绝缘层通过涂布、光刻的方式制作于所述驱动芯片上。
23.作为本发明的进一步改进,步骤2中的绝缘材料层的厚度小于等于发光二极管的叠层厚度;步骤4中隔离柱的高度小于等于发光二极管的叠层厚度。
24.作为本发明的进一步改进,在步骤9中,对所述n型半导体层进行台阶化刻蚀,以使发光二极管的叠层厚度大于等于所述隔离柱的高度,且发光层的中心高度满足发光层在类抛物面的焦平面位置。
25.本发明的有益效果是:
26.本发明不但可以减小像素发光角度,使microled像素沿与发光面垂直的方向以近
乎0度准直发光,有利于提高microled显示器件与光学成像器件之间的光耦合效率,而且可以提高microled出光效率,从而显著提高图像亮度,降低功耗。本发明为microled行业关键共性技术问题提供了很好的技术解决方案,故具有很高的技术价值和很强的实用性。
附图说明
27.图1为本发明实施例中microled显示器件的结构示意图;
28.图2为本发明实施例中microled显示器件制备过程中各个阶段的结构示意图。
具体实施方式
29.下面结合附图对本发明的实施例进行详细说明。
30.实施例
31.本发明microled显示器件的像素结构的实施例如图1所示,包括驱动背板和发光二极管。所述驱动背板包括驱动芯片a1、绝缘层a2、像素公共电极a3、像素驱动电极a4、类抛物镜e1;所述发光二极管包括衬底h1、缓冲层h2、n型半导体层h3、发光层h4、p型半导体层h5、n型电极i1、p型电极i2。
32.所述驱动背板可以为硅基cmos驱动背板,其中的驱动芯片a1包含驱动电路(图1中未画出驱动芯片内的驱动晶体管等电路);所述像素驱动电极a4与驱动芯片a1内的驱动晶体管的输出电极相连,所述像素公共电极a3布置在驱动芯片a1的周边,与驱动芯片a1的地电极相连,绝缘层a2覆盖在驱动芯片a1上,用于将各像素的驱动电极彼此分隔开来;所述类抛物镜e1是本发明区别于现有技术新增的功能层,类抛物镜e1为制作在绝缘层a2和驱动电极a4上的类抛物面的台面,由多层材料叠层构成,其中在绝缘层a2侧为非金属绝缘材料层,该层在抛物面底部与驱动电极a4接触处有开口,使驱动电极a4外露,非金属绝缘材料层之上为高反光金属层,该层在抛物面底部与驱动电极a4电连接。
33.所述发光二极管外延叠层的n型电极i1布置在发光二极管阵列的周边,且与n型半导体层h3电连接;所述p型电极i2与p型半导体层h5电连接。发光二极管倒置后与驱动背板键合在一起,所述发光二极管的n型电极i1与驱动背板的公共电极a3电连接。本实施例所述发光二极管的p型电极i2与类抛物镜e1的反光金属层在驱动电极a4位置电连接,且发光二极管的发光层h4在类抛物镜e1的接近焦平面位置,发光层h4发出的光经类抛物镜e1反射汇集,经衬底h1沿与发光面垂直的方向以近乎0度准直发出。特别地,选择合适的发光层h4区域的n型半导体层h3的台阶高度,使发光层h4处于越接近类抛物镜e1的焦平面位置,可以使像素发光角度越小,越接近平行光准直发出。同时,类抛物镜e1可以将发光层h4向侧面和底面等方向发射的光也反射出去,提高了发光二极管的出光效率。
34.本实施例的microled显示器件的制备方法包括以下步骤,如图2所示。为更清楚地理解各步骤形成的图案,本实施例以三个相邻像素为例:
35.第一步,完成驱动芯片a1的制备后,先在驱动芯片a1上经镀膜、光刻、刻蚀制作像素公共电极a3和第一像素驱动电极a41、第二像素驱动电极a42、第三像素驱动电极a43,其中像素公共电极a3布置在驱动背板的周边;再经涂布、光刻制作绝缘层a2。其中像素公共电极和像素驱动电极可以为包括镍(ni)、铬(cr)、钛(ti)、铝(al)、银(ag)、金(au)中的任一种金属或它们的合金,绝缘层可以为包括氧化硅(siox)、氮化硅(sixnx)、氮氧化硅(sioxny)、
氧化铝(al2o3)中的一种或多种。该步骤形成如图2中的(a)所示图案。
36.第二步,如图2中的(b)所示,先后沉积绝缘材料层b1和涂覆光刻胶b2,绝缘材料层b1的厚度h1可以为1~10um,实施例为4um,应等于或略小于图2中的(i)中发光二极管的叠层厚度h2。
37.第三步,如图2中的(c)所示,用图案开口与像素电极一一对应的掩模板c1覆盖在光刻胶b2之上,并对光刻胶b2曝光、显影。掩模板c1的开口尺寸取决于像素发光面的大小,实施例的掩模板开口尺寸为6x6um。
38.第四步,显影后对绝缘材料层b1进行各向同性刻蚀。掩模板遮挡部分被保留下来形成像素隔离柱d1,隔离柱d1的高度即绝缘材料层b1的厚度h1,隔离柱d1的顶部宽度d可以为0.1~4um,实施例为1um;曝光部分被刻蚀后形成类抛物面,控制刻蚀深度,使类抛物面底部露出像素公共电极a3和像素驱动电极a41、像素驱动电极a42、像素驱动电极a43。刻蚀后形成的图案如图2中的(d)所示。
39.第五步,如图2中的(e)所示,沉积高反光金属膜e1,可以为包括镍(ni)、铬(cr)、铝(al)、银(ag)中的任一种金属或它们的合金。金属膜e1覆盖在像素隔离柱及像素公共电极和像素驱动电极上,并与像素公共电极和像素驱动电极电连接。
40.第六步,如图2中的(f)所示,涂覆光刻胶f1并用图案开口与像素隔离柱一一对应的掩模板f2进行曝光。
41.第七步,经显影、刻蚀,去除覆盖在像素隔离柱顶部的金属膜,再剥离掉类抛物面上残留的光刻胶,形成如图2中的(g)所示的图案。高反光的类抛物面e11、类抛物面e12、类抛物面e13分别为各像素的发光限定区,类抛物面底部分别与像素公共电极和像素驱动电极电连接,隔离柱d1用于分隔各像素并有遮光防串扰的作用。
42.第八步,如图2中的(h)所示,在蓝宝石等衬底h1上外延制备发光二极管各叠层,包括缓冲层h2、n型半导体层h3、发光层h4、p型半导体层h5,叠层厚度应满足第九步中厚度h2和h3的要求。
43.第九步,如图2中的(i)所示,光刻形成发光二极管像素阵列并经过镀膜、光刻、刻蚀制作n型电极i1和第一像素p型电极i21、第二像素p型电极i22、第三像素p型电极i23,其中n型电极i1通过n型半导体层h3将所有发光二极管像素的负电极相连且布置在像素阵列的周边。n型电极和p型电极可以为包括镍(ni)、铬(cr)、钛(ti)、铝(al)、银(ag)、金(au)中的任一种金属或它们的合金,p型电极厚度可以为1~10um,实施例为1.8um,n型电极厚度等于发光二极管的叠层厚度h2,实施例为4um。
44.特别地,所述n型半导体层h3可以进行台阶化刻蚀,以使发光层h4的中心高度h3满足发光层在类抛物面的接近焦平面位置,且叠层厚度h2等于或略大于图2的(d)中隔离柱d1的高度h1。发光层h4的中心高度h3可以为0.1~4um,实施例1.8um。
45.第十步,如图2中的(j)所示,将发光二极管倒置后与驱动背板键合在一起,使所述发光二极管的n型电极i1与驱动背板的像素公共电极a3电连接,第一像素p型电极i21经类抛物面底部的反光金属膜与第一像素驱动电极a41电连接,第二像素p型电极i22经类抛物面底部的反光金属膜与第二像素驱动电极a42电连接,第三像素p型电极i23经类抛物面底部的反光金属膜与第三像素驱动电极a43电连接。
46.特别地,对microled微显示屏,所述发光二极管的衬底h1可以直接用作微显示屏
的保护盖板而不需衬底剥离步骤;此外,对单色microled微显示屏,硅基cmos驱动背板可以与上述像素阵列化的发光二极管外延片直接进行晶圆级的键合,不需巨量转移步骤。
47.以上所述实施例仅表达了本发明的具体实施方式,其描述较为具体和详细,但并不能因此而理解为对本发明专利范围的限制。应当指出的是,对于本领域的普通技术人员来说,在不脱离本发明构思的前提下,还可以做出若干变形和改进,这些都属于本发明的保护范围。