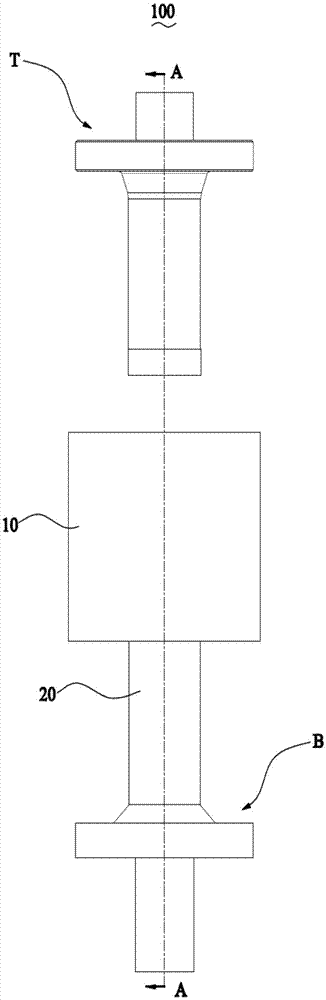
本发明属于一种粉末成型设备及其方法,特别涉及一种粉末填充模具单元及填充方法。
背景技术:
:粉末填充是粉末成型中的重要环节。在粉末填充时,将粉末混合物可控并可调节地均匀填充于特定模腔中,并通过压制压实成具有一定外观形状、尺寸和机械强度的压坯,以便后续的烧结热处理。在填充过程中,粉末先沉积在模具的模腔中,并在高压作用下压紧粉末。然后将所得到的粒料烧结。粉末是否被均匀地、连续地的填充到模腔中,直接关系到压制过程是否可以顺利成型,以及烧结过程中坯料的均匀收缩和最终产品的机械性能和物理性能。传统的粉末成型过程中,粉末填充时,粉末重力作为唯一的源动力,需要克服粉末间的机械咬合力、静电力、静磁力、范德华力、摩擦力等阻力的共同作用。如图1所示,当动力小于阻力时,粉末p因无法实现自由均匀的填充,将出现粉末团聚、架桥、不连续等现象,导致粉末在模腔200中的填充率低,粉末在模腔中的分布不均匀,并且重复性差(每一模的填充率变化大),引起后续的压制困难(如不成型、开裂、密度分布不均匀等)、烧结不良(烧结开裂、变形等)、以及组织性能分布不均,产品合格率低下。已有的模具和填充方法很难实现粉末尤其是超微粉末的连续均匀填充。技术实现要素:本发明提出了一种粉末填充模具单元及填充方法,其解决了现有粉末填充技术中粉末难以填充均匀影响产品合格率的问题。本发明所采用的技术方案之一为:粉末填充模具单元,所述模具单元包括第一模具、第二模具和至少一个气流通道,所述第二模具套设于所述第一模具之内,所述气流通道由所述第一模具和第二模具之间的空间形成,所述第一模具底端设有至少一个孔,所述孔连通所述气流通道;其还包括设于所述第一模具和第二模具之间且用于气流通道的密封装置。本发明所采用的技术方案之二为:粉末填充方法,其采用本发明技术方案之一所述的模具单元,还包括以下步骤:将气流导入所述气流通道,接触并冲散模腔内的粉末;根据粉末 的填充程度,实时调节所述气流的气体压力;其中,所述气流的流动方向与粉末的填充方向相反,充气方式为脉冲式或恒定式。本发明提供了一种粉末填充模具单元和填充方法,其在模具内开设一条气流通道,所述气流通道设置于第一模具和第二模具之间,并贯穿连通第一模具端面与第二模具端面;还设置了密封装置,使得模具单元的密闭性良好,避免漏粉漏气现象。采用这种结构及本发明的填充方法,填充粉末时,驱动气流进入气流通道,然后接触到从上方往下填充的粉末,位于第一模具附近的粉末加料口原本可能存在团聚而无法下落的粉末,由于气流动力作用,这些团聚的粉末被冲散并开始往下填充。需要注意的是,本发明所采用的填充方法可以是脉冲充气方式或是恒定充气方式。这样就可以根据粉末的填充情况和粉末本身的性质,实时调整气流充气方式,调节气体压力;脉冲充气时,可以预设充气时间和脉冲时间或者采用固定值。无论是脉冲充气还是恒定充气方式,都可以实时调整气体压力,比如持续增强或者降低,而预设了气体压力调整范围,以此实时控制充气,改善粉末填充效果,如提高粉末填充均一性,得到高密度的填充体,成形体的成形度较好,不容易开裂。在填充钕铁硼等合金粉末时,还可以提高合金颗粒的取向度。附图说明图1为现有技术的粉末填充模具单元的剖面示意图。图2为本发明粉末填充模具单元的外部示意图。图3为沿图2中模具单元a-a线的剖面示意图。图4为图3中c处的放大示意图。图5为本发明粉末填充模具单元二的剖面示意图。图6为图5中d处的放大示意图。图7为本发明粉末填充模具单元三的外部示意图。图8为沿图7中模具单元e-e线的剖面示意图。图9为图8中f处的放大示意图。附图标记说明:粉末填充模具单元-100、100a、100b;第一模具-10、10b;第二模具-20、20b;气流通道-30、30a、30b;第一通道-31、31a、31b;第二通道-32、32a、32b;第三通道-33、33a、33b;孔-34、34a、34b;气流通道出口-35、35a、35b;芯棒-40;加料口-50、50b;模腔-60、60b;下冲头-b、b’;上冲头-t、t’;密封圈-s;粉末-p,模腔-200。具体实施方式以下结合附图具体描述本发明的粉末填充模具单元及粉末填充方法。请参考图2至图4,为本发明粉末填充模具单元100的结构示意图。粉末填充模具单元100主要包括第一模具10、第二模具20和气流通道30。其中,第一模具10为阴模,第二模具20为阳模,第二模具套设于第一模腔10之内。芯棒40固定套设于第二模具20之内并延伸至第一模具10,其能够在第二模腔20内沿着第二模腔20的长度方向上下运动,芯棒40和第二模具20组合成为下冲头b。还包括一个上冲头t与下冲头b为对称设置,它们的运动轨迹相反以压制模腔60内的粉末。气流通道30的数量至少为一条,本实施例中设置两条气流通道30,图2所示,这两条气流通道30相对模具中心线对称设置。以位于图2中左边的气流通道30为例,气流通道30设于第一模具10和第二模具20之间,第一模具10的底端端面设有一个孔34作为气流通道30的气流入口,气流通道30的位于第二模具20顶端的另一端设有气流出口35;气流通道30的宽度设为3~80μm,其包括三部分,分别为相互连通的第一通道31、第二通道32和第三通道33,孔34位于第一通道31的端口,第一通道31和第二通道32之间的夹角为0~180°。第一通道31与模具底端的夹角为90~180°。图4所示,第一通道31和第二通道32之间的夹角为90°。第一模具10和第二模具20之间的空隙形成了第三通道33。本实施例中,第三通道33为环形,即第一模具10的内表面和第二模具20的外表面之间的空间定义为第三通道33。模具单元100还包括环形加料口50,其为放置粉末的初始位置,第一模腔10内表面与芯棒40之间的空间定义为模腔60,其为环形,环形加料口50位于模腔60的上端。放置粉末的初始位置连通气流通道30的气流出口。所述环形模腔60的厚度为3~10mm。图4中的虚线绘示了气流通道的运动轨迹,箭头标识了气流方向。在模具单元100的下端位置,第一模具10内表面和第二模具20外表面之间还设有密封装置,本发明中为密封圈s,充气时,气流通道30内的气体不会从第一通道10与第二通道20之间泄露,而且在粉末填充时,避免了微小的粉末从此处泄露。当没有气流被充气进入气流通道时,孔34处设有密封盖(图中未绘示)。需要充气时,才打开密封盖。本实施例中,由于模具单元100的第一模具10、第二模具20和芯棒40的形状为圆形,因此加料口50相应地设为环形,填充压制得到的是环形产品。但是不限于此形状的产品,改变模具、芯棒和冲头的形状,加料口的形状也可以进行适应性的调整,比如三角形、方形、棱形和多边形等。本发明还提出了一种粉末填充模具单元100a,请参考图5至图6。模具100a的主要结构与第一实施例中的模具单元100的主要结构相同,其气流通道30a也包括气流入口34a和气流出口35a。区别在于,模具单元100a的第一通道31a与模具底端的夹角为120°,第一通道31a与第二通道32a的夹角为180°,即二者重合,这样在充气时可以直接导入气体进入气流通道30a内,刮壁效果显著。当然,第一通道31a与模具底端的夹角也可以是120~150°之间,如130°、140°或者150°,同样也具有较为显著的刮壁效果。并且,模具的气流通道也可以设置为,第一通道、第二通道和第三通道均重合,即它们之间的夹角均为180°。图6中的虚线绘示了气流通道的运动轨迹,箭头标识了气流方向。本发明还提出了一种粉末填充模具单元100b,请参考图7至图9。模具单元100b主要包括第一模具10b和第二模具20b,第二模具20b可以直接作为下冲头b’使用,同上述模具单元,上冲头t’与也是对称设置。密封圈s设于第一模具10b和第二模具20b之间。模具单元100b的模腔60b为长方体,其宽度为1~10mm,可用于生产方块状磁铁。如图9所示,气流通道30b的结构与前述模具单元100相同,也是包括第一气流通道31b、第二气流通道32b和第三气流通道33b。当然,气流通道也可以采用如前述模具单元100b相同的结构设计。图8中的虚线绘示了气流通道的运动轨迹,箭头标识了气流方向。现有技术中,由于粉末较难均匀连续的填充入模腔中,因此在小尺寸薄型磁铁的生产中 存在难度。本发明的模具单元100b,其内设气流通道30b于模腔60b下端的两侧,当模腔60b开始填充粉末时,由于模腔60b厚度较窄,较容易堆积粉末,借助气流冲散了堆积的粉末,因此实现了小尺寸薄型磁铁的高效填充,为后续的压制烧结提供良好基础。如上所述,本发明所提供的模具单元,其在内外套设的两个模具之间设置至少一条气流通道,所述气流通道包括三部分,其中第一部分设有开口作为气流的入口,第三部分接通模具的模腔并由第一和第二模具之间的间隙定义而成,气流的出口设于第三部分和模腔重合处,第二部分连接于第一和第三部分之间。因此,提供了一条完整的气流通道,使得气流的运动轨迹与粉末的运动轨迹相对,这种结构设计的模具加工更为简单,也有效改善了粉末填充效果。气流通道宽度范围设为1~100μm,配合粉末的粒径尺寸,避免粉末从气流通道漏出。下面以本发明的粉末填充模具单元100为例,说明本发明的粉末填充方法。本发明中,当填充粉末是稀土合金粉末时,其成分为retfagjhgidk,其中,r为nd或保护nd和选自la、ce、pr、sm、gd、dy、tb、ho、er、eu、tm、lu或y中的至少一种,t为fe或包含fe和选自ru、co或ni中的至少一种,a为b或包含b和选自c或p中的至少一种,j为选自cu、mn、si或cr中的至少一种,g为选自al、ga、ag、bi或sn中的至少一种,d为选自zr、hf、v、mo、w、ti或nb中的至少一种。由于本发明的填充粉末是稀土合金粉末,相应的,气流为纯度99%以上的惰性气体。当然,根据粉末的性质,气流可以是空气。气流还可以包括负离子,其具有去除磁粉静电的作用。由于填充粉末是磁性粉末,需要在磁场下才能成形,因此第一模具10、上冲头和下冲头是导磁的,以形成磁路。开始填充粉末时,先将粉末放置于环形加料口50,在重力作用下,粉末开始往下掉落至模腔60中。也就是说,本发明的粉末填充方向是从上到下的。由于粉末之间存在机械咬合力、静电力、静磁力、范德华力、摩擦力等阻力,在粉末下落过程中,部分的粉末出现团聚、架桥和不透气等现象。打开气流通道的孔34的密封盖,然后启动充气机,使气流从孔34进入气流通道30,依次通过第一通道31、第二通道32和第三通道33。气流的运动方向是从下到上的,其到达第三通道33后,接触到团聚在环形加料口50附近的粉末,由于气流具有一定的压力(0.02 ~0.65mpa),产生的动力对这些团聚的粉末进行冲击,使得粉末被冲散,然后掉落至模腔60之内。气流的流动路径可以是直线形或者螺旋形的。当流动路径为直线形时,气流的方向及强度较为均一稳定,其具有刮壁的作用,因此气流通道内壁上粘着的粉末可以很快被气流冲散掉落至模腔60内。流动路径为螺旋形时,其不仅具有刮壁作用,而且冲刷强度较大,因此相应地可以设置较小的气体压力或者较短的充气时间,这样就能够以较小的输入得到较大的输出,节约能源并提高效率。并且,螺旋形气流的运动空间更全面,运动路径规律,也具有提升冲散效果的作用。充气过程是可以实时控制的,根据粉末的填充情况,可以选择脉冲充气方式或者恒定充气方式;并且,也可以实时调节气体压力,比如持续增加、持续减少或保持恒定,以适应粉末的填充程度。气体压力每次调整幅度在0~0.2mpa。采用脉冲充气方式时,单次充气时间的范围设置为大于1~500ms,单次停顿时间也为1~500ms。下面以脉冲式充气方式为例,具体说明粉末填充的情况。以下实施例中,准备200g的合金粉末作为填充材料。合金粉末为钕铁硼合金粉末,平均粒径在10μm以下,大部分粒径在4μm以下,粒径范围是2~12μm(费氏粒度仪测得)。模具100的尺寸设置为,模腔高度60mm,外径50mm,内径40mm,气流通道的宽度为20μm。实施例1采用脉冲式充气方式,采用不同的气体压力,如下表所示,每种气压充气下的粉末填充总时间长度均为10s。脉冲频率设定为,开500ms→关500ms→开500ms→关500ms→···如此反复循环直到加粉时间结束。加粉结束后,粉末在0.8t/cm2的压力下进行压制成圆环形压坯,压坯再在1010~1070℃温度下真空烧结成致密的烧结体,以制造出100个烧结体为例,分别统计各过程中的缺陷情况和烧结体的尺寸变形情况,如下表所示。表一从表一可知,采用脉冲式充气方式时,不同的气体压力下,粉末填充的效果不同。可以看出,采用0.3mpa的气体压力时,填充效果是最好的,填充粉重rsd值最低。0.3mpa气体压力下,压坯成功率高达95%,将压坯进行烧结后,再对烧结体进行外观检测,烧结开裂率降低至5%,烧结体成形也较好,其完整烧结体圆柱度小于0.2mm。实施例2第二实施例中,也采用脉冲充气方式,气体压力保持0.3mpa不变,粉末填充总时间长度为10s,脉冲频率从10ms到500ms变化。其中,脉冲频率10ms时,开10ms→关10ms→开10ms→关10ms→···如此反复循环直到加粉时间结束。其他脉冲频率下的工作过程相同,在此不赘述。加粉结束后的压制烧结及相关统计与实施例1相同,具体如下表所示。表二脉冲频率(ms)10100200500填充粉重rsd(%)3.52.11.52.0压坯成功率(%)72939995烧结开裂率(%)29815完整烧结体圆柱度(mm)0.80.250.150.20从表二可知,采用相同的气体压力时,不同脉冲频率下,粉末填充的效果不同。可以看出,采用200ms的脉冲频率时,填充效果是最好的,填充粉重rsd最小。压坯成功率高达99%,将压坯进行烧结后,再对烧结体进行外观检测,烧结开裂率降低至1%,烧结体成形也较好,其完整烧结体圆柱度小于0.15mm。比较例1作为比较,粉末填充时不充气,让粉末依靠自身重力填充至模具中,加粉结束后的压制烧结及相关统计与实施例1相同。具体参考下表。表三从表三可知,粉末填充时若不借助气体,与实施例1和2相比,耗时更多,而且填充率也很低。随着填充时间的延长,粉末填充率增大的幅度也在减小,这是由粉末团聚等现象造成的。粉末填充至100s后,填充粉重rsd为2.7,高于实施例1和2的。压坯合格率也较低,只有79%。将压坯进行烧结,对其进行外观检测,烧结开裂率达到22%,而且完整烧结体圆柱度数值也不乐观。上述两个实施例与比较例的比对可知,粉末填充时,借助气体的填充效果有了明显提升,而采用固定气体压力(0.3mpa),脉冲频率为200ms时,填充效果是最好的。没有采用充气方式的比较例中,耗时10倍还未能完成粉末填充。并且,充气时采用脉冲时间并调整气体压力对粉末填充效果也有提升作用。根据不同粉末的性质,不需要采取很高的气速,也不需要一直充气,控制气体压力在一定范围并调整脉冲频率,可以达到较佳的粉末填充效果。参考比较例2,本发明所提供的粉末填充模具单元和方法,还具有延长模具使用寿命的效果。由于现有的粉末填充技术,不可避免地在模具内滞留残粉,而造成模具损伤。本发明模具单元的结构和方法,提高了粉末填充效率,减少了残粉滞留量,因此能够有效延长模具使用寿命。比较例2:作为比较例,分别采用充气和不充气的方式进行加粉压制,统计在压制不同模数后,模具表面的光洁度变化,揭示不同加粉填充模式下,模具寿命的变化情况。其中,充气模具采用脉冲式充气方法,脉冲动作设定为200ms开/200ms关,加粉总时间长度为10s,不充气的 常规模具加粉总时间长度为100s。加粉填充完毕后,采用浮动压配合80mpa的单位压力进行粉末压制成型,每压100模后,测试模具阴模内表面的光洁度变化,及目视外观变化情况。两种方式下,模具阴模的材质均为hrc=40~45的炭素钢、阳模的材质为硬质合金,hra>86。具体实施情况如下表所示。表四从上述统计结果来看,通过采用充气式的加粉方式,在保证粉末均匀连续的情况下,可以有效地减轻模具的损伤,从而延长模具的使用寿命,这主要得益于:一方面,由于采用充式加粉,气体通过第一模具与第二模具的间隙时,吹走前一模残留于间隙中的残粉,而这种残粉在模具间隙中的残留是造成模具工作表面逐渐粗糙化的主要原因之一;其次,在充气模式下,粉末在模腔中的分布更加均匀,在后续的压实过程中,在压制总压力相同的情况下,布粉均匀时压坯横截面上各点的应力分配均匀;相比之下,未充气时,由于布粉不均,压坯各点实际应力差异大,局部高单位应力部位处,模具的摩擦加剧,加速该处模壁粗糙化。因上述两个已知的原因,在未充气时,模具使用寿命缩短。从上述统计结果来看,本发明所提供的粉末填充模具单元,其包括相互套设的第一模具和第二模具,至少一条气流通道开设于所述两个模具之间,气流通道还设有位于模具单元底端端面的气体入口以及位于模具单元顶端的气体出口,还增设了用于气流通道的密封装置。气流通道连通模具单元的模腔,因此在粉末填充时,借助气体的外力,以相反方向和可控的力度冲击粉末,即可实现优异的粉末填充效果。模具单元的设计简单合理,密封性能好,易于制造,适于工业化量产。本发明还提供了一种粉末填充的方法,其结合模具单元中开设的气流通道,在粉末填充时,打开充气机,使气体从气流通道接触到模腔中团聚的粉末,从而冲散这些粉末。这种方 法采用可控的充气方式,如脉冲式或是恒定式充气方式,气体压力设定在0.02~0.65mpa,设定脉冲频率以及选择气体流动路径的形状等因素。因此,使用时能够根据粉末填充效果,实时控制充气过程,以优化粉末填充效率,与现有技术相比,减少了粉末填充耗时,还增加了填充粉重,提高了压坯成功率,压坯烧结后,烧结开裂率降低,完整烧结体圆柱度也较好。以上显示和描述了本发明的基本原理、主要特征和优点。本领域的普通技术人员应该了解,上述实施例不以任何形式限制本发明的保护范围,凡采用等同替换等方式所获得的技术方案,均落于本发明的保护范围内。当前第1页12