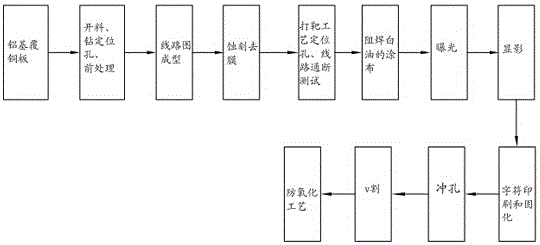
本发明涉及LED光电技术领域,具体地说是一种LED铝基线路板的制作方法。
背景技术:追求轻巧、方便是当前LED照明电器的趋势,人们期望有一种集电源部分和光源于一体的LED照明器具,可以极大方便日常使用。制作铝基线路板通常包括制作铝基覆铜板和以其为基础制作铝基线路板两大部分,在制作铝基覆铜板的过程中,目前涂胶步骤采用滚涂、印刷和喷涂这几种,这几种涂胶方式存在以下不足:1、滚涂,胶的厚度很难调整、厚薄不均,生产速度较慢:一般在3-4m/min左右;2、印刷,效率低、速度慢,产品尺寸小,一般产品宽度在60cm以下,不能生产尺寸1m*2m这样的大规格铝基覆铜板;3、喷帘,产品可以喷得很均匀,也能生产大规格板,但大量胶体物质飘散在空气环境,除了严重影响环境,而且大量浪费原材料。而且,覆铜板板材在上胶加工过程中,如遇表面有粉尘或平整度不好的情况,对滚涂和印刷工艺都有影响,例如导热胶与铝板、铜箔之间易有空隙,出现附着力不强等问题,从而影响铝基覆铜板的质量。另一方面,目前集电源部分和光源于一体的有两种做法,其中一种做法是在铝基线路板上直接以贴片的方式将驱动电源部分置于LED光源电路之内,以AC-AC的方式驱动,这种方式LED具有闪烁现象,并且受到线路浪涌等因素的影响,驱动芯片极易损坏,LED灯具的稳定性受到严重影响。另一种做法是用铣好(或用冲床冲好)尺寸的FR4或CEM-1板作基板,镶嵌到铣好(或冲好)同样尺寸的铝板上,然后涂布绝缘层,覆上铜箔板压合,再进行线路板加工生产,制成电源光源一体式LED灯具,这种方法的缺点是加工成本高、生产效率很低,只能少量制造,无法规模化生产;而且压合时,由于基板和铝板本身裁切时产生的厚度误差、基板镶嵌在铝板上出现的加工误差以及冲切等加工时产生的粉尘落入铝板上,这几个因素都会严重影响到绝缘层与铜箔、铝板的结合,最终影响到产品的剥离强度、绝缘性和导热性。
技术实现要素:本发明提供了一种LED铝基线路板的制作方法,通过该工艺可大批量生产铝基线路,且制作的LED和电源均具有良好的散热性。本发明是通过以下技术方案实现的:一种LED铝基线路板的制作方法,包括铝基覆铜板的制作以及基于铝基覆铜板制作铝基线路板,包括以下步骤:。(1)铝板表面处理:选用铝基底板0.2-1.5mm经处理后水洗烘干,制备得铝基底板;(2)配制导热胶;(3)喷涂导热胶:采用喷刀喷涂技术直接将导热胶喷淋在铝板上,喷涂好的铝板放隧道炉中烘烤,并使导热胶处半固化状态的胶化时间控制在50-70秒;采用喷刀喷涂技术,解决现有几种涂胶方式带来的缺陷,高压喷刀在其下方喷出的是帘幕,可均匀地对线路板进行涂胶,且节省油墨或胶,工作速度快,每分钟可以走到20-25米,劳动效率成几何倍数的增长。(4)覆合铜箔:将厚度为0.018-0.072mm的铜箔层叠在涂好的导热胶膜的铝板上,并经层压、剪切成型,得铝基覆铜板;(5)开料、钻定位孔、前处理;(6)线路图成型:包括双面感光油墨涂布、曝光、显影,首先是液态感光涂布要用双面同时完成,铜面为上温区,其温度控制在80-110℃,铝面为下温区,其温度控制在70-90℃,曝光能量分别为铜箔面光能量为450-550mj,铝板面曝光能量为550-650mj;双面显影,浓度为0.8-1.2%的碳酸钠溶液,速度3.2m-4m/分钟,压力1.8-2.4kg;(7)蚀刻去膜:将铝板面与铜箔面印刷成型固化后,进行蚀刻、去膜,去膜后再进行表面清洗、干燥,表面清洗水压控制在2.4-3.6kg,冲洗时间达到20秒以上;(8)打靶工艺定位孔、线路通断测试;(9)阻焊白油的涂布;(10)曝光;(11)显影;(12)字符印刷和固化;(13)冲孔;(14)v割;(15)防氧化工艺:得铝基线路板进一步地,所述步骤(1)铝板表面处理的具体方法为:a、将该铝板浸泡在10%-12%,温度为56-60°的碱蚀槽处理3.5-4.5分钟,b、碱蚀好的铝板经水洗后泡在硝酸含量为10%-12%的中和槽处理2-3分钟,进一步除去铝板表面残留物,c、处理好的铝板水洗烘干。进一步地,步骤(3)中的导热胶的厚度在300μm以上,按导热胶的厚度调整喷涂的次数,每次喷涂厚度为50um-150um之间,喷涂好的铝板放隧道炉在140℃-150℃的条件下,烘烤4-6分钟。进一步地,在喷涂导热胶后加覆一层半固化片,再覆合铜箔,半固化片采用玻璃布,导热系数在1W/mk以上。进一步地,步骤(4)中,先将排版好的复合铝基板转入压机加温、加压,抽真空压合,使铝板、导热胶膜、铜箔结合一起,再将热压好的铝基板转入冷压机冷却。进一步地,所述步骤(5)中,将铝基覆铜板经过烘道预算加热,烘道温度参数为160-180℃,传动速度在3.5-4M/分钟。进一步地,步骤(10)中,在铝板面垫0.1-0.15mm厚的菲林墨片,对线路阻焊进行曝光。进一步地,步骤(11)显影,采用碳酸钠溶液,浓度是0.8-1.2%,速度3.2m-4m/分钟,压力1.8-2.4kg,清洗的下喷压力为2.5-3.5kg,热风刀压力为2.0-3.0kg。本发明采取了上述改进措施进行,其有益效果显著:本发明可大批量生产集电、光源于一体的铝基线路板,改变了线路板的传统形式,为线路板植入新的功能;摒除了在铝板开设凹槽再镶嵌FR4或CEM-1板的繁琐、低效、易损的做法。且该发明无加工时的落灰,产品具有铜箔附着力强、散热性好、导热性强、耐压性高等特点,可以改变当前LED筒灯、射灯、平板灯等室内外照明灯具的装配结构,有节能降耗、节材增效特点。附图说明图1为本发明铝基覆铜板的生产工艺框图;图2为生产铝基线路板的框图。具体实施方式下面对照附图结合实施例对本发明作进一步的说明:参照图1、图2所示,一种LED铝基线路板的制作方法,通常包括制作铝基覆铜板和以其为基础制作铝基线路板两大部分,步骤包括:(1)铝板表面处理:a、将该铝板浸泡在10%-12%,温度为56-60°的碱蚀槽处理3.5-4.5分钟,b、碱蚀好的铝板经水洗后泡在硝酸含量为10%-12%的中和槽处理2-3分钟,进一步除去铝板表面残留物,c、处理好的铝板水洗烘干。(2)配制导热胶:将质量百分数为15%的901树脂,3%的295树脂,6.7%的128树脂,3.2%的塑化剂,0.57%的双氰胺,1.2%的DDS固化剂,0.19%的流平剂,0.47%的偶联剂,0.07%的催化剂,15.6%的DMF溶剂混合均匀,连续搅拌30-40分钟后,静置1-3小时制得环氧树脂混合剂;将质量百分数为54%的氧化铝和46%的环氧树脂混合剂混合均匀,搅拌2-3小时后,经球磨处理,使填料和树脂均相分布,再进行除杂后待用。(3)喷涂导热胶:采用喷刀喷涂技术直接将导热胶喷淋在铝板上,导热胶的厚度在300μm以上,按导热胶的厚度调整喷涂的次数,每次喷涂厚度为50um-150um之间,可通过调整喷涂传送速度和胶水泵电机变频得到要求的胶膜厚度,喷涂好的铝板放隧道炉在140℃—150℃的条件下,烘烤4-6分钟,并使导热胶处半固化状态的胶化时间控制在50-70秒;可在喷涂导热胶后加覆一层半固化片,再覆合铜箔,半固化片采用玻璃布,导热系数在1w/mk以上。(4)覆合铜箔:将厚度为0.018-0.072mm的铜箔层叠在涂好的导热胶膜的铝板上,先将排版好的复合铝基板转入压机加温、加压,抽真空压合,使铝板、导热胶膜、铜箔结合一起,压合所需工艺参数为(a)起始温度为180°C,升温到185°C,加压50kgf,(b)保温185°C加压到70kgf,时间为2分钟,(c)保温185°C加压到120kgf,时间为7分钟,(d)保温185°C加压到180kgf,时间为17分钟,(e)保温185°C加压至200kgf,压20分钟,(f)由185°升温至210°C,时间为5分钟,压力增到250kgf,(h)保温210°C,压力为250kgf的条件下压合22分钟,(i)升温到215°C升温时间5分钟,压力增加到280kgf压合50分钟,(j)由215°降温到180°C,时间为6分钟,压力降为50kgf,(k)降温至150°C,时间为4分钟,压力降为4Kgf,热压完成;热压好的铝基板转入冷压机冷却,压力为100kgf,冷却时间为100分钟。(5)开料、钻定位孔、前处理:开料,由于这种材料的特性是铝层较薄、介质层较厚韧性降低,只能用剪切床分切。其在分切前,经过烘道预算加热,烘道温度参数为160-180℃,传动速度在3.5-4M/分钟,主要是为了介质层的热作用韧化,减少切面的分层边裂不良。同时设置有效边距达到2.5mm-3.5mm,可以保证蚀刻后,磨边后的边框在后工序冲切边框的完整性,减少边框断裂而掉入冲模内产生的压痕性不良;开料后的工作板先清洗,烘干处理。主要目的是防止有板屑之类的异物在叠板中间存在间隙,再使用铝基板专用的钨钢或钻石刀进行钻孔;再做线路图形前都需要经过清洁,除氧化处理,用98﹪浓度硫酸配比成体积比2-3﹪的浓度的硫酸水溶液,可以同时使铜面和铝面得到氧化去除,上下抛刷刷辊刷目要给予区别,上刷在350目左右,磨痕在12-15MM,下刷在500目,磨痕在6-9MM,烘干温度在60-70℃.这样能保证铜面和铝面干净,使油墨的结合力达到要求。(6)线路图成型:包括双面感光油墨涂布、曝光、显影,首先是液态感光涂布要用双面同时完成,由于铝层、中间介层、铜的厚度差异,其吸收能量的差异较大,所以烘道炉要用上下双供热系统,铜面为上温区,其温度控制在80-110℃,铝面为下温区,其温度控制在70-90℃,这样才不会使液态感光膜因温度偏高产生曝光后的显影不净,同样在曝光工艺上也有所不同,因同一种油墨附着在不同基色时,会产生吸光性能差异,为能在双面显影都能干净,曝光能量分别为铜箔面光能量为450-550mj,铝板面曝光能量为550-650mj,可以达到双面同时显影干净;双面显影,浓度为0.8-1.2%的碳酸钠溶液,速度3.2m-4m/分钟,压力1.8-2.4kg。(7)蚀刻去膜:先检验双面图形开短路的不良,铝面的油墨保护完整理性,铝面与铜面图形成型后,放入酸性药液中进行蚀刻去膜,液浓度铍值1.19-1.21,药液温度为35-45℃,放入酸性蚀刻液中进行蚀刻、去膜,去膜后再进行表面清洗、干燥处理,清洗水压控制在2.4-3.6kg,清洗时间达到20秒以上。(8)打靶工艺定位孔、线路通断测试。(9)阻焊白油的涂布:涂布和印刷都要洁净处理,化学溶液稀硫酸浓度控制在3-5%,能保证铜面和铝面的效果,铜面的抛刷纤维刷及目数,磨痕宽度在工艺和单面板一样,不再描述。白油涂布后烘干后等待曝光。(10)曝光:因介质层薄,又是半透明,所以必须在铝面这面垫一张0.1-0.15mm厚的菲林墨片,防止上下框同曝时的现象,曝光时具有对曝光灯散射作用而影响显影效果。(11)显影:采用碳酸钠溶液。浓度是0.8-1.2%。速度3.2m-4m/分钟,压力1.8-2.4kg。因铝板面的电源驱动部分有下凹,所以清洗的下喷压力要提高到2.5-3.5kg,热风刀压力要达到2.0-3.0kg,使水分能够吹散完全烘干,防止水分溶入介层和铝基。(12)字符印刷所需的要求不同,有些是元件标识,有些是商标型号。因铝面有些不平,无法通过印刷来完成下凹部分的字符印刷,所以将商标等标识设计在铝面上,而其他所有的元件符号设计在白油面为好。印刷好字符的工作板将在温度150℃时间45分钟的条件下进行热固化。(13)冲孔:1、白油面朝下,用冲床一次完成孔径和外形的冲切。2、少量或样品,采用数控钻孔,对电源驱动板部分的元件孔进行钻孔,钻速要进行调整,以3-4万钻为宜。(14)v割。(15)防氧化工艺:采用浓度为5-6%的双氧水,硫酸浓度为4-5%,降低对铝基的微蚀损伤。在防氧化后清洗的下喷压力要提高到2.5-3.5kg,热风刀压力要达到2.0-3.0kg,使水分能够吹散完全烘干,温度控制在65-80度之间。以上列举的仅为本发明的具体实施例,显然,本发明不限于以上实施例,本领域的普通技术人员能从本发明公开的内容直接导出或联想到的所有变形,均应属于本发明的保护范围。