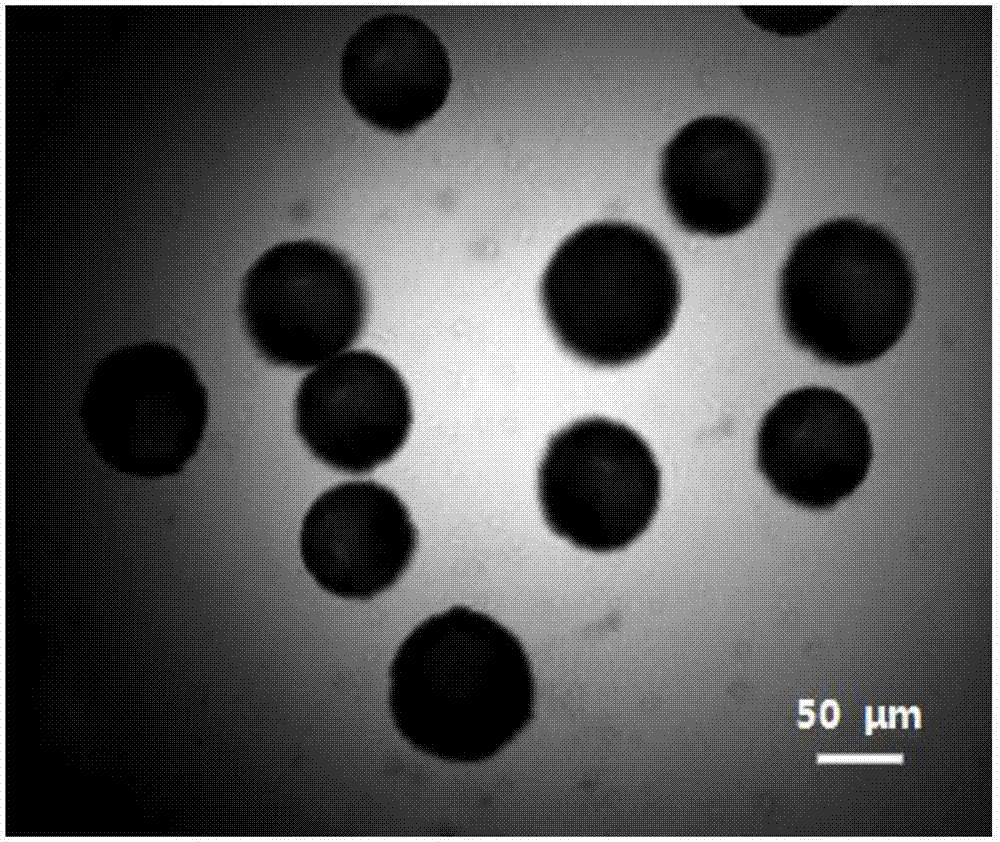
所属领域本发明涉及催化剂制备领域,具体涉及流化床蒽醌法制备过氧化氢的氢化过程用催化剂。
背景技术:
:流化床工艺广泛应用于化工、石油、能源、环保和冶金等工业领域中的气固、液固和气液固相反应过程,该工艺具有催化剂加入量少、传质性能优异以及反应物转化效率高等优点,对于气液通量、生产能力和反应速度等要求较高的反应,尤其对于强放热并需保持反应器温度稳定的反应,流化床反应器和流化床工艺是最理想的选择,因此在一些重要反应过程中,以流化床工艺取代原有的固定床工艺已成为一种趋势。在流化床工艺中,催化剂性质、流化过程的工艺条件和反应器结构是三个重要的影响因素,在各影响因素中催化剂性质占主导地位,而载体的选择对催化剂起着至关重要的作用,因此制备粒度大小适宜、孔结构优异和表面性质良好的流化床催化剂载体十分重要。氧化铝具有比表面大、孔结构优良和机械强度高等特点,作为催化剂载体获得了广泛应用。近年来,研究人员对微球形氧化铝载体的制备方法进行了深入研究。丁祥金等在挤出成型用喷雾造粒氧化铝粉料(工业催化,2005,2:36-42)中以氧化铝溶胶为结合剂,采用喷雾干燥技术制备微球形氧化铝。分析结果表明,该方法可以制备粒径范围适宜的微球形氧化铝载体,但该方法所制备的载体存在成球率低、表面粗糙且耐磨损强度低的缺点。研究表明,在氧化铝中引入适量的sio2能够对氧化铝的性质产生显著影响。专利usp7186757采用将si-al两种凝胶机械混合的方法制备含硅氧化铝,其中硅源为硅酸钠。结果表明,通过该方法制备的含硅氧化铝的比表面积较大且孔分布集中,但简单机械混合后硅铝结合较弱,导致样品稳定性差,因其硅源为硅酸钠,为了保证产物中具有较低钠含量,洗涤过程将产生大量的废水。liang等在studyonproductiontechnologyofisobutanedehydrogenationfluidcatalyst(catal.commun.2007,4,131-136)中研究了浸渍法负载sio2对微球形k2o-crox/al2o3催化剂的表面性质和催化活性的影响,结果表明,负载sio2后该催化剂的稳定性得到增强,但催化活性有所降低,其原因是浸渍法负载的sio2堵塞了al2o3载体的部分孔道,导致比表面降低,影响了活性组分crox的分散度,从而影响了其催化活性。本发明的有益效果:所采用的制备方法是基于油柱成型法原理,将铝溶胶与系列含硅前驱物在分子簇水平实现混合,通过对含硅前驱物的用量进行调控,得到具有大比表面积、适宜孔结构以及良好耐磨损强度的系列微球形sio2-al2o3,以sio2-al2o3为载体通过负载贵金属并对组成和结构进行调控,提出一种新型高分散负载型贵金属催化剂的制备方法,为流化床用微球形催化剂的制备提供新的研究思路和制备途径。技术实现要素:本发明的目的是提供一种微球形sio2-al2o3基贵金属催化剂及其制备方法。该催化剂可用于流化床蒽醌法制备过氧化氢的氢化过程,也可用于石油化工及精细化工生产中的加氢精制、选择性加氢和选择性氧化等反应过程。本发明提供的催化剂是以微球形sio2-al2o3为载体,以贵金属为活性组分,其中贵金属占催化剂的质量分数为0.1~20%,较佳的是0.5~5%。所述的贵金属为au、ag、pt或pd中的一种,较佳的是pd;所述的微球形sio2-al2o3载体的粒径为1~1000μm,较佳的粒径为10~500μm。其中sio2占载体的质量分数为1~30%,较佳的是2~15%;氧化铝晶型为γ、δ、η或θ中任意一种,较佳的是δ型或θ型。本发明提供的微球形sio2-al2o3基贵金属催化剂的制备方法,具体制备步骤如下:a.将铝粉加到质量浓度为5~20%的稀盐酸溶液中,在80~100℃条件下溶解,制备外观透明的铝溶胶;其中铝的质量含量为5~20%,较佳的为9~15%。b.向步骤a的铝溶胶中加入质量含量为20~50%的六次甲基四胺溶液充分混合,再加入硅溶胶充分混合制备成型溶胶,其中有机胺中的-nh2基或-nh-基与铝溶胶中的cl-离子的摩尔比为1.0~2.0,硅溶胶的加入量按照使载体中sio2占载体的质量分数为1~30%确定,较佳的是2~15%;将成型溶胶输送至分散喷头,在0.05~0.2mpa的压力下分散到温度为50~100℃的热油柱中成型;分离出成型后的微球,于100~200℃条件下老化2~12h;所述的硅溶胶是sio2质量含量为0.5~5%的硅溶胶,其ph值为5~7。硅溶胶的制备方法是:将质量浓度为2~15%的硅酸钠溶液通过阳离子交换树脂进行交换;所用的阳离子交换树脂是001×7(732)型强酸性聚苯乙烯系阳离子交换树脂、001×12/14/16型强酸性聚苯乙烯系阳离子交换树脂或7320型强酸性聚苯乙烯系阳离子交换树脂。硅溶胶也可以是市售的或其他方法得到的。成型过程中使用的油是定子油、液体石蜡、变压器油、通用机床油或真空泵油。c.将步骤b老化后的微球滤出,洗涤,于60~120℃下干燥5~20h,再于500~1300℃焙烧4~10h,得到微球形sio2-al2o3载体,颗粒尺寸为1~1000μm,较佳的粒径为10~500μm;其中sio2质量分数为1~30%,较佳的是2~15%;氧化铝的晶型为γ、δ、η或θ中的一种,较佳的是δ或θ型。d.用贵金属盐溶于水中配制浓度为0.01~0.30mol/l的浸渍溶液,将步骤c制备的微球形sio2-al2o3载体加入浸渍液中,按照催化剂中贵金属含量为0.5~5%确定浸渍溶液与载体的加入量;静置2~6h,使贵金属活性组分充分浸渍于载体上,待浸渍液的颜色逐渐退去,倒去上层透明溶液,用去离子水洗涤3~7次,室温下陈化12~24h;再以3~10℃·min-1的速率升温至100~200℃,保温4~8h,然后以5~15℃·min-1的速率升温至300~600℃,保温3~6h,冷却至室温,即得微球形sio2-al2o3基贵金属催化剂。所述贵金属盐为na2pdcl4、pd(nh3)2cl2、pd(no3)2、pd(ch3coo)2、haucl4、naaucl4、na2pt(oh)6、pt(no3)2、k2ptcl4、k2ptcl6、agno3或ag(nh3)2cl中的一种,较佳的是na2pdcl4或pd(ch3coo)2。图1为实施例1制备的微球形sio2-al2o3载体的显微分光光度计照片。从显微分光光度计照片可以看出,该微球形sio2-al2o3载体具有球形度高、表面光滑和粒径分布集中的特点,最可几粒径为57.1μm。图2为实施例1制备的微球形pd/sio2-al2o3催化剂的xrd图。从xrd图中并未发现sio2的特征衍射峰,证明sio2以无定型状态均匀分散。图3为实施例1制备的微球形pd/sio2-al2o3催化剂的hrtem照片。从hrtem照片可看出制备的负载型催化剂中,活性组分均匀地分散在载体表面,且颗粒尺寸范围为0.5~5nm,平均粒径为3.7nm。图4为实施例1制备的催化剂在流化床蒽醌加氢反应中的性能评价结果,(a)为蒽醌加氢活性随时间的变化曲线,(b)为蒽醌加氢稳定性随时间的变化曲线,(c)蒽醌加氢选择性随时间的变化曲线。图4表明,该催化剂在流化床蒽醌加氢反应中具有较高的催化活性、选择性和稳定性,其氢化效率为12.5g·l-1,选择性保持在97%。图1为实施例1制备的微球形sio2-al2o3载体的显微分光光度计照片。从显微分光光度计照片可以看出,该微球形sio2-al2o3载体具有球形度高、表面光滑和粒径分布集中的特点,最可几粒径为57.1μm。图2为实施例1制备的微球形pd/sio2-al2o3的n2吸脱附曲线和孔径分布图。从n2吸脱附曲线可以看出,该载体具有丰富的介孔结构,从孔径分布图可以看出,该载体孔道分布集中。图3为实施例1制备的微球形pd/sio2-al2o3催化剂的xrd图。从xrd图中并未发现sio2的特征衍射峰,证明sio2以无定型状态均匀分散。图4为实施例1制备的微球形pd/sio2-al2o3催化剂的hrtem照片。从hrtem照片可看出制备的负载型催化剂中,活性组分均匀地分散在载体表面,且颗粒尺寸范围为0.5~5nm,平均粒径为3.7nm。图5为实施例1制备的催化剂在流化床蒽醌加氢反应中的性能评价结果,(a)为蒽醌加氢活性随时间的变化曲线,(b)为蒽醌加氢稳定性随时间的变化曲线,(c)蒽醌加氢选择性随时间的变化曲线。图4表明,该催化剂在流化床蒽醌加氢反应中具有较高的催化活性、选择性和稳定性,其氢化效率为12.5g·l-1,选择性保持在97%。本发明的有益效果:本发明将含有铝、硅的成型溶胶采用喷雾分散油柱成型法得到微球形sio2-al2o3载体,其中sio2均匀分散于其中。以该微球形sio2-al2o3为载体制备的催化剂具有比表面及孔容较大,活性组分分散度高,磨损指数较小,耐磨损强度较高的特点。该催化剂用于流化床蒽醌法制备过氧化氢的氢化过程,具有较高的催化活性、选择性和稳定性。也可用于石油化工及精细化工生产中的加氢精制、选择性加氢和选择性氧化等反应过程。附图说明:图1为实施例1制备的微球形sio2-al2o3载体的显微分光光度计照片。图2为实施例1制备的微球形pd/sio2-al2o3的n2吸脱附曲线和孔径分布图。图3为实施例1制备的微球形pd/sio2-al2o3催化剂的xrd图。图4为实施例1制备的微球形pd/sio2-al2o3催化剂的hrtem照片。图5为实施例1制备的催化剂在流化床蒽醌加氢反应中的性能评价结果,(a)为蒽醌加氢活性随时间的变化曲线,(b)为蒽醌加氢稳定性随时间的变化曲线,(c)蒽醌加氢选择性随时间的变化曲线。具体实施方式:实施例1a.将10.00g平均粒径为50μm的铝粉溶于100.00g质量浓度为10%的盐酸溶液中制备铝溶胶。b.将4.47gna2sio3·9h2o溶于5.00g去离子水中,通过001×7(732)型强酸性聚苯乙烯系阳离子交换树脂,得到硅溶胶。c.将上述两溶液充分混合,再加入32.18g六次甲基四胺溶液(40wt%),搅拌均匀。通过蠕动泵以20ml/min的流速输送到分散喷头中,然后以0.15mpa的压力喷射到温度为80℃的25号变压器油中成型。从油中分离出成型的微球,于130℃烘箱中老化5h。d.将上述产品抽滤洗涤,90℃干燥12h,然后于马弗炉中960℃条件下焙烧4h,得到sio2含量为4%的微球形sio2-al2o3载体。e.称取2.00g步骤d制备的微球形sio2-al2o3载体置于100ml烧杯中,将10ml0.0305m的na2pdcl4溶液迅速倒入上述载体中,并不断晃动使其充分接触,静置3h,待浸渍溶液颜色褪去后,倾去上层透明溶液,用去离子水洗涤4次,然后于室温下陈化14h,再以5℃·min-1的速率升温至120℃并恒温保持4h。冷却后,将其置于马弗炉中,以10℃·min-1的速率升温至450℃,保温4h,冷却至室温,即得pd含量为1.5%的微球形pd/sio2-al2o3催化剂。对制备的微球形pd/sio2-al2o3的比表面积、孔结构和磨损指数进行分析,结果如表1所示,从表中可以看出,该催化剂具有较大的比表面积和适宜的孔结构,且磨损指数较小,表明其耐磨损强度较高。表1比表面积/(m2·g-1)孔容/(cm2·g-1)平均孔径/(nm)磨损指数(wt%)119.10.5921.21.9将0.3g催化剂装填入流化床反应器中,在反应器外有恒温水浴夹套,温度控制在50±5℃。工作液中蒽醌浓度为100g/l,溶剂为磷酸三辛酯和1,3,5-三甲苯的混合物,气体采用高纯氢气,评价该催化剂的流化床蒽醌加氢的活性、稳定性和选择性。实施例2a.将12.00g平均粒径为50μm的铝粉溶于100.00g质量浓度为10%的盐酸溶液中制备铝溶胶。b.将6.86gna2sio3·9h2o溶于7.00g去离子水中,通过001×12型强酸性聚苯乙烯系阳离子交换树脂,得到硅溶胶。c.将上述两溶液充分混合,再加入34.32g六次甲基四胺溶液(40wt%),搅拌均匀。通过蠕动泵以20ml/min的流速输送到分散喷头中,然后以0.15mpa的压力喷射到温度为80℃的25号变压器油中成型。从油中分离出成型的微球,于130℃烘箱中老化5h。d.将上述产品抽滤洗涤,90℃干燥12h,然后于马弗炉中1000℃条件下焙烧4h,得到sio2含量为6%的微球形sio2-al2o3载体。e.称取2.00g步骤d制备的微球形sio2-al2o3载体置于100ml烧杯中,将10ml0.061m的na2pdcl4溶液迅速倒入上述载体中,并不断晃动使其充分接触,静置3h,待浸渍溶液颜色褪去后,倾去上层透明溶液,用去离子水洗涤4次,然后于室温下陈化14h,再以5℃·min-1的速率升温至120℃并恒温保持4h。冷却后,将其置于马弗炉中,以10℃·min-1的速率升温至500℃,保温4h,冷却至室温,即得pd含量为3%的微球形pd/sio2-al2o3催化剂。实施例3a.将14.00g平均粒径为50μm的铝粉溶于100.00g质量浓度为10%的盐酸溶液中制备铝溶胶。b.将8.22gna2sio3·9h2o溶于7.00g去离子水中,通过7320型强酸性聚苯乙烯系阳离子交换树脂,得到硅溶胶。c.将上述两溶液充分混合,再加入35.24g六次甲基四胺溶液(40wt%),搅拌均匀。通过蠕动泵以20ml/min的流速输送到分散喷头中,然后以0.15mpa的压力喷射到温度为80℃的25号变压器油中成型。从油中分离出成型的微球,于130℃烘箱中老化5h。d.将上述产品抽滤洗涤,90℃干燥12h,然后于马弗炉中1050℃条件下焙烧4h,得到sio2含量为8%的微球形sio2-al2o3载体。e.将2.00g上述载体在10ml0.0915m的na2pdcl4溶液中浸渍3h,待浸渍溶液颜色褪去后,倾去上层透明溶液,用去离子水洗涤4次,然后于室温下陈化14h,再以5℃·min-1的速率升温至120℃并恒温保持4h。冷却后,将其置于马弗炉中,以10℃·min-1的速率升温至550℃,保温4h,冷却至室温,即得pd含量为4.5%的微球形pd/sio2-al2o3催化剂。实施例4a.将16.00g平均粒径为50μm的铝粉溶于100.00g质量浓度为10%的盐酸溶液中制备铝溶胶。b.步骤b.将11.93gna2sio3·9h2o溶于12.00g去离子水中,通过7320型强酸性聚苯乙烯系阳离子交换树脂,得到硅溶胶。c.将上述两溶液充分混合,再加入36.62g六次甲基四胺溶液(40wt%),搅拌均匀。通过蠕动泵以20ml/min的流速输送到分散喷头中,然后以0.15mpa的压力喷射到温度为80℃的25号变压器油中成型。从油中分离出成型的微球,于130℃烘箱中老化5h。d.将上述产品抽滤洗涤,90℃干燥12h,然后于马弗炉中1100℃条件下焙烧4h,得到sio2含量为10%的微球形sio2-al2o3载体。e.将2.00g上述载体在10ml0.0305m的na2pdcl4溶液中浸渍3h,待浸渍溶液颜色褪去后,倾去上层透明溶液,用去离子水洗涤4次,然后于室温下陈化14h,再以5℃·min-1的速率升温至120℃并恒温保持4h。冷却后,将其置于马弗炉中,以10℃·min-1的速率升温至600℃,保温4h,冷却至室温,即得pd含量为1.5%的微球形pd/sio2-al2o3催化剂。实施例5步骤a、b同实施例1。步骤c.将六次甲基四胺溶液(40wt%)的质量为36.6g,搅拌均匀。通过蠕动泵以30ml/min的流速输送到自制的喷头中,然后以0.15mpa的压力喷射到温度为90℃的真空泵油中成型。从油中分离出成型的微球,于140℃烘箱中老化12h。步骤d.将得到的产品进行抽滤洗涤,120℃干燥6h,待完全干燥后,在960℃下焙烧4h,得到sio2含量为4%的微球形sio2-al2o3载体。步骤e.将2.00g上述载体在10ml0.0166m的h2ptcl4溶液中浸渍3h,待浸渍溶液颜色褪去后,倾去上层透明溶液,用去离子水洗涤5次,再在室温下陈化12h,再以5℃·min-1的速率升温至110℃干燥并恒温保持4h。干燥后,将其置于马弗炉中,以10℃·min-1的速率升温至450℃,保温4h,然后冷却至室温,即得pt含量为1.5%的催化剂。实施例6步骤a、b同实施例1。步骤c.将六次甲基四胺溶液(40wt%)的质量为36.6g,搅拌均匀。通过蠕动泵以10ml/min的流速输送到自制的喷头中,然后以0.1mpa的压力喷射到温度为90℃的定子油中成型。从油中分离出成型的微球,于140℃烘箱中老化12h。步骤d.将得到的产品进行抽滤洗涤,100℃干燥12h,待完全干燥后,于960℃下焙烧6h,得到sio2含量为4%的微球形sio2-al2o3载体。步骤e.将2.00g上述载体在10ml0.0165m的haucl4浸渍溶液中浸渍3h,待浸渍溶液颜色褪去后,倾去上层透明溶液,用去离子水洗涤6次,再在室温下陈化12h,再以5℃·min-1的速率升温至110℃干燥并恒温保持4h。干燥后,将其置于马弗炉中,以10℃·min-1的速率升温至450℃,保温4h,然后冷却至室温,即得au含量为1.5%的催化剂。当前第1页12