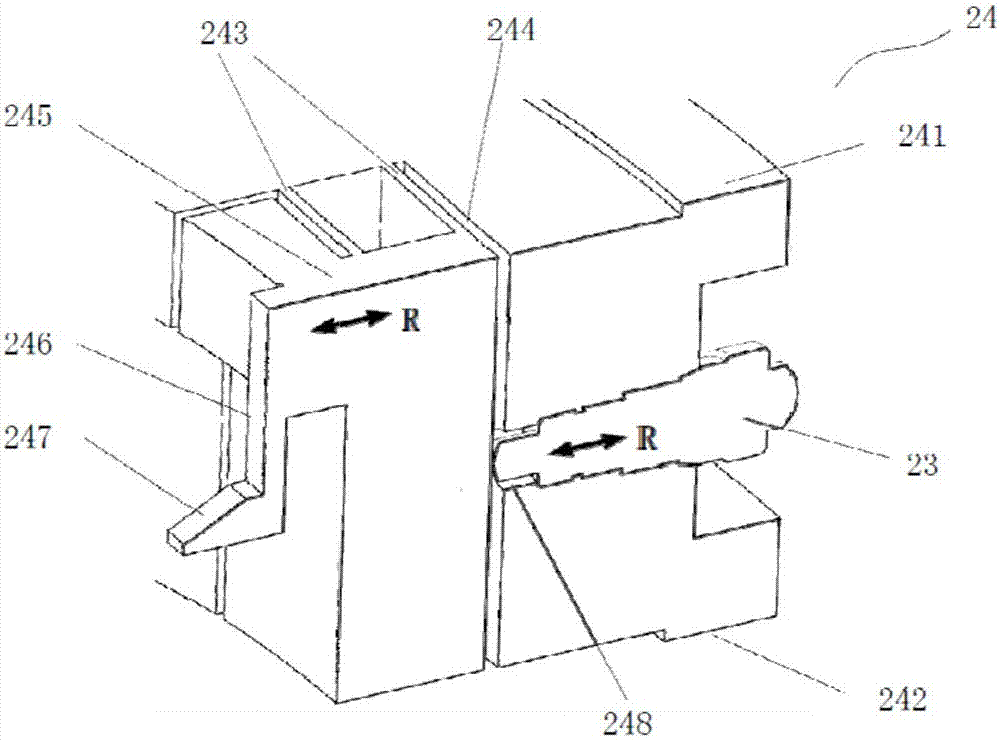
本发明属于高精密光学镜头制造和装调技术领域,特别是涉及一种可补偿面形的光学元件支撑结构、单元镜组、曝光光学系统及光刻机。
背景技术:高端光刻投影物镜的设计、加工、制造及装调是一个非常精密、复杂的系统工程。随着摩尔定律的延伸,半导体业界对处理器芯片最小线宽分辨率的要求越来越高,为了实现高质量的成像性能、获得更高的分辨率,要求光学元件面形精度RMS值达到1nm~2nm水平。随着光刻机投影物镜光学系统的NA值逐渐增大,光刻投影物镜中光学元件的通光孔径也越来越大,透镜的外径往往达到320mm甚至更大。然而,随着光学元件外径尺寸的增大,外力对光学元件面形的影响也愈加敏感。如不进行精确控制,由重力或紧固力导致的面形误差很可能超出期望值的2~3倍甚至10倍以上。除了光学加工过程中光学元件自身残余的面形误差,由镜框等支撑结构加工引起的尺寸、形位公差会导致光学元件受力不均匀,也会产生面形误差;此外,在将光学元件固定在镜框或镜座中时,无论是采用粘胶还是夹紧的方式,均无法实现完全“无应力”的效果,也会引入面形误差;最后,在将所有的光学元件和镜框连接成一个投影物镜整体时,必须采用一定的固定和联接措施,在此过程中产生的应力也会传入到光学元件上,引入一定程度的面形误差。上述这些对光学元件面形精度产生影响的因素均称为静态面形影响因素。在光刻机工作过程中,经过持续曝光之后,投影物镜的每个光学元件都会吸收一定的激光能量,由于光学元件大小、厚度不同,各个光学元件产生的温度变化量是不同的。由于大口径光学透镜对于温度的变化更为敏感,温度差异造成的光学元件面形的改变会对光学系统成像性能产生不利的影响。此外,环境温度、气压的变化也会导致投影物镜成像性能的劣化。上述光刻机工作过程中对投影物镜成像性能产生干扰的因素可称为动态面形影响因素。为了实现更高精度的分辨率,必须对上述静态面形误差和动态面形误差进行补偿。专利US6392825B1公开了一种具有多个弹性支撑单元的镜框结构,通过支撑单元的弹性抵消外界应力变形的影响;由于弹性支撑单元通过薄板材料加工而成,难以实现微米级的加工精度,并且弹性支撑单元和镜框通过焊接或螺钉紧定的方式连接,焊接应力和螺钉预紧力也会降低弹性支撑单元的最终精度。专利US6229675B1中提出一种将内外框变形解耦的结构形式,这种结构加工工艺性不好,是一种被动补偿方式,虽然能够消除外界应力对光学元件面形精度的影响,却无法补偿动态面形误差。专利US7031082B2公开一种可使光学元件变形的镜框结构,还具备变形监测单元,然而这种结构的变形调节部分由多个零部件装配而成,结构复杂、装调困难,难以实现对光学元件面形纳米级精度的调整。专利US7193794B2公开了一种主动补偿光学元件面形误差的镜框结构,可在不改变光学元件空间位置的情况下补偿像散和三叶对系统成像性能的影响;然而,这种方式沿轴向即光轴方向布置驱动器或传动结构,占用较大空间,难以实现对每个支撑点处光学元件受力的调整,且无法在同一个物镜中用于更多光学元件的面形补偿。
技术实现要素:本发明为解决光刻投影物镜曝光光学系统中光学元件静态面形误差和动态面形误差的补偿问题,保障光刻投影物镜制造过程中光学元件的高精度支撑、定位问题,提出一种可补偿或调整光学元件面形的光学元件支撑结构,该结构形式简单、工艺性好,能够补偿加工误差、装调力及外界温度变化等因素对光学元件面形精度的影响,可灵活应用于物镜装调、测试及工作等多个环节。本发明解决上述技术问题所采用的技术方案如下:提供一种光学元件支撑结构,用于支撑单元镜组的光学元件,包括镜座,所述镜座为一个圆周对称的机械构件,所述镜座内环向中心伸出一圈支撑杆,所述支撑杆在光轴方向和镜座径向上均具有一定柔性,所述支撑杆末端设置有支撑面,所述支撑面与光学元件下表面相互匹配,以将光学元件固定在所述镜座上;所述支撑杆的内侧连接一运动台,所述运动台通过一导向机构与镜座外环连接,所述导向机构用于运动台的运动导向。本发明的光学元件支撑结构应用于曝光光学系统的单元镜组中,镜座内环向中心伸出一圈支撑杆,支撑杆在光轴方向和镜座径向上均具有一定柔性,支撑杆末端设置有支撑面,支撑面与光学元件下表面相互匹配以将光学元件固定在镜座上,不但能够实现光学元件的超高精度支撑定位,通过驱动运动台使得支撑杆发生一定的变形和位移,还可以有效补偿由于外部加工、装配公差导致的面形误差,同时还能够实时补偿工作过程中环境温度、压力、激光辐照产生的像差。因而,该光学元件支撑结构能够在整个生命周期内保证光刻投影物镜曝光光学系统的整体像质。另外,本发明的光学元件支撑结构占用空间小,与曝光光学系统的镜座可呈一体式加工,且易于加工制造、成本低。能够在降低光学元件支撑镜座尺寸、形位公差要求的情况下,通过手动或自动的方式补偿光学元件静态和动态面形,最终实现光学元件超高精度面形的要求。且该结构能够应用于各种类型光学元件,并可在广泛的补偿范围之间使用,能够保证曝光光学系统的最终像质要求。根据本发明的一个实施例,所述镜座的顶部和底部分别伸出有上连接法兰和下连接法兰。根据本发明的一个实施例,所述导向机构与所述镜座的外环连接形成有狭缝,所述运动台的运动范围通过狭缝的宽度约束。根据本发明,所述光学元件支撑结构带有导向结构的运动台,能够将径向位移转化为光学元件的面形变化,实现物镜像质的主动补偿,可手动或自动驱动。根据本发明的一个实施例,所述导向机构为呈对称分布的平行四连杆结构,所述平行四连杆结构能够保证运动台按照预设的径向方向往复运动,所述导向机构的径向尺寸远小于其轴向尺寸和周向尺寸,使得其在光轴方向上的刚度远大于其在径向方向上的刚度,进而使得所述导向机构具有径向方向的移动自由度。在这里,远小于指的是尺寸比例小于1:10;远大于指的是尺寸比例大于10:1。根据本发明的一个实施例,所述导向机构由四个薄型板弹簧组成,四个薄型板弹簧相对径向两两呈对称形式分布,以形成一对平行四连杆机构。根据本发明的一个实施例,所述支撑面与光学元件下表面相互匹配的表面为平面、凹面或凸面的一种,所述支撑杆数量大于等于3,且所述支撑杆绕光轴呈周向均布排列。根据本发明的一个实施例,所述支撑结构还包括多个驱动机构,所述镜座形成有多个沿镜座径向延伸的定位孔,所述定位孔由镜座外环表面延伸至与所述狭缝相通,所述驱动机构插入所述定位孔中以此固定于镜座中,所述驱动机构末端与运动台接触,所述驱动机构末端能够输出一定位移和力,并传递至运动台使之产生径向位移,所述支撑杆与运动台直接相连,所述运动台所产生的径向位移可直接带动支撑杆产生位移和变形,所述支撑杆可将力和变形传递至光学元件。本发明的驱动机构有多种选择,易于实现光学元件面形的高精度的补偿调整。另外,本发明还提供了一种单元镜组,其包括上述的光学元件支撑结构。另外,本发明还提供了一种曝光光学系统,其由多个上述的单元镜组堆叠而成。另外,本发明还提供了一种光刻机,其包括掩模台、上述的曝光光学系统及硅片台,所述曝光光学系统设置在所述掩模台与硅片台之间,用于将所述掩模台上的图形在硅片台上实现完美成像。本发明提供的光学元件支撑结构可实现任意多个驱动点布置,不仅能够补偿低阶像差,还能够补偿高阶像差。本发明的导向机构简单、紧凑,为一体式结构,能够在光刻物镜有限的空间内实现更多元件的调节补偿。本发明机械加工工艺性好,易于实现支撑面高精度加工和检测。本发明的光学元件支撑结构具有通用性,能够适应不同用途、不同种类的光学元件。附图说明图1是本发明一实施例提供的单元镜组的轴测图;图2是本发明一实施例提供的单元镜组的局部剖视图;图3是本发明一实施例提供的单元镜组的局部俯视图;图4是本发明一实施例提供的单元镜组的轴测图;图5是本发明一实施例提供的单元镜组的光学元件表面面形变化测量图;图6是本发明一实施例提供的光刻机的结构示意图。图中:1掩模台,2曝光光学系统,3硅片台,4测量光线,5面形测量干涉仪,21单元镜组,22光学元件,23驱动机构,24镜座,25光轴,241上连接法兰,242下连接法兰,243导向机构,244狭缝,245运动台,246支撑杆,247支撑面,248定位孔。具体实施方式结合图1至图5,本发明一实施例提供的光学元件支撑结构,包括镜座24及驱动机构23。镜座24包括一体加工成型的上连接法兰241、下连接法兰242、导向机构243、狭缝244、运动台245、支撑杆246、支撑面247及定位孔248。如图1,所述光学元件支撑结构包含于单元镜组21中,所述单元镜组21通常由光学元件22、驱动机构23和镜座24组成。通常将与光学元件22光轴平行的方向定义为Z轴,坐标系中心位于光学元件22上表面或下表面的中心位置,与Z轴垂直的平面为XY平面。所述光学元件1的材料为深紫外投影光刻物镜中常用到的熔石英、微晶玻璃、ULE或者氟化钙,也可以是普通镜头中所采用的常用光学材料。所述镜座24为一环形旋转对称金属构件,其中心有通孔用于放置光学元件22,通孔直径范围由光学元件22决定,一般为50mm~350mm,以便光线能够通过。所述镜座24和光学元件22之间通常具有一定的间隙,用于光学元件22的装配和调整。镜座24需采用具有较高强度和稳定性的材料,一般为金属材料,如:不锈钢、铝合金、铜合金、铟钢、钛合金、高强度工具钢等。所述镜座24内通常放置一个或多个光学元件22,图示实例中放置一个光学元件22。如图2,所述镜座24的顶部和底部分别伸出有上连接法兰241和下连接法兰242,二者可通过螺钉或其它方式与相邻的镜组固定连接。所述镜座24靠近中心通孔处延伸有支撑杆246,支撑杆246末端有支撑面247,用于光学元件22的支撑定位,每个支撑杆246对应一个支撑面247。所述光学元件22通过机械紧固、弹性夹紧(本实例中未给出详细结构)、焊接或者胶黏剂粘接的方式固定在支撑面247上,根据光学元件22表面曲率的不同,支撑面247可以是平面、凹面或凸面。所述支撑面247近似为长方形,其面积可在2mm×2mm~10mm×10mm之间,根据固定光学元件22的不同方式,可选择不同的支撑面积,可使光学元件22能够得以稳定、可靠地固定在镜座24内。支撑面247通常采用超精密车削、精密激光加工、精密电火花加工、超声振动加工、精密磨削等方式加工。所述支撑杆246为沿与光轴25平行的Z轴同向的长条状结构,其沿Z向的长度为L,沿径向(从光轴25出发指向镜座24外圆周,并垂直于光轴25)的尺寸为厚度T,沿周向(与镜座24外圆周相切,并垂直于光轴25和径向)的尺寸为A。大部分情况下L>A>T,L的尺寸范围为3mm~30mm,A的尺寸范围为1mm~20mm,T的尺寸范围为0.1mm~5mm。根据光学元件22重量、尺寸、材料的不同,支撑杆246的尺寸也有所不同,以使其在径向或光轴方向具有一定的柔性。支撑杆246位于运动台245上,为一体式加工结构或装配结构。所述运动台245具有足够的刚度以承载支撑杆246和光学元件22的重量。运动台245通过导向机构243与镜座24外环连接。如图3,所述导向机构243由四个薄型板弹簧组成,四个薄型板弹簧相对径向两两呈对称形式分布,形成一对平行四连杆机构。根据光学元件22和镜座24大小和重量的不同,每个薄型板弹簧厚度在0.1mm~2mm之间,长度在10mm~40mm之间,这样就使得薄型板弹簧厚度在径向上具有一定柔度,在外部作用力下便可产生沿径向的变形。由于薄型板弹簧平行四连杆的导向作用,所述运动台245便可沿径向,即图示的R方向进行往复运动。所述导向机构243的薄型板弹簧结构在与光轴平行的Z方向上是贯通的,与运动台245和镜座24连接形成一体式结构。所述导向机构243可通过激光加工、化学腐蚀、线切割、电火花等方式加工而成。通过上述方式加工后形成狭缝244,狭缝244的缝宽一般在0.2mm~3mm之间,用于限制运动台245的运动范围,防止由于运动行程过大导致导向机构243的薄型板弹簧应力超出其屈服极限,进而发生结构破坏。所述导向机构243也可采用分离式的板簧进行装配,以用于运动台245的运动导向。所述导向机构243也设计为非对称形式,或平行六连杆或其它具有导向功能的结构形式。所述驱动机构23的典型实例为螺旋测微仪,固定于定位孔248中,其末端与运动台245接触,用于输出力和位移。驱动机构23沿径向R布置,其输出位移方向也为径向。驱动机构23的Z向位置处于运动台245的中间部位,与支撑面247基本处于同一水平面,以保证运动台245只产生平行于R向的运动,不产生其他方向的位移。驱动机构23也可采用其他类型位移输出机构,如:压电驱动器、气动元件、液压驱动元件、直线电机及磁力器件等,驱动方式既可以采用手动驱动,也可采用自动驱动。在典型实例中,所述驱动机构23与运动台245、导向机构243、支撑杆246和支撑面247一一对应。如图4,上述驱动机构23与运动台245、导向机构243、支撑杆246和支撑面247绕Z轴呈周向均布,根据不同应用场合,其数量通常为3~40之间。在其他应用实例中部分运动台245可不包含驱动机构23和导向机构243,仅保留支撑杆246和支撑面247。如图5,通过驱动机构23沿R向输出位移和力,便可驱动运动台245沿R向产生相应位移,最终将驱动力传递至支撑杆246和支撑面247。由于,支撑面247通常为斜面,传递到此斜面上的驱动力可分解为沿Z方向的轴向力,从而使光学元件22表面面形发生变化。所述光学元件22表面面形可由驱动机构23进行控制,如:通过对间隔180°的两个驱动机构23沿相同方向进行驱动,可使光学元件22表面产生象散;通过对间隔120°的三个驱动机构23沿相同方向进行驱动,可使光学元件22表面产生三叶像差;通过对间隔45°的8个驱动机构23沿相同方向进行驱动,可使光学元件22表面产生四叶像差。以此类推,通过对不同位置、数量的驱动机构23输出不同方向和大小驱动位移,便可人为实现光学元件22表面面形的多种像差,其像差大小可通过控制驱动力或驱动位移来实现。所述单元镜组21的光学元件22表面面形变化可由面形测量干涉仪5向光学元件照射测量光线4进行检测。通过对上述光学元件22表面面形产生期望像差可用于曝光光学系统2的像质补偿和调节。如图6所示,掩模台1、曝光光学系统2、硅片台3均为大规模集成电路制造设备光刻机的组成部分,曝光光学系统2用于将掩模台1上的图形在硅片台3上实现完美成像。曝光光学系统2由多个单元镜组21堆叠而成。在工作过程中,曝光光学系统2受外界温度、气压变化影响,其成像焦点位置会发生一定漂移,同时其内部光学元件22吸收激光能量导致的变形也会产生不同种类的成像像差。通过对单元镜组21的不同位置、数量的驱动机构23进行控制,便可对曝光光学系统2的成像质量进行调节和补偿。本发明上述实施例的工作原理如下:所述单元镜组中光学元件通过激光焊接、胶黏剂粘接或其它机械锁紧方式固定于镜座的多个周向均布的支撑面上,支撑面通过支撑杆与镜座相连。由于光学元件的面形精度要求极高,通常要求在0.3nm~2nm之间,考虑光学元件自重的影响,因而对所有支撑面的轮廓度等形位公差要求极高,通常会是亚微米甚至纳米级的要求,即使采用超精密车削也难以完全保证其形位公差满足要求。本发明上述实施例在镜座上加工或装配所述导向机构和狭缝,便可形成与支撑杆相连的运动台,使导向机构按照对称布置的平行四连杆原理工作,进而保证运动台能够按照期望的径向方向往复运动。所述驱动机构通过定位孔固定在镜座的外环中,在工作过程中驱动机构前段会按照调节量要求输出位移,推动运动台产生期望的运动量和驱动力。驱动机构既可以是手动驱动也可以是自动驱动,其最大输出位移由导向机构的狭缝限制,以避免导向机构受力过大发生损坏。本实施例中,由于镜框加工装配导致的尺寸、形位公差会带来光学元件的支撑面形误差。因此,在进行单元镜组装配、集成前,首先必须对其支撑状态下的面形进行检测。通过面形干涉仪便可测得支撑面形中的各项误差成分,如:象散、彗差、球差、三叶及四叶等,通过对其泽尼克系数大小进行理论计算或仿真分析,从而获得各个驱动机构的补偿调节位移量。将各个驱动机构的调节量分别输出并施加在运动台上,进而通过支撑杆和支撑面的传递使光学元件产生定量的受力变形,抵消由于加工、装配误差产生的影响。此阶段的调节可称为静态支撑面形补偿。此后,需采用精密焊接、胶黏剂粘接或机械夹紧的方式将光学元件固定在镜座中,随后,要将所有的单元镜组连接成一个投影物镜曝光光学系统,这个过程中会不可避免地产生装配应力,也会引入不同程度的面形误差。同样采用面形干涉仪对单元镜组面形的各项误差成分进行检测。但此时由于光学元件已经固定在镜座中,由于刚度耦合导致补偿同样的面形误差所需的调节机构数量和输出位移量与静态支撑面形补偿阶段相比更为精确和难以控制。因而,必须采用实时监测的方式进行调节量和补偿效果的标定,方可实现最佳效果。上述补偿均是针对静态面形误差实施的。最后,在曝光光学系统实际工作过程中,由于环境温度、气压变化和激光能量吸收均会引入一定程度的像质误差,通过对系统像质进行分析和模拟,便可计算出需要补偿的光学元件及其面形改变量,通过对光学元件相应驱动机构输出所需的位移便可实现曝光光学系统的像质补偿。上述这些对光学元件面形精度产生影响的因素均称为动态面形影响因素。本发较明中的光学元件支撑结构,在曝光光学系统2中的个数不局限于一个,根据不同应用场合,其数量可以是4、6或者全部。显然,上述实施例仅仅是为清楚地说明本发明所作的举例,而并非是对本发明的实施方式的限定。对于所属领域的普通技术人员来说,在上述说明的基础上还可以做出其它不同形式的变化或变动。这里无需也无法对所有的实施方式予以穷举。而这些属于本发明的精神所引伸出的显而易见的变化或变动仍处于本发明的保护范围之中。