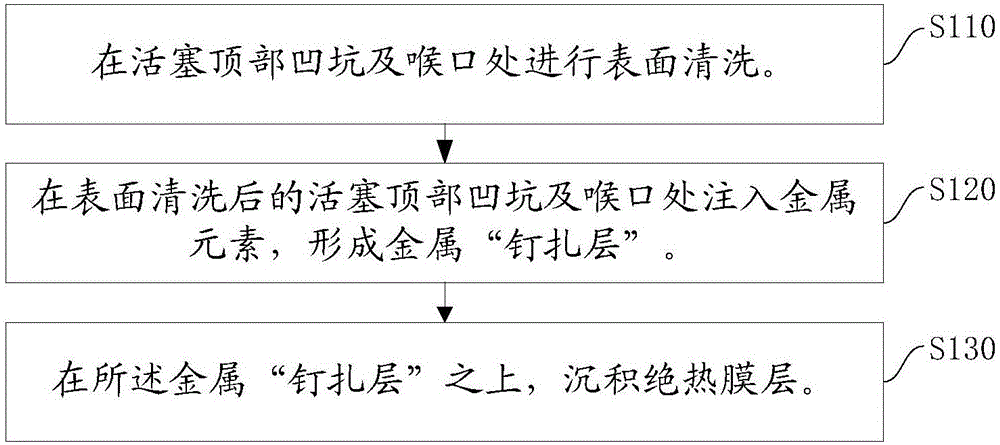
本发明涉及材料表面改性
技术领域:
,尤其涉及一种解决发动机活塞拉缸的方法。
背景技术:
:活塞被称为内燃机的“心脏”,承受交变的机械负荷和热负荷,是内燃机中工作条件最恶劣的关键零部件之一,对其材料具有特殊的要求:热膨胀系数小、密度小、传热导电性好、耐蚀性及耐磨性等。目前,国内外车辆发动机均向高速和高功率密度的方向发展,其中,卡车柴油机的升功率提升了三倍,军车柴油机的升功率提升速度更高。随着内燃机的大幅度强化,缸内燃气的最大爆发压力逐渐升高,同时,缸内燃气温度也大幅度升高,导致和燃气直接接触的活塞热负荷迅速增加,即随着发动机强化程度的提高,活塞的温度也逐渐增高,而过高的温度使得活塞材料强度降低,进而导致活塞的高温强度和承载能力降低。高温和高负荷等恶劣的工作环境,使得活塞成为疲劳失效较多的发动机零价之一,其可靠性成为制约整个发动机安全运行的重要目标。新材料技术是我国乃至全世界都非常重视的研究领域之一,从我国“863”计划设立起,新材料技术就是其中的一个重要的研究领域,而材料表面改性技术是新材料技术研究的一个重要方向。通过合适的表面改性处理,可以显著提高材料表面的多种性能,例如材料表面的光洁度、硬度、抗磨性、抗氧化、耐温以及抗腐蚀等性能,从而显著提高材料的使用寿命和工作效率,实现节约原材料、降低能源消耗等目的。技术实现要素:随着内燃机的大幅度强化,缸内燃气的最大爆发压力逐渐升高,以及缸内温度的不断升高,对活塞相关联的关键部件稳定、可靠性方面的要求越来越高,研制出高寿命、高稳定性的活塞对内燃机的发展显得非常重要。鉴于此,为解决目前发动机存在的活塞拉缸的问题,本发明实施例提供了一种解决发动机活塞拉缸的方法,在活塞顶部凹坑及喉口处沉积绝热膜层,用以阻止燃烧室热量向活塞下的关键部件的传导,解决活塞拉缸的问题。优选地,所述在活塞顶部凹坑及喉口处沉积绝热膜层包括:在活塞顶部凹坑及喉口处进行表面清洗;在表面清洗后的活塞顶部凹坑及喉口处注入金属元素,形成金属“钉扎层”;在所述金属“钉扎层”之上,沉积绝热膜层。进一步优选地,利用金属离子束对所述活塞顶部凹坑及喉口处进行表面清洗。进一步优选地,金属离子束所用金属元素为Ti、Ni或Al。进一步优选地,所述金属元素为Ti、Ni或Al。进一步优选地,所述绝热膜层为Al2O3膜或TiC-DLC膜。进一步优选地,所述绝热膜层为TiC-DLC膜。进一步优选地,注入金属元素时的电压为4-15V;注入金属元素时的束流强度为1-15mA;注入金属元素的剂量为1×1014-1×1017/cm2;注入金属元素时的深度为70-120nm。进一步优选地,沉积绝缘热膜层时采用的是磁过滤阴极真空弧系统。进一步优选地,所述绝热膜层的厚度为20-30μm。相对于现有技术,本发明实施例具有以下优势:1、在活塞顶部凹坑及喉口处沉积超厚绝热膜层能够非常方便的解决因热量传递带来的活塞部件以下各关键部件因热膨胀系数不一致带来的问题。2、在膜层制备技术方面:(a)通过对活塞基材进行高能量的金属元素注入,使基材亚表面原子与注入金属形成金属-基材原子混合的“钉扎层”结构,这样形成的“钉扎层”结构与基底层乃至后续磁过滤沉积出的结构性膜层的结合力都非常好,从而使其抗剥离强度得以增强;(b)相比磁控溅射、电子束蒸发等PVD沉积方法,磁过滤电弧沉积设备原子离化率非常高,大约在90%以上。由于原子离化率高,可使等离子体密度增加,成膜时大颗粒减少,有利于提高薄膜硬度、耐温性、耐磨性、致密性以及膜基结合力等。附图说明构成本发明实施例部分的附图是用来提供对本发明实施例的进一步理解,本发明的示意性实施例及其说明用于解释本发明,并不构成对本发明的限制。图1为本发明实施例提供的在活塞顶部凹坑及喉口处沉积绝热膜层的流程示意图;图2为本发明实施例提供的绝热膜层结构示意图;图3(a)为本发明实施例提供的Al2O3绝热膜层实物图;图3(b)为本发明实施例提供的TiC-DLC绝热膜层实物图;图4(a)为本发明实施例提供的Al2O3绝热膜表面金相显微图;图4(b)为本发明实施例提供的TiC-DLC绝热膜表面金相显微图;图5为本发明实施例提供的Al2O3和TiC-DLC绝热膜热循环测试时的热电偶位置;图6为本发明实施例提供的Al2O3、TiC-DLC绝热膜与磷化活塞测温点处加热到100℃-250℃时所需时间对比图;附图标记说明:200—活塞基材;210—金属清洗层;220—金属“钉扎层”;230—绝热膜层;具体实施方式下面通过附图和实施例,对本发明的技术方案做进一步的详细描述。应当理解为这些实施例仅仅是用于更详细具体地说明,但并不意于限制本发明的保护范围。此外,还需要说明的是,本部分对本发明实验中所使用到的材料以及试验方法进行一般性的描述。虽然为实现本发明目的所使用的许多材料和操作方法是本领域公知的,但是本发明仍然在此作尽可能详细描述。本领域技术人员清楚,在上下文中,如果未特别说明,本发明所用材料和操作方法是本领域公知的。实施例一为解决目前发动机存在的活塞拉缸的问题,本实施例提供了一种解决发动机活塞拉缸的方法,在活塞顶部凹坑及喉口处沉积绝热膜层,用以阻止燃烧室热量向活塞下的关键部件的传导,解决活塞拉缸的问题。图1为本发明实施例提供的在活塞顶部凹坑及喉口处沉积绝热膜层的流程示意图,图2为本发明实施例提供的绝热膜层结构示意图。如图1所示,所述方法包括:S110,在活塞顶部凹坑及喉口处进行表面清洗。在一个示例中,利用金属离子束对所述活塞顶部凹坑及喉口处进行表面清洗,形成基底层。优选地,采用磁过滤阴极真空弧(filteredcathodicvacuumarc,FCVA)系统在活塞顶部凹坑及喉口处进行金属离子束表面清洗。如图2所示,在活塞基材200处进行表面清洗,形成基底层,即金属清洗层210。本步骤可选地,表面清洗时所用金属元素为Ti、Ni或Al,能更好的与活塞基材结合。需要说明的是,在清洗过程中,FCVA系统的负压在400-1000V,清洗时的金属离子束流强度为300-1000mA。S120,在表面清洗后的活塞顶部凹坑及喉口处注入金属元素,形成金属“钉扎层”.在一个示例中,利用金属蒸汽真空弧(Metalvaporvacuumarc,MVVA)离子源向基底层注入金属元素,形成金属“钉扎层”。即,利用高能金属离子注入基底,能够形成金属和基底材料的混合层,提高其表面后续膜层与基底的结合力。如图2所示,在金属清洗层210上注入金属元素,形成金属“钉扎层”220。需要指出的是,注入的金属元素可采用Ti、Ni或Al。作为一种可选实施方式,注入金属元素的过程中,注入电压为4-15kV,束流强度为1-15mA,注入剂量为1×1014-1×1017/cm2,注入深度为70-120nm。S130,在所述金属“钉扎层”之上,沉积绝热膜层。在一个示例中,采用磁过滤阴极真空弧(filteredcathodicvacuumarc,FCVA)系统在基底“钉扎层”表面,磁过滤沉积,同时通入反应气体,得到绝热膜层。如图2所示,在金属“钉扎层”220上面沉积得到绝热膜层230。在本步骤中,可选地,绝热膜层为Al2O3膜或TiC掺杂DLC(类金刚)薄膜等,即绝热膜可以为Al2O3膜或TiC-DLC膜等,且绝热膜层的厚度为20-30μm。进一步可选的,绝热膜层为TiC-DLC膜。本实施例提供的解决发动机活塞拉缸的方法,主要是通过FCVA系统利用金属离子束Ti、Al或Ni中的一种元素对活塞顶部凹坑及喉口处进行表面清洗,之后通过(MEVVA系统注入的Ti、Al或Ni中的一种元素在基底上制备金属“钉扎层”,最后通过FCVA系统沉积超厚绝热膜层构成了整个膜层的主体结构,同时厚度在20-30μm;该结构膜层利用金属离子注入系统形成了金属混合“钉扎层”,使后续沉积膜层与基底材料有着非常好的结合强度;同时选择了绝热效果好的膜层,使其沉积在活塞顶部凹坑及喉口超厚具有明显的隔热效果,同时阻止了燃烧室的相对高温向活塞顶部以下关键部件的热传导,明显减小其热膨胀量,同时可直接避免因膨胀系数不一致带来的各种问题。为更好的理解本发明提供的技术方案,下面,结合附图说明,以在塞顶部凹坑及喉口处沉积Al2O3以及TiC-DLC两种绝热膜层为例,详细的介绍本发明的基于离子束技术解决发动机活塞拉缸的方法,并对沉积的两种绝热膜层进行性能分析。实施例二在活塞顶部凹坑及喉口处沉积Al2O3绝热膜层。实施步骤如下:S110,金属清洗层210制备Al沉积:将活塞基材200固定于样品台,转动样品至沉积靶位,开始沉积,即对活塞基材200进行表面清洗,获得金属清洗层210。沉积弧源为纯度99%的Al弧源,沉积条件为:真空度1×10-3-6×10-3Pa,沉积弧流:100-120A,磁场电流:1.4-2.4A,弧流:380-440mA,负压:400V-1000V,占空比50%-100%,沉积时间3-60S,磁过滤管道为90°过滤。S120,金属“钉扎层“220制备:注入:转动至注入靶位开始注入,即在金属清洗层210之上注入金属离子,获得金属“钉扎层”220。注入离子源为纯度99.9%的纯Ti,注入条件为:真空度1×10-3-6×10-3Pa,注入弧压:50-70V,注入电压:6-10kV,弧流:3-6mA,注入剂量1×1014-1×1015Ti/cm2。S130,Al2O3超厚绝热层230制备:Al2O3膜沉积:在220之上沉积Al2O3膜230,沉积条件为:沉积弧源为纯度99%的Al弧源,真空度:1×10-2-6×10-2Pa,沉积弧流:100-120A,磁场电流:1.4-2.4A,弧流:180-240mA,负压:150V-350V,占空比50%-100%,氧气进气量20-100sccm,沉积厚度为20-30μm。图3(a)为本实施例制备的Al2O3绝热膜层实物图。后续对其进行性能测试和分析。实施例三在活塞顶部凹坑及喉口处沉积TiC-DLC绝热层。实施步骤如下:S110,金属清洗层210制备:Ti沉积:将活塞基材200固定于样品台,转动样品至沉积靶位开始沉积。沉积弧源为纯度99%的Ti弧源,沉积条件为:真空度1×10-3-6×10-3Pa,沉积弧流:100-110A,磁场电流:1.4-2.4A,弧流:380-440mA,负压:-400V-1000V,占空比50%-100%,沉积时间3-60S,磁过滤管道为90°过滤。S120,金属“钉扎层”220制备:注入:转动至注入靶位开始注入。注入离子源为纯度99.9%的纯Ti,注入条件为:真空度1×10-3-6×10-3Pa,注入弧压:50-70V,注入电压:6-10kV,弧流:3-6mA,注入剂量1×1014-1×1015Ti/cm2。S130,TiC-DLC超厚绝热层230制备:TiC-DLC膜沉积:在220之上沉积TiC-DLC膜230,沉积条件为:沉积弧源为纯度99%的Ti弧源,真空度:1×10-2-6×10-2Pa,沉积弧流:100-120A,磁场电流:3.4-5.0A,弧流:180-240mA,负压:150V-350V,占空比10%-100%,乙炔气进气量200-300sccm,沉积厚度为20-30μm。图3(b)为本实施例制备的TiC-DLC绝热膜层实物图,后续对其进行性能测试和分析。为对超厚绝热层性能进行说明,这里可参照图图4(a)和图4(b)、图5及图6,其分别为Al2O3绝热膜层和TiC-DLC绝热膜层的表面光学形貌图、活塞截面及热电偶安装位置图,以及500次热冲击循环试验结果示意图,需要说明的是,作为对比,对活塞进行磷化处理,图6中还包括磷化活塞测量点的热冲击循环试验结果。并对Al2O3、TiC-DLC超厚绝热膜层进行硬度测试,测试过程中,其载荷为100g,其总体的显微硬度结果如表1所示。表1实施例二和实施例三提供的Al2O3和TiC-DLC绝热膜的显微硬度值测试点12345平均硬度Al2O3硬度/HV183614671776168016201675.8TiC-DLC硬度/HV212322002100209023232167.2结合表1可知,Al2O3超厚绝热层显微硬度可达1675.8HV,TiC-DLC膜层的显微硬度可达2167.2HV。图6为超厚绝热层500次热冲击循环试验结果示意图,本试验方法按照Q/LE107.093-2010《活塞热疲劳试验规范》进行。热电偶安装位置及测量点的分布见图5,其中,A点为热偶安装位置及测量点。从试验分析结果可以看出:(1)燃烧室表面经过物理气相沉积处理的G4700B活塞经过500次热冲击循环试验后,渗透层未出现脱落现象;(2)燃烧室表面物理气相沉积处理的活塞与表面理化处理的活塞在加热100℃-250℃同一温度段下,在加热同一段温度下,燃烧室表面经过物理气相沉积TiC-DLC处理的活塞比表面磷化的活塞加热时间均长40S以上,沉积超厚Al2O3膜层的活塞加热时间比磷化活塞延时20S,说明物理气相沉积TiC-DLC和Al2O3能够起到很好的隔热效果。本发明提供的解决发动机活塞拉缸的方法,主要是通过FCVA系统利用金属离子束对活塞顶部凹坑及喉口处进行表面清洗,之后通过MEVVA系统注入金属元素在基底上制备金属“钉扎层”,使后续沉积膜层与基底材料有着非常好的结合强度,从而使其抗剥离强度得以增强;此外,沉积膜层具有明显的隔热效果,阻止了燃烧室的相对高温向活塞顶部以下关键部件的热传导,明显减小其热膨胀量,同时可直接避免因膨胀系数不一致带来的各种问题。需要说明的是,尽管本发明已进行了一定程度的描述,明显地,在不脱离本发明的精神和范围的条件下,可进行各个条件的适当变化。可以理解为本发明不限于所述实施方案,而归于权利要求的范围,其包括所述每个因素的等同替换。以上所述的具体实施方式,对本发明的目的、技术方案和有益效果进行了进一步详细说明,所应理解的是,以上所述仅为本发明的具体实施方式而已,并不用于限定本发明的保护范围,凡在本发明的精神和原则之内,所做的任何修改、等同替换、改进等,均应包含在本发明的保护范围之内。当前第1页1 2 3