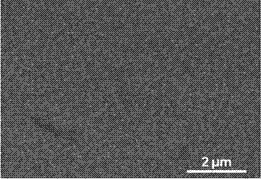
本发明属于铝基纳米复合材料领域,具体来说是一种基于SLM成形的铝基纳米复合材料及其制备方法。技术背景随着对高性能的轻质合金材料的需求越来越强烈,特别是在航空航天、汽车、医疗等领域,对于新颖的金属基复合材料的设计与制备正得到越来越多研究者的关注。传统的铝硅合金由于在比强度、耐磨损性能以及热膨胀系数等方面具有显著的优势而受到广泛关注,但无论如何其性能也已不能满足于现有的需求。借助颗粒增强获得的铝硅基复合材料可显著提高传统的铝硅合金的力学性能,已经被广泛的研究并在实际工程中获得应用,这其中常用的增强体包括Al2O3、TiC、TiB、SiC等。激光增材制造技术是从上世纪80年代初在美国产生并在90年代得到迅速发展的一门综合性、交叉性前沿技术。它基于全新的增材制造理念,从构建零件的CAD模形出发,通过软件分层离散以及数控成形系统,控制激光束将铺放在粉末床中的粉体材料熔融并逐层堆积而形成三维实体零件。目前按照粉末成形特性主要分为选择性激光烧结(selectivelasersintering,SLS)技术和选择性激光熔化(selectivelasermelting,SLM)技术两种,其与传统的加工制造相比较,其突出优势主要体现在:(1)成形过程无需工装夹具或模具的支持,成形灵活并缩短成形时间、减少了成形成本;(2)改变传统材料变形加工及减材成形的思路,易于实现“净成形”,特别适合于制造具有复杂结构的金属零件;(3)从冶金学角度来看,在所成形的零件中形成微细、均匀的激光快速凝固组织,从而决定了成形件优异的综合机械性能。用于激光增材制造的金属材料包括了不锈钢、工具钢、钛合金、镍基高温合金、Co-Cr-Mo合金、铝合金等,但对于金属基复合材料的激光增材制造研究还相对较少。目前对于激光增材制造的颗粒增强铝基复合材料,在成形加工过程中主要面临这样一些问题:(1)由于铝对激光具有很高的激光反射率,通常低功率激光器难以使得铝合金发生完全熔化,增强颗粒的加入能够在程度上提高粉体对激光的吸收率,但增强颗粒加入过多则会导致材料延伸性能下降;(2)研究表明,降低增强体的颗粒尺寸达到纳米级可以有效提高金属基复合材料的机械性能,如提高强度和减少裂纹,但是当增强颗粒的尺寸减小至纳米尺度时,颗粒之间会因强烈的范德瓦尔力以及极大的表面张力而紧密地团聚在一起,从而很不利于增强颗粒在基体中的均匀分散,在激光增材制造过程中,所形成熔池中特有的Marongoni流可以起到均匀分散第二相的作用,但该Marangoni流又与熔池的温度场紧密相连;(3)由于通常加入的增强颗粒为陶瓷相,而陶瓷相与基体相之间的润湿性很差,同时它们之间的热膨胀系数差异也往往较大,这就导致在成形过程中形成的液相不能均匀铺展,同时在随后的凝固过程中产生较大的收缩应力而出现裂纹。
技术实现要素:为解决上述存在的技术问题,本发明提供一种基于SLM成形的铝基纳米复合材料,其能用于激光增材技术领域,有效的解决铝基纳米复合材料在激光增材过程中工艺性能与力学性能不匹配、增强颗粒分布不均匀以及陶瓷相与基材相之间润湿性较差的问题,使得所获得的产品具备良好的界面结合以及优异的力学性能。本发明的目的在于提供一种基于SLM成形的铝基纳米复合材料,所述铝基纳米复合材料是由铝基纳米复合粉末经SLM成形获得;所述铝基纳米复合粉末包括陶瓷相、稀土相和铝基体相,其中,稀土相的添加量小于等于0.8wt%;SLM成形工艺参数为:激光功率在100-130W之间,扫描间距为30μm以及铺粉层厚为50μm;有效体能量密度控制在288-398.65J/mm3;其中,有效体能量密度为ωeff,其中P为激光功率,υ是扫描速度,s是扫描间距,h为铺粉层厚,ηeff为有效激光吸收率,ηeff=B(A*η1*ζ1+η2*ζ2);其中ζ1表示铝基体相的比表面积分数和ζ2表示陶瓷相的比表面积分数,η1代表铝基体相的激光吸收率和η2代表陶瓷相的激光吸收率,以及A表示添加的稀土相对铝基体相激光吸收率的修正系数,取1.04,B为整体吸收率的一个修正系数,取0.92。作为本发明的改进的技术方案,铝基纳米复合粉末中,稀土相含量在0.3-0.8wt%,陶瓷相含量在4-6wt%,其余为铝基体相。作为本发明的改进的技术方案,所述稀土相为La、Nd、Sm或Y,平均粒径范围为10-15μm。作为本发明的改进的技术方案,所述的陶瓷相为TiC或SiC,平均粒径范围在10-30nm,纯度在99.9%以上。作为本发明的改进的技术方案,所述的铝基体相为亚共晶铝硅合金,其中硅的质量分数在6.8-10.5wt%,其他杂质含量控制在0.1wt%以下,其余均为Al成分,平均粒径范围在15-30μm。本发明的另一目的在于提供一种基于SLM成形的铝基纳米复合材料的制备方法,包括机械高能球磨制备铝基纳米复合粉末阶段和铝基纳米复合粉的SLM成形固化两个阶段:(i)机械高能球磨制备铝基纳米复合粉末阶段:将稀土相和铝基体相进行配比混合,得到混合粉末a;将混合粉末a置于球磨机中,对球磨罐进行连续抽真空并用氩气将残余空气排尽,之后向罐中通入氩气,气压控制在0.5Mpa;对混合粉末a进行间歇式球磨,得到复合粉末b;秤取陶瓷相粉末与复合粉末b混合进行二次间歇式球磨,最终得到铝基纳米复合粉末;其中,所述采用的是行星式高能球磨机,球磨介质为陶瓷球,球磨罐采用陶瓷罐体,球磨过程中的球料比为10:1,球磨转速在250-350r/min,球磨时间则控制在4-8h,同时每球磨15min,冷却10min;(ii)铝基纳米复合粉末的SLM成形:(1)在计算机中利用CAD软件构建三维实体几何模形并通过路径规划软件进行分层切片,每层设定30μm;(2)在成形腔体内铺放成形铝基板,并在粉料缸中倒入已制备好的铝基纳米复合粉末,密封腔体同时开启循环除气净化系统;(3)建立加工任务,并设定铺粉厚度为30μm,粉料每层供应为60μm;(4)成形过程中铺粉装置首先在粉床上均匀铺置一层厚度在30μm铝基纳米复合粉末,随后激光束根据计算机模形的分层路径优化数据,对已铺置的粉层进行逐行扫描,形成二维平面;每层扫描完毕后,成形缸下降一个粉层高度,铺粉缸则上升一个粉层高度再度铺粉,激光束根据几何模形信息进行下一层的扫描,直至最终完整的实体被成形加工完毕,得到铝基纳米复合材料。其中,所述SLM成形是在高纯氩气保护气氛环境中进行的,成形过程中维持在正压0.9-1.2atm。其中,对于激光增材制造,加工参数和粉体性能是影响激光最终成形件的两个最主要因素。从粉体成分角度考虑,稀土元素和陶瓷颗粒的添加必然会增强铝合金粉体对激光的吸收率,从而可保证在的激光功率下熔池具有充足的液相量,这里基于金属材料的激光吸收率相关研究以及若干实验数据,该有效激光吸收率ηeff,可定义为:ηeff=B(A*η1*ζ1+η2*ζ2)其中ρ1表示铝基体相的密度和ρ2表示陶瓷相的密度,r1表示铝基体相的粒径和r2表示陶瓷相的粒径,δ1表示铝基体相的质量分数和δ2表示陶瓷相的质量分数,S1为铝基体相的比表面积和S2为陶瓷相的比表面积,ζ1表示铝基体相的比表面积分数和ζ2表示陶瓷相的比表面积分数,η1代表铝基体相的激光吸收率和η2代表陶瓷相的激光吸收率,以及A表示添加的稀土相对铝基体相激光吸收率的修正系数,取1.04;B为整体吸收率的一个修正系数,取0.92。由定义的公式可知,添加的陶瓷相其粒径大小、密度以及质量分数均会影响到激光吸收率。对于上述的公式,我们通过相应的温度场模拟证实这样一个加权公式的合理性,具体的参看实施例3和4。从加工工艺角度考虑,激光成形工艺参数同样会显著影响到铝基纳米复合材料成形过程中熔池的热动力学特性以及随后的显微组织和性能,有如下体能量密度参数给出:其中P为激光功率,υ是扫描速度,s是扫描间距,h为铺粉层厚。结合上面两种影响因素,定义如下的综合工艺参数,即有效体能量密度ωeff:与现有技术相比,本发明具有以下优点:A本发明提供的铝基纳米复合材料是由铝基纳米复合粉末借助SLM成形获得,其中优化的粉末成分设计保证了最终SLM成形件优异的力学性能。该粉末成分包括了铝硅合金粉末、稀土相和陶瓷相,其中稀土相为La、Nd、Sm或Y中的任意一种,所选择的这些稀土元素按照其热物性(熔点、热膨胀系数和表面张力)处于基体相和增强相之间的原则进行选取,保证了在激光加工过程中陶瓷增强相与基体之间良好的润湿性能和避免因热物性差异过大而导致在凝固过程中的开裂情况,其含量控制在0.3-0.8wt%,避免加入过多导致性能恶化;陶瓷颗粒选用碳化物,旨在成形过程中产生原位反应,改善界面结构,在尺寸方面选择纳米尺寸,则借助小尺寸和表界面效应有效提高材料的强韧性,此外陶瓷相的添加还可有效提高粉末对激光的吸收率,提高粉末的加工性能,但其添加含量需控制在4-6wt%,保证材料不会因增强相的过高而引起延展性下降。B本发明提供的铝基纳米复合材料,在增强相与基体相之间形成一定厚度的梯度界面层,从基体相到增强相Al及稀土元素成分呈现梯度变化,在加载过程中,增强颗粒处往往容易造成应力集中而导致开裂情况,但这种梯度界面层的存在则有效缓解了应力集中的发生,从而对材料起到了强韧化的作用;同时增强颗粒由于稀土元素的加入变得更加的细小和圆润,也减小了材料内部在加载中发生应力集中的几率。C利用高能球磨作用实现对陶瓷增强相和稀土相的包覆作用,借助二次球磨作用,有效获取满足于SLM成形工艺的粉体,即具有良好的流动性、球形度以及均匀的成分分布、较窄的粒径分布,该粉体制备方法简单、操作简便。D本发明提供的铝基纳米复合材料是通过优化SLM成形中有效体能量密度来控制获得良好的成形质量,有效体能量密度的作用体现在对激光加工中熔池的稳定性、温度场、流场以及伴随的激光显微组织结构的影响,综合的反映了粉体物性和加工参数这两者对SLM加工过程的影响。本发明中有效体能量密度控制在,在此情况下所形成的熔池具有很好的稳定性,成形件表面具有光滑并呈现出波纹状的熔道轨迹,同时几乎看不到球化效应并获得近全致密的结构。显微组织分析表明增强颗粒得到均匀的弥散分布,基体晶粒细小并呈胞状结构生长。附图说明图1是本发明中实施例1所制备得到的铝基纳米复合粉体放大5000倍的SEM图;图2本发明实施例1中经SLM成形铝基纳米复合材料试样的截面显微组织放大1500倍的SEM图;图3本发明实施例1中经SLM成形铝基纳米复合材料试样中增强颗粒边缘放大80k倍的SEM图;图4本发明实施例2中经SLM成形铝基纳米复合材料试样的截面显微组织放大1500倍的SEM图;图5本发明实施例2中经SLM成形铝基纳米复合材料试样中增强颗粒边缘放大80k倍的SEM图;图6本发明实施例3中SLM成形过程中熔池温度场的分布情况;图7本发明实施例3中经SLM成形铝基纳米复合材料试样的截面显微组织放大1500倍的SEM图;图8本发明实施例3中经SLM成形铝基纳米复合材料试样中增强颗粒边缘放大80k倍的SEM图;图9本发明实施例4中SLM成形过程中熔池温度场的分布情况;图10本发明实施例4中经SLM成形铝基纳米复合材料试样的截面显微组织放大1500倍的SEM图;图11本发明实施例4中经SLM成形铝基纳米复合材料中增强颗粒边缘放大80k倍的SEM图;图12对比试验1中SLM成形铝基纳米复合材料试样截面显微组织放大1500倍的SEM图。具体实施方式为了更好的解释本发明的技术方案,以下结合附图1-5对本发明实施方案作进一步描述:以下实施例在以本发明技术方案为前提下进行实施,给出了详细的实施方式和具体的操作过程,但本发明的保护范围不限于此。一种基于SLM成形的铝基纳米复合材料,所述铝基纳米复合材料是由铝基纳米复合粉末经SLM成形获得;所述铝基纳米复合粉末包括陶瓷相、稀土相和铝基体相,在经二次球磨工艺后稀土相分布于铝基体相中,陶瓷相嵌入在铝基体相表层;SLM成形工艺参数为:激光功率在100-130W之间,扫描间距为30μm以及铺粉层厚为50μm;有效体能量密度控制在288-398.65J/mm3。激光功率优选为100W,120W和130W。铝基纳米复合粉末是通过二次间歇式球磨工艺获得的,其中间歇式球磨的工艺参数为:采用的是行星式高能球磨机,球磨介质为陶瓷球,球磨罐采用陶瓷罐体,球磨过程中的球料比为10:1,球磨转速在250-350r/min,球磨时间则控制在4-8h,同时每球磨15min,冷却10min;所制备的纳米铝基复合粉末中稀土相含量在0.3-0.8wt%,陶瓷相含量在4-6wt%,其余为铝基体相。其中,所述稀土相为La、Nd、Sm或Y,平均粒径范围为10-15μm。其中,所述的陶瓷相为TiC或SiC,平均粒径范围在10-30nm,纯度在99.9%以上。其中,所述的铝基体相为亚共晶铝硅合金,其中硅的质量分数在6.8-10.5wt%,其他杂质含量控制在0.1wt%以下,其余均为Al成分,平均粒径范围在15-30μm。实施例1本发明是一种基于SLM成形的铝基纳米复合材料,所述铝基纳米复合材料的制备过程包括机械高能球磨制备铝基纳米复合粉末阶段和铝基纳米复合粉的SLM成形固化两个阶段:一、机械高能球磨制备铝基纳米复合粉末阶段将稀土相Y(含量为0.3wt%,平均粒径为10μm)和铝基体相粉末(其中硅成分含量为7.8wt%,平均粒径为15μm)粉末进行配比混合,得到混合粉末a;将混合粉末a置于球磨机中,对球磨罐进行连续抽真空并用氩气将残余空气排尽,之后向罐中通入氩气,气压控制在0.5Mpa;对混合粉末a进行间歇式球磨,球磨转速为250r/min,球磨时间为4h,得到复合粉末b;秤取陶瓷相TiC(含量为5wt%,平均粒径为20nm)与复合粉末b混合进行二次间歇式球磨,球磨转速为250r/min,球磨时间为4h,最终得到铝基纳米复合粉末,该粉末呈现近球形形貌,并具有良好的流动性和铺展性,平均粒径为18μm,如附图1所示,其成分如表1所示;表1铝基纳米复合粉末的成分表ElementWeightratio(wt.%)Atomratio(at.%)Al86.7987.39Si7.417.08Ti4.062.18C1.453.27Y0.290.08二、铝基纳米复合粉的SLM成形固化(1)在计算机中利用CAD软件构建三维实体几何模形并通过路径规划软件进行分层切片,每层设定30μm;(2)在成形腔体内铺放成形铝基板,并在粉料缸中倒入已制备好的铝基纳米复合粉末,密封腔体同时开启循环除气净化系统,腔体气压控制在0.9-1.2atm,本实施例中选用0.9atm;(3)建立加工任务,并设定铺粉厚度为30μm,粉料每层供应为60μm;(4)成形过程中,首先在粉床上均匀铺置一层厚度在30μm的铝基纳米复合粉末,随后采用激光功率为100W,扫描速度为120mm/s、扫描间距为50μm的激光加工参数,根据计算机模形的分层路径优化数据,对已铺置的粉层进行逐行扫描,形成二维平面;每层扫描完毕后,成形缸下降一个粉层高度,铺粉缸则上升一个粉层高度再度铺粉,激光束根据几何模形信息进行下一层的扫描,直至最终完整的实体被成形加工完毕,至此成功制备出铝基纳米复合材料。经计算,该实施例中的有效激光吸收率为0.65,由此计算获得的有效体能量密度为383.33J/mm3,根据单位时间传递的热量与焓、温度之间的关系,可以算出对应的最大温度为1017.8K,与此同时对应的温度场模拟结果表明所获得的最大温度为1053K,基本相近。在SLM成形过程中,TiC增强颗粒与Y发生原位反应形成YCx和TiC1-x的界面过渡层,有效改善了基体与陶瓷颗粒之间的界面结合情况,形成了具有梯度的界面(如附图3所示),并避免了在快速凝固条件下的开裂现象,同时细化了显微组织,提高了成形件的力学性能;所述梯度界面其形成机制是由稀土元素与增强相之间发生原位反应,从而在增强相边缘形成一薄层,所述原位反应导致增强颗粒的边缘变得更加圆润化,有助于提高材料的强韧性或力学性能;此外,成形后所形成的梯度界面避免了陶瓷颗粒与金属基体间的直接接触,解决了润湿性差的问题,另一方面则在增强颗粒与基体间起到一个过渡缓冲的作用,避免了两者之间较大的热膨胀系数差所导致的开裂现象。图2显示了经SLM成形试样的截面显微组织放大1500倍的SEM图;从颗粒边缘到基体采样8个点对应的元素成分如下表2所示。所述一种基于SLM成形的铝基复合材料中的界面过渡层从陶瓷增强颗粒边缘到铝合金基体厚度达到约110nm。表2不同位置的元素成分表实施例2本发明是一种基于SLM成形的铝基纳米复合材料,所述铝基纳米复合材料的制备过程包括机械高能球磨制备铝基纳米复合粉末阶段和铝基纳米复合粉的SLM成形固化两个阶段:一、机械高能球磨制备铝基纳米复合粉末阶段将稀土相La(含量为0.5wt%,平均粒径为15um)和铝基体相(其中硅成分含量为9wt%,平均粒径为30μm)粉末进行配比混合,得到混合粉末a;将混合粉末a置于球磨机中,对球磨罐进行连续抽真空并用氩气将残余空气排尽,之后向罐中通入氩气,气压控制在0.5Mpa;对混合粉末a进行间歇式球磨,球磨转速为350r/min,球磨时间为5h,得到复合粉末b;秤取陶瓷相SiC(含量为4wt%,平均粒径为30μm)粉末与复合粉末b混合进行二次间歇式球磨,球磨转速为350r/min,球磨时间为5h,最终得到铝基纳米复合粉末,该粉末呈现近球形形貌,并具有良好的流动性和铺展性,平均粒径为15μm。二、铝基纳米复合粉的SLM成形固化(1)在计算机中利用CAD软件构建三维实体几何模形并通过路径规划软件进行分层切片,每层设定30μm;(2)在成形腔体内铺放成形铝基板,并在粉料缸中倒入已制备好的铝基纳米复合粉末,密封腔体同时开启循环除气净化系统,腔体气压控制在1.0atm;(3)建立加工任务,并设定铺粉厚度为30μm,粉料每层供应为60μm;(4)成形过程中,首先在粉床上均匀铺置一层厚度在30μm的铝基纳米复合粉末,随后采用激光功率为100W,扫描速度为125mm/s、扫描间距为50μm,其有效体能量密度为288J/mm3的激光束,根据计算机模形的分层路径优化数据,对已铺置的粉层进行逐行扫描,形成二维平面;每层扫描完毕后,成形缸下降一个粉层高度,铺粉缸则上升一个粉层高度再度铺粉,激光束根据几何模形信息进行下一层的扫描,直至最终完整的实体被成形加工完毕,至此成功制备出铝基纳米复合材料。经计算,该实施例中的有效激光吸收率为0.61,由此计算获得的有效体能量密度为288J/mm3,根据单位时间传递的热量与焓、温度之间的关系,可以算出对应的最大温度为983.2K,与此同时对应的温度场模拟结果表明所获得的最大温度为1016K,基本相近。在SLM成形过程中,SiC增强颗粒与La发生原位反应形成LaCx和SiC1-x的界面过渡层,有效改善了基体与陶瓷颗粒之间的界面结合情况,并避免了在快速凝固条件下的开裂现象,同时细化了显微组织,提高了成形件的力学性能。图4显示了经SLM成形试样的截面显微组织放大1500倍的SEM图;图5是经SLM成形试样中增强颗粒边缘放大200k倍的SEM图;从颗粒边缘到基体采样6个点对应的元素成分如下表3所示。所述一种基于SLM成形的铝基复合材料中的界面过渡层从陶瓷增强颗粒边缘到铝合金基体厚度达到约60nm。表3不同位置的元素成分表实施例3本发明是一种基于SLM成形的铝基纳米复合材料,所述铝基纳米复合材料的制备过程包括机械高能球磨制备铝基纳米复合粉末阶段和铝基纳米复合粉的SLM成形固化两个阶段:一、机械高能球磨制备铝基纳米复合粉末阶段将稀土相Sm(含量为0.8wt%,平均粒径为12um)和铝基体相粉末(其中硅成分含量为6.8wt%,平均粒径为20μm)进行配比混合,得到混合粉末a;将混合粉末a置于球磨机中,对球磨罐进行连续抽真空并用氩气将残余空气排尽,之后向罐中通入氩气,气压控制在0.5Mpa;对混合粉末a进行间歇式球磨,球磨转速为300r/min,球磨时间为8h,得到复合粉末b;秤取陶瓷相TiC(含量为5wt%,平均粒径为25nm)粉末与复合粉末b混合进行二次间歇式球磨,球磨转速为300r/min,球磨时间为8h,最终得到铝基纳米复合粉末,该粉末呈现近球形形貌,并具有良好的流动性和铺展性,平均粒径为25μm;二、铝基纳米复合粉的SLM成形固化(1)在计算机中利用CAD软件构建三维实体几何模形并通过路径规划软件进行分层切片,每层设定30μm;(2)在成形腔体内铺放成形铝基板,并在粉料缸中倒入已制备好的铝基纳米复合粉末,密封腔体同时开启循环除气净化系统,腔体气压控制在1.2atm;(3)建立加工任务,并设定铺粉厚度为30μm,粉料每层供应为60μm;(4)成形过程中,首先在粉床上均匀铺置一层厚度在30μm的铝基纳米复合粉末,随后采用激光功率为120W,扫描速度为138mm/s、扫描间距为50μm,其有效体能量密度为398.65J/mm3的激光束,根据计算机模形的分层路径优化数据,对已铺置的粉层进行逐行扫描,形成二维平面;每层扫描完毕后,成形缸下降一个粉层高度,铺粉缸则上升一个粉层高度再度铺粉,激光束根据几何模形信息进行下一层的扫描,直至最终完整的实体被成形加工完毕,至此成功制备出铝基纳米复合材料。经计算,该实施例中的有效激光吸收率为0.54,由此计算获得的有效体能量密度为398.65J/mm3,根据单位时间传递的热量与焓、温度之间的关系,可以算出对应的最大温度为977.4K,与此同时对应的温度场模拟结果表明所获得的最大温度为1000K,基本相近。图6显示了该成形条件下的温度场情况,由于采用了密度更高以及粒径更大的陶瓷相颗粒,因此显示出较低的激光吸收率以及对应的较低的熔池温度。在SLM成形过程中,TiC增强颗粒与Sm发生原位反应形成SmCx和TiC1-x的界面过渡层,有效改善了基体与陶瓷颗粒之间的界面结合情况,并避免了在快速凝固条件下的开裂现象,同时细化了显微组织,提高了成形件的力学性能。图7显示了经SLM成形试样的截面显微组织放大1500倍的SEM图;图8是经SLM成形试样中增强颗粒边缘放大200k倍的SEM图;从颗粒边缘到基体采样8个点对应的元素成分如下表4所示。所述一种基于SLM成形的铝基复合材料中的界面过渡层从陶瓷增强颗粒边缘到铝合金基体厚度达到约115nm。表4不同位置的元素成分表实施例4本发明是一种基于SLM成形的铝基纳米复合材料,所述铝基纳米复合材料的制备过程包括机械高能球磨制备铝基纳米复合粉末阶段和铝基纳米复合粉的SLM成形固化两个阶段:一、机械高能球磨制备铝基纳米复合粉末阶段将稀土相Nd(含量为0.4wt%,平均粒径为14μm)和铝基体相粉末(其中硅成分含量为10.5wt%,平均粒径为30μm)进行配比混合,得到混合粉末a;将混合粉末a置于球磨机中,对球磨罐进行连续抽真空并用氩气将残余空气排尽,之后向罐中通入氩气,气压控制在0.5Mpa;对混合粉末a进行间歇式球磨,球磨转速为280r/min,球磨时间为8h,得到复合粉末b;秤取陶瓷相SiC(含量为6wt%,平均粒径为10nm)粉末与复合粉末b混合进行二次间歇式球磨,球磨转速为280r/min,球磨时间为8h,最终得到铝基纳米复合粉末,该粉末呈现近球形形貌,并具有良好的流动性和铺展性,平均粒径为20μm。二、铝基纳米复合粉的SLM成形固化(1)在计算机中利用CAD软件构建三维实体几何模形并通过路径规划软件进行分层切片,每层设定30μm;(2)在成形腔体内铺放成形铝基板,并在粉料缸中倒入已制备好的铝基纳米复合粉末,密封腔体同时开启循环除气净化系统;(3)建立加工任务,并设定铺粉厚度为30μm,粉料每层供应为60μm;(4)成形过程中,首先在粉床上均匀铺置一层厚度在30μm的铝基纳米复合粉末,随后采用激光功率为130W,扫描速度为147mm/s、扫描间距为50μm,其有效体能量密度为398.65J/mm3的激光束,根据计算机模形的分层路径优化数据,对已铺置的粉层进行逐行扫描,形成二维平面;每层扫描完毕后,成形缸下降一个粉层高度,铺粉缸则上升一个粉层高度再度铺粉,激光束根据几何模形信息进行下一层的扫描,直至最终完整的实体被成形加工完毕,至此成功制备出铝基纳米复合材料。经计算,该实施例中的有效激光吸收率为0.69,由此计算获得的有效体能量密度为398.65J/mm3,根据单位时间传递的热量与焓、温度之间的关系,可以算出对应的最大温度为1182.6K,与此同时对应的温度场模拟结果表明所获得的最大温度为1200K,基本相近。图9显示了在该成形条件下熔池的温度场情况,与实施例3相比,由于采用了更低密度和更小粒径的陶瓷相,因此反映出更高的激光吸收率,从而也获得更高的熔池温度。在SLM成形过程中,SiC增强颗粒与Nd发生原位反应形成NdCx和SiC1-x的界面过渡层,有效改善了基体与陶瓷颗粒之间的界面结合情况,并避免了在快速凝固条件下的开裂现象,同时细化了显微组织,提高了成形件的力学性能。所图10显示了经SLM成形试样的截面显微组织放大1500倍的SEM图;图11是经SLM成形试样中增强颗粒边缘放大200k倍的SEM图;从颗粒边缘到基体采样9个点对应的元素成分如下表5所示。所述一种基于SLM成形的铝基复合材料中的界面过渡层从陶瓷增强颗粒边缘到铝合金基体厚度达到约120nm。表5不同位置的元素成分表对比实施例本对比实施例是利用不添加稀土相的铝硅合金与TiC陶瓷颗粒作为原始粉末材料进行相应的SLM成形,得到的铝基纳米复合材料的截面显微组织放大1500倍的SEM图如图12所示,在本对比实施例与具体实施例1不同的是原始粉末中未添加稀土相粉末,其他与具体实施例1相同。从图3、4、5、6、7、8、9和10可以看出,原始RE(La、Nd、Sm或Y)粉末与所加入的碳化物颗粒在SLM成形过程中发生原位扩散反应形成具有一定厚度的梯度界面层,增强颗粒与基体相间结合良好,没有显微裂纹产生;图12显示了本对比实施例中增强颗粒与基体相间界面的结合情况,有很明显的裂纹萌生。此外,成形后的添加有稀土元素的铝基纳米复合材料与没有添加稀土元素的铝基纳米复合材料分别进行拉伸试验测试和显微硬度的测量,相应的数据如表6,以反映在实施例1-4中所形成的界面过渡层对力学性能的提高具有显著的作用。表6实施例1-4及对比例中的铝基纳米复合材料的综合力学性能经激光增材制造成形,不同工艺参数下的SLM试样被获得,通过一系列的分析检测,发现在合适的工艺参数条件下,经激光成形后纳米增强相能够均匀弥散分布并保持在纳米尺度,同时可以看出增强相与基体之间具有良好的界面结合,相应的力学性能测试也表明这样的梯度界面层的存在可有效提高试样的拉伸性能和显微硬度。本发明采用二次机械球磨的方法获取了添加有稀土相的铝基纳米复合粉体,并在激光增材制造成形中成功获得具有梯度界面结构的铝基纳米复合材料,同时具有良好的成形性能,方法简单,成本低廉,这为设计和制备高性能的纳米颗粒增强铝基复合材料提供了方法,同时也为其工业化应用奠定基础。应当理解的是,本发明的上述具体实施方式仅仅用于示例性说明或解释本发明的原理,而不构成对本发明的限制。因此,在不偏离本发明的精神和范围的情况下所做的任何修改、等同替换、改进等,均应包含在本发明的保护范围之内。此外,本发明所附权利要求旨在涵盖落入所附权利要求范围和边界、或者这种范围和边界的等同形式内的全部变化和修改例。