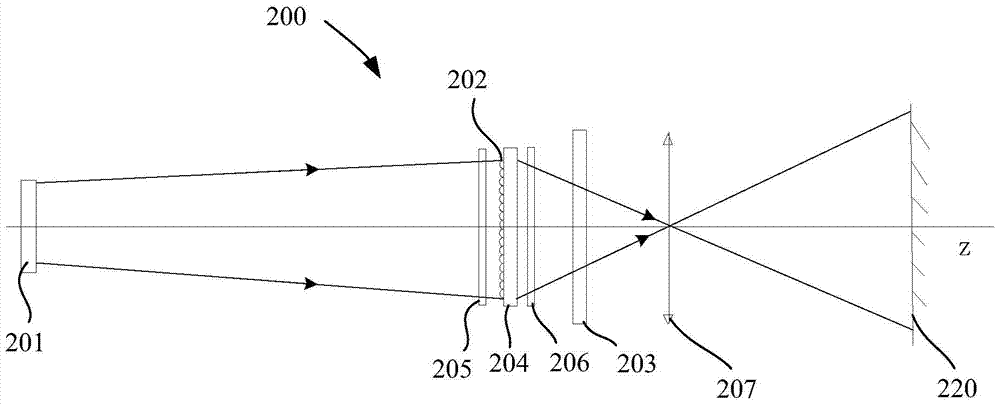
本发明涉及光固化型3D打印设备,尤其是涉及光固化型3D打印设备的成像系统。
背景技术:
:3D打印技术,是以计算机三维设计模型为蓝本,通过软件分层离散和数控成型系统,利用激光束、热熔喷嘴等方式将金属粉末、陶瓷粉末、塑料、细胞组织等特殊材料进行逐层堆积黏结,最终叠加成型,制造出实体产品。与传统制造业通过模具、车铣等机械加工方式对原材料进行定型、切削以最终生产成品不同,3D打印将三维实体变为若干个二维平面,通过对材料处理并逐层叠加进行生产,大大降低了制造的复杂度。这种数字化制造模式不需要复杂的工艺、不需要庞大的机床、不需要众多的人力,直接从计算机图形数据中便可生成任何形状的零件,使生产制造得以向更广的生产人群范围延伸。目前3D打印技术的成型方式仍在不断演变,所使用的材料也多种多样。在各种成型方式中,光固化法是较为成熟的方式。光固化法是利用光敏树脂被紫外激光照射后发生固化的原理,进行材料累加成型,具有成型精度高、表面光洁度好、材料利用率高等特点。图1示出光固化型3D打印设备的基本结构。这一3D打印设备100包括用于容纳光敏树脂的物料槽110、用于使光敏树脂固化的成像系统120、以及用于连接成型工件的升降台130。成像系统120位于物料槽110上方,并可照射光束图像使物料槽110液面的一层光敏树脂被固化。每次成像系统120照射光束图像致使一层光敏树脂固化后,升降台130都会带动成型的那层光敏树脂略微下降,并通过刮板131使固化后的工件顶面均匀铺展光敏树脂,等待下一次照射。如此循环,将会得到逐层累加成型的三维工件。成像系统120普通通常使用的是激光成型技术或者数字光处理(DigitalLightProcession,DLP)投影技术。激光成型技术是使用激光扫描设备进行逐点扫描。但是由于光敏树脂的特性,激光功功率不能过大,否则会损伤树脂。因此,激光移动速度被限制在几米到十几米/秒,造成成型速度过慢。DLP投影成像技术是使用数字微镜元件(DigitalMicromirrorDevice,DMD)控制对光的反射来实现的。数字微镜元件可视为一镜面。这面镜子是由数十万乃至上百万个微镜所组成的。每一个微镜代表一个像素,图像就由这些像素所构成。每一个微镜可独立受控以决定是否反射光线到投影镜头。最终,整面镜子反射出所需的光束图像。由于DMD芯片分辨率的限制,造成DLP投影成像技术成型尺寸较小的缺点,存在瓶颈。液晶投影技术作为一种面阵图象源,理论上可以投影与DLP投影成像技术相似的光束图像,从而可用来构造光固化型3D打印设备的成像系统。液晶面板中包含了许多像素,每个像素可以单独控制偏振光的偏振方向,配合液晶面板两侧的偏振光滤光器可控制某一像素的光线是否通过,因此经过液晶面板系统的光束是图像化的。然而液晶面板使用在光固化型3D打印设备中有明显的不足。原因在于光敏树脂需要的固化光源的波长通常在430nm以下,这一波长范围的光线对液晶面板中的液晶是有伤害的,会缩短液晶的寿命。而且液晶面板不高的透光率,会使面板寿命进一步缩短。众所周知,液晶面板在每一个像素的周围有一定面积不透光的黑色掩模区域,用来覆盖像素的控制电路(包括薄膜晶体管、布线等)。这部分掩模区域将减少LCD面板透光能力,从而影响成像系统的亮度和对比度。透光区域(即未被掩模覆盖的区域)占全部像素面积的比率称为开口率(apertureratio)。假设液晶面板的开口率为60%,意味着有高达40%的面积无法透光,这对光亮度的损失是很大的。同时,这些光线被液晶面板吸收后,将造成液晶过高的温升,造成液晶面板老化和损坏。改善上述问题的一种方式是尽可能提高开口率。这固然有助于减少光损失,但是开口率的提高在技术上有极限的,依赖于更先进的液晶面板制造工艺。因此在光固化型3D打印设备中,弥补透光率不足的方式是使用更高亮度的光源。然而在光固化型3D打印设备本就需要较强的投影亮度的情况下,一味提高通过液晶面板的光线亮度,加剧了液晶寿命的缩短。下表1示出在液晶投影技术中液晶接受到足够强各种波长的光照射后的寿命比较。光波长(nm)寿命4100.44331.04704.2表1从表1可以看出,以光波长在433nm的寿命为基准1,则当波长下降到410nm时,寿命显著下降到0.4。与之形成明显对比的是,波长在470nm时,寿命显著上升到4.2。由于上述的寿命方面缺陷,目前尚未有应用液晶系统的光固化型3D打印设备出现。技术实现要素:本发明的目的是提供一种光固化型3D打印设备及其成像系统,其基于液晶系统,且可以在可接受的较低光功率下投影出光固化所需的光束图像。本发明提供一种光固化型3D打印设备的成像系统,包括光源、液晶面板、第一偏振光滤光器、第二偏振光滤光器、聚焦透镜阵列、投影镜头、偏转镜片以及控制器。光源出射一光束。液晶面板位于该光源的出光光路上,该液晶面板包含多个像素。第一偏振光滤光器设置于该液晶面板的入光侧,第二偏振光滤光器设置于该液晶面板的出光侧,该第一偏振光滤光器和该第二偏振光滤光器配合该液晶面板遮挡该光束的一部分,以形成一光束图像。聚焦透镜阵列设置于该液晶面板的入光侧,该聚焦透镜阵列的每一聚焦透镜对应该液晶面板的每一像素,每一聚焦透镜能够会聚照射到对应像素的光束,使该光束尽可能多的透过该像素的透光区域,并在该液晶面板的出光侧成像,且像的尺寸小于对应像素的透光区域的尺寸。投影镜头布置在该液晶面板与光敏材料表面之间,且位于该像与该光敏材料表面之间,将该光束图像投影到该光敏材料表面,使该光源通过各聚焦透镜所成的像在该光敏材料表面形成多个光斑。偏转镜片布置在该液晶面板的出光侧,该偏转镜片能够围绕垂直于该成像系统的光轴的至少一转轴偏转,以微调该光束图像投影到该光敏材料表面的位置。控制器命令该光源进行多次曝光,在每次曝光时命令该偏转镜片进行偏转,以将各次曝光的光束图像投影到该光敏材料表面的不同位置。在本发明的一实施例中,该聚焦透镜阵列覆盖在该液晶面板上。在本发明的一实施例中,各次曝光的光束图像在该光敏材料表面所形成的各个光斑基本上互不重叠。在本发明的一实施例中,各次曝光的光束图像所形成的光斑布满该光敏材料表面。在本发明的一实施例中,其中该像的尺寸小于、等于或略大于该液晶面板的像素尺寸的一半。在本发明的一实施例中,各次曝光的光束图像包含相同的图像信息。在本发明的一实施例中,各次曝光的光束图像包含不同的图像信息。在本发明的一实施例中,该像的尺寸与该液晶面板的像素尺寸之比大约为1:2、1:3或1:4,同时该光源的曝光次数为4、9或16次。在本发明的一实施例中,设该光源与该聚焦透镜的距离为L1,该聚焦透镜到成像面的距离是L2,该聚焦透镜的前焦距和后焦距分别为f和f’,该光源的尺寸为A,该像的尺寸为d,则满足以下条件:f’/L2+f/L1=1;L1/L2=A/d。在本发明的一实施例中,该光束的波长在430nm以下。本发明还提出一种光固化型3D打印设备的成像系统,包括光源、液晶面板、第一偏振光滤光器、第二偏振光滤光器、聚焦透镜阵列、投影镜头、微位移驱动机构以及控制器。光源出射一光束。液晶面板位于该光源的出光光路上,该液晶面板包含多个像素。第一偏振光滤光器设置于该液晶面板的入光侧。第二偏振光滤光器设置于该液晶面板的出光侧,该第一偏振光滤光器和该第二偏振光滤光器配合该液晶面板遮挡该光束的一部分,以形成一光束图像。聚焦透镜阵列设置于该液晶面板的入光侧,该聚焦透镜阵列的每一聚焦透镜对应该液晶面板的每一像素,每一聚焦透镜能够会聚照射到对应像素的光束,使该光束尽可能多的透过该像素的透光区域,并在该液晶面板的出光侧成像,且像的尺寸小于对应像素的透光区域的尺寸。投影镜头布置在该液晶面板与光敏材料表面之间,且位于该像与该光敏材料表面之间,将该光束图像投影到该光敏材料表面,使该光源通过各聚焦透镜所成的像在该光敏材料表面形成多个光斑。微位移驱动机构连接该液晶面板,能够驱动该液晶面板在相互垂直的第一方向和第二方向移动,以微调该光束图像投影到该光敏材料表面的位置。控制器命令该光源进行多次曝光,在每次曝光时命令该微位移驱动机构动作,以将各次曝光的光束图像投影到该光敏材料表面的不同位置。本发明还提出一种光固化型3D打印设备,包括如上所述的成像系统。本发明的上述技术方案通过设置聚焦透镜阵列,将照射到液晶面板上的光束会聚,使其尽可能多透过液晶面板的各像素的透光区域,以减小直至避免液晶面板的不透光部分的遮挡。而且通过光束会聚,使照射到光敏材料表面上的光斑亮度显著提高。在液晶面板总体光通量较小的情况下,仍能达到树脂感光阀值,并进入其感光的相对线性区段,大幅提高固化速度,延长LCD寿命。此外,光固化材料在固化时,材料会有一定量的收缩,当大面积光固化材料同时感光固化时,会产生较大的连续的内应力,使固化的物体翘曲、变形,本发明通过多次曝光来使光敏材料的不同像素点分时固化,避免了大面积光固化材料同时固化的情况发生,降低像素点固化收缩时对周围像素点拉扯的影响,从而改善了打印体翘曲、变形的程度。附图说明为让本发明的上述目的、特征和优点能更明显易懂,以下结合附图对本发明的具体实施方式作详细说明,其中:图1示出光固化型3D打印设备的基本结构。图2示出本发明一实施例的3D打印设备的成像系统。图3示出本发明一实施例的聚焦透镜阵列与液晶显示面板的配合关系。图4示出图2所示成像系统单个像素的光路原理图。图5示出液晶面板上的黑色掩模。图6示出本发明实施例的成像系统一次曝光在光敏材料表面上所形成的图像。图7示出本发明实施例的成像系统的未进行偏转的光线示意图。图8示出本发明实施例的成像系统的已进行偏转的光线示意图。图9示出本发明另一实施例的3D打印设备的成像系统。图10示出本发明一实施例的成像系统4次曝光在光敏材料表面上所形成的图像。图11示出光敏树脂固化所需的能量与光照功率的关系曲线。图12示出本发明另一实施例的成像系统4次曝光在光敏材料表面上所形成的图像。具体实施方式本发明的实施例描述一种光固化型3D打印设备及其成像系统,该成像系统使用液晶面板作为面阵图像源。为避免液晶面板寿命的显著缩短,本发明的实施例可以在可接受的较低光源功率下投影出满足光固化所需亮度的光斑图像。图2示出本发明一实施例的3D打印设备的成像系统。参照图2所示,本实施例的成像系统200包括光源201、聚焦透镜阵列202、偏转镜片203、液晶面板204、第一偏振光滤光器205、第二偏振光滤光器206、投影镜头207以及控制器(图未示出)。为简明起见,不示出与本发明无关的器件。光源201可出射一光束。光源201所发出的光的波长随固化成型的光敏材料而定。例如,选择UV树脂作为光敏材料时,光束可为紫光至紫外光,其波长在430nm以下,例如400-405nm。液晶面板204位于光源201的出光光路上。液晶面板204包含有多个像素,其主要作用是偏转光源201所发出的光束的偏振方向,配合偏振光滤光器可遮挡光源发出的一部分光,以形成光束图像。液晶面板204的入光侧和出光侧分别设置第一偏振光滤光器205和第二偏振光滤光器206,组成液晶系统。第一偏振光滤光器205和第二偏振光滤光器206只允许和其极化方向相同的光通过,而且二者极化方向相互垂直。在没有液晶面板204的情况下,第一偏振光滤光器205和第二偏振光滤光器206会阻断所有试图穿透的光线。但是,由于两个偏振光滤光器之间为液晶面板204。液晶面板204被分隔为许多充满液晶的液晶单元。每一液晶单元对应一个像素。光线穿出第一偏振光滤光器205后,经过液晶面板204,会被液晶分子扭转一定角度,扭转角度受加在液晶面板上的电压控制。这些光线只有和第二偏振光滤光器206极化方向相同的分量才能从第二偏振光滤光器206中穿出。因此,个别控制各液晶单元的液晶分子的排列方向,就可控制光线透过液晶系统的亮度和图像。当用于3D打印时,液晶面板204所形成的光束图像可以只包含灰阶信息。因此,液晶面板204可不需要彩色滤色片等在用作显示面板时需要的光学元件。在本发明的实施例中,第一偏振光滤光器205可以是偏振片或者偏振光分光棱镜。第二偏振光滤光器206也可以是偏振片或者偏振光分光棱镜。对液晶面板204的每一像素而言,由于液晶单元附近需要布置薄膜晶体管和布线等,并无法让光束全部通过。考虑到包含透光率在内的各种光能量损失,光源201需要达到一定的照射功率才能使光敏材料固化,或者使固化的时间在可接受的程度。如前文所述,波长在430nm以下的光,达到一定功率后对液晶的损害较大。因此如何在满足使光敏材料固化的条件下,尽可能地降低光源201的照射功率成为基于液晶面板的成像系统可实施的关键。本实施例引入聚焦透镜阵列202并配合对聚焦程度的控制来达成前述目的。聚焦透镜阵列202设置于液晶面板204的入光侧。聚焦透镜阵列202包含了许多微小的聚焦透镜。每一聚焦透镜对应液晶面板204的每一像素。图3示出本发明一实施例的聚焦透镜阵列与液晶面板的配合关系。在此实施例中,聚焦透镜阵列202是覆盖在液晶面板204上。举例来说,某一聚焦透镜402对应液晶面板204的某一像素404。此像素404包含不透光的黑色掩模404a和透光区域404b。聚焦透镜阵列202可以是由树脂材料压制而成。通过布置在液晶面板的入光侧聚焦透镜的聚焦作用,可以使更多的光透过液晶面板,并且提高了液晶面板的出光侧的聚焦点亮度。这种设计带来两个有利的效果:首先,光源201的照射功率没有提高,因此液晶面板免于受到更高光强的紫外光照射;其次,经过聚焦后,聚焦点亮度得到成倍提升,该聚焦点最终成像与光敏材料,使其更容易固化。在此,聚焦点亮度取决于聚焦程度。在本实施例中,光源201的形状、面积、发散角、到液晶面板204的距离需要被严格设计,以得到所期望的光斑亮度,后文将详细描述。图4示出图2所示成像系统单个像素的光路原理图。参照图4所示,光源201发出光束,设其发光面的高和宽都为A,光源发散角能够配合液晶面板204需要照射的面积,光源201到聚焦透镜阵列402的距离为L1,光束照射到聚焦透镜阵列202,其中部分光线照射到某一聚焦透镜402,对应液晶面板204的某一像素404。像素404的尺寸为P。聚焦透镜402会对光源201发出的光束进行汇聚,同时,在聚焦透镜402后端会产生光源201的像401a。像401a经过投影镜头207后,投影在光敏材料(图中未示出)表面上形成光斑。设聚焦透镜的前焦距为f,后焦距为f’(f’≈f),光源201的像高为d,聚焦透镜402到成像面的距离为L2,按照高斯公式我们可以得到:f/L1+f’/L2=1;L1/L2=A/d。在一个示例中,f=100μm,P=20μm,L1=200mm,A=20mm代入上式则:100μm/200mm+100μm/L2=1;L2=100.05μm;200mm/100.05μm=20mm/d;d=10μm。通过上述计算可知,可以通过适当的设计,控制成像光斑的大小。在此,光斑越小,意味着聚焦程度越高,则聚焦后的光斑亮度越高。与之对照的是,如果液晶面板用于投影显示,通过设计使光斑尽量大些,只要能通过黑色掩模即可,这样对比度最高,画面质量最好。然而这种设计不适用于3D打印。事实上由于聚焦透镜402可能的制造缺陷,特别是光的衍射效应的存在,光斑尺寸会略大于实际计算,而且光斑的形状也可能成为圆形,而和光源201原来的形状不一样,这需要在实际试验中对前述参数进行调整,以确定最终数据。无论如何这种会聚作用具有多种潜在的技术效果。首先,经过会聚之后的光束在聚焦点的亮度更高,比如,如果尺寸减小为1/2则亮度将提高至原来的4倍,这对光敏材料的感光有利,后文将展开描述。其次,光束的尽可能透过减少了液晶面板吸收光束而产生的热量,有助于延长液晶面板寿命。再者,经过会聚之后的光束,在光敏材料表面上所形成的光斑尺寸较小,有助于提升打印的分辨率。下面将描述如何发挥上述潜在的技术效果。投影镜头207布置在液晶面板204与三维打印设备的光敏材料表面220之间,将液晶面板204及偏振光滤光器205、206所形成并出射的光束图像投影到光敏材料表面220。再参考图4所示,光源201在液晶面板204的每一像素后有一像401a。投影镜头207的位置,则是位于该像与光敏材料表面之间,如图4所显示的那样。因此,光源201经液晶面板204后形成的多个像将清晰地投影到光敏材料表面220上。可使会聚后的像401a的尺寸与液晶像素尺寸之比为1:2,即面积之比为1:4,这会使亮度相应为原来的4倍。尽管经过投影,像401a的尺寸会扩大,但这一比例在像401a投影到光敏材料表面上时会保持不变。下面将参考光敏材料表面的光斑来继续讨论比例的设定。图6示出本发明实施例的成像系统一次曝光在光敏材料表面上所形成的图像。作为比较,如果光线直接通过图5示出的成像系统的黑色掩模进行成像,则会得到类似于此黑色掩模的图像。比较图5和图6可知,经过聚焦透镜阵列202的会聚后,图像中光斑的尺寸缩小了,而光斑亮度则相应提高了。通过如前文所述的适当的光学设计来调整会聚的程度,以决定光斑的尺寸缩小比例。举例来说,可使会聚后的光斑尺寸(像401a投影在光敏材料表面的尺寸)与像素尺寸(液晶像素投影在光敏材料表面的尺寸)之比为1:2,即面积之比为1:4,亮度则相应为原来的4倍。因此,总的到达光敏材料表面的能量没有减少。可以理解,考虑到前述聚焦透镜402制造的缺陷和光的衍射效应等因素,当所设计光斑尺寸与像素尺寸之比为1:2时,实际的光斑尺寸与像素尺寸之比会略大于1:2。本实施例的成像系统允许适当的误差,即前述尺寸之比约为1:2。此外,可使会聚后的光斑尺寸与像素尺寸之比约为1:3或1:4。这里取整数倍的原因是考虑到后续偏转时,需要在各个光斑的空白部分插入新的光斑。如图6所示,光敏材料表面上一次曝光的图像中,光斑之间留有空白。为此,通过多次曝光来填补这些空白,使光斑布满整个光敏材料表面。在本实施例中,在液晶面板204的出光侧,例如液晶面板204与投影镜头207之间(或者投影镜头207之后)布置有偏转镜片203。偏转镜片203能够围绕至少一转轴偏转,以微调光束图像投影到光敏材料表面220的位置。前述的转轴均垂直于成像系统的光轴z,在偏转镜片和液晶面板204平行(和光轴z垂直)时,光线垂直照射在偏转镜片203,这时没有折射现象发生,光线a直接经过偏转镜片(如图7);如果偏转镜片203围绕一转轴倾斜一个角度,光线从空气进入偏转镜片203将会产生折射,光线从偏转镜片203进入空气时再次发生折射,两个折射的折射角度相同,方向相反,折射后的光线b将按原有方向前进,但是发生微小的位移(如图8)。举例来说,偏转透镜的这一转轴是图7所示的转轴x。另外,这一转轴可以是位于包含转轴x且垂直于光轴z的平面内,且垂直于转轴x的转轴y(图未示出)。在本发明的实施例中,偏转镜片203可以既能够绕转轴x偏转,也能绕转轴y偏转。上述的偏转可以结合多次曝光,使各次曝光的光束图像叠加,令光斑布满光敏材料表面220。具体地说,可以令光源201进行多次曝光,在每次曝光时,命令偏转镜片203进行偏转以将各次曝光的光束图像投影到该光敏材料表面的不同位置。图10示出本发明实施例的成像系统4次曝光在光敏材料表面上所形成的图像。参照图10所示,在第一次曝光时,形成了投影图像A;在第二次曝光时,由于偏转镜片203绕着x轴偏转,使光束图像略微沿图中的水平方向移动,投影到两列光斑之间的空白中,形成投影图像B;在第三次曝光时,偏转镜片203绕着y轴偏转,使光束图像略微沿图中的垂直方向移动,投影到两行光斑之间的空白中,形成投影图像C;同理,形成投影图像D。投影图像D已布满了光敏材料表面220。在实际实施时,可以使用成像系统200的控制器,命令光源201进行多次曝光,同时在每次曝光时命令该偏转镜片203配合进行x、y两个方向的偏转。在本发明的另一实施例中,如图9所示,液晶面板204连接有微位移驱动机构208以代替偏转镜片203。微位移驱动机构208能够驱动液晶面板在x方向和y方向移动,以微调光束图像投影到光敏材料表面220的位置。在此,x、y方向在同一平面,且这一平面垂直于成像系统的光轴z。在微位移驱动机构208没有驱动液晶面板位移时,液晶面板204的光束图像在光敏材料表面220的第一位置;当微位移驱动机构208驱动液晶面板204在一方向(x或y方向)微位移时,液晶面板204的整个光束图像将随着液晶面板204发生微小的位移。微位移驱动机构208可以是压电陶瓷。在图4和图9的实施例以及本发明的其它实施例中,光路还可以采用远心光路实现。需要指出的是,各次曝光的光束图像的叠加虽然布满该光敏材料表面,但是各次曝光的光束图像在光敏材料表面220的位置可以基本上互不重叠。这是通过控制像素尺寸与光斑的尺寸之比为整数,且偏转的步距刚好为光斑尺寸来实现的。这种基本上互不重叠的设置可以避免重叠区域所接收的光照高于平均水平,造成固化的不均匀。可以理解,考虑光衍射效应等因素,略微的重叠有助于弥补光斑非矩形边缘部分的缺失。因此并不要求光斑之间完全不重叠。此外,光束图像的叠加虽然布满该光敏材料表面,但是可以理解,光束图像中并非每个位置都是亮点,而是可能有暗点。在本发明的一实施例中,各次曝光的光束图像可以包含相同的图像信息。以图10为例,投影图像D中,虚框内的四个光斑包含相同的图像信息。这一实施例的优势在于提高每次曝光时,到达光敏材料表面光斑的亮度。上述的例子是在控制光斑尺寸为像素尺寸的1/2时,进行4次曝光。可以理解,控制光斑为像素尺寸的1/3时进行9次曝光,控制光斑为像素尺寸的1/4时进行16次曝光,以次类推。接下来说明曝光亮度有利于光敏材料的感光的原理。光敏材料接受一定量的光照射后,在一定时间内会固化,这一时间称为固化时间。光照射的功率,即光敏材料在单位时间内接收到的光照能量,会显著影响固化时间。理论上一定面积的光敏材料的固化需要的能量可以表达为:W=P*t,P为照射到树脂上的光功率,t为曝光时间。即,可以通过提高光功率减少曝光时间或较小光功率增加曝光时间来达到同样的能量以达到同样的固化效果,这称为“互易律”。但是在光敏树脂中存在互易律失真的情形。图11示出光敏树脂固化所需的能量与光照功率的关系曲线。如图11所示,x轴表示光照功率,y轴表示固化需要的能量W。曲线表示在不同光照功率下,一定面积的光敏材料的固化需要的能量。当光照功率在P0以下时,需要能量W为无穷大,由于t=W/P,即需要无穷大时间。曲线包含了线性段(图中接近水平的部分)和非线性段(图中斜线部分)。在线性段,随着光照功率加大,所需固化时间和光照功率成反比,固化需要的能量基本不变;在非线性段,随着光照功率减小,所需固化时间非线性快速增加,固化需要的能量非线性增大。总结来说,光敏树脂具有以下特性:1.光照射的功率必须达到一定的下限P0,才可能发生固化,低于这一功率无论如何延长曝光时间,也不能固化,这一光功率称为阀值功率。2.只有在线性段,才能基本符合上述“互易律”。3.但是在接近P0的区域,光照功率的微小减低都需要大量增加曝光时间才能使树脂固化到同样程度。由于光敏树脂需要的光照的波长在430nm以下,这一波长的光线过强对液晶面板中的液晶是有伤害的。因此使用液晶面板的3D打印设备,其光照强度会选择较低,例如设定在略大于P0的位置,以延长液晶面板的寿命。然而这也意味着,需要大量增加曝光时间才能使光敏树脂固化,这大大降低了感光速度。本发明的实施例通过缩小光斑,成倍增加光斑亮度,从而使成像系统摆脱需要大量增加曝光时间才能使树脂固化的非线性段,进入相对线性段,从而大大减小了光敏材料的固化时间,提高了感光速度。同时,减少了固化需要的总能量W(这也是通过液晶面板的光能),延长了液晶面板的寿命。在本发明的另一实施例中,各次曝光的光束图像包含不同的图像信息。以图10为例,投影图像D中,虚框内的四个光斑包含互不相同的图像信息。这就意味着,图像的分辨率相应变为原来的4倍。因此3D打印的精度得到显著提高。此外,通过实验发现,这种通过多次曝光来使光敏材料的不同像素点分时固化的方法还有其它优点。具体地说,光固化材料在固化时,材料会有一定量的收缩,当大面积光固化材料同时感光固化时,会产生较大的连续的内应力,使固化的物体翘曲、变形。本发明上述实施例的方法,通过让不同像素点在不同时间固化,可以降低像素点固化收缩时对周围像素点拉扯的影响,从而改善了固化的物体翘曲、变形的程度。参考图10所示,先对光敏材料上间隔排列的多个像素点进行曝光固化形成投影图像A,各个像素点固化收缩时拉扯的周围区域都还是液态的光敏材料,液态材料的易变性抵消了拉扯的影响避免了内应力的累计;接着,进行第二次曝光固化形成投影图像B,这次固化的像素(偶数列)在上、下两个方向周围都还是液态的光敏材料,因此这两个方向的液态材料的易变性抵消了拉扯的影响;然后进行第三次曝光固化形成投影图像C,这次固化的像素(偶数行)在左侧方向周围还是液态的光敏材料,因此这个方向的液态材料的易变性抵消了拉扯的影响;最后进行第四次曝光固化形成投影图像D,只有这次固化的像素周围均是固态的光敏材料。但这时只有1/4的材料被固化,而且聚焦后像素点的特性是中间比周围更亮,这样在固化发生时像素中间会比边缘更快固化,中间固化时的内应力还可被周围未固化树脂吸收一部分,等完全固化时积聚的内应力已十分小了。更重要的是,因同一时刻只有相互隔开的像素点在进行固化,而相邻的像素不会同时进行固化,避免了各个像素点同时固化时的互相拉扯。在较佳实施例中,参考图12所示,在进行第一次曝光固化形成投影图像A后,接着进行第二次曝光固化形成投影图像B。投影图像B中进行固化的像素点与投影图像A中固化的像素点位于对角而互不相邻,因而这次固化的像素在周围四个方向都还是液态的光敏材料,液态材料的易变性抵消了拉扯的影响。然后进行第三次曝光固化形成投影图像C和第四次曝光固化形成投影图像D的方式和图10所示实施例相同,在此不再展开。同理,在进行9次曝光或16次曝光时,也可以优先让相互间像素点互不相邻的几个投影图像先进行曝光,以最大程度地减少相互拉扯的影响。本发明的上述实施例通过设置聚焦透镜阵列,将照射到液晶面板上的光束会聚,使其能透过液晶面板的各像素的透光区域,尽可能穿过液晶面板,以减小直至避免液晶面板的不透光部分的遮挡。而且通过光束会聚,使照射到光敏材料表面上的光斑面积缩小,亮度显著提高,在液晶面板总体光通量较小的情况下,仍能达到光敏树脂感光阀值,提高感光速度。再者,通过多次曝光配合偏转镜片的微位移可将光敏材料表面填满曝光光斑,再针对各次曝光使用不同成像信息,可提高成像的分辨率,从而提高打印的精度。另外,由于通过多次曝光来使光敏材料的不同像素点分时固化,可以降低像素点固化收缩时对周围像素点拉扯的作用,从而改善了打印体翘曲和变形程度。虽然本发明已以较佳实施例揭示如上,然其并非用以限定本发明,任何本领域技术人员,在不脱离本发明的精神和范围内,当可作些许的修改和完善,因此本发明的保护范围当以权利要求书所界定的为准。当前第1页1 2 3