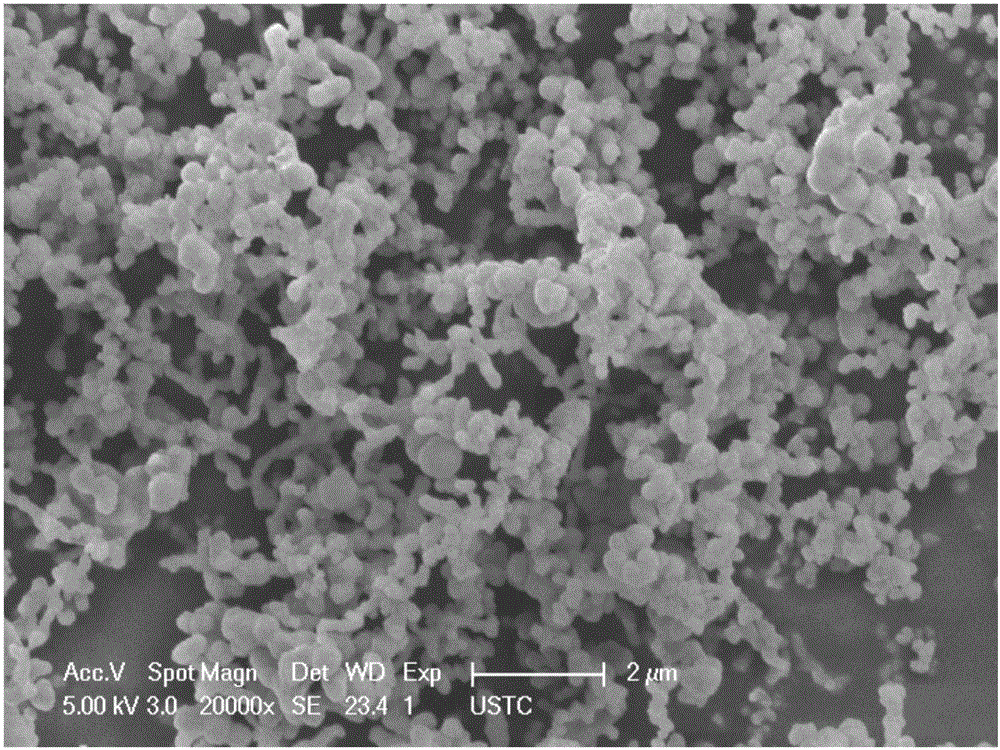
本发明涉及一种三维石墨烯的生产方法、所用装置、复合电极材料及其制备方法与其作为电化学储能器件的电极的应用,属于石墨烯生产及应用
技术领域:
。
背景技术:
:石墨烯是由碳原子组成的二维网状平面,它具有特异的光学特性、超高的电子迁移率、极高的热传导性能和良好的化学稳定性。石墨烯还可以被看作是大的层片分子,其双面都可以吸附小分子物质,此外还具有较高的力学性能和透光性,这些特性导致石墨烯有望在超导、电化学储能和聚合物增强方面获得巨大的发展。石墨烯开放的表面和规整的层片结构有利于加快离子的吸脱附速度,如果用于超级电容器的电极材料可望获得优异的双电层容量和大的功率密度。自从人们认识到石墨烯可以单独存在以后就开始探索大量制备这种物质的方法,其中最大规模的制备方法是在水溶液中将石墨层片剥离,石墨氧化后由于存在大量的亲水性官能团,在强烈机械作用下通过调整溶液的pH值获得单独分散的氧化石墨胶体溶液,这就为石墨烯的制备提供了可能在溶液中被剥离的氧化石墨层片,再经过化学还原,即可制备出石墨烯。然而,石墨烯层与层之间具有强烈的范德瓦尔斯相互作用,分离后的石墨烯单层极易复合,严重抑制内在的高导电性机械强度,减小接触的表面面积,阻碍了应用。尽管人们已做出许多努力来应对这一挑战,例如,一个有效的方法是让多个单层的石墨烯片粘结在一起,构建三维(3D)网络,避免出现重复的单个的石墨烯片层。这对于保持散装石墨烯的内在特性十分重要,同时有利于促进其实际应用。人们一直致力于开发三维网络石墨烯的合成及应用(3D-smx)。典型的3D-smx文献报道包括石墨泡沫(GFS)、石墨烯海绵(GSS)和石墨烯气凝胶(气)。Ma及其团队(YanfengMaandYongshengChen,NationalScienceReview20152:40–53,17December2014)以泡沫镍为模板合成了GFS,该GFS继承了泡沫镍的大孔结构,具有连续的、相互关联的3D-smx。GSS具有与GFS相似的多孔结构,但部分取向或排列彼此近乎平行,这为GSS创造了各向异性层状结构。石墨烯海绵GSS被认为具有高效和可回收的吸收性能,其类似海绵。石墨烯气 凝胶通常是采用溶胶凝胶化学法制备,其包括以下步骤:还原氧化石墨烯(GO)形成高度交联的石墨烯水凝胶(GH),冷冻干燥和超临界干燥除去吸附水。虽然它们的结构和性质存在差异,但GFS,GSS和气体都具有优异的性能,如高的比表面积,孔隙度高,低密度,高的导电性和良好的机械性能。直到最近,大量的采用基于从碳源的直接增长的策略或装配/石墨烯片合成方法制备3D-smx的技术已被开发。三维结构使得石墨烯材料具有高的比表面积(SSA),较强的机械强度,快速的质量和电子传输动力学。三维结构可以用在更广泛领域包括用作吸附剂、催化剂、传感器,并用于能量储存和转换以及生物应用。然而,这些制备方法都太复杂,成本太高,引入的外来支撑模板等对性能有极大的负面影响,同时由于模板占据了材料空间,不可能形成原子或纳米量级的石墨烯间隙结构,可形成的石墨烯成分极少。另外,所有现有技术工艺复杂不能大规模工业化生产,能耗高,回收不彻底,有效利用少,生产成本高,难以被应用所接受。锂离子电池由于具有能量密度高、循环寿命好、安全性好、自放电率低、无记忆效应、污染小等优点,使得其在电动汽车、便携式电子设备等方面得到了广泛应用。电极材料作为锂离子电池的存储主体,其在电池工作过程中伴随着锂离子的嵌入与脱出,是提高锂离子电池容量与库伦效率、改善循环性能等电池参数的关键。自1990年代锂离子电池首次商业化以来,石墨一直作为商业化锂离子电池电极的主要材料。然而,石墨的理论比容量只有372mAh/g,且实际商业化应用中其比容量也已接近这一个理论值并很难提高,这大大限制了锂离子电池容量的进一步提升。所以,探索具有高比容量的电极材料有现实需求。电化学储锂的过程中,硅和锂可形成多种合金,其中Li22Si5的理论比容量高达4200mAh/g,其是石墨的10倍,在能合金化储锂的元素(Sn、Pb、Al、Au、Pt、Zn、Cd、Ag、Mg)中是最高的。此外,硅的嵌锂电位(0.4VvsLi/L1.)较低,从安全性能考虑,硅的电压平台略高于石墨,在充电时不会发生表面析锂的现象。而且,硅的来源广泛,无毒无害。因此,硅成为锂离子电池电极材料的研究热点之一。但是,由于锂离子在充放电过程中硅锂合金存在体积膨胀与收缩(高达300%),造成材料粉化、结构坍塌,引起活性物质与集流体之间的电接触变差,最终会导致电池的容量和循环性能迅速下降。针对这些问题,目前普遍采用的是将硅材料纳米化、硅材料与其他材料复合化、将纳米化与复合化结合等措施。硅材料纳米化是通过合成纳米颗粒、纳米线、纳米管、纳米薄膜等材料以降低硅在嵌锂/脱锂过程中的体积膨胀与收缩,减少对电池性能的不利影响。文献报道,当硅颗粒的尺寸合适时,特别是硅呈非晶时,硅的体 积膨胀现象会消失,利用合适的硅纳米颗粒作为电池电极材料引起业界广泛的兴趣。将硅材料与其他材料复合化是通过合成硅-化合物复合物、硅-金属复合物、硅-碳复合物来实现的,这些研究能够缓解体积膨胀,有效地改善了硅基电极材料的循环性能、提高了电池比容量、降低了不可逆容量。将上述两种方法结合是目前采用最广泛的方法。在众多基质材料中,碳材料由于具有良好的导电性、较小的体积膨胀等优点而受到重视。与纯硅材料相比,硅碳复合材料作为锂离子电池电极明显地改善了电池性能。碳材料种类众多包括天然石墨、人造石墨、软碳和硬碳。石墨由于具有良好的导电性、较大的比表面积、柔性、化学稳定性等,使得其在锂离子电池中得到广泛应用。相比于其它碳基底材料,高比表面积石墨可以为硅纳米粒子提供良好的分散性,保证整个电极结构的导电性,有利于实现电池的高倍率。目前作为锂离子电池电极的复合材料,特别是以纳米硅为原料的复合材料通常是采用预先制备的纳米硅粉与基体混合进而制得的,但存在以下缺点:第一,纳米硅的制备成本极高;第二,复合过程复杂,不均匀,引入杂质,特别是在有溶剂中操作和有后续高温处理的情况下,另外纳米硅极易被氧化从而丧失其储锂性能;第三,与现有工艺很难匹配,仍存在比容量低、循环性能不稳定等缺点,影响了复合材料及锂离子电池电极材料的发展,有待进一步改进,这对锂离子电容也是一样。另外,研究显示其它离子如钠、钾、镁和铝离子电池和离子电容的情况更为严重。另一方面,离子电池充电普遍太慢,不能满足日益增长的应用要求,有时用户为了应急,采用高电流快充,这对电池材料造成不可逆的负面影响,永久的减少了电池的容量和使用寿命。理论上,提高功率密度可通过使用高表面积具有合适孔径分布的电极材料,但是这些材料的能量密度通常较低,从而影响电极的整体性能。目前最为理想的材料是三维石墨烯,然而传统方法制备的石墨烯大多是二维平片叠加,很难形成三维结构,即使采用较为复杂的工艺生产出带有三维特征的石墨烯材料,所用方法都太复杂,成本太高,且引入的外来支撑模板等对性能有极大地负面影响。另外所有现有技术工艺都不能大规模工业化生产,能耗高,回收不彻底,有效利用率低,生产成本高。技术实现要素:为解决上述的缺点和不足,本发明的目的在于提供一种三维石墨烯的生产方法。本发明的目的还在于提供一种三维石墨烯的生产方法所用的装置。本发明的目的还在于提供一种复合电极材料。本发明的目的还在于提供一种上述复合电极材料的制备方法。本发明的目的还在于提供上述复合电极材料作为电化学储能器件的电极的应用。为实现上述目的,本发明提供了一种生产三维石墨烯的方法,该方法包括:将含石墨烯结构的材料通过选择性物理化学反应除去非石墨烯成分,生成三维石墨烯;优选地,在生成的三维石墨烯结构中,石墨烯成分占10-90v%,更优选为20-80v%;还优选所述生成的三维石墨烯含有通孔,其孔隙率至少为10%。根据本发明所述的方法,优选地,所述含有石墨烯结构的材料为人工合成的材料或天然的材料,所述含有石墨烯结构的材料至少含有石墨烯或类石墨烯成分;更优选地,所述含有石墨烯结构的材料包含石墨烯或类石墨烯成分及非石墨烯成分;其中,所述石墨烯成分或类石墨烯成分占5-90v%,进一步优选为10-80v%;更进一步优选地,所述含有石墨烯结构的材料包含金属碳化物、不完全石墨化碳、由热固性树脂炭化而成的硬碳、软碳;再进一步优选地,所述金属碳化物包括碳化硅、碳化钨、碳化钛或碳化钼。根据本发明所述的方法,优选地,所述物理化学反应包括热处理、变压膨胀、真空蒸发、气化、液体刻蚀和电化学溶解;更优选地,气化所用气体或刻蚀所用液体为可与材料中非石墨烯成分进行化学或物理反应生成气相或液相物质并能被排出材料结构而与石墨烯分离的气体或液体;进一步优选地,所述气化气体包括卤素气体、卤化氢气体、氧气、氢气、水蒸气、二氧化碳或氮氧化合物;所述刻蚀液体包括各种酸、碱和非中性溶液以及电化学溶液;更进一步优选地,所述卤素气体为氟、氯、溴或碘,卤化氢气体为氟化氢、氯化氢、溴化氢或碘化氢。根据本发明所述的方法,优选地,控制反应的条件为:反应温度200-3000℃,反应压力0.01-100MPa;更优选地,反应温度为300-2100℃,反应压力为0.1-10MPa;还更优选地,所述反应是在催化剂存在条件下进行的,所述的催化剂包含金属、合金、各种金属化合物和盐;进一步优选地,所述催化剂的活性组分选自以下物质中的一种或多种:a)贵金属,特别是钯、铂、铑、铼、钌、和它们的合金;b)过渡金属,特别是镍、铜、钴、铁、以及它们的合金;c)碱金属,特别是钠、钾、锂、钙和它们的合金;d)稀土金属;e)金属盐、金属化合物;和f)金属氢化物。根据本发明所述的方法,优选地,该方法还包括在气化反应过程中对三维石墨烯进行掺杂的操作;掺杂物包含选自以下物质中的一种或多种:a)硅、锗、锡、硫、铅、Sb、Li、Na、K、Pt、Au、Ag、Mg、Mo或Al;b)与a)中所述元素所形成的合金;c)过渡金属氧化物、碳化物、氮化物、硫化物,磷酸盐,无机盐、有机盐,以及金属氢氧化物;更优选地,所述掺杂物的掺杂量为制备得到的三维石墨烯体积的1-90%,进一步优选为5-70%;还更优选地,所述掺杂物占通孔体积的10-90%,更进一步优选为20-80%,再进一步优选为30-60%。根据本发明所述的方法,优选地,该方法包括以下具体步骤:将固体碳化硅与卤素气体、卤化氢气体或氢气进行气化反应,生成三维石墨烯与卤硅烷、卤氢硅烷或硅烷;更优选地,控制气化反应的条件为:反应温度200-1400℃,反应压力0.01-100MPa;进一步优选地,所述反应温度为300-1100℃,反应压力为0.1-10MPa;还更优选地,所述气化反应是在催化剂存在条件下进行的,所述的催化剂为钴和/或氯化钴。本发明还提供了一种复合电极材料的制备方法,该方法包括以下具体步骤:(1)制备具有通孔的电极基体材料;(2)将掺杂物的前躯体通入电极基体材料的通孔中,并将掺杂物以单质、合金或化合物的形式预留在孔中,形成含掺杂物材料;(3)将步骤(2)所述含掺杂物材料进行掺杂物封闭,以使掺杂物被封闭在材料的通孔内从而避免该掺杂物与外界气体或液体相接触,得到所述复合电极材料;优选 地,所述电极为负极。根据本发明所述的制备方法,优选地,所述含硅复合电极材料的制备方法包括以下具体步骤:(1)制备具有通孔的电极基体材料;(2)将含硅气体或含硅液体通入电极基体材料的通孔中,并将硅以单质硅为主的形式预留在孔中,形成含硅材料;(3)将步骤(2)所述含硅材料进行硅封闭,以使单质硅被封闭在含硅材料内从而避免该单质硅与外界气体或液体相接触,得到所述含硅复合电极材料;更优选地,所述电极为负极。根据本发明所述的制备方法,优选地,所述电极基体材料的原料包含但不限于天然石墨、由上述方法制备得到的三维石墨烯、软碳、硬碳石墨烯及其他电极材料;更优选地,所述其他电极材料包括Li4Ti5O12(LTO)、Li0.6Co0.4N、Co3O4、Fe3BO6、CuSn、FeSn、高分子材料PMT和、PFPT、硫、锂、及钠。根据本发明所述的制备方法,优选地,所述电极基体材料的比表面积为0.1m2/g以上;孔体积占该材料总体积的10-90%,更优选为20-80%,进一步优选为30-70%。根据本发明所述的制备方法,优选地,在步骤(2)所述的含硅材料中,所述硅占通孔体积的10-90%,更优选为20-80%,进一步优选为30-60%。根据本发明所述的制备方法,优选地,所述掺杂物包含选自以下物质中的一种或多种:a)硅、锗、锡、硫、铅、Sb、Li、Na、K、Pt、Au、Ag、Mg、Al或Mo;b)与a)中所述元素所形成的合金;c)过渡金属氧化物、碳化物、氮化物、硫化物,磷酸盐,无机盐、有机盐,以及金属氢氧化物。本发明还提供了上述复合电极材料的制备方法制备得到的复合电极材料。本发明还提供了上述复合电极材料作为电化学储能器件的电极的应用;优选地,所述电化学储能器件包括离子电池、离子电容以及电化学电容;更优选地,离子电池包括锂离子电池、钠离子电池、镁离子电池和铝离子电池;离子电容包括锂离子电容、钠离子电容、钾离子电容、镁离子电容和铝离子电容。本发明还提供了一种用于实现上述三维石墨烯的生产方法所用的装置,该装置包括:用于进行气化反应的反应器,用于将原料气体输送入反应器的进气系统,用于将 固体原料输送入反应器的进料系统,以及用于将气化反应产生气体导出反应器并冷凝进行收集的产物收集系统;其中:所述反应器设置温控设备,反应器中部为用于填充固体原料的主反应区,反应器下部设置有分布器;反应器底部设有原料气体入口和固体排渣口,顶部设置有固体进料口和产物气体出口;该产物气体出口设置有过滤器;所述进气系统包括储存气体原料的气源,该气源通过管路与反应器底部的原料气体入口相连;所述进料系统为多级锁斗进料系统,且该多级锁斗之间为串联设置,相邻锁斗之间的管路上设置有阀门,固体原料储罐通过管路与第一级锁斗的入口相连,最后一级锁斗的出口通过管路与所述反应器的固体进料口相连且该管路上也设置有阀门;所述产物收集系统包括冷凝器,该冷凝器的上游端与反应器顶部的产物气体出口相连,冷凝器的下游端依次串接冷凝液体收集装置以及尾气处理装置;优选地,所述反应器为气流床反应器、流化床反应器、喷动床反应器、固定床反应器或移动床反应器;还优选地,所述分布器所在区截面为锥形或倒梯形;还优选地,所述进气系统包括多个并联设置的气源;还优选地,气源与反应器底部的原料气体入口之间的管路上设置有气体干燥器;还优选地,产物收集系统的尾气处理装置为串联设置的分离、吸附或中和单元;还优选地,所述反应器的内衬和分布器为由耐腐蚀材料制成的;更优选地,所述耐腐蚀材料包括石英、石墨、陶瓷或不锈钢。本发明提供了一种利用碳化硅生产三维石墨烯的方法。本发明针对现有技术中三维石墨烯制备方法流程长,过程复杂,能耗高,产率低的缺点,采用催化气化的方法将碳化硅(SiC)中的Si选择性地进行气化而保留之中碳元素的石墨烯结构,保持一种三维的空间分布,从而达到高性能,流程短,能耗低,纯度高的效果。本发明涉及一种三维石墨烯材料的制备方法和气固反应器,该方法利用改进的化学法来腐蚀碳化硅得到三维石墨烯材料。通过本发明所述方法和反应器获得的三维石墨烯材料为具有三维连续结构的石墨烯宏观体,该方法和反应器可以实现宏量生产、且成本低廉、操作简便、产率高以及孔径结构易调控,所得三维石墨烯基泡沫材料具有导电率高、比表面积大等优点,为其在储能材料、导热复合材料、催化、相分离材料以及吸附材料等领域的应用奠定了基础。具体是:将碳化硅粉末与催化剂混合(如必要可造粒或压制成型),干燥后输送 至反应器中,保持反应器内温度和压力在适当范围内,与引入反应气体,如氯化氢或氯气反应生成三维石墨烯粉末,副产氯硅烷可另出售,其中反应所生成的大量余热可用于固体干燥,产生加热蒸汽用于氯硅烷精馏。为达上述目的,本发明提供了一种大规模生产三维石墨烯的方法,该方法包括:将固体碳化硅与卤素气体、卤化氢气体或氢气进行气化反应,生成三维石墨烯和卤硅烷(如四氯化硅)和卤氢硅烷(三氯氢硅)或硅烷(本发明中前述卤硅烷和卤氢硅烷统称为卤硅烷)。根据本发明的具体实施方案,本发明的方法中,所述卤素气体为氟、氯、溴或碘,优选为氯气;卤化氢气体为氟化氢、氯化氢、溴化氢或碘化氢,优选为氯化氢气体。本发明的方法中所需的固体碳化硅原料,可以是天然或人工合成的,也可以是回收的碳化硅磨料废渣直接作为反应原料,它与卤素气体、卤化氢气体或氢气进行气化反应,这可以将工艺流程简化,且能耗低、分离完全和利用充分,特别是反应副产物还能够为多晶硅和有机硅生产提供廉价的原料。根据本发明具体实施方案,固体碳化硅与卤素气体或卤化氢气体进行气化反应,除三维石墨烯外,还可以生成卤硅烷和卤氢硅烷;固体碳化硅与氢气进行气化反应,可以生成硅烷。根据本发明的具体实施方案,控制气化反应的条件为:反应温度200-1400℃,反应压力0.01-100MPa;优选地,反应温度为300-1100℃,反应压力为0.1-10MPa。根据本发明的具体实施方案,本发明的方法中,所述气化反应是在催化剂存在条件下进行的,所述的催化剂包含金属、合金、各种金属化合物和盐;优选地,所述催化剂的活性组分选自以下物质中的一种或多种:a)贵金属,特别是钯、铂、铑、铼、钌、和它们的合金;b)过渡金属,特别是钴、镍、铜、铁、以及它们的合金;c)碱金属,特别是钠、钾、锂、钙和它们的合金;d)稀土金属;e)金属盐、金属氧化物;和f)金属氢化物。根据本发明的更优选具体实施方案,本发明的气化反应中所用催化剂的活性组分为钴和/或氯化钴。可以是直接以金属钴和/或氯化钴作为催化剂,也可以将这些活性组分担载在适当的载体上。催化剂的使用主要是促进反应的进行,其用量通常可为固体碳化硅重量的0.01%-30%,优选为0.01%-10%。在本发明所述的温度范围及催化剂存在条件下,固体碳化硅与卤素气体、卤化氢气体接触进行气化反应的速度很快。因此,本发明中对反应时间不做特殊限定,整体反应时间根据反应物料、通气速度可适 当调整。通常情况下,所生成的卤氢硅烷或硅烷产物是被导出反应器后再通过冷凝方式收集,当观察到冷凝产物不再增多,即可停止反应(或是观察到固体碳化硅已完全反应,即停止反应)。根据本发明的通常操作条件,可控制反应气体与固体碳化硅的接触停留时间为0.01s-1000s。根据本发明的具体实施方案,本发明的方法中,所述气化反应在反应器中进行,所述反应器为流化床、稀相气流床、喷动床、固定床或移动床。固体物料(固体碳化硅,以及所述的催化剂,这些固体物料可以预先混合均匀)装填到反应器内,再向反应器内通入气化反应所需气体,在适宜的温度下进行气化反应,并将反应生成物(气态)导出反应器,经冷凝即可收集得到液态的卤硅烷或硅烷。根据本发明的具体实施方案,本发明的方法中,可以是将固体碳化硅原料粉碎、研磨、或制粒后再进行气化反应。具体可以是根据反应器的操作需求而选择适宜的粉碎、研磨或是制粒操作。根据本发明的具体实施方案,通常情况下,粉碎可以是将固体碳化硅粉碎至30目以下,研磨可以是将固体碳化硅研磨至20微米以下,粉碎或研磨的目的均是为了使固体物料与气体接触更充分以利反应。制粒的目的主要是为了避免气速过大的情况下将物料吹走,碳化硅与催化剂可分别制粒,或是混合制粒;在制粒的情况下,可适当加大气体与固体物料的接触停留时间,以利反应充分。根据本发明的具体实施方案,本发明的方法还包括将生成的卤硅烷进一步精馏分离的过程。具体的精馏分离可以按照所属领域的常规操作进行,本发明中不做赘述。根据本发明的具体实施方案,本发明的方法还包括从固体碳化硅制得三维石墨烯的过程。即本发明还提供了一种利用碳化硅生产三维石墨烯的方法,该方法包括:步骤一:对碳化硅硅原料干燥,制得干燥的固体碳化硅;步骤二:按照本发明前述方法对所述固体碳化硅进行回收利用。根据本发明的具体实施方案,所述碳化硅可以从硅切割废砂浆分离过程制得,该过程可以按照现有技术进行操作,例如,通过任何可行的方法从从硅切割废砂浆中回收颗粒SiC,所得固体碳化硅进一步干燥即可作为本发明气化反应主原料。在本发明的一具体实施方案中,对得到的固体碳化硅进行气化的过程按照以下操作进行:采用真空干燥设备对半干碳化硅进行干燥处理,得到干燥的固体碳化硅。根据本发明的具体实施方案,气化反应所生成的大量余热可用于固体干燥,产生加热蒸汽用于氯硅烷精馏提纯。在本发明的一具体实施方案中,本发明提供了一种由碳化硅制取三维石墨烯的方法,其包括如下步骤:1、选择原料添加含有金属的催化剂;2、干燥:采用真空干燥设备对半干粉末进行干燥处理(可以是回转炉,流化床,风力干燥等,可选择地,采用加压的方法或造粒方法压制成型),得到碳化硅硅粉;3、反应:将干燥或成型后的混合硅粉与氯气或氯化氢反应生成三维石墨烯(副产氯硅烷;转入下一步骤继续处理);更具体而言,本发明的一具体实施方案中的利用回收利用硅切割废砂浆的方法制备碳化硅的方法按照如下操作进行:干燥:在经过除杂和固液分离后,所得的固体的主要成分主要是碳化硅和硅。进一步干燥可除去水分对下游反应的影响。具体方式采用流化床干燥,回转炉干燥,或其它形式,甚至在造粒成型之后。添加催化剂成型:在添加含有金属的催化剂、压制成型;采用加压的方法或造粒方法来成型。气化反应:本发明不刻意分SiC,而是将催化剂和SiC粉可压制成型,也可以是粉末形式与氯气或氯化氢反应生成氯硅烷,如三氯氢硅或四氯化硅。而这类反应都是放热反应,在反应过程中会产生大量热能,需将反应器冷却下来。这样冷却剂可利用水或水蒸气,带出的热量可用于固液分离,干燥采用流化床,固定床,移动车等均可达到所需理想效果。而蒸汽用于氯硅烷的精馏提纯。精馏:在气化反应中产生的气相化合物含四氯化硅,三氯氢硅和氯气。这很容易由精馏装置进行提纯,采用物理分离方法对产品中不同氯硅烷进行分离(由于他们不同的沸点),获得所需品质和纯度的氯硅烷产品,可外售,或作为下游白炭黑、多晶硅或有机硅生产原料。本发明提供了一种利用碳化硅生产三维石墨烯的方法,该方法包括:将固体碳化硅与卤素气体、卤化氢气体或氢气进行气化反应,生成三维石墨烯与卤硅烷、卤氢硅烷或硅烷。根据本发明所述的方法,优选地,所述卤素气体为氟、氯、溴或碘;所述卤化氢气体为氟化氢、氯化氢、溴化氢或碘化氢。根据本发明所述的方法,优选地,控制气化反应的条件为:反应温度200-1400℃,反应压力0.01-100MPa;更优选地,反应温度为300-1100℃,反应压力为0.1-10MPa。根据本发明所述的方法,优选地,所述气化反应是在催化剂存在条件下进行的,所述的催化剂包含金属、合金、各种金属化合物和盐;更优选地,所述催化剂的活性组分选自以下物质中的一种或多种:a)贵金属,特别是钯、铂、铑、铼、钌、和它们的合金;b)过渡金属,特别是镍、铜、钴、铁、以及它们的合金;c)碱金属,特别是钠、钾、锂、钙和它们的合金;d)稀土金属;e)金属盐、金属氧化物;和f)金属氢化物;进一步优选地,所述催化剂的活性组分为钴和/或氯化钴。根据本发明所述的方法,优选地,该方法还包括将固体物料粉碎、研磨、或制粒后再进行气化反应的过程。根据本发明所述的方法,优选地,所述气化反应是在反应器中进行的,所述反应器为流化床、稀相气流床、喷动床、固定床或移动床。根据本发明所述的方法,优选地,该方法还包括将生成的卤硅烷和卤氢硅烷进一步精馏分离的过程。本发明还提供了一种生产三维石墨烯的方法,该方法包括:步骤一:对固体碳化硅预加催化剂和干燥;步骤二:按照权利要求1-7任一项所述的方法对步骤一得到的产物进行气化反应。综上所述,本发明提供了一种利用碳化硅生产三维石墨烯的方法及所用装置,其中主要是将催化剂与SiC的混合(可选择地,可在干燥之前加酸洗或其它方法先除出杂质,也可以在在粉末中加入适量催化剂,如必要可造粒或压制成型),与卤化氢或卤素气体甚至氢气选择气化反应生成各类卤硅烷或硅烷,本发明的技术也可有效利用切割废砂浆或硅渣固体成分中不能返回利用的碳化硅和被切割下的硅微粉,集硅切割废渣的分离与有效转换合为一体,同时生产出高附加值的工业原料,并可进一步利用反应余热进行物料干燥和产品精馏提纯,实现了硅切割废砂浆大型、高效、节能、连续和低成本完全循环利用。另一方面,本发明提供了一种利用含碳物生产三维石墨烯的方法。本发明针对现有技术中三维石墨烯制备方法流程长,过程复杂,能耗高,产率低的缺点,采用物理化学方法将含石墨烯结构的材料如不完全石墨化的碳材料中非结晶碳除去而保留石墨化的石墨烯成分。其中,所述含有石墨烯结构的材料可以是人工合成的也可是天然的,至少含有石墨烯或类石墨烯成分,包括单层和多层结构,而其它部分为非碳元素或结晶不完整的碳元素,这类材料包含金属碳化物(碳化硅、碳化钨、碳化钛、碳化钼)不完全石墨化碳、由热固性树脂炭化而成的硬碳、软碳等。所述物理化学反应包括真空蒸发或气化刻蚀,刻蚀气体(液体)为可与材料中非 石墨烯成分进行化学或物理反应生成气相或液相物质并能被排出材料结构而与石墨烯分离的气体(液体);刻蚀气体包括氟、氯、溴或碘,卤化氢气体、氟化氢、氯化氢、溴化氢或碘化氢等可与金属形成低沸点化合物的气体,也包括可与非石墨烯碳结构形成挥发气体的氧气、氢气、水蒸气、二氧化碳、氮氧化合物(NOx)等。其中,控制反应的条件为:反应温度为200-3000℃,反应压力为0.01-100MPa;优选地,反应温度为300-2100℃,反应压力为0.1-10MPa。其中,可选择的,所述反应是在催化剂存在条件下进行的,所述的催化剂包含金属、合金、各种金属化合物和盐;优选地,所述催化剂的活性组分选自以下物质中的一种或多种:a)贵金属,特别是钯、铂、铑、铼、钌、和它们的合金;b)过渡金属,特别是镍、铜、钴、铁、以及它们的合金;c)碱金属,特别是钠、钾、锂、钙和它们的合金;d)稀土金属;e)金属盐、金属氧化物;和f)金属氢化物;本发明涉及一种三维石墨烯材料的制备方法和气固反应器,用该反应器通过物理或化学反应来除去含石墨烯结构的材料中非石墨烯成分进而得到三维石墨烯材料。通过本发明所述方法和反应器获得的三维石墨烯材料为具有三维连续结构的石墨烯宏观体,该方法和反应器可以宏量生产、且成本低廉、操作简便、产率高以及孔径结构易调控,所得三维石墨烯基材料具有导电率高、比表面积大等优点,为其在储能材料、导热复合材料、催化、相分离材料以及吸附材料等领域的应用奠定了基础。根据本发明的更优选具体实施方案,催化剂的使用主要是促进反应的进行,其用量通常可为固体含石墨烯结构的材料重量的0.01%~30%。优先地为0.01%~10%,在本发明所述的温度范围及催化剂存在条件下,固体含石墨烯结构的材料与卤素气体、卤化氢气等气体接触进行气化反应的速度很快。因此,本发明中对反应时间不做特殊限定,整体反应时间根据反应物料、通气速度可适当调整。通常情况下,所生成的卤氢硅烷或硅烷产物是被导出反应器后通过冷凝方式收集,当观察到冷凝产物不再增多,即可停止反应(或是观察到固体含石墨烯结构的材料已完全反应,即停止反应)。根据本发明的通常操作条件,可控制反应气体与固体含石墨烯结构的材料的接触停留时间为0.01s~1000s。另外,在石墨烯中掺入某些元素后可极大的提高其特定性能,如在石墨烯中加入纳米硅可提高石墨烯作为锂离子电池电极的容量,掺入过渡金属Co、Ni等氧化物可改善电化学性能。同时,离子电池和离子电容充放电过程中SEI的过渡形成而造成锂、 钠、钾、镁、铝等离子的损失与电池性能的衰减,特别是首次充电会有这些元素的损失,一个较有效的补救方法是在电极中预先加入这些元素,从而抵消首次充电的损失。本发明的另一个实施例是在石墨烯中进行预掺杂,特别是将硅、锂和催化剂等直接作为掺杂物,集成生产和掺杂于一个过程,而避免反复多重工艺。其中,可选择的,是在反应过程中对三维石墨烯预掺杂以达到更佳性能效果,预掺杂物包含:a)硅、锗、锡、硫、铅、Sb、Li、Na、K、Pt、Au、Ag、Mg、Mo、Al等;b)与这些元素所形成的合金;c)过渡金属氧化物、碳化物、氮化物、硫化物,磷酸,各种盐以及氢氧化物等。掺杂的操作可以在生产石墨烯的各阶段加入,如a)在前期作为催化剂加入而留于石墨烯中;b)在中期通过反应在石墨烯结构中转换生成;c)在后期通过二次加入,掺杂量为成品石墨烯的1-90%,优选地为5-70%。这些元素可以在生产过程中以催化剂的形式加入;也可以是原来材料中元素的形式转移,如碳化硅中的硅从共价键的形式转化为单质硅。具体是,例如SiC与HCl反应生产SiCl4和H2,从而使硅脱离SiC的强共价键结构而生成四氯化硅和氢气,而四氯化硅与氢气迁移到SiC晶态之外的孔间隙而被可转化为单质硅,以纳米颗粒的形式存在于颗粒结构中。还可以用化学气相沉积、溶液渗透然后挥发溶剂、溶液渗透然后挥发溶剂再加热处理、气相渗透、电镀、融熔体渗透将这些物质保留在所形成的石墨烯结构之中,保持一种三维的空间分布,从而达到高性能。具体是:将含石墨烯结构的材料粉末通过物理化学反应如蒸发、气体(包括液体)刻蚀除去其中非石墨烯成分从而获得具有三维石墨烯结构的材料。可选择地,将材料与催化剂混合(如必要可造粒或压制成型),干燥后输送至反应器中,保持反应器内温度和压力在适当范围内,与引入反应气体反应生成三维石墨烯粉末,副产可另出售,其中反应所生成的大量余热可用于固体干燥,产生加热蒸汽用于副产精馏。为达上述目的,一方面,本发明提供了一种大规模生产三维石墨烯的方法,该方法包括:将固体含石墨烯结构的材料与气体选择性进行气化反应,生成三维石墨烯。本发明的方法中所需的固体含石墨烯结构的材料原料,可以是天然或人工合成的。根据本发明的一个具体实施方案,本发明的方法中,利用石油焦生产石墨烯。石油焦是一种半结晶的产品,其结构中含有石墨化较完整的部分完全类似于多层石墨烯,同时,它还有未石墨化的非晶碳区域,两种结构相互交织。而非晶部分与气体反应较石墨化部分容易得多,极易被气化形成三维石墨烯。根据本发明的另一个具体实施方案,本发明的方法中,利用炭化的热固性树脂生产石墨烯。炭化的热固性树脂是一种与石油焦类似的半结晶的产品,其结构中含有石墨化较完整的部分完全类似于多层石墨烯,同时,它还有未石墨化的非晶碳区域,两种结构相互交织。而非晶部分与气体反应较石墨化部分容易得多,极易被气化形成三维石墨烯。根据本发明的再一个具体实施方案,是将含石墨烯结构的金属碳化物作为原料,更具体的是将回收的含碳化硅的多晶硅切割磨料废渣直接作为反应原料,它与卤素气体、卤化氢气体或氢气进行气化反应,其可以实现工艺流程简化,能耗低、分离完全和利用充分的效果,特别是反应副产物还能够为多晶硅和有机硅生产提供廉价的原料。所述卤素气体为氟、氯、溴或碘,优选为氯气;所述卤化氢气体为氟化氢、氯化氢、溴化氢或碘化氢,优选为氯化氢气体。根据本发明的这个具体实施方案,固体含石墨烯结构的材料为碳化硅,它与卤素气体或卤化氢气体进行气化反应,除三维石墨烯外还可以生成卤硅烷和卤氢硅烷;固体含石墨烯结构的材料与氢气进行气化反应,可以生成硅烷。根据本发明的具体实施方案,本发明的方法中,所述气化反应在反应器中进行,所述反应器包含流化床、稀相气流床、喷动床、固定床或移动床之一或组合。固体物料(固体含石墨烯结构的材料,以及所述的催化剂,这些固体物料可以预先混合均匀)装填到反应器内,向反应器内通入气化反应所需气体,在适宜的温度下进行气化反应,并将反应生成物(气态)导出反应器,经冷凝即可收集得到液态的卤硅烷或硅烷。根据本发明的具体实施方案,本发明的方法中,可以是将固体含石墨烯结构的材料原料粉碎、研磨、或制粒后再进行气化反应。具体可以是根据反应器的操作需求而选择适宜的粉碎、研磨或是制粒。根据本发明的具体实施方案,通常情况下,粉碎可以是将固体含石墨烯结构的材料粉碎至30目以下,研磨可以是将固体含石墨烯结构的材料研磨至20微米以下,粉碎或研磨的目的均是为了使固体物料与气体接触更充分以利反应。制粒的目的主要是避免气速过大的情况下将物料吹走;在制粒的情况下,可适当加大气体与固体物料的接触停留时间,以利反应充分。根据本发明的具体实施方案,本发明的方法还包括将生成的卤硅烷进一步精馏分离的过程。具体的精馏分离可以按照所属领域的常规操作进行,本发明中不做赘述。根据本发明的具体实施方案,本发明的方法还包括从固体含石墨烯结构的材料制得三维石墨烯的过程。即,另一方面,本发明还提供了一种利用含石墨烯结构的材料 生产三维石墨烯的方法,该方法包括:步骤一:对含石墨烯结构的材料原料干燥,制得干燥的固体含石墨烯结构的材料;步骤二:按照本发明前述方法对所述固体含石墨烯结构的材料进行回收利用。在本发明的一具体实施方案中,对得到的固体含石墨烯结构的材料进行气化的过程按照以下操作进行:采用真空干燥设备对半干含石墨烯结构的材料进行干燥处理,得到干燥的固体含石墨烯结构的材料。根据本发明的具体实施方案,气化反应所生成的大量余热可用于固体干燥,产生加热蒸汽用于氯硅烷精馏提纯。在本发明的一具体实施方案中,本发明提供了一种由含石墨烯结构的材料制取三维石墨烯的方法,其包括如下步骤:(1)、选择原料添加含有金属的催化剂;(2)、干燥:采用真空干燥设备对半干粉末进行干燥处理(可以是回转炉,流化床,风力干燥等,可选择地压制成型:采用加压的方法或造粒方法来成型),得到含石墨烯结构的材料和硅粉;(3)、反应:将干燥或成型后的混合硅粉与气体反应生成三维石墨烯;更具体而言,本发明的一具体实施方案中的方法按照如下操作进行:干燥:在经过除杂和固液分离后,所得的固体的主要成分主要是含石墨烯结构的材料和硅。进一步干燥可除去水分对下游反应的影响。具体方式采用流化床干燥,回转炉干燥,或其它形式,甚至在造粒成型之后。添加催化剂成型:在添加含有金属的催化剂、压制成型;采用加压的方法或造粒方法来成型。气化反应:本发明的一个实施例是将不完全石墨化的石油焦与气体反应,除去其中的非石墨化成分;本发明的另一个实施例是将热固性酚醛树脂进行炭化,其中源于聚合的高分子成分就转变为含有石墨烯结构的固态碳,将其与与气体反应,除去其中的非石墨化成分就形成三维石墨烯;本发明的再一个实施例是将催化剂和SiC粉可压制成型,也可以粉末形式与氯气或氯化氢反应生成氯硅烷如三氯氢硅或四氯化硅。而这类反应都是放热反应,在反应过程中会产生大量热能,需将反应器冷却下来。这样冷却剂可利用水或水蒸气,带出的热量可用于固液分离,干燥采用流化床,固定床,移动车等多可达到所需理想效果。而蒸汽用于氯硅烷的精馏提纯。本发明提供了一种利用含碳物生产三维石墨烯的方法,该方法包括:将含有石墨烯结构的材料通过选择性物理化学反应除去非石墨烯成分,生成三维石墨烯。根据本发明所述的方法,优选地,所述含有石墨烯结构的材料包括人工合成的材料和天然的材料,至少含有石墨烯或类石墨烯成分,包括单层和多层结构,而其它部分为非碳元素或结晶不完整的碳元素,这类材料包含金属碳化物、不完全石墨化碳、由热固性树脂炭化而成的硬碳、软碳。根据本发明的方法,优选地,物理化学反应包括真空蒸发或气化刻蚀;刻蚀气体或液体为可与材料中非石墨烯成分进行化学或物理反应生成气相或液相物质并能被排出材料结构而与石墨烯分离的气体或液体;刻蚀气体包括氟、氯、溴或碘,卤化氢气体、氟化氢、氯化氢、溴化氢或碘化氢可与金属形成低沸点化合物的气体,也包括可与非石墨烯碳结构形成挥发气体的氧气、氢气、水蒸气、二氧化碳、氮氧化合物。根据本发明所述的方法,优选地,控制反应的条件为:反应温度200-3000℃,反应压力0.01-100MPa;更优选地,反应温度为300-2100℃,反应压力为0.1-10MPa。根据本发明所述的方法,优选地,所述反应是在催化剂存在条件下进行的,所述的催化剂包含金属、合金、各种金属化合物和盐;更优选地,所述催化剂的活性组分选自以下物质中的一种或多种:a)贵金属,所述贵金属包括钯、铂、铑、铼、钌及其合金;b)过渡金属,所述过渡金属包括镍、铜、钴、铁及其合金;c)碱金属,所述碱金属包括钠、钾、锂、钙及其合金;d)稀土金属;e)金属盐、金属氧化物;和f)金属氢化物;进一步优选地,所述催化剂的活性组分为钴和/或氯化钴。根据本发明所述的方法,优选地,所述方法还包括在反应过程中对三维石墨烯进行预掺杂以使其达到更佳性能效果的操作,所述预掺杂物包含:a)硅、锗、锡、硫、铅、Sb、Li、Na、K、Pt、Au、Ag、Mg、Mo、Al;b)与这些元素所形成的合金;c)过渡金属氧化物、碳化物、氮化物、硫化物,磷酸,盐,以及氢氧化物,这些元素可以在生产过程中以催化剂的形式加入,也可以是原来材料中元素的形式转移,如碳化硅中的硅从共价键的形式转化为单质硅以纳米颗粒的形式存在于颗粒结构中。本发明还提供了一种生产三维石墨烯的方法,该方法包括:步骤一:对含石墨烯结构的材料预加催化剂和干燥;步骤二:按照上述方法对所述含石墨烯结构的材料进行气化反应。综上所述,本发明提供了一种利用含石墨烯结构的材料生产三维石墨烯的方法及所用装置,其中主要是将含石墨烯结构材料与催化剂混合(可选择地,可在干燥之前加酸洗或其它方法先除出杂质,也可以在在粉末中加入适量催化剂,如必要可造粒或压制成型),与气体选择气化反应生成三维石墨烯。本发明的技术也可有效利用催化剂作为预掺杂,集石墨烯生产与有效掺杂转换合为一体,同时生产出高性能的三维石墨烯,实现了三维石墨烯大型、高效、节能、连续和低成本完全循环利用。另一方面,本发明还提供了一种用于实现本发明所述利用碳化硅生产三维石墨烯的方法的装置,该装置包括:用于进行气化反应的反应器;该反应器设置温控设备;优选地,所述反应器为移动床、流化床、稀相气流床、喷动床或固定床;将固体碳化硅输送入反应器的进料系统;将卤素气体、卤化氢气体或氢气输送入反应器的进气系统;将气化反应产生气体导出反应器并冷凝进行收集的产物收集系统;将气化反应产生固体粉末石墨烯导出反应器并冷凝进行收集的产物收集系统。另一方面,本发明还提供了一种用于实现所述利用含石墨烯结构的材料生产三维石墨烯的方法的装置/用于回收利用固体碳化硅生产三维石墨烯的装置,该装置包括:用于进行气化反应的反应器,该反应器设置温控设备;优选地,所述反应器为流化床、气流床、喷动床、固定床或移动床或它们的组合;用于将反应气体输送入反应器的进气系统;用于将气化反应产生气体导出反应器并冷凝进行收集石墨烯产物的收集系统。根据本发明所述的装置,优选地,该装置适用于细微颗粒,其包括:用于进行气化反应的反应器,用于将卤素气体、卤化氢气体或氢气输送入反应器的进气系统,以及用于将气化反应产生气体导出反应器并冷凝进行收集的产物收集系统;其中:所述反应器设置温控设备,反应器中部为用于填充固体硅渣的主反应区,反应器下部设置分布器,反应器上部设置过滤器;反应器底部设有原料气体进口和固体排渣口,顶部设置固体进料口和产物气体出口;所述进气系统包括储存卤素气体、卤化氢气体或氢气的气源,通过管道与反应器底部的原料气体进口连通;所述产物收集系统包括冷凝器,冷凝器的上游端与反应器顶部的产物气体出口连通,冷凝器的下游端依次串接冷凝液体收集装置以及尾气处理装置。根据本发明所述的装置,优选地,所述反应器的内衬和分布器由耐腐蚀材料如石 英,石墨、陶瓷或不锈钢制成。本发明还提供了一种用于实现本发明所述利用含石墨烯结构的材料生产三维石墨烯的方法的装置,该装置包括:用于进行气化反应的反应器;该反应器设置温控设备;优选地,所述反应器为移动床、流化床、气流床、喷动床、固定床之一或组合;将固体含石墨烯结构的材料输送入反应器的进料系统;将卤反应气体输送入反应器的进气系统;将气化反应产生气体导出反应器并冷凝进行收集的产物收集系统;将气化反应产生固体粉末石墨烯导出反应器并冷凝进行收集的产物收集系统。所述的用固体含石墨烯结构的材料生产三维石墨烯的反应器,优选地,所述反应器为气流床反应器、流化床反应器、固定床反应器或移动床反应器之一或组合。所述的用固体含石墨烯结构的材料生产三维石墨烯的反应器的进气系统与反应器底部的原料气体进口之间的管道上设置有气体干燥器。在所述的用固体含石墨烯结构的材料生产三维石墨烯的反应器,产物收集系统的尾气处理装置为串联设置的分离、吸附或中和单元。又一方面,本发明还提供了一种电化学储能器件如离子电池、离子电容、以及电化学电容及其复合电极以及材料的制备方法,选择有高能量密度和功率密度的电极材料形成复合材料电极。根据本发明所述的锂离子电池复合电极的制备方法,其中高能量密度材料优选地为含硅负极材料,而高功率密度材料优选地为三维石墨烯,这两者的比例按照应用需求而定,它们由粘合剂导电剂与集流体相连。根据本发明所述的含硅电极材料方法,该方法包括:(1)制备有通孔或有较大表面积的电极基体材料原料;(2)让含硅气体或液体流体通入孔中并将硅以单质硅为主的形式的预留在孔中,形成含硅材料,(3)将让含硅材料然后通过挤压,整形造粒或涂覆碳层(回填可透离子材料)中的至少一种方法封闭硅与外界气体或液体的接触被封闭在体内从而避免后续工艺中与外界气体或液体接。根据本发明所述的锂离子电池复合负极材料,该负极基体原料包括但不限于天然石墨、人造石墨、软碳、硬碳及其它负极材料,如LiTiO2的原料、前躯体、,半产品或成品。根据本发明所述的复合锂离子电池负极材料的制备方法其中通孔或有较大表面积的形成可以根据原料不同采取包括膨胀、研磨、发泡、气化刻蚀或催化气化刻蚀,模块预制等多样方法之一种或组合制成一定形状和尺寸。优选地,比表面积为每克 0.1平方米以上。孔体积占总体积的10-90%、较为优选地为20-80%,更优选地30-70%的预留空间,可选择地,高表面积和孔可被挤压收缩。根据本发明所述的催化气化刻蚀,该方法包括将固体电极基体与氧化气体、或还原气体进行气化反应,生成可挥发性气体离开基体形成孔洞。根据本发明所述的方法,其中,所述气体为氧气,氢气,水蒸气,二氧化碳,氮氧化合物等。根据本发明的方法,其中,控制基体气化反应的条件为:反应温度200-1400℃,反应压力0.01-100MPa;优选地,反应温度300-1100℃,反应压力0.01-10MPa。根据本发明所述的方法,其中,所述气化反应是在催化剂存在条件下进行,所述的催化剂包含金属、合金、各种金属化合物和盐;优选地,所述催化剂的活性组分选自以下物质中的一种或多种:a)贵金属,特别是钯、铂、铑、铼、钌、和它们的合金;b)过渡金属,特别是镍、铜、钴、铁、以及它们的合金;c)碱金属,特别是钠、钾、锂、钙和它们的合金;d)稀土金属;e)金属盐、金属氧化物;和f)金属氢化物;根据本发明所述的复合锂离子电池负极材料的制备方法,含硅气体如硅烷SiH4,Si2H6和卤硅烷的分解或还原,由气相渗透化学气相渗透(CVI)和/或化学气相沉积(CVD),含硅液体为硅或含硅合金熔体沁入孔内冷凝;硅占孔通10-90%、较为优选地为20-80%,更优选地30-60%的预留空间,而硅的状态优选地为非晶状态或无序结构,更优选地,为松散纳米颗粒硅聚合。根据本发明渗透硅的加热采取电加热辐射,微波,等离子还有气体燃烧,过热液体气体换热加热,反应温度20-1400℃,反应压力0.01-100KPa;优选地,反应温度300-900℃,反应压力0.1-100KPa,反应时间控制在99%的含硅气体完全被分解或还原成硅。根据本发明所述的复合锂离子电池负极材料的制备方法,可选择的,也可以让锂与硅按预先设定的比例一起置入其中。可选择的,也可以让锂与硅按预先设定的比例一起置入其中。根据本发明所述的复合锂离子电池负极材料的制备方法,可选择的,(1)通过挤压收缩有较大可收缩表面积前躯体;(2)通过整形(所在气氛氮气氩气惰性气体),可将所致材料进一步制成一定尺寸和形状以满足锂离子电池电极要求;(3)并通过涂覆碳闭合通孔或封闭硅与外界气体或液体的接触被封闭在体内从而避免后续工艺中 与外界气体或液体接,优选地靠压缩或CVD碳密封)。此外,针对现有技术的不足,本发明旨在提供一种比容量高、循环性能稳定的,同时兼顾能量密度和功率密度的离子电池(同样适合钠、钾、镁、铝等离子电池)及其复合电极以及电极材料的制备方法。离子电池选择有高能量密度和高功率密度的电极材料形成复合材料电极。本发明中含硅材料按如下操作实现:先选择制备有孔高表明积负极基体材料,所述的锂离子电池复合负极基体材料原料包括但不限于天然石墨、人造石墨、软碳、硬碳石墨烯及其它负极材料,如Li4Ti5O12(LTO)、Li0.6Co0.4N、Co3O4、Fe3BO6、CuSn、FeSn、高分子材料PMT和PFPT、硫、锂、钠等(它们可以是现有技术应用中的原料、前躯体、半产品或成品);再将硅以硅单质为主或合金的形式,通过化学气相渗透(CVI)、沉积(CVD)或硅合金熔体沁入的方式置入孔内,在这种材料中硅的主要部分处于基体材料体内(硅可以是连续的薄膜,分散颗粒、松散的堆积的结构,硅的状态优选地为非晶状态或无序结构);然后可选择地通过挤压,研磨、整形、造粒、或涂覆碳层中的至少一种方法封闭硅与外界气体或液体的接触得到复合负极材料。高比表面积和通孔基体材料制备:所述的复合锂离子电池负极材料的制备方法其中通孔或有较大可收缩表面积的形成可以根据初始原料不同采取以下多样方法至少一种或它们的组合,这些方法包括膨胀、研磨、发泡、凝胶制备、气化刻蚀、催化气化刻蚀、引入的外来支撑模板等制成一定形状和尺寸。优选地,最终渗硅之前材料比表面积为每克0.1平方米以上,孔体积占总体的10-90%、较为优选地为20-80%,更优选地30-70%,表面积和孔可被挤压收缩。这里对多孔材料制备简述,后续结合实施例子作进一步详细描述。所述的膨胀法是特别针对天然鳞片石墨和相似可膨胀材料。以双氧水为氧化剂,有机物如乙酸等为氧化插层剂,制备无硫无灰可膨胀石墨的技术工艺。采用液体氧化剂取代固体强氧化剂,有效降低了可膨胀石墨的灰分;通过混酸作插层剂有效控制了产品的硫含量,特别要减少可与锂形成稳定巩固化合物的原料以防止电极的最终不可逆成份太多,从而影响电极的整体性能。对于这些材料,首先让它们在高温条件下膨胀,通过抽真空除去气体和可挥发性杂质,同时也让它们变成较高的可收缩的比表面积,有利于后续硅的均匀渗透和沉积,从而达到广泛分布。在获得硅的沉积后又可以通过压缩将硅封闭在石墨薄层之中再进行研磨整形造粒和表明涂覆。所述的研磨是在制备负极材料特别是在研磨整形过程中通过控制工艺参数来得到合适的孔隙率的过程。所述的发泡法是利用沥青在没有固化之前可以通过加热让它软化甚至熔化的流变特性,加入发泡剂,使其发泡形成相连的微孔结构,然后固化,石墨化。这不仅适合中间相沥青微球,也适合在人造石墨、碳纤维和硬碳电极材料。所述的凝胶生产利用高分子材料在超临界状态下干燥固化,然后通过加热让它炭化形成相连的微孔结构。这个过程中可添加中间相沥青、人造石墨、碳纤维和硬碳电极材料。所述的模块两相预混就是将一种电极活性原材料如中间相沥青与另一种非电极材料如高比表面积的SiO2(白炭黑)或活性炭等在纳米量级得以充分混合,按照常规手段制成电极材料,然后有选择性的除去非活性电极材料,从而形成带开通孔的材料用于渗透硅。所述的气化刻蚀气化方法是用气体与基体材料中结构较弱的部分如晶粒边界反应,形成可挥发性气体或液体,对于碳素材料基体而言可用气体包括氧气,氢气,水蒸气,二氧化碳,氮氧化合物等,从而制得高表面积、孔隙丰富的渗硅电极材料。所述的催化气化刻蚀,该方法包括将固体电极基体与氧化气体、还原气体或氢气进行气化反应,生成可挥发性气体离开基体形成孔洞,这种刻蚀有催化剂的介入可以形成较为理想的孔径分布,同时极大加快刻蚀过程。基体材料包括碳素和过渡金属碳化物,后者形成三维石墨烯(见下面详解)。所述的催化气化刻蚀方法,其中,所述催化气化反应是在催化剂存在条件下进行,所述的催化剂在电极基体材料气化之前的任何阶段加入;所述催化剂的活性组分选自以下物质中的至少一种或多种组合,优选地为锂及其化合物和非磁性材料:a)贵金属:特别是钯、铂、铑、铼、钌、和它们的合金;b)过渡金属:特别是镍、铜、钴、铁、以及它们的合金;c)碱金属:特别是钠、钾、锂、钙和它们的合金;稀土金属;d)金属盐包括碳酸盐、硝酸盐,等、金属氧化物;和e)金属氢化物。渗透硅:所述的复合锂离子电池负极材料的制备方法,用含硅气体如硅烷SiH4、Si2H6和卤硅烷,由化学气相渗透和/或化学气相沉积在由上述方法制备的电极基体材料的孔内或表面分解或还原成硅,也可以含硅液体为硅或含硅合金熔体沁入由上述方法制备的电极基体材料的孔内沉积冷凝,渗硅可在材料制备不同阶段多次反复进行。得到的硅可以是连续的薄膜,分散颗粒、松散的堆积的结构,硅的状态优选地为非晶状态或无序结构。优选地,在渗硅后闭合通孔或有较大可收缩表面积,让含硅材料被 封闭在体内从而避免后续工艺中与外界气体或液体接(机靠压缩或CVD碳密封,涂覆碳层可以在同一反应器的后续区段进行)。渗透硅方法,其中控制反应的条件为:反应温度20-1400℃,反应压力0.001-100KPa;优选地,反应温度30-1100℃,反应压力0.001-50KPa,反应时间控制在99%的含硅气体完全被分解或还原成单质硅或硅氢化合物,硅占孔通10-90%、较为优选地为20-80%,更优选地30-60%的预留空间。渗硅过程中对材料的加热可采取电加热、光辐射、微波、等离子增强、气体燃烧加热、过热液体气体换热加热至少一种或组合。所述的复合锂离子电池负极材料的制备方法,可选择地,让锂一定量的与硅一样预置入于电池负极材料中,以减少充电中锂的不可逆损失,从而提高电池的整体性能。颗粒外表密封:所根据所述的复合锂离子电池负极高能量密度含硅材料的制备方法,可选择的,在渗透硅之后针对不同的原料特性采取以下手段之至少一种或重复使用将所致材料进一步制成一定尺寸和形状满足锂离子电池电极要求:挤压、研磨、整形(所在气氛氮气氩气惰性气体)造粒、表面涂覆碳层封闭硅与外界气体或液体的接触。这样可减少硅的氧化和在锂离子电池充放电过程中SEI的过渡形成而造成锂的损失与电池性能的衰减。用于进行气化反应、渗透硅、锂等有益杂质和表面涂覆的的反应器为移动床、流化床、稀相气流床、喷动床、旋转床,搅拌床、固定床之至少一种或组合。图1给出了电极材料制备流程:a为成品电极石墨颗粒(内部结构较弱部分未示出),b为经过化学气相刻蚀后,颗粒从外向里形成的通孔和高表面积结构,c为硅向石墨颗粒内部渗透后的结构,d为渗透硅、锂等有益杂质后石墨颗粒涂覆碳后的最终含硅、锂等有益杂质电极材料结构。与现有技术相比,本发明复合锂离子电池负极材料,一方面采用的硅在预留空间内沉积,有效地抑制了硅的体积膨胀问题,此外,后处理采用通孔闭合与整形的办法确保硅具有良好的单分散性,有效的避免了硅的团聚现象的发生,避免与空气氧化和被电解液,结合优良的导电性,具有较高的容量。同时,预掺杂锂等增加了离子电池的循环寿命。由于引进三维石墨烯,还提高了电池的功率密度,从而有效地提高了电池的容量和倍率性能与循环性能。附图说明图1为本发明中针对电极成品材料所用气体刻蚀和硅沉积示意和原理图;图2a为本发明实施例中所产硅纳米粉电子显微图(20000×);图2b为本发明实施例1中所产硅纳米粉电子显微图(50000×);图3a为本发明实施例11中所产固体成分的扫描电子显微图(3000×);图3b为本发明实施例11中所产固体成分的扫描电子显微图(15000×);图4a为本发明实施例11中所产固体成分中三维石墨烯的透射电子显微图(25000X);图4b为本发明实施例11中所产固体成分中三维石墨烯的透射电子显微图(20000X);图5为本发明实施例11中所产三维石墨烯的拉曼光谱图;图6a为本发明实施例11中所产三维石墨烯的电池充放电图;图6b为本发明实施例11中所产三维石墨烯的电池充放电倍率图;图7为本发明实施例13中由石油焦所产三维石墨烯的透射电子显微图(5000X);图8为本发明实施例14中所产三维石墨烯的透射电子显微图(400000X);图9为本发明提供的生产三维石墨烯方法所用装置的结构示意图。主要附图标号说明:1、固体原料储罐2、输送机构3、第一级锁斗31、第一阀门4、第二级锁斗41、第二阀门5、第三级锁斗51、第三阀门7、产物气体出口8、观察窗口9、反应器10、主反应区11、分布器12、固体排渣口13、废渣储罐15、气源16、流量计。具体实施方式为了对本发明的技术特征、目的和有益效果有更加清楚的理解,现对本发明的技术方案进行以下详细说明,但不能理解为对本发明的可实施范围的限定。下面结合附图和具体实施例进一步说明本发明的技术方案,它具有操作步骤少、流程短、分离干净、副产有利等优点。这些实施例并非用于限制本发明。本发明的方法主要是对含石墨烯结构的材料中的非石墨烯成分(如碳化硅中的硅)进行选择性气化获得三维石墨烯。其中,固体含石墨烯结构的材料的收集提纯干燥以及催化剂的添加等操作可以按照任何可行的现有技术进行。含石墨烯结构的材料经干燥后与卤素气体和/或卤化氢气体进行气化反应生成三维石墨烯和卤硅烷。以下进行更具体描述:第一、含石墨烯结构的材料的分离:含石墨烯结构的材料或含石墨烯结构的材料与一定比例的催化剂混合后。第二、干燥:在经过加入催化剂后,含石墨烯结构的材料中可能含有有机溶剂和水分,进一步干燥可除去水分以减少其对下游反应的影响。具体方式可以采用流化床 干燥、回转炉干燥、喷动床或其它形式的干燥组合体进行干燥。干燥后的含石墨烯结构的材料可选择性成型、或是可选择性添加其他成分,用于后续的气化反应:2.1可选择地成型:采用加压的方法或其它造粒方法将上述含石墨烯结构的材料粉末成型,在成型过程中可添加有机或无机粘结机,在造粒成型之后再进行干燥,这有利于反应。2.2可选择地添加其它成分:可选择地在上述含石墨烯结构的固体材料粉末中添加本发明气化反应的催化剂。这种添加可以结合干燥程序进行,达到充分混合的目的。催化剂也可以事先溶于溶剂中再加入到干燥之前的物料中,搅拌均匀后或压制成型后进行干燥。第三、选择性气化反应:在传统硅与含石墨烯结构的材料的分离过程中,SiC粉以粉末形式或造粒后的颗粒形式与卤素气体或卤化氢选择气化反应生成卤硅烷如三卤氢硅或四卤化硅等。3.1反应装置根据本发明的更具体实施方案,本发明提供的用于实现本发明所述三维石墨烯制备方法的装置可参见图9所示,其主要包括:用于进行气化反应的反应器9,用于将原料气体输送入反应器的进气系统,用于将固体原料输送入反应器的进料系统,以及用于将气化反应产生气体导出反应器并冷凝进行收集的产物收集系统;其中:所述反应器9设置温控设备,反应器9中部为用于填充固体原料的主反应区10,反应器下部设置有分布器11;反应器底部设有原料气体入口和固体排渣口12,顶部设置有观察窗口8、固体进料口和产物气体出口7;该产物气体出口7设置有过滤器;所述进气系统包括储存气体原料的气源16,该气源16通过管路与反应器底部的原料气体入口相连;所述进料系统为三级锁斗进料系统,且该三级锁斗之间为串联设置,固体原料储罐1通过管路与第一级锁斗3的入口相连,第一级锁斗3的出口通过管路与第二级锁斗4的入口相连,第二级锁斗4的出口通过管路与第三级锁斗5的入口相连,第三级锁斗5的出口通过管路与所述固体进料口相连;第一级锁斗3与第二级锁斗4之间的管路上,第二级锁斗4与第三级锁斗5之间的管路上,第三级锁斗5与固体进料口之间的管路上分别设置有第一阀门31、第二阀门41及第三阀门51。所述产物收集系统包括冷凝器,该冷凝器的上游端与反应器顶部的产物气体出口 相连,冷凝器的下游端依次串接冷凝液体收集装置以及尾气处理装置;所述反应器为气流床反应器、流化床反应器、喷动床反应器、固定床反应器或移动床反应器;所述反应器下部的分布器所在区截面为锥形或倒梯形;所述进气系统包括多个并联设置的气源;气源与反应器底部的原料气体入口之间的管路上设置有气体干燥器;产物收集系统的尾气处理装置为串联设置的分离、吸附或中和单元;所述反应器的内衬和分布器为由耐腐蚀材料制成的;所述耐腐蚀材料包括石英、石墨、陶瓷或不锈钢。固体原料加入系统:固体原料经干燥后存在固体原料储罐1中,也可以由输送机构2直接输送到反应器顶部设置的第一级锁斗3中;输送方法可以采用气体输送,由于反应器中压力为0-0.5MPa,为了防止反应生成气体外泻和用于气体输送的气体与生成气体混合增加后续分离困难,可采取惰性气体输送至3然后抽空,再用反应生成气体将固体原料压到下一级锁斗以至最终进入反应器腔体顶部。该装置采用多级锁斗进料系统是由于反应器内温度压力较高,物料从大气状态加入反应器必须进行多次锁斗切换,逐级加进反应器。气体原料加入系统:气体原料HCl或Cl2由储罐(气源)15经预热后经流量计16从下部通入反应器,由枝状分布器11分散输出然后由下向上通过反应器内固体废渣和新生固体副产床层逆向而行并与其中的硅(或其他含石墨烯结构的材料中的非石墨烯成分)反应生成氯硅烷,最终上升到反应器顶部由气体出口7排出,经后续降温热能回收后备用或直接输送到配套工厂的下一个工序;原料气体在到达反应器顶部之前已完全转化为生成气体,固体原料中的硅在下行到分布器之前已将其中所含的所有硅完全反应掉了;固体副产品排出系统:得到的三维石墨烯碳素从反应器底部由螺杆输出至废渣储罐13后再包装外卖。热能回收主要在高温合成物冷却和反应器外部冷却上,固体副产排出余热利用可视情况再考虑。(1)用于进行气化反应的反应器;该反应器设置温控设备(图中未显示)。具体的,该反应器可以是气流床、流化床、固定床或移动床,优选地为移动床或是气流床,因为物料干燥后为细粉,传统流化床反应很难控制,大量未反应硅渣被带到下游造成物料浪费和管道堵塞,而气流床使得物料与反应气体得以完全混合,极大的增加反应表面。如图9所示,反应器中部为用于填充固体含石墨烯结构的材料的主反应区。(2)将卤素气体、卤化氢气体或氢气等输送入反应器的进气系统;该进气系统主要是将原料气体(卤素气体、卤化氢气体或氢气等)通过反应器底部设有原料气体进口输送入反应器,自下而上流经填充固体含石墨烯结构的材料的主反应区,与固体含石墨烯结构的材料反应生成产物气体(卤硅烷或硅烷);所述进气系统包括多个并联设置的气源及与气源串联设置的气体干燥器,气体干燥器可以是填充沸石的容器,用于吸收原料气中可能含有的水分,以防止携带水分进入反应器。(3)将气化反应产生气体导出反应器并冷凝进行收集的产物收集系统。产物收集系统主要包括通过管道串联设置的冷凝器、液体收集装置以及尾气处理装置,其中,冷凝器主要是用于将从反应器导出的产物气体冷凝为液体,冷凝后的液体用液体收集装置收集,未冷凝的尾气(主要是未反应的卤素气体、卤化氢气体)经尾气处理装置(主要是盛装碱性溶液的容器,利用碱性溶液吸收尾气中未反应的卤素气体、卤化氢气体)处理,为确保对尾气中可能存在的卤素气体、卤化氢气体的吸收,可串联设置多个尾气处理装置。3.2催化剂本发明中的催化剂包含金属,合金,各种金属化合物和盐,可压制成型。3.3可选择地精馏提纯本发明的气化反应是放热反应,在反应过程中会产生大量热能,需控制反应温度(反应过程中通常需将反应器冷却下来。这样冷却剂可利用水或水蒸气,带出的热量可用于反应前含石墨烯结构的材料的干燥,干燥可采用流化床、固定床、移动床等。而蒸汽可用于卤硅烷的精馏提纯。在卤化反应中产生的化合物含四卤硅、三卤氢硅和卤气。这很容易由精馏装置进行提纯,采用物理分离方法对产品中不同卤硅烷进行分离(由于他们不同的沸点),获得所需品质和纯度的氯硅烷产品,可外售或作为下游白炭黑、多晶硅或有机硅生产原料。实施例1:膨胀石墨生产连体石墨烯渗透硅本实施例通过以下步骤来实现:(1)将100克可膨胀鳞片石墨(100目)置入反应器,在抽真空下加热至600℃,体积膨胀100倍成为连体石墨烯,向反应器中通入惰性气体Ar将挥发成分、氧化成分排除并抽真空;(2)向(1)中的反应器中通入20克硅烷气体(MEMC)直至分解反应完毕(可采取逐步方式),观察压力增加以确定反应完成。图2a、2b为硅烷分解的纳米硅附着在石墨上的电子显微图;(3)向反应器中通入惰性气体Ar,排除氢气,将(2)中的沉积有硅的膨胀石墨冷却至室温通过挤压恢复到原有密度,含硅15%(wt);(4)将(3)中所得挤压后含硅石墨整形成为圆形颗 粒;(5)将所得整形成为圆形颗粒置入同(1)类似的小反应器,抽真空后通入丙烷让其在颗粒表面分解沉积碳起保护作用从而制得成品含硅锂离子电池电极材料。作为比较,在上述步骤(1)和(2)之间加入真空蒸发锂的过程,即完成(1)后,将10克金属锂碎片分布在连体石墨烯中加热至800℃保持1小时,然后重复以上过程,得到掺杂硅和铝的电极材料。对本实施例步骤(1)的连体石墨烯、步骤(5)制备得到的含硅石墨烯电极材料及所制备得到的掺杂硅和锂的电极材料进行电化学测试(武汉蓝博),测试过程中,连体石墨烯/含硅石墨烯电极材料/掺杂硅和锂的电极材料与导电炭黑以及粘合剂的重量比分别是90:5:5;其中,所用粘合剂为SBRGlue,电解质为(三星)1.0MLiPF6溶液,该溶液的溶剂为同等比例的碳酸乙烯酯(ethylenecarbonate,EC)和碳酸二乙酯(diethylcarbonate,DEC),充电电流密度为50mA/g,其测试结果见表1所示,从表1可见,对于含硅石墨烯电极材料,其首次充电不可逆损失为50mAh/g,一百次充放电后还有600mAh/g的容量,是普通石墨的两倍。对于掺杂硅和锂的电极材料,其首次充电不可逆损失仅为1mAh/g,一百次充放电后还有570mAh/g的容量,可见掺锂和硅是获得高性能电极材料的重要手段。表1实施例2:活性炭模块制备高通孔高内表面积石墨本实施例通过以下步骤来实现:(1)将1公斤中间相沥青与200克高表面积活性炭混合均匀;(2)通过氧化固化制备材料让中间相成为热固性的材料,同时(3)让活性炭被气化形成有通孔的可石墨化的材料;(4)将(3)所得含通孔的材料高温石墨化而获得有通孔的石墨;(5)重复实施例1中渗透硅至表面涂覆碳保护层得到含硅复合锂离子电池电极材料。实施例3:二氧化硅模块制备高通孔高内表面积石墨本实施例通过以下步骤来实现:(1)将1公斤中间相沥青与200克高表面积白炭黑(SiO2)混合均匀,(2)通过氧化固化所制备材料让中间相成为热固性的材料,同时(3)让白炭黑被NaOH腐蚀形成有通孔的可石墨化的材料;(4)将(3)所得含通 孔的材料高温石墨化而获得有通孔的石墨;(5)重复实施例1中渗透硅至表面涂覆碳保护层得到含硅复合锂离子电池电极材料。实施例4:中间相沥青发泡制备高通孔高内表面积石墨本实施例中发泡石墨通过以下步骤来实现:(1)将1公斤中间相沥青与发泡剂混合发泡成通孔材料;(2)加温让(1)材料炭化获得多孔石墨;(3)重复实施例1中渗透硅至表面涂覆碳保护层得到含硅复合锂离子电池电极材料。实施例5:成品人造石墨气体刻蚀后获得高通孔高内表面积石墨本实施例通过以下步骤来实现:(1)将1公斤成品人造石墨锂离子电极材料(2.6m2/g)与10克Li2CO3催化剂混合;(2)真空干燥(1)获得载有催化剂的人造石墨;(3)在反应器中加热载(2)中制得的载有催化剂的人造石墨到600℃,通入10%氧气进行气体刻蚀一小时后获得多孔石墨;(4)重复实施例1中渗透硅至表面涂覆碳保护层得到含硅复合锂离子电池电极材料。实施例6:成品软碳催化气体刻蚀本实施例通过以下步骤来实现:(1)将1公斤成品软碳锂离子电极材料(3.6m2/g)与10克Li2CO3催化剂混合;(2)真空干燥(1)获得载有催化剂的软碳;(3)在反应器中加热载(2)中制得的载有催化剂的软碳到600℃,通入10%氧气进行气体刻蚀一小时后获得多孔石墨;(4)重复实施例1中渗透硅至表面涂覆碳保护层得到含硅复合锂离子电池电极材料。实施例7:成品硬碳气体刻蚀本实施例通过以下步骤来实现:(1)将1公斤成品硬碳锂离子电极材料(2.9m2/g)与10克Li2CO3催化剂混合;(2)真空干燥(1)获得载有催化剂的硬碳;(3)在反应器中加热载(2)中制得的载有催化剂的硬碳到600℃,通入10%氧气进行气体刻蚀一小时后获得多孔石墨;(4)重复实施例1中渗透硅至表面涂覆碳保护层得到含硅复合锂离子电池电极材料。实施例8:成品天然石墨气体刻蚀后获得高通孔高内表面积石墨(1)将1公斤成品天然石墨锂离子电极材料(3.1m2/g)与10克Li2CO3催化剂混合;(2)真空干燥(1)获得载有催化剂的天然石墨;(3)在反应器中加热载(2)中制得的载有催化剂的天然石墨到600℃,通入10%氧气进行气体刻蚀一小时后获得多孔石墨;(4)重复实施例1中渗透硅至表面涂覆碳保护层得到含硅复合锂离子电池电极材料。实施例9:成品石墨化中间相微球气体刻蚀后获得高通孔高内表面积石墨本发明通过以下步骤来实现:(1)将1公斤成品石墨化中间相锂离子电极材料(3.7m2/g)与10克Li2CO3催化剂混合;(2)真空干燥(1)获得载有催化剂的石墨化中间相;(3)在反应器中加热载(2)中制得的载有催化剂的石墨化中间相到600℃,通入10%氧气进行气体刻蚀一小时后获得多孔石墨;(4)重复实施例1中渗透硅至表面涂覆碳保护层得到含硅复合锂离子电池电极材料。实施例1-9所制备得到产物的比表面积和内孔增加情况见表2所示。表2原料比表面积增加倍数空洞率(%)实施例1可膨胀石墨(连体石墨烯)>50>80实施例2中间相沥青+活性炭>20>50实施例3中间相沥青+白炭黑>20>60实施例4中间相沥青+发泡>10>40实施例5成品人造石墨>10>30实施例6成品软碳>10>30实施例7成品硬碳>10>30实施例8成品天然石墨>5>30实施例9成品石墨化中间相微球>8>30实施例10碳化硅>10>60实施例11碳化硅>10>60实施例12碳化硅>10>60实施例10从商业硅切割浆料回收工厂获得的固体块状硅渣料,呈褐色,其主要含硅粉和碳化硅,将该固体碳化硅原料在110℃下干燥24小时;首先在250-300℃之间在氮气中加热,直至没有任何可见物质挥发后,切换成通入气体HCl进行反应,控制HCl气体流量为200mL/min,在300-350℃保持2小时后冷凝收集到透明液体,化学分析为SiHCl3,纯度99.5%以上。反应器内硅渣冷却后外观基本没变。实施例11与实施例10中的条件相同只是在硅渣粉末中加入占硅渣重量10%的CoCl3·6H2O催化剂,反应气体还是200mL/minHCl,反应温度升高到500-900℃,二小时后,冷凝收集到透明液体,化学分析为主要成分为SiCl4但含12%三氯氢硅。同时,反应器内硅渣冷却后外观明显变化,可明显看出硅渣残留部分有碳黑(未能完全收集)。图3a、3b为本实施例中所产固体成分的扫描电子显微图,从图中可以看出,低 放大倍数扫描电子显微图中颗粒的形状基本保持在原来的状态,但是,在高放大倍数下颗粒成明显的多孔松散结构。这是因为催化剂颗粒进入了原来碳化硅结构产生通道并将硅气化而成。图4a、4b为本发明中所产两个典型的透射电子显微图,图4a中石墨的层状结构明显可见,而且呈现三维空间立体交叉结构。图4b中除了三维的堆积结构,小片的单层石墨烯样品也清晰可见。图5为本实施例中所产三维石墨烯的拉曼光谱图,该图可以证明三维石墨烯的存在。另外,X-射线衍射表面样品中含有不同于原硅粉的纳米硅颗粒,这也在透射电子显微照片中的到证实。图6a、6b分别为本实施例中所产三维石墨烯作为锂离子电池电极材料的电化学充放电测试结果图及电池充放电倍率图,从图中可以看出在非常高的功率密度(50C)下仍然具有大于200mAh的容量。实施例12与实施例11中的条件一样,只是在粉末中加入占硅渣重量10%CoCl3·6H2O催化剂,气化气体原料为200mL/minCl2,二小时后,冷凝生成物为120克99.5%的四氯化硅,反应器内剩余残渣主要是碳黑(未能完全收集)。实施例13将石油焦同水蒸气在900℃,处理2小时得到材料A,将该材料A进行透射电子显微镜分析,其透射电子显微镜分析图如图7所示,从图7中可以看出该材料中包含石墨烯结构。如图7所示,可以看出片状石墨烯成为主要成分。实施例14对于炭化热固性酚醛树脂,采用与实施例13同样的处理,处理后再对所得材料进行透射电子显微镜分析,其透射电子显微镜分析图如图8所示,从图8中可以看出该材料中包含石墨烯结构(线条为石墨烯层状结构)和少量非晶碳。最后应说明的是,以上各实施例仅用以说明本发明的技术方案,而非对其限制;尽管参照前述各实施例对本发明进行了详细的说明,本领域的普通技术人员应当理解:其依然可以对前述各实施例所记载的技术方案进行修改,或者对其中部分或者全部技术特征进行等同替换;而这些修改或者替换,并不使相应技术方案的本质脱离本发明各实施例技术方案的范围。当前第1页1 2 3