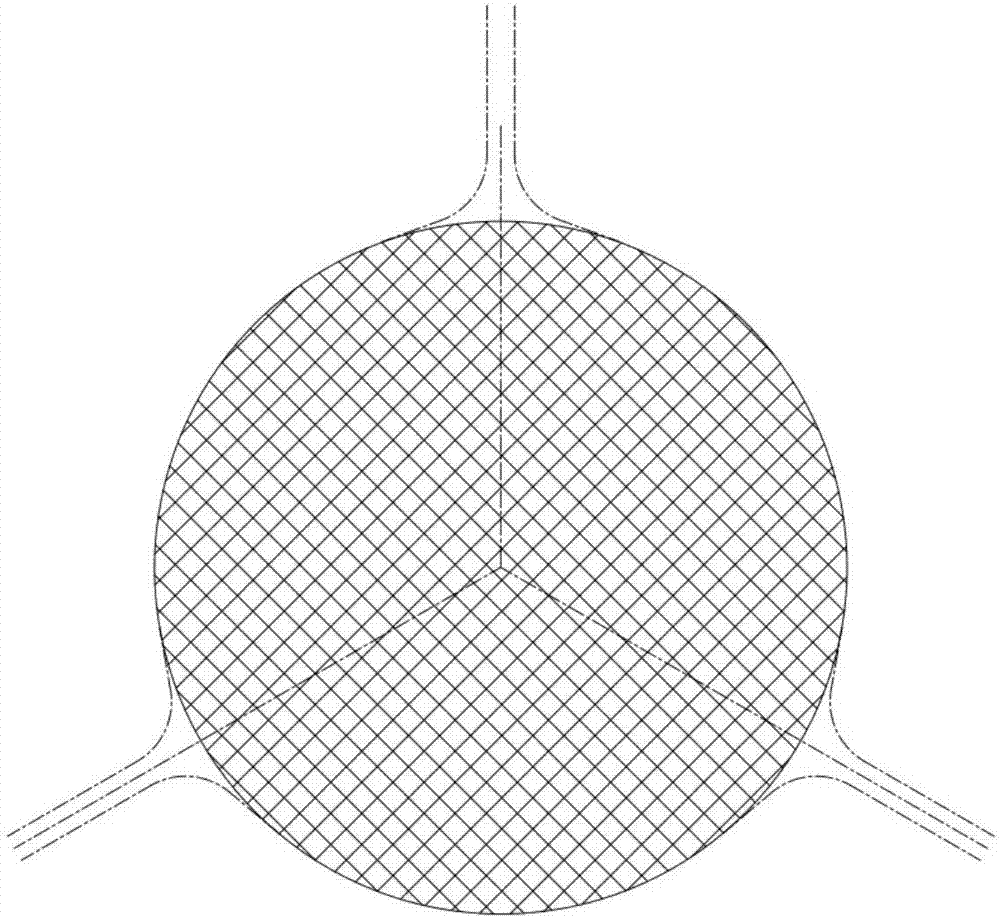
本实用新型属于冶金
技术领域:
,特别是涉及一种采用四辊轧机的圆钢轧制设备。
背景技术:
:我国现有棒材轧线450套以上,生产的产品绝大部分是普通建筑用材和一般优质钢材,棒材市场呈现以下几个特点:一方面,普通建材和中低端优钢棒材产品过剩,且生产成本较高,利润薄;另一方面,随着近些年机械、汽车等行业的发展壮大,市场对高品质高精度优特钢棒材的需求明显增加,是今后线棒材产品结构调整的主要方向。为适应市场的发展和竞争需求,生产企业非常渴望通过应用新装备和新技术来提高产品质量、降低生产成本。常规情况,生产棒材均采用二辊轧机,二辊轧制圆钢时由两个轧辊组成的椭圆型或者圆孔型系统对轧件进行连续变形,在最后一架轧机上通过圆形孔轧制出最终圆形断面。此种生产方法存在尺寸精度不高、轧件内应力较大、产品成材率低、单道次延伸系数小、轧制负荷较大、生产效率较低等问题。为解决该种问题,有些生产线采用三辊轧机轧制圆钢,通过三个轧辊组成的类似圆形孔型对轧件变形,轧制出最终圆形断面,此种轧制工艺在一定程度上改善了二辊轧机生产圆钢的缺点,对于追求更高精度、更高效率的产品,生产塑性更差的金属还是无能无力。技术实现要素:鉴于以上所述现有技术的不足,本实用新型的目的在于提供一种采用四辊轧机的圆钢轧制设备,能显著提高产品尺寸精度,降低圆钢产品的不圆度。此外,通过四辊轧制方式可以提高圆钢道次变形量,减少变形道次,提升变形效率,节约生产能耗。为实现上述目的及其他相关目的,本实用新型技术方案如下:一种采用四辊轧机的圆钢轧制设备,包括沿轧制方向前后布置的2道次以上四辊轧机;前后道次四辊轧机相互交错45°布置,每道次四辊轧机包含4个变形辊,每个变形辊变形区相同,变形区夹角均为90°。进一步,同一道次四辊轧机的4个变形辊的孔型和嵌入圆坯的深度相同。4个变形辊具有相同的孔型,使得4个辊环孔槽深度相同,并且辊环孔槽浅,槽底速度与轧件的速度差小,提高轧件表面质量;辊环孔槽浅,辊环消耗小,单槽轧制量提高,生产成本较低。进一步,所述变形辊的孔型由圆弧段和位于圆弧段两端的切线段组成,圆弧段夹角为10°~80°。进一步,越接近成品道次,相应圆弧段的夹角越大。进一步,所述每个变形道次延伸系数为1~1.5,越接近成品道次,相应延伸系数越小。如上所述,本实用新型的有益效果是:1)能显著提高产品尺寸精度,降低圆钢产品的不圆度,下游机械加工减少剥皮、拉拔、锻压工序,可降低下游行业生产成本;2)变形特点使得轧件宽展小,道次变形效率高,节约生产能耗;3)轧件受到四向压力,头尾变形较好,劈头开裂情况少,提高金属成材率;4)辊环孔槽浅,槽底速度与轧件的速度差小,提高轧件表面质量;5)辊环孔槽浅,辊环消耗小,单槽轧制量提高,生产成本较低;6)四辊变形特点使得通过调整辊缝生产不同规格的产品更加便捷;7)四辊轧制为四向压力,更适合生产难变形、变形抗力大的金属产品;8)辊环孔槽浅,更适合生产大规格圆钢产品。附图说明图1为传统二辊轧制圆钢孔型结构示意图;图2为传统三辊轧制圆钢孔型结构示意图;图3为本实用新型四辊轧机轧制圆钢孔型系统示意图;图4为本实用新型四辊轧机轧制圆钢孔型系统局部示意图;图5为本实用新型四辊轧机轧制圆钢孔型结构示意图;图6和图7为本实用新型孔型构成示意图;图8为现有技术中圆坯轧制时由相邻轧辊之间挤出的示意图;图9为本实用新型中圆坯轧制时由相邻轧辊之间挤出的示意图。零件标号说明1-圆坯2-变形辊3-挤出部分具体实施方式以下由特定的具体实施例说明本实用新型的实施方式,熟悉此技术的人士可由本说明书所揭露的内容轻易地了解本实用新型的其他优点及功效。实施例如图5所示:本实施例中的四辊轧机轧制圆钢的孔型结构图,如图3所示:本实施例中采用四辊轧机的圆钢轧制设备,包括沿轧制方向布置的2道次以上四辊轧机,前后道次四辊轧机相互呈45°交错布置,轧制时,将上游工序输送来的中间断面的圆形轧件(圆坯1),经过2道次以上,相互呈45°交错的四辊轧机进行连续轧制,最终形成高品质高精度的圆钢产品;其中每道次四辊轧机包含4个变形辊,每道次的4个变形辊2变形区相同(即轧辊宽度相同),变形区夹角均为90°。其中,相互呈45°交错是指,前后相邻两个四辊轧机的轧辊在圆坯周向上相差45°,保证在变形区为90°的机组中,圆坯在前机架的辊缝位置与后机架的辊中心一致,保证变形的对称性和均匀性。如果同一道次轧辊结构不同,轧辊嵌入圆坯1的深度不同,不对称压缩变形导致轧制圆坯易产生弯曲和扭转,圆坯四周表面易产生翘皮。本实用新型同一道次的四个变形辊2结构相同,变形辊2嵌入圆坯的深度相同,辊环孔槽较二辊、三辊浅,辊环消耗小,槽底速度与轧件的速度差小,提高轧件表面质量。如图6和图7所示,变形辊的孔型由中间的圆弧段L1和两端的切线段L2组成,切线段L2与轧辊边缘倒角R。圆弧段夹角a为10°~80°。越接近成品道次,相应圆弧段L1的夹角a越大,切线段L2越短。即,沿轧制方向,圆弧段夹角a呈增大趋势,可以逐道次增大(如40、50、60、70),也可以隔几个道次增大(如40、50、50、60、60、70)。圆弧段夹角逐渐增大,孔型与圆钢接触面积越大,使得圆钢越近成品道次,尺寸精度越高,最终达到设定的工艺效果。如果轧机孔型都是由圆弧段直接形成,圆弧段末端与轧辊边缘连接。这样在轧制过程中由于轧辊对轧件的挤压,会使得轧件沿相邻轧辊之间的间隙挤出形成条状结构等,挤出部分4在下一道次中被压回轧件外圆范围内,如此反复,挤出部分4会在产品表面形成缺陷。如图8所示。本实用新型中,如图9所示,通过切线段与轧辊边缘进行过渡,在轧制时,挤出部分4会贴着切线段流动,位于切线段与轧机外圆面空间内,从而为挤出部分提供容纳空间,使挤出部分停留在离圆坯1外圆面更近的位置,并扩大其截面,防止其挤出高度过高,影响表面质量。每个变形道次延伸系数为1~1.5,越接近成品道次,相应延伸系数越小。即,沿轧制方向,延伸系数呈减小趋势,可以逐道次减小,也可以隔几个道次减小。由于每道次的4个轧辊变形区(宽度)相同,并且圆弧段夹角a相同,在轧制工艺中同一道次中每个轧辊接触轧件的面积相同,相对于现有轧辊接触轧件面积不同的轧机,本实用新型轧辊与轧件速度差小,表面质量好,并且,辊环消耗小,单槽轧制量提高,生产成本较低。本例中,将上游工序输送来的中间断面的大圆形断面轧件,经过共计4道次的四辊轧机连续轧制第一道次至第四道次的圆弧段夹角a分别为40°、50°、60°、60°。第一道次至第四道次的变形道次延伸系数分别为1.3、1.2、1.15、1.1。下图为对同一圆坯采用传统二辊、三辊轧制和本实用新型设备轧制的对比:产品精度(mm)宽展(%)自由尺寸范围(%)成材率(%)二辊轧制±0.25100%5%97%三辊轧制±0.1025%9%98%本工艺±0.0815%12%98.5%从上表中可以看出,采用实用新型相对于传统轧制设备,在圆钢产品的精度和成材率得到提高,并且宽展减小,道次变形效率高,节约生产能耗。任何熟悉此技术的人士皆可在不违背本实用新型的精神及范畴下,对上述实施例进行修饰或改变。因此,举凡所属
技术领域:
中具有通常知识者在未脱离本实用新型所揭示的精神与技术思想下所完成的一切等效修饰或改变,仍应由本实用新型的权利要求所涵盖。当前第1页1 2 3