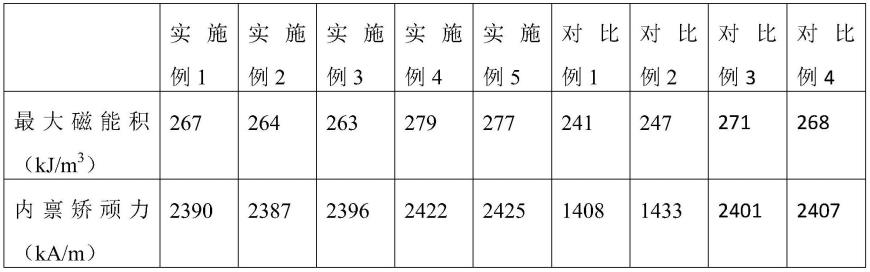
1.本发明属于磁性材料制备技术领域,更具体地说,本发明涉及一种高磁能积稀土钴永磁材料的制备方法。
背景技术:2.稀土钴永磁材料是指由稀土元素(如:钐(sum)、镨(pr)、钆(gd)、铒(er)、铈(ce)等)与钴元素及过渡金属元素合成的合金材料
3.稀土钴永磁材料的温度系数不到钕铁硼永磁材料的三分之一,相对于钕铁硼永磁材料具有更高的最高工作温度、更小的温度系数、而且耐腐蚀等优点。因此在高可靠军民用微波功率器件(环形器/隔离器)中占据着不可替代的地位。随着我国军用微波功率器件(环形器/隔离器)向高功率、小型化、高可靠等方向发展,对稀土永磁材料的磁性能、稳定性和一致性提出更高的要求,现阶段无法完全满足,急需开展高性能稀土钴永磁材料的研究及制备。随着我国5g的快速发展,对5g通信用微波功率器件(环形器/隔离器)也提出高性能、大批量和高一致性要求,减少5g通信用环形器/隔离器的重复调试难题,提高批量生产水平。
4.永磁材料的磁能积是指退磁曲线上任何点的b(磁感应强度)和h(磁化场强度)的乘积,单位为goe或kj/m3,磁能积是衡量磁体所储存能量大小的重要参数之一,而b
×
h的最大值称之为最高磁能积,为退磁曲线上的d点,最高磁能积(bh)max代表了磁体两磁极空间所建立的磁能量密度,即气隙单位体积的静磁。相同尺寸、相同极数和相同的充磁电压条件下的两个磁体,磁能积高的磁件所获得的表磁也高。分子式为pr2co
17
的稀土钴永磁材料相对于sm2co
17
具有更高的饱和磁化强度,通过稀土金属pr替代稀土金属sm理论上可以较大幅度的提高材料的剩磁和最高磁能积,稀土金属pr含量的增加可以提高材料的饱和磁化强度ms,但会带来内禀矫顽力的下降和更苛刻的工艺条件。因而,目前需要拟通过配方优化、晶粒细化(干法低氧工艺)、烧结热处理工艺优化,从而提高稀土钴永磁材料的内禀矫顽力,而获得高最高磁能积。
技术实现要素:5.本发明的一个目的是解决至少上述问题和/或缺陷,并提供至少后面将说明的优点。
6.为了实现根据本发明的这些目的和其它优点,提供了一种高磁能积稀土钴永磁材料的制备方法,其由pr、co、fe、cu、zr的粉末通过熔化铸锭、粉碎、取向、烧结和热处理制备得到。
7.优选的是,其中,包括以下步骤:
8.步骤一、按照化学表达式pr(co
1-u-v-w-y
feucuvzr
wry
)z设定pr、co、fe、cu、zr、r的使用比例分别称量pr、co、fe、cu、zr、r的粉末,0.15≤u≤0.30,0.02≤v≤0.04,0.03≤w≤0.05,0.14≤z≤0.22;
9.步骤二、使用电磁感应法对pr、co、fe、cu、zr、r的粉末进行加热熔化,混合得到熔液,将熔液浇入水冷铜模进行冷却形成铸锭;
10.步骤三、采用干法球磨工艺将将铸锭粉碎为粉末;
11.步骤四、使粉末在平行磁场中进行取向,同时使用液压机将粉末压制成型,得到生坯,再使用等静压机对生坯进行二次成型等静压,得到坯体;
12.步骤五、对二次成型静压的坯体进行烧结;
13.步骤六、对烧结后的材料进行热处理,得到高磁能积稀土永磁材料。
14.优选的是,其中,所述步骤一中,r为ni或nd中的一种,或是ni和nd摩尔比1比1的合金,且0≤y≤0.05。
15.优选的是,其中,所述步骤二中,加热熔化的步骤包括:
16.步骤s21、将pr、co、fe、cu、zr、r的粉末装入熔炼炉中的熔炼坩埚中,其中co粉末应放于容易浸入熔液的位置;
17.步骤s22、对熔炼炉抽真空,真空度达到15mpa以下,然后充入氩气,压力为﹣0.03mpa~-0.05mpa;
18.步骤s23、加大电磁感应的功率,对各粉末进行加热熔化,当原材料全部熔化后,保持功率使熔液在沸腾状态下保持3~5min,电磁感应的熔炼功率为3600~7500kw;
19.步骤s24、将熔液浇入水冷铜模进行冷却形成铸锭,当铸锭温度低于不对造成高温伤人后,向熔炼炉充入氩气,开启熔炼炉门取出铸锭,其中合金铸锭的氧含量<400ppm,合金熔炼的熔损<3%。
20.优选的是,其中,所述步骤三中,使用干法球磨工艺将铸锭粉碎的粉末平均粒径为4.0~8.0μm,粉碎后的粉末氧含量≤2000ppm,球磨时间为2~12h。
21.优选的是,其中,所述步骤四中,使用的取向磁场的磁感应强度≥0.6t,液压机将粉末压制成型的压力≥10mpa,二次成型等静压力为100mpa~250mpa。
22.优选的是,其中,所述步骤五中,使用烧结炉采用真空或氩气保护的方式进行烧结,烧结的温度为1160~1240℃,烧结时间0.5~3h,烧结后进行固溶,固溶温度比烧结温度低20~60℃,固溶时间大于等于烧结时间,固溶后得到的材料密度≥8.2g/cm3,材料氧含量≤3000ppm。
23.优选的是,其中,所述步骤六中,使用热处理炉采用氩气保护的方式进行热处理,热处理温度为750~900℃,热处理温度保温4~24h,然后从热处理温度冷却到400℃,冷却速率小于2℃/min。
24.优选的是,其中,所述r为ni和nd按照摩尔比1比1的合金,其制备方法包括:按照ni和nd摩尔比1比1的比例,分别称量ni粉末和nd粉末,混合后得到前驱体混合物,在1500~1600℃温度下熔炼混合,冷却后粉碎为平均粒径为8~12μm的合金粉末;向粉碎后的合金粉末中加入沉淀剂,并从小到大依次加入五种梯度体积浓度的醇溶液,搅拌后获得钕镍沉淀物料;对钕镍沉淀物料进行真空干燥,真空干燥温度为110~150℃,干燥时间为4~7h,对真空干燥后的钕镍沉淀物料进行二次真空烧结,真空烧结温度为800~1120℃,烧结时间为2~3h,冷却后得到r。
25.优选的是,其中,所述沉淀剂的为尿素或甲酰胺,沉淀剂的质量与前驱体混合物的总质量的质量比为1:15~20;
26.所述醇溶液为乙醇或乙二醇,醇溶液的五种梯度体积浓度分别为85%、70%、55%、40%和25%,每次加入的醇溶液体积与真空烧结后的产物的体积质量比为70~200ml:10g。
27.本发明至少包括以下有益效果:本发明使用pr取代稀土金属sm,并通过配方优化和加工工艺参数的优化,制备得到了具有高磁能积和高内禀矫顽力的稀土钴永磁材料。本发明通过对pr、co、fe、cu、zr、r晶粒的细化,明显降低了烧结温度,有利于稀土钴永磁材料内部结构的形成,提高了稀土钴永磁材料的内禀矫顽力。与湿法球磨工艺相比,干法工艺更有利于晶粒的细化和粒度分布的有效控制,同时还能降低氧含量,实现内禀矫顽力的提高。
28.本发明还对ni和nd进行预先处理,先对ni粉末和nd粉末进行煅烧,再与沉淀剂和五种梯度的醇溶液混合、烘干,最后真空烧结得到r,采用这种方法获得了结构稳定的r,与pr、co、fe、cu、zr进行熔化后,增大了原材料的导热率,有利于后续的电磁感应熔炼,适用于更温度的熔炼和烧结要求,从而制得了更高磁能积和更高内禀矫顽力的稀土钴永磁材料。
29.本发明的其它优点、目标和特征将部分通过下面的说明体现,部分还将通过对本发明的研究和实践而为本领域的技术人员所理解。
具体实施方式
30.下面对本发明做进一步的详细说明,以令本领域技术人员参照说明书文字能够据以实施。
31.应当理解,本文所使用的诸如“具有”、“包含”以及“包括”术语并不排除一个或多个其它元件或其组合的存在或添加。
32.实施例1
33.本实施例提供了一种高磁能积稀土钴永磁材料的制备方法,包括以下步骤:
34.步骤一、按照化学表达式pr(co
0.80
fe
0.15
cu
0.02
zr
0.03
)
0.14
设定pr、co、fe、cu、zr的使用比例分别称量pr、co、fe、cu、zr的粉末;
35.步骤二、使用电磁感应法对pr、co、fe、cu、zr的粉末进行加热熔化,混合得到熔液,将熔液浇入水冷铜模进行冷却形成铸锭;其中,加热熔化的步骤包括:
36.步骤s21、将pr、co、fe、cu、zr的粉末装入熔炼炉中的熔炼坩埚中,其中co粉末应放于容易浸入熔液的位置;
37.步骤s22、对熔炼炉抽真空,真空度达到15mpa以下,然后充入氩气,压力为﹣0.03mpa;
38.步骤s23、加大电磁感应的功率,对各粉末进行加热熔化,当原材料全部熔化后,保持功率使熔液在沸腾状态下保持3min,电磁感应的熔炼功率为3800kw;
39.步骤s24、将熔液浇入水冷铜模进行冷却形成铸锭,当铸锭温度低于不对造成高温伤人后,向熔炼炉充入氩气,开启熔炼炉门取出铸锭,其中合金铸锭的氧含量200ppm,合金熔炼的熔损为1%;
40.步骤三、使用干法球磨工艺将铸锭粉碎的粉末平均粒径为4.0μm,粉碎后的粉末氧含量为1500ppm,球磨时间为4h;
41.步骤四、使粉末在平行磁场中进行取向,使用的取向磁场的磁感应强度为0.8t,同时使用液压机将粉末压制成型,液压机将粉末压制成型的压力为12mpa,得到生坯,再使用
等静压机对生坯进行二次成型等静压,二次成型等静压力为100mpa,得到坯体;
42.步骤五、对二次成型静压的坯体进行烧结,具体为使用烧结炉采用真空或氩气保护的方式进行烧结,烧结的温度为1240℃,烧结时间0.5h,烧结后进行固溶,固溶温度比烧结温度低20℃,固溶时间大于等于烧结时间,固溶后得到的材料密度8.8g/cm3,材料氧含量2500ppm;
43.步骤六、对烧结后的材料进行热处理,使用热处理炉采用氩气保护的方式进行热处理,热处理温度为750℃,热处理温度保温4h,然后从热处理温度冷却到400℃,冷却速率为1.5℃/min,得到高磁能积稀土永磁材料。
44.实施例2
45.本实施例提供了一种高磁能积稀土钴永磁材料的制备方法,包括以下步骤:
46.步骤一、按照化学表达式pr(co
0.73
fe
0.20
cu
0.03
zr
0.04
)
0.18
设定pr、co、fe、cu、zr的使用比例分别称量pr、co、fe、cu、zr的粉末;
47.步骤二、使用电磁感应法对pr、co、fe、cu、zr的粉末进行加热熔化,混合得到熔液,将熔液浇入水冷铜模进行冷却形成铸锭;其中,加热熔化的步骤包括:
48.步骤s21、将pr、co、fe、cu、zr的粉末装入熔炼炉中的熔炼坩埚中,其中co粉末应放于容易浸入熔液的位置;
49.步骤s22、对熔炼炉抽真空,真空度达到15mpa以下,然后充入氩气,压力为﹣0.04mpa;
50.步骤s23、加大电磁感应的功率,对各粉末进行加热熔化,当原材料全部熔化后,保持功率使熔液在沸腾状态下保持4min,电磁感应的熔炼功率为4500kw;
51.步骤s24、将熔液浇入水冷铜模进行冷却形成铸锭,当铸锭温度低于不对造成高温伤人后,向熔炼炉充入氩气,开启熔炼炉门取出铸锭,其中合金铸锭的氧含量200ppm,合金熔炼的熔损1.2%;
52.步骤三、使用干法球磨工艺将铸锭粉碎的粉末平均粒径为4.5μm,粉碎后的粉末氧含量1800ppm,球磨时间为6h;
53.步骤四、使粉末在平行磁场中进行取向,使用的取向磁场的磁感应强度0.8t,同时使用液压机将粉末压制成型,液压机将粉末压制成型的压力12mpa,得到生坯,再使用等静压机对生坯进行二次成型等静压,二次成型等静压力为150mpa,得到坯体;
54.步骤五、对二次成型静压的坯体进行烧结,具体为使用烧结炉采用真空或氩气保护的方式进行烧结,烧结的温度为1200℃,烧结时间2h,烧结后进行固溶,固溶温度比烧结温度低30℃,固溶时间大于等于烧结时间,固溶后得到的材料密度8.7g/cm3,材料氧含量2400ppm;
55.步骤六、对烧结后的材料进行热处理,使用热处理炉采用氩气保护的方式进行热处理,热处理温度为800℃,热处理温度保温8h,然后从热处理温度冷却到400℃,冷却速率为1℃/min,得到高磁能积稀土永磁材料。
56.实施例3
57.本实施例提供了一种高磁能积稀土钴永磁材料的制备方法,包括以下步骤:
58.步骤一、按照化学表达式pr(co
0.61
fe
0.30
cu
0.04
zr
0.05
)
0.20
设定pr、co、fe、cu、zr的使用比例分别称量pr、co、fe、cu、zr的粉末;
59.步骤二、使用电磁感应法对pr、co、fe、cu、zr的粉末进行加热熔化,混合得到熔液,将熔液浇入水冷铜模进行冷却形成铸锭;其中,加热熔化的步骤包括:
60.步骤s21、将pr、co、fe、cu、zr的粉末装入熔炼炉中的熔炼坩埚中,其中co粉末应放于容易浸入熔液的位置;
61.步骤s22、对熔炼炉抽真空,真空度达到15mpa以下,然后充入氩气,压力为-0.05mpa;
62.步骤s23、加大电磁感应的功率,对各粉末进行加热熔化,当原材料全部熔化后,保持功率使熔液在沸腾状态下保持5min,电磁感应的熔炼功率为6000kw;
63.步骤s24、将熔液浇入水冷铜模进行冷却形成铸锭,当铸锭温度低于不对造成高温伤人后,向熔炼炉充入氩气,开启熔炼炉门取出铸锭,其中合金铸锭的氧含量150ppm,合金熔炼的熔损2%;
64.步骤三、使用干法球磨工艺将铸锭粉碎的粉末平均粒径为4.6μm,粉碎后的粉末氧含量1600ppm,球磨时间为8h;
65.步骤四、使粉末在平行磁场中进行取向,使用的取向磁场的磁感应强度0.8t,同时使用液压机将粉末压制成型,液压机将粉末压制成型的压力12mpa,得到生坯,再使用等静压机对生坯进行二次成型等静压,二次成型等静压力为250mpa,得到坯体;
66.步骤五、对二次成型静压的坯体进行烧结,具体为使用烧结炉采用真空或氩气保护的方式进行烧结,烧结的温度为1160℃,烧结时间2h,烧结后进行固溶,固溶温度比烧结温度低40℃,固溶时间大于等于烧结时间,固溶后得到的材料密度8.9g/cm3,材料氧含量2200ppm;
67.步骤六、对烧结后的材料进行热处理,使用热处理炉采用氩气保护的方式进行热处理,热处理温度为900℃,热处理温度保温8h,然后从热处理温度冷却到400℃,冷却速率1℃/min,得到高磁能积稀土永磁材料。
68.实施例4
69.本实施例提供了一种高磁能积稀土钴永磁材料的制备方法,包括以下步骤:
70.步骤一、按照化学表达式pr[co
0.8
fe
0.15
cu
0.02
zr
0.03
(nind)
0.02
]
0.14
设定pr、co、fe、cu、zr、ni、nd的使用比例分别称量pr、co、fe、cu、zr粉末和ni、nd的混合粉末;其中ni、nd混合粉末由以下方法制备得到:
[0071]
按照ni和nd摩尔比1比1的比例,分别称量59g ni粉末和144g nd粉末,混合后得到前驱体混合物,在1600℃温度下熔炼混合,冷却后粉碎为平均粒径为8μm的合金粉末;向合金粉末中加入20.4g尿素,并从小到大依次加入85%、70%、55%、40%和25%五种梯度体积浓度的乙醇溶液,每次加入的醇溶液体积与真空烧结后的产物的体积质量比为100ml:10g,搅拌后获得钕镍沉淀物料;对钕镍沉淀物料进行真空干燥,真空干燥温度为120℃,干燥时间为5h,对真空干燥后的钕镍沉淀物料进行二次真空烧结,真空烧结温度为850℃,烧结时间为2h,冷却后得到ni和nd的混合粉末。
[0072]
步骤二、使用电磁感应法对pr、co、fe、cu、zr的粉末和ni、nd的混合粉末进行加热熔化,混合得到熔液,将熔液浇入水冷铜模进行冷却形成铸锭;其中,加热熔化的步骤包括:
[0073]
步骤s21、将pr、co、fe、cu、zr的粉末和ni、nd的混合粉末装入熔炼炉中的熔炼坩埚中,其中co粉末应放于容易浸入熔液的位置;
[0074]
步骤s22、对熔炼炉抽真空,真空度达到15mpa以下,然后充入氩气,压力为﹣0.03mpa;
[0075]
步骤s23、加大电磁感应的功率,对各粉末进行加热熔化,当原材料全部熔化后,保持功率使熔液在沸腾状态下保持3min,电磁感应的熔炼功率为3800kw;
[0076]
步骤s24、将熔液浇入水冷铜模进行冷却形成铸锭,当铸锭温度低于不对造成高温伤人后,向熔炼炉充入氩气,开启熔炼炉门取出铸锭,其中合金铸锭的氧含量180ppm,合金熔炼的熔损为0.8%;
[0077]
步骤三、使用干法球磨工艺将铸锭粉碎的粉末平均粒径为4.0μm,粉碎后的粉末氧含量为1500ppm,球磨时间为4h;
[0078]
步骤四、使粉末在平行磁场中进行取向,使用的取向磁场的磁感应强度为0.8t,同时使用液压机将粉末压制成型,液压机将粉末压制成型的压力为12mpa,得到生坯,再使用等静压机对生坯进行二次成型等静压,二次成型等静压力为100mpa,得到坯体;
[0079]
步骤五、对二次成型静压的坯体进行烧结,具体为使用烧结炉采用真空或氩气保护的方式进行烧结,烧结的温度为1160℃,烧结时间0.5h,烧结后进行固溶,固溶温度比烧结温度低20℃,固溶时间大于等于烧结时间,固溶后得到的材料密度8.9g/cm3,材料氧含量2100ppm;
[0080]
步骤六、对烧结后的材料进行热处理,使用热处理炉采用氩气保护的方式进行热处理,热处理温度为750℃,热处理温度保温4h,然后从热处理温度冷却到400℃,冷却速率为1.5℃/min,得到高磁能积稀土永磁材料。
[0081]
实施例5
[0082]
本实施例提供了一种高磁能积稀土钴永磁材料的制备方法,包括以下步骤:
[0083]
步骤一、按照化学表达式pr[co
0.73
fe
0.20
cu
0.03
zr
0.04
(nind)
0.05
]
0.18
设定pr、co、fe、cu、zr、ni、nd的使用比例分别称量pr、co、fe、cu、zr粉末和ni、nd的混合粉末;其中ni、nd混合粉末由以下方法制备得到:
[0084]
按照ni和nd摩尔比1比1的比例,分别称量59g ni粉末和144g nd粉末,混合后得到前驱体混合物,在1600℃温度下熔炼混合,冷却后粉碎为平均粒径为8μm的合金粉末;向合金粉末中加入20.4g尿素,并从小到大依次加入85%、70%、55%、40%和25%五种梯度体积浓度的乙醇溶液,每次加入的醇溶液体积与真空烧结后的产物的体积质量比为150ml:10g,搅拌后获得钕镍沉淀物料;对钕镍沉淀物料进行真空干燥,真空干燥温度为120℃,干燥时间为5h,对真空干燥后的钕镍沉淀物料进行二次真空烧结,真空烧结温度为1000℃,烧结时间为2h,冷却后得到ni和nd的混合粉末。
[0085]
步骤二、使用电磁感应法对pr、co、fe、cu、zr的粉末和ni、nd的混合粉末进行加热熔化,混合得到熔液,将熔液浇入水冷铜模进行冷却形成铸锭;其中,加热熔化的步骤包括:
[0086]
步骤s21、将pr、co、fe、cu、zr的粉末和ni、nd的混合粉末装入熔炼炉中的熔炼坩埚中,其中co粉末应放于容易浸入熔液的位置;
[0087]
步骤s22、对熔炼炉抽真空,真空度达到15mpa以下,然后充入氩气,压力为﹣0.04mpa;
[0088]
步骤s23、加大电磁感应的功率,对各粉末进行加热熔化,当原材料全部熔化后,保持功率使熔液在沸腾状态下保持4min,电磁感应的熔炼功率为4500kw;
[0089]
步骤s24、将熔液浇入水冷铜模进行冷却形成铸锭,当铸锭温度低于不对造成高温伤人后,向熔炼炉充入氩气,开启熔炼炉门取出铸锭,其中合金铸锭的氧含量170ppm,合金熔炼的熔损1.1%;
[0090]
步骤三、使用干法球磨工艺将铸锭粉碎的粉末平均粒径为4.8μm,粉碎后的粉末氧含量1500ppm,球磨时间为6h;
[0091]
步骤四、使粉末在平行磁场中进行取向,使用的取向磁场的磁感应强度0.8t,同时使用液压机将粉末压制成型,液压机将粉末压制成型的压力12mpa,得到生坯,再使用等静压机对生坯进行二次成型等静压,二次成型等静压力为150mpa,得到坯体;
[0092]
步骤五、对二次成型静压的坯体进行烧结,具体为使用烧结炉采用真空或氩气保护的方式进行烧结,烧结的温度为1200℃,烧结时间2h,烧结后进行固溶,固溶温度比烧结温度低30℃,固溶时间大于等于烧结时间,固溶后得到的材料密度8.9g/cm3,材料氧含量2000ppm;
[0093]
步骤六、对烧结后的材料进行热处理,使用热处理炉采用氩气保护的方式进行热处理,热处理温度为800℃,热处理温度保温8h,然后从热处理温度冷却到400℃,冷却速率为1℃/min,得到高磁能积稀土永磁材料。
[0094]
对比例1
[0095]
本对比例提供了一种高磁能积稀土钴永磁材料的制备方法,包括以下步骤:
[0096]
步骤一、按照化学表达式sm(co
0.80
fe
0.15
cu
0.02
zr
0.03
)
0.14
设定sm、co、fe、cu、zr的使用比例分别称量sm、co、fe、cu、zr的粉末;
[0097]
步骤二、使用电磁感应法对sm、co、fe、cu、zr的粉末进行加热熔化,混合得到熔液,将熔液浇入水冷铜模进行冷却形成铸锭;其中,加热熔化的步骤包括:
[0098]
步骤s21、将sm、co、fe、cu、zr的粉末装入熔炼炉中的熔炼坩埚中,其中co粉末应放于容易浸入熔液的位置;
[0099]
步骤s22、对熔炼炉抽真空,真空度达到15mpa以下,然后充入氩气,压力为﹣0.03mpa;
[0100]
步骤s23、加大电磁感应的功率,对各粉末进行加热熔化,当原材料全部熔化后,保持功率使熔液在沸腾状态下保持3min,电磁感应的熔炼功率为3800kw;
[0101]
步骤s24、将熔液浇入水冷铜模进行冷却形成铸锭,当铸锭温度低于不对造成高温伤人后,向熔炼炉充入氩气,开启熔炼炉门取出铸锭,其中合金铸锭的氧含量200ppm,合金熔炼的熔损为1%;
[0102]
步骤三、使用干法球磨工艺将铸锭粉碎的粉末平均粒径为4.0μm,粉碎后的粉末氧含量为1500ppm,球磨时间为4h;
[0103]
步骤四、使粉末在平行磁场中进行取向,使用的取向磁场的磁感应强度为0.8t,同时使用液压机将粉末压制成型,液压机将粉末压制成型的压力为12mpa,得到生坯,再使用等静压机对生坯进行二次成型等静压,二次成型等静压力为100mpa,得到坯体;
[0104]
步骤五、对二次成型静压的坯体进行烧结,具体为使用烧结炉采用真空或氩气保护的方式进行烧结,烧结的温度为1240℃,烧结时间0.5h,烧结后进行固溶,固溶温度比烧结温度低20℃,固溶时间大于等于烧结时间,固溶后得到的材料密度7.9g/cm3,材料氧含量2700ppm;
[0105]
步骤六、对烧结后的材料进行热处理,使用热处理炉采用氩气保护的方式进行热处理,热处理温度为750℃,热处理温度保温4h,然后从热处理温度冷却到400℃,冷却速率为1.5℃/min,得到稀土永磁材料。
[0106]
对比例2
[0107]
本对比例提供了一种高磁能积稀土钴永磁材料的制备方法,包括以下步骤:
[0108]
步骤一、按照化学表达式sm(co
0.73
fe
0.20
cu
0.03
zr
0.04
)
0.18
设定sm、co、fe、cu、zr的使用比例分别称量sm、co、fe、cu、zr的粉末;
[0109]
步骤二、使用电磁感应法对sm、co、fe、cu、zr的粉末进行加热熔化,混合得到熔液,将熔液浇入水冷铜模进行冷却形成铸锭;其中,加热熔化的步骤包括:
[0110]
步骤s21、将sm、co、fe、cu、zr的粉末装入熔炼炉中的熔炼坩埚中,其中co粉末应放于容易浸入熔液的位置;
[0111]
步骤s22、对熔炼炉抽真空,真空度达到15mpa以下,然后充入氩气,压力为﹣0.04mpa;
[0112]
步骤s23、加大电磁感应的功率,对各粉末进行加热熔化,当原材料全部熔化后,保持功率使熔液在沸腾状态下保持4min,电磁感应的熔炼功率为4500kw;
[0113]
步骤s24、将熔液浇入水冷铜模进行冷却形成铸锭,当铸锭温度低于不对造成高温伤人后,向熔炼炉充入氩气,开启熔炼炉门取出铸锭,其中合金铸锭的氧含量200ppm,合金熔炼的熔损1.2%;
[0114]
步骤三、使用干法球磨工艺将铸锭粉碎的粉末平均粒径为4.5μm,粉碎后的粉末氧含量1800ppm,球磨时间为6h;
[0115]
步骤四、使粉末在平行磁场中进行取向,使用的取向磁场的磁感应强度0.8t,同时使用液压机将粉末压制成型,液压机将粉末压制成型的压力12mpa,得到生坯,再使用等静压机对生坯进行二次成型等静压,二次成型等静压力为150mpa,得到坯体;
[0116]
步骤五、对二次成型静压的坯体进行烧结,具体为使用烧结炉采用真空或氩气保护的方式进行烧结,烧结的温度为1200℃,烧结时间2h,烧结后进行固溶,固溶温度比烧结温度低30℃,固溶时间大于等于烧结时间,固溶后得到的材料密度8.1g/cm3,材料氧含量2500ppm;
[0117]
步骤六、对烧结后的材料进行热处理,使用热处理炉采用氩气保护的方式进行热处理,热处理温度为800℃,热处理温度保温8h,然后从热处理温度冷却到400℃,冷却速率为1℃/min,得到稀土永磁材料。
[0118]
对比例3
[0119]
本对比例提供了一种高磁能积稀土钴永磁材料的制备方法,包括以下步骤:
[0120]
步骤一、按照化学表达式pr[co
0.8
fe
0.15
cu
0.02
zr
0.03
(nind)
0.02
]
0.14
设定pr、co、fe、cu、zr、ni、nd的使用比例分别称量pr、co、fe、cu、zr、ni、nd的粉末;
[0121]
步骤二、使用电磁感应法对pr、co、fe、cu、zr、ni和nd的粉末进行加热熔化,混合得到熔液,将熔液浇入水冷铜模进行冷却形成铸锭;其中,加热熔化的步骤包括:
[0122]
步骤s21、将pr、co、fe、cu、zr、ni和nd的粉末装入熔炼炉中的熔炼坩埚中,其中co粉末应放于容易浸入熔液的位置;
[0123]
步骤s22、对熔炼炉抽真空,真空度达到15mpa以下,然后充入氩气,压力为﹣
0.03mpa;
[0124]
步骤s23、加大电磁感应的功率,对各粉末进行加热熔化,当原材料全部熔化后,保持功率使熔液在沸腾状态下保持3min,电磁感应的熔炼功率为3800kw;
[0125]
步骤s24、将熔液浇入水冷铜模进行冷却形成铸锭,当铸锭温度低于不对造成高温伤人后,向熔炼炉充入氩气,开启熔炼炉门取出铸锭,其中合金铸锭的氧含量183ppm,合金熔炼的熔损为0.9%;
[0126]
步骤三、使用干法球磨工艺将铸锭粉碎的粉末平均粒径为4.0μm,粉碎后的粉末氧含量为1530ppm,球磨时间为4h;
[0127]
步骤四、使粉末在平行磁场中进行取向,使用的取向磁场的磁感应强度为0.8t,同时使用液压机将粉末压制成型,液压机将粉末压制成型的压力为12mpa,得到生坯,再使用等静压机对生坯进行二次成型等静压,二次成型等静压力为100mpa,得到坯体;
[0128]
步骤五、对二次成型静压的坯体进行烧结,具体为使用烧结炉采用真空或氩气保护的方式进行烧结,烧结的温度为1160℃,烧结时间0.5h,烧结后进行固溶,固溶温度比烧结温度低20℃,固溶时间大于等于烧结时间,固溶后得到的材料密度8.8g/cm3,材料氧含量2070ppm;
[0129]
步骤六、对烧结后的材料进行热处理,使用热处理炉采用氩气保护的方式进行热处理,热处理温度为750℃,热处理温度保温4h,然后从热处理温度冷却到400℃,冷却速率为1.5℃/min,得到高磁能积稀土永磁材料。
[0130]
对比例4
[0131]
本对比例提供了一种高磁能积稀土钴永磁材料的制备方法,包括以下步骤:
[0132]
步骤一、按照化学表达式pr[co
0.73
fe
0.20
cu
0.03
zr
0.04
(nind)
0.05
]
0.18
设定pr、co、fe、cu、zr、ni、nd的使用比例分别称量pr、co、fe、cu、zr、ni、nd的粉末;
[0133]
步骤二、使用电磁感应法对pr、co、fe、cu、zr、ni、nd的粉末进行加热熔化,混合得到熔液,将熔液浇入水冷铜模进行冷却形成铸锭;其中,加热熔化的步骤包括:
[0134]
步骤s21、将pr、co、fe、cu、zr、ni、nd的粉末装入熔炼炉中的熔炼坩埚中,其中co粉末应放于容易浸入熔液的位置;
[0135]
步骤s22、对熔炼炉抽真空,真空度达到15mpa以下,然后充入氩气,压力为﹣0.04mpa;
[0136]
步骤s23、加大电磁感应的功率,对各粉末进行加热熔化,当原材料全部熔化后,保持功率使熔液在沸腾状态下保持4min,电磁感应的熔炼功率为4500kw;
[0137]
步骤s24、将熔液浇入水冷铜模进行冷却形成铸锭,当铸锭温度低于不对造成高温伤人后,向熔炼炉充入氩气,开启熔炼炉门取出铸锭,其中合金铸锭的氧含量190ppm,合金熔炼的熔损1.4%;
[0138]
步骤三、使用干法球磨工艺将铸锭粉碎的粉末平均粒径为4.4μm,粉碎后的粉末氧含量1620ppm,球磨时间为6h;
[0139]
步骤四、使粉末在平行磁场中进行取向,使用的取向磁场的磁感应强度0.8t,同时使用液压机将粉末压制成型,液压机将粉末压制成型的压力12mpa,得到生坯,再使用等静压机对生坯进行二次成型等静压,二次成型等静压力为150mpa,得到坯体;
[0140]
步骤五、对二次成型静压的坯体进行烧结,具体为使用烧结炉采用真空或氩气保
护的方式进行烧结,烧结的温度为1200℃,烧结时间2h,烧结后进行固溶,固溶温度比烧结温度低30℃,固溶时间大于等于烧结时间,固溶后得到的材料密度8.6g/cm3,材料氧含量1700ppm;
[0141]
步骤六、对烧结后的材料进行热处理,使用热处理炉采用氩气保护的方式进行热处理,热处理温度为800℃,热处理温度保温8h,然后从热处理温度冷却到400℃,冷却速率为1℃/min,得到高磁能积稀土永磁材料。
[0142]
分别测定实施例1-5制备的高磁能积稀土钴永磁材料和对比例1-2制备的稀土钴永磁材料的最大磁能积和内禀矫顽力,得到下表:
[0143][0144]
结果表明,实施例1-3制备得到的高磁能积稀土钴永磁材料的最大磁能积均在263kj/m3以上,内禀矫顽力均在2387ka/m以上,而实施例4和实施例5制备得到的高磁能积稀土钴永磁材料的最大磁能积则分别达到了279kj/m3和277kj/m3,内禀矫顽力这则达到了2422ka/m和2425ka/m,实施例1-5制备的高磁能积稀土钴永磁材料的最大磁能积和内禀矫顽力均显著优于对比例1和对比例2制备的稀土钴永磁材料,而实施例4和实施例5制备的高磁能积稀土钴永磁材料的最大磁能积和内禀矫顽力又优于对比例3和对比例4制备得到稀土钴永磁材料。
[0145]
这里说明的设备数量和处理规模是用来简化本发明的说明的。对本发明的应用、修改和变化对本领域的技术人员来说是显而易见的。
[0146]
尽管本发明的实施方案已公开如上,但其并不仅仅限于说明书和实施方式中所列运用,它完全可以被适用于各种适合本发明的领域,对于熟悉本领域的人员而言,可容易地实现另外的修改,因此在不背离权利要求及等同范围所限定的一般概念下,本发明并不限于特定的细节和这里示出与描述的实例。