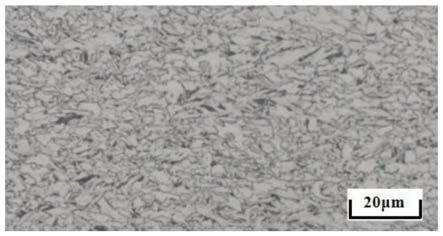
管线用屈服强度360mpa级热轧钢板及其制造方法
技术领域
1.本发明涉及一种石油天然气管线用钢,特别涉及一种管线用屈服强度360mpa级热轧钢板及其制造方法,具体而言,涉及采用低精轧压缩比生产管线用屈服强度360mpa级热轧钢板,属于石油天然气管线用钢技术领域。
背景技术:2.管道运输是长距离输送石油、天然气最经济、最安全的输送方式,具有高效、经济、安全、无污染等特点。为了提高输送效率、降低能耗、减少投资,长输管线向厚规格、高压、大口径输送发展已成为趋势。
3.新建热连轧机组不断向更宽规格、更高强度方向发展,以满足输送主线长距离、高压需求。另一方面,作为大多数传统热连轧机组,由于其飞剪能力有限,中间坯厚度限制在50mm以下,如生产厚度为15.8mm以上规格钢板,精轧压缩比只有3.16。精轧压缩比下降,冲击韧性及落锤撕裂试验(dwtt)断口剪切面积平均值性能会降低,管线钢精轧压缩比一般要求在4.0以上,低精轧压缩比无法满足生产厚规格管线钢性能要求。
4.如设备改造,生产厚度为15.8mm以上规格钢板,精轧压缩比保证4以上要求,则中间坯厚度需达到64mm以上,中间坯剪切投资巨大,会造成固定成本增加,不利于经济性生产。
5.申请公布号为cn103572025a的中国专利申请公开了一种低成本x52管线钢的生产方法,所述生产方法包括将铁水进行脱硫、转炉冶炼、连铸成管线钢连铸坯,还包括将所述管线钢连铸坯均热至1160-1200℃、利用粗轧机进行3-7道次粗轧,得到中间坯,利用精轧机进行4-7道次精轧,最后已50-100℃/s的冷却速度快速冷却至550-610℃,卷取后获得产品。其化学成分重量百分比为:c:0.08%-0.12%,si≤0.35%,mn:1.10%-1.40%,p:≤0.025%,s:≤0.025%,ti:0.010%-0.020%,其余为fe和不可避免的杂质;根据其生产的产品厚度只有2.0-10.0mm,不能满足生产16mm以上规格产品的要求。该发明c含量在0.08%-0.12%,处于包晶区,连铸坯易产生角裂缺陷,同时,碳含量高对冲击韧性不利。因此该设计不具备满足屈服强度360mpa级经济型低压缩比焊管用热连轧钢板制造方法要求。
6.申请公布号为cn101928884a的中国专利申请公开了一种x52管线钢及其生产方法,该发明使用炉卷轧机生产,不是常规热连轧机组;其化学成分为c:0.070~0.090%,si:
7.0.15~0.25%,mn:1.10~1.30%,s≤0.006%,p≤0.020%,nb:0.020~0.040%,n≤0.008%,其余为铁和不可避免夹杂;该项发明材料碳含量较高,对冲击韧性不利,由于未提供产品的厚度范围和实际性能,因此该设计不具备满足屈服强度360mpa级经济型低压缩比焊管用热连轧钢板制造方法要求。
8.申请公布号为cn1927486a的中国专利申请公开了一种低压缩比高级别管线钢生产工艺,该发明涉及高强度低合金钢生产工艺,包括工序:冶炼、精炼、板坯连铸、板坯加热、除鳞、热轧、轧后冷却、平整矫直。该发明可针对铸坯厚度较小的生产线生产厚规格管线钢,产品为x70,其化学成分为c:0.03~0.06%,si:0.15~0.25%,mn:1.55~1.65%,s≤
0.002%,p≤0.01%,nb:0.03~0.05%,ti:0.015~0.025%,mo:0.15~0.25%,氮、氢、氧、硫、磷含量总和小于100ppm,其余为铁和不可避免夹杂;该项发明针对x70,使用炉卷轧机生产,不是常规热连轧机组,因此该设计不具备满足屈服强度360mpa级经济型低压缩比焊管用热连轧钢板制造方法要求。
技术实现要素:9.本发明的目的是提供一种管线用屈服强度360mpa级热轧钢板及其制造方法,主要解决现有管线用屈服强度360mpa级热轧钢板的生产成本高、冲击韧性差及落锤撕裂试验(dwtt)断口剪切面积平均值性能低的技术问题。
10.本发明通过采用nb、ti合金化,严格控制保证产品最终落锤性能的关键固溶强化元素碳,控制ca含量在0.0015%-0.0040%以保证夹杂物球化效果,结合合适的炼钢、连铸、热轧工艺设计,在传统热连轧机组低精轧压缩比情况下采用严格控制精轧后机架压缩比的工艺,满足15.8mm以上厚规格热连轧钢板落锤等性能的要求。
11.本发明热轧钢板用于制造输送石油天然气的管道。
12.本发明采用的技术方案是,一种管线用屈服强度360mpa级热轧钢板,其化学成分重量百分比为:c:0.03-0.07%,si:0.10-0.20%,mn:1.20-1.30%,p≤0.020%,s≤0.010%,nb:0.025-0.035%,ti:0.013-0.023%,ca:0.0015-0.0040%,n≤0.006%,余量为铁和不可避免夹杂,上述元素含量须满足碳当量ce
pcm
为0.09-0.14%,其中ce
pcm
=c+v/10+mo/15+(cr+mn+cu)/20+si/30+ni/60+5b,式中:c、mn、cr、mo、v、ni、cu、si、b为热轧钢板中该元素的重量百分比。
13.本发明热轧钢板的金相组织为铁素体+少量珠光体,铁素体的晶粒度为8~12级;15.8~17.5mm厚热轧钢板的规定总延伸强度r
t0.5
为360~510mpa,抗拉强度r
m
为460~760mpa,断后伸长率a
50mm
为45~55%,-25℃冲击功值akv为300~450j,-20℃落锤撕裂试验(dwtt)断口剪切面积平均值sa≥85%,180
°
弯曲试验,d=2a合格。
14.本发明热轧钢板适用于制作石油天然气输送用焊管。
15.本发明所述的管线用屈服强度360mpa级热轧钢板的化学成分限定在上述范围内的理由如下:
16.碳:碳是最基本的强化元素,碳溶解在钢中形成间隙固溶体,起固溶强化作用,与强碳化物元素形成碳化物析出,起到沉淀强化作用。本成分体系充分利用c的强化作用。但它是易偏析元素,含量高会增加连铸坯的中心偏析,也降低材料韧性,恶化性能。同时碳太高易进入低碳钢的包晶区。碳太低,会降低钢种强度。因此,本发明综合考虑传统热连轧机组生产厚规格钢板精轧压缩比低会降低韧性的因素,设定的c含量为0.03~0.07%。碳成分控制是实现本发明的技术关键。
17.锰:锰也是本成分体系主要元素,可以起到固溶强化的作用,是钢中补偿因碳降低而引起强度损失的最主要且最经济的强化元素。mn还是扩大γ相区的元素,可降低钢的γ
→
α相变温度,有助于获得细小的相变产物,可提高钢的韧性。但mn是易偏析元素,含量高会增加连铸坯的中心偏析。mn是本发明成分体系中严格控制的元素,进一步限定mn含量为1.20~1.30%。
18.硅:硅在钢中通过固溶强化适当地提高钢的强度,过高的si含量会降低mn/si比,
对板坯的表面质量和焊管的焊接性能有不良影响,焊接韧性随mn/si比的提高而提高。但si过低将影响ca处理钢的浇注质量。mn/si在5~10之间最优,本发明限定si含量为0.10%~0.20%。
19.硫和磷:硫和磷元素过高会对材料韧性和塑性有不利影响,而硫和璘过低,又会增加炼钢的脱硫和脱磷成本。考虑经济型生产,本发明限定s≤0.010%,p≤0.020%。
20.氮:氮含量过高会严重恶化材料的塑性和韧性,本发明限定n≤0.006%。
21.钛:是一种强的固n元素。微量的钛就能起着强化的作用,它的影响是通过tin的形成,这种细小的tin粒子可有效阻碍板坯再加热时的奥氏体晶粒长大,从而对提高最终产品的韧性有积极的作用。此外,tin粒子在焊接时还可避免焊接热影响区的晶粒长大,改善焊接热影响区的冲击韧性。本发明限定ti含量为0.013~0.023%。
22.铌:是低合金高强度钢的主要微合金化元素,主要起细晶强化作用。通过热轧过程中nbc应变诱导析出阻碍形变奥氏体的回复、再结晶,经控制轧制和控制冷却使非再结晶区轧制的形变奥氏体组织在相变时转变为细小的相变产物,使钢具有较高强度和高韧性。为达到15.8mm以上厚度规格钢种所需的强度,通过增加铌含量提高强度以弥补降低碳、锰含量造成的强度损失,根据试验结果,本发明限定nb含量为0.025%~0.035%。
23.钙:采用钙处理,进行硫化物变态处理,提高钢板韧性。本发明限定ca含量为0.0015~0.0040%。
24.碳当量:冷裂纹是管线钢焊接过程中可能出现的一种严重缺陷,碳当量是衡量钢的焊接裂纹倾向性的依据。碳当量ce
pcm
=c+v/10+mo/15+(cr+mn+cu)/20+si/30+ni/60+5b。综合考虑焊接无裂纹及钢种的高强度、高韧性要求,碳当量ce
pcm
为0.09-0.14%。
25.一种管线用屈服强度360mpa级热轧钢板的制造方法,该方法包括:
26.钢水经连铸得到连铸板坯,其中所述钢水化学成分的重量百分比为:c:0.03-0.07%,si:0.10-0.20%,mn:1.20-1.30%,p≤0.020%,s≤0.010%,nb:0.025-0.035%,ti:0.013-0.023%,ca:0.0015-0.0040%,n≤0.006%,余量为铁和不可避免夹杂,上述元素含量须满足碳当量ce
pcm
为0.09-0.14%,其中ce
pcm
=c+v/10+mo/15+(cr+mn+cu)/20+si/30+ni/60+5b,式中:c、mn、cr、mo、v、ni、cu、si、b为热轧钢板中该元素的重量百分比;控制连铸板坯中夹杂物等级,连铸板坯中夹杂物等级按美标astm e45夹杂物分析标准,采用方法a进行检验,其中,a类、b类、c类、d类夹杂物等级均控制在2.0级以下;控制连铸板坯中心偏析等级在曼内斯曼标准2级以下;
27.连铸板坯于1140~1180℃,加热150~240min后进行热轧,所述的热轧为两段式轧制工艺,粗轧为6道次连轧,在奥氏体再结晶温度以上轧制,粗轧结束温度为950~990℃;中间坯厚度为49-50mm;精轧为6道次连轧,精轧入口温度为930~970℃,精轧结束温度为800~840℃;精轧后,控制钢板厚度为15.8~17.5mm,层流冷却采用前段冷却,层流冷却速度为15~25℃/s,卷取温度为500~540℃时卷取得热轧钢卷。
28.进一步,所述精轧,精轧机为7机架连轧机,精轧机第5机架的压下率为0,精轧机第6机架的压下率为14-16%,精轧机第7机架的压下率为12-14%。
29.热轧工艺以及其中热轧钢板表面氧化铁皮控制是实现本发明的技术关键。通过计算,本发明成分体系a3为823℃,a1为704℃。本发明所采取的热轧工艺均是基于本发明成分体系和计算的相变点。
30.本发明采取的生产工艺制度的理由如下:
31.1、连铸板坯中心偏析的设定和连铸板坯中夹杂物等级的设定
32.连铸板坯中心偏析控制和钢水夹杂物控制是实现本发明的技术关键,为保证热连轧机组在低精轧压缩比时,还要有足够的韧性,必须控制连铸板坯中夹杂物等级。本发明设定控制连铸板坯中夹杂物等级,连铸板坯中夹杂物等级按美标astm e45夹杂物分析标准,采用方法a进行检验,其中,a类、b类、c类、d类夹杂物等级均控制在2.0级以下;控制连铸板坯中心偏析等级在曼内斯曼标准2级以下。
33.2、连铸板坯加热温度和加热时间的设定
34.连铸板坯加热温度和时间的设定在于保证连铸坯中碳化铌和碳氮化铌得到充分溶解,并不致使原始晶粒长得过大。因此加热温度对于本发明技术方案非常重要,温度过低或加热时间过短,连铸板坯中碳化铌和碳氮化铌不能充分溶解,而温度过高,加热时间过长,板坯原始组织粗大,会使钢板韧性降低。本发明设定连铸板坯加热温度为1140~1180℃,加热时间为150~240min。
35.3、粗轧结束温度的设定
36.粗轧轧制过程控制在奥氏体再结晶温度以上轧制,确保得到均匀细小的奥氏体晶粒。因此本发明设定粗轧结束温度为950~990℃。
37.4、中间坯厚度和精轧入口温度的设定
38.为了获得良好的冲击韧性,尤其对于厚度≥15.8mm的热连轧钢板,需要控制精轧阶段较高的有效压缩比和较低的精轧入口温度。有效压缩比为精轧阶段发生在奥氏体未再结晶区温度区间变形的压缩比,其与精轧入口中间坯厚度和温度有关。现有常规热连轧机组飞剪剪切的最大钢板厚度为50mm,综合考虑,本发明设定中间坯厚度为49-50mm,控制精轧压缩比在3.16以下;本发明精轧入口温度为930~970℃。
39.5、精轧机机架负荷分配的设定
40.精轧机为7机架轧机,通过试验研究发现,精轧低温大压下有利于提高冲击韧性,尤其是后道次影响明显。综合考虑,本发明设定精轧机第6机架的压下率为14-16%,精轧机第7机架的压下率为12-14%;为精轧机第6机架、第7机架获得大压下率,精轧机第5机架的压下率为0,其它各机架选择自动负荷。
41.6、精轧结束温度的设定
42.终轧温度设定的作用是,通过奥氏体未再结晶区轧制,得到内部有变形带的扁平状奥氏体晶粒,在随后的层流冷却过程中转变成细小的铁素体晶粒,发挥细晶强化的作用。因此本发明设定精轧结束温度为800~840℃。
43.7、层流方式和层流冷却速度的设定
44.本发明设定的精轧后的层流冷却速度非常关键,采用快的冷却速度来抑制铁素体晶粒的长大和tic在高温阶段的析出。快速冷却使得在较低温度下的铁素体内析出细小弥散的tic等粒子成为可能。冷却速度过慢,无法抑制tic在高温变形奥氏体中的提前析出;冷却过快,会对钢板韧性不利,也会对板形带来很大影响。本发明层流冷却采用前段冷却,冷却速度15~25℃/s。
45.8、卷取温度的设定
46.卷取温度主要影响带钢的组织和性能。卷取温度的设定主要考虑二次析出粒子相
的强化效果和晶粒度长大。卷取温度高有利于ti、nb合金碳、氮的粒子二次相析出,但容易导致基体铁素体组织长大,nb、ti微合金碳、氮化物析出物粗化,降低钢板的韧性;卷取温度过低,ti、nb合金碳、氮的粒子二次相析出被抑制,提高钢板强度的析出强化效果不佳。综合考虑,本发明设定热轧卷取温度为500~540℃。
47.本发明方法生产的热轧钢板的金相组织为铁素体+少量珠光体,铁素体的晶粒度为8~12级;15.8~17.5mm厚热轧钢板的规定总延伸强度r
t0.5
为360~510mpa,抗拉强度r
m
为460~760mpa,断后伸长率a
50mm
为45~55%,-25℃冲击功值akv为300~450j,-20℃落锤撕裂试验(dwtt)断口剪切面积平均值sa≥85%,180
°
弯曲试验,d=2a合格。
48.本发明相比现有技术具有如下积极效果:1、本发明采用nb、ti合金化,严格控制保证产品最终落锤性能的关键固溶强化元素碳,控制ca含量在0.0015%-0.0040%以保证夹杂物变态效果,保证成分设计满足热连轧钢板性能稳定。结合合适的炼钢、连铸、热轧工艺设计,在传统热连轧机组低精轧压缩比情况下采用严格控制精轧后机架压下率的工艺,满足15.8mm以上厚规格热连轧钢板落锤等性能的要求。2、本发明要求连铸板坯中心偏析控制达到曼内斯曼标准2级以下,以及连铸板坯中夹杂物等级按美标astm e45夹杂物分析标准,采用方法a进行检验,其中,a类、b类、c类、d类夹杂物等级均控制在2.0级以下,这样可满足低精轧压缩比情况下获得较好的落锤等性能要求。3、本发明通过成分设计和制造工艺设计,可以满足传统热连轧机组低精轧压缩比情况下生产厚规格热轧钢带,从而满足厚规格、高压、大口径长输管线工程焊管用钢需求。在不增加精轧中间坯剪切能力的情况下,充分发挥传统热连轧机组产能,生产出质量满足要求的屈服强度360mpa级经济型低压缩比焊管用热连轧钢带。4、本发明的成分体系,结合合适的炼钢、连铸、热轧工艺设计,得到的屈服强度360mpa级经济型焊管用热轧钢板,与同精轧压缩比的其它钢板相比,组织、性能稳定,能更好的满足焊接、成形等工艺要求,扩大了传统热连轧机组生产厚规格、高压、大口径长输管线工程焊管用钢能力。5、本发明热轧钢板满足了传统热连轧机组不增加高额剪切设备能力的情况下,满足低精轧压缩比生产厚规格、高压、大口径长输管线工程焊管用钢的需求,填补了行业空白。
附图说明
49.图1为本发明实施例1热轧钢板的金相组织照片。
具体实施方式
50.下面结合实施例1~4对本发明做进一步说明,如表1~表3所示。
51.表1为本发明实施例钢的化学成分(按重量百分比计),余量为铁及不可避免杂质。
52.表1本发明实施例钢的化学成分,单位:重量百分比。
53.[0054][0055]
通过转炉熔炼,并经lf钢包精炼炉精炼工序吹脱硫处理和rh炉进行真空循环脱气处理,以及成分微调,得到符合成分要求的钢水,通过连铸得到连铸板坯。连铸板坯厚度为210~230mm,宽度为900~1600mm,长度为8000~11700mm。
[0056]
炼钢生产的定尺板坯送至加热炉进行加热,出炉除鳞后送至热连轧机组进行轧制。通过粗轧和精轧连轧机组控制轧制,经层流冷却后进行卷取,层流冷却采取前段冷却,产出合格热轧钢卷。热轧钢板的厚度为15.8~17.5mm。实施例1-4,中间坯厚度为49mm;热轧工艺控制参数见表2,表2中,f6压下率表示精轧机第6机架的压下率,f7压下率表示精轧机第7机架的压下率。
[0057]
表2本发明实施例热轧工艺控制参数
[0058][0059]
利用上述方法得到的热轧钢板,参见图1,热轧钢板的金相组织为铁素体+少量珠光体,铁素体的晶粒度为8~12级;热轧钢板的规定总延伸强度r
t0.5
为360~510mpa,抗拉强度r
m
为460~760mpa,断后伸长率a
50mm
为45~55%,-25℃冲击功值akv为300~450j,-20℃落锤撕裂试验(dwtt)断口剪切面积平均值sa≥85%,180
°
弯曲试验,d=2a合格。
[0060]
将本发明得到的热轧钢板进行取样,拉伸、弯曲试验取横向试样,冲击试验取纵向试样,按照《gb/t228.1-2010金属材料拉伸试验第1部分:室温试验方法》进行拉伸试验;按照《gb/t 232-2010金属材料弯曲试验方法》进行弯曲试验;按照《gb/t 229-2007金属材料夏比摆锤冲击试验方法》进行冲击试验,其力学性能见表3。
[0061]
表3本发明实施例热轧钢板的力学性能
[0062]
[0063][0064]
由表3可见,本发明得到的热连轧钢板具有良好的强韧性和弯曲成型性。
[0065]
除上述实施例外,本发明还可以有其他实施方式。凡采用等同替换或等效变换形成的技术方案,均落在本发明要求的保护范围。