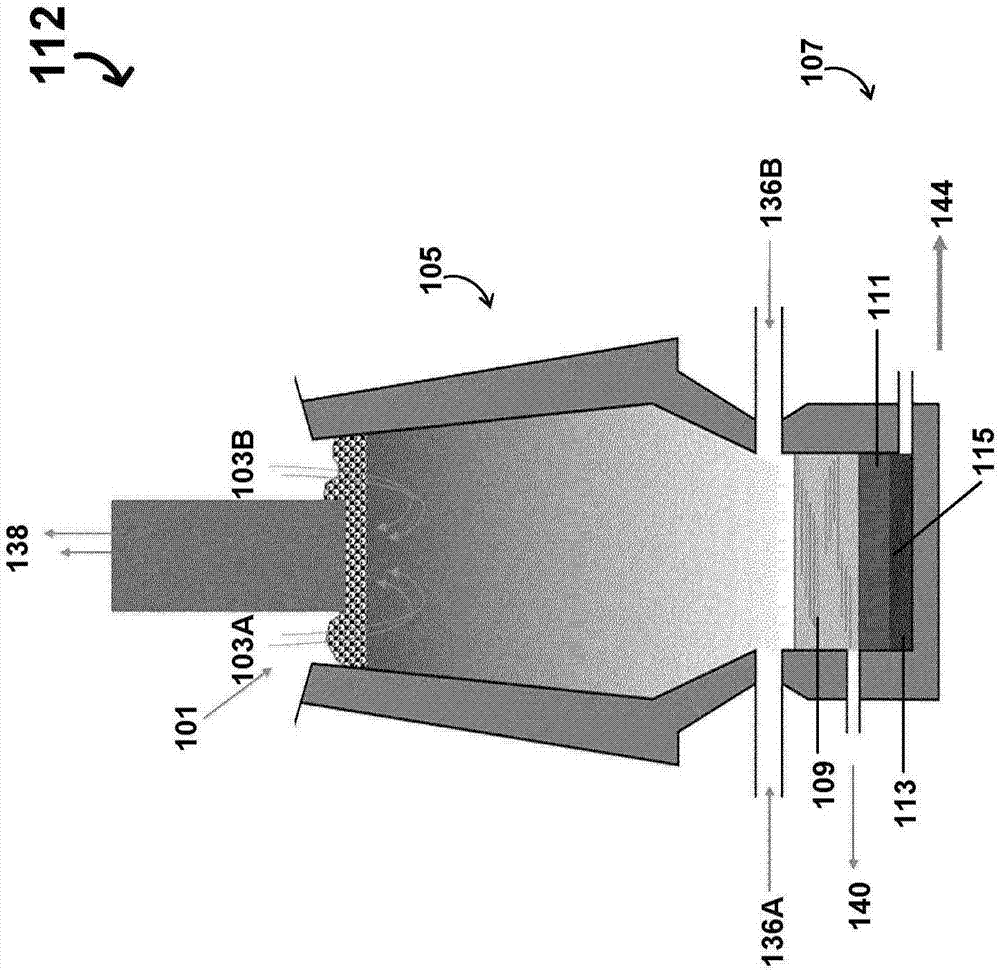
本申请要求2015年8月24日提交的第62/208,993号和2015年11月3日提交的第62/250,056号共同待审的美国临时申请的优先权权益。这些文件通过引用以其整体并入本文。
技术领域:
本公开涉及应用于金属、合金及其各种衍生物的提取和再循环的化学领域的改进。例如,本公开涉及在采矿、冶金过程和/或工业过程期间处理各种原材料或所产生的残渣的方法。本公开背景虽然在过去数十年中湿法冶金方法和矿物加工方法变得更具竞争力,但用这些方法加工含有多种元素的材料通常是具有挑战性的,这导致操作成本高。作为示例,作出了许多尝试以使熔炼炉粉尘以湿法冶金再循环,以回收诸如Cu、Pb、Sb、Bi、Ag、Au、Ge和In的微量元素。这种方法通常产生复杂的流程图(水平衡、氯化物限制、热平衡、水污染、操作成本等)。因此,对用于处理这种粉尘残渣和/或其他多金属原材料的现有解决方案存在至少提供替代技术或补充技术的需求。本公开概述根据一方面,提供了制备各种金属及其衍生物的方法,所述方法包括:向鼓风炉或任选的另一熔融装置中供入含铜的团矿,所述含铜的团矿具有约0.5至约2.0的(2*%S)/(%Cu)比率,并且供入碳源以便获得多层产物和废气;任选地控制多层产物中存在或不存在黄渣层;以及任选地将铁源供入鼓风炉,其中所获得的产物任选地包含:布置在多层产物的顶部的第一层,所述第一层包含矿渣;布置在所述第一层下方的第二层,并且所述第二层包含锍;任选的布置在所述第二层下方的黄渣层;以及任选的布置在所述第二层下方或所述黄渣层下方的底层,并且所述底层包含至少两种金属的合金。根据另一方面,提供了制备各种金属及其衍生物的方法,所述方法包括:将含铜的材料(例如球团矿或团矿)供入熔炉,使得所述含铜的材料中含有的砷和铟中的至少一种至少部分挥发,由此获得砷和铟中的至少一种至少部分贫化的材料,其中在使所述材料挥发之前,任选地调整所述材料的组成以便获得约0.5至约2.0的2*%S/(%Cu)比率;以及将所述经贫化的材料和碳源供入熔融装置,以便获得多层产物和废气,其中在使所述经贫化的材料熔融之前,任选地调整所述经贫化的材料的组成以便获得约0.5至约2.0的2*%S/(%Cu)比率;其中所述方法任选地包括以下中的至少一个:在挥发之前调整所述材料的组成以便获得约0.5至约2.0的2*%S/(%Cu)比率;以及在熔融之前调整所述经贫化的材料的组成以便获得约0.5至约2.0的2*%S/(%Cu)比率。根据另一方面,提供了制备各种金属及其衍生物的方法,所述方法包括:向鼓风炉或任选的另一熔融装置供入:-团矿,包含(i)选自含铜的材料、含镍的材料、含钴的材料以及它们的混合物的原材料,所述团矿具有约0.5至约2的%S/((%Cu/2)+%Ni+%Co)比率;-以及碳源,以便获得多层产物和废气;任选地控制在所述多层产物中存在或不存在黄渣层;以及任选地将铁源供入鼓风炉,其中所获得的产物任选地包含:布置在多层产物的顶部的第一层,所述第一层包含矿渣;布置在所述第一层下方的第二层,并且所述第二层包含锍;任选的布置在所述第二层下方的黄渣层;以及任选的布置在所述第二层下方或所述黄渣层下方的底层,并且所述底层包含至少两种金属的合金。根据另一方面,提供了制备各种金属及其衍生物的方法,所述方法包括:将选自含铜的材料、含镍的材料、含钴的材料以及它们的混合物的原材料(例如团矿)供入熔炉,使得所述原材料中含有的砷和铟中的至少一种至少部分挥发,由此获得砷和铟中的至少一种至少部分贫化的材料,其中在使所述材料挥发之前,任选地调整所述材料的组成以便获得约0.5至约2的%S/(%(Cu/2)+%Ni+%Co)比率;以及将所述经贫化的材料和碳源供入熔融装置以便获得多层产物和废气,其中在使所述经贫化的材料熔融之前,任选地调整经贫化的材料的组成以便获得约0.5至约2的%S/(%(Cu/2)+%Ni+%Co)比率;其中所述方法包括以下中的至少一个:在挥发之前调整所述材料的组成以便获得约0.5至约2的%S/((%Cu/2)+%Ni+%Co)比率;以及在熔融之前调整所述经贫化的材料的组成以便获得约0.5至约2的%S/((%Cu/2)+%Ni+%Co)比率。附图简述在以下附图中,仅通过示例的方式表示本公开的各个实施方案:图1示出了根据本公开的方法的示例的方框图;图2示出了根据本公开的方法的另一示例的方框图;图3示出了根据本公开的方法的另一示例的方框图;图4示出了根据本公开的方法的另一示例的方框图;以及图5示出了根据本公开的方法的另一示例的方框图。各种实施方案详述由以下仅通过示例并且以非限制性方式例示的各种实施方案的描述,其他特征和优点将变得更加显而易见。如本文所使用的术语“团矿”是指可以任选地包含粘合剂的经压实的颗粒。如本文所使用的这种表述涵盖了团矿以及其他形状或形式的经压实的和/或致密的材料混合物或颗粒,例如球团矿、烧结矿、团块和砖制品,其可以在进行或不进行在高于环境温度的温度下压实和/或处理的情况下产生。如本文所使用的表述“原材料”是指可以用于本公开的方法的起始材料。例如,这种起始材料可以是废料、工业废料或工业副产物。例如,原材料可以是有害的或无害的或其混合物。例如,原材料可以选自熔炼炉粉尘、浸出残渣、灰分、矿渣、精矿、浆料、浮选精矿、矿渣精矿、催化剂、氧化物、寿命终结的产品或它们的混合物。例如,原材料可以包含选自Pb、Cu、Ni和Co中的至少一种金属。如本文所使用的表述“黄渣层”是指主要包含As、Sb、Fe、Cu、Co和Ni的熔融层。例如,黄渣层还可以包含硫(例如硫可以具有较少的量)。例如,熔炉可以是竖炉、鼓风炉、烧结装置、回转窑或流化床。例如,熔炉可以是烧结装置、回转窑或流化床。例如,熔炉可以是竖炉、回转窑、烧结装置或流化床。例如,熔炉可以是竖炉。例如,熔炉可以是鼓风炉。例如,熔炉可以是回转窑。例如,熔炉可以是流化床或烧结装置。例如,熔炉可以是鼓风炉。例如,熔融装置可以是电炉、鼓风炉、反射炉或旋转炉。例如,方法可以包括控制多层产物中存在或不存在黄渣层。例如,所获得的产物可以包含:布置在多层产物的顶部的第一层,所述第一层包含矿渣;布置在所述第一层下方的第二层,并且所述第二层包含锍;任选的布置在所述第二层下方的黄渣层;以及任选的布置在所述第二层下方或所述黄渣层下方的底层,并且所述底层包含至少两种金属的合金。例如,所获得产物可以包含:布置在多层产物的顶部的第一层,所述第一层包含矿渣;布置在所述第一层下方的第二层,并且所述第二层包含锍;任选的布置在所述第二层下方的黄渣层;以及任选的布置在所述第二层下方或黄渣层下方的底层,并且所述底层包含选自Pb、Bi、Ag、Au和Sb的至少两种金属的合金。例如,团矿可以包含助熔剂。例如,助熔剂可以包含二氧化硅、氧化铁和/或氧化钙。例如,团矿可以包含选自硫源和铁源的至少一种添加剂。例如,可以通过将含铜的材料连同选自硫源(例如元素硫、硫化物和硫酸盐)、助熔剂、氧化钙源、氧化铁源、SiO2及它们的混合物的成分一起混合并制团来获得团矿。例如,可以通过将含铜的材料连同选自硫源、助熔剂、氧化钙源、铁源或氧化铁源、SiO2及它们的混合物的成分一起混合并制团来获得团矿。例如,可以通过将含铜的材料、含镍的材料、含钴的材料以及它们的混合物连同选自硫源、助熔剂、氧化钙源、铁源、SiO2及它们的混合物的成分一起混合并制团来获得团矿。例如,碳源可以有效地用作还原剂和/或用于提供熔炉的热平衡。例如,碳源可以选自煤、焦炭及其混合物。例如,碳源可以选自活性炭、焦炭屑、碳或石油焦碳、柴油、天然气和其他烃(例如丙烷、乙烷、乙醇、甲醇和沥青)以及它们的混合物。例如,方法可以包括将铁源供入鼓风炉。例如,铁源可以是氧化铁。例如,方法可以包括将金属铁(Fe0)源供入鼓风炉。例如,方法可以包括控制第二层的组成。例如,方法可以包括控制第二层的硫含量并且如果硫含量超过预定值则将铁源供入鼓风炉,致使第二层达到给定的金属化水平。例如,方法还可以包括将多层产物的层至少基本上彼此分离。例如,第一层可以包含氧化铁和/或氧化钙和二氧化硅。例如,第一层可以包含氧化铁和/或氧化铜。例如,第一层可以包含氧化铁、氧化铜、氧化镍和氧化钴中的至少一种。例如,第二层可以包含Cu、Fe、Pb、S或其混合物。例如,第二层可以包含Cu-Fe-Pb-S。例如,第二层可以包含Cu-Fe-Pb-S的混合物。例如,第二层可以包含Cu-Ni-Co-Fe-S。例如,第二层可以包含Cu。例如,第二层可以包含Ni。例如,第二层可以包含Co。例如,黄渣层可以包含Fe和As。例如,黄渣层可以包含Fe、As和Ge。例如,黄渣层可以包含Cu、Fe、As和Ge。例如,黄渣层可以包含Fe、As和Ge,并且方法还可以包括从黄渣层中回收Ge。例如,黄渣层可以包含Fe、As和Ge,并且方法还可以包括通过至少一种化学或物理技术从黄渣层中回收Ge。例如,黄渣层可以包含Ni。例如,黄渣层可以包含Co。例如,黄渣层可以包含Cu、Ni和Co,并且方法还可以包括从黄渣层中回收Cu、Ni和Co。例如,黄渣层可以包含Cu、Ni和Co,并且方法还可以包括通过至少一种化学或物理技术从黄渣层中回收Cu、Ni和Co。例如,黄渣层可以包含至少30重量%的铁。例如,黄渣层可以包含约55重量%至约75重量%的铁。例如,黄渣层可以包含约55重量%至约90重量%的铁。例如,黄渣层可以包含至少30重量%的(Fe+Ni+Co)。例如,黄渣层可以包含约55重量%至约90重量%的(Fe+Ni+Co)。例如,底层可以包含选自Pb、Bi、Ag、Au和Sb的至少两种金属的合金。例如,底层可以包含选自Pb、Bi、Ag、Au、Pt和Sb的至少两种金属的合金。例如,废气可以包含As。例如,废气可以包含In。例如,废气可以包含As和任选的Ge。例如,方法可以包括在鼓风炉的竖井的上部使用进气口,由此在装填熔炉时使逸散性排放最小化。例如,方法可以包括在鼓风炉的竖井的上部使As、In、Ge和Sb中的至少一种烟化以便从熔炉废气中进一步回收/稳定化。例如,团矿可以包含含铜的材料。例如,团矿可以包含含镍的材料。例如,团矿可以包含含钴的材料。例如,含铜的团矿可以包含含铜的材料。例如,含铜的材料可以是铜精矿、熔炼炉粉尘、浸出熔炼炉粉尘、浸出残渣、焙烧炉粉尘或它们的混合物。例如,含铜的材料可以是含铜的矿渣、含铜的金属合金、铜精矿、熔炼炉粉尘、浸出熔炼炉粉尘、浸出残渣、焙烧炉粉尘、废催化剂、含铜的工业副产物、含铜的生产废料、寿命终结的产品或它们的混合物。例如,含铜的材料还可以包含以矿渣、金属合金、精矿、熔炼炉粉尘、浸出熔炼炉粉尘、浸出残渣、焙烧炉粉尘、废催化剂、工业副产物、生产废料、寿命终结的产品或它们的混合物的形式的镍和/或钴。例如,含镍的材料可以是含镍的矿渣、含镍的金属合金、镍精矿、含镍的熔炼炉粉尘、废催化剂、含镍的工业副产物、含镍的生产废料、寿命终结的产品或它们的混合物。例如,含钴的材料可以是含钴的矿渣、含钴的金属合金、钴精矿、含钴的熔炼炉粉尘、废催化剂、含钴的工业副产物、含钴的生产废料、寿命终结的产品或它们的混合物。以下实施例是非限制性的。实施例1例如,进行从浸出残渣中回收铜和其他有价值的金属、同时去除源材料中含有的大量砷的过程的设备可以使用图1所示的方法。一旦在湿法冶金回路中被浸出以去除大部分铜和砷,则其变成含有几种金属(Ag、Cu、Au、Ge、Pb、Bi等)的浸出残渣。表1中提出了该组成的示例。表1:样品组成–实施例1As1-5%Ag500ppm-1000ppmGe500ppm-1000ppmPb10%-20%Bi1%-3%Cu5%-10%SiO215%-25%Zn0-5%Fe8%-15%S8%-14%图1示出了本实施例中用于处理这些类型的残渣的一般方法10。工艺线路包括分为以下更详细描述的三个区域的设备/过程:材料处理和制团区域、熔炉区域和气体净化区域。在鼓风炉12中挥发并在洗涤器14溶液中捕获的砷可以在CaSO4-臭葱石混合物或替代产品中被稳定,所述替代产品例如砷水铁矿的钙亚砷酸盐/砷酸盐和碱性钙亚砷酸盐/砷酸盐。还可以将硅酸盐水泥(Portlandcement)或其他添加剂加入到砷残渣中以增强其稳定性。1-处理和制团区域含有高含量砷的残渣的处理可需要封闭或通风良好的处理系统,直到残渣与水和其他组分共混。用于处理和制团的设备的区域可以配备有二级通风设备以确保共混区域中的适当的卫生条件。例如,在鼓风炉中加工之前可以将添加剂(例如CaO源和铁源例如铁矿石)与浸出残渣混合。可以提供单独的仓用于储存实施例1的材料或实施例2的粉尘(16,18)、铁矿石和CaO/CaCO3(添加剂储存装置20,22,24)。考虑到材料具有特定的物理和化学性质,每个仓(16,18,20,22,24)可以包含适当的材料和外围输送系统。可以考虑密封的进料螺杆和气动系统。可以将不同的混合系统和螺杆输送机用于浆料输送。例如,可以使用浆料泵以将进料/水糊料输送至混合器单元26,可以将水28混合于其中。制团可以用于压实颗粒材料。辊压机、砌块机或其他类似设备30可以用于此目的。可以将原料/添加剂压实成限定的形式和尺寸,使其能够用于后续的生产步骤。可以在最终团矿32中提供一些孔隙度以允许在加热团矿32的过程中释放气体,例如来自碳酸盐分解、硫酸盐分解或鼓风炉竖井中的砷-氧化物蒸发的CO2。在一些实施方案中,将压块机用于制团。这种制团方式简单并且需要的资本投资适度。例如,可以在通风区域中封闭机器以避免工作场所中存在细粉尘。一旦产生出团矿32,则可以进行干燥/固化。例如,根据例如干燥速率,该步骤可以使用三天或更少的时间。技术人员将会认识到,现场条件和所用设备(如果使用了设备)可以显著影响干燥速率。可以将所需量的进料、添加剂和水28供入混合单元26。根据所选的制团技术,可以将包含约10%至约20%湿度的湿混合物供入制团机30。基于所选的制团技术,技术人员可以选择合适的湿度。一经干燥和固化,团矿32可以具有约1%至约8%的最终湿度水平。2-熔炉区域2.1进料至冶炼单元图2所示的熔炉示意图中更详细地示出了图1的鼓风炉12。与参考图1所述的组件大体相似的图2的组件用加有前缀数字1的相同参考数字表示。如图2所示,可以将连续的焦炭层和团矿层(图1:分别是34,32)从顶部经由进料口101供入鼓风炉112。可以在熔炉(图1:12,图2:112)底部以相对高的体积(即,高压)注射工艺空气(图1:36;图2:136A,136B)。可以在熔炉(图1:12;图2:112)的顶部取出废气(图1:38;图2:138)。该废气(图1:38;图2:138)可以包含例如工艺气体和渗透空气(图2:103A,103B),其可以具有巨大体积。如图2所示,由于通过进料口101的高的空气纳入103A、103B,因此可以使用“开放”的熔炉进料口101。与工艺空气(图1:36;图2:136A,136B)相比,空气渗透103A、103B在体积上显著较高。这种渗透气体(图2:103A,103B)用于促进工艺气体中留下的一些CO的燃烧,并且还用于通过稀释将气体冷却到适当的温度。2.2冶炼单元参考图2,可以用熔炉焦炭(未示出)以提供热源和竖井105中的还原条件,使进料团矿(未示出)在鼓风炉112中熔融。随着熔融发生,团矿在熔炉112中熔融并下沉至熔炉的底部(炉缸107)。一些不可混合的层可以在熔炉112中形成,上层或顶层可以是包含CaO-FeO-SiO2-Fe2O3-Na2O等的矿渣109。还形成了“锍”层111,其刚好在矿渣层109下方,并且可以包含硫化铜、硫化铁和硫化铅。最后,第三层113可以包含金属铅和铋与大部分的银和金“金属合金”。矿渣109可以单独地流出(图1:40;图2:140)并且可以引导至堆放处或浮选处42,并且可以将锍111和金属113相一起流出(图1:44,图2:144)。参考图1,锍层48(其可以被引导以进行冶炼)在仍然呈液体的金属层(金属合金50)上凝固后,锍层和金属层可以在模具中进行分离。2.3第一基本原则–挥发As、In和一些Pb、Bi在高温下挥发。低p(O2)和高p(S2)还可以帮助给定微量元素挥发。根据所选的条件,一些元素将保留在凝聚相中或与熔炉气体一起离开。例如,该方法可以用中性、受控的还原条件或过量的硫(FeS2、S2等)进行以使大部分的砷、锑和铋挥发。如果需要,添加恰当形式的金属组分或者过度的还原可以通过形成黄渣组分减少砷和锑的挥发。参考图2,该黄渣层115通常位于锍层111和金属层113之间。许多硫酸盐在低温(例如低于800℃)的还原条件下分解。在中性或温和的还原条件下,As2O5(例如,在FeAsO4中)将在低于约900℃下分解,在煅烧材料中提供较少的砷。在进料/添加剂中含有的一些硫化物或甚至元素硫促进了某些元素挥发。例如,如图3所示,在方法200的示例中,在适当的条件(例如受控的温度和压力255)下,残渣251(或粉尘;参见:实施例2)和添加剂253的热处理可以使257In、Sb、As、Bi和其他挥发物烟化。例如,As硫化物和Sb硫化物是挥发性的(存在几种挥发性物质)。Bi硫化物在某种程度上也是挥发性的。当在系统中调整p(S2)时其他微量元素可以挥发。例如,在特定条件(例如受控p(S2)和金属化259)下可以进行冶炼。这可以例如通过将261硫、FeS2、FeS或少量的精矿加入到熔炉进料中来实现。还可以将其他硫添加剂加入到261。大体与参考其他附图描述的组件相似的图3的组件用加有前缀数字2的相同参考数字表示。2.4基本原则–金属化通过还原金属氧化物或通过向熔炉添加金属(例如Fe或Cu)可以产生熔炉中的金属元素。在高温下,硫(被添加或存在于进料中)将按照以下顺序与可用金属结合:Fe+S=FeS(锍)2Cu+S=Cu2S(锍)Pb+S=PbS(锍)2Bi+3S=Bi2S3(锍)2Ag+S=Ag2S(锍)再次参考图3,关于非挥发性组分263,调整熔炉进料中的总金属元素和硫可以允许大部分Cu归入锍211。在熔炉中添加铁矿石可以用于两个目的:允许在操作温度下获得流体矿渣209,但是还用于硫螯合目的。用这种控制系统中的金属化的方法,Pb、Bi、Ag和Au组分可以保留在金属相213中,即,例如如果没有足够的硫用于它们,则它们将停留在金属相213中。在方法200的实施方案中,锍211、矿渣209和金属213可以分离并使用适当的方法进行再循环。当以适当的方式设定热和化学条件时,可以在金属、黄渣、锍、矿渣和气相之间获得有利的行为。图4更详细地描述了实例300,所述实例300发生于加工干燥团矿(图1:32;图4:332)时的竖炉的不同层级(图1:12;图2:112;图4:312),所述团矿由浸出残渣(或粉尘;参见:实施例2)和添加剂制成。大体与参考其他附图描述的组件相似的图4的组件用加有前缀数字3的相同参考数字表示。如图4所示,风口空气(注射空气336)可以在熔炉312的下部317中与焦炭床反应,由此提供还原条件和维持熔炉热平衡所需的热量。矿渣309温度可以在1100℃与1350℃之间,而由于熔炉炉缸的热损失,铜锍311和金属313层可以处于稍低的温度。根据进料(装填料)的进料速率和化学组成,熔炉312可以以给定频率流出。矿渣309可以更频繁地流出340,而锍311和金属313相以减小的频率分别流出(344A,344B)或一起流出(未示出)。例如,从熔炉312中可以获得四种产物:熔炉矿渣309;用于冶炼或作为商业产品出售的熔炉锍311;熔炉合金(金属313;铅、铋和银含量高并含有大部分金);以及通向气体净化系统的工艺废气(含有粉尘;图4中作为挥发物示出,并夹带材料338)。在金属313锍311界面任选获得第五产物(黄渣315)。仍然参考图4,所述方法使用负压、空气渗透(303A,303B)。在适当的条件下进行热处理373以烟化As、Sb和其他挥发物,如参考图3的更详细的描述。进行在特定条件下的冶炼375以分离Pb、Bi、Ag、Cu等。图4的示意图显示出以下区域:氧化条件和低温377;还原条件(CO)和升高的温度371;以及金属化条件和高温375。3-气体净化系统主风扇可以吸取来自熔炉中的工艺气体和渗透气体。例如,使用高效湿洗涤系统可以清洗所有离开熔炉(500℃-700℃)的工艺气体。可以考虑不同的气体净化系统。一些示例如下:组合:热交换器+袋滤捕尘室+湿洗涤系统。2个湿步骤:骤冷塔+洗涤塔。3个湿步骤:骤冷塔+洗涤塔+湿电除尘器。返回图1,在其中所示的实例10中,废气38行进至气体净化系统,所述气体净化系统包括骤冷塔52、洗涤器/洗涤塔14和湿除尘器54。将水56用于气体净化系统。引导来自气体净化系统的固体和溶液58用于进一步的处理60。鼓风机62将来自系统的清洁气流吸至烟道64。实施例2本实施例与实施例1所述的方法类似并示于图1中。在这种情况下,将在铜精矿加工设备回收的粉尘用作该方法中的原料。这种材料由于其小的尺寸分布及其高的Sb和As含量而难以在铜熔炼炉中再循环。这种材料可以有利地在别处进行加工。本实施例的目标是用本技术提供这类材料的替代处理。如所表示的,铜粉尘的加工方法可以类似于用于浸出残渣处理的方法,并且可以包括制团、冶炼和气体净化步骤。用于焙烧炉粉尘处理的一般描述类似于浸出残渣加工(参见,例如图1和实施例1)。因为焙烧炉粉尘可以具有与浸出残渣非常不同的化学组成(高的铜含量,而没有铅或铋),因此原料在制团制备中需要不同量的每种添加剂。与浸出残渣加工的主要区别在于不必产生金属合金,因此在该实施例中除了气相之外仅产生锍和矿渣。任选地,金属层或黄渣层可以形成以收集砷并分别进行加工。存在的少量金属层(或黄渣)可以用作Ag、Au和PGM的收集器。铜粉尘的化学组成示于表2中:表2:铜粉尘样品化学组成Ag200ppm-800ppmCu15%-25%As3%-7%Sb0-5%Fe5%-15%SiO210%-25%S3%-7%这种从干燥静电除尘器中回收的粉尘是非常细的固体,其大部分质量包含在低于10微米直径的颗粒中,因此难以在铜熔炼炉中进行再循环。例如,加工线路可以包括三个区域:处理和制团区域、熔炉区域和气体净化区域。1-处理和制团区域。对于储存和处理系统,铜粉尘的许多关注点类似于浸出残渣。对于焙烧炉粉尘更复杂的一个方面是其物理特性:超细的尺寸分布且非常干燥,这使其倾向于在处理过程中成为空传污染。考虑到高含量的砷,在储存和输送系统的设计中可能需要特别的注意。例如,可以考虑使用具有气动输送的密封或加压仓。2-熔炉区域设计用于铜粉尘的冶炼熔炉可以类似于浸出残渣冶炼熔炉。例如,根据铜粉尘的特定化学定制助熔参数。例如,将熔炉的底部(炉缸)的绝热定制为用于待包含的材料,在这种情况下,所述材料为锍且不为铅合金,因此具有较高的熔点。在这个实施例中,从熔炉中获得三种产物:熔炉矿渣、熔炉锍(商业产品)和工艺废气。可以将鼓风炉的容量调整至可用于加工的铜粉尘的量。实施例3图5中示出了方法400的另一实例。方法400可以包括以将有价值的组分有效分离成四个(或五个)主要流之一的方式处理原材料(例如熔炼炉粉尘402)。最终产物流可以是金属404、矿渣406、锍408、粉尘434和任选的黄渣410。待加工/再循环的粉尘402可以与用于产生稳定矿渣的助熔剂412和任选的其他添加剂414混合,所述添加剂414允许控制每个所产生的流中的元素的分离。这些材料可以与任何再循环的流418A-D一起共混(416)。还可以添加水和粘合剂(未示出)以帮助凝集不同的进料。然后将该混合物送至制团420,其中材料可以被压实成砖制品。在被供入熔炉424之前,这种砖制品可以容易地储存和固化以减小其湿度含量(干燥)(422)。可以将砖制品以与焦炭交替的层供给至熔炉424。可以将空气/氧气注入熔炉424的底部。挥发物426通过废气烟道排出,挥发物426可以输送通过两个废气处理阶段。第一洗涤阶段428可以是酸洗429。酸洗429可以通过在液滴中夹带细粒来去除颗粒。酸洗429还可以将砷和铜部分溶解于溶液中。可以在固/液分离432中将富含Cu和As的洗涤溶液430与收集的粉尘分离。回收的固体434可以再循环(418A)至共混阶段416,同时溶液430可以被输送用于进一步处理以回收铜并稳定砷(436)。二级洗涤器438可以用于去除剩余的SO2并产生清洁气体440。碱性浆料442(例如:Ca(OH)2)可以用于产生石膏和/或CaSO3。所产生的石膏444可以任选地再循环(418B)作为助熔剂(CaO源和/或硫源)。一旦产生足够量的矿渣、锍和金属,它们可以从熔炉424中流出。锍408可以以受控方式进行固化(446)以分离不同的相,然后进行处理以回收任何夹带的金属或某些元素。例如,可以使用磁重力或浮选448,其中PbS/金属精矿450可以从经研磨的锍452中浮选出来并返回至熔炉(418D)。经研磨的固化锍452的处理可以基于物理分离技术,例如粒级分离、重力分离技术、浮选磁分离等。可以将剩余的锍输送进行进一步处理以回收所含的铜454(冶炼、浸出等)。矿渣406可以以与锍408相似的方式进行后处理以收集夹带的锍和金属(受控固化+物理分离技术,例如重力浮选456),由此产生矿渣精矿458和矿渣尾矿460,所述矿渣精矿458可以再循环(418C)。任选地,工艺参数可以调整以有利地产生黄渣410、金属砷化物和锑化物的混合物,以便分离该阶段中的关键元素(Ge、Co、Ni等)。本文公开了用于处理粉尘的简单且有效的方法,其相比于现有方法提供了优点。本公开的方法可以在锍中回收大部分铜和一些银,同时在金属合金中回收Pb、Bi、Au和剩余的银。熔炉中所产生的锍可以进一步进行加工以回收所含的Cu和Ag。回收Cu、Ag、Au、Pb、Bi、Ge的方法相对简单并且存在低风险。通过将其他现有技术集合到本实施例中,其他金属(例如Sb、Zn)以及精制产物(例如精制的Pb、Bi、ZnSO4)的回收也是可能的。实施例4该实施例涉及从浸出残渣中回收Ge。程序和方法将200gm干燥的浸出残渣(32%Pb,7%Cu,2%As,1.4%Bi,0.11%Ge)与含有36.2gmSiO2+38.8gmCa(OH)2+60.4gmFe2O3和7.2gm铁粉(为增加金属化)的助熔剂混合。将19.1gm焦炭(碳)加入到装填料中以用作金属氧化物的还原剂。然后将全部装填料置于混合器中均匀混合。MgO炉缸用于熔融,其置于用于熔融的改进的马弗炉中。将熔炉完全密封并用以5L/min流动的氮气持续吹扫以带出粉尘和冶炼气。将熔炉的温度以150℃/h升至1300℃,在最高温度下保持30分钟的时间。在熔融后,将熔炉以与加热相同的速率进行冷却。将熔炉排气装置连接于洗涤器,该洗涤器处理有害气体以避免排放至环境中。分析熔融产生的矿渣、锍、金属和黄渣分别是总装填料重量的35%、9%、15%和7%。由于粉尘和气体造成的重量损失为装填料的34%。在冶炼过程中,所含的As的约50%在气相中被去除(作为不同的物质)。残渣的大部分Pb和Bi(分别为80%和90%)在金属相中被回收。在黄渣中发现大约70%Ge,黄渣还含有相当部分的砷。一定体积的黄渣用于获得至黄渣的最大量的Ge回收(较高的体积通常提高Ge回收)。黄渣的组成对Ge的回收也有影响,特别是黄渣的Fe含量,所述Fe含量与系统的氧势有关(较高Fe含量的合金产生较高的Ge回收)。在具有较高金属化的情况下,黄渣还可以用作砷收集器,导致在熔炉废气中有待回收较低的砷量。固化黄渣的矿物学显示出,Ge作为‘FeGe’相与金属Fe分离,该‘FeGe’相形成具有5μm-10μm直径的球形。黄渣可以用于浸出过程以回收Cu、Ge和其他有价值的金属,同时稳定砷。实施例5该实施例涉及从具有高砷含量的铜粉尘中回收各种金属的方法。程序和方法将200gm干燥的残余滤液(粉尘)与24gm(10.7%的粉尘)Cu精矿混合。然后将46.3gm助熔剂(9.2gmCaO+34.4gmFe2O3)与粉尘和精矿混合。在混合物中将全部的装填料共混在一起。铜粉尘组成:18.8%Cu,9.7%Fe,2.3%Sb,6.1%As,6.2%Al,8.5%Si,6.8%S。Cu精矿:21.1%Cu,37.5%Fe,31.9%S。将装填料与水(90ml)混合以制成糊料。将液压机用于制备团矿。然后将团矿在80℃下干燥2h以减小水含量(<13%湿度)。平均砖制品密度为1.17gm/cc。砖制品具有足够的孔隙度用于使气体在加热过程中逸出。将所有的团矿装入在底部具有8gm焦炭(碳)的MgO炉缸中。将炉缸置于改进的马弗炉中,马弗炉具有受控的气氛,以5L/min流动的氮气。熔炉的温度升至200℃保持2h,以便蒸发所有的湿气。然后将熔炉的温度以150℃/h升至1300℃保持40分钟。在熔融后,将温度逐渐降低至室温。将熔炉排气装置连接至洗涤器,在将废气释放至环境中之前,该洗涤器处理有害组分。分析熔融产生总装填料重量的17%的锍和47%的矿渣。由于粉尘和气体造成的重量损失为36%。将大部分铜和银回收至锍。在该过程中消除了约84%的As。可以使由此过程产生的锍按原样进行商业化或可以进一步进行加工以降低其As和Sb含量。固化锍的矿物学显示出三个主要相:基质(Cu-Fe-S)、Sb-Cu化合物和As2Fe化合物,注意到相组成仅表示矿物中的关联,并且组成可以更复杂。形成的基质显示出具有高的(Cu2S)和较低的CuCu-S-Fe矿物的交替的层。基质(主要是Cu载体)中具有相对低含量的Sb或As,因此As-Sb在技术上可以通过矿物加工/湿法冶金技术进行分离,因为它们包含在可以从基质释放的颗粒中。发现As和Sb缔合在一起;使得它们容易从基质中去除。实施例6该实施例涉及从浸出残渣中回收各种金属的方法。程序和方法将250gm干燥的浸出残渣(10%Pb,7%Cu,5%As,1%Bi)与助熔剂[48gmSiO2+32.4gmCaO+48.97gmFeO(OH)]混合。使用FeO(OH)作为FeO源。将6.45gm元素硫与装填料混合以增加锍形成。将16gm焦炭(碳)加入到装填料中,其中一半置于MgO炉缸的底部,并且将剩余部分与助熔剂和粉尘混合。将6.45gm高碳钢块置于炉缸的底部以增加金属化。然后将炉缸置于在密封环境中的改进的马弗炉中,所述环境具有5L/min的氮气流。将熔炉的温度以150℃/h升高至1300℃,在最高温度下保持40分钟。在熔融后,将熔炉以相同速率进行冷却。将熔炉排气装置连接于洗涤器,在将气体释放至环境中之前,该洗涤器处理有害气体。分析熔融产生矿渣、锍、金属和黄渣,分别为总装填料重量的46%、39%、6%和5%。由于粉尘和气体造成的重量损失为32%。所产生的合金含有73%Pb、12%Bi、5%Sb、4%Cu和1.3%As,大部分Pb、Bi、Ag和Au回收至该相中。大部分投入的铜被回收至锍,并且硫存在于锍(60%)和矿渣(30%)中。仅有10%的S损失于熔炉废气(粉尘+含硫物质)。以这样的方式呈现本公开的实施方案,以便证明当可应用时可以进行实施方案的每个组合。因此,以相当于将引用任何前述权利要求的所有实施方案(涵盖之前呈现的实施方案)做成从属权利要求的方式在说明书中呈现这些实施方案,由此证明它们可以以所有可能的方式组合在一起。例如,当可应用时,本公开由此涵盖段落[0009]至[00131]的实施方案以及段落[0005]至[0008]的方法之间的所有可能的组合。尽管特别参考具体的实施方案进行了描述,但应理解的是,对其进行的许多修改对于本领域技术人员来说是显而易见的。权利要求的范围不应受限于本公开和附图中提供的具体实施方案和示例,而应作为整体给予与本公开一致的最宽泛的解释。当前第1页1 2 3