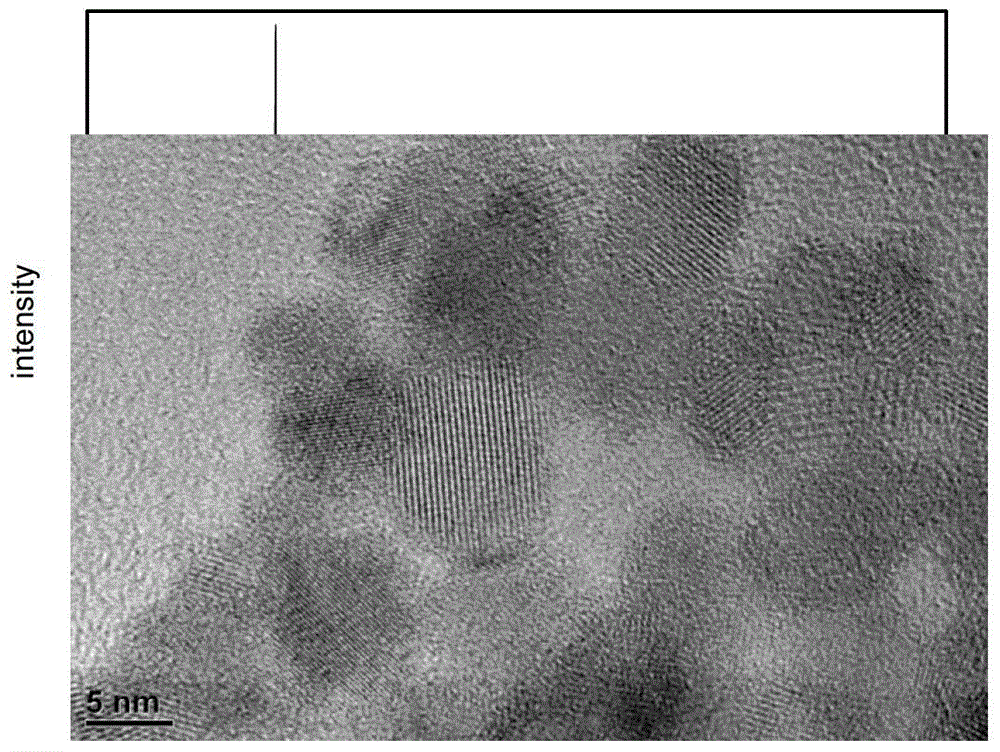
本发明涉及石油化工领域,具体地说,涉及一种FCC再生烟气脱硝用复合氧化物催化剂及其制备方法。
背景技术:催化裂化(FCC)装置是原油深度加工过程中的重要单元,在炼油工业中占有举足轻重的地位。在催化裂化反应过程中,原料油发生裂化的同时,其中30%~50%的含氮化合物进入油焦,并随之沉积在催化剂表面。催化剂因表面附着油焦而活性降低,必须进行再生处理。在再生器烧焦过程中,大部分含氮化合物转化为N2,但也有10%~30%转化为NOx,随再生烟气排出。其中主要成分为NO,体积百分数约为90%,剩余10%左右为NO2。根据原料和操作条件的不同,再生烟气中NOx浓度也存在差异,但普遍高于《大气污染物综合排放标准》(GB16297-1996)中要求的420mg/m3(1997年以前建设的装置)和240mg/m3(1997年及以后建设的装置),且均未配备烟气脱硝设施。另一方面,由于原油加工业的迅速发展和原油劣质化的不利影响,炼油企业的NOx排放量越来越大。通常,再生烟气是炼油厂NOx排放的主要来源,约占其总排放量的50%。截止目前,中国石油共有41套FCC装置,总生产能力达5080万吨/年,再生烟气排放总量超过500万Nm3/h,NOx年排放量约为1.2万吨。如果采用烟气脱硝技术对其进行处理,以NOx去除率为80%计算,仅此一项,就可实现集团公司NOx排放量降低10%。可见,FCC再生烟气中NOx排放问题已成为中国石油各炼油企业的共性问题,严重地制约了中国石油节能减排和清洁生产工作的向前推进。可以预见,随着环保标准的日益严格,中国石油各炼油企业对FCC再生烟气脱硝技术的生产需求必将迅速扩大。目前,国内外也已工业应用的FCC再生烟气脱硝技术包括:低NOx烧焦技术、氧化吸收法、添加助剂法、选择性非催化还原(SNCR)法和选择性催化还原(SCR)法。五种FCC再生烟气脱硝技术特点不同,分别适用于不同的处理条件和处理要求,需要因地制宜地进行选择。但是,就中国石油现有的41套FCC装置而言,若要从整体上解决再生烟气脱硝问题,选择性催化还原(SCR)因处理效果稳定、适应范围广、工艺成熟,无疑是最有竞争力的技术。目前,国内已申请了很多关于SCR催化剂的专利。公开号为CN101480611介绍了一种水溶液体系中原位钒掺杂钛基脱硝催化剂,但是由于是水溶液体系,所以钒的掺杂形式主要是在钛氧化物的表面;公开号为CN102198397介绍了一种利用沉淀法,通过添加硅溶胶合成具有高比表面积的纳米二氧化钛载体,从而使活性组分之间产生强的相互作用,提高催化剂的活性。
技术实现要素:本发明的目的在于提供一种FCC再生烟气脱硝用催化剂,其是一种乙醇体系中的原位骨架掺杂钒的纳米二氧化钛,使催化剂的活性组分直接分散在二氧化钛的骨架中,分散性好。该方法制备简单,且合成的全为结晶度较高的锐钛矿晶型,在很宽的温度区间具有很好的活性,具有很好的抗SO2性能。本发明所制备是基于乙醇体系,采用溶胶凝胶法合成的原位骨架掺杂钒的纳米二氧化钛催化剂。钒的掺杂量为0.8%~1.4%,活性组分钒进入二氧化钛的骨架。本发明所述的钒钛骨架掺杂氧化物催化剂及其制备方法,包括如下步骤:(1)将0.5~2gP123溶解到10~30g乙醇中称为a液;(2)将0.0338~0.0591g钒源溶解到1~2g浓缩的HCl和0.2~0.6g44%的H2SO4中称为b液;(3)将b液加入a液中,至于水浴中,在40~50℃下强力搅拌溶解3~4小时,获得均一透明溶胶;(4)然后加入3~4g钛源,继续强力搅拌20~25小时;(5)用培养皿转移至恒温恒湿干燥箱中,溶剂蒸发并诱导P123的自组装,蒸发诱导后形成凝胶,然后干燥,最终在N2气氛以及空气气氛下焙烧获得催化剂;溶剂蒸发并诱导P123自组装过程:保持恒温恒湿,温度40~50℃,相对湿度50~60%,蒸发诱导时间持续40~50小时所采用的前躯体钒源是偏钒酸铵、钛源是异丙醇钛。所述的凝胶的干燥温度为100~120℃,持续40~50h。所述的焙烧条件为在氮气氛中300~400℃气氛下处理3~4h,随后在空气中400~500℃焙烧6~7h,升温速率为每分钟1~2℃。本复合氧化物催化剂用作FCC再生烟气脱硝用催化剂,在其作用下进行高效选择催化还原形成氮气进行消除。通过本发明,可制得纳米粒子形貌,抗热及抗二氧化硫稳定性较好的原位骨架掺杂的钒钛氧化物催化剂。该方法合成的钒钛氧化物催化剂比普通的钒钛催化剂具有较强的稳定性,较高的比表面积,并且在FCC再生烟气脱硝中具有较高的反应活性及抗SO2的性能。该合成方法简单,制备周期短,具有较好的应用前景。附图说明图1为实施例1制备的催化剂V2O5/TiO2的TEM照片图2为实施例1制备的催化剂V2O5/TiO2的HR-TEM照片图3为实施例1制备的催化剂V2O5/TiO2的XRD谱图图4为实施例1~4制备的催化剂V2O5/TiO2的活性测试图具体实施方式以下通过具体实施例介绍本发明的实现和所具有的有益效果,但不应据此对本发明的实施范围构成任何限定。催化剂的活性测试方法:催化剂压片后研磨过筛,取40~60目的部分。实验在连续流动的固定床反应器上进行,具体是将0.4g过筛后的催化剂装入到石英玻璃管中,管内温度由管式电阻炉和控温仪进行程序升温控制。混合气体模拟真实烟气,由其所对应的钢瓶提供。相应的混合气体组成为:CNO=CNH3=1000ppm,CO2=3%,平衡气为N2,体积空速为16000h-1。进出口NO的浓度值由ThermoFisher42iHLNO分析仪在线检测。NO转化率的具体计算公式如下:测得的活性结果如附图4所示。实施例11%V2O5/TiO2催化剂的制备将1gP123溶解到20g乙醇中称为a液,将0.0422g偏钒酸铵溶解到1.4g的HCl和0.46g的44%的H2SO4称为b液,将b液加入a液中,至于水浴中,强力搅拌,获得均一透明溶胶。随后加入15g异丙醇钛,继续强力搅拌一定时间,在相对湿度为50-60%下40℃空气中静置2天,形成的薄膜在100℃干燥2天,在氮气氛中350℃气氛下处理3h,随后在空气中450摄氏度焙烧6h。图1为实施例1制备的催化剂V2O5/TiO2的TEM照片,由图中显示,制备的催化剂颗粒粒径均在5~10nm,粒径均匀,具有纳米粉体形貌,颗粒间存在较大间隙;图2为实施例1制备的催化剂V2O5/TiO2的HR-TEM照片,由图中可以看到原子条纹相,条纹密集均匀;图3为实施例1制备的催化剂V2O5/TiO2的XRD谱图,结果显示,合成的催化剂显示为纯锐钛矿晶型,且结晶度较高,没有发现氧化钒的衍射峰,可能是由于钒的负载量较少,且分散均匀。图4为实施例1~4制备的催化剂V2O5/TiO2的活性测试图,结果显示当V2O5负载量为1%时,催化剂的催化活性表现出最佳效果。最高脱硝率能达到95.4%,在300~450℃都能保持80%以上的转化率。实施例20.8%V2O5/TiO2催化剂的制备将1gP123溶解到20g乙醇中称为a液,将0.0338g偏钒酸铵溶解到1.4g的HCl和0.46g的44%的H2SO4称为b液,将b液加入a液中,至于水浴中,强力搅拌,获得均一透明溶胶。随后加入15g异丙醇钛,继续强力搅拌一定时间,在相对湿度为50-60%下40℃空气中静置2天,形成的薄膜在100℃干燥2天,在氮气氛中350℃气氛下处理3h,随后在空气中450摄氏度焙烧6h。实施例31.2%V2O5/TiO2催化剂的制备将1gP123溶解到20g乙醇中称为a液,将0.0506g偏钒酸铵溶解到1.4g的HCl和0.46g的44%的H2SO4称为b液,将b液加入a液中,至于水浴中,强力搅拌,获得均一透明溶胶。随后加入15g异丙醇钛,继续强力搅拌一定时间,在相对湿度为50-60%下40℃空气中静置2天,形成的薄膜在100℃干燥2天,在氮气氛中350℃气氛下处理3h,随后在空气中450摄氏度焙烧6h。实施例41.4%V2O5/TiO2催化剂的制备将1gP123溶解到20g乙醇中称为a液,将0.0591g偏钒酸铵溶解到1.4g的HCl和0.46g的44%的H2SO4称为b液,将b液加入a液中,至于水浴中,强力搅拌,获得均一透明溶胶。随后加入15g异丙醇钛,继续强力搅拌一定时间,在相对湿度为50-60%下40℃空气中静置2天,形成的薄膜在100℃干燥2天,在氮气气氛中350℃气氛下处理3h,随后在空气中450摄氏度焙烧6h。