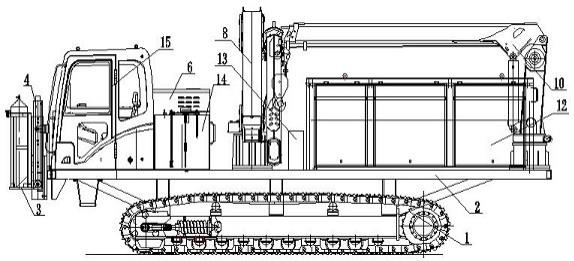
1.本实用新型涉及一种焊接装置,尤其是一种适用于带双起吊和双发动机的基于移动运动的焊接装置。
背景技术:2.在大口径、厚壁钢、高钢级长输管道的施工中,管道全位置自动焊是管道施工主要焊接方法,在施工现场组对焊接过程中,一般都采用了流水线作业。内焊(根焊)、热焊、填充焊、盖面焊有序进行,每一道焊接工序都需要配置一台焊接车为焊接作业供电及配电,因此基于移动运动的焊接装置是一种重要的焊接装置,在现有的基于移动运动的焊接装置中,还都是在每一道焊接工序都配置一台焊接车为焊接作业供电及配电,但在焊接过程中,还需要提供起吊作业、工具放置、气瓶及供气,从而满足管道焊接工序的需要,提高对管道焊接的效率,
3.基于申请人的技术交底书和背景技术中现有的技术问题、技术特征和技术效果,做出本发明的申请技术方案。
技术实现要素:4.本实用新型的客体是一种基于移动运动的焊接装置。
5.为了克服上述技术缺点,本实用新型的目的是提供一种基于移动运动的焊接装置,因此提高了对管道焊接的效率。
6.为达到上述目的,本实用新型采取的技术方案是:包含有用于作为移动载体的动力机动盘装置、设置在动力机动盘装置上并且用于放置储气瓶的气瓶架、设置在动力机动盘装置上并且用于放置电焊机的电焊机箱、设置在动力机动盘装置上并且用于作为搬运部件的起重机组、设置在动力机动盘装置上并且用于作为供电电源的发电发动机。
7.由于设计了动力机动盘装置、气瓶架、电焊机箱、起重机组和发电发动机,通过动力机动盘装置,实现了在管道施工现场的运动,通过气瓶架和电焊机箱,实现了对管道焊接用品的承载,通过起重机组,实现了对焊接部件的搬运,通过发电发动机,实现了对焊接的单独电源,方便了对管道焊接的操作,因此提高了对管道焊接的效率。
8.本实用新型设计了,按照对管道焊接用品的承载的方式把动力机动盘装置、气瓶架、电焊机箱、起重机组和发电发动机相互联接。
9.本实用新型设计了,按照对储气瓶和电焊机进行前后安置的方式把气瓶架和电焊机箱与动力机动盘、起重机组和发电发动机装置联接。
10.本实用新型设计了,动力机动盘装置设置为包含有底盘总成、平台总成、液压系统、行走发动机、柴油箱、驾驶室和液压油箱,
11.本实用新型设计了,起重机组设置为包含有折臂式随车起重机或直臂式随车起重机。
12.本实用新型设计了,还包含有第一附件装置并且第一附件装置设置在动力机动盘
装置上,第一附件装置设置为包含有配电柜。
13.本实用新型设计了,还包含有第二附件装置并且第二附件装置设置在气瓶架上,第二附件装置设置为气瓶架油缸。
14.本实用新型设计了,在底盘总成上设置有平台总成,在平台总成上分别设置有气瓶架、液压系统、行走发动机、折臂式随车起重机、发电发动机、直臂式随车起重机、电焊机箱、配电柜、柴油箱、驾驶室和液压油箱并且在气瓶架上设置有气瓶架油缸。
15.本实用新型设计了,底盘总成设置为具有履带部件和压轮部件的全液压驱动的履带底盘,履带部件设置为与底盘总成的机架联接并且压轮部件设置在底盘总成的机架与履带部件之间,履带部件设置为具有盘轮的900mm三角湿地履带板并且压轮部件设置为具有九个盘轮的排轮装置,底盘总成的机架设置为与平台总成联接并且底盘总成的操纵装置设置为与液压系统联接。
16.本实用新型设计了,平台总成设置为第一斜梁部、第一横梁部、第二横梁部、第三横梁部、第二斜梁部和板部并且第一斜梁部的下端头、第一横梁部的下端头、第二横梁部的下端头、第三横梁部的下端头和第二斜梁部的下端头分别设置为与底盘总成的机架联接,第一斜梁部的下端头、第一横梁部的上端头、第二横梁部的上端头、第三横梁部的上端头和第二斜梁部的上端头分别设置为与板部的机架联接,板部的前端端面部设置为与气瓶架联接并且板部的上端端面部分别设置为与液压系统、行走发动机、折臂式随车起重机、发电发动机、直臂式随车起重机、电焊机箱、配电柜、柴油箱、驾驶室和液压油箱联接,第一斜梁部、第一横梁部、第二横梁部、第三横梁部和第二斜梁部分别设置为[字形矩形棒状体并且第一斜梁部、第一横梁部、第二横梁部、第三横梁部和第二斜梁部设置为沿板部的横向中心线依次间隔排列分布,第一斜梁部和第二斜梁部设置为呈八字形分布,板部设置为矩形片状体。
17.本实用新型设计了,气瓶架设置为包含有托架部、固定架部和插板部并且托架部的后端端面部设置为与固定架部滑动式联接,托架部的前端端面部设置为与插板部插接式联接并且托架部设置为与平台总成联接,托架部的后端端面上端部和固定架部的下端端端面部分别设置为通过耳座和销轴与气瓶架油缸,托架部设置为l字形架状体并且托架部的横部设置为与储气瓶托接式联接,托架部的竖部设置为与固定架部嵌入式联接并且在托架部的竖部下端头设置有耳座,托架部的横部的前后侧板设置为与插板部接触式联接并且托架部的横部的外端开口槽体设置为与插板部的下端端面部容纳式联接,固定架部设置为u字形板状体并且固定架部的侧面板设置为与托架部接触式联接,在固定架部的竖部上端头设置有耳座并且插板部设置为l字形片状体,插板部的上端横部设置为通过螺栓与托架部的横部的前后侧板联接。
18.本实用新型设计了,气瓶架油缸的端头分别设置为通过销轴与气瓶架联接并且气瓶架油缸的液压端口部设置为与液压系统联接,气瓶架油缸设置为两节式伸缩缸。
19.本实用新型设计了,驾驶室设置为偏置式驾驶室并且驾驶室的下端端面部设置为与平台总成联接,驾驶室设置为与底盘总成的操纵装置容纳式联接。
20.本实用新型设计了,液压油箱设置为矩形盒状体并且液压油箱的下端端面部设置为与平台总成联接,液压油箱的输出端口部设置为与液压系统联接。
21.本实用新型设计了,液压系统设置为包含有液压泵、插装阀组、油源阀、过滤器和电磁阀并且液压泵的输入端口部设置为通过过滤器与油源阀的其中一个端口部联接,油源
阀的控制端口部设置为与电磁阀联接并且油源阀的其中另一个端口部设置为与液压油箱联接,液压泵的输出端口部设置为与插装阀组的其中一个端口部联接,插装阀组的其中另一个端口部分别设置为与底盘总成、气瓶架油缸、折臂式随车起重机和直臂式随车起重机联接并且液压泵的动力轴设置为与行走发动机的端轴联接,液压泵的下端端面部设置为与平台总成联接并且插装阀组的壳体、油源阀的壳体和过滤器的壳体设置为与液压泵联接,电磁阀的壳体设置为与油源阀的壳体联接。
22.本实用新型设计了,柴油箱设置为矩形盒状体并且柴油箱的下端端面部设置为与平台总成联接,柴油箱的输出端口部设置为与发电发动机联接。
23.本实用新型设计了,行走发动机设置为动力柴油或汽油机并且行走发动机的下端端面部设置为与平台总成联接,行走发动机的输入端口部设置为与柴油箱联接并且行走发动机的端轴设置为与液压系统联接。
24.本实用新型设计了,折臂式随车起重机设置为包含有第一主机、第一操作阀门组和第二操作阀门组并且第一主机的下端端面部、第一操作阀门组和第二操作阀门组分别设置为与平台总成联接,第一操作阀门组的端口部和第二操作阀门组的端口部分别设置为与第一主机的液压动力端口部和液压系统的输出端口部联接。
25.本实用新型设计了,发电发动机设置为包含有动力机、发电机、电瓶、水箱和配电箱并且动力机的端轴设置为与发电机的动力轴联接,动力机的冷却端口部设置为与水箱联接并且动力机的电源接口部设置为电源开关与电瓶联接,发电机的输出接口部设置为通过线缆与配电箱联接并且配电箱设置为通过线缆与配电柜联接,动力机的动力油液端口部设置为与柴油箱调节,动力机的下端端面部、发电机的下端端面部、电瓶的下端端面部和水箱的下端端面部分别设置为与平台总成联接并且配电箱设置为与发电机联接。
26.本实用新型设计了,直臂式随车起重机设置为第二主机和第三操作阀门组并且第二主机的下端端面部和第三操作阀门组分别设置为与平台总成联接,第三操作阀门组的端口部分别设置为与第二主机的液压动力端口部和液压系统的输出端口部联接。
27.本实用新型设计了,电焊机箱设置为矩形盒状体并且电焊机箱的下端端面部设置为与平台总成联接,电焊机箱设置为与电焊机容纳式联接。
28.本实用新型设计了,配电柜的下端端面部设置为与平台总成联接并且配电柜的输入端口部设置为通过线缆与发电发动机的输出端口部联接,配电柜的输出端口部设置为通过线缆与电焊机的电源端口部联接。
29.本实用新型设计了,气瓶架和电焊机箱与底盘总成、平台总成、液压系统、行走发动机、折臂式随车起重机、发电发动机、直臂式随车起重机、配电柜、柴油箱、驾驶室和液压油箱设置为按照前后排列分布并且气瓶架、电焊机箱、底盘总成、平台总成、液压系统、行走发动机、折臂式随车起重机、发电发动机、直臂式随车起重机、配电柜、柴油箱、驾驶室和液压油箱与气瓶架油缸设置为按照升降放置的方式分布,底盘总成的中心线、平台总成的中心线、折臂式随车起重机的中心线和直臂式随车起重机的中心线设置在同一条直线上,液压系统、驾驶室和液压油箱设置为沿平台总成的第一条竖向线间隔排列分布并且液压油箱设置在液压系统和驾驶室之间,行走发动机和柴油箱设置为沿平台总成的第二条竖向线间隔排列分布,第一主机、第一操作阀门组和第二操作阀门组设置为沿平台总成的第三条竖向线间隔排列分布并且第一主机设置在第一操作阀门组和第二操作阀门组之间,发电发动
机、直臂式随车起重机和电焊机箱设置为沿平台总成的第四条竖向线间隔排列分布并且直臂式随车起重机设置在发电发动机和电焊机箱之间,配电柜设置在第二操作阀门组和电焊机箱之间并且第三操作阀门组设置在板部的后端端面部,第二主机、第三操作阀门组、第一主机、第一操作阀门组、第二操作阀门组、动力机、发电机、电瓶、水箱、液压泵和固定架部分别设置为与板部联接。
30.本实用新型设计了,在平台总成上分别设置有气瓶架、液压系统、行走发动机、折臂式随车起重机、发电发动机、电焊机箱、配电柜、柴油箱、驾驶室和液压油箱。
31.本实用新型设计了,底盘总成设置为具有履带部件、压轮部件和涨紧部件的全液压驱动的履带底盘,履带部件设置为与底盘总成的机架联接并且压轮部件设置在底盘总成的机架与履带部件之间,在履带部件和压轮部件之间设置有涨紧部件,履带部件设置为具有齿轮的600mm三筋履带板、700mm三筋履带板或800mm三筋履带板并且压轮部件设置为具有九个盘轮的排轮装置,底盘总成的机架设置为与平台总成联接并且底盘总成的操纵装置设置为与液压系统联接。
32.本实用新型设计了,涨紧部件设置为套板部、连接螺杆132、串杆和弹簧并且串杆的其中一个端头设置为通过连接螺杆132与套板部的内端头联接,弹簧设置为与串杆贯串式联接并且弹簧的其中一个端头设置为与串杆联接,弹簧的其中另一个端头和串杆的其中另一个端头分别设置为与压轮部件联接并且套板部的外端头设置为与履带部件的齿轮轴联接。
33.本实用新型设计了,平台总成设置为第一斜梁部、第一横梁部、第二横梁部、第三横梁部和第二斜梁部并且第一斜梁部的下端头、第一横梁部的下端头、第二横梁部的下端头、第三横梁部的下端头和第二斜梁部的下端头分别设置为与底盘总成的机架联接,第一斜梁部的前端端面部设置为与气瓶架联接并且第一斜梁部的上端端面部、第一横梁部的上端端面部、第二横梁部的上端端面部、第三横梁部的上端端面部和第二斜梁部的上端端面部分别设置为与液压系统、行走发动机、折臂式随车起重机、发电发动机、电焊机箱、配电柜、柴油箱、驾驶室和液压油箱联接,第一斜梁部、第一横梁部、第二横梁部、第三横梁部和第二斜梁部分别设置为[字形矩形棒状体并且第一斜梁部、第一横梁部、第二横梁部、第三横梁部和第二斜梁部设置为沿板部的横向中心线依次间隔排列分布,第一斜梁部和第二斜梁部设置为呈八字形分布。
34.本实用新型的技术效果在于:通过动力机动盘装置,实现了在管道施工现场的运动及发电并供电,通过折臂式随车起重机和直臂式随车起重机,实现了管道焊接辅具及焊接设备的同时起吊。本套装置具有行走、发电、供电、焊接、起吊、帯载行走等多种功能,即节省了管道施工的设备,方便了管道焊接的操作,又提高了管道焊接的效率,双发动机系统分为行走动力系统和发电动力系统两个独立系统,互不干涉。行走动力专门供行走系统,用于整机的转场、行走等。整机移动到指定工作位置后,可熄灭也可正常运行行走发动机。需要作业时可直接启动发电机组发动机进行发电作业或随车吊作业。运用发电动力系统进行发电作业稳定,电流电压不受外界影响。双发动机系统使得发动机运行时间减少,延长整机使用寿命,延长发动机保养周期。
35.在本技术方案中,气瓶架和电焊机箱是基础部件,也是本实用新型的必要技术特征,底盘总成、平台总成、气瓶架油缸、液压系统、行走发动机、折臂式随车起重机、发电发动
机、直臂式随车起重机、配电柜、柴油箱、驾驶室和液压油箱是功能部件,是实现本实用新型的其它技术效果的特征,履带部件、压轮部件、第一斜梁部、第一横梁部、第二横梁部、第三横梁部、第二斜梁部、板部、托架部、固定架部插板部、液压泵、插装阀组、油源阀、过滤器、电磁阀、动力机、发电机、电瓶、水箱、配电箱、第一主机、第一操作阀门组、第二操作阀门组、第二主机、第三操作阀门组、涨紧部件、套板部、连接螺杆132、串杆和弹簧这些技术特征的设计,是符合专利法及其实施细则的技术特征。
36.在本技术方案中,对管道焊接用品的承载的动力机动盘装置、气瓶架和电焊机箱为重要技术特征,在基于移动运动的焊接装置的技术领域中,具有新颖性、创造性和实用性,在本技术方案中的术语都是可以用本技术领域中的专利文献进行解释和理解。
附图说明
37.为了更清楚地说明本实用新型实施例或现有技术中的技术方案,下面将对实施例或现有技术描述中所需要使用的附图作简单地介绍,显而易见地,下面描述中的附图仅仅是本实用新型的一些实施例,对于本领域普通技术人员来讲,在不付出创造性劳动的前提下,还可以根据这些附图获得其他的附图。
38.图1为本实用新型的第一个实施例之一的示意图,
39.图2为图1的俯视图,
40.图3为图1的右视图,
41.图4为本实用新型的第一个实施例之一的底盘总成 1和平台总成2的连接关系示意图,
42.图5为本实用新型的第一个实施例之二的示意图,
43.图6为本实用新型的第一个实施例之二的底盘总成 1和平台总成2的连接关系示意图,
44.底盘总成
ꢀ‑
1、平台总成
‑
2、气瓶架
‑
3、气瓶架油缸
‑
4、液压系统
‑
5、行走发动机
‑
6、折臂式随车起重机
‑
8、发电发动机
‑
9、直臂式随车起重机
‑
10、电焊机箱
‑
12、配电柜
‑
13、柴油箱
‑
14、驾驶室
‑
15、液压油箱
‑
16、履带部件
‑
11、压轮部件
‑
121、第一斜梁部
‑
21、第一横梁部
‑
22、第二横梁部
‑
23、第三横梁部
‑
24、第二斜梁部
‑
25、板部
‑
26、托架部
‑
31、固定架部
‑
32、插板部
‑
33、
45.液压泵
‑
51、插装阀组
‑
52、油源阀
‑
53、过滤器
‑
54、电磁阀
‑
55、动力机
‑
91、发电机
‑
92、电瓶
‑
93、水箱
‑
94、配电箱
‑
95、第一主机
‑
81、第一操作阀门组
‑
82、第二操作阀门组
‑
83、第二主机
‑
101、第三操作阀门组
‑
102、涨紧部件
‑
130、套板部
‑
131、连接螺杆
‑
132、串杆
‑
133、弹簧
‑
134。
具体实施方式
46.根据审查指南,对本实用新型所使用的诸如“具有”、“包含”以及“包括”术语应当理解为不配出一个或多个其它元件或其组合的存在或添加。
47.在本实用新型的描述中,需要说明的是,术语“中心”、“上”、“下”、“左”、“右”、“竖直”、“水平”、“内”、“外”等指示的方位或位置关系为基于附图所示的方位或位置关系,仅是为了便于描述本实用新型和简化描述,而不是指示或暗示所指的装置或元件必须具有特定
的方位、以特定的方位构造和操作,因此不能理解为对本实用新型的限制。此外,术语“第一”、“第二”、“第三”仅用于描述目的,而不能理解为指示或暗示相对重要性。
48.在本实用新型的描述中,需要说明的是,除非另有明确的规定和限定,术语“安装”、“相连”、“连接”应做广义理解,例如,可以是固定连接,也可以是可拆卸连接,或一体地连接;可以是机械连接,也可以是电连接;可以是直接相连,也可以通过中间媒介间接相连,可以是两个元件内部的连通。对于本领域的普通技术人员而言,可以具体情况理解上述术语在本实用新型中的具体含义。
49.此外,下面所描述的本实用新型不同实施方式中所涉及的技术特征只要彼此之间未构成冲突就可以相互结合,另外,除非特别说明,在下面的实施例中所采用的设备和材料均是市售可得的,如没有明确说明处理条件,请参考购买的产品说明书或者按照本领域常规方法进。
50.下面将结合本实用新型实施例中的附图,对本实用新型实施例中的技术方案进行清楚、完整地描述,显然,所描述的实施例仅仅是本实用新型一部分实施例,而不是全部的实施例。基于本实用新型中的实施例,本领域普通技术人员在没有做出创造性劳动前提下所获得的所有其他实施例,都属于本实用新型保护的范围。
51.图1为本实用新型的第一个实施例之一,结合附图具体说明本实施例,包含有底盘总成 1、平台总成2、气瓶架3、气瓶架油缸4、液压系统5、行走发动机6、折臂式随车起重机8、发电发动机9、直臂式随车起重机 10、电焊机箱12、配电柜13、柴油箱14、驾驶室15和液压油箱16并且在底盘总成 1上设置有平台总成2,在平台总成2上分别设置有气瓶架3、液压系统5、行走发动机6、折臂式随车起重机8、发电发动机9、直臂式随车起重机 10、电焊机箱12、配电柜13、柴油箱14、驾驶室15和液压油箱16并且在气瓶架3上设置有气瓶架油缸4。
52.在本实施例中,底盘总成 1设置为具有履带部件11和压轮部件121的全液压驱动的履带底盘,履带部件11设置为与底盘总成 1的机架联接并且压轮部件121设置在底盘总成 1的机架与履带部件11之间,履带部件11设置为具有盘轮的900mm三角湿地履带板并且压轮部件121设置为具有九个盘轮的排轮装置,底盘总成 1的机架设置为与平台总成2联接并且底盘总成 1的操纵装置设置为与液压系统5联接。
53.通过底盘总成 1,形成了对平台总成2和液压系统5的支撑连接点,由底盘总成 1,实现了与平台总成2的连接,实现了与液压系统5的连接,由履带部件11和压轮部件121,实现了在沼泽湿地进行行走,其技术目的在于:用于作为平台总成2的支撑载体。
54.在本实施例中,平台总成2设置为第一斜梁部21、第一横梁部22、第二横梁部23、第三横梁部24、第二斜梁部25和板部26并且第一斜梁部21的下端头、第一横梁部22的下端头、第二横梁部23的下端头、第三横梁部24的下端头和第二斜梁部25的下端头分别设置为与底盘总成 1的机架联接,第一斜梁部21的下端头、第一横梁部22的上端头、第二横梁部23的上端头、第三横梁部24的上端头和第二斜梁部25的上端头分别设置为与板部26的机架联接,板部26的前端端面部设置为与气瓶架3联接并且板部26的上端端面部分别设置为与液压系统5、行走发动机6、折臂式随车起重机8、发电发动机9、直臂式随车起重机 10、电焊机箱12、配电柜13、柴油箱14、驾驶室15和液压油箱16联接,第一斜梁部21、第一横梁部22、第二横梁部23、第三横梁部24和第二斜梁部25分别设置为[字形矩形棒状体并且第一斜梁部21、第一横梁部22、第二横梁部23、第三横梁部24和第二斜梁部25设置为沿板部26的横向中心线依
次间隔排列分布,第一斜梁部21和第二斜梁部25设置为呈八字形分布,板部26设置为矩形片状体。
55.通过平台总成2,形成了对底盘总成 1、气瓶架3、液压系统5、行走发动机6、折臂式随车起重机8、发电发动机9、直臂式随车起重机 10、电焊机箱12、配电柜13、柴油箱14、驾驶室15和液压油箱16的支撑连接点,由底盘总成 1,实现了与底盘总成 1的连接,实现了与气瓶架3的连接,实现了与液压系统5的连接,实现了与行走发动机6的连接,实现了与折臂式随车起重机8的连接,实现了与发电发动机9的连接,实现了与直臂式随车起重机 10的连接,实现了与电焊机箱12的连接,实现了与配电柜13的连接,实现了与柴油箱14的连接,实现了与驾驶室15的连接,实现了与液压油箱16的连接,其技术目的在于:用于作为气瓶架3、液压系统5、行走发动机6、折臂式随车起重机8、发电发动机9、直臂式随车起重机 10、电焊机箱12、配电柜13、柴油箱14、驾驶室15和液压油箱16的支撑载体。
56.在本实施例中,气瓶架3设置为包含有托架部31、固定架部32和插板部33并且托架部31的后端端面部设置为与固定架部32滑动式联接,托架部31的前端端面部设置为与插板部33插接式联接并且托架部31设置为与平台总成2联接,托架部31的后端端面上端部和固定架部32的下端端端面部分别设置为通过耳座和销轴与气瓶架油缸4,托架部31设置为l字形架状体并且托架部31的横部设置为与储气瓶托接式联接,托架部31的竖部设置为与固定架部32嵌入式联接并且在托架部31的竖部下端头设置有耳座,托架部31的横部的前后侧板设置为与插板部33接触式联接并且托架部31的横部的外端开口槽体设置为与插板部33的下端端面部容纳式联接,固定架部32设置为u字形板状体并且固定架部32的侧面板设置为与托架部31接触式联接,在固定架部32的竖部上端头设置有耳座并且插板部33设置为l字形片状体,插板部33的上端横部设置为通过螺栓与托架部31的横部的前后侧板联接。
57.通过气瓶架3,形成了对平台总成2和气瓶架油缸4的支撑连接点,由固定架部32,实现了与平台总成2的连接,由托架部31和固定架部32,实现了与气瓶架油缸4的连接,由插板部33,实现了对托架部31的横部处于开放状态处理,其技术目的在于:用于作为储气瓶的支撑载体。
58.在本实施例中,气瓶架油缸4的端头分别设置为通过销轴与气瓶架3联接并且气瓶架油缸4的液压端口部设置为与液压系统5联接,气瓶架油缸4设置为两节式伸缩缸。
59.通过气瓶架油缸4,形成了对气瓶架3和液压系统5的支撑连接点,由气瓶架油缸4,实现了与气瓶架3的连接,实现了与液压系统5的连接,其技术目的在于:用于作为带动储气瓶进行升降的部件。
60.在本实施例中,驾驶室15设置为偏置式驾驶室并且驾驶室15的下端端面部设置为与平台总成2联接,驾驶室15设置为与底盘总成 1的操纵装置容纳式联接。
61.通过驾驶室15,形成了对底盘总成 1和平台总成2的支撑连接点,由驾驶室15,实现了与底盘总成 1的连接,实现了与平台总成2的连接,其技术目的在于:用于作为底盘总成 1的操纵装置的支撑载体。
62.在本实施例中,液压油箱16设置为矩形盒状体并且液压油箱16的下端端面部设置为与平台总成2联接,液压油箱16的输出端口部设置为与液压系统5联接。
63.通过液压油箱16,形成了对平台总成2和液压系统5的支撑连接点,由液压油箱16,实现了与平台总成2的连接,实现了与液压系统5的连接,其技术目的在于:用于作为对高压
液体进行储存的部件。
64.在本实施例中,液压系统5设置为包含有液压泵51、插装阀组52、油源阀53、过滤器54和电磁阀55并且液压泵51的输入端口部设置为通过过滤器54与油源阀53的其中一个端口部联接,油源阀53的控制端口部设置为与电磁阀55联接并且油源阀53的其中另一个端口部设置为与液压油箱16联接,液压泵51的输出端口部设置为与插装阀组52的其中一个端口部联接,插装阀组52的其中另一个端口部分别设置为与底盘总成 1、气瓶架油缸4、折臂式随车起重机8和直臂式随车起重机 10联接并且液压泵51的动力轴设置为与行走发动机6的端轴联接,液压泵51的下端端面部设置为与平台总成2联接并且插装阀组52的壳体、油源阀53的壳体和过滤器54的壳体设置为与液压泵51联接,电磁阀55的壳体设置为与油源阀53的壳体联接。
65.通过液压系统5,形成了对底盘总成 1、平台总成2、气瓶架油缸4、折臂式随车起重机8和直臂式随车起重机 10的支撑连接点,由液压泵51,实现了与平台总成2的连接,由插装阀组52,实现了与底盘总成 1的连接,实现了与气瓶架油缸4的连接,实现了与折臂式随车起重机8的连接,实现了与直臂式随车起重机 10的连接,由油源阀53、过滤器54和电磁阀55,实现了液压泵51与液压油箱16之间进行连接处理,其技术目的在于:用于作为对产生输出高压液体的部件。
66.在本实施例中,柴油箱14设置为矩形盒状体并且柴油箱14的下端端面部设置为与平台总成2联接,柴油箱14的输出端口部设置为与发电发动机9联接。
67.通过柴油箱14,形成了对平台总成2和发电发动机9的支撑连接点,由柴油箱14,实现了与平台总成2的连接,实现了与发电发动机9的连接,其技术目的在于:用于作为对发电发动机9的动力油液进行储存的部件。
68.在本实施例中,行走发动机6设置为动力柴油或汽油机并且行走发动机6的下端端面部设置为与平台总成2联接,行走发动机6的输入端口部设置为与柴油箱14联接并且行走发动机6的端轴设置为与液压系统5联接。
69.通过行走发动机6,形成了对平台总成2、液压系统5和柴油箱14的支撑连接点,由行走发动机6,实现了与平台总成2的连接,实现了与液压系统5的连接,实现了与柴油箱14的连接,其技术目的在于:用于作为带动液压系统5进行工作的动力部件。
70.在本实施例中,折臂式随车起重机8设置为包含有第一主机81、第一操作阀门组82和第二操作阀门组83并且第一主机81的下端端面部、第一操作阀门组82和第二操作阀门组83分别设置为与平台总成2联接,第一操作阀门组82的端口部和第二操作阀门组83的端口部分别设置为与第一主机81的液压动力端口部和液压系统5的输出端口部联接。
71.通过折臂式随车起重机8,形成了对平台总成2和液压系统5的支撑连接点,由第一主机81、第一操作阀门组82和第二操作阀门组83,实现了与平台总成2的连接,由第一操作阀门组82和第二操作阀门组83,实现了与液压系统5的连接,其技术目的在于:用于作为对防风棚进行起吊的部件。
72.在本实施例中,发电发动机9设置为包含有动力机91、发电机92、电瓶93、水箱94和配电箱95并且动力机91的端轴设置为与发电机92的动力轴联接,动力机91的冷却端口部设置为与水箱94联接并且动力机91的电源接口部设置为电源开关与电瓶93联接,发电机92的输出接口部设置为通过线缆与配电箱95联接并且配电箱95设置为通过线缆与配电柜13联
接,动力机91的动力油液端口部设置为与柴油箱14调节,动力机91的下端端面部、发电机92的下端端面部、电瓶93的下端端面部和水箱94的下端端面部分别设置为与平台总成2联接并且配电箱95设置为与发电机92联接。
73.通过发电发动机9,形成了对平台总成2、配电柜13、柴油箱14的支撑连接点,由动力机91、发电机92、电瓶93和水箱94,实现了与平台总成2的连接,由配电箱95,实现了与配电柜13的连接,由动力机91,实现了与柴油箱14的连接,其技术目的在于:用于作为对配电柜13进行供电的部件。
74.在本实施例中,直臂式随车起重机 10设置为第二主机101和第三操作阀门组102并且第二主机101的下端端面部和第三操作阀门组102分别设置为与平台总成2联接,第三操作阀门组102的端口部分别设置为与第二主机101的液压动力端口部和液压系统5的输出端口部联接。
75.通过直臂式随车起重机 10,形成了对平台总成2和液压系统5的支撑连接点,由第二主机101和第三操作阀门组102,实现了与平台总成2的连接,由第三操作阀门组102,实现了与液压系统5的连接,其技术目的在于:用于作为对加热带进行起吊的部件。
76.在本实施例中,电焊机箱12设置为矩形盒状体并且电焊机箱12的下端端面部设置为与平台总成2联接,电焊机箱12设置为与电焊机容纳式联接。
77.通过电焊机箱12,形成了对平台总成2的支撑连接点,由电焊机箱12,实现了与平台总成2的连接,其技术目的在于:用于作为对电焊机进行盛放的部件。
78.在本实施例中,配电柜13的下端端面部设置为与平台总成2联接并且配电柜13的输入端口部设置为通过线缆与发电发动机9的输出端口部联接,配电柜13的输出端口部设置为通过线缆与电焊机的电源端口部联接。
79.通过配电柜13,形成了对平台总成2和发电发动机9的支撑连接点,由配电柜13,实现了与平台总成2的连接,实现了与发电发动机9的连接,其技术目的在于:用于作为对电焊机进行供电的部件。
80.在本实施例中,气瓶架3和电焊机箱12与底盘总成 1、平台总成2、液压系统5、行走发动机6、折臂式随车起重机8、发电发动机9、直臂式随车起重机 10、配电柜13、柴油箱14、驾驶室15和液压油箱16设置为按照前后排列分布并且气瓶架3、电焊机箱12、底盘总成 1、平台总成2、液压系统5、行走发动机6、折臂式随车起重机8、发电发动机9、直臂式随车起重机 10、配电柜13、柴油箱14、驾驶室15和液压油箱16与气瓶架油缸4设置为按照升降放置的方式分布,底盘总成1的中心线、平台总成2的中心线、折臂式随车起重机8的中心线和直臂式随车起重机 10的中心线设置在同一条直线上,液压系统5、驾驶室15和液压油箱16设置为沿平台总成2的第一条竖向线间隔排列分布并且液压油箱16设置在液压系统5和驾驶室15之间,行走发动机6和柴油箱14设置为沿平台总成2的第二条竖向线间隔排列分布,第一主机81、第一操作阀门组82和第二操作阀门组83设置为沿平台总成2的第三条竖向线间隔排列分布并且第一主机81设置在第一操作阀门组82和第二操作阀门组83之间,发电发动机9、直臂式随车起重机 10和电焊机箱12设置为沿平台总成2的第四条竖向线间隔排列分布并且直臂式随车起重机 10设置在发电发动机9和电焊机箱12之间,配电柜13设置在第二操作阀门组83和电焊机箱12之间并且第三操作阀门组102设置在板部26的后端端面部,第二主机101、第三操作阀门组102、第一主机81、第一操作阀门组82、第二操作阀门组83、动力机
91、发电机92、电瓶93、水箱94、液压泵51和固定架部32分别设置为与板部26联接。
81.在进行管道进行焊接时,把电焊机安装在电焊机箱12中,把电焊机的电源端口部通过线缆与配电柜13连接,
82.启动行走发动机6,使液压泵51处于工作状态,使油源阀53和电磁阀55处于开通状态,液压油箱16中的高压液体通过液压泵51后,由插装阀组52输出高压动力液体,
83.通过电瓶93启动动力机91,动力机91带动发电机92进行工作,发电机92产生的电能通过配电箱95传输到配电柜13中,作为电焊机的供电电源,使电焊机处于工作状态,
84.通过插装阀组52,使气瓶架油缸4处于伸长状态,把托架部31处于低位,把位于插板部33的上端横部与托架部31的横部的前后侧板上的螺栓松开,把插板部33与托架部31分开,把储气瓶放到托架部31上,再把插板部33与托架部31安装,把位于插板部33的上端横部与托架部31的横部的前后侧板上的螺栓拧紧,再使气瓶架油缸4处于收缩状态,把储气瓶进行提起,
85.通过插装阀组52,使第一操作阀门组82和第二操作阀门组83处于工作状态,通过第一操作阀门组82和第二操作阀门组83,使第一主机81处于工作状态,
86.通过插装阀组52,使第三操作阀门组102处于工作状态,通过第三操作阀门组102,使第二主机101处于工作状态,
87.通过插装阀组52,使底盘总成 1的操纵装置处于工作状态,实现对底盘总成 1的行驶操纵。
88.图5为本实用新型的第一个实施例之二,结合附图具体说明本实施例,包含有底盘总成 1、平台总成2、气瓶架3、气瓶架油缸4、液压系统5、行走发动机6、折臂式随车起重机8、发电发动机9、电焊机箱12、配电柜13、柴油箱14、驾驶室15和液压油箱16并且在平台总成2上分别设置有气瓶架3、液压系统5、行走发动机6、折臂式随车起重机8、发电发动机9、电焊机箱12、配电柜13、柴油箱14、驾驶室15和液压油箱16。
89.在本实施例中,底盘总成 1设置为具有履带部件11、压轮部件121和涨紧部件130的全液压驱动的履带底盘,履带部件11设置为与底盘总成 1的机架联接并且压轮部件121设置在底盘总成 1的机架与履带部件11之间,在履带部件11和压轮部件121之间设置有涨紧部件130,履带部件11设置为具有齿轮的600mm三筋履带板、700mm三筋履带板或800mm三筋履带板并且压轮部件121设置为具有九个盘轮的排轮装置,底盘总成 1的机架设置为与平台总成2联接并且底盘总成 1的操纵装置设置为与液压系统5联接。
90.通过底盘总成 1,形成了对平台总成2和液压系统5的支撑连接点,由底盘总成 1,实现了与平台总成2的连接,实现了与液压系统5的连接,由履带部件11和压轮部件121,实现了在干燥地进行行走,其技术目的在于:用于作为平台总成2的支撑载体。
91.在本实施例中,涨紧部件130设置为套板部131、连接螺杆132、串杆133和弹簧134并且串杆133的其中一个端头设置为通过连接螺杆132与套板部131的内端头联接,弹簧134设置为与串杆133贯串式联接并且弹簧134的其中一个端头设置为与串杆133联接,弹簧134的其中另一个端头和串杆133的其中另一个端头分别设置为与压轮部件121联接并且套板部131的外端头设置为与履带部件11的齿轮轴联接。
92.由涨紧部件130,实现了与履带部件11的连接,实现了与压轮部件121的连接,其技术目的在于:用于作为履带部件11的齿轮轴进行涨紧的部件。
93.在本实施例中,平台总成2设置为第一斜梁部21、第一横梁部22、第二横梁部23、第三横梁部24和第二斜梁部25并且第一斜梁部21的下端头、第一横梁部22的下端头、第二横梁部23的下端头、第三横梁部24的下端头和第二斜梁部25的下端头分别设置为与底盘总成 1的机架联接,第一斜梁部21的前端端面部设置为与气瓶架3联接并且第一斜梁部21的上端端面部、第一横梁部22的上端端面部、第二横梁部23的上端端面部、第三横梁部24的上端端面部和第二斜梁部25的上端端面部分别设置为与液压系统5、行走发动机6、折臂式随车起重机8、发电发动机9、电焊机箱12、配电柜13、柴油箱14、驾驶室15和液压油箱16联接,第一斜梁部21、第一横梁部22、第二横梁部23、第三横梁部24和第二斜梁部25分别设置为[字形矩形棒状体并且第一斜梁部21、第一横梁部22、第二横梁部23、第三横梁部24和第二斜梁部25设置为沿板部26的横向中心线依次间隔排列分布,第一斜梁部21和第二斜梁部25设置为呈八字形分布。
94.由第一斜梁部21、第一横梁部22、第二横梁部23、第三横梁部24和第二斜梁部25,实现了与底盘总成 1的连接,实现了与气瓶架3的连接,实现了与液压系统5的连接,实现了与行走发动机6的连接,实现了与折臂式随车起重机8的连接,实现了与发电发动机9的连接,实现了与电焊机箱12的连接,实现了与配电柜13的连接,实现了与柴油箱14的连接,实现了与驾驶室15的连接,实现了与液压油箱16的连接,其技术目的在于:用于作为气瓶架3、液压系统5、行走发动机6、折臂式随车起重机8、发电发动机9、电焊机箱12、配电柜13、柴油箱14、驾驶室15和液压油箱16的支撑载体。
95.通过连接螺杆132,调节套板部131和串杆133之间的距离,实现对履带部件11的齿轮的横向位置调节。
96.本实用新型的第二个实施例,按照对管道焊接用品的承载的方式把动力机动盘装置、气瓶架3、电焊机箱12、起重机组和发电发动机9相互联接。
97.在本实施例中,按照对储气瓶和电焊机进行前后安置的方式把气瓶架3和电焊机箱12与动力机动盘、起重机组和发电发动机9装置联接。
98.在本实施例中,动力机动盘装置设置为包含有底盘总成 1、平台总成2、液压系统5、行走发动机6、柴油箱14、驾驶室15和液压油箱16,
99.在本实施例中,起重机组设置为包含有折臂式随车起重机8或直臂式随车起重机 10。
100.在本实施例中,还包含有第一附件装置并且第一附件装置设置在动力机动盘装置上,第一附件装置设置为包含有配电柜13。
101.在本实施例中,还包含有第二附件装置并且第二附件装置设置在气瓶架3上,第二附件装置设置为气瓶架油缸4。
102.本实用新型的第二个实施例是以第一个实施例为基础,
103.本实用新型具有下特点:
104.1、由于设计了动力机动盘装置、气瓶架3、电焊机箱12、起重机组和发电发动机9,通过动力机动盘装置,实现了在管道施工现场的运动,通过气瓶架3和电焊机箱12,实现了对管道焊接用品的承载,通过起重机组,实现了对焊接部件的搬运,通过发电发动机9,实现了对焊接的单独电源,方便了对管道焊接的操作,因此提高了对管道焊接的效率。
105.2、由于设计了底盘总成 1、平台总成2、液压系统5、行走发动机6、柴油箱14、驾驶
室15和液压油箱16,实现了液压驱动运动。
106.3、由于设计了发电发动机9和配电柜13,实现了随车供电设置。
107.4、由于设计了气瓶架油缸4,实现了对储气瓶的提升储存。
108.5、由于设计了折臂式随车起重机8或直臂式随车起重机 10,实现了对随车起重机组的设置。
109.6、由于设计了对结构形状进行了数值范围的限定,使数值范围为本实用新型的技术方案中的技术特征,不是通过公式计算或通过有限次试验得出的技术特征,试验表明该数值范围的技术特征取得了很好的技术效果。
110.7、由于设计了本实用新型的技术特征,在技术特征的单独和相互之间的集合的作用,通过试验表明,本实用新型的各项性能指标为现有的各项性能指标的至少为1.7倍,通过评估具有很好的市场价值。
111.还有其它的与对管道焊接用品的承载的动力机动盘装置、气瓶架3和电焊机箱12联接的技术特征都是本实用新型的实施例之一,并且以上所述实施例的各技术特征可以进行任意的组合,为满足专利法、专利实施细则和审查指南的要求,不再对上述实施例中的各个技术特征所有可能的组合的实施例都进行描述。
112.因此在基于移动运动的焊接装置技术领域内,凡是包含有用于作为移动载体的动力机动盘装置、设置在动力机动盘装置上并且用于放置储气瓶的气瓶架3、设置在动力机动盘装置上并且用于放置电焊机的电焊机箱12、设置在动力机动盘装置上并且用于作为搬运部件的起重机组、设置在动力机动盘装置上并且用于作为供电电源的发电发动机9的技术内容都在本实用新型的保护范围内。