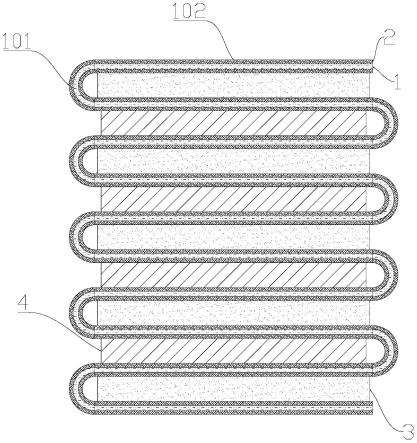
1.本发明涉及锂离子电池领域,尤其是涉及一种电芯叠片结构、制备方法及电化学装置。
背景技术:2.锂离子电池的基本单元为正极/隔膜/负极结构,将上述基本单元进行堆叠或卷绕组成了锂离子电池的电芯,再将电芯、电解液、极耳以及电池外壳组装后就形成了锂离子电池;现有技术中的锂离子电池电芯工艺基本包括卷绕工艺、堆叠工艺以及层压工艺。
3.卷绕工艺对极片的涂布制备工艺需求高,所使用的极片需有一定的弹性和可弯折性,避免卷绕时活性材料脱落或断裂,同时卷绕制成的电芯存在正面与侧面张力不一致的情况,其内部电化学反应不均匀;堆叠工艺,采用的是z字型叠片,隔膜和极片之间不做粘结处理,靠机械手抓取极片对应叠在隔膜带上,其生产效率较低,在加工尺寸较长的电池中隔膜与极片之间的界面易发生褶皱等不良;层压工艺是针对堆叠工艺的缺陷进行的改进,可显著提高生产效率,但层压式工艺采用的是先将第一极片插设在隔膜中,再将第二极片粘结在相邻的两个第一极片外侧的隔膜之间,工艺操作繁琐,生产效率低,且成本高。
4.如公开号cn113611912b,公开了一种电极组件的叠片结构,包括叠层布置的若干叠片单元,叠片单元包括由隔膜形成的隔膜扁腔、设于隔膜扁腔内的第一极片和设于隔膜扁腔外的第二极片;隔膜扁腔的一侧向上延伸形成连接上方相邻叠片单元隔膜扁腔的对应同侧的连接膜,隔膜扁腔的另一侧与上方相邻叠片单元隔膜通腔的对应同侧相断开,能有效避免或降低第一极片和第二极片在电池震动时出现的错位,但上述结构存在制备工艺繁琐,成本高的问题。
技术实现要素:5.为了克服现有技术中的层压堆叠型电芯结构的结构复杂,制备工艺繁琐,成本高问题,提供了一种电芯叠片结构、制备方法及电化学装置,本技术提供的电芯叠片结构通过胶层将负极片和正极片交替粘结在相邻的粘结隔膜间隙中,具备结构简单、牢固性高、安全性高的技术效果;本技术提供的电芯叠片结构制备方法具备操作简单、成本低、生产效率高的技术效果。
6.本发明的具体技术方案为:一种电芯叠片结构,包括堆叠设置的隔膜、设在隔膜两侧的胶层、设在隔膜堆叠间隙中与胶层连接的负极片以及设在相邻隔膜堆叠间隙中与胶层连接的正极片,所述隔膜包括层叠设置的粘结隔膜和设置在相邻粘结隔膜间的间隙隔膜。
7.本技术提供的电芯叠片结构将负极片和正极片交替粘结在粘结隔膜上,再通过弯折间隙隔膜对使粘结隔膜上的负极片和正极片进行交替堆叠,再通过胶层将负极片和正极片粘结在相邻两层粘结隔膜形成的间隙中,通过胶层将负极片和正极片固定在隔膜上不会出现错位,牢固性更强,同时电芯叠片结构在受到外力挤压时,由于胶层将电极片和隔膜隔
离,电极片对隔膜的破坏性显著降低,安全性高。
8.作为优选,所述间隙隔膜长度为1~5μm。
9.作为优选,所述胶层厚度为0.01~0.05mm。
10.作为优选,所述涂胶隔膜的基膜为聚乙烯、聚丙烯、聚乙烯和聚丙烯组合的复合单层膜,基膜厚度6~20μm。
11.作为优选,所述胶层包括质量份数比为20~50:50~80的热熔胶和无机粒子,所述热熔胶选自聚偏氟乙烯、聚甲基丙烯酸甲酯、聚对苯二甲酰苯二胺和聚间苯二甲酰苯二胺中的任一一种或几种,所述无机粒子选自氧化铝陶瓷、勃姆石、氧化镁陶瓷和氧化硅中的任一一种或几种;本技术中胶层为绝缘性胶层,胶层中添加了绝缘性无机粒子,可以提高隔膜的阻隔性能,本技术的胶层在粘结过程中,无机粒子在极片和粘结隔膜的中间形成一层间隔带,防止极片与隔膜在热熔胶融化后贴合在一起,上述结构可以使电芯结构在受到外部压力时,防止正极片和负极片在受到挤压时穿透隔膜造成短路,显著提高了电芯的安全性。
12.一种电芯叠片结构的制备方法,包括以下制备步骤:(1)按照20%~100%的覆盖比例将胶层涂覆在隔膜上,按一定宽度裁切隔膜、正极片和负极片;(2)将裁切完成的负极片预热并辊压至粘结隔膜侧面上形成第一复合体,间隔间隙隔膜将裁切完成的正极片预热并辊压至与第一复合体相邻的粘结隔膜另一侧面上形成第二复合体,按照隔膜延伸方向使第一复合体和第二复合体交替排列;(3)弯折间隙隔膜,依次将未贴合粘结隔膜的负极层一面与相邻的正极层的粘结隔膜侧面贴合,将未贴合的正极层一面与相邻的负极层的粘结隔膜侧面贴合,负极层和正极层交替堆叠设置,设置完成后进行热压制成电芯叠片结构;(4)将胶带粘贴在电芯叠片结构外侧制成裸电芯。
13.本技术提供的制备方法将负极片预热并辊压至粘结隔膜侧面上形成第一复合体,再将间隙隔膜作为间隔段,再将正极片预热并辊压至与负极层相邻的粘结隔膜另一侧面上形成第二复合体;沿隔膜延伸方向使第一复合体和第二复合体交替排列,在通过弯折间隙隔膜,将未贴合粘结隔膜的负极层一面与相邻的正极层的粘结隔膜侧面贴合,再将未贴合的正极层一面与相邻的负极层的粘结隔膜侧面贴合,使负极层始终排布在正极层的外侧,设置完成后进行热压,热压过程中,胶层将负极片和正极片与其两侧的粘结隔膜粘合在一起制成电芯叠片结构,上述过程中无需对隔膜进行加工,只需通过涂胶
→
裁片
→
交替压片
→
层压堆叠即可制成电芯叠片结构,上述制备过程可连续进行,制备操作简单且生产效率显著提高,同时生产成本显著降低。
14.作为优选,所述步骤(1)中的胶层涂覆厚度为1~5μm。
15.作为优选,所述步骤(2)中预热温度为30-90℃,辊压压力为0.1-2.0mpa。
16.作为优选,所述步骤(3)中热压温度为30-120℃,热压压力为20-5000kg,热压时间为2s-600s。
17.一种电化学装置,包括上述的叠片结构,或采用上述的叠片结构的制备方法制备得到。
18.与现有技术相比,本技术具有以下技术效果:(1)本技术提供的本技术提供的电芯叠片结构通过胶层将负极片和正极片交替粘
结在相邻的粘结隔膜间隙中,具备结构简单、牢固性高、安全性高的技术效果;(2)本技术提供的电芯叠片结构制备方法具备操作简单、成本低、生产效率高的技术效果。
附图说明
19.图1是本发明的结构示意图。
20.图2是本发明的制备工艺示意图。
21.图中,隔膜1、粘结隔膜101、间隙隔膜102、胶层2、负极片3、正极片4、第一复合体5和第二复合体6。
具体实施方式
22.下面结合实施例对本发明作进一步的描述。
23.如无特别说明,本发明中所采用的原料均可从市场上购得或是本领域常用的,如无特别说明,下述实施例中的方法均为本领域的常规方法实施例1:如图1所示,一种电芯叠片结构,包括堆叠设置的隔膜1、设在隔膜两侧的胶层2、设在隔膜堆叠间隙中与胶层连接的负极片3以及设在相邻隔膜堆叠间隙中与胶层连接的正极片4,负极片包括负极集流体和设在负极集流体两侧的负极浆料,正极片包括正极集流体和设在正极集流体两侧的正极浆料;负极片共有5个,正极片共4个,电芯叠片结构从电芯的尾端开始延伸至头端结束,依次由负极片、正极片、负极片的顺序进行排列,电芯叠片结构的两侧都为负极片,隔膜基膜为10μm厚的聚乙烯膜,单侧胶层的厚度为2μm,胶的材质为聚偏氟乙烯,陶瓷为勃姆石,二者质量分数比为3:7,胶层在基膜上的覆盖面积达到80%;隔膜包括层叠设置的粘结隔膜102和设置在相邻粘结隔膜间的间隙隔膜101,间隙隔膜长度为2mm,间隙隔膜呈弯曲状,堆叠后热压条件为:热压压力在500kg,热压温度在85℃,热压时间60s,在裸电芯四周贴胶固定并向下流转。
24.实施例2:如图2所示,一种电芯结构的制备方法,包括以下步骤:(1)按照50%的覆盖比例将胶层涂覆在隔膜上,隔膜的基膜为厚度12μm的聚丙烯膜,单侧涂覆厚度为4μm,热熔胶的材质为聚甲基丙烯酸甲酯,无机粒子为氧化铝,热熔胶和陶瓷的质量份数比为4:6,按一定宽度裁切隔膜、正极片和负极片,隔膜幅宽200mm,正极片的裁切宽度为193*95mm,负极片的裁切宽度为196*98mm;(2)将裁切完成的负极片预热并辊压至粘结隔膜侧面上形成第一复合体5,间隔间隙隔膜将裁切完成的正极片预热并辊压至与第一复合体相邻的粘结隔膜另一侧面上形成第二复合体6,按照隔膜延伸方向使第一复合体和第二复合体交替排列;预热温度为50℃,辊压压力为0.5mpa,间隙隔膜宽度3mm;(3)弯折间隙隔膜,依次将未贴合粘结隔膜的负极层一面与相邻的第一复合体的粘结隔膜侧面贴合,将未贴合的第二复合体一面与相邻的第一复合体的粘结隔膜侧面贴合,第一复合体和第二复合体交替堆叠设置,设置完成后进行热压制成电芯叠片结构,热压条件为,热压压力1000kg,热压温度95℃,热压时间120s;
(4)将胶带粘贴在电芯叠片结构外侧制成裸电芯并向下流转。
25.以上所述,仅是本发明的较佳实施例,并非对本发明作任何限制,凡是根据本发明技术实质对以上实施例所作的任何简单修改、变更以及等效变换,均仍属于本发明技术方案的保护范围。